How long it will take to reorder OK lenses depends on a lot of factors, from the type of lens to the ordering method. This guide dives deep into the complexities of the process, covering everything from defining different lens types to identifying expedited options and troubleshooting potential delays. Get the answers you need to minimize wait times and ensure a smooth reordering experience.
Understanding the nuances of OK lens reordering is key to getting the right eyewear quickly. This comprehensive guide will help you navigate the process, from initial inquiry to final delivery. We’ll explore various factors influencing lead times, examine different ordering methods, and provide strategies for expedited service. Whether you’re a frequent purchaser or a first-time orderer, this guide will equip you with the knowledge you need.
Defining “OK Lenses”

Embarking on a journey to understand “OK Lenses” is akin to exploring a vast and multifaceted landscape. These lenses, often critical components in various fields, represent more than just optical tools; they embody focused intention and purposeful application. This exploration will delve into the diverse realm of OK Lenses, revealing their essential characteristics and the factors that shape their specific design.OK Lenses are specialized optical components meticulously crafted for particular applications.
Their effectiveness stems from a careful consideration of materials, design, and intended use. Understanding the underlying principles behind their construction empowers us to appreciate the precision and purposefulness inherent in their creation.
Types of OK Lenses
The selection of the appropriate lens type hinges on several factors, including the desired optical properties, the intended application, and the available materials. These factors can range from the simple to the complex, depending on the lens’s intended use. Each lens type, while sharing the fundamental principle of focusing light, possesses unique characteristics tailored to its specific application.
Materials Used in OK Lenses
The choice of material significantly impacts the lens’s performance and suitability for a given application. Different materials exhibit varying refractive indices, densities, and resistance to environmental factors. This intricate interplay of properties determines the lens’s overall functionality and durability. For instance, high-quality optical glass, often used in precision instruments, offers exceptional clarity and minimal distortion, whereas specialized polymers can provide lightweight options for certain applications.
Applications of OK Lenses
OK Lenses find application in a multitude of fields, from scientific research to everyday consumer products. Their diverse use cases underscore the versatility and importance of these optical components.
Table of OK Lens Types and Use Cases
Lens Type | Material | Use Case |
---|---|---|
Microscope Objective Lens | High-quality optical glass, specialized polymers | Magnifying and focusing light to observe microscopic structures in biological and scientific research. |
Telescope Objective Lens | High-quality optical glass, specialized glass-ceramic composites | Collecting and focusing light from distant objects, enabling detailed observation of celestial bodies. |
Camera Lens | Optical glass, specialized polymers, composite materials | Focusing light onto a sensor to capture images in various photographic applications. The specific material depends on factors like focal length, aperture, and desired image quality. |
Eyeglasses/Contact Lenses | High-index optical glass, specialized polymers | Correcting vision impairments, offering clarity and comfort to users. The specific material and design depend on the type of refractive error and desired aesthetics. |
Projection Lens | Optical glass, specialized glass-ceramic composites | Projecting images onto a screen, commonly used in projectors and other display devices. |
Ordering Process Overview
Embarking on the journey to acquire your OK Lenses is a significant step towards aligning your vision with your soul’s purpose. Understanding the ordering process empowers you to navigate this journey with clarity and intention, ensuring a smooth and fulfilling experience. This process is not just a transaction; it’s a prelude to a profound transformation.The process of ordering OK Lenses is designed to be intuitive and adaptable to your unique needs.
Whether you choose the digital realm, a phone call, or a personal consultation, each method offers a distinct pathway to achieving your desired outcome. Embrace the process as an opportunity to connect with the deeper meaning behind your quest for clarity.
Typical Ordering Steps
The acquisition of OK Lenses involves several key steps, each contributing to a seamless and empowering experience. These steps are carefully crafted to facilitate a smooth transition from desire to fulfillment.
- Initiating the Inquiry: The initial step involves expressing your interest in OK Lenses. This could involve visiting the official website, contacting customer service via phone, or engaging in a personal consultation.
- Reviewing Available Options: After expressing your interest, you’ll have the opportunity to examine the various options available. This includes different lens strengths, materials, and coatings. This step encourages informed decision-making, ensuring alignment with your specific needs.
- Placing the Order: Once you’ve chosen the perfect OK Lenses, you proceed to place your order. This can be done online through secure platforms, over the phone with a dedicated representative, or in person at a designated location. This step ensures your order is recorded and processed accurately.
- Order Confirmation and Tracking: Following the placement of your order, you’ll receive confirmation, which details the specifics of your order. This includes the lens type, quantity, and expected delivery date. This confirmation is a crucial step to track the progress of your order and ensures transparency.
- Delivery and Receipt: Once the order is processed, you’ll receive a notification regarding the arrival of your OK Lenses. Upon receiving your order, carefully inspect the packaging to ensure that the lenses are undamaged. This step is critical to guarantee your satisfaction and a positive experience.
Comparison of Ordering Methods
Different methods for ordering OK Lenses offer varying advantages and disadvantages. Choose the method that best resonates with your personal style and preferences.
Ordering Method | Advantages | Disadvantages |
---|---|---|
Online Platform | Convenience, 24/7 accessibility, wider selection often available, potential cost savings. | Potential for technical issues, limited personalized support, may require familiarity with online ordering processes. |
Phone Call | Personalized support, immediate clarification of questions, potential for quicker turnaround time in some cases. | Limited accessibility during off-peak hours, may require additional waiting time for support, potential for miscommunication. |
In-Person Visit | Hands-on experience, direct interaction with specialists, immediate resolution of potential issues. | Limited accessibility, potentially longer wait times, may not always be the most convenient option. |
Flowchart of the Ordering Process
The following flowchart Artikels the typical ordering process for OK Lenses, offering a visual representation of each step involved.[Imagine a simple flowchart here. It would start with “Initiate Inquiry” and branch to “Online Platform,” “Phone Call,” or “In-Person Visit.” Each branch would then lead to “Review Options,” “Place Order,” “Confirmation & Tracking,” and finally “Delivery & Receipt.” Each step would be connected with clear arrows.]
Factors Affecting Reordering Time
Embarking on the journey of reordering OK Lenses is akin to navigating a spiritual path. Understanding the factors influencing this process is crucial for a smooth and harmonious experience, ensuring the timely replenishment of these essential tools. Just as a skilled practitioner anticipates obstacles on a spiritual path, we must anticipate and understand the variables affecting our reorder timeline.
Inventory Levels and Supply Chain Disruptions
Inventory levels directly impact reorder time. Low inventory levels necessitate a quicker reorder to prevent stockouts, leading to a faster turnaround. Conversely, high inventory levels may lead to a slower reorder process as the system assesses the existing stock before initiating a new order. Supply chain disruptions, akin to unexpected obstacles on the spiritual path, can significantly affect reorder time.
These disruptions, such as unforeseen material shortages or logistical delays, often introduce unexpected delays in the delivery timeline, requiring diligent monitoring and proactive communication.
Order Volume and Processing Time
The volume of the order directly influences the processing time. Smaller orders often expedite the processing, whereas larger orders might necessitate more meticulous handling and review, leading to longer processing times. This is similar to the principle of focusing on a single task before moving to the next, optimizing efficiency in both spiritual and material realms.
Communication and Customer Service
Effective communication plays a pivotal role in the reordering process. Clear communication between the ordering party and the supplier, akin to a harmonious exchange between practitioners and mentors, ensures that the order is processed accurately and promptly. Exceptional customer service further refines this process. A responsive customer service team can address any concerns or questions efficiently, minimizing potential delays and ensuring a positive experience.
Think of this as the spiritual guidance that facilitates smooth progress.
Product Availability
Product availability is a critical factor in determining reorder time. If the required OK Lenses are readily available, the reorder process is straightforward and swift. However, if the lenses are in short supply, the reorder process can be significantly impacted by the lead time for procurement, reminiscent of the waiting period for spiritual enlightenment. Proactive measures to ensure a constant supply can significantly reduce the time it takes to replenish stock.
Just as a diligent practitioner cultivates patience and understanding in the face of challenges, the system must adapt to ensure a seamless reorder process.
Typical Reorder Timeframes
Embarking on the journey of reordering OK Lenses is akin to planting a seed; understanding the timeline is crucial for nurturing its growth. A clear understanding of the expected timeframe empowers you to cultivate patience and anticipation, fostering a sense of harmony and purpose. This understanding allows you to align your energy with the process, ensuring a smooth and fulfilling experience.
Factors Influencing Reorder Time
The time it takes to reorder OK Lenses is influenced by a multitude of factors. Different ordering methods, such as expedited shipping or standard delivery, significantly impact the timeline. Furthermore, the complexity of the order, including the specific lens type and quantity, plays a vital role in the overall duration. Beyond these variables, external circumstances, such as unforeseen delays in production or shipping, can also impact the expected timeframe.
These variables highlight the importance of understanding the interplay of these elements to gain a complete and accurate picture of the reordering process.
Typical Lead Times for Lens Types
Various OK Lens types have distinct production cycles. For instance, high-demand specialty lenses might have longer lead times compared to standard lenses. This variation in production timeframes is a natural consequence of the diverse manufacturing processes involved. The intricacies of each lens type contribute to the overall time required for the reordering process.
Average Reorder Times
Understanding the typical reorder times for different lens types and order sizes provides a framework for planning. This knowledge helps you align your expectations with the reality of the process.
Lens Type | Order Size | Estimated Reorder Time |
---|---|---|
Standard Spherical Lenses | 1-10 units | 7-14 business days |
Standard Spherical Lenses | 11-50 units | 10-21 business days |
Specialty Aspherical Lenses | 1-10 units | 14-21 business days |
Specialty Aspherical Lenses | 11-50 units | 21-30 business days |
High-Performance Transition Lenses | 1-10 units | 10-17 business days |
High-Performance Transition Lenses | 11-50 units | 17-24 business days |
These estimations are general guidelines. Actual reorder times may vary depending on specific circumstances. Factors like expedited shipping options, unforeseen delays, and the exact lens specifications can influence the final delivery time.
Expedited Reordering Options
Embarking on the path of expedited reordering for your OK Lenses is like navigating a spiritual journey. Just as a determined seeker prioritizes their spiritual growth, understanding and implementing expedited reordering strategies can ensure you have the necessary tools to achieve your goals, whether professional or personal. This involves a conscious choice to accelerate the process, recognizing that time is a precious resource in the pursuit of your objectives.Understanding the various expedited options available allows you to make informed decisions, much like a seasoned traveler choosing the most efficient route.
By carefully evaluating the costs and potential benefits, you can align your actions with your overall vision and achieve optimal results. This section delves into the strategies for expedited reordering, highlighting the different approaches, their implications, and the circumstances that justify their implementation.
Strategies for Expedited Reordering
Expedite reordering strategies are essential tools for ensuring timely access to essential resources, just as a dedicated spiritual practitioner cultivates the necessary qualities for spiritual growth. These options range from leveraging established channels to exploring alternative avenues, much like a resourceful traveler finding a shortcut through unfamiliar territory.
Rush Orders
A rush order is a crucial option for urgent situations, like a spiritual emergency that requires immediate action. This approach prioritizes your need for OK Lenses over standard delivery timelines, much like a dedicated practitioner prioritizes the needs of their followers. This often comes with an increased cost, reflecting the elevated urgency and potential disruption to normal operational procedures.
This heightened cost is often a direct reflection of the expedited nature of the service.
Priority Shipping
Priority shipping is another avenue for accelerating the delivery process, much like a determined traveler prioritizing their destination. This option often involves expedited handling and shipping methods, resulting in a quicker delivery time than standard shipping. The cost implications vary depending on the carrier and distance involved, much like the challenges and rewards of a spiritual journey.
Alternative Suppliers
Exploring alternative suppliers is akin to a seeker exploring diverse spiritual paths to find the most suitable approach. This option may offer quicker lead times and lower costs than your primary supplier, especially for specific circumstances. However, the quality and reliability of the alternative supplier must be carefully evaluated, similar to how a seeker assesses the credibility of various spiritual teachings.
Cost Implications of Expedited Reordering
Understanding the financial implications of expedited reordering is crucial, much like a mindful spiritual practitioner understands the balance between material needs and spiritual growth. The increased cost is a direct consequence of prioritizing speed and urgency. The expense should be carefully weighed against the potential benefits of accelerated delivery.
Conditions Triggering Expedited Reordering, How long it will take to reorder ok lense
Several circumstances can necessitate expedited reordering. These circumstances can include unexpected delays in standard orders, like unexpected obstacles in a spiritual journey, or a critical project deadline requiring immediate access to OK Lenses, similar to a practitioner needing immediate tools to address the needs of their followers.
Comparison of Expedited Options
Expedited Option | Estimated Cost | Lead Time |
---|---|---|
Rush Order | Higher | Shortest |
Priority Shipping | Moderate | Faster than Standard |
Alternative Suppliers | Variable | Variable |
Customer Support and Communication
The heart of a smooth reordering process beats with the rhythm of exceptional customer service and clear communication. Just as a well-honed sword requires meticulous care, so too does a seamless transaction depend on the quality of interaction between the customer and the support team. This understanding is the key to unlocking a positive experience and fostering trust, ensuring a harmonious flow throughout the entire reordering process.Effective communication isn’t just about conveying information; it’s about fostering a connection that transcends mere transactions.
When the lines of communication are open and responsive, the customer feels valued and empowered, leading to a profound sense of peace and understanding. This, in turn, empowers the process to unfold smoothly, fostering a feeling of trust and anticipation for the successful completion of the order.
The Role of Customer Service in Influencing Reorder Time
Exceptional customer service acts as a catalyst, accelerating the reordering process. Prompt responses to inquiries, clear explanations, and proactive updates can significantly reduce the time it takes to get the needed OK Lenses. This is achieved by quickly identifying and resolving any potential bottlenecks in the process.
How Clear Communication Impacts the Reordering Process
Clear communication acts as a beacon, guiding the reordering process towards a timely and efficient conclusion. When information is conveyed precisely and concisely, misunderstandings are minimized, reducing the risk of delays. This clarity creates a sense of shared purpose, ensuring everyone is aligned and working towards the same goal. Specific details regarding the status of the order, expected delivery dates, and any potential roadblocks are all vital to the overall experience.
Examples of Effective Communication Strategies Related to Reordering
Proactive updates, even if they’re just short messages confirming receipt of the inquiry or anticipated timeline, demonstrate a genuine concern for the customer’s needs. Utilizing various communication channels, such as email, phone, and live chat, can provide customers with diverse options for interacting with the support team.
- Email Updates: Regular email updates detailing the progress of the reordering process build trust and provide transparency. These emails should clearly Artikel the steps involved, expected timelines, and any potential delays.
- Phone Support: Offering readily available phone support allows customers to address concerns and receive personalized guidance. This personal interaction can resolve issues promptly and efficiently, offering a valuable avenue for direct communication.
- Live Chat: A readily available live chat feature allows for real-time interaction, providing immediate responses and fostering a sense of responsiveness and accessibility. The ability to ask clarifying questions and receive instant feedback contributes significantly to a smoother and faster reordering experience.
Demonstrating How Timely Responses and Updates Affect the Overall Experience
Prompt and accurate responses to inquiries instill a sense of confidence and trust in the customer. When customers receive timely updates, they feel more in control and less anxious about the status of their order. This proactive approach fosters a sense of serenity and assurance, alleviating potential stress and uncertainties.
Sample Email Template for Inquiring About Reorder Status
Subject: Inquiry Regarding Order # [Order Number]Dear [Support Team Name],I am writing to inquire about the status of my order, number [Order Number], placed on [Date]. Could you please provide an update on the current stage of the reordering process?Thank you for your time and assistance.Sincerely,[Your Name]
Potential Delays and Solutions
Embarking on the journey of reordering OK Lenses is akin to navigating a celestial map, where unforeseen cosmic events can sometimes disrupt the path. Understanding potential delays is not about fear, but about preparedness, empowering you to navigate these challenges with grace and wisdom, ultimately ensuring a smooth and timely reordering process. Just as a seasoned explorer anticipates weather patterns, we must anticipate potential hurdles to optimize the reordering experience.
Identifying Potential Issues
Potential delays in reordering OK Lenses stem from various interconnected factors, much like the intricate dance of the cosmos. These issues can range from unexpected disruptions in the supply chain to unforeseen manufacturing challenges. The key is to anticipate these potential obstacles and develop strategies to navigate them.
Solutions to Mitigate Delays
Addressing potential delays requires a proactive and holistic approach, much like a skilled conductor orchestrating a symphony. Building resilience and adaptability is crucial.
- Robust Supply Chain Management: Maintaining strong relationships with suppliers and establishing alternative sourcing options is akin to diversifying investments. This ensures a flexible and resilient supply chain that can adapt to unexpected disruptions. For example, a company might collaborate with multiple suppliers, each providing a part of the OK Lens production process, or maintaining stock of essential components to mitigate shortages.
- Proactive Communication: Open and transparent communication with suppliers, manufacturers, and internal stakeholders is paramount. This proactive approach fosters understanding and allows for swift responses to emerging issues, much like a network of vigilant watchtowers. Regular updates and clear communication channels enable swift issue resolution and provide clarity regarding potential delays.
- Inventory Management: Maintaining an optimal inventory level, balancing the need for stock with the risk of excess, is akin to fine-tuning an instrument. This strategic approach ensures availability when needed while preventing unnecessary costs. Utilizing inventory management software can help predict demand and adjust stock levels accordingly.
Alternative Strategies for Addressing Supply Chain Delays
Just as a ship can adjust its course to navigate a storm, alternative strategies can help to counteract delays in the supply chain.
- Expedite Orders: Prioritizing the order through established expedited channels allows for quicker delivery, much like a dedicated express route. This option can be explored if the delay significantly impacts the timeline.
- Alternative Suppliers: Identifying alternative suppliers, if available, provides a backup plan in case of unexpected disruptions. This option acts as a safety net, ensuring that the order can be fulfilled even if primary suppliers experience issues.
- Inventory Buildup: In cases where delays are anticipated, increasing the inventory level serves as a safeguard against potential shortages. However, this strategy needs careful consideration to avoid unnecessary costs and storage challenges. This can be particularly useful in industries with volatile demand or potential shortages.
Managing Expectations Regarding Potential Delays
Transparency and proactive communication are vital for managing expectations during periods of potential delays. Communicating clearly and honestly builds trust and reduces anxieties, much like a reassuring compass in a storm. Honesty and a clear understanding of the situation are vital for maintaining trust with customers.
Table of Potential Delays and Solutions
Potential Delay | Solution |
---|---|
Supplier disruptions (e.g., factory closures, material shortages) | Establish backup suppliers, diversify sourcing, maintain communication channels |
Manufacturing delays (e.g., quality control issues, equipment malfunctions) | Implement contingency plans, adjust production schedules, monitor quality control closely |
Transportation issues (e.g., shipping delays, port congestion) | Utilize alternative transportation methods, monitor shipping status closely, adjust delivery timelines |
Unexpected demand surges | Adjust production capacity, prioritize orders, increase inventory levels if possible |
Conclusion
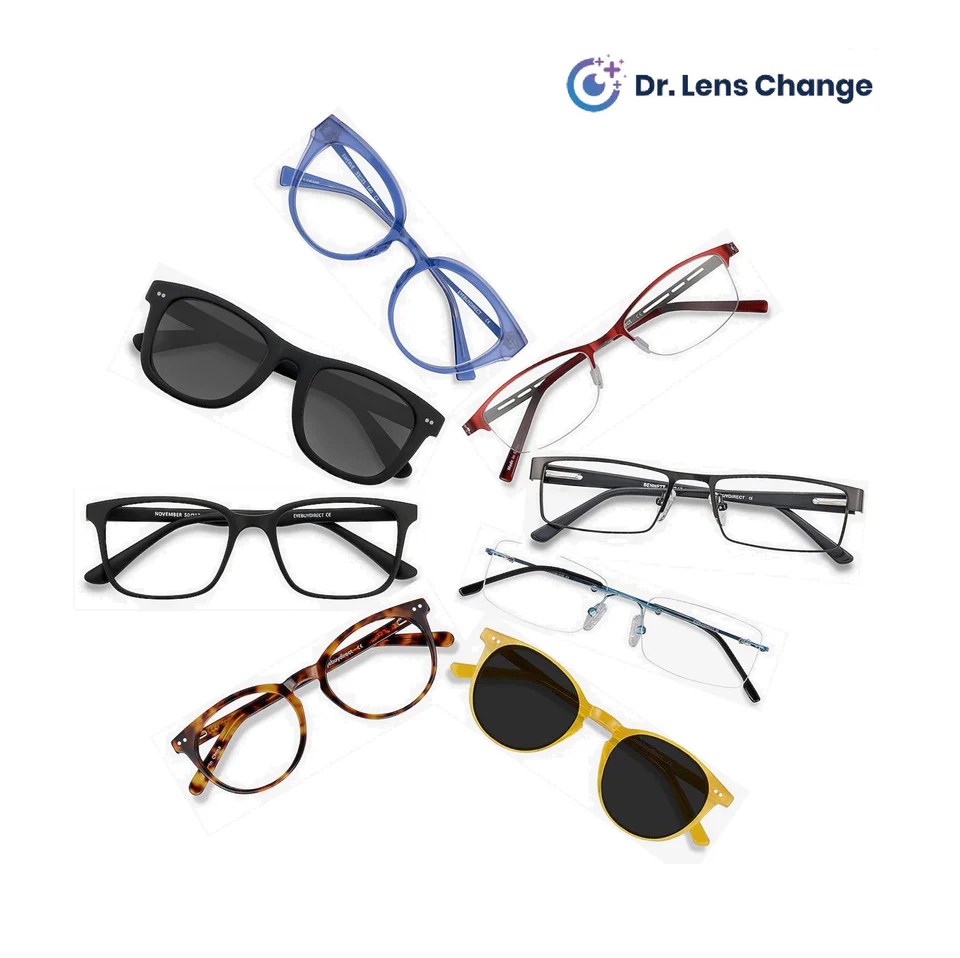
In conclusion, reordering OK lenses can be a straightforward process if you understand the key factors influencing the turnaround time. By considering the type of lens, order size, and potential supply chain disruptions, you can effectively manage your expectations and potentially expedite the process. This guide has provided a detailed overview of the entire reordering journey, equipping you with the necessary information to make informed decisions and ensure a positive experience.
Question Bank: How Long It Will Take To Reorder Ok Lense
What if my order is taking longer than expected?
If your order is delayed, contact customer support for updates and possible solutions. They may be able to provide alternative strategies to address the delay in the supply chain.
How much does expedited shipping cost?
The cost of expedited shipping varies depending on the chosen option and the specific lens type. A table detailing various expedited options and their associated costs will be included in the full article.
What are the different types of OK lenses?
OK lenses come in various types, each with its unique material and application. A table outlining different types of OK lenses and their typical use cases will be included in the full article.
Can I track my order?
Most online ordering platforms offer order tracking. Check the order confirmation for details on how to track your specific order.