How long does it take to build a deck? This isn’t just about lumber and nails; it’s a whole project, from initial blueprints to the final, satisfying reveal. Factors like deck size, design intricacy, and the materials chosen all play a crucial role in the overall timeline. Let’s break down the key elements that affect the construction process, from planning and design to the actual building phase.
From a simple wooden platform to a multi-level masterpiece complete with a gazebo, the construction time varies significantly. Understanding these differences will help you anticipate the timeframe and manage expectations. We’ll also explore common delays and strategies for avoiding them, ensuring your dream deck becomes a reality without unnecessary stress.
Project Scope and Factors Affecting Time
Building a deck, from a simple wooden platform to a complex multi-level structure, is a significant undertaking requiring careful planning and consideration of numerous factors. The final construction time is heavily influenced by the project’s scope, materials, and the presence of specialized features. Understanding these variables is crucial for homeowners and contractors alike to accurately estimate project completion dates and manage expectations.
Deck Size and Design Complexity
The size and design complexity of a deck are fundamental determinants of the overall construction time. A small, simple deck built from readily available materials will typically take considerably less time to construct than a large, multi-level deck with intricate features like stairs, railings, and built-in seating. Elaborate designs, incorporating features like gazebos, pergolas, or customized lighting, will invariably increase the construction duration.
Furthermore, the intricacy of the design’s architectural elements significantly influences the time needed for fabrication and assembly.
Material Selection and Availability, How long does it take to build a deck
The choice of materials plays a crucial role in determining the construction timeframe. Using readily available and readily processed materials often speeds up the process. For example, pressure-treated lumber is a common choice for its durability and speed of processing. Conversely, exotic hardwoods or custom-designed materials may necessitate more time for procurement and specialized fabrication, lengthening the overall construction period.
Furthermore, the availability of the selected materials can impact the timeframe, with delays potentially occurring if materials need to be ordered or shipped from distant locations.
Special Features and Their Impact
Incorporating special features, such as stairs, railings, built-in seating, or outdoor kitchens, will undoubtedly add to the overall construction time. The design and installation of these features require more specialized labor, potentially involving additional permits and inspections. For instance, constructing a complex staircase with intricate balustrades or a custom-designed outdoor kitchen will typically take longer than adding a simple railing.
Deck Types and Construction Timelines
Different types of decks have varying construction timelines. A simple wooden platform, often consisting of decking boards and supports, can be constructed relatively quickly. Conversely, a multi-level deck with a gazebo or pergola, requiring more complex framing, roofing, and finishing, will take considerably longer. Furthermore, the incorporation of specialized elements, like a built-in fireplace or an integrated sound system, further prolongs the project’s completion.
Average Construction Time for Different Deck Sizes
Deck Size | Materials | Complexity | Estimated Time (Weeks) |
---|---|---|---|
Small (100 sq ft) | Pressure-treated lumber, composite decking | Simple platform | 2-4 |
Medium (200 sq ft) | Pressure-treated lumber, composite decking | Simple platform with stairs | 4-6 |
Large (300+ sq ft) | Pressure-treated lumber, composite decking, concrete | Multi-level, gazebo | 6-12+ |
Potential Delays and Mitigation Strategies
Cause of Delay | Effect | Mitigation Strategies |
---|---|---|
Material shortages | Project standstill, extended timelines | Source alternative materials, secure early material orders |
Adverse weather conditions | Delayed outdoor work, potential damage to materials | Adjust work schedule, use protective coverings |
Unforeseen structural issues | Significant cost overruns, project delays | Thorough site inspections, hiring qualified inspectors |
Permitting complications | Project delays, unexpected hold-ups | Obtain necessary permits in advance, engage with local authorities early |
Labor shortages | Slowed progress, missed deadlines | Engage multiple contractors, utilize pre-fabrication |
Material Selection and Impact on Timeline
Deciding on the right materials for a deck is crucial, not just for aesthetics but also for the project’s overall timeline. The type of wood, composite, or railing material significantly influences the time needed for cutting, assembling, and installation. Choosing wisely can streamline the process and prevent costly delays.Wood types, from pressure-treated lumber to exotic hardwoods, play a significant role in construction duration.
The inherent characteristics of each material—like moisture content, density, and grain patterns—affect the cutting and shaping process. Furthermore, the complexity of the design, including the number of support beams and the intricate details of the railing, directly influences the time required.
Impact of Wood Type on Build Time
Different wood types exhibit varying levels of durability and workability, impacting the overall build time. Pressure-treated lumber, a popular choice for its resistance to rot and decay, often requires less finishing and maintenance, which can translate to a quicker installation. Cedar and redwood, known for their natural beauty and resistance to insects, typically require more time for staining or sealing, lengthening the build process.
The drying time for the wood also plays a crucial factor, and in some cases, a delay might be needed for proper drying.
- Pressure-treated lumber, due to its pre-treatment, often results in faster installation times compared to other wood types. This is because the pre-treatment minimizes the need for on-site treatments, saving valuable time.
- Cedar and redwood, owing to their natural beauty and inherent properties, often require more time for staining or sealing. These processes need careful consideration, potentially leading to delays in the project timeline.
- Exotic hardwoods, with their unique characteristics, may necessitate specialized tools and techniques, potentially leading to increased construction time.
Impact of Composite Decking Materials on Timeline
Composite decking materials, engineered from plastic and wood fibers, are gaining popularity for their low maintenance and long lifespan. The manufacturing process for composite decking is often more streamlined compared to traditional wood, allowing for faster assembly on-site. However, the specific design and complexity of the deck’s features will still affect the timeline.
- Composite decking often comes in pre-fabricated panels, reducing the amount of on-site cutting and shaping required, leading to a potentially shorter construction timeline.
- The need for specialized tools or equipment for installing composite decking can also be a factor in the overall project time.
- Composite decks might require precise measurements and fitting, potentially leading to minor delays.
Impact of Railing Material on Installation Time
The choice of railing material significantly affects the installation time. Wood railings, while visually appealing, often require more time for finishing and installation. Metal railings, on the other hand, can be faster to install but may require specialized tools and expertise. Glass railings, often used for modern designs, can be more complex to install and may involve additional safety measures, potentially leading to delays.
- Wood railings, due to their design, can be labor-intensive and require more time for finishing and installation compared to metal or glass.
- Metal railings, with their standardized components, often offer a quicker installation time compared to wood, given proper expertise.
- Glass railings, while visually appealing, may require specialized installation techniques and safety considerations, increasing the overall installation time.
Planning and Design Considerations
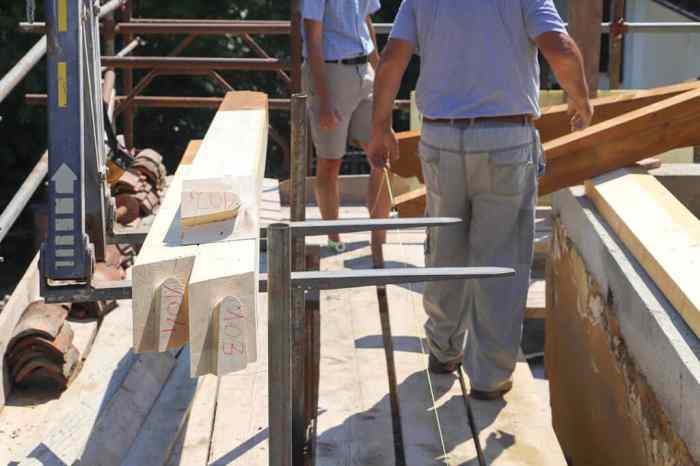
Careful planning is crucial for a successful and timely deck construction project. Thorough pre-construction steps minimize potential delays and ensure the final product meets the homeowner’s vision. Understanding the intricate interplay between design, site preparation, permitting, and subcontractor coordination directly affects the project’s overall duration.
Essential Planning Steps
A well-defined plan is the bedrock of any successful deck construction. Key planning steps significantly impact the project timeline. These steps include detailed site surveys, accurate measurements, and a comprehensive design that accounts for local building codes and regulations. A detailed plan allows for better resource allocation, efficient material procurement, and a more precise timeline for each phase of the project.
- Detailed Site Surveys and Measurements: Accurate site surveys and measurements are essential for proper design and construction. A professional surveyor or contractor can identify any challenges or obstacles on the property, such as uneven terrain, utilities, or existing structures. Precise measurements ensure the deck’s dimensions conform to the homeowner’s specifications and local building codes. A site survey also aids in accurate cost estimation, as the true extent of work becomes clear, minimizing future surprises.
- Comprehensive Design and Drawings: A detailed design plan, including blueprints and specifications, ensures all elements of the deck are precisely planned. This plan must address aspects like structural support, railing design, material choices, and connections to the house. Clear and comprehensive drawings facilitate communication between the homeowner, the contractor, and any subcontractors involved, reducing misunderstandings and potential delays. Well-defined plans lead to fewer on-site adjustments, contributing to a smoother construction process.
- Building Code Compliance: Understanding and adhering to local building codes is paramount. Building codes dictate safety standards, structural requirements, and accessibility guidelines for decks. Consulting with local authorities and incorporating code requirements in the design phase will prevent costly and time-consuming revisions later in the process. Failure to comply can result in delays or even project rejection, incurring further costs and time.
Site Preparation and Measurements Impact
Proper site preparation and accurate measurements are foundational to a timely construction process. These elements directly influence the construction timeline by reducing the risk of unexpected issues and delays.
- Impact of Uneven Terrain: Uneven terrain requires more extensive site preparation, including grading, leveling, and potentially reinforcing the foundation. If these issues are not identified and addressed during the initial survey, they can significantly prolong the construction process. Proper site preparation, with precise grading and leveling, ensures the deck is stable and built to last.
- Accurate Measurements: Inaccurate measurements can lead to material waste, costly adjustments, and delays in construction. A professional surveyor or contractor can guarantee accurate dimensions, reducing the likelihood of errors that affect the timeline and the overall budget. Measurements must align with the structural calculations to avoid any unforeseen problems.
Impact of Permits and Inspections
Obtaining necessary permits and undergoing inspections are integral parts of the construction process. Delays in these processes can have a cascading effect on the entire project timeline.
- Permitting Process Time: The time taken to obtain building permits varies depending on local regulations and the complexity of the project. The homeowner can streamline this process by providing complete and accurate information to the relevant authorities, including necessary documentation. Anticipating potential delays and having alternative plans for potential roadblocks is key.
- Inspection Requirements: Inspections ensure the construction complies with local building codes and safety standards. The frequency and duration of inspections are determined by local regulations. Understanding these requirements and coordinating with the inspector can help minimize disruptions to the construction schedule.
Impact of Subcontractors
Hiring subcontractors can streamline the project but requires careful planning and coordination. Their impact on the overall timeline is significant, particularly concerning permitting and scheduling.
- Subcontractor Coordination: Proper coordination with subcontractors is essential for a smooth workflow. Clear communication regarding timelines, responsibilities, and deadlines helps avoid conflicts and delays. A well-defined project schedule and clear communication channels with all subcontractors ensure everyone works together toward a shared goal.
- Permitting and Scheduling Coordination: Subcontractors involved in the project may have their own permitting requirements. Coordinating these requirements with the main contractor’s schedule can affect the overall project timeline. To minimize potential delays, all subcontractors should be made aware of the overall schedule, permitting requirements, and project deadlines.
Construction Methods and Techniques
Deciding on the appropriate deck-building technique is crucial for a successful project, directly impacting the overall timeline and budget. Factors such as the chosen materials, site conditions, and the desired aesthetic play significant roles in selecting the optimal method. Different approaches offer varying degrees of complexity and speed, which must be carefully considered to ensure a project stays on track.
Comparison of Deck-Building Techniques
Various techniques influence the construction timeline and final cost. Post-and-beam construction, often favored for its robust design, involves supporting the deck with vertical posts and horizontal beams. Ledger board methods, typically employed for attaching decks to existing structures, are simpler but may require more site preparation. These methods, along with other techniques, require careful planning and material selection to meet the specific needs of each project.
Impact of Prefabricated Components
Prefabricated deck components, such as pre-cut lumber and pre-assembled railings, are gaining popularity. Their use significantly reduces on-site labor and potential delays, often leading to a shorter construction timeline. Prefabricated elements usually involve precise measurements and pre-assembly, minimizing errors and wasted time. However, the cost of these prefabricated components must be weighed against the potential for faster construction.
Timeline for Different Framing Methods
The construction timeline varies based on the framing method employed. A post-and-beam deck, due to its more complex framework, generally takes longer to construct than a ledger board deck. Estimating the exact time for each method depends on factors such as the size of the deck, the complexity of the design, and the availability of materials and labor.
For instance, a 10×12 post-and-beam deck might take 5-7 days for framing alone, whereas a comparable ledger board deck could be completed in 3-5 days.
Typical Deck Construction Process
The deck construction process follows a series of steps, each with an approximate duration. These steps can be broadly categorized as follows:
- Site Preparation (1-3 days): This involves clearing the area, leveling the ground, and installing necessary utilities. The exact duration depends on the size and condition of the site, potentially requiring additional time for site remediation or excavation.
- Framing (2-7 days): This is the crucial phase where the deck’s structure is built. The time required depends on the chosen framing method, the size of the deck, and the complexity of the design. For example, a larger deck with intricate support systems will take longer to frame.
- Decking Installation (1-5 days): This involves laying the decking boards. The duration depends on the type of decking material, the size of the deck, and the skill of the installers.
- Railing Installation (1-3 days): This step involves installing railings, typically after the decking is complete. The complexity of the railing design will impact the duration.
- Finishing (1-2 days): This includes tasks like sealing the deck and adding any finishing touches. The time needed will depend on the specific finishing tasks.
Labor and Staffing Considerations: How Long Does It Take To Build A Deck
Deciding on the right labor force is critical for a deck construction project. The availability and skill level of the workforce, along with the need for specialized contractors, directly impacts the project’s duration and overall cost. Unexpected delays, often stemming from weather or scheduling conflicts among tradespeople, can significantly alter the original timeline. Understanding these factors allows for proactive planning and mitigation strategies.
Impact of Labor Availability and Skill Level
The availability of skilled labor in a given area can significantly influence the project timeline. Regions with a high demand for construction workers might face shortages, leading to delays as the contractor struggles to find suitable candidates. The skill level of the crew also plays a crucial role. A team with extensive experience in deck construction will likely complete tasks more efficiently, minimizing potential errors and accelerating the project’s progress.
Conversely, a less experienced crew may require more supervision, increasing the overall project duration. In some cases, this might even necessitate additional training or a longer period for quality control.
Influence of Specialized Contractors
Hiring specialized contractors, such as carpenters, electricians, or plumbers, can significantly impact the project duration. Each trade has unique requirements, including specific licensing, permits, and specialized equipment. Scheduling these contractors to work harmoniously and avoid conflicts is crucial. A skilled project manager can streamline the process, ensuring efficient coordination between different trades. Delays can arise if specialized contractors are unavailable or if scheduling conflicts arise, which can impact the entire project’s timeline.
For instance, a delay in obtaining necessary electrical permits can delay the entire installation process.
Weather-Related Delays
Weather conditions can create substantial delays in deck construction. Rain, strong winds, or extreme temperatures can halt work, potentially delaying the project for days or even weeks. Properly considering weather patterns in the region and the project timeline is critical. Construction schedules should incorporate buffer time to account for unforeseen weather events. The project’s design and materials must also be weather-resistant.
For instance, a project scheduled for the rainy season may require indoor work to protect the deck materials.
Coordination of Multiple Trades
Coordinating multiple trades, such as plumbers, electricians, and landscapers, is essential for a smooth project. Each trade has specific timelines and tasks that must be executed in a coordinated manner. Scheduling conflicts between different trades can lead to delays. An effective project manager can mitigate these risks through meticulous scheduling, clearly defined responsibilities, and constant communication between trades.
For instance, a delay in the plumbing work can disrupt the electrician’s schedule, leading to cascading effects throughout the project. To avoid such scenarios, a detailed schedule with overlapping tasks, including buffer time, is essential.
Real-World Examples
Deck construction projects vary widely in scope, from simple additions to elaborate designs. Understanding the real-world application of these factors is crucial for accurate estimations and successful project completion. This section delves into specific examples, highlighting successful and less-successful projects, to provide a practical understanding of the entire process.
Case Studies of Deck Projects
Real-world deck projects offer valuable insights into the complexities of construction. The scope, materials, and timelines can vary dramatically, influenced by design choices, site conditions, and contractor expertise. Examining these projects provides a practical perspective on the factors that impact project outcomes.
- Project A: A homeowner commissioned a 12×16-foot wooden deck addition. The project utilized pressure-treated lumber for the framing and composite decking for the surface. The project spanned 10 weeks, including permit acquisition, material delivery, and construction. This project demonstrated a relatively straightforward build with a predictable timeline, due to the clear scope and uncomplicated design.
- Project B: A homeowner sought a complex, multi-level deck with intricate railing designs and a pergola. The project used composite decking, steel framing, and exotic hardwoods for the railings. The project timeline stretched to 16 weeks due to the intricate design, specialized materials, and the need for precise craftsmanship.
- Project C: This project involved a deck renovation incorporating a hot tub. The scope included removing an existing deck, installing new supports, and running electrical for the hot tub. The original estimate was 8 weeks, but unforeseen issues with the existing foundation extended the project to 12 weeks. This illustrates how unexpected site conditions can significantly impact the timeline.
Delayed Deck Project Case Study: Project D
Project D, a 15×20-foot deck with a custom railing system, faced delays due to several factors. The initial estimate was 12 weeks, but it extended to 18 weeks.
- Unforeseen Soil Conditions: Subsurface issues were discovered during excavation, requiring additional reinforcement and redesign, delaying the project by 4 weeks.
- Material Shortages: Unexpected delays in the delivery of custom railing materials extended the timeline by 2 weeks.
- Contractor Scheduling Conflicts: The contractor experienced conflicts with other projects, impacting the availability of skilled labor and pushing the completion date back by 2 weeks.
The project taught valuable lessons, including the importance of thorough site assessments, contingency planning for material delays, and the necessity of clear communication between the homeowner and contractor.
Estimating Deck Construction Costs
Accurate cost estimation is essential for budgeting and managing project expectations. The following table Artikels the factors impacting cost and provides an example of an estimated cost for a 10×12-foot deck using pressure-treated lumber and composite decking.
Factor | Description | Estimated Cost (USD) |
---|---|---|
Materials | Pressure-treated lumber, composite decking, fasteners, and hardware | $3,500 |
Labor | Carpenter labor, including framing, decking, and railing installation | $4,000 |
Permitting | Obtaining necessary permits and inspections | $200 |
Contingency | Buffer for unexpected costs or delays | $500 |
Total Estimated Cost | $8,200 |
Note: Costs are estimates and can vary based on location, material quality, and labor rates.
Deck Construction Timeline
A visual representation of a typical deck construction timeline helps illustrate the various stages and expected durations.
[A visual representation of a timeline would be displayed here. This would include phases like site preparation, framing, decking, railing installation, and final inspection. Each phase would be labeled and have an estimated duration.]
Ending Remarks
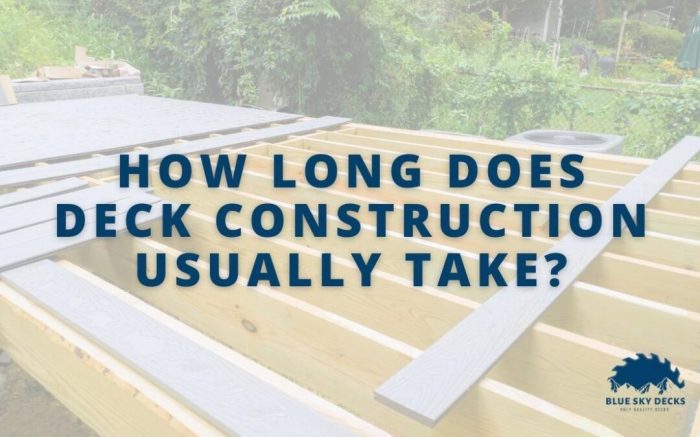
Building a deck is a rewarding project, but knowing the expected timeline is crucial. This guide has illuminated the key factors influencing construction duration, from material selection to labor considerations. By understanding these variables, you can better estimate the time required and proactively address potential delays. Remember, a well-planned project is a project completed on time and within budget.
Now, go forth and build your dream deck!
Question Bank
How much does a deck cost, on average?
Average deck costs vary widely depending on size, materials, and complexity. Expect to see prices ranging from a few thousand to tens of thousands of dollars. Detailed quotes from contractors are essential for accurate cost estimates.
What permits are needed for deck construction?
Permit requirements vary by location. Always check with your local building department for specific regulations regarding deck construction, including size limitations and necessary inspections.
What are some common causes of delays in deck projects?
Delays can stem from unforeseen weather conditions, material shortages, permit issues, or difficulties coordinating multiple trades. Careful planning and contingency measures can minimize these risks.
How do I choose the right materials for my deck?
Consider factors like budget, aesthetic preferences, and long-term maintenance needs when selecting materials. Pressure-treated lumber is a popular choice for its durability, while composite decking offers low-maintenance appeal. Wood types like cedar and redwood also have their own pros and cons.