How long for driveway sealant to dry? This isn’t just about waiting; it’s about achieving a perfect, long-lasting seal. Understanding the factors that influence drying time is key to a successful project. From the type of sealant to the weather, we’ll explore every aspect of this crucial process, ensuring your driveway is protected and beautiful for years to come.
Different sealants have different drying times, and understanding these variations is crucial. Environmental factors like temperature and humidity play a significant role, so choosing the right sealant and conditions for your project is paramount.
Drying Times and Factors
Yo, driveway sealant ain’t gonna dry itself, you know? Loads of factors play a role in how long it takes to go from gooey to solid. Understanding these will help you avoid a sticky situation later on.Different sealants have different drying speeds, and the weather plays a massive part too. Knowing the ideal conditions for your chosen sealant is crucial for a proper job.
Think of it like baking a cake – you need the right ingredients and oven temperature to get the perfect result.
Drying Time Variables
Knowing the variables impacting drying time is key to avoiding any nasty surprises. Different sealants react differently to the environment, so understanding the specific conditions is important.
- Sealant Type: Acrylics are generally quicker to dry than epoxies or polyurethanes. Epoxy sealants, being more chemically complex, take longer to cure and develop their full strength. Polyurethanes, being super durable, often need more time to harden completely.
- Temperature: Warmer temps speed up the drying process. A scorching summer day will see your sealant dry much faster than a chilly autumn morning. Think of it like paint drying quicker in sunshine. If it’s freezing, you might need to delay the job.
- Humidity: High humidity can slow down the drying process, creating a damp environment that prevents the sealant from properly curing. Imagine trying to dry your hair on a humid day; it just takes longer. Low humidity, on the other, will accelerate the process.
- Sunlight: Direct sunlight can speed up the evaporation process, but too much can also cause the sealant to dry unevenly. Think of a puddle drying quicker in the sun.
Sealant Drying Time Comparison
Different sealant types have vastly different drying times. It’s like comparing apples and oranges – they’re all fruits, but they have unique characteristics.
Sealant Type | Typical Drying Time (hours) | Ideal Temperature Range (°C) | Ideal Humidity Level (%) |
---|---|---|---|
Acrylic | 4-24 | 15-30 | 30-60 |
Epoxy | 24-72 | 15-25 | 30-50 |
Polyurethane | 24-48 | 15-25 | 30-60 |
Drying Stages and Time Estimates
Understanding the stages of sealant drying is vital for quality control and to avoid applying further treatment too early.
Sealant Type | Wet | Tacky | Dry |
---|---|---|---|
Acrylic | 0-2 hours | 2-6 hours | 6-24 hours |
Epoxy | 0-6 hours | 6-24 hours | 24-72 hours |
Polyurethane | 0-6 hours | 6-24 hours | 24-48 hours |
Drying Stages and Indicators
Right, so you’ve got your driveway sealant sorted, now you need to know how long it takes to properly dry. Knowing the stages is crucial, ’cause different stages look totally different, and you don’t wanna end up with a dodgy finish.Understanding these stages helps you avoid common mistakes and ensures your driveway sealant does its job properly, looking fresh and lasting for ages.
Visual Indicators of Drying Stages
Knowing the visual cues is key to making sure your sealant is fully cured. Different stages have different looks, and rushing things can lead to problems down the line.
- Wet Stage: The sealant will appear glossy and sticky, like a freshly-applied layer of honey. This is the initial stage where the sealant is still absorbing into the surface, and it’s crucial not to walk or drive on it during this period. You’ll want to avoid any disturbance to let it do its job properly. Think of it like a liquid that’s just settling in.
Don’t put any pressure on it, especially heavy things like cars or people walking, or you’ll risk messing up the finish.
- Tacky Stage: The sealant will start to lose its shine and stickiness. It’ll still be a bit tacky to the touch, but not as much as in the wet stage. This is where you might start seeing some initial signs of the sealant hardening and becoming more resistant to surface disturbances. The surface will have a slight haze, like a bit of a film.
- Drying Stage: The sealant will now be dry to the touch, with a matte finish. There’s no stickiness at all, and you can safely walk on it, but you’re still best to avoid heavy vehicles or tools from this point until the final stage.
- Hardened Stage: The sealant is fully cured and hardened, with a smooth, non-tacky surface. It’s tough enough to handle heavy traffic and won’t be affected by minor weather changes. You can now drive or walk on it without any worries about disturbing the finish. It’s like a rock-solid surface, ready for anything.
Comparing Visual Indicators
This table summarizes the visual indicators for each drying stage, helping you quickly identify where your sealant is in the process.
Drying Stage | Visual Indicator | Significance |
---|---|---|
Wet | Glossy, sticky | Sealant is still absorbing and hasn’t fully set yet. |
Tacky | Slightly tacky, loses gloss | Sealant is starting to harden and is less susceptible to disturbance. |
Drying | Dry to the touch, matte finish | Sealant is mostly cured but avoid heavy traffic until fully hardened. |
Hardened | Smooth, non-tacky surface | Sealant is fully cured and ready for normal use. |
Application Methods and Their Impact

Right, so you’ve got your sealant sorted, now it’s all about the application. Different ways of slapping it on can totally change how long it takes to dry, so pay attention, yeah? This ain’t rocket science, but it’s important for a proper finish.Applying sealant the right way is crucial for a long-lasting driveway. Different techniques affect the evenness of the coat, the amount of sealant used, and ultimately, the drying time.
Think about it like painting; a bad brush stroke leaves you with an uneven finish. Same goes for sealant, so let’s dive into the deets.
Brush Application
Brush application is a classic method, often favoured for its control and ability to get into tight corners. However, it can be a bit more time-consuming than other methods. Brush application usually involves applying the sealant in thin, even coats. This method often leads to a more even finish, which can be a good thing. But, it can be harder to achieve a consistent thickness.
Spray Application
Spraying is faster and allows for more coverage in a shorter time. It’s perfect for large areas and can create a nice, uniform coat. But, you need to be careful about overspray and ensuring the sealant is applied evenly across the entire surface. A good spray technique can make a huge difference. Think about how much faster spraying a wall is than painting it by hand!
Roller Application
Using a roller can be a good middle ground between brush and spray. It gives you decent control over the application, and it can be faster than using a brush. But it does take some practice to get the hang of it. Make sure you’re using the right type of roller for the job, though. You don’t want any lumps or bumps in your sealant!
Comparison of Drying Times
Application Method | Drying Time (General Estimate) | Advantages | Disadvantages |
---|---|---|---|
Brush | Generally 24-72 hours | Good control, can work in tight spots | Slower, can be more labour-intensive |
Spray | Generally 12-48 hours | Faster, covers larger areas more quickly | More potential for unevenness, requires careful technique |
Roller | Generally 18-48 hours | Good balance of speed and control, good for medium-sized areas | Can be harder to get a perfectly smooth finish |
Sealant Thickness and Drying Time
Thicker coats take significantly longer to dry compared to thinner coats.
A thicker application means the sealant has more material to dry, which naturally extends the drying time. Think of it like trying to dry a puddle – the bigger it is, the longer it takes to evaporate. It’s crucial to apply a consistent, appropriate thickness for a uniform drying process. Don’t be a sealant slatherer; stick to the recommended thickness!
Step-by-Step Application Procedure
- Thoroughly clean the driveway surface, removing any dirt, debris, or oil.
- Apply a thin, even coat of sealant, working in sections.
- Allow the sealant to dry completely before applying a second coat.
- Ensure that all the coats are uniform and have no gaps or overlaps.
- Follow the manufacturer’s instructions carefully.
Troubleshooting and Solutions
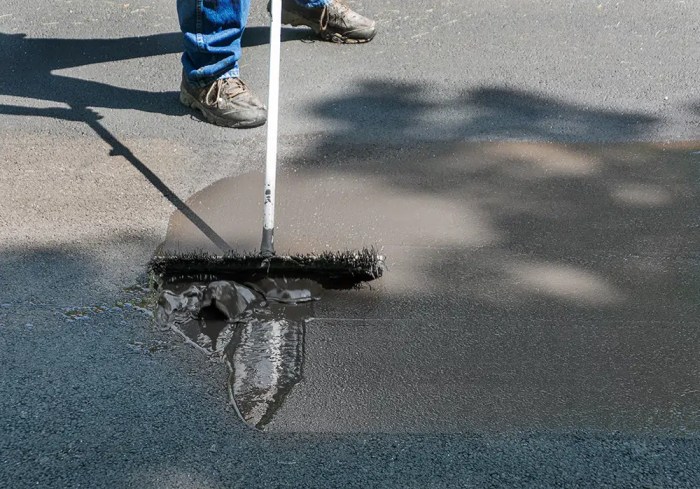
Right, so you’ve got your driveway sealant all prepped, but now it’s not drying like you were expecting? No worries, mate. We’ll sort out these common issues and get your driveway looking fresh again.Common problems with driveway sealant drying can stem from a few different factors, from the weather to the sealant itself. Understanding these causes is key to fixing any issues and getting a smooth, even finish.
Knowing what’s up can save you a lot of hassle and wasted sealant.
Common Drying Issues
Sealant drying can be affected by a bunch of things, from the weather to the surface prep. Knowing what might be causing problems is the first step to fixing them.
- Uneven Drying: This can be caused by inconsistent application, like not spreading the sealant evenly, or differences in the surface’s absorbency. Patches drying faster than others could also indicate a problem with the sealant or its application.
- Slow Drying: Temps are too low, the sealant wasn’t mixed right, or there might be too much moisture in the air or on the surface. A thicker application also leads to slower drying, making sure you’re using the right amount for the job is essential.
- Premature Cracking: This is often due to the sealant being applied too thick or using a sealant that’s not suitable for the weather conditions. Applying too much or too quickly can also cause issues.
Troubleshooting Table, How long for driveway sealant to dry
This table breaks down common sealant drying problems, their potential causes, and how to fix them.
Problem | Possible Causes | Solutions |
---|---|---|
Uneven Drying | Inconsistent application, variations in surface absorbency, differences in sealant thickness, or uneven mixing | Ensure even application using a spreader. Clean and prep the surface thoroughly. Use the recommended amount of sealant per area, and ensure the sealant is properly mixed before application. Consider using a primer if the surface is uneven. |
Slow Drying | Low temperatures, insufficient mixing, too much moisture in the air or on the surface, thick application, unsuitable sealant for the conditions | Wait for better weather conditions, mix the sealant thoroughly. Ensure the surface is clean and dry before application. Use a thinner application. Use a sealant specifically designed for low-temperature applications. |
Premature Cracking | Too thick an application, unsuitable sealant for the weather conditions, improper mixing, or applying in direct sunlight. | Use the recommended amount of sealant for the job. Apply in cooler temperatures or on cloudy days. Mix the sealant thoroughly. Use a sealant that’s appropriate for your climate. |
Example Solutions
Let’s say you’re experiencing slow drying. First, check the weather forecast. If it’s chilly, you might need a sealant designed for low temperatures. If the surface isn’t totally dry, give it some more time to dry completely before applying the sealant. Also, ensure the sealant is thoroughly mixed before application, as this can affect the drying time.
Safety Precautions During Drying
Right, so you’ve got your driveway sealant all prepped and ready to go, but safety’s key, mate. Don’t wanna end up with a nasty accident or a ruined day because you weren’t careful. This section’s all about keeping you and your crew safe while the sealant does its thing.Proper safety precautions during the drying phase are crucial to avoid potential hazards.
This includes understanding the risks associated with the sealant in different stages and taking the necessary steps to mitigate those risks. Following these safety measures ensures a smooth and safe application process.
Potential Hazards During Different Drying Stages
Sealant, especially when it’s fresh, can be a bit of a hazard. Different stages present different risks. Freshly applied sealant is sticky and can cause skin irritation. It also releases fumes that can be harmful if inhaled in large quantities. As it cures, the fumes lessen but can still pose a problem if ventilation isn’t good.
Safety Precautions for Workers
Workers need to be clued up on safety gear and procedures to avoid any nasty situations. Always ensure adequate ventilation during application and drying. This is super important to reduce the risk of breathing in harmful fumes. Using respirators when needed is essential, especially if the sealant has strong odours. Protective gloves, eyewear, and clothing should be worn throughout the process.
This is to prevent contact with the sealant and potential skin irritation or chemical burns. Regular breaks are vital, too. Keeping hydrated is also key to staying healthy, especially in warm weather. Make sure you have a buddy system in place, especially for larger jobs.
Weather-Specific Safety Guidelines
Weather Condition | Safety Precautions |
---|---|
Sunny, Hot Weather | Increased risk of skin irritation and overheating. Take frequent breaks in shaded areas. Ensure adequate hydration and use sunscreen. Reduce working hours to avoid heat exhaustion. Increase ventilation to disperse fumes. |
Rainy Weather | Sealant can be diluted or washed away prematurely if it rains before the sealant is completely cured. Monitor weather forecasts and adjust work schedules accordingly. Consider using sealant resistant to moisture. Cover the sealant if possible. |
Cold Weather | Sealant may take longer to dry in cold temperatures. Adjust drying times based on the weather. Use sealant designed for cold temperatures if possible. Avoid working in extremely cold temperatures that could affect worker safety and reduce application efficiency. |
Windy Weather | Wind can affect drying times and cause sealant to spread unevenly. Monitor wind conditions and adjust work schedules if necessary. Consider using windbreaks or working in sheltered areas. |
Appropriate Protective Equipment
Protective gear is crucial, folks. The right gear can protect you from chemical burns, skin irritation, and breathing problems. A proper respirator is essential if the sealant has strong fumes. Gloves, eye protection, and long-sleeved clothing will shield you from direct contact with the sealant. Remember, safety gear is your friend, so wear it properly.
Don’t be a hero, wear the gear.
Preventing Problems During Drying
Right, so you’ve got your driveway sealant all prepped and ready to go. Now, the crucial part – keeping it from turning into a dodgy mess while it dries. Avoiding common problems like cracking, bubbling, or adhesion issues is key to a smooth, long-lasting finish. This ain’t rocket science, but knowing the dos and don’ts will save you a whole heap of hassle down the line.Proper prep and understanding the drying conditions are crucial for a flawless finish.
This section dives into the nitty-gritty of preventing issues during the drying process, ensuring your sealant performs like a champ.
Surface Preparation for Optimal Drying
Getting the surface spot on is mega important for a smooth drying process. A properly prepped surface allows the sealant to bond properly and dry evenly, preventing future problems. This involves more than just a quick clean; it’s about creating an ideal environment for the sealant to work its magic.
- Thorough Cleaning: Make sure the area is squeaky clean. Remove any loose debris, dirt, or oil residue. This prevents these particles from interfering with the sealant’s bonding. Think of it like getting a fresh canvas ready for a masterpiece – a clean surface is a happy sealant’s dream.
- Surface Repairs: Patch up any cracks or holes in the driveway before applying the sealant. This ensures the sealant can bond to the entire surface and prevents the sealant from pulling away. This will save you a ton of grief later on.
- Proper Priming: Using a primer is a top tip, especially for porous surfaces. It creates a better bond for the sealant and helps prevent issues like bubbling. This is a key step, so don’t skip it!
- Temperature and Humidity Control: Ideally, you want to apply the sealant in conditions with moderate temperatures (not too hot or cold) and low humidity. High temperatures can lead to fast drying that isn’t even, while high humidity can cause issues with the sealant bonding properly. Think of it like baking a cake – you need the right temperature and humidity for a perfect outcome.
Maintaining Optimal Drying Conditions
Keeping the right conditions during the drying period is vital. Think of it like looking after a delicate plant – you need to give it the right amount of sun and water to thrive. This section highlights the vital factors for optimal drying.
- Shade and Protection: If possible, provide shade to the sealed area, especially during peak sun hours. Direct sunlight can cause uneven drying, leading to cracking and other problems. Consider using shade cloths or other temporary coverings.
- Avoiding Direct Sunlight: Prolonged exposure to direct sunlight can lead to rapid drying. This can cause issues with the sealant’s adhesion, leading to cracking or bubbling. Apply sealant during the cooler parts of the day for best results.
- Preventing Moisture: Keep moisture away from the freshly applied sealant. Rain or excessive humidity can hinder the drying process and lead to issues like bubbling. If rain is anticipated, postpone application until conditions are favourable.
- Maintaining Consistent Temperature: Consistent temperatures during the drying process are ideal for even drying. Fluctuating temperatures can disrupt the sealant’s drying process, leading to issues with adhesion. Monitor the weather forecast and plan your application accordingly.
Preventing Cracking, Bubbling, and Adhesion Issues
Addressing these issues early on can prevent a whole heap of future problems. This involves understanding the causes and taking the necessary steps to avoid them.
- Avoiding Over-Application: Applying too much sealant can lead to pooling and bubbling. Make sure you’re applying the correct amount of sealant per square metre, following the manufacturer’s instructions. A good coat is key; too much is a no-go.
- Addressing Imperfections: Ensure that you deal with any imperfections before sealing, such as uneven surfaces or small holes. This ensures a smooth, even surface for the sealant to adhere to, preventing bubbling and cracking.
- Using Appropriate Sealant Type: Selecting the correct sealant type for your driveway is essential. Different sealants have different drying times and characteristics. Using the right sealant for the job will help avoid issues like cracking or bubbling.
Preventing Drying Issues: A Step-by-Step Guide
Following these steps will greatly increase your chances of a successful sealant application. This detailed guide helps you through the process from start to finish.
- Thoroughly clean the driveway.
- Patch up any cracks or holes.
- Apply a primer, if needed.
- Apply the sealant in optimal conditions (moderate temperatures, low humidity).
- Protect from direct sunlight or rain.
- Allow the sealant to dry completely according to the manufacturer’s instructions.
Visual Aids and Illustrations
Right, so you wanna see the sealant drying process in action? We’re gonna break it down with some visuals, so you can ace this driveway job. No more guessing games, just clear, visual guides.Visual aids are key for understanding the sealant drying process. They help you visualize the different stages and spot potential issues early. This section provides detailed illustrations to help you every step of the way.
Stages of Sealant Drying
Visualizing the stages of sealant drying is crucial for identifying problems. This visual breakdown shows the various stages and helps you understand what to expect at each point. It’s like having a cheat sheet for the drying process. Stage 1: Initial Wetness. Imagine a freshly applied coat of sealant, still looking a bit like a wet, sticky film.
The liquid is spread out, but not fully absorbed. This image would show a surface with a noticeable sheen, a little like a freshly waxed car. Stage 2: Tack-Free. The sealant is starting to lose its tackiness. It’s not dripping, but it still feels slightly sticky if you rub it.
This image would depict a surface that’s no longer shiny, with the wet look almost gone, and a slight, almost imperceptible stickiness. Stage 3: Initial Set. The sealant is mostly dry but still might show some minor imperfections. It’s firm to the touch, but might have some minor surface irregularities. This image would display a surface that’s hardened but still showing some slight texture, like a slightly rough but dry surface.
Stage 4: Fully Cured. The sealant is fully cured, looking smooth and solid. You can walk on it without any issues, and it’s ready for use. This image would depict a smooth, glossy surface that’s completely hardened and ready for use.
Environmental Factors Affecting Drying
Understanding how the weather affects drying time is crucial for planning. Different conditions can significantly impact the speed at which sealant cures.
Factor | Visual Representation | Explanation |
---|---|---|
Sunlight | Direct sunlight can speed up the drying process, as heat evaporates the solvent. | |
Temperature | Warmer temperatures generally lead to faster drying, while cooler temperatures result in slower drying. | |
Humidity | High humidity can slow down the drying process. The sealant needs drier air to evaporate the solvent properly. | |
Wind | Wind can affect drying time by increasing evaporation rates. |
Application Methods and Their Impact
Different application methods can affect the drying time. The way you apply the sealant can impact how evenly it spreads and dries. Method 1: Brush Application. A brush will leave slight brush marks on the surface. This method usually takes longer to dry completely, as the sealant might pool in certain areas.
Method 2: Roller Application. A roller will create a more even coat, leading to a faster drying time than the brush method.
Method 3: Spray Application. A spray method will ensure even coverage but can result in uneven drying times, especially in areas where the spray is thinner or thicker.
End of Discussion
In conclusion, knowing how long for driveway sealant to dry is essential for a successful application. By considering the type of sealant, application method, and environmental conditions, you can optimize the drying process and achieve a durable, beautiful finish. Remember to prioritize safety and follow proper procedures throughout the entire process.
Quick FAQs: How Long For Driveway Sealant To Dry
How do I prevent cracking in the sealant?
Proper surface preparation and application technique are key. Ensure the surface is clean, dry, and free of debris before applying the sealant. Apply a thin, even coat, avoiding thick applications that can lead to cracking. Allow sufficient drying time for each layer, following manufacturer guidelines.
What if my sealant is drying unevenly?
Uneven drying often stems from inconsistent application or environmental factors. Ensure a consistent application technique and monitor the temperature and humidity levels. If the issue persists, contact a professional for advice.
Can I speed up the drying process?
While you can’t significantly speed up the drying process, maintaining ideal temperature and humidity conditions (as Artikeld in the table) will help it dry quicker and more evenly.
What are the safety precautions for working with sealant?
Always wear appropriate protective gear, such as gloves, eye protection, and a mask. Ensure proper ventilation, especially in enclosed spaces. Follow manufacturer instructions carefully for handling and storage.