How to oil a sequential turbo setup is crucial for optimal performance and longevity. Sequential turbocharging systems, unlike parallel setups, deliver power in stages, demanding precise oiling procedures. This guide details the critical steps, from component identification to advanced considerations for diverse applications.
Understanding the specific needs of a sequential turbo system ensures smooth operation and prevents costly damage. This guide walks you through every step, from the fundamental principles to troubleshooting common issues.
Introduction to Sequential Turbo Systems
Sequential turbocharging, a sophisticated approach to engine power enhancement, employs multiple turbochargers in a series. Each turbocharger is designed to operate at a specific engine speed range, optimizing performance across the power band. This contrasts sharply with parallel setups, which utilize multiple turbos working simultaneously.
Fundamental Differences
Sequential turbocharging differs significantly from parallel systems. In sequential setups, turbos are engaged in a staged manner, each responding to a specific engine speed or load. This differs from parallel setups where multiple turbos work concurrently, typically producing a higher boost at lower engine speeds. The key distinction lies in the dynamic response and optimized performance across various RPM ranges.
This precision in operation allows for superior fuel efficiency and reduced emissions at low to mid-range RPMs.
Typical Applications and Advantages
Sequential turbocharging is often seen in high-performance applications, particularly in engines designed for a broad power band and a high torque output. Its primary advantages include improved low-end torque, optimized mid-range power, and enhanced overall performance characteristics. A significant benefit is reduced turbo lag, which is often a concern in high-output engines. These systems are frequently employed in race cars and high-performance vehicles.
Importance of Proper Oiling
Proper oiling is paramount in sequential turbo systems due to the complex and potentially high-stress operating conditions. The intricate system demands precise oil delivery to all components, including the turbos and the engine itself. Failure to maintain adequate oil pressure can lead to severe damage to the turbos and engine components. This is particularly critical in maintaining the high-pressure and high-temperature environment, which can lead to premature wear.
Maintaining precise oil viscosity is also important to optimize performance and reduce wear.
Comparison of Sequential and Parallel Turbo Systems
Feature | Sequential Turbo | Parallel Turbo |
---|---|---|
Oiling Method | Requires a dedicated oiling system for each turbo, often with complex piping and filtration to ensure proper pressure and temperature regulation. | Usually shares the engine’s main oiling system. Simplified design but can potentially lead to pressure fluctuations, particularly with high output engines. |
Boost Response | Staggered boost delivery across RPM ranges, generally leading to a smoother and more linear power delivery. | Higher boost at lower engine speeds due to simultaneous operation, potentially leading to more turbo lag in higher RPM ranges. |
Applications | High-performance vehicles, race cars, and engines demanding a broad power band. | Common in production vehicles needing a good balance of low-end torque and mid-range power. |
Complexity | More complex system requiring careful design and maintenance. | Relatively simpler design, but potentially requiring more sophisticated engine management systems to regulate the turbos. |
Sequential turbo setups offer superior control over boost pressure and responsiveness, but require more complex oiling systems.
Oil System Components and Functions
Sequential turbo setups demand a sophisticated oiling system to ensure smooth operation and prevent catastrophic failure. Proper oil delivery to both turbos is critical, especially when operating under high load and demanding conditions. A robust system needs careful consideration of each component and its specific function within the intricate network.The sequential turbo system’s oiling network is a precisely engineered pathway, ensuring the right amount of oil reaches the right turbo at the right time.
This ensures optimal lubrication for each turbocharger, preventing overheating and wear, and maximizing performance and longevity.
Key Components of the Sequential Turbo Oiling System
The oiling system in a sequential turbo setup comprises several interconnected components. Each plays a crucial role in the consistent supply of oil to the turbochargers. Understanding these components and their specific functions is paramount to maintaining a healthy and efficient setup.
- Oil Pump: The heart of the system, the high-volume oil pump provides the initial pressure and flow needed to circulate oil throughout the entire system. Its capacity needs to be substantial to meet the demands of both turbos, especially during high-performance operation.
- Oil Filter: Ensuring clean oil is essential for optimal turbo performance. The oil filter traps contaminants, preventing them from reaching the turbochargers and causing damage. A high-quality filter with a sufficient filtration rating is vital.
- Oil Cooler: Maintaining the correct oil temperature is paramount. The oil cooler helps dissipate heat generated during operation, preventing oil from reaching damaging temperatures. This component is especially important for high-power applications or extended use cases.
- Oil Pressure Regulators: Precisely regulating oil pressure is crucial. These components maintain the optimal pressure required for lubrication while preventing overpressure situations, which could lead to leaks or damage. Multiple regulators may be needed to control pressure to each turbo individually.
- Oil Lines and Fittings: These components provide the pathways for oil to travel from the pump to the turbos. The lines need to be robust enough to handle high pressure and temperature, and properly sized to ensure adequate flow to each turbo. Materials resistant to wear and degradation are essential.
- Turbocharger Oil Feed Lines and Galleries: These lines deliver oil specifically to each turbocharger. The design must ensure proper oil flow to the compressor and turbine sections, preventing starvation or excess lubrication. Proper routing is critical to avoid pressure drops or oil starvation issues.
Oiling Requirements for Each Turbocharger
Each turbocharger in a sequential setup has specific oiling requirements. This is crucial to maintain optimal lubrication and avoid potential issues.
- Individual Oil Feed Lines: Dedicated oil lines ensure each turbo receives the required oil flow and pressure. This prevents cross-contamination and allows for precise control of the oil supply to each turbocharger. This is often a key difference between sequential and parallel setups.
- Optimized Oil Delivery Rates: The oil delivery rate must be optimized for each turbo based on its individual needs. This is dependent on variables such as the turbo’s size, the rotational speed, and the operating conditions. This necessitates careful calibration.
- Pressure Monitoring Systems: Monitoring oil pressure at each turbocharger is vital. This allows for early detection of any issues with oil delivery or pressure loss, enabling prompt action to prevent potential damage. Dedicated pressure sensors are used for this purpose.
Diagram of the Sequential Turbo Oil System
(A detailed diagram of the oiling system, illustrating the flow from the pump, through the filter, cooler, regulators, and individual feed lines to each turbocharger, would be included here. Each component would be clearly labeled.)
Components and Functions Table
Component | Function |
---|---|
Oil Pump | Provides high-volume oil flow and pressure. |
Oil Filter | Removes contaminants from the oil. |
Oil Cooler | Keeps oil temperature within the optimal range. |
Oil Pressure Regulators | Maintains the required oil pressure to each turbo. |
Oil Lines & Fittings | Convey oil from the pump to the turbos. |
Turbocharger Oil Feed Lines & Galleries | Deliver oil specifically to each turbocharger. |
Oil Viscosity and Selection
Oil viscosity is a critical factor in the performance and longevity of sequential turbo systems. It directly impacts lubrication, heat dissipation, and overall efficiency. Choosing the correct viscosity is paramount for preventing wear, maximizing turbocharger lifespan, and ensuring optimal system performance across varying operating conditions.
Significance of Oil Viscosity
Viscosity, essentially the resistance of a fluid to flow, is crucial in sequential turbo systems. A proper viscosity ensures adequate lubrication of all moving parts, including bearings, shafts, and seals. This reduces friction, minimizing wear and tear, and maintaining optimal performance. High viscosity can hinder oil flow, potentially leading to insufficient lubrication and overheating, while low viscosity can result in inadequate lubrication and increased wear.
Factors Influencing Oil Viscosity Selection
Several factors influence the optimal oil viscosity for a sequential turbo system. These include operating temperature, engine load, and the specific design of the turbocharger. Higher operating temperatures often necessitate higher viscosity oils to maintain lubrication and prevent excessive thinning. Conversely, lower temperatures may allow for lower viscosity oils, promoting better flow. Heavy engine loads, which generate more heat, will typically require a higher viscosity grade.
Impact of Different Viscosity Grades on Turbocharger Performance
Different viscosity grades will have different impacts on turbocharger performance. High viscosity oils can provide excellent lubrication under high load conditions but may experience reduced flow at low loads, leading to potential pressure drop issues. Low viscosity oils, conversely, flow readily, but may not offer sufficient lubrication under high load conditions, potentially resulting in increased wear and tear.
The right viscosity strike a balance between these extremes.
Recommended Oil Viscosities for Various Operating Conditions
Selecting the correct oil viscosity depends heavily on the expected operating conditions. Different operating temperatures and load scenarios require different viscosity grades. The goal is to select an oil that adequately lubricates all components at various temperatures and loads.
Viscosity Recommendations Table
This table provides a general guideline for viscosity recommendations based on temperature ranges and application types. Specific recommendations may vary depending on the manufacturer’s specifications and the particular turbocharger design.
Temperature Range (°C) | Application Type | Recommended Viscosity (e.g., SAE) |
---|---|---|
-20°C to 40°C | Mild Conditions (Low Load) | 0W-20, 5W-30 |
40°C to 80°C | Moderate Conditions (Medium Load) | 5W-40, 10W-40 |
80°C to 120°C | High Conditions (High Load) | 15W-50, 20W-50 |
Above 120°C | Extreme Conditions (High Load, High Temp) | 20W-60, 25W-60 |
Oiling Procedures and Maintenance
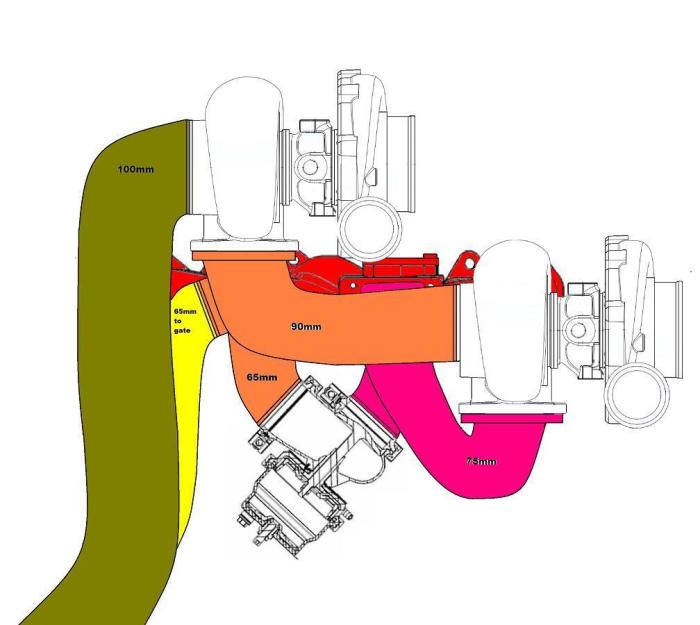
Sequential turbo setups demand meticulous oiling procedures and maintenance to ensure peak performance and longevity. Proper lubrication is critical for preventing damage to the intricate components and maintaining optimal turbocharger efficiency. Neglecting these procedures can lead to catastrophic failure, expensive repairs, and potentially hazardous situations.
Lubrication Procedure for Sequential Turbochargers
The sequential turbo system requires a dedicated oiling strategy. Oil flow must be precisely managed to ensure each turbo receives the necessary lubrication. This is typically achieved through a dedicated oil pump, ensuring consistent pressure and flow to each turbo as needed. The design of the oiling system should include bypass valves to regulate pressure and prevent damage to the turbochargers from over-pressurization or starvation.
An effective lubrication system is crucial for optimal performance and reliability.
Oil Changes and Top-Ups
Regular oil changes are paramount for maintaining the health of the sequential turbo system. Frequency is dependent on usage, environmental conditions, and manufacturer recommendations. Improper oil changes can lead to sludge buildup and component degradation. A complete oil change typically involves draining the old oil, replacing the filter, and adding the correct type and amount of fresh oil, adhering to the manufacturer’s specifications.
Top-ups should only be performed with the recommended oil grade to avoid performance issues or damage.
Importance of Regular Oil Analysis
Regular oil analysis provides valuable insights into the health of the sequential turbo system. Oil samples can reveal the presence of contaminants, wear particles, or other anomalies. These analyses provide a crucial diagnostic tool, helping to detect potential issues before they escalate into costly repairs or complete system failure. The data obtained allows for proactive maintenance, preventing costly repairs and maintaining consistent performance.
Maintenance Checks for the Oiling System
Thorough inspection of the oiling system is crucial. Visual inspections of oil lines, filters, and pumps should be performed regularly to identify any leaks, blockages, or other abnormalities. Checking the oil pressure gauge regularly and comparing readings to manufacturer specifications can reveal issues. Proper functioning of the bypass valves should also be checked. Monitoring the oil pressure ensures adequate lubrication.
Step-by-Step Procedure for Oiling the Sequential Turbo Setup
- Verify the vehicle is off and safely parked. Ensure the parking brake is engaged.
- Locate the oil drain plug and carefully position a suitable container to collect the old oil. Allow sufficient time for draining.
- Replace the oil filter, ensuring it is correctly installed.
- Carefully add the recommended type and quantity of fresh oil to the system.
- Verify the oil level using the dipstick, ensuring it’s within the manufacturer’s specifications.
- Start the vehicle and allow it to idle for a few minutes to ensure the oil circulates through the system.
- Check for any leaks or unusual noises. If issues arise, immediately stop the vehicle and investigate.
- Perform a thorough inspection of the oiling system components, checking for any damage, leaks, or unusual signs.
Troubleshooting Common Oil Issues
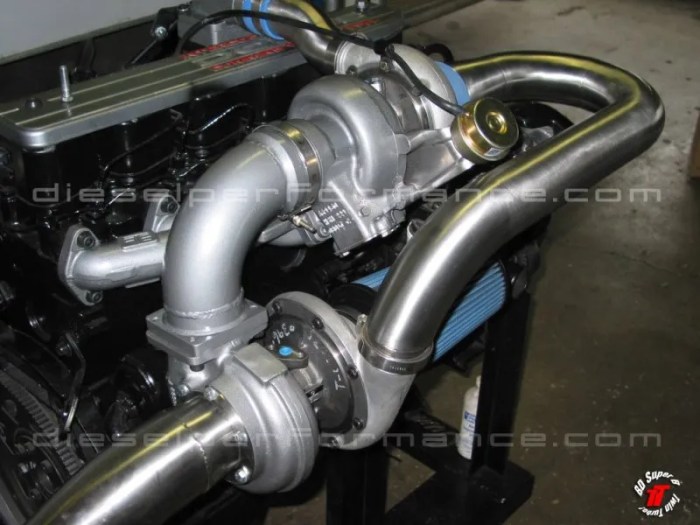
Sequential turbo setups, while powerful, demand meticulous oil management. Problems can arise, impacting performance and potentially damaging components. Addressing these issues proactively is crucial for longevity and optimal operation.
Identifying Low Oil Pressure
Low oil pressure in a sequential turbo system is a critical issue. Several factors can contribute, from a failing oil pump to restricted oil passages. Diagnosing the root cause is essential to implement the correct fix. A low oil pressure reading on your gauge, combined with unusual noises or vibrations, often signals a problem.
- Inspecting the Oil Pump: A worn-out or failing oil pump is a common culprit. Symptoms often include a noticeable drop in pressure, especially under load. Replacing the oil pump is typically the solution, requiring specialized tools and potentially significant labor.
- Checking Oil Filter Restriction: A clogged oil filter can impede oil flow, leading to low pressure. Regular filter changes are paramount. Clogged filters are a common issue, easily remedied by replacement.
- Evaluating Oil Viscosity: Incorrect viscosity can hinder oil flow. Using oil outside the recommended range can result in pressure issues, especially in extreme temperatures. Use the correct oil grade specified by the manufacturer.
- Assessing Oil Level: Insufficient oil level is another cause. Low oil level directly impacts pressure, potentially causing damage to bearings and components. Checking and topping up the oil level is a straightforward preventative measure.
Diagnosing Oil Leaks
Leaks in the sequential turbo’s oiling system can significantly reduce oil volume, eventually leading to low pressure and potential damage. Systematic inspection is vital to pinpoint the leak’s source.
- Visual Inspection: A thorough visual inspection of all oil lines, connections, and components is the initial step. Look for drips, puddles, or oil residue around components, especially those with high stress points. Oil leaks can manifest in several areas.
- Tracing Oil Leaks: Following the oil lines visually or with a leak detection dye can help locate the source. Using a leak detection dye can make finding the leak more efficient and accurate.
- Pressure Test: A pressure test of the oiling system can pinpoint leaks by detecting pressure drops. Pressure testing allows you to isolate areas with compromised seals or connections.
Troubleshooting Table
Problem | Cause | Solution |
---|---|---|
Low Oil Pressure | Clogged oil filter, worn oil pump, incorrect oil viscosity, insufficient oil level | Replace oil filter, replace oil pump, use correct oil viscosity, check and top up oil level |
Oil Leaks | Damaged seals, loose connections, worn oil lines | Replace damaged seals, tighten loose connections, replace worn oil lines |
Oil Delivery and Pressure Control
Precise oil delivery and pressure control are critical for sequential turbo setups. Proper pressure ensures lubrication of the turbocharger components, preventing premature wear and maximizing performance. Variations in pressure can lead to reduced efficiency and potentially damage the system. Understanding the methods for regulating oil pressure is key to maintaining a healthy and high-performing turbo setup.
Oil Pump Types and Functions
Sequential turbo setups rely on dedicated oil pumps to supply oil to each turbocharger. These pumps are typically high-pressure gear pumps, delivering the required oil volume and pressure to the turbochargers under varying engine loads. Different pump designs cater to specific performance needs. For example, some setups use variable displacement pumps to adapt to changing engine demands.
Oil Pressure Regulators
Oil pressure regulators play a crucial role in maintaining consistent oil pressure across the system. They precisely control the flow of oil, ensuring that the pressure remains within the optimal range for each turbocharger. These regulators often incorporate pressure sensors and solenoids to adjust the oil flow in response to changes in the system. This precise control prevents excessive pressure buildup, which can damage components, and ensures adequate lubrication under all operating conditions.
Oil Pressure Sensors and Their Function
Oil pressure sensors are integral to the regulation process. They monitor the oil pressure within the system and relay this information to the engine management system (EMS). The EMS uses this data to adjust the oil flow rate through the regulators, ensuring that the pressure remains within the predetermined parameters. Failure of the pressure sensor or incorrect readings can lead to erratic performance or potential damage.
Oil Delivery Flowchart
- Engine oil is drawn from the oil pan via the main oil pump.
- The main oil pump pressurizes the oil, ensuring adequate pressure to meet the demands of the system.
- The oil is routed through dedicated oil lines to each sequential turbocharger, ensuring consistent flow and pressure to each turbine.
- Pressure sensors monitor the oil pressure at each turbocharger.
- The EMS receives data from the pressure sensors and adjusts the flow through oil regulators to maintain the desired pressure.
- Oil returns to the oil pan after performing its function, completing the loop.
Oil Cooling and Filtration: How To Oil A Sequential Turbo Setup
Maintaining optimal oil temperature and cleanliness is crucial for the longevity and performance of a sequential turbo setup. Excessive heat degrades oil viscosity and performance, potentially leading to premature wear on components. Conversely, clean oil ensures smooth operation and prevents the build-up of contaminants that can clog passages and hinder the efficiency of the system.
Importance of Oil Cooling
High-performance sequential turbo setups generate significant heat during operation. This heat is transferred to the oil, potentially leading to thermal breakdown of the oil molecules. Maintaining an optimal oil temperature range ensures the oil retains its lubricating properties and viscosity, protecting components from wear and tear. Oil coolers effectively dissipate this heat, preventing thermal degradation and enhancing the system’s overall reliability.
Oil Cooling Methods
Oil coolers are the most common method for cooling the oil in sequential turbo systems. These coolers use a heat exchanger, often employing a finned design, to transfer heat from the oil to a coolant medium (typically air or water). The efficiency of the cooler depends on factors like surface area, flow rate, and the difference in temperature between the oil and the coolant.
- Air-to-Oil Coolers: These are typically used in applications with readily available air, such as open-air environments. They are often cost-effective and relatively simple to install. However, their cooling capacity is limited compared to water-to-oil coolers.
- Water-to-Oil Coolers: These utilize a closed-loop water system to cool the oil. They offer higher cooling capacity than air-to-oil coolers, making them suitable for high-performance applications and demanding operating conditions. Water-to-oil coolers are typically more complex to install and maintain.
Oil Filtration
Maintaining a clean oil system is paramount for the longevity of the sequential turbo system. Particles, contaminants, and debris can accumulate in the oil over time, potentially leading to mechanical failures and performance issues. A robust filtration system effectively removes these contaminants, ensuring optimal lubrication and reducing wear on moving components.
Types of Oil Filters
Sequential turbo systems employ various oil filters, each designed for specific applications and performance requirements.
- Spin-on Filters: These are commonly used and provide a simple method for filtering the oil. Their ease of replacement makes them a popular choice for maintenance.
- Cartridge Filters: These filters are often employed in more complex systems, providing a higher level of filtration than spin-on filters. They are often more difficult to replace and require specific tools for servicing.
- In-Line Filters: These filters are placed directly in the oil circuit, ensuring constant filtration of the oil as it flows through the system. This approach can provide better protection against contaminants.
Oil Cooling Solution Comparison
The choice of oil cooling solution depends on the specific application and the desired level of performance. A comparison of common solutions reveals that water-to-oil coolers generally provide superior cooling capacity, making them suitable for high-performance applications. Air-to-oil coolers, while more cost-effective, may not offer the same level of cooling in demanding conditions.
Cooling Solution | Efficiency | Cost | Complexity |
---|---|---|---|
Air-to-Oil | Moderate | Low | Low |
Water-to-Oil | High | Medium | Medium |
“Proper oil cooling and filtration are critical for the reliable and long-lasting operation of a sequential turbo setup.”
Advanced Considerations for Specific Applications
Optimizing sequential turbo oiling systems demands careful consideration of specific application needs. High-performance setups, extreme operating conditions, and unique engine designs all influence the oiling strategy. Understanding these nuances is crucial for reliable and long-lasting performance.
Variations in Oiling Procedures for Different Applications
Different sequential turbo setups, from everyday performance cars to high-performance racing engines, require tailored oiling procedures. For example, a street-driven car might utilize a simpler oiling system with less emphasis on extreme pressure or high-temperature protection. However, a high-performance racing engine needs a more robust system capable of handling significantly higher pressures and temperatures. This involves specialized oil coolers, higher-viscosity oils, and precise pressure control mechanisms.
Impact of Engine Operating Conditions on the Oiling System
Engine operating conditions significantly impact the oiling system’s performance. High RPM operation generates greater shear forces on the oil, demanding a higher viscosity grade to maintain adequate film strength. Similarly, high boost pressures necessitate oil pumps capable of delivering adequate volume and pressure to the turbochargers and engine components. Additionally, prolonged high-temperature operation requires a sophisticated cooling system to prevent oil degradation.
Special Considerations for Maintaining Oiling in Extreme Environments
Extreme environments, such as high altitude or desert conditions, can impact the oiling system’s performance. Reduced atmospheric pressure at high altitudes can lead to lower oil boiling points, demanding specialized oil additives and/or a more robust cooling system. Similarly, extremely high temperatures in desert climates require advanced oil coolers and potentially the use of synthetic oils with superior thermal stability.
In these scenarios, proper oil filtration becomes paramount to maintain cleanliness and avoid performance issues.
Examples of Different Sequential Turbo Setups and Their Unique Oiling Requirements
A common sequential turbo setup in a high-performance street car might use a high-flow oil pump, a dedicated oil cooler, and a pressure regulator. In contrast, a racing application with extreme boost levels and higher operating temperatures could require a high-volume oil pump with multiple oil coolers, specialized oil filters, and an advanced pressure control system to ensure consistent oil delivery and pressure regulation.
Comparison Table of Oiling Requirements for Various High-Performance Sequential Turbo Setups, How to oil a sequential turbo setup
Sequential Turbo Setup | Oil Viscosity | Oil Pump Type | Oil Cooler(s) | Pressure Control System | Other Considerations |
---|---|---|---|---|---|
Street Performance (High Boost) | 5W-40 or 10W-60 synthetic | High-flow gear pump | One or two dedicated oil coolers | Pressure regulator with bypass | Oil filter with high-flow rating |
Race Car (Extreme Boost) | 10W-60 or 15W-60 synthetic | High-volume electric pump with multiple outlets | Multiple oil coolers with integrated heat exchangers | Dual pressure regulators with adjustable bypass valves | Oil analysis monitoring, specialized oil additives |
Off-Road (High Temperatures) | 15W-50 or 20W-50 synthetic | High-flow gear pump with thermal protection | Dual oil coolers with bypass systems | Pressure regulator with thermal compensation | High-temperature-resistant oil additives |
Last Point
In conclusion, mastering how to oil a sequential turbo setup requires meticulous attention to detail. Proper oil selection, component understanding, and consistent maintenance are key to maximizing performance and extending the lifespan of your system. Remember, the right oiling strategy is crucial for reliable and efficient operation.
Answers to Common Questions
What are the typical applications of sequential turbo setups?
Sequential turbo setups are often found in high-performance vehicles and applications requiring high torque across a wide range of RPMs, such as trucks and some sports cars.
What’s the difference between sequential and parallel turbocharging?
Sequential systems use multiple turbochargers, activating them in stages to enhance torque across a wider RPM range. Parallel systems use multiple turbos simultaneously, often offering better low-end torque.
What are some common oiling problems in sequential turbo systems?
Low oil pressure, leaks, and incorrect oil viscosity are some common problems. Insufficient oil cooling can also lead to overheating.
How often should I perform oil analysis on my sequential turbo system?
Regular oil analysis is essential for monitoring the health of the system. The frequency depends on operating conditions and manufacturer recommendations, but monthly checks are a good starting point.