How long does it take driveway sealcoating to dry? Understanding the drying process is crucial for achieving a durable and long-lasting driveway. Factors like temperature, humidity, and the type of sealer significantly impact the time it takes for the sealant to fully cure. Proper drying is essential for avoiding premature traffic, ensuring optimal performance, and preventing potential issues like cracking or bubbling.
This comprehensive guide delves into the intricacies of driveway sealer drying times, offering insights into the various stages, safety precautions, and troubleshooting techniques. We’ll explore the effects of environmental conditions, sealer types, and application methods on the drying process. Furthermore, we will examine how drying time relates to the overall quality and longevity of the sealed surface.
Factors Affecting Drying Time
Driveway sealer drying time is a crucial aspect of the application process. Understanding the factors that influence this time is essential for achieving a durable and aesthetically pleasing finish. Optimizing drying conditions minimizes the risk of issues like uneven curing or premature traffic.
Environmental Conditions
Environmental conditions significantly impact the drying time of driveway sealer. Temperature and humidity play key roles in evaporation rates, affecting the time it takes for the sealer to reach its final, hardened state. Wind also influences the drying process, as it can accelerate the evaporation of solvents, leading to faster drying but potentially uneven curing.
- Temperature: Higher temperatures generally lead to faster drying times, as the increased heat accelerates the evaporation of the solvents in the sealer. Conversely, cooler temperatures can significantly slow down the drying process. For example, a sealer applied on a hot summer day might dry in a few hours, while the same sealer applied on a cool spring evening could take several days to cure completely.
- Humidity: High humidity can hinder the drying process by increasing the moisture content in the air. This moisture competes with the sealer’s solvents for evaporation, thus increasing the drying time. In contrast, low humidity facilitates faster drying. For instance, a sealer applied in a dry desert climate will likely dry more quickly than the same sealer applied in a humid coastal area.
- Wind: Wind can accelerate the evaporation of solvents in the sealer. While this can speed up the drying time, strong winds can also lead to uneven drying, creating areas that cure more quickly than others. This uneven drying can lead to a less durable and potentially aesthetically displeasing finish. Consider the wind conditions when scheduling your sealing project to minimize the effects of strong winds.
Sealer Type
The type of sealer used directly impacts its drying time. Solvent-based sealers typically dry faster than water-based sealers due to the quicker evaporation of their solvents. However, water-based sealers often provide a longer lasting protection, though they require longer drying times.
- Solvent-based sealers: These sealers generally dry quickly, often within a few hours in ideal conditions. This speed is often advantageous for projects where time is a factor. However, the rapid drying can also lead to more volatile fumes and may not be as environmentally friendly as water-based sealers.
- Water-based sealers: Water-based sealers, conversely, dry more slowly. This slower drying time is usually offset by a longer-lasting protection, as well as a lower impact on the environment. It is common for water-based sealers to require a few days to dry fully.
Application Thickness
The thickness of the sealer application significantly affects the drying time. A thicker application will take longer to dry completely than a thinner one, as the sealer has a larger volume to evaporate. The application method also plays a role. Different application methods can influence the uniformity of the sealer’s application, which in turn can affect drying time.
- Application Thickness: A thicker application creates a larger volume of sealer that needs to dry. This requires more time for the solvents to evaporate, leading to a longer drying period. Conversely, a thin application dries more quickly.
- Application Methods: Spraying the sealer often leads to a thinner application compared to using a roller. Spray application can result in faster drying times because the sealer is distributed more thinly. However, the spray method can also result in uneven application and potential pooling, which can negatively impact drying time and the final quality of the sealer.
Comparative Drying Time Table
Sealer Type | Temperature (°C) | Humidity (%) | Estimated Drying Time (Hours) |
---|---|---|---|
Solvent-based | 25 | 40 | 4-6 |
Solvent-based | 35 | 80 | 8-12 |
Water-based | 20 | 60 | 24-48 |
Water-based | 30 | 40 | 16-24 |
Drying Time Stages
Understanding the different stages of driveway sealer drying is crucial for preventing premature traffic and ensuring a long-lasting, well-maintained surface. Each stage presents distinct characteristics and visual cues that allow homeowners and contractors to assess the appropriate time for traffic resumption and other activities.A comprehensive understanding of these stages helps to avoid potential issues like cracking or damage to the newly sealed surface, and contributes to the overall satisfaction with the sealing process.
Careful observation during each stage ensures a high-quality result.
Initial Drying and Solidification
The initial stage following application involves the sealer forming a thin, slightly tacky film on the surface. This is a critical stage where the sealer begins its bonding process with the existing pavement. The sealer is still in a semi-liquid state and will adhere strongly to the surface when it is sufficiently cured.
Identifying the Completion of this Stage
The initial drying stage is typically characterized by the reduction of tackiness. The surface will no longer stick to the touch. A light touch should not leave a residue on the sealer. This is the key indicator that the surface is ready to progress to the next stage. The duration of this stage can vary significantly based on environmental factors.
Intermediate Drying and Solidification
As the sealer continues to dry, it transitions from a slightly tacky film to a more robust, solid layer. This stage marks a significant shift in the sealer’s physical properties. The sealer will start to harden and develop strength, providing more resistance to the elements. It’s important to recognize that this stage is crucial to the long-term performance of the seal coating.
Identifying the Completion of this Stage
The intermediate drying stage is typically characterized by a noticeable increase in the sealer’s hardness. The surface will feel significantly less sticky or tacky to the touch, and it will show increased resistance to pressure. Avoidance of any premature traffic is essential to prevent damage during this stage.
Final Curing and Hardening
The final stage of the drying process is characterized by the sealer achieving its full cure. This is where the sealer develops its maximum strength and resistance to external factors. The surface will become completely hardened and ready for normal traffic. A crucial aspect of this stage is achieving full penetration and bonding.
Identifying the Completion of this Stage
The final curing stage is characterized by a completely hard and unyielding surface. The surface will resist indentation or scratching, and it will exhibit a high level of elasticity, showing resilience to the impact of traffic and weather conditions. At this point, the sealer has achieved its full bonding potential.
Drying Time Stages: A Step-by-Step Guide
- Initial Drying (0-24 hours): The sealer forms a thin, slightly tacky film. Visual cue: Reduced tackiness, no stickiness to the touch. Expected duration: Varies significantly, typically from a few hours to a day. Avoid any traffic or heavy use during this period.
- Intermediate Drying (24-72 hours): The sealer transitions to a more robust, solid layer. Visual cue: Increased hardness, noticeable resistance to pressure. Expected duration: Typically 1-3 days. Avoid traffic to prevent potential damage.
- Final Curing (72+ hours): The sealer achieves its full cure, becoming fully hardened and resistant to external factors. Visual cue: Completely hard, unyielding surface, resistance to indentation or scratching. Expected duration: Usually 3+ days, depending on environmental conditions and sealer type. Normal traffic is permitted after full cure.
Safety Precautions During Drying
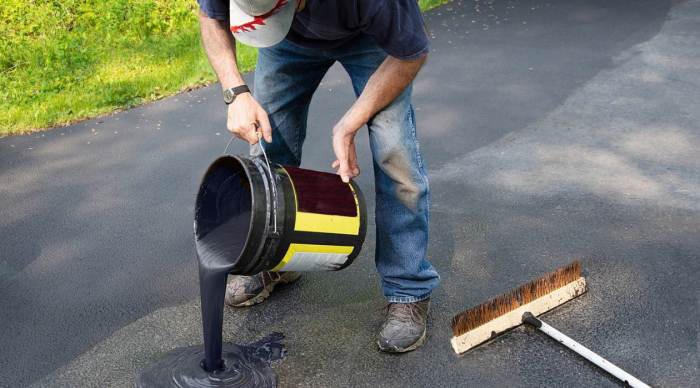
Ensuring the safety of those involved in driveway sealing is paramount. Proper precautions during the drying phase are crucial to minimize potential hazards and ensure a smooth, incident-free process. Following these safety measures helps prevent accidents and allows for a more efficient and responsible approach to the task.Understanding the potential hazards associated with the sealer’s drying process is essential for proactive safety measures.
These hazards, though often subtle, can lead to discomfort or injury if not anticipated and addressed. A thorough understanding of these potential issues allows for the development and implementation of preventative measures.
Safety Measures During the Drying Phase
Proper safety precautions during the drying period are essential to protect workers and the public. These measures not only mitigate risks but also ensure a more controlled and efficient application process. Understanding the importance of these measures helps in creating a safe environment for all involved.
- Protective Gear: Workers should consistently wear appropriate personal protective equipment (PPE) throughout the entire sealing process, including but not limited to, safety glasses, gloves, and respirators. This is critical for preventing skin contact and inhalation of potentially harmful fumes. Suitable footwear should also be worn to prevent slips and falls on potentially slick surfaces.
- Air Quality Monitoring: In situations involving potentially harmful vapors or fumes, monitoring the air quality is crucial. This helps in maintaining acceptable levels and ensuring worker well-being. Regular air quality checks, including the use of air quality monitors, should be performed to identify and address any potential health risks.
- Traffic Control: To prevent accidents and ensure public safety, appropriate traffic control measures should be implemented during the drying period. This includes clearly marking the sealed area with caution tape or signage, ensuring pedestrian and vehicular traffic is appropriately managed. Restricting access to the sealed area, especially during critical drying stages, is a significant aspect of this precaution.
- Avoidance of Contact: Direct contact with the wet sealer should be strictly avoided. The sealer’s components may cause skin irritation, allergic reactions, or other adverse effects. This precaution is crucial for maintaining worker health and preventing discomfort or injury.
Handling and Applying Sealer Safely
Implementing safe handling and application procedures is critical to prevent accidents and maintain worker health throughout the entire process. These procedures are vital in minimizing the risk of exposure to hazardous materials.
- Proper Ventilation: Adequate ventilation is essential during the sealer application and drying periods. This helps to minimize exposure to potentially harmful fumes and vapors. Appropriate ventilation systems, such as fans or exhaust systems, should be employed to maintain safe air quality levels.
- Spill Prevention: Implementing measures to prevent spills is crucial. Careful handling and storage of sealer materials are necessary. Spills can lead to contamination of surrounding areas and pose risks to individuals and the environment. Quick clean-up procedures for spills should be readily available.
- Emergency Procedures: Having well-defined emergency procedures in place is crucial for addressing any unforeseen incidents. Knowing how to handle spills, contact with the sealer, or other potential emergencies is vital for ensuring the safety of workers and the public.
Impact of Drying Time on Quality: How Long Does It Take Driveway Sealcoating To Dry

Proper drying time is crucial for achieving the best possible results in driveway sealcoating. A thorough understanding of how drying time affects the long-term durability of the sealant is essential for homeowners and contractors alike. This knowledge allows for informed decisions, ensuring the driveway’s protection and longevity.The drying process significantly impacts the sealer’s ability to withstand the elements.
A proper drying time allows the sealant to cure completely, forming a strong, cohesive bond with the existing surface. This robust bond is essential in preventing premature cracking, fading, and other signs of deterioration. A thorough understanding of this crucial process is key to achieving a durable and long-lasting seal.
Long-Term Durability
Adequate drying time is paramount for the long-term durability of the sealed driveway. A properly cured sealant forms a protective barrier against the elements, including UV radiation, temperature fluctuations, and moisture penetration. This protective layer shields the underlying surface from degradation, extending the lifespan of the driveway significantly.
Resistance to Cracking, Fading, and Weathering
The sealer’s resistance to cracking, fading, and weathering is directly correlated with the drying time. Incomplete drying can lead to a weaker bond, making the sealer more susceptible to cracking under stress. Exposure to sunlight and moisture before complete curing can also accelerate fading and weathering, resulting in premature deterioration. Conversely, a complete drying process strengthens the bond, making the sealer more resilient to environmental stressors.
Optimal Performance and Consequences of Incomplete Drying
Complete drying is essential for achieving optimal performance from the driveway sealer. A completely cured sealant creates a robust, uniform surface that effectively repels water and protects against damage. This translates into a longer lifespan and reduced maintenance costs for the homeowner. Conversely, incomplete drying can lead to a range of issues, including premature cracking, peeling, and reduced water repellency.
These issues can result in costly repairs and a less attractive driveway appearance. For example, a driveway sealed in a humid climate with inadequate drying time might exhibit cracking and peeling within the first year of application. A properly cured sealer will show minimal signs of deterioration over several years.
Troubleshooting Drying Issues
Addressing potential problems during driveway sealer drying is crucial for achieving a long-lasting and aesthetically pleasing finish. Understanding the causes of these issues and employing appropriate solutions can prevent costly repairs and ensure a professional-looking result. Careful attention to environmental factors and proper application techniques are key to a successful drying process.
Common Drying Problems
Various factors can influence the drying process, potentially leading to uneven drying, bubbling, or cracking. These issues can arise from inconsistencies in application, environmental conditions, or product compatibility. Identifying the root cause is essential for implementing effective corrective measures.
Uneven Drying
Uneven drying can manifest as sections of the sealer drying at different rates. This can lead to an inconsistent finish, affecting the overall aesthetic appeal. Several factors can contribute to this issue. Insufficient sealer application or improper mixing can result in varying thicknesses, leading to differential drying times. Temperature fluctuations during the drying process can also play a significant role, with cooler areas taking longer to dry.
A thorough inspection of the application process and environmental conditions is crucial to resolve this problem.
Bubbling
Bubbling is another common problem that can occur during the sealer drying process. It appears as small pockets of air trapped beneath the sealer surface. Bubbling can arise from inadequate mixing of the sealer, which can introduce air pockets. Improper application techniques, such as applying the sealer too thickly or in overly wet conditions, can also trap air, leading to the formation of bubbles.
Addressing these factors through meticulous application and proper mixing techniques will often prevent bubbling.
Cracking
Cracking in the sealer can occur due to several factors. Improper application, such as applying the sealer too thickly, can lead to stress on the material and result in cracks. Uneven drying, as discussed earlier, can also contribute to cracking. Another important consideration is the sealer’s compatibility with the existing surface. If the sealer is not compatible with the driveway’s surface, it may not bond properly, leading to cracking over time.
Troubleshooting Table
Problem | Cause | Solution |
---|---|---|
Uneven Drying | Insufficient sealer application, temperature fluctuations, improper mixing, or variations in surface porosity | Ensure even application, monitor temperature, thoroughly mix sealer according to manufacturer instructions, and consider the surface characteristics before application. |
Bubbling | Improper mixing, applying sealer in overly wet conditions, or applying sealer too thickly | Thoroughly mix the sealer before application, ensure the surface is dry, and apply the sealer in thin, even coats. |
Cracking | Improper application (e.g., too thick a coat), incompatible sealer, or uneven drying | Apply sealer in thin coats, ensure compatibility with the existing surface, and address uneven drying concerns. Check manufacturer specifications and guidelines for appropriate application and material selection. |
Tips for Faster Drying
Enhancing the drying process of driveway sealer without compromising its quality is a crucial aspect of a successful application. By understanding and implementing these practical tips, you can achieve a quicker drying time while maintaining the sealer’s long-term effectiveness and durability. Optimizing weather conditions, efficient application techniques, and proper surface preparation are key elements in this process.Optimizing these factors allows for a quicker and more reliable curing process, ensuring a longer lifespan for the sealer.
Optimal Weather Conditions
Favorable weather significantly influences the drying time of driveway sealer. Sunlight provides essential heat, accelerating the evaporation process. A moderate temperature range, typically between 65°F and 85°F (18°C and 29°C), is ideal. Avoid applying the sealer during extremely hot or cold temperatures, as these conditions can hinder the curing process and potentially damage the sealer’s protective properties.
Wind conditions also play a role; moderate wind speeds are beneficial for evaporation, while high winds can cause uneven drying and potential issues. Humidity levels should be moderate. High humidity slows the evaporation process, prolonging the drying time.
Efficient Application Techniques, How long does it take driveway sealcoating to dry
A consistent and controlled application method is essential for faster drying. A proper application technique ensures even coverage and minimizes the thickness of the sealer applied. Using the correct application equipment, such as a spray pump or a high-quality roller, is key to achieving a uniform coat. This helps to reduce the surface area requiring drying and allows for faster evaporation.
A thin, even layer of sealer allows the sealer to dry quickly without forming potential issues such as cracking.
Proper Surface Preparation
A clean and properly prepared surface is crucial for a quicker drying time and a high-quality seal. Removing loose debris, dirt, and other contaminants from the driveway is vital. A thoroughly cleaned surface promotes even absorption and adhesion, facilitating a faster drying process. Addressing cracks and imperfections before application also contributes to a more efficient drying process.
A properly prepared surface ensures that the sealer can fully penetrate the substrate, aiding in a quicker curing process.
Recommendations for Faster Drying
- Apply the sealer in early morning or late afternoon hours to take advantage of lower sun intensity and moderate temperatures.
- Use a high-quality sealer formulated for faster drying, taking into consideration the specific requirements for your driveway type.
- Ensure the surface is completely clean and dry before applying the sealer.
- Apply a thin, even coat of sealer to minimize the amount of material that needs to dry.
- Avoid applying sealer during periods of high wind or excessive heat/cold.
- Use a professional-grade sealer applicator for even application.
Concluding Remarks
In conclusion, the drying time for driveway sealcoating is a critical aspect of the process. By understanding the various factors that influence drying time, implementing safety precautions, and addressing potential issues, homeowners and contractors can ensure a successful and durable sealcoating job. This guide provides a thorough understanding of the process, enabling informed decisions and optimal results.
Q&A
How does temperature affect the drying time of driveway sealer?
Higher temperatures generally accelerate the drying process, while lower temperatures slow it down. Extremely high temperatures can lead to rapid evaporation, potentially resulting in uneven drying. Conversely, low temperatures can hinder the curing process, potentially leading to longer drying times and increased risk of cracking.
What are the different types of driveway sealers, and how do they affect drying time?
Solvent-based sealers typically have faster drying times but may have stronger odors and potential environmental concerns. Water-based sealers often have longer drying times but are generally considered safer and more environmentally friendly. The drying time will also vary depending on the specific product formulation.
What are some common problems during the driveway sealer drying process, and how can they be addressed?
Uneven drying can result from inconsistent application or temperature fluctuations. Bubbling can be caused by trapped air or improper surface preparation. Cracking can stem from insufficient curing or temperature changes. Troubleshooting techniques often involve identifying the cause and implementing corrective measures, such as reapplying the sealer or adjusting the application method.
What are the safety precautions when handling and applying driveway sealer?
Always follow the manufacturer’s instructions and wear appropriate protective gear, including gloves, eye protection, and a mask. Avoid contact with the sealer, and ensure proper ventilation during application to minimize exposure to fumes. Dispose of materials responsibly and keep children and pets away from the treated area during the drying period.