How long does it take for window tint to cure? It’s a crucial question for any DIYer or pro tinting expert. The curing process, a chemical reaction that makes the tint stick and last, depends on a bunch of things, from the type of tint to the weather. Wanna know the exact time? Read on!
This guide breaks down the science behind window tint curing, covering everything from the initial chemical reactions to the crucial post-cure steps. We’ll explore the key factors influencing curing time, including material types, temperature, and humidity. Get ready to become a tint-curing pro!
Understanding the Curing Process: How Long Does It Take For Window Tint To Cure
Window film curing is a critical step in ensuring the longevity and performance of window tinting. Proper curing transforms the initially applied liquid film into a durable, weather-resistant, and aesthetically pleasing finish. This process involves intricate chemical reactions and careful control of environmental factors, ultimately determining the film’s performance and lifespan.The curing process of window film is not merely a drying process; it’s a complex transformation where the liquid film undergoes chemical changes, forming strong bonds and a stable structure.
These changes are influenced by several factors, including temperature, humidity, and the type of film used. Different types of films may require distinct curing conditions, reflecting the unique chemical compositions and formulations of the materials.
Chemical Reactions Involved
The chemical reactions underlying window film curing vary depending on the specific film type. Commonly, they involve the cross-linking of polymer chains. This process, often accelerated by UV light and heat, creates a strong, interconnected network that gives the film its strength and durability. For example, in some films, the curing process involves the polymerization of monomers, resulting in a three-dimensional polymer network.
Other films utilize different chemical reactions, like the formation of chemical bonds between different components of the film.
Stages of the Curing Process
The curing process typically progresses through distinct stages:
- Initial Stage: The application of the liquid film, which often involves careful spreading and even distribution to ensure uniform coverage. The liquid state of the film allows for adjustments in placement, smoothing out imperfections.
- Polymerization/Cross-linking: This stage involves the crucial chemical reactions that create the strong bonds within the film. It’s during this stage that the film transitions from a liquid to a solid state, and the strength and properties of the film are developed.
- Stabilization: The final stage involves the stabilization of the cured film. This stage ensures the film has achieved its full structural integrity and resistance to various environmental stresses. During this phase, the film is exposed to the necessary curing conditions to achieve its optimal physical properties.
Factors Influencing Curing Time
Numerous factors influence the curing time of window film, impacting the rate and completeness of the chemical reactions.
- Film Type: Different window film types have varying chemical compositions and curing requirements. Some films require longer curing times than others to achieve optimal performance. This difference in curing time arises from the specific formulations and chemical structures of the materials in the different film types.
- Temperature: Higher temperatures generally accelerate the curing process by increasing the kinetic energy of the molecules involved in the chemical reactions. Lower temperatures will slow down the curing process, potentially leading to incomplete curing or a compromised film.
- Humidity: High humidity can interfere with the curing process, particularly in some types of films. Humidity levels influence the rate at which solvents evaporate, affecting the overall curing time.
- UV Light Exposure: UV light plays a crucial role in initiating and accelerating certain curing reactions in some window film types. The intensity and duration of UV light exposure can significantly affect the curing time and the final properties of the film.
Importance of Proper Curing
Proper curing is essential for achieving the desired long-term performance characteristics of the window film. Inadequate curing can lead to reduced durability, increased susceptibility to cracking, and diminished UV protection. This highlights the need for meticulous adherence to the manufacturer’s recommendations for curing conditions.
Curing Methods
Different curing methods are employed, each with its advantages and limitations.
- Heat Curing: This method often utilizes specialized equipment to provide controlled heat to the applied film. This method is generally faster than other methods, leading to increased efficiency in installation and reducing overall project time.
- UV Curing: This method leverages ultraviolet light to initiate and accelerate the curing process. UV curing is frequently used for films that are sensitive to high temperatures, preventing potential damage or alteration of the film’s properties.
- Combined Heat and UV Curing: This method often combines the benefits of both heat and UV curing, optimizing the curing process and achieving a high level of film performance. This method is often preferred for its comprehensive approach to the curing process, leading to a more robust and durable final product.
Role of UV Light and Heat
UV light and heat play crucial roles in the curing process. UV light can initiate certain chemical reactions, while heat accelerates the rate of these reactions. The combination of both factors is frequently employed to achieve a more complete and efficient curing process. This process results in a more durable and stable film that effectively resists various environmental factors.
Factors Affecting Curing Time
The curing process of window tint, a crucial step for its long-term performance, is influenced by a variety of factors. Understanding these factors is essential for ensuring proper installation and maximizing the lifespan of the film. A thorough understanding of these influences allows installers to optimize the curing process, leading to superior adhesion and durability.The curing process, essentially the time it takes for the adhesive in the tint film to fully harden and bond to the window, is a complex interaction of material properties and environmental conditions.
Proper curing ensures a strong, lasting bond, protecting the film from peeling, bubbling, or other issues.
Different Types of Window Tint Materials and Their Curing Characteristics, How long does it take for window tint to cure
Various window tint materials exhibit differing curing rates. Metallic-infused tints, for instance, often require longer curing times compared to standard ceramic or polymer-based tints. The presence of metallic particles or special additives can influence the chemical reactions during the curing process, resulting in variations in the time required for full adhesion. The chemical composition of the adhesive layer within the film significantly affects the curing process.
Different formulations may have different reaction rates, impacting the time needed for the adhesive to reach its optimal strength.
Influence of Ambient Temperature on the Curing Process
Temperature plays a critical role in the curing process. Higher temperatures generally accelerate the chemical reactions within the adhesive, leading to a faster curing time. Conversely, lower temperatures slow down the process, requiring a longer curing period. For example, installing tint in a climate-controlled environment with consistent temperatures will lead to a more predictable and consistent curing time, whereas installation in extreme heat or cold could cause variations.
Impact of Humidity Levels on the Curing Time
Humidity levels can also impact the curing process. High humidity can sometimes interfere with the adhesive’s ability to fully dry and cure, potentially resulting in a longer curing time. This is because high humidity can lead to the presence of water molecules in the air, which can interfere with the chemical reactions needed for curing. Installing tint in a dry environment will often yield faster curing compared to installation in a humid environment.
Comparison of Curing Times for Different Tint Film Thicknesses
Thicker window tint films typically require a longer curing time than thinner films. This is because the adhesive needs more time to penetrate and fully bond to the thicker layer of the film. Increased thickness necessitates a more comprehensive and prolonged curing process. Practical examples show that thinner films often cure within a few hours, whereas thicker ones may take a day or more.
Role of Curing Time on Tint’s Adhesion and Durability
Adequate curing time is paramount for achieving optimal adhesion and durability. Insufficient curing time can result in a weak bond, making the film more susceptible to peeling or bubbling. Conversely, a longer curing time ensures the adhesive has fully reacted, resulting in a stronger, more durable bond that is resistant to environmental stress.
Examples of How Different Installation Methods Can Affect Curing
Installation methods can significantly affect the curing process. Using a proper installation technique, such as applying pressure evenly and avoiding wrinkles, can help ensure a uniform and effective curing process. In contrast, improper installation methods, such as applying uneven pressure or not using the recommended tools, may result in uneven curing or hindered adhesion. For instance, the use of specialized curing lamps or UV light exposure can speed up the process.
The proper use of these tools can influence the final results, whereas their misuse can lead to inconsistent curing times.
Curing Time Ranges
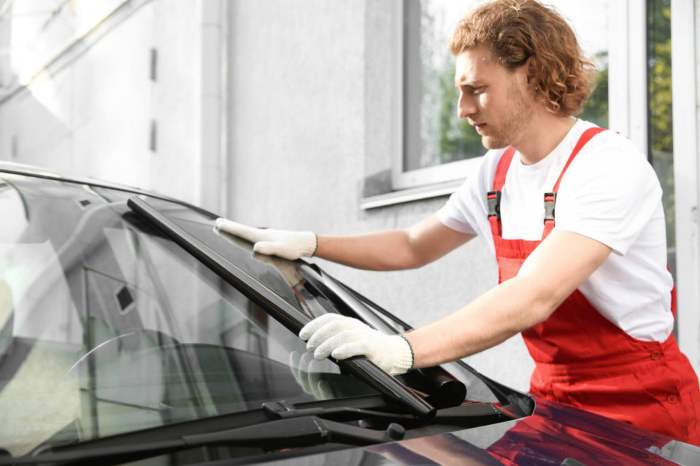
Window film curing time is a crucial aspect of installation, directly impacting the film’s long-term performance and adhesion. Understanding the varying curing times for different types of window film, coupled with the impact of environmental factors, allows installers to ensure proper adhesion and prevent potential issues down the line. This section delves into the specifics of curing times for various window film types, thicknesses, and application conditions.
Material Type-Based Curing Time Ranges
Different window film materials exhibit varying curing characteristics. This is largely due to the chemical reactions involved in the adhesive’s curing process. For example, some films use UV-cured adhesives that require specific exposure times to solidify, while others utilize solvent-based adhesives with different curing kinetics.
- Metalized Films: Metalized films, often featuring reflective properties, frequently use specialized adhesives that require extended curing times compared to standard window films. This allows for a more robust and reliable bond, particularly crucial for the long-term durability of the reflective coating. For instance, a typical metalized film may need 24-48 hours for complete cure, with variations dependent on thickness and specific adhesive formulations.
- Ceramic Films: Ceramic films, often utilized for their thermal control properties, generally have curing times similar to standard window films. However, specific formulations may have unique curing requirements, necessitating adherence to the manufacturer’s instructions for optimal results.
- Standard Window Films: Standard window films, commonly used for privacy or aesthetics, typically cure within a shorter timeframe, often within 24 hours. This allows for quicker installation turnaround times, which is a significant advantage for installers.
Estimated Curing Times for Various Window Tint Types
This table provides estimated curing times for various window tint types. Note that these are general guidelines and specific curing times may vary based on factors like film thickness, application conditions, and the specific adhesive used.
Window Tint Type | Estimated Curing Time (Hours) | Brand (Example) |
---|---|---|
Standard Solar Control | 24 | 3M |
Infrared Blocking | 24-48 | LLumar |
High-Performance Heat Rejection | 48 | SunTek |
Metalized Films (Specific Type) | 48-72 | Avery Dennison |
Curing Times Based on Application Conditions
Application conditions significantly impact the curing process. Temperature and humidity are critical factors influencing the rate of curing. High temperatures can accelerate the curing process, while low temperatures can slow it down.
- Temperature: Warmer temperatures generally accelerate the curing process, while cooler temperatures slow it down. This is particularly important for installers working in climates with varying temperatures.
- Humidity: High humidity can hinder the curing process by affecting the evaporation of solvents in solvent-based adhesives. This may necessitate adjustments to curing times or the selection of humidity-resistant adhesives.
Curing Time Comparison Across Film Thicknesses
The thickness of the window tint significantly influences the curing time. Thicker films, often featuring stronger UV protection or greater reflectivity, may require longer curing periods due to the increased material depth.
Film Thickness (mm) | Standard Solar Control Curing Time (Hours) | High-Performance Heat Rejection Curing Time (Hours) |
---|---|---|
1.5 | 24 | 48 |
2.0 | 36 | 72 |
2.5 | 48 | 96 |
Typical Curing Time Range for Window Tint
The typical curing time for window tint ranges from 24 to 72 hours, contingent on the material type, application conditions, and the specific adhesive used. Factors such as temperature and humidity can affect this range. For example, in very hot climates, the curing time might be shorter, while in very cold or humid environments, it might be longer. It is crucial to consult the manufacturer’s specifications for precise curing times.
Post-Curing Considerations

Proper post-curing is critical for achieving the desired performance and longevity of window tint. This phase, following the initial curing process, involves specific actions to ensure the adhesive bonds fully and the tint film adheres correctly to the glass surface. Ignoring these steps can lead to premature failure, uneven adhesion, and a compromised aesthetic.The window tint curing process is not simply a matter of time; it’s a delicate balance of temperature control, ventilation, and careful handling.
Understanding and implementing post-curing strategies is key to maximizing the window tint’s performance and appearance over its lifespan.
Importance of Avoiding Direct Sunlight and Heat
Direct sunlight and high temperatures significantly accelerate the curing process. While this might seem beneficial, it often leads to premature curing, resulting in potential issues like uneven adhesion, blistering, and cracking. Excessive heat can also cause the adhesive to lose its tackiness before the tint film is fully bonded, compromising the overall integrity of the installation. This is especially true for darker tints and films that absorb more solar radiation.
Steps to Ensure Proper Post-Curing Maintenance
Following installation, maintain the temperature of the treated area as closely as possible to the ambient temperature. This is achieved by minimizing direct exposure to heat sources, including direct sunlight. Ensuring proper ventilation is equally crucial. The recommended approach is to allow the window tint to cure in a shaded, well-ventilated area, preferably in a temperature range similar to the ambient temperature of the surrounding environment.
Factors Affecting the Curing Process After Installation
Several factors can affect the curing process after installation. These include ambient temperature fluctuations, humidity levels, and air circulation. For example, significant temperature fluctuations, especially in regions with large daily temperature swings, can disrupt the curing process, causing uneven adhesion and potentially damaging the tint. Similarly, high humidity can create condensation, hindering the curing process and potentially leading to water spots or other issues.
Good ventilation helps mitigate these issues.
Preventing Premature Curing or Uneven Curing
Premature curing, as discussed previously, is a result of high temperatures. To prevent this, keep the treated area shaded and avoid direct exposure to intense sunlight. Employing proper ventilation also plays a key role. Uneven curing can result from localized heat sources or inadequate ventilation. A balanced approach that includes temperature regulation, proper ventilation, and careful handling throughout the curing process is essential to ensure a consistent and optimal cure.
Best Practices for Post-Curing to Achieve Optimal Performance
For optimal performance, avoid exposing the window tint to direct sunlight or intense heat for the duration of the curing period. Use appropriate shading or protective coverings to minimize exposure. Maintaining a consistent ambient temperature and ensuring proper ventilation are crucial for a complete and even cure. In regions with high temperature fluctuations, consider adjusting the curing time accordingly.
Professional installers often provide specific post-curing instructions based on the tint type and installation conditions.
Need for Proper Ventilation During Curing
Adequate ventilation during the curing process is critical for the adhesive to cure properly. Proper ventilation removes any trapped air pockets and promotes even curing. Lack of ventilation can lead to uneven adhesion, air bubbles, and other defects in the final product. Open windows, fans, or other methods of enhancing air circulation can help ensure the curing process is successful.
Troubleshooting Curing Issues
Troubleshooting incomplete curing in window tint is crucial for achieving the desired results and longevity of the film. Identifying the root cause of issues like uneven curing or bubbling allows for targeted solutions, ultimately preventing costly reapplication or compromised performance. Proper diagnosis and effective remediation steps ensure a professional-looking finish and a long-lasting window tint installation.
Potential Causes of Incomplete Curing
Several factors can disrupt the curing process, leading to incomplete adhesion and potentially problematic results. These include improper application techniques, environmental conditions, and even the quality of the tint film itself. Understanding these contributing elements is key to effective troubleshooting.
- Inadequate Application Pressure: Insufficient pressure during application can lead to air pockets trapped beneath the film. This lack of proper contact prevents the adhesive from fully bonding to the glass surface, creating a weak bond susceptible to bubbling and peeling over time. For example, a poorly applied tint might reveal noticeable air pockets after a few weeks, as the adhesive begins to lose its hold.
- Inadequate Temperature: The ideal curing temperature for window tint is often specified by the manufacturer. Temperatures outside this range can slow or hinder the curing process, resulting in uneven curing and potentially creating imperfections. For example, working in extreme cold can significantly delay curing time, resulting in inconsistent adhesion across the window. Similarly, excessively high temperatures can cause the adhesive to cure too quickly, leading to a different type of uneven curing issue.
- Contamination: Any foreign material, such as dust, dirt, or oil, on the glass surface can prevent proper adhesion. This contamination interferes with the adhesive’s ability to bond to the glass, leading to weak spots and potential bubbling. For example, a small speck of dirt on the glass may cause a noticeable imperfection in the cured film.
- Incorrect Film Selection: Choosing a tint film not suitable for the specific application or environment can also contribute to incomplete curing. Some films may not cure properly under certain conditions, leading to problems. Incorrect film selection may lead to uneven curing patterns or premature failure of the bond.
Recognizing Signs of Incomplete Curing
Identifying signs of incomplete curing is crucial for timely intervention and preventing long-term issues. Common indicators can be observed during and after the application process.
- Bubbling: Visible air pockets trapped beneath the film are a clear sign of incomplete curing. These bubbles can be small or large, and they often indicate insufficient pressure during application or improper technique.
- Uneven Curing: Differences in the tint’s appearance or texture across the window suggest uneven curing. This could be caused by temperature fluctuations or inconsistent application pressure. For example, a section of the window might look darker or lighter than the surrounding area, indicating uneven curing.
- Peeling or Lifting: If the film starts to peel or lift from the glass, it’s a strong indication of a weak bond resulting from inadequate curing. This is often a consequence of trapped air, contamination, or improper application techniques.
- Streaking: Streaks in the tint film’s appearance can signify uneven curing or contamination that hindered proper adhesion.
Troubleshooting Steps for Curing Problems
Addressing incomplete curing issues requires a systematic approach. The following steps provide a guide for resolving common problems.
- Inspect for Contamination: Thoroughly clean the glass surface to remove any dirt, dust, or oil before applying the tint. Using a specialized cleaning solution tailored for window tint applications is recommended.
- Ensure Proper Application Techniques: Employ appropriate application tools and techniques to ensure even pressure and minimize air pockets during the installation process. Proper use of squeegees and other tools is essential.
- Control Environmental Conditions: Maintain the appropriate temperature and humidity levels as recommended by the tint manufacturer. Adjusting the environment to optimal conditions can significantly improve the curing process.
- Re-apply the Tint: In some cases, reapplying the film may be necessary if the initial application failed to achieve proper curing. Ensure that all previous steps are followed meticulously to prevent repeating the same mistakes.
Visual Representation of Curing
Window film curing, a crucial aspect of the installation process, is not just about the passage of time; it’s a dynamic transformation involving distinct stages. Understanding these stages, visually represented, allows installers to monitor the process effectively and ensure optimal adhesion and long-term performance. Visual cues provide valuable insights into the chemical reactions taking place within the film, confirming the proper curing of the adhesive layer.Visual observation of the curing process is essential for identifying any anomalies that might indicate issues or require corrective actions.
This visual representation, therefore, plays a critical role in ensuring a high-quality installation.
Stages of the Curing Process
Visual identification of the curing stages is vital for quality control and troubleshooting. Recognizing the progression of these stages allows for early intervention in case of issues. Accurate monitoring and recognition of these stages are essential to guarantee a successful curing process.
Stage | Visual Representation | Explanation |
---|---|---|
Stage 1: Initial Application | A smooth, even application of the window film, potentially with some slight tackiness. | The film is freshly applied to the window surface. The adhesive layer is initially tacky, offering a degree of adhesion. This stage is characterized by the physical contact between the film and the window, establishing the initial mechanical bond. |
Stage 2: Early Curing (Tack Free) | The film appears tack-free, with the adhesive layer no longer tacky. The film is now firmly attached to the window. | The adhesive begins to cure, transforming from a tacky state to a solid, stable bond. This stage involves the polymerization of the adhesive components, developing a robust, structural bond. The film should be firm and not easily removable. |
Stage 3: Intermediate Curing | The film exhibits a consistent, uniform appearance across the surface. The adhesive layer appears fully integrated with the window’s surface. | The curing process continues, with the adhesive layer fully penetrating and binding to the substrate. The film’s surface may exhibit a slight sheen or gloss, depending on the specific type of film. |
Stage 4: Final Curing (Complete Adhesion) | The film is fully cured and displays a completely smooth and uniform surface, showing no signs of tackiness or imperfections. | The curing process is complete. The adhesive has fully cured, forming a strong, permanent bond between the film and the window. Any residual solvents have evaporated, leaving behind a strong, durable bond. |
Curing Process with Illustrations
Visualizing the curing process with illustrations helps to comprehend the impact of different environmental factors. This is particularly helpful for installers to anticipate potential variations in curing times and adjust their approach accordingly.
Stage | Illustration (Heat Lamp Curing) | Illustration (UV Light Curing) | Environmental Considerations |
---|---|---|---|
Initial Application | Film applied evenly to the window | Film applied evenly to the window | Temperature, humidity, and airflow influence the initial adhesion. |
Early Curing | Heat lamp positioned to warm the film’s adhesive layer. | UV light source directed at the film, activating the curing agents. | Higher temperatures and direct sunlight will accelerate the curing process. |
Intermediate Curing | Heat lamp continues to maintain the temperature required for optimal curing. | UV light source continues to expose the film for proper polymerization. | Humidity can slow down the curing process by interfering with solvent evaporation. |
Final Curing | Heat lamp removed once the film is fully cured. | UV light source turned off after the film is fully cured. | Airflow can affect the rate of solvent evaporation, influencing the curing time. |
Diagram of the Curing Process
The diagram below illustrates the curing process and the interplay of environmental conditions. This graphical representation shows how various factors can affect the duration and quality of the curing process.
The curing process is highly sensitive to environmental factors.
[Diagram illustrating the curing process, with different environmental factors like temperature, humidity, and airflow, shown as influencing arrows affecting the curing time and quality. The diagram should include visual cues for different stages of curing, including examples of heat lamps and UV light positioning.]
Epilogue
So, there you have it—a complete guide to window tint curing. From understanding the process to handling potential problems, this guide gives you all the tools to get the perfect, long-lasting tint job. Remember, proper curing is key for a durable and aesthetically pleasing result. Now you can confidently tackle your next tinting project!
Question Bank
How does humidity affect curing time?
High humidity can slow down the curing process, potentially leading to weaker adhesion. Lower humidity generally speeds things up.
What if my tint bubbles after curing?
Bubbles usually indicate uneven curing. Check for trapped air during application and ensure proper ventilation during the curing phase. If the issue persists, consult a professional.
Can I use a heat lamp to speed up curing?
Using a heat lamp can help speed up curing, but it’s crucial to follow the manufacturer’s instructions and avoid overheating the tint, which could damage the film.
What’s the difference between different window tint materials?
Different materials have varying curing characteristics. Some materials cure faster than others, and the curing process may be affected by the thickness of the film.