How to sharpen bush hog blades is crucial for maintaining optimal performance and longevity of your equipment. Different blade types, from sturdy steel to more specialized alloys, react differently to sharpening techniques. Knowing the right approach for your specific blade and terrain is key to preventing costly repairs and maximizing your machine’s effectiveness. This guide will walk you through the entire process, from essential tools and safety precautions to troubleshooting common issues and alternative sharpening methods.
Let’s dive in!
This comprehensive guide covers everything from selecting the right tools to mastering the precise techniques needed to keep your bush hog blades razor-sharp. We’ll explore various sharpening methods, highlighting the pros and cons of each. From basic maintenance to advanced techniques, you’ll gain a complete understanding of how to prolong the life and efficiency of your bush hog.
Introduction to Bush Hog Blade Sharpening
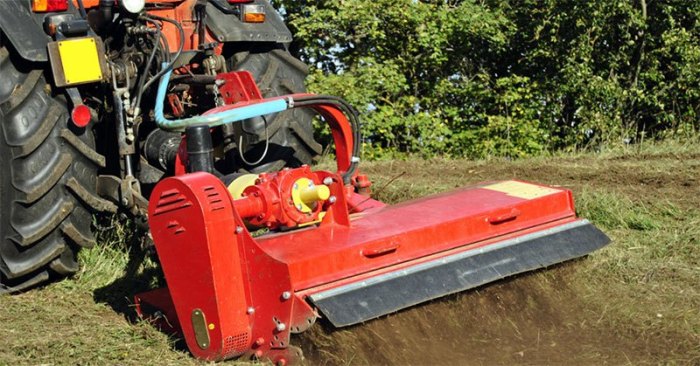
Sharp blades are the heart of a productive bush hog, ensuring efficient cutting and longevity for your machine. A well-maintained blade, honed to a razor’s edge, minimizes strain on the engine and maximizes the output of your efforts. Without regular sharpening, blades become dull, leading to reduced performance and increased wear and tear on your investment.A keen blade dances across the terrain, a precise instrument for the task at hand.
The efficiency of a bush hog depends critically on the sharpness of its blades. Different blade types cater to various terrain, from the dense undergrowth to the open field. Understanding the nuances of blade selection and sharpening is paramount to maximizing the performance and longevity of your equipment. Dull blades, however, lead to reduced cutting efficiency, increasing the strain on the machine’s components and potentially shortening its lifespan.
Bush Hog Blade Types and Suitability
Bush hog blades come in a variety of materials and designs, each tailored for specific terrains and cutting requirements. Steel alloys, tempered to varying degrees, determine the blade’s durability and resistance to wear. Blade shapes, from the aggressive to the more gradual curves, dictate the blade’s ability to tackle diverse vegetation types.
Consequences of Using Dull Blades
Dull blades significantly impact the overall performance of a bush hog. Reduced cutting efficiency translates to longer operating times, higher fuel consumption, and increased operator fatigue. Moreover, the strain placed on the machine’s components, including the motor and transmission, accelerates wear and tear, potentially leading to premature repairs or replacements. A dull blade, instead of cleanly severing the vegetation, will instead tear and shred it, requiring more passes to complete the job.
Sharpening Methods for Different Blade Types
Optimal sharpening methods vary according to the blade material and design. Proper sharpening techniques ensure the blade’s integrity and prolong its useful life. The following table Artikels recommended sharpening procedures for various blade types:
Blade Type | Material | Design | Recommended Sharpening Method |
---|---|---|---|
High-Carbon Steel | High-carbon steel alloys | Typically used for aggressive cutting | Grinding with a diamond file or abrasive wheel; followed by honing with a sharpening steel. |
Stainless Steel | Stainless steel alloys | Often preferred for durability in wet or corrosive environments | Grinding with a fine grit abrasive wheel or diamond file; followed by polishing with a fine grit stone or compound. |
Composite Blades | Composite materials | Combining high-strength materials | Grinding with a fine grit abrasive wheel or diamond file; special sharpening techniques might be required based on the specific composite composition. |
Essential Tools and Equipment
Forging a keen edge on your bush hog blades requires a precise and measured approach. Like a sculptor shaping clay, each tool and technique plays a crucial role in the final, formidable sharpness. Safety is paramount, for a blade, sharp and untamed, can inflict harm. Therefore, preparation and precaution are the cornerstones of successful sharpening.Understanding the tools and techniques necessary for a successful sharpening process empowers you to achieve optimal results while mitigating potential risks.
This section delves into the essential tools and equipment, emphasizing safety and the importance of proper maintenance for consistent outcomes.
Essential Sharpening Tools
A sharpened blade is a testament to careful preparation and selection of tools. The right equipment allows for precision and control during the sharpening process. A well-maintained collection of tools will yield consistent results, transforming dull blades into instruments of efficiency.
- A sturdy workbench or vise provides a stable platform to securely hold the blade during sharpening, preventing slippage and accidents.
- A set of sharpening stones, ranging in grit, is indispensable for progressively refining the blade’s edge. Different grit levels accommodate different stages of the sharpening process.
- A sturdy metal file is critical for initial shaping and removing significant amounts of metal to ensure proper angle alignment. The file should have a handle that allows for comfortable and controlled application.
- A quality honing steel is vital for maintaining the edge and ensuring the blade maintains its sharpness. Honing steel is an essential tool for maintaining a sharp edge.
- Safety glasses, gloves, and ear protection are crucial to prevent injury during the sharpening process. These safeguards mitigate risks associated with the use of sharp tools.
Safety Precautions
Safety is paramount when working with sharp blades and potentially hazardous tools. Proper precautions mitigate the risk of accidents and ensure a safe working environment.
- Always wear appropriate safety gear, including safety glasses, gloves, and hearing protection. This safeguards against flying debris, sharp edges, and loud noises.
- Secure the blade firmly in a vise or on a workbench to prevent slippage or accidental movement during sharpening. This crucial step prevents injury.
- Use caution when handling sharpening stones and other tools. Their sharp edges require careful attention and handling.
- Maintain a clear and uncluttered workspace to prevent tripping hazards. This prevents accidents and promotes a safe work environment.
- Never attempt to sharpen a blade that is not securely held in place. This crucial step minimizes the risk of injury.
Sharpening Stone Comparison
The selection of sharpening stones directly influences the quality of the blade’s edge. Different materials and grit levels offer varying degrees of suitability. This table provides a comparison of different types of sharpening stones and their appropriateness for various blade materials.
Stone Type | Material | Grit | Suitability for Blade Materials |
---|---|---|---|
Diamond | Diamond | Very Fine | Suitable for all types of blades, including those made from high-carbon steel. |
Ceramic | Ceramic | Fine to Medium | Excellent for maintaining a sharp edge on blades made of various materials. |
Natural Stone (Arkansas) | Natural Stone | Medium to Coarse | Suitable for removing significant amounts of metal and initial shaping. Effective for blades made from softer metals. |
Blade Sharpening Techniques
A keen edge, a whisper of steel against the earth, is the essence of a productive bush hog. Sharpening techniques are not merely about achieving a sharp edge; they are about preserving the blade’s integrity and maximizing its lifespan. Mastering these techniques will transform your mowing experience from a struggle to a symphony of precision.Sharpening bush hog blades involves a delicate dance between precision and power.
Different blade types respond to varying sharpening methods, and the choice of technique dictates the blade’s longevity and effectiveness. Maintaining the correct angle is paramount, ensuring a consistently sharp edge that cuts cleanly and efficiently.
Grinding Techniques
Grinding, a powerful method, excels at removing significant material. Its efficiency, though, demands careful attention to avoid overheating and distortion. A grinding wheel, with its controlled abrasiveness, allows for rapid material removal, essential for re-profiling worn blades. Precise control of the blade’s position and angle is critical to prevent damage and maintain the desired geometry.
- A step-by-step procedure for sharpening a bush hog blade using a grinder typically involves securing the blade firmly in a vise. Carefully approach the grinding wheel, maintaining a consistent angle, which is usually 20-25 degrees, while rotating the blade slowly. Regularly inspect the blade’s profile to ensure an even sharpening. This process removes material from the blade’s cutting edge, effectively renewing its sharpness.
- To ensure consistency, mark the blade with a reference point and maintain this reference during the sharpening process. Visualize the blade’s geometry. Avoid excessive pressure, as this can lead to warping or distortion of the blade. This procedure also demands an understanding of the blade’s specific curvature to avoid damaging the blade.
- After each pass, inspect the blade for any irregularities or unevenness. Adjust the blade’s position and angle as needed. This meticulous attention ensures that the blade achieves the optimal sharpness and durability.
Honing Techniques
Honing, a more precise method, refines an already sharpened blade. It’s ideal for fine-tuning and restoring a blade’s edge. Honing with a sharpening stone is a precise process, requiring meticulous attention to detail. The choice of stone and the pressure applied are crucial to the outcome. This method is beneficial for maintaining the blade’s existing shape and sharpening its cutting edge, but it’s not suitable for substantial reshaping.
- A sharpening stone, with its graded abrasiveness, allows for gradual, controlled sharpening. Maintaining a consistent angle is essential. Applying a light pressure, consistent with the stone’s grain, while moving the blade along the stone in a smooth, controlled manner is key to achieving a keen edge. The direction of the stroke should be consistent with the blade’s profile.
- This method involves repeated strokes, each pass refining the blade’s edge further. Regular inspection of the blade’s edge during the honing process is crucial to ensure that the blade’s profile is maintained, and an even sharpening is achieved. This attention to detail ensures that the blade retains its strength and maintains its precise cutting geometry.
- Consistent pressure and angle are essential to avoid creating an uneven edge. Adjust the blade’s angle as necessary. This method ensures that the blade’s cutting edge is uniformly honed, ensuring that the blade can efficiently engage the vegetation being cut. The consistent sharpening also ensures a consistent cutting performance, and the ability to effectively cut through various types of vegetation.
Angle Maintenance
Maintaining the correct sharpening angle is critical. A consistent angle ensures a uniform cutting edge, extending the blade’s lifespan. The angle is often specific to the blade’s design and type of material.
- An incorrect angle can result in a dull or uneven edge, reducing the blade’s efficiency and lifespan. This angle is crucial in ensuring the blade’s longevity and effectiveness. The angle ensures the blade cuts through vegetation with minimal resistance, and ensures consistent cutting performance.
- A precise angle, often between 20-25 degrees, is critical. The exact angle will depend on the blade’s design. Different types of blades require specific sharpening angles. Consistent angle maintenance is critical for the effectiveness and longevity of the blade.
Safety Considerations During Sharpening
The dance with steel, a delicate ballet of precision and power, demands respect for the inherent dangers. Sharpening bush hog blades, though rewarding, requires vigilance and a keen awareness of potential hazards. A misstep can quickly transform a controlled process into a perilous one.Sharpening blades involves working with sharp, heavy, and potentially dangerous objects. Improper handling or lack of safety precautions can lead to severe injuries.
Understanding and diligently practicing safe sharpening techniques is paramount. A focus on meticulous preparation, careful execution, and unwavering vigilance is essential to avoid mishap.
Potential Hazards
Sharpening bush hog blades presents several potential hazards. Flying debris, the inherent sharpness of the blades, and the force required for sharpening are all significant risks. Unforeseen circumstances can easily escalate into serious incidents. Proper safety measures are vital for a successful and safe sharpening experience.
Safety Precautions
To mitigate these risks, a comprehensive safety plan is necessary. A well-structured approach involves careful planning, the selection of appropriate equipment, and unwavering adherence to safety protocols. It’s crucial to recognize the dangers and implement proactive safety measures.
- Protective Gear: Ensuring adequate personal protective equipment (PPE) is essential. Safety glasses or goggles are crucial to shield the eyes from flying metal fragments. Heavy-duty work gloves are vital to protect hands from cuts and abrasions. Robust steel-toed safety boots should be worn to prevent foot injuries from falling objects or sharp metal shards. These precautions are fundamental for safeguarding your well-being.
- Secure Workspace: A stable and well-organized workspace is critical. Position the sharpening tools on a sturdy, level surface. Clear the area of any obstructions or distractions. A designated sharpening zone, free of clutter and hazardous materials, is paramount. This will prevent slips and falls, keeping the sharpening process safe and efficient.
- Proper Blade Handling: Handle sharp blades with extreme care. Use appropriate lifting techniques to avoid dropping or throwing them. Secure the blades firmly in a vice or other holding device. Avoid touching the cutting edges with bare hands, as they can cause severe cuts. Employ specialized blade holders for extra security and protection.
- Ventilation: Adequate ventilation is crucial to mitigate the risk of inhaling metal dust or particles generated during sharpening. Work in a well-ventilated area, or use a respirator if necessary. Proper airflow helps maintain a healthy and safe environment.
Ventilation and Workspace Setup
A well-ventilated and organized workspace is essential for a safe sharpening session. Airborne particles can cause respiratory problems, and a cluttered workspace increases the risk of accidents. A thoughtful layout and sufficient ventilation are vital for minimizing potential hazards.
- Ventilation Systems: Employ exhaust fans or other ventilation systems to remove metal dust and particles from the air. This helps to create a cleaner and healthier environment. Consider the use of local exhaust ventilation (LEV) systems, which are designed to capture and remove dust at its source. These systems are effective in preventing the inhalation of harmful particles.
- Designated Sharpening Area: Designate a specific area for sharpening, keeping it free from clutter and other hazards. A clear and organized workspace reduces the risk of slips, trips, and falls. This dedicated space should be well-lit and easily accessible.
Maintaining Blade Sharpness
Honing the blade’s edge, a testament to meticulous care, is paramount for sustained performance. A sharp blade dances across the landscape, a graceful instrument of efficiency, effortlessly slicing through vegetation. Conversely, a dull blade, a weary warrior, struggles against its task, demanding excessive effort and ultimately diminishing the overall effectiveness of your bush hog.The keen edge, a testament to diligent maintenance, is the key to a productive and satisfying experience.
This chapter unveils the secrets to preserving the razor-sharp acumen of your blades, ensuring years of dependable service from your trusty bush hog.
Blade Storage and Handling
Proper handling and storage are crucial for preserving the sharpness of your blades. Carefully handle sharpened blades to avoid nicks and damage. Use protective gloves and a soft cloth to prevent scratches or abrasions. Employ a dedicated blade storage area to safeguard against environmental factors like moisture and dust.
Frequency of Sharpening
The frequency of blade sharpening hinges on the intensity of use and the type of vegetation encountered. Regularly scheduled blade checks, a proactive approach to maintenance, are essential to detect early signs of dullness. Intense, heavy-duty use in thick, dense vegetation necessitates more frequent sharpening. Conversely, lighter use in less demanding environments may allow for longer intervals between sharpenings.
Importance of Regular Blade Checks
Regular blade checks are vital for detecting early signs of dullness. A visual inspection can reveal subtle signs like a loss of sharpness or uneven wear. This proactive approach allows for timely sharpening, preventing further deterioration and extending the lifespan of your blades. A dull blade demands greater effort, leading to increased wear on your machine.
Blade Storage Best Practices
Store sharpened blades in a cool, dry place, away from moisture and direct sunlight. Use protective covers or containers to shield them from dust and debris. Proper storage protects the blades’ sharpness, extending their operational life and maintaining their performance.
Routine Blade Maintenance Checklist
- Visual Inspection: Carefully examine the blade for any signs of damage, nicks, or uneven wear. Observe the edge for any loss of sharpness or discoloration. This proactive step is a critical first step in maintaining blade sharpness.
- Cleaning: Thoroughly clean the blades using a brush and mild detergent. Remove any debris or dirt that may be clinging to the blade’s surface. This meticulous cleaning step is a vital aspect of maintaining blade sharpness.
- Storage: Store the blades in a designated area, shielded from the elements and protected from potential damage. This careful storage is crucial for preventing damage.
- Sharpening Schedule: Establish a schedule for sharpening based on usage and the type of vegetation. This proactive approach helps extend the life of the blades and maintain their peak performance.
- Record Keeping: Maintain a record of sharpening dates and the conditions under which the blades were used. This detailed record will be instrumental in adjusting your maintenance schedule and improving efficiency.
Troubleshooting Common Issues: How To Sharpen Bush Hog Blades
A keen eye and steady hand are paramount in the blade-sharpening ritual. Yet, even the most practiced artisan may encounter snags. Understanding the potential pitfalls allows for swift resolution, ensuring your bush hog blades remain honed for optimal performance. This section will dissect common issues, offering solutions and insights into the underlying causes of blade dullness.
Identifying Blade Dullness Beyond Sharpening
Dull blades, a frustrating foe to the meticulous farmer, aren’t always the result of insufficient sharpening. External factors and operational misuse contribute to the issue. Understanding these culprits empowers you to tackle blade-related problems proactively.
- Incorrect Blade Type for the Task: Employing an unsuitable blade type for the terrain can lead to rapid dulling. A blade designed for light brush may be overwhelmed by dense, thick vegetation, resulting in premature wear. Matching the blade to the job is paramount for longevity and performance.
- Improper Blade Mounting: A poorly affixed blade, loose or improperly tightened, may cause uneven wear and tear, resulting in a dulling effect. Ensuring a precise and secure fit is crucial for consistent cutting performance.
- Excessive Blade Angle: An incorrectly sharpened blade, with an angle exceeding the recommended value, may result in a compromised cutting edge. Maintaining the correct sharpening angle, as detailed in previous sections, is essential for optimal blade efficiency.
- Operating Conditions: Harsh conditions like stones, rocks, or dense roots can quickly erode the blade’s sharpness. Operating the bush hog in areas with excessive debris necessitates more frequent sharpening, often a preventative measure rather than a reactive response.
Common Blade Sharpening Problems and Solutions
Problem | Possible Cause | Solution |
---|---|---|
Blade not cutting effectively | Insufficient sharpening angle, incorrect blade type, or excessive blade wear. | Recheck sharpening angle, ensure correct blade type for the task, and consider replacing the blade if significantly worn. |
Uneven blade sharpness | Improper sharpening technique, inconsistent grinding pressure, or loose blade mounting. | Practice consistent sharpening technique, apply even pressure throughout the process, and ensure the blade is securely mounted. |
Blade chipping or cracking | Excessive force during sharpening, using blunt tools, or improper blade material. | Use appropriate grinding tools, apply moderate pressure, and select blades made from durable materials to prevent chipping and cracking. |
Blade losing sharpness rapidly | Operating in conditions with excessive debris or using a blade not suited to the task. | Avoid operating in areas with high levels of debris. Ensure the blade type matches the vegetation. |
Alternative Sharpening Methods

Beyond the time-honored grindstone, a world of blade-honing possibilities unfurls. Alternative methods offer unique approaches to restoring the keen edge of your bush hog blades, each with its own strengths and weaknesses. From specialized machinery to ingenious home-brewed solutions, the journey to a razor-sharp blade is as diverse as the landscape it traverses.These alternative methods provide varying degrees of precision and speed, influencing the overall efficiency of the sharpening process.
Understanding these differences allows for informed decisions tailored to specific needs and resources. Some techniques are best suited for maintaining existing sharpness, while others excel in achieving a completely new edge.
Specialized Sharpening Equipment
Alternative sharpening methods often involve specialized equipment designed for optimal blade geometry. These machines, often powered, allow for controlled, repeatable sharpening strokes. They are frequently equipped with adjustable angles and calibrated pressure settings, ensuring consistent sharpness across multiple blades. This precision often leads to more durable edges than hand-held methods, making them ideal for intensive use.
Homemade Sharpening Solutions
Resourcefulness often leads to innovative solutions. A keen eye for repurposed materials can unveil surprisingly effective homemade sharpening methods. For instance, a meticulously crafted sharpening stone, fashioned from a hard, dense material like granite or even a well-worn concrete slab, can serve as a robust and affordable alternative. Paired with a steady hand, these makeshift solutions can deliver impressive results.
Comparison of Alternative Methods
A table comparing the effectiveness and efficiency of different methods, including hand-held and specialized equipment, highlights the trade-offs involved.
Method | Effectiveness | Efficiency | Cost | Skill Required |
---|---|---|---|---|
Hand-held sharpening stones | Good, but can be inconsistent | Slow | Low | Moderate |
Specialized sharpening machines | Excellent, highly consistent | Fast | High | Low (with proper training) |
Homemade sharpening solutions | Variable, dependent on quality of materials | Variable, dependent on materials and technique | Very low | Moderate to high, dependent on complexity |
Using a Rotary Tool for Blade Sharpening, How to sharpen bush hog blades
A rotary tool, equipped with a suitable sharpening attachment, provides a streamlined approach to sharpening. First, ensure the blade is securely mounted on a stable surface. Next, select a sharpening attachment designed for the blade’s shape. Maintain a consistent, even pressure while rotating the tool along the blade’s edge, avoiding excessive force or rapid movement. The key to success lies in meticulous attention to maintaining the correct angle.
Use a guide or jig to ensure consistent angles during the process. Finally, inspect the blade for sharpness and adjust the angle if necessary.
Illustrative Examples
The art of sharpening bush hog blades transcends mere technique; it’s a dance between precision and purpose. Each blade, a sculpted instrument of agricultural artistry, demands a tailored approach to achieve peak performance. Understanding the unique characteristics of various blade types and the optimal sharpening angles for each is key to maintaining efficiency and longevity.This section delves into practical examples, demonstrating the diverse needs of bush hog blades and the crucial role of consistent sharpening.
We explore the subtle differences in blade geometries and their impact on the final sharpness and durability.
Blade Type Variations and Sharpening Methods
Different bush hog blades, each designed for specific terrains and tasks, require tailored sharpening methods. The geometry and material composition of the blade dictate the optimal approach. A keen eye for detail is essential when evaluating the blade’s condition.
- High-carbon steel blades: These blades, renowned for their resilience, often require a more aggressive sharpening approach. A series of carefully executed passes with a grinder or sharpener, ensuring even wear, will restore their cutting edge. The crucial element is maintaining a consistent angle throughout the sharpening process.
- Composite blades: These blades, often featuring a hardened steel core within a protective composite shell, need a more delicate touch. A fine-grit sharpening stone, used in gentle, controlled strokes, is the preferred method. Excessive pressure can compromise the composite layer’s integrity, leading to premature failure.
- Serrated blades: These blades excel in tackling tough vegetation and have a unique serrated edge. Sharpening these blades requires careful attention to the serration pattern. A specialized sharpening tool designed for serrations, or meticulous manual sharpening, is necessary to maintain the blade’s intricate structure. Each serration needs individual attention, and the consistency of the sharpening angle is paramount.
Determining Optimal Sharpening Angles
Precise angle control is fundamental to achieving the desired cutting edge. A blade sharpened at an improper angle will either lack sharpness or be prone to premature breakage. The optimal angle is dependent on the specific blade type and the desired cutting performance.
- High-carbon steel blades: A typical sharpening angle for high-carbon steel blades ranges from 25 to 30 degrees. A bevel angle is created to ensure the cutting edge is sharp and resistant to damage.
- Composite blades: Composite blades benefit from a slightly shallower angle, typically between 15 and 20 degrees. This gentler angle helps to prevent compromising the composite material.
- Serrated blades: Serrated blades require a more nuanced approach to determining the optimal angle. Each serration’s angle needs careful consideration to maintain its intended cutting action. Consistency in the sharpening angle for each serration is crucial for uniform performance.
Consistency in Sharpening for Performance
Maintaining consistent sharpening practices is vital for sustained performance and blade longevity. This ensures that each blade delivers the expected cutting power. Varied sharpening angles will lead to uneven blade performance.
- Repeated testing and analysis: Regular testing and evaluation of the blade’s sharpness are crucial to maintaining consistency. This approach allows for adjustments in the sharpening process based on performance data. This ensures that each sharpening session yields consistent results.
- Standardized procedures: Developing and following standardized procedures for blade sharpening ensures that every blade receives the same level of care. This approach eliminates inconsistencies and guarantees optimal performance.
Illustrative Table of Blade Types and Sharpening Results
Blade Type | Image Description | Sharpening Method | Result |
---|---|---|---|
High-carbon steel | A robust blade with a sharp, well-defined cutting edge. | Grinding with a consistent 25-30 degree angle. | Exceptional sharpness, long-lasting performance. |
Composite | A blade with a protective composite exterior and a hardened steel core. | Gentle sharpening with a fine-grit stone at a 15-20 degree angle. | Sharp, durable edge, minimizing the risk of composite damage. |
Serrated | A blade with multiple serrations designed for aggressive cutting. | Sharpening each serration with a consistent angle, using a specialized tool. | Improved cutting action on tough vegetation, consistent results for each serration. |
Concluding Remarks
In conclusion, maintaining sharp bush hog blades is essential for both productivity and machine longevity. By understanding the different blade types, sharpening techniques, and safety considerations, you can significantly extend the lifespan of your equipment and ensure efficient operation. Remember to prioritize safety, use the right tools, and consistently check your blades for wear. With a little know-how and care, you’ll be well-equipped to keep your bush hog performing at its best, season after season.
FAQ
What are the common causes of dull blades besides insufficient sharpening?
Dull blades can also result from improper mowing techniques, like hitting rocks or other hard obstacles. Overloading the machine with excessively thick vegetation or using the wrong blade type for the terrain can also lead to premature blade dulling.
How often should I sharpen my bush hog blades?
The frequency of sharpening depends on several factors, including the type of vegetation, mowing frequency, and the blade material. Regular checks for signs of dullness, like reduced cutting efficiency, are crucial. You should sharpen your blades when you notice a significant decrease in cutting performance.
What safety gear should I wear when sharpening blades?
Always wear safety glasses or a face shield to protect your eyes from flying debris. Use heavy-duty work gloves to prevent cuts and abrasions. Additionally, consider using ear protection if working with noisy equipment like a grinder.
What are some homemade sharpening solutions?
While less common, some resourceful individuals utilize homemade sharpening solutions using materials like carborundum stones or grinding wheels. These methods can be effective, but require caution and precise control to prevent damage to the blades. Consult a reputable source for advice if considering these techniques.