How to pin and weld a muzzle device is a critical procedure for firearm modifications, requiring meticulous attention to safety and precise execution. This guide provides a detailed, step-by-step approach, encompassing safety precautions, tool selection, and the meticulous techniques for successful pinning and welding. Understanding the diverse types of muzzle devices and their respective applications is fundamental to a safe and effective outcome.
From the initial disassembly of the muzzle device to the final post-weld inspection, this comprehensive guide addresses every facet of the process. Proper procedures and techniques are paramount to ensuring both the integrity of the firearm and the safety of the practitioner. A strong foundation in metalworking and welding principles is also highly recommended for successful completion.
Introduction to Muzzle Devices
Alright, folks, let’s talk about muzzle devices. Think of them as the accessories for your firearm’s muzzle – the end of the barrel where the bullet exits. They’re not just for looks, though a snazzy compensator can certainly impress your buddies at the range. They serve a variety of important functions, from reducing recoil to controlling muzzle flash.
Let’s dive in!Muzzle devices are essentially modifications or attachments to the end of a firearm’s barrel. They’re designed to modify the projectile’s trajectory, control muzzle flash, reduce recoil, and often improve accuracy. Think of them as tuning your firearm’s output.
Types of Muzzle Devices
Muzzle devices come in a range of styles, each with its own unique function. From the subtle to the flashy, they all have a purpose.
- Compensators: These are like tiny, intricate turbines designed to reduce recoil and improve accuracy. Imagine the spinning parts redirecting the gases from the bullet’s exit, smoothing out the whole firing experience. They’re popular with shooters who want to keep their aim steady after each shot. They can also reduce muzzle rise, especially in high-powered rifles. They’re essentially sophisticated recoil management systems.
- Flash Hiders: These are the more straightforward, less flashy devices. They’re designed to reduce the amount of muzzle flash, which is important for both safety and stealth. Think about the difference between a bright, glaring flash and a more contained, controlled burst of light. They can also help reduce the visibility of the shooter’s position to an enemy.
- Suppressors (or Mufflers): These are the heavy hitters in the noise reduction game. They significantly reduce the sound of the gunshot. They work by using baffles and chambers to contain and absorb the expanding gases, making them a must-have for many shooters in quiet shooting environments.
- Breachers: These are specialized muzzle devices designed for use with breaching rounds. They’re specifically designed to minimize the risk of ricochet or over-penetration when firing rounds designed to breach walls or doors.
Pinning and Welding
Pinning and welding is the process of permanently attaching a muzzle device to the barrel. It’s a critical step that requires precision and care. Improper installation can lead to malfunctions and, in extreme cases, injury. It’s like securing a vital piece of machinery to your vehicle – you need it to be sturdy and dependable.
Proper pinning and welding is essential for the safety and reliability of the firearm. Improper techniques can lead to premature failure and unsafe operation.
Importance of Proper Techniques
Proper pinning and welding techniques are crucial to ensure the muzzle device’s durability and the firearm’s safety. Think of it like building a house – you wouldn’t want shoddy foundations, would you? Correct techniques ensure the attachment is strong enough to withstand the forces of firing a round without compromising the barrel’s integrity.
Muzzle Device Comparison Table
This table summarizes the different muzzle device types and their common applications.
Muzzle Device Type | Primary Function | Common Applications |
---|---|---|
Compensator | Reduce recoil, improve accuracy | Competition shooting, precision rifles, target shooting |
Flash Hider | Reduce muzzle flash | Hunting, tactical applications, self-defense |
Suppressor | Reduce noise | Hunting, law enforcement, tactical applications |
Breacher | Minimize ricochet, over-penetration | Breaching doors or walls, controlled demolition |
Safety Precautions and Gear
Alright, folks, let’s talk about the
crucial* safety stuff. Pinning and welding a muzzle device isn’t rocket science, but it’s definitely not something you want to tackle without the proper precautions. Think of it like this
you wouldn’t go into a kitchen without an apron, right? Same idea here. Safety first!Welding and pinning can get messy, and we don’t want any accidents or injuries. Protecting yourself is paramount. So, let’s dive into the essential gear and procedures to keep you safe and sound.
Essential Safety Precautions
Proper safety precautions are the bedrock of any successful welding or pinning project. Ignoring them can lead to serious consequences, from minor burns to major injuries. Treating safety as a top priority is crucial for a smooth and accident-free process.
- Eye Protection: Welding sparks are like tiny, fiery projectiles. They can blind you in a flash. Always wear appropriate safety glasses or a full-face shield. Think of them as your first line of defense against those pesky sparks.
- Respiratory Protection: Welding fumes can be toxic. If you’re working in a confined space or dealing with heavy fumes, a respirator is essential. Don’t underestimate the importance of breathing properly while working with these materials. You wouldn’t want to risk lung damage, would you?
- Hearing Protection: Welding and hammering generate intense noise. Protect your ears with earplugs or muffs to prevent hearing loss. This is often overlooked, but it’s just as important as protecting your eyes.
- Appropriate Clothing: Wear long sleeves, pants, and sturdy shoes to prevent burns and injuries from sparks or flying debris. Think of it as your second layer of defense against the unpredictable.
- Fire Suppression Equipment: Keep fire extinguishers readily available in the work area. It’s a good idea to have a designated fire safety plan in place. A small fire can quickly escalate, so having the right equipment and knowing how to use it can be a lifesaver.
Required Safety Gear
Now, let’s talk about the essential gear. Having the right tools in your arsenal is key.
- Welding Helmet: A certified welding helmet is an absolute necessity. It shields your face and eyes from intense heat and radiation. Imagine a shield protecting you from a fiery dragon’s breath.
- Welding Gloves: Protect your hands from heat and sparks with heavy-duty welding gloves. You don’t want to end up with blisters or burns, do you?
- Safety Glasses/Face Shield: Protect your eyes from flying debris and sparks. These are crucial to prevent injuries. Imagine a shield protecting your eyes from a dangerous projectile.
- Hearing Protection: As mentioned before, protect your ears from loud noises. You’ll thank yourself later for not ending up with tinnitus or hearing loss.
Ventilation and Safe Environment
Working in a well-ventilated area is critical. Welding fumes can be harmful if inhaled, and a good airflow will help prevent health issues. Remember, a safe environment is crucial for a successful job.
Safety Gear | Role |
---|---|
Welding Helmet | Protects eyes and face from sparks and intense heat |
Welding Gloves | Protects hands from heat and sparks |
Safety Glasses/Face Shield | Protects eyes from flying debris and sparks |
Hearing Protection | Protects ears from loud noises |
Respiratory Protection (e.g., respirator) | Protects lungs from welding fumes |
Required Tools and Materials
Alright, folks, let’s dive into the nitty-gritty of the pinning and welding process. You need more than just a gun and a desire to create a masterpiece. We’re talking precise tools and carefully chosen materials – think of it as assembling a top-tier welding squad. Proper preparation is key, and we’ll cover everything from the essentials to the specifics.
Essential Welding Tools
The welding process demands specific tools for precise work. A well-equipped arsenal is crucial to avoid frustration and potential hazards. A basic toolkit is a must-have.
- Welding Machine: Not just any old machine will do. A DC stick welder, ideally with adjustable amperage settings, is a good start. The correct amperage is vital for the right weld penetration without scorching the metal. Think of it like dialing in the perfect volume on your favorite amplifier; too loud, and you damage the speakers.
Too quiet, and the music’s muffled. The same principle applies here.
- Welding Helmet: Safety first, right? A high-quality welding helmet with a dark-tinted lens is non-negotiable. This shields your eyes from harmful ultraviolet and infrared radiation. Imagine trying to watch a movie with your eyes wide open under a bright spotlight; not pleasant, right?
- Gloves: Welding gloves protect your hands from burns and flying debris. Choose heavy-duty leather gloves. You don’t want to be playing with fire without proper protection, right?
- Wire Brush: A wire brush is used to clean the weld area before welding. This ensures a strong and reliable weld. Think of it like a thorough scrub before a big dinner party; you wouldn’t want to serve food with leftover crumbs, would you?
- Protective Clothing: Welding can create sparks and spatter. Wear a long-sleeved shirt, pants, and shoes to protect your skin. Think of it as your armor against the unpredictable nature of the welding process.
Welding Materials
The right materials are as crucial as the right tools. Let’s get into the specifics.
- Pins: The pins secure the muzzle device to the firearm. They need to be strong enough to hold the device in place but not so strong that they deform the barrel. Consider using stainless steel pins, as they are durable and resist corrosion. Imagine using a flimsy paperclip to hold a heavy object; it’s not going to work.
- Welding Rods: The type of welding rod used is dependent on the specific metal you are working with. Stainless steel welding rods are common for welding steel muzzle devices. Ensure that the rod’s composition matches the metal you are working with for a strong and reliable weld. Don’t use the wrong paint for your car; you’ll end up with a mess, right?
- Safety Glasses: Welding safety glasses are a must. Protect your eyes from flying sparks and debris. Imagine trying to watch a movie with your eyes wide open under a bright spotlight; not pleasant, right?
- Metal Cutting Tool: This is a necessity for trimming and shaping metal pieces. A metal cutting tool with the correct blade is essential to get the perfect cut for welding. Think of it as a precision knife for the metal.
Specifications Table
Here’s a quick overview of the tools and materials, along with their specifications.
Item | Description | Specifications |
---|---|---|
Welding Machine | DC stick welder | Adjustable amperage settings |
Welding Helmet | High-quality | Dark-tinted lens |
Welding Gloves | Heavy-duty leather | Appropriate for welding tasks |
Wire Brush | Cleaning tool | Suitable for metal surfaces |
Protective Clothing | Long-sleeved shirt, pants, shoes | Provides comprehensive protection |
Pins | Securing pins | Stainless steel, appropriate strength |
Welding Rods | Welding material | Match the barrel metal composition |
Safety Glasses | Eye protection | High-quality lenses, for sparks and debris |
Metal Cutting Tool | Metal shaping | Correct blade for metal type |
Preparing the Muzzle Device
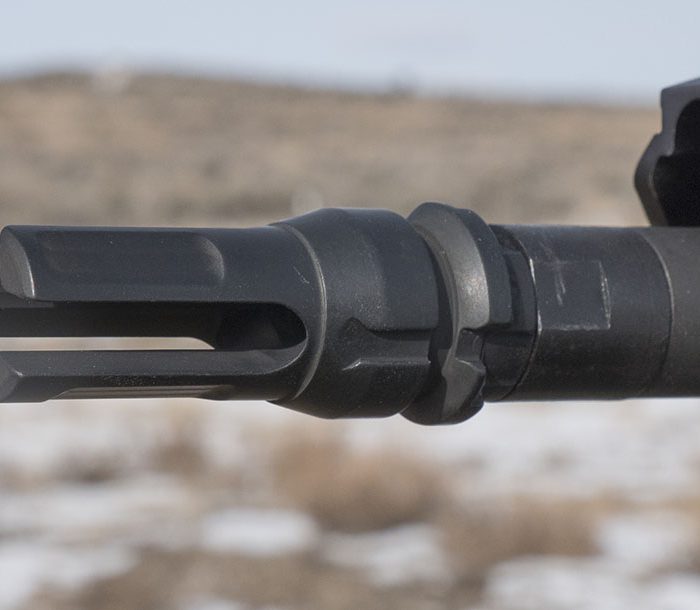
Alright, folks, let’s talk about getting that muzzle device ready for its pinning and welding party. This isn’t rocket science, but precision is key. Think of it as preparing a gourmet dish – you wouldn’t want to throw raw ingredients into a hot oven without prepping them first, would you?This section details the crucial steps in disassembling, cleaning, and inspecting your muzzle device to ensure a flawless welding job.
We’ll cover the process from start to finish, so you can confidently tackle this part of the project.
Disassembling the Muzzle Device
Before you even think about pinning and welding, you gotta take the device apart. This lets you get a good look at everything and make sure nothing’s hiding any nasty surprises. Proper disassembly prevents damage during the welding process.
- First, carefully remove any screws, pins, or fasteners holding the muzzle device to the firearm. Consult the manufacturer’s instructions for the exact procedure.
- Once all the fasteners are removed, gently separate the device from the firearm, ensuring no damage occurs to either component. Treat the firearm and muzzle device with respect. A little care goes a long way!
- If your device has internal components, such as a flash hider or compensator, now’s the time to remove them. Keep track of every piece, noting their position and any identifying marks. A messy disassembly is a disaster waiting to happen!
Cleaning and Inspecting the Device
A clean device is a happy device. Before pinning and welding, give it a good scrubbing. This ensures a strong bond and prevents corrosion later. Inspect for any damage or defects that might affect the weld.
- Use a degreaser to remove any oils, grease, or dirt from the muzzle device’s surfaces. A good degreaser is your friend here.
- Inspect for any cracks, chips, or deformations. A tiny imperfection can become a major problem down the road. Look closely!
- Thoroughly rinse the device with clean water to remove any traces of the degreaser. And dry it completely to prevent rust formation.
Preparing the Device for Welding, How to pin and weld a muzzle device
Now, let’s get ready for the weld. This is where precision matters most. Make sure the surfaces are perfectly clean and free of contaminants. A good weld is the result of careful preparation.
- Ensure the surfaces intended for welding are smooth and free of any burrs or imperfections. A smooth surface gives you a better weld.
- Apply a suitable primer to the surfaces where the welding will take place. This helps the weld adhere properly and increases its strength.
- Check the device’s alignment with the firearm to ensure a perfect fit. Misalignment leads to issues with the finished product. Verify the fit now.
Ensuring Readiness for Pinning and Welding
This is the final checklist. Double-check everything to guarantee a smooth pinning and welding process. A flawless weld starts with meticulous preparation.
- Verify all fasteners are present and in good condition. A missing screw can cause problems.
- Confirm the surfaces are properly cleaned, primed, and free of contaminants. A contaminated surface will affect the weld.
- Check that the device is aligned with the firearm and that all components are in place. A misalignment will create a poor weld.
Pinning Procedure
Alright, buckle up buttercup, because we’re about to dive into the delicate art of pinning a muzzle device. This ain’t rocket science, but precision is key. Think of it like assembling a tiny puzzle, where one wrong move can lead to a catastrophic malfunction. So, let’s get this show on the road!This section details the crucial steps in pinning your muzzle device securely.
Correct pinning ensures the device stays put and functions as intended. Improper pinning, on the other hand, can lead to wobbly devices and, in worst-case scenarios, potentially dangerous malfunctions. So, let’s make sure we do this right the first time!
Pin Installation Procedures
Pinning is a straightforward process, but it’s important to maintain accuracy. The pins are designed to be precisely aligned to ensure a snug fit, and prevent movement under stress. Proper installation is essential to prevent any unwanted movement or vibrations during firing. A well-pinned muzzle device guarantees optimal performance and reduces the risk of malfunction.
Precise Pin Alignment
To ensure proper function, aligning the pins precisely is critical. Misalignment can lead to the device shifting during firing, causing inaccurate firing or potentially even dangerous malfunctions. Accurate alignment is key to ensuring a secure fit. Visual inspection using a ruler or similar measuring device, and ensuring the pins are centered within the holes, is critical. Consider using a flashlight to check for any misalignment.
Utilizing the Pin-Setting Tool
Using the correct pin-setting tool is essential. A poorly chosen tool can damage the device or cause the pins to be improperly set. The right tool ensures the pins are driven into place without damaging the threads or the material. A suitable pin-setting tool is designed for the specific type of pin used, and will help you to achieve the necessary pressure without marring the surface.
Ensuring Secure Pins
There are several methods for ensuring the pins are securely in place. A common technique involves using a small amount of threadlocker, or using specialized locking pins. These methods ensure the pins don’t work their way loose over time. Another crucial step is inspecting the pins for any signs of looseness or movement after installation.
Pinning Procedure Table
Step Number | Actions | Necessary Tools |
---|---|---|
1 | Inspect the muzzle device and the pins for any damage or imperfections. | Magnifying glass, flashlight |
2 | Clean the pin holes and the pin ends with a clean cloth or appropriate cleaning agent. | Cleaning cloth, degreaser (optional) |
3 | Insert the pin into the designated hole, ensuring proper alignment. | Pin-setting tool, alignment guide (optional) |
4 | Using the pin-setting tool, carefully drive the pin into the hole until it is fully seated. | Pin-setting tool |
5 | Inspect the pins for any signs of movement or looseness. | Visual inspection |
6 | Apply a small amount of threadlocker to the pin threads, if applicable. | Threadlocker, small applicator |
Welding Procedure
Alright, buckle up buttercups, because we’re about to dive into the fiery world of muzzle device welding! This isn’t your grandma’s knitting circle; we’re talking about precision and heat, baby. Getting the weld just right is crucial for a strong, reliable, and safe attachment.
Welding Techniques
Various welding techniques can be used for this task, each with its own pros and cons. MIG (Metal Inert Gas) welding is a popular choice for its speed and relatively straightforward setup. Stick (SMAW) welding offers a bit more control, great for those hard-to-reach spots. TIG (Tungsten Inert Gas) welding, while more finicky, provides the highest precision.
Choosing the right technique depends on your experience level and the specific design of your muzzle device. For most DIY projects, MIG welding is a good starting point.
Welding Machine Settings
The welding machine’s settings are paramount. Incorrect settings can lead to a weak weld, or worse, a weld that’s too hot, warping the metal and potentially causing a catastrophic failure. The amperage and voltage must be precisely calibrated to the specific metal and the thickness of the pins. Too little heat, and you’ll end up with a weak weld.
Too much heat, and you’ll melt your pins right off. Think of it like cooking; you need the right temperature for the right ingredient. Experimentation with a scrap piece of metal is always recommended before tackling your actual muzzle device.
Applying the Weld
Proper weld application is key. Start with a clean, smooth surface. Overlap the weld beads to create a continuous and even layer. Focus on maintaining a consistent speed and consistent weld depth to prevent creating weak spots. Imagine a beautiful, flowing river; that’s what a good weld should look like.
Avoid creating ripples or excessive spatter. These imperfections can compromise the weld’s integrity. Take your time, and focus on quality over quantity.
Cooling and Post-Weld Checks
After welding, proper cooling is critical. Allow the metal to cool gradually to avoid warping or cracking. Don’t rush the process. Let it cool completely before handling it. After cooling, meticulously examine the weld for any cracks, voids, or other imperfections.
A magnifying glass can be your best friend here. A properly executed weld should have a smooth, consistent appearance with no signs of flaws. A simple visual inspection is a crucial first step.
Welding Steps and Parameters
Step | Technique | Amperage (Amps) | Voltage (Volts) | Wire Feed Speed (in/min) | Description |
---|---|---|---|---|---|
1 | MIG | 100 | 20 | 10 | Initial pass, establish weld puddle |
2 | MIG | 120 | 22 | 12 | Add layers to fill gap |
3 | MIG | 100 | 20 | 10 | Final pass for smoothness |
Welding parameters are approximate and should be adjusted based on the specific materials and equipment.
Post-Welding Inspection and Finishing: How To Pin And Weld A Muzzle Device
Alright, so you’ve wrestled with the welding torch, and now your muzzle device is practically a work of art… almost. Time to make sure it’s not just pretty, but also functional and safe. Let’s get down to the nitty-gritty of post-weld checks and cleanup.This meticulous inspection and finishing phase is crucial. A poorly inspected weld can lead to weak spots, leaks, or even catastrophic failures, which is something you definitely don’t want.
Proper finishing, on the other hand, makes your device look professional and ensures it’s ready for duty.
Weld Defect Inspection
Proper inspection is vital to ensure the weld meets quality standards. A visually sound weld doesn’t necessarily mean it’s structurally sound. You need to check for cracks, porosity (little holes), and other defects.
- Visually examine the weld for any cracks, gaps, or unevenness. Look for signs of incomplete fusion or burn-through. A magnifying glass is your best friend here; you’ll spot the flaws that the naked eye misses.
- Use a non-destructive testing (NDT) method, like a dye penetrant test, to find hidden flaws. This is like a detective’s toolkit, uncovering the secrets hidden beneath the surface. If you’re not familiar with NDT methods, consult a professional. It’s better to be safe than sorry.
- Pay particular attention to the weld bead’s shape and contour. A well-executed weld will exhibit a smooth, continuous profile. Any significant deviations indicate potential issues.
Weld Smoothing and Finishing
Once you’ve confirmed the weld’s integrity, it’s time for some finesse. You want to make the weld not just strong, but also visually appealing.
- Use a file, grinder, or other appropriate tools to smooth out any imperfections in the weld bead. Don’t be too aggressive, or you’ll weaken the weld. Remember, precision is key.
- Use a wire brush to remove any slag or excess metal from the weld area. A clean weld is a strong weld, and a strong weld is a safe weld.
- A final polish can really make your weld shine, like a freshly polished gun. Use a polishing compound designed for metal to get that gleaming finish. It not only looks good, but it also helps prevent corrosion.
Surface Treatment
A properly treated surface is a vital component in the long-term success of your work.
- Thoroughly clean the weld area to remove any contaminants, like dirt, oil, or paint. A good cleaning will help prevent rust and corrosion.
- Apply a protective coating (paint, sealant, etc.) to the weld area. This is especially important in environments prone to rust or corrosion. This is a step that shouldn’t be skipped; it’s a vital part of the process.
Ensuring a Clean and Secure Finish
This is where you ensure your work is up to snuff.
- Double-check all welds for proper tightness. A loose weld is a dangerous weld. Make sure the pinning and welding are secure and won’t come loose under stress.
- Inspect the finished product thoroughly, from every angle. Look for any residual defects, loose parts, or unanticipated issues. A good final inspection can prevent problems down the road.
- Ensure that the muzzle device is properly aligned with the firearm’s barrel. A misaligned device is not only ugly, it’s also dangerous.
Troubleshooting and Common Mistakes
Alright, folks, let’s talk about potential pitfalls in your muzzle device pinning and welding adventure. We’ve covered the basics, now let’s get real. Avoiding those embarrassing “oops” moments is key to a smooth, safe, and successful project. We’ll delve into common errors, how to spot them, and what to do about them. So grab your safety glasses (and maybe a stiff drink – just kidding, stay safe!), and let’s get this show on the road!
Welding Issues
Welding problems can arise from various factors, ranging from incorrect settings to inadequate preparation. Understanding these issues is critical to achieving a strong and reliable weld. A poorly welded muzzle device is a recipe for disaster.
- Porosity: Tiny holes in the weld, often caused by insufficient shielding gas or contaminants in the metal. Think of it like air bubbles in your favorite drink; they weaken the weld and can lead to failure. Addressing this usually involves cleaning the area, adjusting the shielding gas, and ensuring the weld area is free from contaminants.
- Cracking: Stress cracks can develop due to improper heat input or cooling rates. Imagine a brittle cookie that shatters when you bend it; the same principle applies here. Solutions involve adjusting the welding parameters, checking for excessive stress concentrations, and maybe even re-evaluating your entire process.
- Undercut: When the weld doesn’t completely fuse with the base metal. Visualize a missing piece of the puzzle; the weld is incomplete. Proper techniques and equipment settings are crucial to prevent this issue. Recheck your electrode type and welding speed.
Pinning Problems
Pinning errors can stem from poor planning or improper execution. A misplaced pin is as bad as a misplaced comma in a love letter; it can completely change the outcome.
- Incorrect Pin Size or Type: Using the wrong pin size or type can lead to a weak or unstable joint. This is akin to using the wrong size bolt for a construction project; it just won’t hold. Always double-check your specifications and use the correct pin diameter, material, and length.
- Improper Pin Placement: Misaligned pins can compromise the structural integrity of the muzzle device. This is like placing a keystone in the wrong position in an arch; it throws everything off. Verify the pin’s location relative to the surrounding metal, and ensure it is correctly aligned.
- Pin Hole Alignment Issues: Misaligned holes can result in poor alignment and stress concentrations, potentially leading to breakage. It’s like trying to fit a square peg in a round hole; it’s just not going to work. Double-check your hole preparation to ensure accurate alignment and dimensions.
Troubleshooting Table
Problem | Cause | Solution |
---|---|---|
Porosity in weld | Insufficient shielding gas or contaminants in the metal | Clean the area, adjust shielding gas, ensure weld area is free from contaminants |
Cracking in weld | Improper heat input or cooling rates | Adjust welding parameters, check for excessive stress concentrations, re-evaluate entire process |
Undercut in weld | Incorrect electrode type or welding speed | Recheck electrode type and welding speed |
Weak or unstable joint | Incorrect pin size or type | Use the correct pin diameter, material, and length |
Misaligned pins | Poor planning or improper execution | Verify pin location relative to surrounding metal, ensure correct alignment |
Misaligned holes | Inaccurate hole preparation | Double-check hole preparation to ensure accurate alignment and dimensions |
Examples and Variations
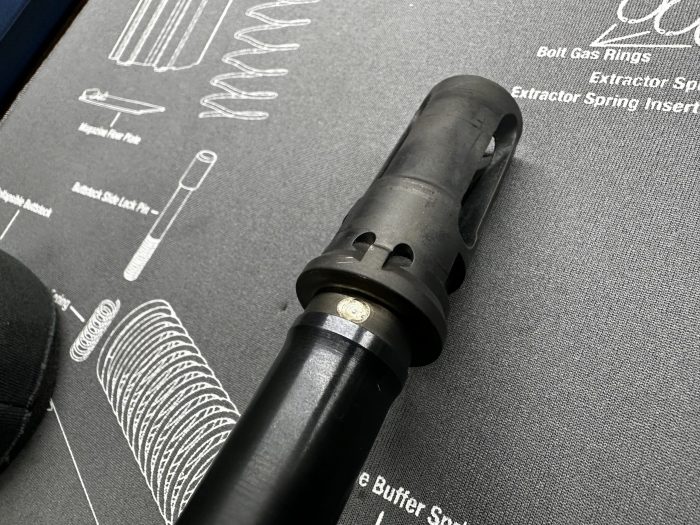
Alright, buckle up buttercups, because we’re diving into the wild world of muzzle device customization! Different firearms, different needs, different… well, different
- looks*. We’re talking about everything from the subtle to the… well, let’s just say
- noticeable*. From simple flash hiders to elaborate compensators, the options are practically endless. Let’s explore some examples and how pinning and welding techniques vary for each.
Different muzzle devices require different pinning and welding techniques. The key is understanding the device’s design and the firearm’s specific geometry. A simple flash hider, for instance, might only need a few strategically placed pins, whereas a more complex compensator might demand precise welds and a more intricate pinning pattern. Each application requires careful consideration and adherence to the specific manufacturer’s instructions.
Different Muzzle Device Types
Various muzzle devices serve different purposes, from reducing flash to managing recoil and controlling muzzle rise. Each type requires a unique approach to pinning and welding, accounting for the device’s shape, size, and material.
- Flash Hiders: These simple devices are designed to reduce the flash and muzzle report of a firearm. Pinning usually involves strategically placing pins that secure the device to the barrel. Welding is often limited to a small weld area around the pins to create a secure attachment. A common approach is to use a simple, quick weld to the pins.
This is often seen in semi-automatic weapons where the flash hider is used as a form of safety or aesthetic enhancement.
- Compensators: These more complex devices aim to reduce recoil and muzzle rise. They often involve multiple components and more intricate welding. Pinning is crucial for maintaining the compensator’s structural integrity, ensuring proper alignment with the barrel, and preventing it from vibrating or shifting during firing. Welding needs to be precisely executed to maintain structural stability and prevent the compensator from deforming during high-pressure situations.
- Suppressors (Silencers): These are complex and heavy devices that need very careful and specialized pinning and welding. Suppressors often have intricate internal chambers and baffles that demand precision in the welding process. Pinning often requires specialized tools to ensure the suppressor is accurately mounted to the barrel. Welding in these cases usually includes more steps and more rigorous quality control to guarantee structural stability under extreme pressure.
Variations in Pinning and Welding Processes
Different muzzle devices necessitate different pinning and welding approaches. The materials, the design, and the desired outcome all play a role in the process.
- Material Considerations: The material of the muzzle device and the firearm barrel significantly impacts the pinning and welding process. Different metals require different welding techniques to ensure a strong and lasting bond. For example, welding stainless steel to carbon steel demands specific precautions and welding parameters.
- Design Complexity: The complexity of the device dictates the level of precision and care required during pinning and welding. A simple flash hider might only need a few carefully placed pins and a short weld, whereas a compensator with intricate internal components requires more precise welding and pinning procedures to ensure functionality.
- Firearm Application: The intended application of the firearm will affect the choice of muzzle device and the subsequent pinning and welding. A hunting rifle might use a simple flash hider, while a tactical rifle might employ a more elaborate compensator to improve accuracy in rapid fire situations.
Firearm Applications
The choice of muzzle device and the subsequent pinning and welding procedures directly influence the firearm’s performance in various applications.
- Hunting: Flash hiders are common for hunting rifles to reduce flash and noise. Welding is often limited to securing the flash hider to the barrel, without significantly impacting the barrel’s structural integrity.
- Tactical Applications: Compensators are frequently employed in tactical rifles to reduce recoil and muzzle rise, improving accuracy and control in rapid-fire scenarios. The welding and pinning procedures are crucial for maintaining the compensator’s integrity and performance during high-pressure situations.
- Competition Shooting: Muzzle devices like compensators or specific flash hiders might be used to improve accuracy and control. Pinning and welding should be performed with extreme precision to prevent any interference with the firearm’s performance.
Final Wrap-Up
In conclusion, the successful pinning and welding of a muzzle device necessitates a thorough understanding of safety protocols, precise tool selection, and meticulous execution of each step. By adhering to the guidelines presented in this comprehensive guide, practitioners can achieve a safe and reliable modification while understanding the potential risks and troubleshooting common issues. Proper planning and execution are essential for a successful outcome.
Questions and Answers
What types of welding techniques are suitable for muzzle device pinning?
MIG, TIG, and stick welding are common techniques used for pinning muzzle devices, depending on the material and desired finish. Specific techniques might be more appropriate for different types of muzzle devices.
What are the most common mistakes made during the welding process?
Improper preheating, insufficient weld penetration, inadequate cooling time, and improper electrode selection are common mistakes. Using incorrect welding settings or inadequate shielding gas can also lead to problems.
How important is proper ventilation when welding a muzzle device?
Ventilation is crucial for removing harmful fumes and gases produced during welding. Adequate ventilation is essential for a safe and healthy working environment. Failure to ensure proper ventilation can lead to serious health problems.
What are the specific safety precautions when working with firearms and welding equipment?
Strict adherence to firearm safety rules is mandatory. Wear appropriate protective gear, including eye protection, hearing protection, and appropriate clothing. Ensure the area is clear of flammable materials and follow all safety regulations.