How to use a swamp cooler motor for bicycle? This exploration delves into the intriguing possibility of repurposing a swamp cooler motor for bicycle propulsion. We’ll examine the potential benefits and drawbacks, the necessary modifications, and the safety considerations involved in this unconventional approach to bicycle design. Understanding the nuances of adapting this unique motor type will allow for a deeper appreciation of its potential and the challenges that must be addressed.
This comprehensive guide will walk you through the process of selecting a suitable motor, adapting it for bicycle use, designing a safe and effective power transmission system, and implementing the modifications in a way that optimizes efficiency and safety. We’ll cover critical design considerations, safety precautions, and troubleshooting steps to ensure a successful project. Beyond the bicycle, we’ll also explore the broader potential of this motor for alternative uses.
Introduction to Swamp Cooler Motors and Bicycle Applications: How To Use A Swamp Cooler Motor For Bicycle
Swamp cooler motors, often overlooked in the realm of bicycle mechanics, present an intriguing avenue for exploring alternative power sources. These motors, typically found in evaporative cooling systems, possess unique characteristics that might be adaptable for bicycle propulsion. This exploration delves into the potential of leveraging these motors for bicycle applications, considering their advantages, disadvantages, and inherent challenges.Swamp cooler motors are driven by a compressor, often using a small AC motor to facilitate the evaporative cooling process.
Understanding their basic function is crucial for assessing their suitability for bicycle use. They typically generate a relatively low amount of power compared to more conventional bicycle motors, but their inherent simplicity might make them an interesting alternative for specific applications.
Basic Function of a Swamp Cooler Motor
Swamp cooler motors, unlike typical bicycle motors, operate on a different principle. They utilize a compressor to force air through a water-soaked filter, creating a cooling effect. The motor’s function is directly linked to the cooling process. This differs significantly from the direct rotational power output of a traditional bicycle motor.
Bicycle Mechanics Relevant to Motor Integration
Integrating any motor into a bicycle requires careful consideration of the bicycle’s existing components and mechanics. Key considerations include the motor’s power output, the bicycle’s frame design, and the available space for mounting and wiring. The bicycle’s gearing system must be compatible with the motor’s output to ensure efficient power transfer. A detailed understanding of torque and speed characteristics is essential.
Potential Advantages and Disadvantages
- Advantages: Swamp cooler motors may offer a unique approach to alternative bicycle propulsion due to their relative simplicity and potential cost-effectiveness, especially if components can be repurposed from existing swamp coolers. The quiet operation of some swamp cooler motors could be advantageous in certain situations.
- Disadvantages: The limited power output of swamp cooler motors, often geared towards a specific cooling capacity, might prove insufficient for typical bicycle speeds and gradients. The high maintenance requirements of the water-cooling mechanism could pose a challenge for reliable operation over time. The unique design of a swamp cooler motor may also make integration into a standard bicycle frame less straightforward than using a motor designed for cycling.
Potential Challenges in Adaptation
Adapting a swamp cooler motor for bicycle use presents several challenges. The motor’s design may not directly translate to bicycle propulsion, requiring significant modifications. The motor’s power output might not be sufficient for consistent acceleration and hill climbing. Integrating the motor into the bicycle’s existing structure could also present significant mechanical challenges. Ensuring smooth operation and proper power transmission is paramount to successful integration.
Examples of Existing Bicycle Designs
Currently, there are no widespread examples of bicycles utilizing swamp cooler motors for propulsion. While the concept has not been fully explored in the realm of bicycle design, its potential application remains a topic for future exploration. The unique characteristics of swamp cooler motors could lead to interesting, potentially unconventional bicycle designs.
Comparison of Swamp Cooler Motors with Other Motor Types
Feature | Swamp Cooler Motor | Electric Motor (Brushless DC) | Internal Combustion Engine |
---|---|---|---|
Power Output | Low | Medium to High | Medium to High |
Maintenance | Potentially High (water cooling) | Low | Medium |
Cost | Potentially Low (repurposing) | Medium | Medium to High |
Efficiency | Variable (depending on design) | High | Variable |
Noise Level | Potentially Low | Low | High |
Motor Selection and Modification
Choosing the right swamp cooler motor and adapting it for bicycle use requires careful consideration of several key factors. This process involves understanding the motor’s specifications, making necessary modifications, and ensuring compatibility with the bicycle’s mechanical system. A well-selected and properly modified motor can significantly enhance the bicycle’s performance and functionality.
Key Specifications for Motor Selection
Swamp cooler motors vary in their power output, voltage, and RPM (rotations per minute). Identifying these specifications is crucial for determining the motor’s suitability for bicycle propulsion. Factors like the desired speed, terrain, and rider weight will influence the appropriate motor choice. For instance, a motor with higher RPMs might be ideal for hilly terrain, while a motor with a higher power output could be suitable for heavier riders.
Careful consideration of these factors will ensure a balanced and efficient power delivery system.
Necessary Modifications for Bicycle Adaptation
Several modifications are often needed to adapt a swamp cooler motor for bicycle use. These modifications ensure proper integration with the bicycle’s existing components and the motor’s effective functioning. This includes adjustments to the motor’s mounting, wiring, and gear system.
Potential Components Requiring Modification
- Motor Housing: The motor housing might need alterations for secure and stable mounting on the bicycle frame.
- Wiring: The motor’s wiring system may require adjustments to connect it to the bicycle’s battery and control system. Appropriate connectors and wiring harnesses should be used to ensure electrical safety and efficiency.
- Gear System: The motor’s output shaft might need a gearbox or other gearing mechanism to match the bicycle’s chain or belt drive system.
- Mounting Brackets: Custom brackets may be required to securely attach the motor to the bicycle frame, ensuring structural integrity and preventing vibrations.
- Control System: A control system is required to manage the motor’s operation, including speed adjustments and stopping mechanisms.
Motor Power Output and Voltage Specifications
The power output and voltage of the motor are essential considerations. The power output should be sufficient to propel the bicycle at the desired speed and handle the terrain. For instance, a motor with a higher power output will be more suitable for steeper hills or heavier riders. The voltage should match the bicycle’s battery system to ensure proper operation and prevent damage.
Matching the motor’s voltage to the battery system is critical for a safe and effective setup.
Mounting the Motor to the Bicycle Frame
Different mounting methods can be used to attach the motor to the bicycle frame. Some common methods include direct mounting, using a bracket system, or integrating the motor into the frame’s design. The chosen mounting method should consider the motor’s size, weight, and the bicycle’s frame structure. Careful planning and precise implementation of the mounting system are essential for a reliable and durable setup.
Example Table of Motor Adaptation Steps
Step | Description |
---|---|
1 | Disassemble the swamp cooler motor to access internal components. |
2 | Design and fabricate mounting brackets to attach the motor to the bicycle frame. |
3 | Connect the motor’s wiring to the bicycle’s battery and control system. |
4 | Integrate the motor’s output shaft with a suitable gear system to match the bicycle’s drive system. |
5 | Test the motor’s functionality and make necessary adjustments to ensure optimal performance. |
Power Transmission and Control Systems
Harnessing the power of a swamp cooler motor for a bicycle requires careful consideration of how the motor’s rotational energy is transferred and controlled. This section details the various methods for transmitting power from the motor to the bicycle’s drivetrain, as well as options for regulating the motor’s speed and direction. Understanding these systems is crucial for creating a reliable and efficient power system.
Power Transmission Methods
Several methods exist for transferring the rotational energy from the motor to the bicycle’s wheels. The optimal choice depends on the motor’s characteristics, the desired bicycle configuration, and the overall design goals.
- Chain Drive: A chain drive is a common and robust method for transmitting power. A chain connects the motor’s output shaft to a sprocket, which is then linked to the bicycle’s rear wheel sprocket. This method is reliable, efficient, and readily available, making it a popular choice. However, chain maintenance, lubrication, and wear can be factors to consider.
A well-maintained chain drive can provide consistent power transfer.
- Belt Drive: Belt drives offer a smoother, quieter operation compared to chain drives. A toothed belt connects the motor to a pulley system, which in turn drives the bicycle’s rear wheel. Belt drives are generally low-maintenance, but the selection of a suitable belt is critical for appropriate power transfer. The durability of the belt can vary based on the material and quality.
- Direct Drive: In a direct drive system, the motor’s output shaft is directly coupled to the bicycle’s rear wheel hub. This method eliminates the need for intermediate components like chains or belts, potentially simplifying the design and reducing friction. However, direct drive systems can be more complex to implement and may not be suitable for all motor types.
Speed and Direction Control, How to use a swamp cooler motor for bicycle
Controlling the speed and direction of the motor is essential for a functional bicycle. Several methods can achieve this.
- Variable Speed Control: A variable speed controller allows the user to adjust the motor’s speed. These controllers typically utilize electronic components to regulate the power delivered to the motor, allowing for smooth acceleration and deceleration. This type of control is particularly valuable for achieving different speeds for varying terrains or user preferences. Different controllers offer different levels of precision and responsiveness.
- Reversing Mechanism: To change the motor’s direction of rotation, a reversing mechanism is necessary. This mechanism typically involves a motor controller with specific settings for forward and reverse operation. The controller manages the current flow to the motor, allowing for effortless switching between directions.
Examples of Suitable Power Transmission Systems
Examples of suitable power transmission systems depend on the specific motor and bicycle configuration.
- Bicycle with a chain drive: A swamp cooler motor, with its output shaft connected to a chain sprocket, can be used to drive the rear wheel through a standard bicycle chain and cassette. The system would likely require a variable speed controller to manage acceleration and deceleration.
- Electric Bicycle with a belt drive: A swamp cooler motor coupled with a belt drive can create a quiet and efficient power system for an electric bicycle. The belt’s smooth operation and minimal maintenance make it suitable for this type of application. The motor controller is essential for controlling speed and direction.
Limitations of Power Transmission Methods
Each power transmission method has potential limitations.
- Chain Drive: Chain drives can experience wear and require lubrication, potentially affecting performance over time. Careful selection of the chain and sprockets is essential for maintaining efficiency.
- Belt Drive: Belt drives might experience slippage under heavy loads or if the belt is not properly tensioned. The lifespan of the belt can vary depending on its quality and use conditions.
- Direct Drive: Direct drive systems might not be suitable for all swamp cooler motors, as the motor’s torque and rotational speed may not perfectly match the bicycle’s needs. The motor’s size and weight are also critical factors.
Power Transmission Systems Comparison
Power Transmission System | Pros | Cons |
---|---|---|
Chain Drive | Robust, efficient, readily available, relatively inexpensive | Requires maintenance, lubrication, and wear can occur |
Belt Drive | Smooth operation, low maintenance, quieter than chain drives | Potential for slippage under heavy load, more expensive than chain drive in some cases |
Direct Drive | Simplified design, potentially reduced friction | May not be suitable for all motor types, complexity in implementation |
Connecting the Motor to the Bicycle’s Drivetrain
A step-by-step procedure for connecting the motor to the bicycle’s drivetrain is detailed below.
- Assess the bicycle’s drivetrain: Carefully inspect the bicycle’s current drivetrain components, paying attention to the chain, cassette, and rear wheel hub.
- Select compatible components: Choose sprockets, chains, or belts that match the motor’s output specifications and the bicycle’s existing drivetrain. Consider the bicycle’s wheel size, gearing, and desired torque.
- Mount the motor: Securely mount the motor to the bicycle frame using appropriate brackets and hardware. Ensure proper alignment and stability.
- Connect the power transmission system: Connect the chosen power transmission system (chain, belt, or direct drive) to the motor’s output shaft and the bicycle’s rear wheel.
- Install the controller: Install the motor controller according to the manufacturer’s instructions. Connect the controller to the motor and the battery.
- Test the system: Carefully test the system for smooth operation, ensuring that the motor functions as expected. Adjust the controller as needed for optimal performance.
Design Considerations and Safety
Converting a swamp cooler motor for bicycle use requires careful attention to safety and durability. A poorly designed or implemented conversion can lead to accidents, damage to the bicycle, and even injury. Thorough planning and adherence to safety guidelines are paramount.Designing for safety and durability is critical to prevent potential hazards. This includes ensuring the motor is securely mounted, the power transmission system is robust, and the overall design is stable.
A well-engineered conversion allows for safe and enjoyable use.
Importance of Safety Precautions
Proper safety precautions are essential when operating a modified bicycle. These precautions help prevent accidents and maintain control. Using a modified bicycle with a swamp cooler motor requires adjustments to handling and awareness of potential hazards. A thorough understanding of these precautions is vital for safe operation.
Potential Hazards Associated with Swamp Cooler Motors on Bicycles
Several potential hazards are associated with using a swamp cooler motor on a bicycle. These hazards include: the increased weight of the motor, the added complexity of the power transmission system, and the potential for electrical issues. Careful consideration of these factors during the design and modification process is crucial. Improper installation can lead to a sudden loss of control.
Impact of Motor Weight on Bicycle Handling
The added weight of the motor can significantly impact the bicycle’s handling characteristics. A heavier motor will affect the center of gravity, potentially making the bicycle less stable and responsive. This effect can be mitigated by strategic motor placement and careful selection of components. Testing and adjustments to the bike’s geometry will be necessary for effective handling.
Optimizing Motor Efficiency for Bicycle Use
Optimizing the motor’s efficiency for bicycle use is essential for maximizing performance and minimizing power consumption. Factors like gear ratios, motor speed, and power transmission efficiency all influence the system’s overall effectiveness. Using appropriate gearing and careful selection of motor RPM can help optimize the efficiency of the entire system. Consideration of factors such as load, speed, and terrain are key to achieving optimal performance.
Safety Guidelines and Precautions for Modified Bicycles
- Secure Mounting: The motor must be securely fastened to the bicycle frame using appropriate mounting hardware and techniques to prevent slippage and vibrations. Using high-quality, appropriately sized fasteners and securing the motor with bracing, where needed, will prevent vibrations and damage. A correctly designed mounting system ensures the motor remains firmly in place during operation.
- Adequate Power Transmission: The power transmission system must be robust enough to handle the motor’s output without failure. Ensure that the chain, sprockets, and any other components in the transmission system are appropriately sized and capable of handling the power output. The choice of chain, gears, and sprockets should account for the motor’s power and the rider’s weight.
- Electrical Safety: Ensure all electrical connections are properly insulated and protected. All wiring should be routed to avoid chafing or contact with moving parts. Using appropriate electrical connectors and protecting the wires with tubing can ensure the safety of the system.
- Proper Load Assessment: The bicycle’s load capacity should be evaluated with the added weight of the motor and any accessories. The bike’s structure and components should be suitable for the increased load. Overloading can lead to damage and safety issues.
- Regular Inspection: Regular inspection and maintenance of the modified bicycle are crucial to identify potential issues before they become major problems. Regular checks for wear and tear and proper lubrication of moving parts can significantly improve the safety and longevity of the converted bike.
Safety Guideline | Precautions |
---|---|
Secure Mounting | Use appropriate hardware, bracing, and secure fastening techniques. |
Power Transmission | Select components appropriate for the motor’s output. |
Electrical Safety | Insulate all wiring and protect from contact with moving parts. |
Load Assessment | Evaluate the bicycle’s capacity with the added weight. |
Regular Inspection | Check for wear and tear, lubrication, and potential issues. |
Implementation and Testing
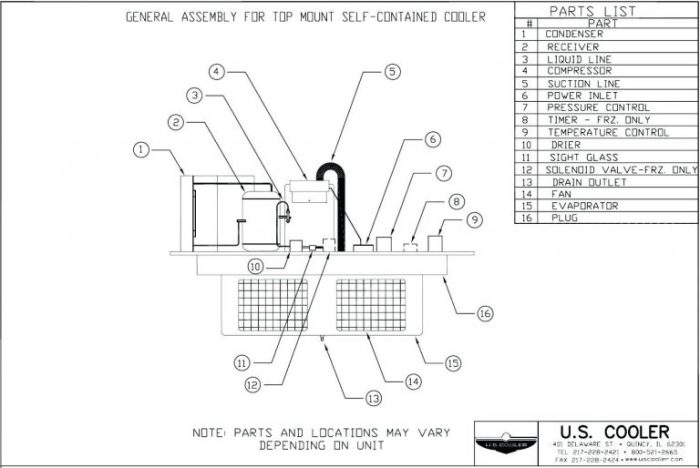
Putting your swamp cooler motor-powered bicycle together is an exciting step. This section details the assembly process and crucial testing procedures to ensure a smooth and safe ride. Careful attention to detail during implementation and thorough testing will help guarantee the bicycle’s reliability and longevity.
Assembly of the Modified Bicycle
The assembly process involves carefully integrating the swamp cooler motor into the bicycle frame. Start by mounting the motor to a suitable location on the frame, ensuring proper alignment with the power transmission system. Secure the motor with appropriate mounting hardware, guaranteeing its stability during operation. Connect the motor wires to the power source and control system, confirming correct polarity to prevent damage.
Subsequently, install the power transmission components, such as chains, belts, or gears, ensuring they are properly aligned and tensioned. Final steps include installing any necessary safety equipment and verifying the functionality of the entire system before riding.
Testing Procedures for Proper Functionality
Thorough testing is essential to validate the motor’s performance and the overall system’s reliability. Begin with static tests to evaluate the motor’s operation without any load. Observe the motor’s speed and torque characteristics, and listen for any unusual noises or vibrations. These preliminary checks help identify potential mechanical issues before loading the system. Subsequently, perform load tests to determine the motor’s performance under actual riding conditions.
Methods for Testing Motor Performance
Several methods can be used to evaluate the motor’s performance. Measure the motor’s speed and torque using appropriate tools. Observe the motor’s efficiency by measuring the power output compared to the energy input. Record these data points and analyze them to understand the motor’s behavior. A critical aspect is assessing the motor’s ability to maintain a consistent speed under varying loads.
Monitor the system’s performance under different conditions, including inclines and different rider weights.
Potential Issues During Testing and Troubleshooting
During testing, various issues might arise. Problems like incorrect wiring connections or inadequate power supply can lead to motor malfunction. Inadequate alignment of the power transmission system or loose components can result in inefficient power transfer and excessive wear. If the motor runs at an inconsistent speed or produces unusual noises, inspect the connections and mechanical components for any issues.
Measuring and Adjusting Motor Performance
Adjusting the motor’s performance involves fine-tuning the power transmission system and control components. Adjust the chain or belt tension to optimize power transfer. Modify the control system to adjust the motor speed and torque according to the desired performance characteristics. Experiment with different control settings to find the optimal balance between speed, torque, and efficiency.
Summary of Test Procedures and Expected Outcomes
Test Procedure | Expected Outcome |
---|---|
Static test (no load) | Motor operates smoothly at expected speed and torque with no unusual noises or vibrations. |
Load test (inclines) | Motor maintains consistent speed and torque even on inclines, demonstrating its ability to handle load variations. |
Speed and torque measurement | Motor speed and torque remain within expected ranges. |
Efficiency measurement | Motor efficiency meets the target specifications. |
System consistency test | The system maintains stable performance and speed during various conditions. |
Alternative Uses and Applications
Harnessing the quiet efficiency of a modified swamp cooler motor opens up a wealth of possibilities beyond bicycle propulsion. This adaptable motor, with its robust construction and relatively low maintenance, can find new life in various mechanical systems. Exploring these alternative applications not only extends the motor’s lifespan but also unlocks its potential for diverse and practical uses.Swamp cooler motors, due to their inherent characteristics, are well-suited for applications requiring consistent, low-speed torque.
Their compact design and ability to be easily integrated into existing systems make them an attractive choice for numerous projects.
Potential Applications in Other Transportation Systems
This section explores the applicability of modified swamp cooler motors in other transportation contexts. These motors can be a suitable option for specialized vehicles, particularly in scenarios where high torque at low speeds is crucial.
- Small-scale agricultural vehicles: The ability to provide steady power for tasks like tilling small plots or transporting light loads makes them suitable for smaller agricultural equipment. The motors’ low speed operation is well-suited for these applications, providing consistent power for the necessary tasks.
- Personal transport devices: Consideration can be given to modifying the motor for use in small, personal transport vehicles such as hand-powered carts or small, specialized vehicles. This might involve adapting the gear ratios and power transmission systems for optimal performance in the targeted application.
- Specialized industrial tools: Swamp cooler motors can be suitable for tools needing steady low-speed torque, such as small-scale grinding wheels or specialized material-handling devices. The consistent torque output makes them ideal for tasks where precision and reliability are key.
Adaptation for Other Mechanical Systems
This section details the process of adapting the motor for use in various mechanical systems. Key considerations include gear ratios, control systems, and power transmission mechanisms.
- Gearbox integration: The motor’s output shaft can be coupled with a gearbox to adjust the speed and torque characteristics for specific tasks. This is a critical step in adapting the motor for various applications, providing a wide range of output characteristics.
- Control systems: Implementing simple control systems such as variable-speed drives (VSDs) can provide precise speed control and enable the motor to be used in systems requiring dynamic adjustments to power output. This allows for greater flexibility in the application of the modified motor.
- Power transmission mechanisms: Adapting the power transmission mechanisms, such as chains, belts, or sprockets, allows the motor to be coupled to various output components. Proper selection of the transmission mechanism is essential for efficient power transfer.
Suitability for Specific Machines
The inherent characteristics of swamp cooler motors make them suitable for specific machine applications. This section will explore examples of their suitability and how modifications can be made.
- Small-scale pumps: The motor’s low speed, high torque characteristics are well-suited for pumping applications, such as small water pumps for irrigation or drainage. The consistent power delivery ensures reliable operation in these applications.
- Small-scale generators: The motor’s ability to produce consistent torque at low speeds makes it suitable for generating small amounts of power for off-grid or backup applications. This can involve adapting the motor’s output to drive a generator, providing a reliable power source.
- Construction equipment: The motor’s robust design and ability to deliver consistent torque make it a viable option for smaller construction tasks. This may involve adaptations to the motor housing and mounting for durability and ease of integration into existing equipment.
Summary Table of Alternative Applications
Application | Modification Points | Suitability |
---|---|---|
Small-scale agricultural equipment | Gearbox, control system | High |
Small-scale pumps | Power transmission, control system | Medium |
Small-scale generators | Generator coupling, control system | High |
Personal transport devices | Gearbox, power transmission | Medium |
Specialized industrial tools | Gearbox, mounting | Medium |
Construction equipment | Mounting, housing | Low |
Final Conclusion
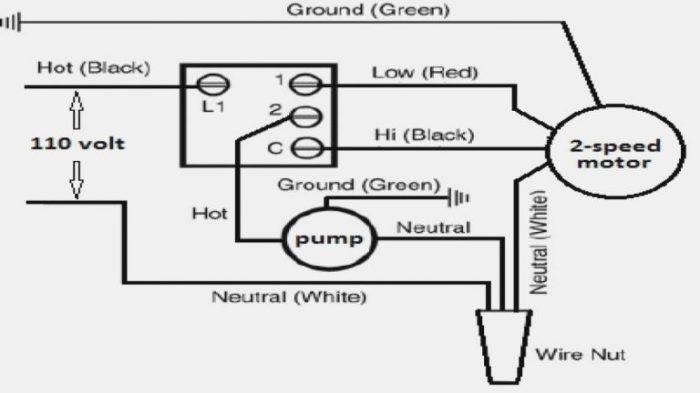
In conclusion, adapting a swamp cooler motor for bicycle use presents a fascinating engineering challenge. While offering the potential for unique propulsion systems, the process demands careful consideration of motor selection, modification, power transmission, and safety. This guide provides a thorough framework to navigate this process, from initial design to final testing and implementation. The potential for alternative applications further expands the scope of this repurposing effort.
Question & Answer Hub
What are the common issues encountered during motor adaptation?
Common issues include mismatched voltage and power output specifications, inadequate mounting solutions leading to instability, and improper power transmission causing reduced efficiency.
What are some safety precautions to take while working on the modified bicycle?
Ensure proper insulation, use appropriate safety gear (gloves, eye protection), and test the system thoroughly before riding to prevent electrical shocks or mechanical malfunctions.
What are the alternatives to using a swamp cooler motor for bicycle?
Other options include using electric motors, internal combustion engines, or human-powered systems like traditional bicycle gears.
How can I optimize the motor’s efficiency for bicycle use?
Optimization involves selecting a motor with appropriate power output, carefully designing the power transmission system, and ensuring minimal friction during operation.