How long to build glass enclosure sunroom? This isn’t just about bricks and mortar; it’s about crafting your dream sun-drenched oasis. From initial design sketches to the final, gleaming glass facade, the project timeline hinges on various crucial factors. Let’s dive into the world of sunroom construction and uncover the key elements affecting the build time.
The construction time for a glass enclosure sunroom depends heavily on the scope of the project. Factors like size, design complexity, material availability, and the chosen construction method all play a significant role. A meticulous understanding of these factors is crucial for setting realistic expectations and avoiding potential delays.
Project Scope and Factors Affecting Duration
A glass enclosure sunroom, while aesthetically pleasing, presents a complex construction project. The duration hinges critically on meticulous planning and execution, influenced by various factors. Proper assessment of these factors is essential for realistic time estimations.The scope encompasses more than just glass walls. It includes structural support, framing, insulation, roofing, and often, interior finishing, heating/cooling systems, and electrical work.
Precisely defining the project’s boundaries and understanding the potential complexities is paramount to an accurate duration estimate.
Components of a Glass Enclosure Sunroom
Understanding the scope involves a detailed breakdown of the components. A typical sunroom project encompasses the following:
- Framing: The structural framework supporting the entire enclosure, usually wood or metal. This dictates the overall strength and stability of the structure.
- Glass Panels: The defining feature, determining the amount of natural light and the aesthetic appeal. Considerations include type (tempered, laminated), size, and installation techniques.
- Roofing System: Essential for weather protection and thermal performance. This includes the roof structure and the roofing material (e.g., glass, polycarbonate, composite).
- Insulation: Critical for thermal efficiency and minimizing energy loss. This includes wall and roof insulation, and sometimes involves specialized glass.
- Exterior Finish: The exterior covering of the sunroom, which may include trims, flashing, and sealing to protect against water damage.
- Interior Finishes: Wall treatments, flooring, lighting, and other interior elements, which can significantly affect the construction time.
- Mechanical Systems: Heating, cooling, and ventilation systems, if included, will extend the construction time.
Factors Influencing Construction Time
Numerous factors impact the overall construction time, each requiring careful evaluation:
- Project Size: A small sunroom will take less time than a large one. Construction time scales roughly with the square footage.
- Complexity: Features like custom designs, intricate architectural details, or specialized materials will significantly extend the construction period. For instance, a sunroom with an integrated fireplace or a complex roof design will take longer to build.
- Materials: The choice of materials, from the type of glass to the wood used for framing, directly impacts the construction process. High-quality, custom materials often mean longer lead times for procurement.
- Labor Availability: Local labor market conditions, availability of skilled contractors, and the demand for construction services influence the project timeline. Seasonal variations can also impact availability and pricing.
- Permits and Approvals: Obtaining necessary permits and approvals from local authorities can introduce delays, depending on the jurisdiction and the project’s complexity.
Typical Construction Times for Different Sizes
The following table provides a general comparison, recognizing that actual times vary widely based on the factors Artikeld above.
Sunroom Size | Estimated Construction Time (Approximate) |
---|---|
Small (100-200 sq ft) | 2-4 weeks |
Medium (200-400 sq ft) | 4-8 weeks |
Large (400+ sq ft) | 8+ weeks |
Comparison of Construction Methods
This table compares the time commitment for different construction methods.
Construction Method | Time Commitment (Approximate) | Considerations |
---|---|---|
DIY | Variable (weeks to months) | Requires significant time investment, expertise, and potentially specialized tools. |
Professional Contractor | 4-12 weeks (depending on complexity) | Experienced professionals handle all aspects, minimizing owner time and potential errors. |
Design and Planning Considerations
A meticulously planned sunroom design is paramount to achieving a functional, aesthetically pleasing, and structurally sound addition to any home. A lack of careful planning can lead to costly rework, structural issues, and a final product that fails to meet the homeowner’s needs. Thorough consideration of every aspect, from initial concept to final blueprints, is crucial for a successful project.Precise measurements and detailed plans are not merely convenient; they are essential for efficient construction.
Inaccurate measurements lead to wasted materials, costly revisions, and potential safety hazards. A comprehensive design package, including detailed floor plans, elevations, and specifications, ensures all parties involved understand the project’s scope and requirements.
Initial Concept and Design
The initial concept stage involves visualizing the sunroom’s purpose and desired aesthetic. This involves determining the size, shape, and location of the enclosure, considering factors such as natural light, views, and the overall architectural style of the home. Sketches, mood boards, and preliminary renderings are invaluable tools in this phase. This phase also considers the integration of the sunroom with existing features and the flow of the home’s layout.
Precise Measurements and Accurate Plans
Accurate measurements are critical to ensuring the sunroom fits seamlessly into the existing structure. Precise measurements of existing walls, windows, doors, and rooflines are essential. These measurements must be meticulously documented and used to create accurate blueprints. Software tools can aid in generating precise plans and providing multiple design options. This allows for informed decisions based on potential challenges and opportunities.
Sunroom Design Types, How long to build glass enclosure sunroom
Different sunroom designs offer unique advantages. Gable sunrooms feature a sloping roof, maximizing headroom and creating a more dramatic architectural statement. Shed sunrooms, with a flat roof, offer a more contemporary aesthetic and often require less complex construction. Lean-to sunrooms are attached to an existing structure, extending the existing space with minimal structural impact. The choice of design depends on the specific site conditions, budget, and the homeowner’s aesthetic preferences.
Common Design Challenges and Solutions
One common challenge is integrating the sunroom with existing plumbing or electrical systems. Careful planning and consultation with contractors can resolve this. Another challenge is ensuring the sunroom’s structural integrity, especially if it’s a significant addition. Consult with a structural engineer to address this concern. Understanding local building codes and regulations is vital to avoid potential setbacks.
Essential Considerations for Structural Integrity and Safety
Aspect | Considerations |
---|---|
Foundation | Ensure adequate foundation support for the sunroom’s weight, especially for larger structures. |
Framing | Use appropriate lumber and framing techniques to resist stress and ensure long-term stability. |
Roofing | Select materials that can withstand local weather conditions and ensure proper drainage. |
Glazing | Use high-quality glass or other glazing materials, properly sealed, to maintain structural integrity and thermal performance. |
Building Codes | Adherence to local building codes is paramount for structural safety and compliance. |
Insulation | Proper insulation is crucial to maintain thermal comfort and energy efficiency. |
Material Procurement and Availability
Reliable material procurement is critical for timely and cost-effective sunroom construction. Delays in acquiring necessary components can significantly impact the entire project schedule. A proactive approach to sourcing materials, understanding lead times, and considering alternative options is essential for maintaining a smooth project trajectory.Proper material selection, including glass, framing, and other components, directly influences the construction timeline. Ignoring lead times or overlooking potential supply chain disruptions can lead to costly and frustrating delays.
This section will explore the typical lead times for various materials, examine the impact of material availability on project duration, and present alternative material choices that may either accelerate or decelerate the construction process.
Lead Times for Common Materials
Understanding lead times for key materials is crucial for accurate project scheduling. Fluctuations in demand, supply chain issues, and manufacturing processes can all influence the time it takes to acquire materials. A thorough understanding of these variables is essential for mitigating potential project delays.
- Glass: Lead times for glass vary widely depending on the type, thickness, and complexity of the order. Standard float glass typically has a shorter lead time than specialized or custom-fabricated glass. For example, ordering tempered or laminated glass for a large sunroom might take several weeks longer than basic float glass.
- Framing Materials: Lead times for framing materials like aluminum, vinyl, or wood can range from a few days to several weeks. Factors like material type, quantity, and whether pre-fabricated sections are required are crucial considerations. For example, custom-fabricated wood frames, especially with intricate designs, can take significantly longer than standard aluminum frames.
- Other Components: This category encompasses everything from hardware like hinges and locks to sealant and insulation. Lead times for these components are generally shorter than those for glass or framing, but can still contribute to overall project duration if not accounted for.
Impact of Material Availability
Unforeseen material shortages or delays can have substantial consequences for a construction project. These disruptions can derail the entire schedule, potentially leading to cost overruns and customer dissatisfaction. Thorough planning and contingency measures are critical.
- Project Duration: Significant material delays can extend the entire project timeline. A shortage of a crucial component, like specific types of tempered glass, could delay the framing and installation phases.
- Project Costs: Delays often translate to increased costs. Labor costs escalate due to idle time, and potential penalties might be incurred for missing project deadlines.
- Customer Satisfaction: Material shortages can lead to disappointment and frustration for the customer. Maintaining transparency and effective communication throughout the process is essential to maintain a positive relationship.
Alternative Materials
Employing alternative materials can sometimes shorten or lengthen construction time. Carefully evaluating the trade-offs between cost, durability, and aesthetics is critical.
- Pre-fabricated Glass Panels: Using pre-fabricated glass panels can accelerate the installation phase, as the panels are often factory-assembled. This can reduce on-site labor and potentially shorten the construction time.
- Recycled or Alternative Framing Materials: Using recycled or alternative framing materials, like bamboo or engineered wood, may have different lead times than traditional materials. Researching availability and lead times for these materials is necessary.
- Standard Glass vs. Specialty Glass: Choosing standard glass types can reduce lead times compared to specialty glasses like low-E or insulated glass units. Weighing the benefits of performance and aesthetics against the time constraints is essential.
Glass Type and Lead Time Table
| Glass Type | Description | Typical Lead Time (Weeks) ||—|—|—|| Float Glass | Standard clear glass | 2-4 || Tempered Glass | Heat-treated for increased strength | 4-6 || Laminated Glass | Multiple layers bonded together | 6-8 || Insulated Glass Units (IGUs) | Multiple panes with air or gas space | 4-8 || Low-E Glass | Coated to reduce heat transfer | 4-6 || Custom Glass | Designed to specific specifications | 8-12+ |
Construction Procedures and Timeline
A meticulously planned construction sequence is paramount for a successful sunroom project. Ignoring the sequential nature of tasks can lead to significant delays and increased costs. Thorough preparation, precise execution, and adherence to a realistic timeline are crucial for achieving the desired outcome.
Framing the Structure
The framing phase is foundational to the entire sunroom project. It involves constructing the structural support system for the enclosure. This includes erecting the exterior walls, the roof framework, and the necessary interior support beams. Properly sized lumber, securely fastened joints, and adherence to building codes are essential. The framing stage usually takes 3-5 days for a standard sunroom, contingent upon the complexity of the design.
A more intricate design, involving non-standard angles or multiple levels, will naturally extend this time.
Glazing the Enclosure
Glazing, the installation of glass panels, is a critical step. The selection of appropriate glass types, such as tempered or laminated safety glass, significantly impacts the sunroom’s durability and energy efficiency. Careful consideration of glass sizes, framing tolerances, and sealing techniques are vital. Professional installation, ensuring proper alignment and sealing, is essential to prevent leaks and maintain the structural integrity of the enclosure.
This phase usually takes 2-3 days, potentially longer if there are complex glass configurations or challenging installation areas.
Interior Finishing
Interior finishing involves tasks such as installing drywall, flooring, and finishing touches like painting, tiling, or installing interior doors. This stage depends heavily on the specific materials chosen and the desired aesthetic. The time commitment for this stage can vary greatly, ranging from 3-7 days, based on the complexity of the finishes. A simple, painted interior will take less time than one incorporating intricate tilework or custom cabinetry.
Exterior Finishing
Exterior finishing often includes tasks like painting or staining the exterior frame, installing exterior trim, and completing any necessary landscaping. The duration of this stage depends on the scope of the work, ranging from 1-3 days for a simple exterior to 5+ days for extensive landscaping and exterior design elements. This stage is important for the longevity and visual appeal of the sunroom.
Timeline Considerations
Different construction methods can significantly affect the overall project timeline. For example, prefabricated sunrooms often have a much faster construction timeline compared to custom-built ones. Furthermore, weather conditions can impact the progress of exterior work. Delays can also arise due to unforeseen issues like material shortages or permit delays.
Task | Estimated Duration (Days) |
---|---|
Framing | 3-5 |
Glazing | 2-3 |
Interior Finishing | 3-7 |
Exterior Finishing | 1-5 |
Inspection and Permits | 2-4 |
The table above provides a general guideline. Actual timelines will vary based on project specifics, local regulations, and the chosen construction methods.
Permits and Regulations
Obtaining the necessary permits and adhering to local building codes is critical for a successful sunroom project. Failure to comply can lead to costly delays, project stoppages, and even legal ramifications. A proactive approach to permit acquisition ensures a smooth and timely construction process.The permitting process for a sunroom addition varies significantly by jurisdiction, but generally involves several key steps.
Understanding these steps and potential roadblocks beforehand is essential for effective project management. This section details the expected process and potential delays to anticipate.
Typical Permitting Process
The permitting process typically begins with a comprehensive application submitted to the local building department. This application should include detailed plans, specifications, and supporting documentation. The submission process can be straightforward or complex, depending on the local regulations. Accurate and thorough documentation is paramount.
Potential Delays
Delays in the permitting process can stem from various factors. Incomplete applications, unclear plans, or discrepancies between submitted documents and actual construction plans can trigger review requests and delays. Unforeseen circumstances, such as staff shortages in the building department or significant backlogs, can also lead to project delays. Reviewing the building department’s recent permit processing times, if available, is crucial.
Examples include projects in similar neighborhoods or regions.
Impact of Local Building Codes
Local building codes dictate the minimum standards for construction, safety, and energy efficiency. These codes are essential for the long-term structural integrity and functionality of the sunroom. Compliance with local codes is mandatory. Building codes often dictate aspects like structural support, insulation requirements, and accessibility features. Deviation from these codes can result in permit denial or significant modifications, leading to project delays.
Steps in the Permitting Process
- Application Submission: Thoroughly complete and submit all required forms, blueprints, and specifications to the building department. Ensure accurate dimensions and adherence to local building codes.
- Plan Review: The building department reviews the submitted plans for compliance with local codes and regulations. This review can take several weeks or months, depending on the complexity of the project and the workload of the department.
- Inspections: The building department conducts various inspections during the construction process to verify compliance. These inspections ensure that the construction adheres to the approved plans and codes.
- Permit Issuance: Upon successful completion of all inspections and approvals, the building department issues the necessary permits. Receiving the permit is a critical step that formally allows the project to proceed.
- Ongoing Compliance: Maintain compliance with all regulations and permits throughout the construction process to avoid project setbacks or delays.
Labor and Workforce Considerations
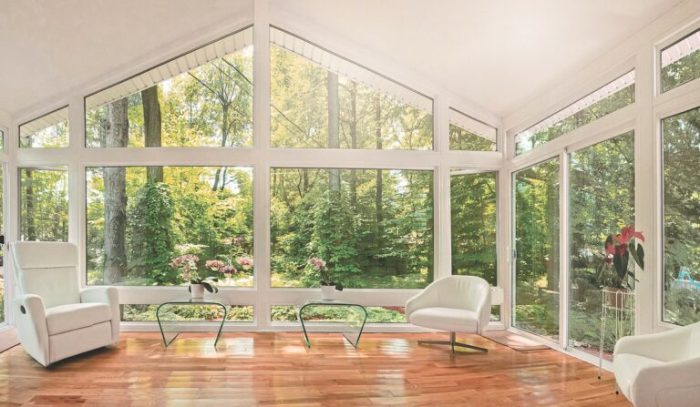
Properly managing labor is critical to the successful and timely completion of a glass enclosure sunroom project. Ignoring workforce considerations can lead to significant delays and cost overruns. A thorough understanding of labor requirements, potential shortages, and contractor expertise is essential for project success.Labor shortages in construction are a pervasive issue, impacting numerous building projects. This necessitates proactive planning and contingency strategies to mitigate potential delays.
A skilled and experienced workforce is vital to quality craftsmanship and adhering to project timelines. The availability and expertise of labor directly correlate to the project’s overall success.
Types of Labor Required
A glass enclosure sunroom project demands a diverse range of labor skills. This includes framing specialists for the structural support, experienced glaziers for the precise installation of glass panels, electricians for the electrical systems, and HVAC technicians for any integrated heating or cooling systems. Failure to account for these specialized needs can lead to significant delays.
- Framing: Experienced carpenters or framers are necessary for creating the structural framework of the sunroom. The quality of framing directly impacts the stability and longevity of the entire structure.
- Glazing: Specialized glaziers are required to install the glass panels with precision and safety. Their expertise ensures proper sealing, structural integrity, and aesthetics.
- Electrical: Qualified electricians are crucial for installing the necessary wiring, outlets, and lighting fixtures. Ensuring proper electrical safety and functionality is paramount.
- HVAC (if applicable): Integration of heating, ventilation, and air conditioning (HVAC) systems demands specialized knowledge and installation by qualified technicians. This is essential for optimal comfort and energy efficiency.
- Other: Additional labor may be required, such as roofers for modifications, masons for foundation work, or painters for finishing touches.
Impact of Labor Shortages
Labor shortages are a significant risk factor for any construction project. These shortages can result in delays ranging from a few weeks to several months. Project managers must account for potential delays due to labor unavailability when developing project schedules. Consider using subcontractors or finding specialized labor pools to mitigate risks. The current market trends for labor availability need to be carefully studied to create a comprehensive contingency plan.
Contractor Expertise and Timeline
The level of contractor expertise directly affects the project timeline. Experienced contractors often have established relationships with skilled labor and streamlined processes. This can lead to quicker turnaround times. Conversely, less experienced contractors might face challenges finding and managing qualified labor, potentially resulting in delays. Hiring a reputable contractor with a proven track record is vital for a smoother and more predictable project timeline.
Potential Weather Delays
Weather conditions can significantly impact construction timelines, particularly for glass enclosure sunrooms. Adverse weather (heavy rain, snow, extreme heat) can disrupt outdoor work and create delays. Experienced contractors often have contingency plans to address potential weather disruptions, but it is important to include these as potential delays in the initial timeline. For example, if a project requires glazing, delays due to inclement weather can extend the project significantly.
Labor Cost and Rates
Type of Labor | Typical Hourly Rate (USD) |
---|---|
Framing | $25-$45 |
Glazing | $30-$55 |
Electrical | $35-$60 |
HVAC | $40-$75 |
General Labor | $15-$25 |
Note: These are estimated rates and can vary significantly based on location, experience, and demand. Always get detailed quotes from contractors for specific labor needs.
Contingency Planning: How Long To Build Glass Enclosure Sunroom
Failing to plan for unforeseen circumstances is a recipe for project disaster, especially in construction. Proactive contingency planning is crucial for a successful sunroom build. It mitigates risks, manages delays, and ensures the project stays on track despite unexpected hurdles. A well-defined plan allows for adjustments and maintains the integrity of the project budget and schedule.
Importance of Contingency Plans
Contingency planning is not an optional add-on but a fundamental aspect of any construction project. It acknowledges that unforeseen issues are inevitable. These issues can range from material shortages to unexpected weather delays or even labor disputes. A well-structured contingency plan anticipates these potential problems and Artikels strategies for dealing with them, ensuring project completion within a reasonable timeframe and budget.
Failure to account for these variables often leads to project overruns and significant financial losses.
Common Unforeseen Issues and Management Strategies
- Material Shortages: This is a common occurrence, particularly for specialized or imported materials. A contingency plan should include alternative suppliers, pre-negotiated contracts with backup vendors, and a robust inventory tracking system to minimize the impact of delays. Having a secondary source for materials ensures a timely replacement if the primary supplier encounters difficulties.
- Unexpected Weather Events: Severe weather conditions can significantly disrupt construction schedules. The plan should include contingency dates for weather-related delays and alternate work strategies to maintain progress during inclement weather. Examples include covered work areas or indoor construction periods.
- Labor Disputes or Shortages: Unforeseen labor issues, such as strikes or shortages of skilled workers, can halt progress. The contingency plan should Artikel a strategy to secure backup labor quickly and include negotiation tactics to resolve any disputes. Having a roster of backup contractors and pre-approved agreements with them can help.
- Permitting Delays: Permitting processes can sometimes be lengthy and unpredictable. The plan should Artikel procedures to expedite the permitting process and include a buffer time in the schedule for potential delays. Knowing the local permitting regulations and having a streamlined application process is crucial.
- Design Changes: Changes in client requirements or unforeseen design challenges can necessitate modifications to the project scope. The plan should Artikel a process for managing these changes, including approvals, cost estimations, and updated timelines.
Mitigating Risks and Maintaining Project Timelines
Implementing a well-defined contingency plan allows for proactive risk mitigation. The plan should detail clear escalation procedures for addressing issues, enabling swift responses to prevent minor problems from escalating into major crises. By establishing clear communication channels and assigning responsibility for each contingency action, the project team can respond effectively and efficiently to unforeseen circumstances. Detailed documentation and reporting are essential for tracking progress, evaluating the effectiveness of contingency plans, and identifying areas for improvement.
Challenges in Managing a Sunroom Construction Project and Solutions
- Complex Design and Installation: Sunrooms often involve intricate framing, glazing, and insulation. Employing skilled professionals with experience in sunroom construction is critical to ensure accurate installation. Thorough pre-construction design reviews and precise construction plans can prevent costly errors.
- Integration with Existing Structures: Sunrooms need to be seamlessly integrated with existing house structures, which can lead to unexpected challenges. A thorough site survey and careful planning, coupled with experienced structural engineers, will ensure compatibility and minimize issues.
- Weather Dependence: Glass sunrooms are highly weather-dependent. The plan should account for potential weather delays and include appropriate protection measures for materials and workers during inclement conditions. Use of weather-resistant materials and scheduled indoor work periods during harsh weather are key.
- Cost Overruns: Unforeseen issues and material cost fluctuations can cause cost overruns. The plan should include a budget buffer and contingency funds to address unexpected expenses. Having a detailed budget with clear cost allocations and a monitoring system to track expenditures will minimize the risk of cost overruns.
Ultimate Conclusion
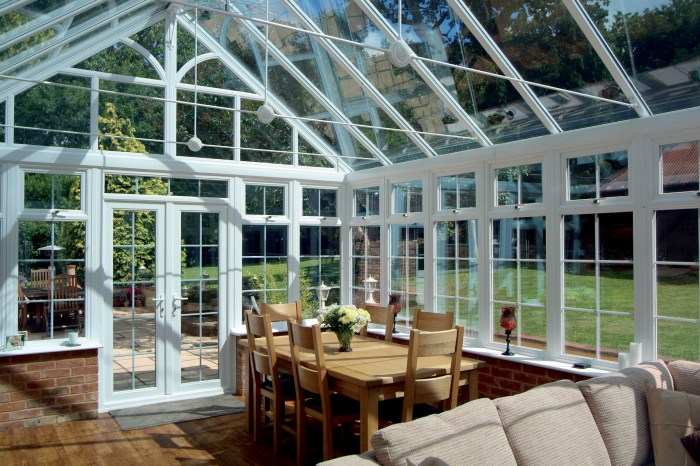
In conclusion, building a glass enclosure sunroom is a multifaceted project demanding careful planning and execution. From meticulous design to the final touches, every step contributes to the overall timeline. By understanding the factors influencing duration and employing strategic contingency plans, you can significantly increase the chances of a smooth and timely project completion. Ultimately, the time it takes to build your dream sunroom is a reflection of your meticulous planning and execution.
User Queries
How much does a glass sunroom cost?
The cost of a glass sunroom varies significantly depending on the size, materials used, and complexity of the design. A basic sunroom will be far less expensive than a high-end, custom-designed structure.
What are the most common delays in sunroom construction?
Weather conditions, material shortages, unforeseen structural issues, and permit delays are frequent causes of project delays. Thorough planning and contingency measures can help mitigate these risks.
What permits are required for a sunroom addition?
The specific permits required depend on local building codes. You will need to check with your local authorities to determine the necessary permits and approvals.
What are some alternative materials to glass for sunrooms?
Polycarbonate or acrylic panels are potential alternatives to glass. These options can offer varied aesthetic and performance characteristics, but their cost and durability can differ.