How long does it take to fix a transformer? Well, it depends on many things, like the size, the problem, and even where the transformer is located. Imagine a big, complicated machine needing a fix – it’s not just a quick trip to the shop, right? We’ll dive into the factors that influence repair time, from the specific fault to the logistics involved.
Get ready for a detailed breakdown, presented in a friendly, easy-to-understand way!
From tiny distribution transformers to massive power transformers, each one has its own repair story. Understanding these nuances is key to appreciating the complexities involved in fixing these vital components of our electricity infrastructure. This guide will equip you with a complete picture of what goes into a transformer repair, so you can grasp the whole process and not just the time it takes.
Let’s get started, shall we?
Factors Affecting Repair Time
The repair time for a transformer is a complex variable, influenced by a multitude of factors. Determining the precise duration requires careful consideration of the specific transformer type, the nature of the fault, and the resources available. This analysis will delve into these influencing factors.The repair process for a transformer is not a standardized procedure; instead, it’s tailored to the unique circumstances of each case.
The time needed for diagnosis, component replacement, and final testing varies depending on the factors Artikeld below.
Transformer Size and Complexity
The size and complexity of a transformer directly impact the repair timeline. Larger transformers, typically used in power distribution systems, necessitate more extensive diagnostic testing and potentially more complex repairs. The intricate internal components and extensive cabling in these transformers increase the time needed for dismantling, inspecting, and reassembling. Furthermore, the logistical challenges associated with transporting and handling large transformers influence the overall repair duration.
For instance, a 500 MVA power transformer will require more time for repair compared to a 25 MVA distribution transformer.
Type of Fault
The nature of the fault significantly impacts the repair time. A simple insulation fault, for example, might require relatively less time than a core damage or winding short circuit. The severity of the fault directly correlates to the required diagnostic procedures, component replacement, and testing procedures. Faults that cause extensive damage to critical components, such as the core or windings, will undoubtedly increase the repair time substantially.
Fault Scenarios and Repair Duration
Different fault scenarios have varying implications for repair time. A simple winding insulation fault, where only a localized section is affected, could be resolved in a matter of weeks. Conversely, a severe short circuit in the windings, potentially leading to core damage, could extend the repair time to several months. The extent of damage to internal components, including the transformer oil and associated cooling systems, significantly impacts the repair timeline.
Moreover, if the fault results in the need for specialized parts, the availability of those parts becomes a critical factor.
Comparison of Repair Times for Different Transformer Types
Transformer Type | Typical Repair Time (Weeks) | Explanation |
---|---|---|
Distribution Transformer (25 MVA) | 2-4 | Generally less complex, localized faults, readily available parts. |
Substation Transformer (100 MVA) | 4-8 | More complex, potentially involving specialized tools and expertise. |
Power Transformer (500 MVA) | 8-12 | Significantly more complex, requiring extensive testing, specialized parts, and often requiring specialized crane equipment for handling. |
Note: The repair times presented in the table are estimates. Actual repair times can vary depending on the specific fault, availability of parts, and the expertise of the repair team.
Repair Procedures and Steps
Transformer repair procedures vary significantly depending on the type of fault, its severity, and the specific design of the transformer. A systematic approach is crucial to ensure safety, efficiency, and the restoration of the transformer’s operational integrity. Thorough documentation of each step is essential for quality control, troubleshooting future issues, and ensuring compliance with safety regulations.
Typical Repair Steps
The process of repairing a transformer typically involves a series of sequential steps, each with specific requirements and potential time constraints. These steps are often tailored to the particular fault and the type of transformer being repaired. Prioritization of safety measures is paramount throughout the entire process.
- Assessment and Diagnosis: This initial stage involves a thorough inspection of the transformer to identify the nature and extent of the fault. Visual inspections, non-destructive testing methods (e.g., ultrasonic testing, radiography), and electrical measurements are commonly employed. The results of these assessments are crucial for determining the appropriate repair methods and the necessary resources. For example, a localized winding fault might require targeted repair, whereas a more extensive core damage might necessitate a complete rebuild.
- Disassembly and Component Removal: This step involves carefully disconnecting the transformer from the power system and systematically removing components such as windings, bushings, and core sections. The sequence of disassembly must adhere to established procedures to prevent further damage and ensure the safe handling of critical components. Detailed documentation and photographic records of the disassembly process are vital for accurate reconstruction and for future reference.
- Fault Repair: Depending on the type of fault, this step may involve various techniques, such as replacing damaged windings, repairing insulation, or replacing faulty components. The choice of repair method will affect the total repair time significantly. For example, a simple insulation repair will take much less time than a complete winding replacement.
- Component Testing and Inspection: After the repair is completed, each component is tested and inspected to ensure it meets the required specifications and standards. Testing includes insulation resistance, winding resistance, and dielectric strength measurements. This step guarantees the quality and reliability of the repaired components.
- Reassembly and Connections: This stage involves the careful and precise reassembly of the transformer components. Careful attention to the original connections and configurations is necessary to ensure proper operation and prevent future issues. This process requires expertise and precision to avoid mistakes that could compromise the transformer’s integrity.
- Testing and Commissioning: Following reassembly, the transformer undergoes rigorous testing to verify its functionality and compliance with safety standards. Tests include load tests, short circuit tests, and insulation resistance measurements. The transformer is then ready for connection to the power system after successful completion of all tests.
Repair Time Variations
Different repair methods and fault types can significantly impact the total repair time. For instance, a minor insulation repair might take a few days, while a complete winding replacement could extend the repair process to several weeks.
Repair Step | Estimated Time (Days) | Factors Affecting Time |
---|---|---|
Assessment and Diagnosis | 1-3 | Fault complexity, equipment availability |
Disassembly and Component Removal | 2-5 | Size and complexity of transformer, availability of skilled personnel |
Fault Repair | 3-14 | Type of fault, complexity of repair method |
Component Testing and Inspection | 1-3 | Testing equipment availability, required tests |
Reassembly and Connections | 2-5 | Complexity of transformer, precision required |
Testing and Commissioning | 1-3 | Testing equipment availability, required tests |
Total | 10-35 | Overall complexity of the repair |
The table above provides a general guideline. Actual repair times can vary based on the specifics of each situation. For instance, a transformer with multiple faults will naturally take longer to repair than one with a single fault.
Tools and Equipment Required
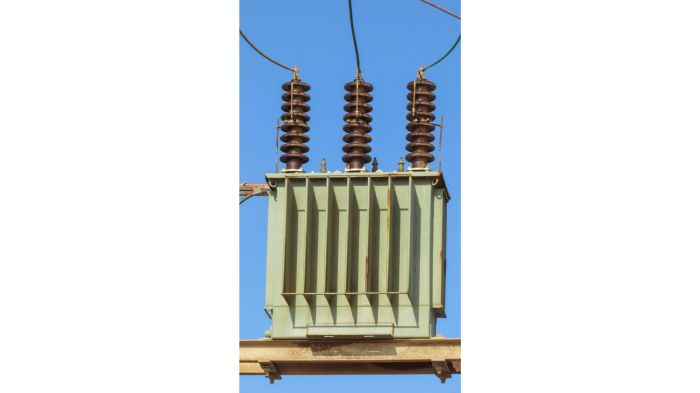
Properly equipped repair facilities and a well-stocked inventory of tools are crucial for efficient and safe transformer repairs. The selection and use of appropriate tools directly influence the speed and quality of the repair process. A comprehensive understanding of the required tools, their functions, and potential hazards is paramount for personnel involved in transformer maintenance.
Essential Tools and Equipment
A wide array of tools and equipment are necessary for transformer repairs, ranging from basic hand tools to specialized diagnostic instruments. The specific requirements vary based on the type of transformer, the nature of the fault, and the repair scope. Critical factors include ensuring electrical safety, proper insulation handling, and accurate component measurements.
Hand Tools
A fundamental set of hand tools is essential for various tasks during transformer repair. These include screwdrivers (Phillips and flathead), wrenches (adjustable and open-end), pliers (needle-nose and slip-joint), and various types of hammers. The precise selection and application of these tools are vital for dismantling and reassembling components, ensuring minimal damage to the transformer.
- Screwdrivers: Used for disassembling and assembling various components. Different types are necessary for different screws and fasteners.
- Wrenches: Necessary for tightening or loosening nuts and bolts, especially on large components. Adjustable wrenches provide flexibility for various bolt sizes.
- Pliers: Used for gripping and manipulating components, wires, and other small parts during the repair process. Needle-nose pliers allow for precise manipulation.
- Hammers: Used for driving or removing components, such as securing plates or removing rivets. Safety considerations are critical when using hammers on electrical components.
Insulation and Electrical Safety Tools
Maintaining electrical safety during transformer repairs is paramount. Specific tools are designed to minimize the risk of electrical shock and ensure proper insulation handling.
- Insulated tools: Insulated screwdrivers, pliers, and wrenches are essential to prevent accidental contact with energized components. These tools have dielectric properties to safeguard workers.
- Voltage testers: These instruments are crucial for verifying the absence of voltage before any work is performed. Different types exist, catering to various voltage ranges.
- Grounding devices: Ensuring a proper grounding system is essential for electrical safety. Grounding rods and clamps are vital components of this system.
Diagnostic and Measurement Tools
Accurate measurements and diagnostics are necessary for determining the extent of the fault and the appropriate repair procedures.
- Meggers: Used to measure insulation resistance, a critical factor in determining the condition of the transformer windings and insulation.
- Multimeters: Used for measuring various electrical parameters, such as voltage, current, and resistance, to identify faults and assess component conditions.
- Temperature sensors: Monitoring temperature is vital to prevent overheating during the repair process and to determine potential issues with the cooling system. Different sensors cater to various temperature ranges and locations.
Specialized Tools and Equipment
Specialized tools are sometimes required for specific types of transformer repairs. The availability of these tools significantly affects repair time and overall success.
- Transformer oil testing equipment: Testing the condition of the transformer oil is essential for identifying potential issues. This equipment includes oil purifiers and testing kits.
- Lifting equipment: For handling heavy transformer components during removal, installation, or transportation. Proper lifting equipment is essential to prevent damage to components and injuries to personnel.
- Specialized tools for winding repairs: For repairs involving the transformer windings, specialized tools and techniques may be necessary. These tools are often specific to the transformer type and the nature of the fault.
Safety Considerations
Proper safety procedures must be followed throughout the repair process. The use of personal protective equipment (PPE) and adherence to safety protocols are crucial.
- Personal Protective Equipment (PPE): Appropriate PPE, including safety glasses, gloves, and hearing protection, must be used to mitigate potential hazards.
- Emergency procedures: Having well-defined emergency procedures in place is crucial for handling unforeseen circumstances. This includes clear communication protocols and access to emergency response teams.
- Environmental considerations: Environmental factors such as dust and fumes can impact the repair process. Proper ventilation and containment procedures must be in place.
Table of Tools and Equipment
Category | Tool/Equipment | Specific Use in Transformer Repairs |
---|---|---|
Hand Tools | Screwdrivers | Disassembling and assembling components |
Hand Tools | Wrenches | Tightening or loosening nuts and bolts |
Insulation & Electrical Safety | Insulated Tools | Working on energized components |
Diagnostic & Measurement | Meggers | Measuring insulation resistance |
Expertise and Personnel
The successful repair of a transformer necessitates a skilled and well-coordinated team. Different levels of expertise are required for various phases of the repair process, from initial assessment to final testing. The individuals involved in the repair must possess specific knowledge and experience to ensure the safety and efficacy of the work. This section details the necessary expertise, roles, and responsibilities of personnel, highlighting the impact of skill level on repair time.
Expertise Levels for Different Repair Phases
The complexity of transformer repair tasks demands varying levels of expertise. Initial assessment, encompassing visual inspection and diagnostic testing, requires a technician with a fundamental understanding of transformer principles and safety procedures. Intermediate-level expertise is necessary for dismantling and component replacement, necessitating a thorough knowledge of transformer construction and relevant safety protocols. Advanced expertise, particularly for specialized repairs or complex fault analysis, is crucial for troubleshooting intricate issues, utilizing advanced diagnostic equipment, and implementing corrective actions.
Roles and Responsibilities of Personnel
A well-structured repair team comprises several roles, each with defined responsibilities. The lead technician, typically a senior engineer, oversees the entire repair process, ensuring adherence to safety regulations and project timelines. Electricians are responsible for the physical dismantling and reassembly of the transformer components, while electromechanical engineers manage the installation and testing of new parts. Quality control personnel are responsible for verifying the quality of repairs and ensuring compliance with industry standards.
Finally, safety officers maintain a safe working environment and enforce strict adherence to safety protocols.
Impact of Skill Level on Repair Time
The proficiency of the repair team significantly impacts the repair time. A highly skilled team can quickly diagnose faults, select appropriate repair methods, and execute the work efficiently. Conversely, a team lacking sufficient expertise may struggle with diagnostics, leading to delays in identifying the root cause and implementing the correct repair procedures. Inaccurate or poorly executed repairs may result in additional downtime and necessitate further corrective actions.
Training and Certifications for Transformer Repair Personnel
Adequate training and relevant certifications are essential for personnel performing transformer repairs. Training programs should encompass safety procedures, transformer theory, fault diagnosis, repair techniques, and testing procedures. Certifications from recognized organizations like the IEEE or industry-specific associations validate the knowledge and skills of the repair team, ensuring a high level of competency. Such certifications are often a prerequisite for employment in this field.
Personnel Involved in Transformer Repair
Personnel | Role | Required Experience |
---|---|---|
Lead Technician | Oversees the entire repair process | Minimum 5 years’ experience in transformer maintenance and repair, including fault diagnosis and corrective action. |
Electrician | Physical dismantling and reassembly of components | Minimum 3 years’ experience in electrical installations and maintenance. |
Electromechanical Engineer | Installation and testing of new parts | Minimum 2 years’ experience in electromechanical engineering, including transformer components. |
Quality Control Personnel | Verifying repair quality and compliance | Minimum 1 year’s experience in quality control procedures. |
Safety Officer | Maintaining a safe working environment | Certified safety officer with experience in high-voltage electrical environments. |
Location and Logistics

The geographical location of the transformer repair site significantly impacts the overall repair time. Factors like proximity to the repair facility, transportation infrastructure, and the availability of specialized equipment and personnel all contribute to the efficiency of the repair process. Furthermore, the accessibility of the repair site itself, including the ease of transporting equipment and materials, is a crucial aspect.
Logistics, encompassing the timely procurement of necessary parts and materials, is paramount in minimizing delays.Effective transformer repair necessitates a meticulous approach to logistics. Optimizing the flow of materials, personnel, and equipment is crucial to adhering to repair schedules. Delays in transportation, material acquisition, or unforeseen logistical challenges can have a considerable impact on the entire repair process.
Understanding these factors and implementing strategies to mitigate potential disruptions is essential for timely and successful transformer repairs.
Influence of Repair Location
The physical location of the transformer significantly influences the repair process. A remote or inaccessible location requires more time for transportation of personnel, equipment, and materials. Conversely, a location with good infrastructure and accessibility facilitates quicker delivery and faster repair times. Consideration of the distance to the repair facility, the availability of suitable transportation routes, and the presence of necessary infrastructure (e.g., loading docks, warehousing) are crucial factors in determining the total repair time.
Impact of Access to Parts and Materials
The availability and accessibility of necessary parts and materials directly affect the repair schedule. A facility with ample inventory and a well-established supply chain can expedite the repair process. Conversely, delays in procurement or logistical issues related to the acquisition of specialized components can significantly increase repair times. Procuring essential parts from distant suppliers or manufacturers may involve considerable lead times, extending the overall repair period.
Potential Delays Due to Logistical Challenges
Unexpected logistical challenges can significantly impede the repair process. Weather conditions, road closures, and unforeseen equipment breakdowns can cause delays in transportation and material delivery. Furthermore, issues with customs clearance, port congestion, or strikes in the transportation sector can further exacerbate these delays. Adequate planning and contingency measures are crucial to mitigate the risk of such disruptions.
Optimizing Logistics for Efficient Repair
To optimize transformer repair logistics, a comprehensive strategy is required. This includes establishing clear communication channels between the repair facility and the location of the transformer. Developing a robust inventory management system is crucial for maintaining sufficient stock of common parts. Identifying and utilizing reliable transportation providers with experience in handling heavy equipment is also essential. Implementing a system for tracking material delivery and anticipating potential delays through robust forecasting and contingency planning can reduce the likelihood of disruptions.
Table: Estimated Transportation and Material Delivery Times
Repair Location | Estimated Transportation Time (Days) | Estimated Material Delivery Time (Days) |
---|---|---|
Urban Center (Proximity to facility) | 1-2 | 2-3 |
Suburban Area (Moderate distance) | 2-3 | 3-4 |
Rural Area (Significant distance) | 3-5 | 4-7 |
Remote Location (Difficult terrain) | 5+ | 7+ |
Potential Delays and Contingencies
Transformer repair projects, like any complex undertaking, are susceptible to unforeseen delays. Accurately predicting and mitigating these delays is crucial for maintaining project schedules and minimizing financial losses. Understanding the potential causes and implementing effective contingency plans are essential components of a robust repair strategy.Predicting the precise duration of a transformer repair is challenging due to the unpredictable nature of component failures, logistical issues, and external factors.
Thorough planning, proactive risk assessment, and flexible contingency strategies are critical to ensuring timely completion and maintaining operational continuity.
Potential Delays
Several factors can disrupt the scheduled completion of a transformer repair project. These factors can be categorized into internal issues related to the repair process and external issues impacting the project timeline. Internal issues include material procurement delays, unexpected component damage during disassembly, and complications arising during the reassembly or testing phase. External issues include unforeseen weather events, supply chain disruptions, or labor shortages.
Mitigation Strategies, How long does it take to fix a transformer
Implementing effective mitigation strategies is vital to minimize the impact of potential delays. These strategies should address both internal and external factors. For instance, securing alternative suppliers, establishing robust communication channels with vendors, and developing contingency plans for adverse weather conditions can mitigate supply chain disruptions and weather-related delays. Regular progress monitoring and proactive communication with stakeholders are crucial to identifying and addressing potential issues early on, enabling prompt corrective action.
Impact of Unforeseen Circumstances
Unforeseen circumstances can significantly impact the repair schedule. For example, discovering extensive internal damage during disassembly can significantly prolong the repair time. Similarly, delays in material procurement or unexpected labor shortages can lead to delays in various stages of the repair process. The magnitude of the impact depends on the severity and duration of the unforeseen circumstances.
Examples of such unforeseen circumstances include unexpected component failures during the disassembly phase or delays in receiving critical replacement parts.
Contingency Plans
A well-defined contingency plan is crucial for handling unexpected issues during transformer repair. This plan should Artikel alternative strategies to address various potential delays, such as using backup suppliers, alternative testing procedures, or adjusting the repair sequence. Contingency plans should also include a mechanism for adjusting the overall repair schedule in response to unforeseen circumstances. An example of a contingency plan could involve maintaining a buffer stock of critical components, thereby minimizing delays associated with procurement issues.
Table of Potential Delays
Potential Delay | Cause | Mitigation Strategy |
---|---|---|
Material Procurement Delays | Supplier issues, unexpected shortages, or transportation problems | Identify alternative suppliers, maintain buffer stock, expedite shipping, and negotiate expedited delivery. |
Unexpected Component Damage | Hidden internal damage, or unforeseen damage during disassembly | Employ non-destructive testing methods to identify potential issues early, and maintain detailed records of the disassembly process. |
Weather-related Delays | Severe weather conditions, such as storms or heavy rain, impacting transportation or field work | Establish clear communication channels with stakeholders, monitor weather forecasts closely, and consider alternative repair methods for inclement weather. |
Labor Shortages | Unexpected illness or absence of skilled personnel | Maintain a pool of skilled backup personnel, establish cross-training programs, and consider using temporary labor when necessary. |
Supply Chain Disruptions | Global events, political instability, or natural disasters | Diversify supply sources, maintain robust communication with suppliers, and establish clear contingency plans for unforeseen global disruptions. |
Illustrative Case Studies: How Long Does It Take To Fix A Transformer
Transformer repair projects, like any complex undertaking, benefit from documented case studies. These provide valuable insights into the factors influencing repair duration, the impact of specific faults, and the effectiveness of implemented troubleshooting and contingency plans. Analyzing past cases enables better estimations for future projects and improves overall repair efficiency.
Case Study 1: Partial Winding Short Circuit
This case study examines a 500 kVA distribution transformer experiencing a partial winding short circuit. The fault manifested as elevated temperature readings in specific sections of the winding and an unusual humming sound. Initial assessments identified the need for a detailed winding analysis and thermal modeling to pinpoint the exact location and extent of the damage.
- Fault Description: A partial short circuit occurred in one of the transformer’s winding phases, resulting in localized overheating and potential damage to the insulation. The extent of the damage was uncertain until the analysis was completed.
- Repair Duration: The total repair time was 10 days. This included 2 days for diagnostics, 5 days for winding repair (including material procurement and quality control checks), and 3 days for testing and commissioning.
- Factors Influencing Repair Time: The complexity of the winding repair, the need for specialized testing equipment, and the procurement of specific insulation materials were key factors. The specific winding configuration and insulation type significantly impacted the repair time.
- Troubleshooting Steps: Detailed thermal modeling was used to identify the precise location of the fault. High-voltage testing was conducted to assess the condition of the windings and confirm the extent of the damage. This involved using partial discharge measurement equipment and insulation resistance measurements.
- Contingency Plans: A backup supply transformer was immediately activated to maintain the electrical load during the repair period. A contingency plan was also in place for potential material delays or unexpected complications in the repair process. This involved identifying alternative suppliers and having a team of experts available on standby. This ensured a timely and seamless repair without jeopardizing the power supply.
Case Study 2: Core Insulation Degradation
This case study involves a 1000 kVA power transformer experiencing core insulation degradation. The initial symptoms included abnormal noise and reduced efficiency. Detailed testing and analysis were required to determine the source and extent of the damage.
- Fault Description: Moisture ingress into the core insulation resulted in a gradual deterioration of the insulation material, leading to increased energy losses and potential failure.
- Repair Duration: The repair took 12 days, including 3 days for detailed testing to assess the extent of the damage, 5 days for drying and conditioning the core, and 4 days for reassembly, testing, and commissioning.
- Factors Influencing Repair Time: The core insulation repair process was time-consuming due to the need for specialized drying and conditioning equipment and the complex nature of the core’s geometry. Careful handling and precision were crucial to prevent further damage to the core and ensure the repair’s longevity.
- Troubleshooting Steps: Initial diagnostics involved noise analysis, monitoring of core temperatures, and efficiency measurements. Detailed testing included insulation resistance and moisture analysis to confirm the extent of the degradation. X-ray analysis and moisture measurements provided crucial data.
- Contingency Plans: An alternative cooling system was implemented to support the core drying process, minimizing the potential for thermal stress and ensuring the transformer’s safety during repair. Backup power supply procedures were reviewed to ensure seamless load transfer in case of unforeseen delays.
Summary Table of Case Studies
Case Study | Fault | Repair Duration (days) | Factors Influencing Repair Time |
---|---|---|---|
Case Study 1 | Partial Winding Short Circuit | 10 | Winding complexity, testing requirements, material procurement |
Case Study 2 | Core Insulation Degradation | 12 | Core drying and conditioning, geometry of the core, testing complexities |
Epilogue
So, there you have it – a comprehensive look at the factors influencing transformer repair time. From the intricate repair procedures to the crucial role of expertise and logistics, we’ve covered it all. Remember, every transformer repair is unique, but by understanding the key elements, you can better appreciate the dedication and skill required to get the job done right.
Hopefully, this insight will help you visualize the whole process and appreciate the efforts involved in fixing these important power systems. Semoga bermanfaat!
Query Resolution
How much does a transformer repair cost?
The cost varies greatly depending on the size and type of transformer, the extent of the damage, and the labor involved. You’ll need to consult a qualified electrician or repair company for a precise estimate.
What are the common causes of transformer faults?
Common faults include insulation damage, overheating, short circuits, and issues with the windings. Over time, age and environmental factors can also play a role.
Can a transformer be repaired or does it need to be replaced?
It depends on the severity of the damage. Minor faults can often be repaired, while extensive damage may necessitate replacement for safety and efficiency reasons.
What safety precautions should be taken during transformer repairs?
Always prioritize safety! High voltage and potential hazards exist. Follow all safety protocols, including proper lockout/tagout procedures, and ensure you have the right training and experience before attempting any repairs.