How to find cost of direct materials used? This guide breaks down the process, from defining direct materials to analyzing usage and variance. We’ll cover everything from inventory methods to journal entries, plus helpful examples and real-world scenarios.
Understanding how to calculate the cost of direct materials is crucial for any manufacturing business. Accurate cost calculations directly impact profitability, inventory management, and ultimately, the bottom line. Let’s dive into the essential steps.
Defining Direct Materials
Unlocking profitability in manufacturing hinges on precise cost accounting. A crucial element in this process is the accurate identification and valuation of direct materials. Understanding the distinction between direct and indirect materials is paramount for accurate cost calculations and informed business decisions.
Definition of Direct Materials
Direct materials are those raw materials that are physically and directly incorporated into the final product. They are integral components that can be readily traced to the finished good. This traceability allows for a precise calculation of the cost of goods manufactured.
Characteristics Distinguishing Direct Materials from Indirect Materials
The key differentiator between direct and indirect materials lies in their traceability to the final product. Direct materials are essential components directly used in the manufacturing process and easily traceable to specific products. Indirect materials, in contrast, are used in the production process but are not easily traceable to individual products. Their cost is allocated to specific products based on appropriate methods, such as machine hours or direct labor hours.
Importance of Accurate Identification and Tracking
Precise identification and tracking of direct materials are essential for several reasons. Accurate cost accounting allows for precise pricing strategies, enabling businesses to determine competitive pricing for their products. Furthermore, it helps in inventory management, preventing overstocking or shortages, which can significantly impact profitability. Effective tracking also aids in budgeting and forecasting, facilitating strategic planning and resource allocation.
Direct vs. Indirect Materials, How to find cost of direct materials used
Category | Definition | Examples |
---|---|---|
Direct Materials | Raw materials that are physically and directly incorporated into the final product and can be readily traced to specific products. | Wood in a chair, steel in a car, fabric in a shirt, flour in a cake, ingredients in a pharmaceutical product. |
Indirect Materials | Materials used in the production process but are not easily traceable to specific products. Their cost is allocated to products using appropriate methods. | Lubricants for machinery, cleaning supplies, glue, nails, screws, small tools used in production, packaging materials (unless specifically part of the product). |
Calculating Direct Materials Used
Unlocking the precise cost of direct materials used in your production process is crucial for accurate financial reporting and informed decision-making. This section will detail the formula, a practical example, and the step-by-step process for calculating direct materials used. Understanding this calculation empowers you to optimize your inventory management and profitability.
The Direct Materials Used Formula
The calculation of direct materials used hinges on the relationship between beginning inventory, purchases, and ending inventory. A key formula captures this relationship:
Direct Materials Used = Beginning Direct Materials Inventory + Purchases of Direct Materials – Ending Direct Materials Inventory
This formula clearly demonstrates the fundamental components required to determine the direct materials consumed during a specific period.
Example Calculation of Direct Materials Used
Imagine a manufacturing company, “Innovate Inc.”, in the first quarter of
2024. They have the following data related to direct materials
Step-by-Step Calculation
- Beginning Direct Materials Inventory: Innovate Inc. started the quarter with 500 units of direct materials, valued at $10 per unit. This translates to a beginning inventory of $5,000.
- Purchases of Direct Materials: During the quarter, Innovate Inc. purchased an additional 1,500 units at $12 per unit. This amounts to $18,000 in purchases.
- Ending Direct Materials Inventory: At the end of the quarter, Innovate Inc. had 200 units of direct materials remaining in inventory, valued at $11 per unit. This results in an ending inventory of $2,200.
Using the formula:
Input | Value |
---|---|
Beginning Direct Materials Inventory | $5,000 |
Purchases of Direct Materials | $18,000 |
Ending Direct Materials Inventory | $2,200 |
Applying the formula:
Direct Materials Used = $5,000 + $18,000 – $2,200 = $20,800
Innovate Inc. used $20,800 worth of direct materials during the first quarter of 2024.
Inventory Accounting Methods for Direct Materials
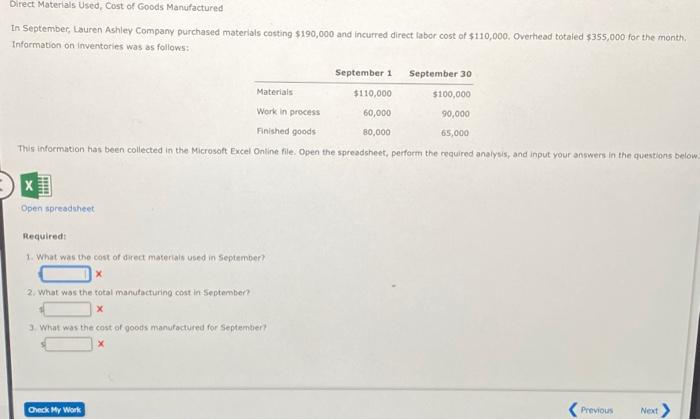
Unlock the secrets to accurate cost calculations for your direct materials. Choosing the right inventory accounting method significantly impacts your financial statements, affecting profitability and tax liabilities. Understanding the nuances of FIFO, LIFO, and weighted-average methods is crucial for informed decision-making.
FIFO (First-In, First-Out) Method
The FIFO method assumes that the first units purchased are the first ones sold. This means the cost of goods sold (COGS) reflects the earliest acquisition costs. This method often aligns with the typical flow of goods in many businesses. For example, perishable goods like food or seasonal products are best tracked using FIFO to ensure older stock is used before newer stock.
LIFO (Last-In, First-Out) Method
Conversely, the LIFO method assumes the last units purchased are the first ones sold. This approach assigns the most recent costs to the cost of goods sold. LIFO can be strategically beneficial in periods of rising prices, as it results in a higher cost of goods sold and a lower reported profit. This lower profit translates to potentially lower tax liabilities.
However, in inflationary environments, LIFO might not always reflect the actual flow of goods.
Weighted-Average Method
The weighted-average method calculates an average cost per unit by dividing the total cost of goods available for sale by the total number of units available for sale. This average cost is then used to determine the cost of goods sold for each sale. This method is relatively straightforward to apply and provides a balance between FIFO and LIFO, smoothing out fluctuations in material costs.
Impact on Financial Statements
The choice of inventory accounting method significantly affects the financial statements, particularly the income statement and balance sheet. FIFO generally results in a higher reported profit in periods of rising prices, while LIFO results in a lower profit and potentially lower taxes. The weighted-average method usually falls between these two extremes, providing a more balanced view. It’s crucial to understand the implications of each method for accurate financial reporting and decision-making.
Comparison of Inventory Accounting Methods
Method | Cost of Goods Sold | Ending Inventory | Impact on Profit |
---|---|---|---|
FIFO | Cost of earliest units | Cost of latest units | Higher in rising prices |
LIFO | Cost of latest units | Cost of earliest units | Lower in rising prices |
Weighted-Average | Average cost of all units | Average cost of all units | Between FIFO and LIFO |
Example Calculation of Direct Materials Used
Using the following data for direct materials:
- Beginning inventory: 100 units at $10 each
- Purchases: 200 units at $12 each
- Purchases: 150 units at $15 each
- Units sold: 350 units
Applying FIFO, LIFO, and weighted-average methods:
- FIFO: 350 units sold: 100 @ $10, 200 @ $12, 50 @ $15. Cost of Goods Sold = $1000 + $2400 + $750 = $4150.
- LIFO: 350 units sold: 150 @ $15, 200 @ $12, 0 @ $10. Cost of Goods Sold = $2250 + $2400 = $4650.
- Weighted-Average: Total cost of all units = $1000 + $2400 + $2250 = $5650. Total units = 450. Average cost per unit = $5650 / 450 = $12.56. Cost of Goods Sold = 350 units
– $12.56 = $4396.
These calculations demonstrate how each method produces a different cost of goods sold.
Recording Direct Materials Costs: How To Find Cost Of Direct Materials Used
Unlocking the secrets to accurate inventory management starts with meticulously recording direct materials costs. This crucial step ensures a precise understanding of your production expenses and ultimately, your profitability. Understanding the journal entries and accounts involved is paramount for informed decision-making.Accurate recording of direct materials costs is critical for financial reporting and internal decision-making. Incorrect entries can lead to inaccurate cost calculations, impacting pricing strategies, profitability assessments, and overall financial health.
Thorough understanding and application of the correct accounting procedures are vital for effective financial management.
Journal Entries for Direct Materials Purchases
Properly recording direct material purchases is essential for maintaining an accurate inventory record. The purchase of direct materials is a common transaction that affects the inventory account. This section details the journal entry for this transaction.
The purchase of direct materials typically involves debiting the inventory account and crediting accounts payable or cash. This reflects the increase in the company’s inventory and the corresponding increase in its obligation to pay for the materials.
- Debit: Inventory. This account increases the balance, reflecting the addition of direct materials to the inventory.
- Credit: Accounts Payable (or Cash). This account reflects the company’s obligation to pay for the materials, or the actual cash outflow.
Journal Entries for Direct Materials Used in Production
Recording the use of direct materials in production is crucial for calculating the cost of goods manufactured. The use of direct materials in production directly impacts the cost of goods produced and subsequently, the cost of goods sold.
The journal entry for direct materials used in production involves debiting the Work-in-Process Inventory account and crediting the Raw Materials Inventory account. This reflects the transfer of direct materials from the raw materials inventory to the work-in-process inventory.
- Debit: Work-in-Process Inventory. This account increases the balance, reflecting the direct materials used in production.
- Credit: Raw Materials Inventory. This account decreases, reflecting the reduction in the raw materials inventory.
Impact on the Accounting Equation
Understanding how these entries affect the accounting equation is vital for financial analysis. The accounting equation, Assets = Liabilities + Equity, must always balance. The journal entries for direct materials purchases and usage directly impact the balance of the equation.
Purchases increase both assets (inventory) and liabilities (accounts payable). Usage reduces the raw materials inventory and increases the work-in-process inventory. These changes maintain the balance of the equation.
Journal Entry Table
This table summarizes the journal entries for various direct materials transactions.
Transaction | Debit | Credit |
---|---|---|
Purchase of Direct Materials | Inventory | Accounts Payable/Cash |
Use of Direct Materials in Production | Work-in-Process Inventory | Raw Materials Inventory |
Factors Affecting Direct Materials Costs
Understanding the cost of direct materials is crucial for accurate financial reporting and sound business decisions. Direct materials costs are not static; various factors influence their price and availability. This section delves into these influential elements.A comprehensive grasp of these factors is vital for businesses to forecast expenses, optimize procurement strategies, and maintain profitability in a dynamic market. Material costs are not a fixed entity but a constantly evolving figure affected by numerous variables.
Market Fluctuations
Market conditions play a significant role in shaping direct material costs. Fluctuations in supply and demand, as well as global economic trends, can drastically impact prices. For example, a surge in demand for a particular raw material, like steel, can drive up its price, increasing production costs for companies reliant on that material. Conversely, a surplus of a commodity can lead to a decrease in price.
Material Quality
The quality of direct materials directly impacts their cost. Higher-quality materials often command a premium price due to enhanced durability, performance, or reduced waste. For instance, using premium-grade steel in a car part might result in a more robust and reliable product, but at a higher material cost. Conversely, lower-quality materials, while potentially cheaper, may necessitate more rework or replacements, leading to increased overall costs.
Supplier Relationships and Negotiation
Strong relationships with suppliers are essential for securing favorable material pricing. Negotiation power and volume discounts can substantially reduce the overall cost of direct materials. Companies with established relationships can leverage their volume to negotiate better prices, potentially achieving significant savings.
Geographic Location
Geographical location of suppliers and production facilities can significantly influence material costs. Transportation costs and tariffs vary depending on the distance between these locations. For example, sourcing materials from a distant location may increase transportation costs, adding to the overall material cost. Conversely, proximity to suppliers can minimize these costs.
Government Regulations and Policies
Government regulations, including environmental standards and import/export policies, can also impact direct material costs. Compliance with regulations often necessitates using specific materials or processes, which can be more expensive than alternative options.
Table: Factors Affecting Direct Material Costs
Factor | Potential Impact |
---|---|
Market Fluctuations | Significant price swings based on supply and demand |
Material Quality | Higher quality often means higher costs, but potentially lower overall expenses due to reduced waste and rework. |
Supplier Relationships | Strong relationships lead to better pricing and terms. |
Geographic Location | Transportation costs and tariffs affect material costs. |
Government Regulations | Compliance can increase material costs due to specific requirements. |
Analyzing Direct Materials Usage
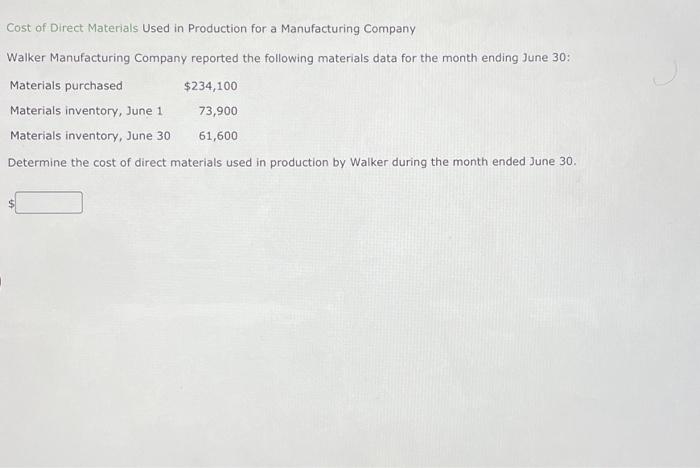
Optimizing direct material usage is crucial for cost reduction and profitability in any manufacturing operation. Understanding how materials are consumed allows businesses to identify inefficiencies, improve processes, and ultimately, boost bottom-line performance. A meticulous analysis of direct materials usage provides valuable insights into potential cost savings and waste reduction strategies.
Importance of Analyzing Direct Materials Usage
Effective analysis of direct materials usage is vital for identifying areas where costs can be reduced and operational efficiency can be improved. By understanding the consumption patterns of materials, companies can pinpoint potential waste and inefficiencies, leading to cost savings and increased profitability. This analysis is instrumental in achieving greater control over inventory levels, minimizing storage costs, and ensuring timely material availability for production.
It also helps identify potential risks associated with material shortages and supply chain disruptions.
Identifying Potential Areas for Cost Savings in Material Usage
Careful scrutiny of material usage patterns can reveal opportunities for significant cost savings. Analyzing historical data on material consumption, coupled with production output, provides a foundation for identifying trends and potential inefficiencies. Comparing material usage against industry benchmarks can further highlight areas where improvements can be made. Detailed process analysis, including the identification of bottlenecks or unnecessary steps, can pinpoint the source of material waste and provide specific avenues for cost reduction.
Methods for Evaluating Material Waste and Scrap
Quantifying material waste and scrap is essential for effective cost control. Establishing precise measurement systems for material loss at different stages of production is critical. This often involves tracking material usage against production targets, and calculating the percentage of waste or scrap generated. The analysis should encompass a comprehensive review of the entire production process, including receiving, storage, and manufacturing stages.
Methods for Analyzing Material Usage
Regular analysis of material usage allows for the identification of areas for improvement. By systematically evaluating the different stages of material usage, companies can pinpoint inefficiencies and implement corrective measures.
Method | Description | Potential Benefits |
---|---|---|
Standard Costing | Establishing predetermined costs for materials used in production. Comparing actual costs against standard costs to identify variances. | Identifies deviations from expected material consumption, pinpointing areas requiring further investigation. |
Material Yield Analysis | Calculating the ratio of usable output to the total input of materials. | Highlights potential waste and scrap generation. Provides insights into material efficiency and potential for process optimization. |
Process Mapping and Value Stream Analysis | Analyzing the flow of materials throughout the production process, identifying bottlenecks and non-value-added activities. | Reveals opportunities for streamlining processes and reducing material waste, enhancing overall efficiency. |
Statistical Process Control (SPC) | Using statistical methods to monitor material usage and identify patterns of variation. | Helps predict potential issues and implement preventative measures to avoid material waste and scrap. |
Illustrative Examples
Unlocking the secrets of direct materials cost calculation is crucial for optimizing your manufacturing process. Understanding how to accurately track and account for direct materials is the cornerstone of profitability and informed decision-making. These examples will illuminate the practical application of the concepts discussed.Accurate cost accounting ensures your manufacturing operations are running smoothly and profitably. This section provides practical examples to illustrate how to calculate direct materials used, manage inventory, and determine the cost of specific products.
Comprehensive Manufacturing Example
Calculating direct materials used in a manufacturing process involves several steps. Consider a furniture manufacturer producing wooden chairs. They need wood, screws, and fabric.
- Beginning Inventory: The company starts the month with 100 board feet of wood valued at $500. They also have 500 screws valued at $25 and 200 yards of fabric valued at $400.
- Purchases: During the month, they purchase an additional 200 board feet of wood for $1000, 1000 screws for $50, and 300 yards of fabric for $600.
- Ending Inventory: At the end of the month, an inventory count reveals 50 board feet of wood, 200 screws, and 150 yards of fabric remaining.
Using these figures, the calculation for direct materials used is as follows:
Direct Materials Used = Beginning Inventory + Purchases – Ending Inventory
Substituting the values:
Direct Materials Used = $500 + $1000 + $50 + $600 – ($250 + $100 + $300) = $2150 – $650 = $1500
The total direct materials used in manufacturing the chairs during the month is $1500.
Inventory Management Scenario
Effective inventory management is vital for smooth production. Consider a bakery producing custom cakes. They use a variety of ingredients, including flour, sugar, and chocolate.
- Maintaining a sufficient stock of ingredients is crucial to avoid delays in production.
- Tracking inventory levels helps predict potential shortages and optimize purchasing strategies.
- Using FIFO (First-In, First-Out) or LIFO (Last-In, First-Out) methods to value inventory is important for accurate cost accounting.
The bakery can utilize these methods to account for the flow of ingredients. For example, if they purchased 100 pounds of flour at $2 per pound and 100 pounds at $2.50 per pound, the cost of flour used will vary depending on the inventory method chosen. This scenario highlights the importance of carefully selecting an inventory method for accurate cost tracking.
Product Cost Calculation
Consider a company manufacturing a specific product, like a smartphone, which has various components:
Component | Quantity | Cost per Unit | Total Cost |
---|---|---|---|
Processor | 1 | $50 | $50 |
Display | 1 | $100 | $100 |
Memory | 1 | $25 | $25 |
Other Parts | Various | Variable | $200 |
The total direct materials cost for one smartphone is the sum of all these components: $50 + $100 + $25 + $200 = $375.
Significance of Accurate Calculations
Accurate direct materials cost calculations are paramount for informed decision-making.
- Pricing Strategies: Accurate cost data enables setting competitive yet profitable prices for products.
- Profitability Analysis: Understanding the cost of materials directly impacts the analysis of profitability and identifying areas for improvement.
- Inventory Management: Precise calculations lead to better inventory management, minimizing waste and maximizing resource utilization.
By meticulously calculating direct materials used, businesses gain a crucial advantage in the marketplace, ensuring sustainable growth and profitability.
Direct Materials Cost Variance Analysis
Uncover hidden opportunities and pinpoint areas for improvement in your direct materials costs with a precise variance analysis. Understanding the difference between predicted and actual costs empowers informed decision-making and optimized resource allocation. This critical step refines your understanding of material expenses, enabling proactive cost management and greater profitability.Variance analysis is a crucial component of cost accounting, offering insights into the efficiency and effectiveness of direct material usage.
It’s a systematic comparison of predicted (standard) costs against actual costs, allowing businesses to identify and address potential discrepancies. This analysis helps in pinpointing the root causes of variances, whether they are related to price, quantity, or both.
Identifying Variances in Direct Materials Costs
The process begins by establishing standard costs for direct materials. These standards represent the anticipated costs for materials based on historical data, industry benchmarks, and anticipated market conditions. Actual costs are then recorded and compared to the standard costs. Any difference between the two represents a variance. These variances can be categorized into price variances and quantity variances.
A price variance reflects the difference between the actual price paid for materials and the standard price. A quantity variance reflects the difference between the actual quantity of materials used and the standard quantity allowed for the actual output.
Comparing Actual Costs to Standard Costs
A critical step in variance analysis is the precise comparison of actual costs with pre-determined standard costs. This meticulous comparison highlights any discrepancies, which can be categorized as either favorable or unfavorable. A favorable variance indicates that actual costs are lower than standard costs, while an unfavorable variance indicates that actual costs are higher than standard costs. This comparison forms the foundation for subsequent analysis, revealing the underlying causes of the observed variances.
Detailed Example of Variance Analysis
Consider a company producing widgets. The standard cost for direct materials per widget is $2.00. During a given period, the company purchased 10,000 units of material at an actual cost of $2.20 per unit. They used 9,500 units in production.The total actual cost is $21,000 (9,500 units
- $2.20). The standard cost for the materials used is $19,000 (9,500 units
- $2.00).
The price variance is calculated as follows:
(Actual Price – Standard Price)
- Actual Quantity = ($2.20 – $2.00)
- 10,000 units = $2,000 (Unfavorable)
The quantity variance is calculated as follows:
(Actual Quantity – Standard Quantity)
- Standard Price = (9,500 – 9,000)
- $2.00 = $1,000 (Unfavorable)
The total materials variance is $3,000 (Unfavorable).
Steps in Direct Materials Cost Variance Analysis
Step | Description |
---|---|
1 | Establish standard costs for direct materials, considering factors like price, quantity, and quality. |
2 | Record the actual costs incurred for direct materials. |
3 | Calculate the price variance by comparing the actual price per unit with the standard price per unit and multiplying by the actual quantity purchased. |
4 | Calculate the quantity variance by comparing the actual quantity of materials used with the standard quantity allowed for the actual output and multiplying by the standard price per unit. |
5 | Determine whether each variance is favorable or unfavorable. |
6 | Analyze the causes of the variances, such as material price fluctuations, inefficiencies in material usage, or changes in supplier relationships. |
7 | Take corrective actions to address the root causes of the variances and improve future material cost management. |
Last Point
In summary, calculating the cost of direct materials used involves a multi-step process that includes defining direct materials, calculating their usage, accounting for inventory, and recording costs. Analyzing usage, identifying potential cost savings, and performing variance analysis are all key to optimizing material management and boosting profitability. This guide has provided the essential tools to master this critical aspect of manufacturing.
User Queries
What are some common inventory accounting methods?
FIFO (First-In, First-Out), LIFO (Last-In, First-Out), and weighted-average are common methods. Each affects the cost of goods sold differently, influencing the financial statements.
How do market fluctuations affect material costs?
Market fluctuations can significantly impact the price of raw materials. Businesses need to monitor these changes to adjust their purchasing strategies and production costs.
What are the journal entries for recording direct material purchases?
A debit to raw materials inventory and a credit to accounts payable are used to record the purchase of direct materials.
What’s the difference between direct and indirect materials?
Direct materials are those used in the production of a specific product, while indirect materials are used in support functions, like cleaning supplies.