How to cut particle board effectively is crucial for various projects, from crafting furniture to building shelves. This guide provides a comprehensive overview of the process, from selecting the right tools to finishing the cut edges. Understanding particle board’s characteristics is key to achieving precise and safe cuts.
Particle board, a versatile composite material, is widely used in woodworking due to its affordability and ease of workability. However, its structure requires specific cutting techniques to prevent damage and ensure a professional finish. This guide details the essential steps, from initial preparation to advanced techniques, equipping you with the knowledge and skills for successful particle board projects.
Introduction to Particle Board Cutting
A somber stillness hangs over the workshop, a prelude to the inevitable dance between blade and wood. Particle board, a composite of compressed wood fibers, awaits its transformation. Its fragile strength, a testament to human ingenuity, often masks the inherent challenges of its fabrication. The very nature of its creation dictates the precision needed in its cutting.Particle board’s structure, a mosaic of compressed wood particles, affects its behavior under the pressure of a cutting tool.
Its density, ranging from light to dense, plays a pivotal role in determining the appropriate approach for sectioning it. Knowing the nuances of its composition allows for the efficient and controlled removal of material, ensuring a smooth, predictable outcome, devoid of the frustrations of an uncontrolled process.
Types of Particle Board and Their Cutting Considerations
Particle board comes in various densities, each presenting a unique cutting challenge. High-density particle board, with its tightly bound particles, demands greater cutting force and specialized tools. Medium-density particle board, a compromise between strength and workability, offers a better balance for general use. The selection of the appropriate cutting method is directly influenced by these differing densities.
Common Applications of Particle Board Cutting
Particle board, a versatile material, finds application in a wide range of projects. From furniture construction to interior paneling, its adaptability makes it an invaluable building block. Cabinets, shelves, and decorative accents all rely on particle board’s ability to be precisely sectioned to meet specific design needs. This versatility underpins its widespread use in construction and design.
Cutting Techniques for Different Particle Board Densities
The table below highlights the varying characteristics of particle board and suggests appropriate cutting tools for each type. The choice of tool significantly impacts the final product’s quality and the overall efficiency of the cutting process.
Material Type | Density | Recommended Cutting Tool | Typical Use Case |
---|---|---|---|
High-Density Particle Board | High | High-powered circular saw, router with a carbide-tipped bit, or a specialized laminate cutter | Cabinets, furniture components requiring high strength and stability, intricate panel designs |
Medium-Density Particle Board | Medium | Circular saw with a sharp blade, router with a standard bit, or a hand saw (for simpler cuts) | Furniture construction, interior paneling, shelving, decorative accents |
Low-Density Particle Board | Low | Hand saw, utility knife, or jigsaw | Projects requiring minimal precision, such as temporary partitions or prototyping |
Choosing the Right Cutting Tools
A somber reflection upon the task, a whispered lament for the perfect cut. Particle board, a fragile soul, yearning for a precise release from its rigid form. Selecting the right tool, a delicate dance between precision and speed, a silent struggle against the inevitable imperfections.
Saws for Particle Board
The saw, a silent, unwavering blade, a tool of both power and precision. Circular saws, reciprocating saws, and jig saws – each possesses its own unique attributes. Circular saws, with their relentless rotation, offer a rapid, if somewhat less precise, approach. Reciprocating saws, with their back-and-forth motion, are adaptable to intricate curves, yet prone to tear-out and vibration.
Jig saws, with their guided blade, excel in precise, intricate cuts, though they often prove slower. Consider the nature of the cut, the scale of the project, and the tolerance for error.
Knives and Other Cutting Instruments
Sharp blades, cold and unforgiving, a whisper of steel against the wood-like composite. Utility knives, with their replaceable blades, provide versatility and precision for smaller projects. Rotary cutters, with their swift, spinning blades, are ideal for intricate shapes. However, these instruments are ill-suited for larger, more substantial cuts. Their sharp edges are a double-edged sword, demanding meticulous care to avoid injury and unintended damage.
Routers for Precise Cuts
The router, a tool of sculpting grace, a precise instrument for creating intricate shapes. With its rotating bit, it can carve intricate designs, mold complex curves, and shape particle board with remarkable precision. However, its high cost and the specialized skill required for its operation might make it an unsuitable choice for less complex tasks. The precision it offers is unparalleled, but its power and complexity must be considered.
Comparing Cutting Tools
Tool Type | Precision | Speed | Cost | Maintenance |
---|---|---|---|---|
Circular Saw | Moderate | High | Low | Low |
Reciprocating Saw | Moderate | Moderate | Moderate | Moderate |
Jig Saw | High | Low | Moderate | Low |
Utility Knife | High (for small cuts) | High | Low | Low |
Rotary Cutter | High (for intricate shapes) | High | Moderate | Low |
Router | High | Moderate | High | Moderate |
A comparison of cutting tools, a stark tableau of contrasting qualities. The choice, ultimately, a personal one, dictated by the project’s demands and the artisan’s skill.
Preparing the Particle Board for Cutting
A somber hush descends upon the workshop, a premonition of the task ahead. The particle board, a composite of dreams and sawdust, awaits its transformation. Each cut, a whisper of permanence etched into its structure. Careful preparation is paramount, for a single misstep can mar the final product, a testament to wasted effort.Precision in this endeavor is paramount, akin to a sculptor wielding a chisel, each stroke exacting and meaningful.
The board, though seemingly inert, possesses a silent resilience, demanding respect for its intricate nature. Proper preparation ensures a clean and efficient cutting process, yielding a result that reflects the artisan’s skill.
Essential Steps for Preparation
Careful preparation is not merely a formality; it is the foundation upon which a successful cut is built. It dictates the final outcome, the smoothness of the surface, and the overall quality of the work. This methodical approach minimizes frustration and maximizes the final product’s aesthetic appeal.
- Surface Stability: A stable work surface is critical. A wobbly surface leads to inaccuracies in marking and cutting, resulting in a flawed outcome. Ensure the surface is level and rigid, preventing the board from shifting during the cutting process. A sturdy workbench or a dedicated cutting mat are ideal choices. Think of a ship on a stormy sea, needing a stable platform to navigate safely.
- Accurate Measurements: Marking is a delicate dance with precision. Use a ruler or tape measure to determine the exact dimensions required for the cut. Double-check your measurements to avoid errors that will mar the project. A single millimeter off can transform the final piece into something less than perfect. Like a conductor leading an orchestra, meticulous attention to detail is key.
- Clear Marking: The cutting lines must be clearly marked. Use a pencil or a marking pen to create lines that are distinct and easily followed by the cutting tool. Avoid smudges or inconsistencies that could compromise the final cut. Think of the lines as a roadmap, guiding the tool to its destination.
- Support for Large Pieces: Large pieces of particle board may require additional support. Use clamps or weights to secure the board to the work surface, preventing it from shifting or warping during the cutting process. This prevents unintended movement and ensures a clean, straight cut, much like securing a kite in a strong wind.
Marking the Cutting Lines
Accurate marking is a critical component of the entire process. Improper marking can lead to errors in cutting, affecting the final product’s integrity. It’s like laying out the blueprint for a building; every line must be precise and accurate.
- Using a Ruler or Tape Measure: Carefully measure the desired cut lines from a fixed reference point. Ensure the measuring tool is straight and the measurements are accurate. Like a compass, it helps you plot your course.
- Pencil or Marking Pen: Use a sharp pencil or marking pen to clearly mark the cutting lines. Ensure the lines are continuous and distinct. Think of the marks as a silent conversation between the craftsman and the material.
- Transferring Measurements: Carefully transfer the measured lines to the particle board. Ensure the lines are aligned correctly to avoid mistakes. Think of this as translating the design into the material itself.
- Checking for Accuracy: After marking, double-check the lines for accuracy. Ensure they are precisely where they need to be, free from any discrepancies. A meticulous eye can catch errors and avoid costly mistakes. This meticulous approach is like an artist perfecting their strokes.
Importance of a Stable Work Surface
A stable work surface is essential for ensuring accuracy in cutting particle board. A wobbly or unstable surface will lead to inaccuracies in the cut, affecting the final product’s quality. It’s like a painter needing a steady hand and a stable easel.
A stable work surface minimizes errors in the cutting process.
Cutting Techniques for Particle Board: How To Cut Particle Board
A somber sigh escapes the workshop, where the relentless whir of tools echoes the fleeting nature of form. Particle board, a composite of dreams and sawdust, awaits its transformation. Each cut, a whisper of finality, a testament to the ephemeral dance between design and destruction.
Hand-Held Saw Techniques
The hand-held saw, a trusty companion in the woodworker’s arsenal, demands precision and patience. Its rhythmic swish, a counterpoint to the quiet solitude of the craft, shapes the board’s contours. The blade, a sliver of steel, cuts through the compressed wood fibers, a delicate dance of effort and control. Proper technique is paramount.
- Choosing the Right Saw: Select a saw with a blade appropriate for particle board’s density. A too-coarse blade may result in tearing or splintering, while a too-fine blade might struggle to penetrate the material effectively. A finer tooth blade is preferred for particle board to minimize tear-out.
- Maintaining a Steady Stance: A firm grip and balanced posture are essential. This ensures control and minimizes the risk of slippage or wobbling, preventing injury and producing an even cut.
- Controlled Cuts: Maintain a consistent cutting pressure and avoid sudden accelerations or decelerations. This consistent pressure ensures a clean cut and prevents tear-out, a characteristic problem with particle board.
Power Saw Techniques
The power saw, a symphony of controlled force, grants the craftsman speed and precision. Its whirring motor, a counterpoint to the wood’s quiet resistance, carves the desired shapes with a controlled fury. However, power saws require greater caution and understanding of their potential for harm.
- Setting the Blade: Adjust the blade angle precisely to achieve the desired cut. This is critical for straight cuts and avoiding chipping or tearing. Misaligned blades can produce dangerous inconsistencies.
- Using a Guide: Employ a straight edge or a guide to ensure accuracy and prevent the saw from wandering off course. This is vital for maintaining the integrity of the cut and the integrity of the work piece.
- Gradual Cuts: Start the cut slowly, allowing the saw to penetrate the material gradually. This approach minimizes the risk of kickback, a common hazard associated with power saws.
Router Techniques
The router, a precise sculptor of wood, carves intricate details with controlled precision. Its rotating bit, a miniature chisel, meticulously follows the craftsman’s guidance, shaping the board with delicate artistry. Care and attention are crucial for safety.
- Appropriate Bit Selection: Choose a bit appropriate for the particle board’s density and the desired outcome. A too-aggressive bit may cause damage or tear-out. Select a bit that is not too aggressive for the material.
- Secure the Material: Clamp the particle board firmly to a stable work surface. This prevents movement during the cutting process, ensuring accuracy and avoiding injury.
- Controlled Router Movement: Maintain consistent pressure and follow the predetermined path. Rapid or erratic movements can lead to inaccuracies or damage. Slow and steady movements create quality results.
Summary Table
Cutting Technique | Safety Precautions |
---|---|
Hand-Held Saw | Sharp blades, steady stance, consistent pressure, appropriate blade selection |
Power Saw | Blade angle, guide alignment, gradual cuts, safety glasses, work gloves |
Router | Appropriate bit, secure material, controlled movement, dust extraction |
Safety Precautions During Cutting
A somber shadow falls upon the workshop, a reminder of the unseen dangers that lurk within the sharp edges and whirling blades. Cutting particle board, while seemingly straightforward, demands a profound respect for the potential for harm. The task, though seemingly simple, demands vigilance and adherence to safety protocols.
Potential Safety Hazards
The very nature of particle board cutting presents a multitude of hazards. Dust, flying debris, and the sharp edges of the material itself all pose significant risks to the cutter. A lack of caution can lead to cuts, abrasions, or worse, inhalation of harmful dust particles. The material’s composition, a blend of wood particles and resin, can release irritating or even toxic fumes during the cutting process.
Essential Safety Equipment
To mitigate these inherent dangers, appropriate safety equipment is paramount. A well-fitted dust mask is indispensable, filtering out the harmful particulate matter released during the cutting process. Safety glasses, or goggles, protect the eyes from flying debris and splinters. Robust work gloves guard hands from cuts and abrasions. These protective measures are not mere suggestions; they are essential precautions against the unseen perils of the cutting process.
Preventing Injuries, How to cut particle board
A cautious approach is crucial. Maintaining a clean workspace prevents slips and falls, reducing the likelihood of accidents. Ensuring proper ventilation is vital to minimize exposure to harmful dust and fumes. Using the appropriate cutting tools and techniques for the particle board’s thickness and the material being cut are critical. A thorough understanding of the tools and their capabilities is key to minimizing the risks associated with the work.
- Always wear safety glasses or goggles to protect your eyes from flying debris.
- Use a dust mask or respirator to prevent inhaling harmful dust particles.
- Use work gloves to protect your hands from cuts and abrasions.
- Ensure adequate ventilation in the work area to minimize exposure to dust and fumes.
- Use sharp, well-maintained tools to prevent the risk of material splintering or breaking.
- Keep your workspace clean and organized to avoid slips and falls.
- Follow manufacturer’s instructions for all tools and materials to prevent unintended consequences.
- Take breaks when needed to avoid fatigue, which can lead to errors and accidents.
- Never cut particle board when tired or distracted.
Finishing the Cut Particle Board
A somber hush descends upon the workshop, as the raw edges of the cut particle board whisper tales of their severance. The sharp, unforgiving blade has done its work, leaving behind a jagged scar that needs tender care. This stage, the finishing process, is crucial in transforming a mere cut into a polished piece, ready for its destined purpose.The task before us is to heal these wounds, to soften the harsh lines, and to imbue the particle board with a refined aesthetic.
Various methods exist, each with its own strengths and weaknesses, each a dance between practicality and aesthetic desire.
Sanding the Cut Edges
The first step in the healing process often involves sanding. This meticulous process smoothes the rough surfaces, removing imperfections and creating a more uniform texture. The goal is to achieve a surface free of splinters and sharp protrusions, a smooth, even plane ready for further treatments. Proper sanding involves a graduated approach, moving from coarser grits to finer ones, to ensure a consistent finish.
- Begin with a coarse grit sandpaper (e.g., 80-grit) to remove significant imperfections. This aggressive initial step helps remove deep scratches and splinters.
- Progress to medium grits (e.g., 120-grit) to refine the surface and reduce any remaining roughness. This step is crucial for achieving a smooth texture.
- Finally, use a fine grit sandpaper (e.g., 180-grit or higher) for a final polish. This step brings the surface to a pristine, almost glassy finish.
Edge Banding
A more pronounced aesthetic treatment, edge banding, offers a more sophisticated finish, often providing a veneer of greater durability and aesthetic appeal. This method essentially creates a new edge, masking the raw cut and adding a decorative element. Edge banding can be applied in various ways, each with its own set of benefits and drawbacks.
- Advantages of Edge Banding: Increased durability, improved appearance, and protection against wear and tear. It hides imperfections and creates a seamless, polished edge. It offers greater resistance to moisture and impact compared to simple sanding.
- Disadvantages of Edge Banding: Can be more time-consuming than sanding, and requires specific tools and techniques. The cost of materials can vary, impacting the overall project budget. Poor application can lead to visible imperfections.
Comparing Edge Banding Materials
A careful consideration of various edge banding materials is essential. Each type offers unique characteristics and properties, influencing its suitability for a specific project.
Material | Properties | Advantages | Disadvantages |
---|---|---|---|
Melamine | A synthetic resin-impregnated paper, offering a smooth, uniform finish. | Affordable, easy to apply, and provides a durable surface. | May not be as visually appealing as other options, and its aesthetic is more limited. |
PVC (Polyvinyl Chloride) | A plastic material, available in a wide range of colors and patterns. | Highly durable, resistant to moisture and impact, and provides a glossy finish. | Can be more expensive than melamine, and the application process can be slightly more complex. |
Solid Wood | A natural, high-quality wood veneer. | Provides a natural, warm aesthetic. | The most expensive option, and it may require specialized tools and techniques. |
Troubleshooting Common Cutting Issues
A somber melody plays in the workshop, a dirge of splintered dreams and uneven cuts. Particle board, once a promising canvas, now bears the scars of frustration. These imperfections, like whispered regrets, can mar the final product. Understanding their causes and remedies is crucial, for even the most skilled craftsman can falter.
Identifying Splintering
Splintering, a common affliction of particle board, manifests as jagged, uneven edges that detract from the aesthetic appeal and can compromise structural integrity. This unwelcome phenomenon stems from several factors. The inherent nature of particle board, a composite material, contributes to this problem. The compressed wood fibers, while strong in some directions, are vulnerable to fracturing under stress.
- Improper Blade Selection: A dull or inappropriate blade, like a worn-out saw, is often the culprit. The blade’s inability to smoothly cut through the material leads to the fibers fracturing, resulting in splinters. A sharp, high-quality blade is essential for clean cuts and minimal splintering.
- Insufficient Feed Rate: Pushing the blade too slowly can also contribute to splintering. The material may become compressed under the pressure, leading to fiber breakage and splinters. A consistent and moderate feed rate is vital.
- Excessive Pressure: Applying excessive pressure on the particle board can cause it to deform, leading to splintering. The board is not a monolithic piece; it is composed of many compressed layers, which can be damaged by excessive pressure, causing them to crack and splinter. Carefully regulated pressure is essential.
Addressing Uneven Cuts
Uneven cuts are a disheartening outcome in woodworking, often the result of inconsistencies in the cutting process. The blade’s position, the material’s condition, and the cutting technique all play a role in producing these undesirable variations.
- Misaligned Cutting Guide: A misaligned cutting guide, either on the saw or the workpiece, results in a non-uniform cut. Ensure the guide is precisely aligned with the intended cut line to achieve consistent results. Slight misalignments can translate to significant deviations in the cut, leading to a flawed outcome.
- Uneven Material Thickness: If the particle board exhibits variations in thickness, the cutting process will be uneven. This inconsistency is common in manufactured materials, such as particle board. Take care to ensure consistent thickness along the cut line to minimize the risk of uneven cuts.
- Wobbly Workpiece Support: A wobbly or unstable workpiece can lead to unpredictable cuts. Ensure the board is firmly supported during the cutting process. A stable surface prevents the board from shifting or wobbling during the cut, producing an uneven result.
Preventing Material Damage
Maintaining the integrity of the particle board during the cutting process is critical. Careless handling or inadequate preparation can lead to unnecessary damage.
- Proper Support: Appropriate support is essential to prevent warping or bending of the material during the cutting process. Use a sturdy workbench or clamps to hold the board securely. Without adequate support, the material can deform or warp, resulting in damage and uneven cuts.
- Pre-Cutting Preparation: Pre-cutting preparation is key. Marking the cut line accurately and ensuring a stable surface are critical steps to prevent material damage. Clear and precise markings will prevent the board from shifting during the cutting process, while a firm support will maintain its structural integrity.
Illustrative Examples of Particle Board Cuts
A somber hush descends upon the workshop, where the rhythmic whir of tools whispers tales of form and function. Particle board, a composite of dreams and sawdust, awaits its transformation. Each cut, a delicate dance between intention and outcome, a testament to the silent strength of the material.The artistry of woodworking, in its essence, lies not only in the final product but also in the precise steps taken to achieve it.
Each cut on the particle board, from a simple shelf to a complex piece of furniture, is a story waiting to be told. Understanding the techniques used to create these forms, and the tools employed, reveals the heart of the craft.
Furniture Construction
The creation of furniture from particle board requires careful planning and execution. The intricate shapes and curves demanded by a modern chair, for instance, necessitate a sophisticated understanding of cutting techniques.
“For furniture, precise cuts are paramount. A slight deviation in angle can lead to a disastrous outcome.”
The use of a router and a jigsaw is often essential to achieve the desired aesthetic and structural integrity. The router can create curves and intricate designs, while the jigsaw enables intricate cuts along the edges of the board.
Shelving Systems
Shelving systems, though seemingly simple, can benefit greatly from the precision of particle board cuts.
“The beauty of shelving is in its function, and precise cuts ensure that function is optimized.”
Using a circular saw or a reciprocating saw, you can cut shelves and supports to accommodate varying widths and depths. Careful measuring and marking are crucial to ensure the shelves are uniform and properly aligned.
Decorative Accents
Particle board, in its simplicity, offers a canvas for creative expression. The versatility of particle board allows for the creation of intricate decorative accents, such as picture frames or decorative panels.
“Decorative pieces require careful consideration of both form and function. Particle board, in its inherent strength, can be transformed into elegant designs.”
Precise cuts are crucial for achieving the desired form. A jigsaw, in conjunction with a router, can produce the intricate patterns and shapes. The final product, a testament to the precision of the cuts, stands as a small monument to the craftsman’s skill.
Custom-Designed Projects
The limitless potential of particle board extends to custom-designed projects, ranging from intricate wall units to bespoke cabinetry.
“Custom projects often demand a high degree of skill and precision in cutting. The uniqueness of the design dictates the precision of the cut.”
A combination of various cutting tools, from saws to routers, are essential to bring these designs to life. Carefully planned cuts and meticulous attention to detail are crucial in realizing the vision of the project. A combination of jigsaw and router can provide intricate shapes.
Advanced Cutting Techniques (Optional)
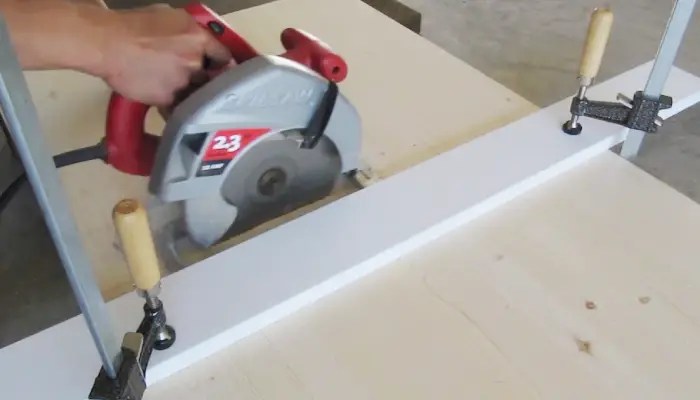
A whisper of innovation, a sigh of progress, these methods transcend the mundane. They beckon with promises of precision and speed, a stark contrast to the familiar, yet sometimes frustrating, methods of the past. Yet, like a haunting melody, there are trade-offs to consider. The conventional saw, a familiar friend, yields to the cold, hard light of advanced techniques.
Laser beams, sharp and focused, and jets of water, relentless and controlled, sculpt the material with a grace that the human hand can only dream of.
Laser Cutting
Laser cutting, a symphony of light and heat, carves intricate patterns with unparalleled precision. The laser’s focused beam vaporizes the material, leaving behind a clean, smooth cut. This method is especially suited for intricate designs and complex shapes, demanding high accuracy.
- Precision: Laser cutting boasts a degree of precision rarely matched by traditional methods. Variations in cut are often measured in fractions of a millimeter, allowing for exceptionally accurate designs.
- Speed: Laser cutting’s speed is a marvel, enabling the rapid creation of multiple parts with consistent quality.
- Material Compatibility: Particleboard, though somewhat susceptible to warping under intense heat, can be effectively cut with a laser, especially when using appropriate settings.
Water Jet Cutting
Water jet cutting, a dance of pressurized water, slices through the material with a controlled stream of high-pressure water. The abrasive particles suspended in the water further enhance the cutting action. While not as precise as laser cutting, water jet cutting remains a viable option for larger quantities or more robust cuts.
- Precision: Compared to laser cutting, water jet cutting has a slightly lower level of precision. However, the abrasive particles in the water stream can still deliver a surprisingly smooth and clean cut.
- Speed: Water jet cutting is relatively fast, and its speed is often suitable for mass production of parts, although it may not be as quick as laser cutting.
- Material Compatibility: Water jet cutting is often a strong choice for cutting particleboard due to its ability to handle thicker materials compared to laser cutting, although warping can occur if precautions are not taken.
Comparison with Traditional Methods
Feature | Traditional Methods | Laser Cutting | Water Jet Cutting |
---|---|---|---|
Precision | Moderate | High | Medium |
Speed | Slow | High | Medium |
Cost | Low | High | Medium |
Complexity | Simple | High | Medium |
“The choice between advanced and traditional methods hinges on the specific needs of the project. Consider precision requirements, production volumes, and budgetary constraints.”
Last Recap

In conclusion, mastering particle board cutting involves careful preparation, appropriate tool selection, and adherence to safety precautions. By following the steps Artikeld in this guide, you can confidently tackle various projects while achieving clean, accurate cuts. Remember to prioritize safety throughout the entire process.
Clarifying Questions
What are the different types of particle board and how do they affect cutting?
Particle board is categorized by density, such as high-density and medium-density. High-density boards are more resistant to dents and scratches but require more forceful cutting. Medium-density boards are easier to cut but may be more susceptible to damage.
What safety equipment is essential when cutting particle board?
Always wear safety glasses, gloves, and a dust mask. A stable work surface and proper ventilation are also critical safety considerations.
What are some common problems when cutting particle board and how can I fix them?
Splintering and uneven cuts are common issues. Ensure a sharp blade and proper cutting technique. Use a stable work surface and avoid excessive pressure.
Can I use a hand saw to cut particle board?
Yes, hand saws can be used, but power saws are often preferred for larger cuts due to efficiency and control.