How much does it cost to manufacture a motorcycle? This ain’t just about raw materials; it’s a complex equation involving everything from the metal to the marketing. From the factory floor to the showroom, the costs add up fast. Different bike types and production methods dramatically impact the final price.
The manufacturing process for a motorcycle is a complex web of factors, spanning from the initial design to the final product. Materials, labor, and production methods all play crucial roles in determining the total cost. Understanding these factors is key to comprehending the financial landscape of motorcycle manufacturing.
Motorcycle Manufacturing Costs: How Much Does It Cost To Manufacture A Motorcycle
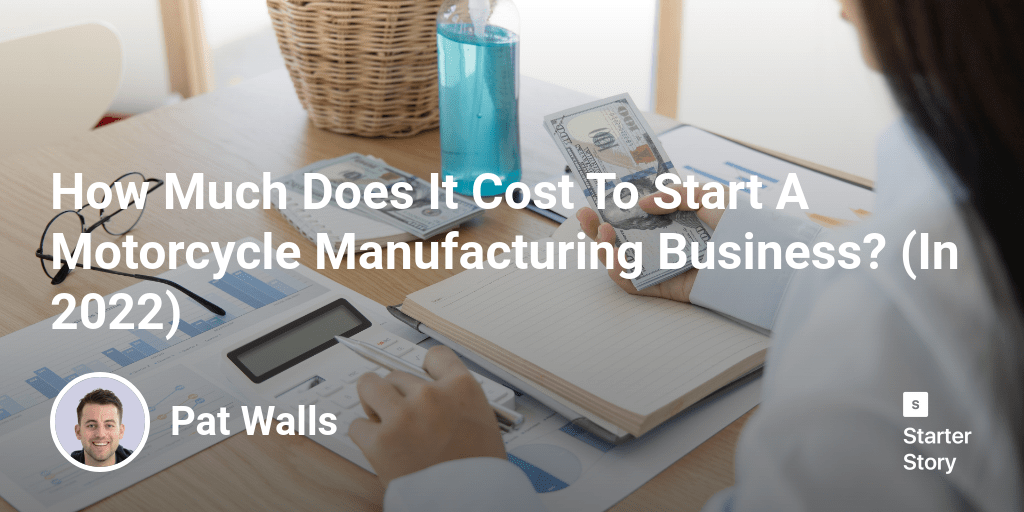
Motorcycle manufacturing, a complex process involving intricate engineering and specialized labor, incurs significant costs across various stages. Understanding these costs is crucial for businesses aiming to compete effectively in the market. Accurate cost analysis allows for precise pricing strategies, optimal resource allocation, and ultimately, profitability.
Major Components of Manufacturing Costs
Motorcycle manufacturing costs are multifaceted, encompassing a wide array of direct and indirect expenses. Direct costs are those directly attributable to producing a specific motorcycle, while indirect costs are incurred regardless of the specific model being produced. Understanding these categories is essential for establishing a comprehensive cost model.
Direct Costs
Direct costs are expenses that can be traced directly to the production of a specific motorcycle. These include raw materials, labor, and manufacturing overheads.
- Raw Materials: This category includes the cost of metals (steel, aluminum), plastics, rubber, and other components crucial to the motorcycle’s structure, engine, and accessories. The price of these materials fluctuates based on market conditions and supply chain dynamics. For instance, a rise in steel prices will directly impact the cost of manufacturing a motorcycle.
- Labor Costs: Direct labor comprises the wages and benefits paid to the workers directly involved in assembling the motorcycle, from welding and machining to painting and final quality checks. The level of skill and experience of the labor force significantly influences the labor costs.
- Manufacturing Overheads: This encompasses costs related to the production process itself, including machine maintenance, tool wear and tear, and factory utilities (electricity, water). These expenses, although not directly tied to a single motorcycle, are crucial for the manufacturing process to run smoothly.
Indirect Costs
Indirect costs are expenses that are not directly tied to a specific motorcycle but are necessary for the overall functioning of the manufacturing operation.
- Research and Development (R&D): Motorcycle manufacturers continuously invest in R&D to develop new models, improve existing designs, and enhance engine performance. These costs can range from basic design studies to extensive testing and prototyping.
- Marketing and Sales: Promoting the motorcycle through advertising, public relations, and sales campaigns contributes to the overall cost of bringing the product to market. Aggressive marketing campaigns can lead to increased sales and brand awareness, but also elevated costs.
- Administrative Expenses: General administrative costs, such as salaries of management personnel, office supplies, and rent, are considered indirect expenses.
- Quality Control: Ensuring the quality of each motorcycle produced is critical. Rigorous testing and inspection procedures, while essential for customer satisfaction, come with associated costs.
Cost Breakdown Across Production Stages
The cost of producing a motorcycle varies significantly across the different stages. A clear breakdown of these costs provides valuable insights for strategic decision-making.
Production Stage | Cost Categories |
---|---|
Component Procurement | Raw material costs, supplier costs, transportation |
Manufacturing Process | Direct labor, manufacturing overheads, machine maintenance |
Quality Control | Inspection costs, testing procedures, rework costs |
Assembly | Assembly labor, assembly line costs, quality checks |
Packaging and Shipping | Packaging materials, transportation costs, storage costs |
Material Costs
Motorcycle manufacturing hinges on the cost-effectiveness of its materials. Different materials offer varying degrees of strength, durability, and weight, impacting both the manufacturing process and the final product’s price. Understanding these variations is crucial for optimizing production and staying competitive in the market.
Frame Material Cost Differences
Frame materials play a pivotal role in a motorcycle’s overall strength and rigidity. Steel frames, while robust and readily available, often incur higher manufacturing costs compared to aluminum frames. Aluminum, being lighter, translates to potential fuel efficiency improvements, but its higher initial cost can be offset by reduced fuel consumption over the motorcycle’s lifespan. Composite frames, utilizing advanced materials like carbon fiber, offer exceptional strength-to-weight ratios, but their high production cost currently limits their widespread use.
The price fluctuations in these materials are also influenced by global supply chain factors and market demand.
Engine Material Cost Fluctuations
Engine materials directly affect the motorcycle’s performance and fuel efficiency. Aluminum, a lightweight metal, is frequently chosen for engine blocks due to its ability to dissipate heat effectively. However, the price of aluminum can fluctuate significantly based on global market conditions and the availability of raw materials. Steel engines, while heavier, can be more cost-effective in certain scenarios, especially when considering the lower initial cost.
These fluctuations impact the overall cost of the motorcycle.
Motorcycle Tire Cost Comparison
Motorcycle tires contribute to both the safety and the overall cost of a motorcycle. High-performance tires, designed for optimal grip and handling, typically come with a higher price tag compared to standard tires. The cost difference reflects the materials used, the manufacturing processes employed, and the performance specifications. Tire costs, like those of other materials, can fluctuate based on factors such as raw material costs and market demand.
Raw Material Costs per Unit
The following is a list of major raw materials and their approximate costs per unit. Keep in mind that these figures are estimates and can vary based on the specific supplier, quantity purchased, and market conditions.
- Steel: Approximately $X per kilogram
- Aluminum: Approximately $Y per kilogram
- Carbon Fiber: Approximately $Z per kilogram
- Rubber (for tires): Approximately $A per kilogram
- Plastics (for body panels): Approximately $B per kilogram
Component Material Cost Comparison
This table illustrates the comparative costs of various motorcycle component materials. These costs can fluctuate, and this table provides a general overview.
Component | Steel | Aluminum | Composite |
---|---|---|---|
Frame | $C | $D | $E |
Engine Block | $F | $G | – |
Wheels | $H | $I | $J |
Tires | $K | $L | $M |
Labor Costs
Labor costs represent a significant portion of the overall manufacturing expenses for motorcycles. Fluctuations in wages, labor regulations, and the demand for skilled versus unskilled labor directly impact the cost of production. Understanding these factors is crucial for evaluating the competitiveness and profitability of motorcycle manufacturing operations globally.
Regional Variations in Labor Costs
Labor costs exhibit substantial differences across geographical regions. Factors such as minimum wage laws, prevailing economic conditions, and the cost of living significantly influence wage rates. For example, labor costs in developed nations like the United States and Japan tend to be higher compared to developing countries in Southeast Asia or South America. This difference in labor costs is a key driver for companies seeking to optimize their manufacturing strategies.
Impact of Labor Regulations on Manufacturing Costs
Labor regulations, including minimum wage laws, overtime pay requirements, and worker safety standards, have a direct influence on manufacturing costs. Compliance with these regulations can increase labor costs. For instance, stricter environmental regulations in developed countries can mandate the use of more expensive, environmentally friendly materials or processes, which ultimately translate into higher manufacturing costs.
Skilled versus Unskilled Labor Costs
The demand for skilled labor in motorcycle manufacturing varies significantly. Positions requiring specialized training, such as engine assembly or electronics integration, command higher wages compared to unskilled roles like material handling or basic assembly. The availability and cost of skilled labor can influence the overall production cost structure, and companies may invest in training programs to address skill gaps.
A company might choose to focus on specific components, relying on skilled labor for critical aspects while outsourcing simpler tasks.
Labor Cost Breakdown by Manufacturing Stage
The labor costs associated with motorcycle manufacturing are not uniform across all stages. The assembly process, for instance, typically involves a larger workforce compared to testing and quality control. The precise breakdown varies depending on the complexity of the motorcycle model and the specific manufacturing techniques employed.
Average Hourly Wages for Motorcycle Manufacturing Jobs
Country | Assembly Worker (USD) | Technician (USD) | Quality Control Inspector (USD) |
---|---|---|---|
United States | 25-35 | 35-55 | 20-30 |
Japan | 30-40 | 45-65 | 25-35 |
Taiwan | 10-20 | 20-35 | 10-15 |
Vietnam | 5-10 | 15-25 | 5-10 |
Note: These figures are approximate averages and may vary based on specific skills, experience, and company policies.
Manufacturing Processes
The intricate process of motorcycle production involves a diverse array of manufacturing techniques, each contributing uniquely to the final product. Understanding these methods is crucial to comprehending the cost structure and the optimization potential within the industry. From initial material shaping to the final assembly, every step influences the overall manufacturing cost.The cost of a motorcycle is not simply the sum of its parts; it’s the culmination of the costs associated with each manufacturing process.
Factors such as material acquisition, labor wages, equipment maintenance, and energy consumption all play a critical role in shaping the final price. Furthermore, the choice of manufacturing process significantly impacts the cost-effectiveness and overall quality of the product.
Machining Processes
Machining, a fundamental process in motorcycle manufacturing, involves shaping raw materials into precise components. This includes operations like cutting, drilling, and grinding. The precision required in motorcycle parts necessitates sophisticated machining equipment, which can vary considerably in cost depending on its complexity and capacity. CNC (Computer Numerical Control) machining, for instance, allows for greater precision and efficiency, but the initial investment in the equipment is significantly higher than traditional methods.
This increase in precision, however, can translate to reduced waste and potentially lower labor costs in the long run. Furthermore, specialized machining techniques can be employed for specific components, such as intricate engine parts, adding to the overall cost.
Welding Techniques
Welding is critical for joining various motorcycle components, such as frames, exhaust systems, and sub-assemblies. Different welding methods, including arc welding, TIG welding, and MIG welding, offer varying degrees of precision and cost. The complexity of the weld, the size of the components, and the required quality all influence the choice and subsequent cost of the welding process.
For example, welding a complex frame structure may necessitate more sophisticated equipment and skilled labor, resulting in higher costs compared to welding simpler components.
Painting and Finishing
The final stage of the manufacturing process involves painting and finishing. Motorcycle frames and components require multiple layers of paint and clear coat to protect against corrosion and enhance aesthetic appeal. The cost of painting depends on the type of paint used, the complexity of the design, and the required quality standards. High-quality paints with superior corrosion resistance tend to increase the manufacturing cost.
Furthermore, the painting process may necessitate specialized equipment and controlled environments, such as electrostatic painting booths, further influencing the overall cost.
Assembly Line Configurations
Assembly lines are critical for streamlining motorcycle production. The layout of the assembly line, the number of workstations, and the division of labor all influence the efficiency and cost-effectiveness. A well-designed assembly line with optimal workflow can significantly reduce production time and costs. However, setting up a complex assembly line requires substantial upfront investment in equipment and infrastructure.
Automation in Motorcycle Manufacturing
Automation in motorcycle manufacturing plays a pivotal role in reducing labor costs and improving production efficiency. Automated welding systems, robotic assembly arms, and automated painting equipment can significantly increase output while potentially reducing labor costs. However, the initial investment in automation equipment can be substantial. Furthermore, retraining of the workforce to operate and maintain the automated systems is crucial to avoid disruptions in production.
The choice to automate a specific process hinges on a cost-benefit analysis that considers the initial investment versus the long-term savings in labor and production time.
Cost Comparison of Manufacturing Processes
Manufacturing Process | Cost Considerations | Cost-Effectiveness |
---|---|---|
Machining | Equipment complexity, precision requirements, material type | High precision components often justify higher cost |
Welding | Complexity of joint, type of welding, skilled labor | Sophisticated welds can be costly, but crucial for structural integrity |
Painting & Finishing | Paint quality, complexity of design, environmental controls | High-quality finishes increase cost but enhance product longevity and aesthetics |
Assembly Line | Layout, number of workstations, automation | Optimized assembly lines can improve efficiency and reduce costs |
Automation | Initial investment, maintenance, training | Long-term savings in labor and production time |
Equipment and Infrastructure Costs
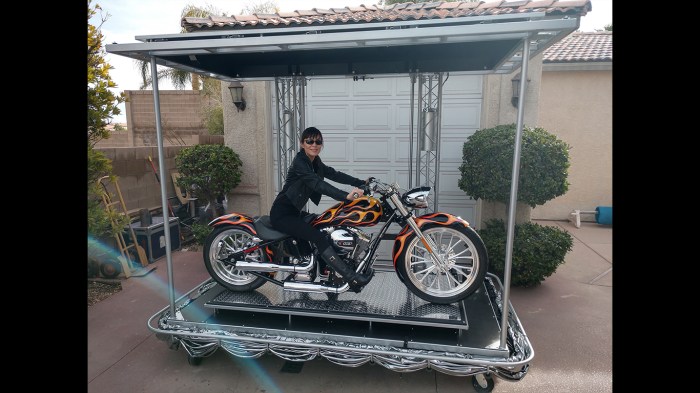
The acquisition and maintenance of specialized manufacturing equipment represent a significant portion of the overall motorcycle manufacturing cost. Factors like precision, durability, and automation directly influence the production output and, consequently, the final product cost. Understanding these costs is crucial for manufacturers to optimize their production processes and remain competitive in the market.
Specialized Manufacturing Equipment Costs
The cost of acquiring and maintaining specialized manufacturing equipment varies greatly depending on the complexity and sophistication of the machinery. These costs include not only the initial purchase price but also ongoing maintenance, repairs, and potential upgrades. The precise nature of the equipment will dictate the price tag, and different machinery will require varying maintenance schedules.
- CNC Machining Centers: These sophisticated machines are essential for precision component production. Their high initial cost, often exceeding $100,000, is offset by the increased efficiency and reduced error rates they provide. Ongoing maintenance costs are also substantial, requiring skilled technicians and specialized parts.
- Welding Robots: Automated welding robots are vital for high-volume production and ensure consistent weld quality. The cost of a robot, encompassing the purchase, setup, and integration into the production line, typically ranges from $50,000 to $200,000, with ongoing maintenance costs that depend on the frequency of use and the complexity of the welding processes.
- Assembly Robots: Essential for complex assembly tasks, these robots automate various procedures. Their cost can range from tens of thousands to hundreds of thousands of dollars, depending on the robot’s capabilities and the complexity of the assembly process. Maintenance and programming support contribute to the ongoing expenses.
Factory Space, Utilities, and Infrastructure Expenses
The facility’s size and location greatly impact the costs associated with factory space, utilities, and infrastructure. Adequate space is required to accommodate the equipment, production lines, and storage areas. Utility costs, including electricity, water, and heating, depend on the factory’s size and the local utility rates. Infrastructure expenses encompass building maintenance, security systems, and any necessary expansions or upgrades.
- Factory Space: The cost of factory space is dependent on location and size. Urban areas typically command higher rents compared to rural areas. Manufacturers need to weigh the pros and cons of different locations to minimize costs without compromising production efficiency.
- Utilities: Electricity consumption for operating machinery, lighting, and climate control plays a crucial role in utility costs. Water usage, though often less significant, also contributes. The cost of utilities fluctuates based on local rates and consumption levels.
- Infrastructure: This encompasses maintenance and repair costs for the factory’s building and equipment, security systems, and any necessary infrastructure upgrades. Upgrades can range from simple repairs to substantial expansions, adding to the ongoing expense.
Impact of Geographical Location on Infrastructure Costs
Geographical location significantly influences infrastructure costs. Areas with high labor costs might have lower equipment costs, but the opposite can also be true. Factors such as proximity to raw materials, transportation networks, and skilled labor availability all affect the overall expense of running a manufacturing facility.
- Proximity to Raw Materials: Manufacturers may choose locations close to their raw material suppliers to reduce transportation costs and delays. This strategy can impact the overall infrastructure costs if it requires significant investment in logistics infrastructure or transportation networks.
- Transportation Networks: Access to efficient transportation networks is critical for the smooth flow of materials and finished goods. Locations with poor transportation networks may lead to increased costs and delays.
- Labor Availability: The availability of skilled labor can affect infrastructure costs. Areas with a large pool of skilled workers may require less investment in training programs, reducing associated infrastructure costs.
Manufacturing Equipment Cost Breakdown
Equipment | Estimated Cost | Estimated Lifespan (Years) |
---|---|---|
CNC Milling Machine | $50,000 – $150,000 | 10-15 |
Welding Robot | $60,000 – $200,000 | 8-12 |
Assembly Robot | $30,000 – $100,000 | 7-10 |
Paint Booth | $20,000 – $50,000 | 5-8 |
Note: Costs are estimates and can vary significantly based on specific models, features, and local market conditions.
Quality Control and Testing Costs
The success of any motorcycle manufacturing process hinges on rigorous quality control. Defects, if not caught early, can lead to costly recalls, damaged reputations, and even safety hazards. Implementing effective quality control measures is an essential investment that safeguards the entire production cycle.
Importance of Quality Control, How much does it cost to manufacture a motorcycle
Quality control in motorcycle manufacturing is crucial for maintaining a high level of reliability, safety, and customer satisfaction. Consistent quality ensures that each motorcycle meets stringent performance and safety standards. This proactive approach minimizes the risk of malfunctions, injuries, and costly repairs, both for the manufacturer and the end-user.
Testing Procedures and Costs
Various testing procedures are employed to ensure the quality of components and finished motorcycles. These procedures can range from simple visual inspections to complex dynamometer tests. The costs associated with these tests vary significantly depending on the complexity and scale of the procedure. For instance, rigorous crash testing to assess structural integrity is considerably more expensive than verifying component dimensions.
Detailed testing protocols are often required for specific components like brakes, engines, and suspension systems. The cost of these tests also includes the specialized equipment, trained personnel, and laboratory facilities needed to conduct them.
Cost of Quality Assurance Measures
Quality assurance measures go beyond simply testing components and motorcycles. These measures include establishing quality standards, training personnel, and maintaining quality control systems. Training programs for inspectors, technicians, and engineers are a significant cost. Robust documentation and record-keeping systems are also vital, contributing to the overall quality assurance infrastructure. The cost of maintaining these quality assurance measures is an ongoing investment crucial for sustaining high quality standards throughout the production process.
Quality Control Measures and Their Costs
Implementing a comprehensive quality control plan involves various measures.
- Visual Inspection: This initial stage involves a meticulous visual examination of components and finished motorcycles. Costs are relatively low, primarily associated with labor and training. This ensures early identification of surface defects or obvious misalignments.
- Dimensional Measurement: Precise measurement of component dimensions is essential for ensuring compatibility and functionality. Costs depend on the accuracy of equipment and the number of components to be measured. This is vital for ensuring that parts fit correctly and function as intended.
- Functional Testing: This involves evaluating the performance of various motorcycle systems, such as the engine, brakes, and suspension. The cost varies greatly depending on the complexity of the testing equipment and the time required for each test.
- Performance Testing: This tests the overall performance of the motorcycle, including acceleration, braking, and handling. It involves sophisticated equipment and experienced personnel. Costs are relatively high due to the complexity and specialized equipment needed.
- Environmental Testing: Testing the motorcycle’s performance in different environmental conditions (temperature, humidity, altitude) can reveal vulnerabilities and ensure reliability. Costs vary according to the range and sophistication of environmental simulation setups.
- Crash Testing: Assessing the motorcycle’s structural integrity and occupant safety during impact is crucial. High costs are associated with specialized crash test facilities, equipment, and trained personnel.
Cost-Effectiveness Analysis of Quality Control Measures
Quality Control Measure | Cost | Effectiveness | Justification |
---|---|---|---|
Visual Inspection | Low | High (detects major defects early) | Quick, simple, and cost-effective initial screening. |
Dimensional Measurement | Medium | High (ensures precise fit) | Crucial for functionality and avoids costly repairs later. |
Functional Testing | Medium-High | High (identifies operational issues) | Ensures proper function of all systems. |
Performance Testing | High | High (comprehensive performance evaluation) | Essential for achieving desired performance characteristics. |
Environmental Testing | High | High (identifies environmental vulnerabilities) | Ensures reliable performance in diverse conditions. |
Crash Testing | Very High | High (assesses safety standards) | Essential for ensuring safety and compliance. |
Marketing and Distribution Costs
A successful motorcycle launch hinges not just on a well-engineered machine, but also on a robust marketing and distribution strategy. Understanding the costs associated with these critical aspects is paramount for accurate financial projections and eventual profitability. This section delves into the various facets of these costs, from promotion to logistics.
Marketing Costs
Motorcycle marketing strategies encompass a wide array of activities, each with associated costs. These strategies aim to build brand awareness, generate interest, and ultimately drive sales. Effective marketing campaigns often combine diverse approaches to maximize reach and impact.
- Advertising Campaigns: Advertising across various media channels, including television, print, online (social media, search engine marketing), and outdoor displays, is crucial. Costs vary dramatically based on the chosen media and the campaign’s scope. For example, a national television campaign targeting a broad audience will command significantly higher costs compared to a targeted social media campaign.
- Public Relations and Media Outreach: Building relationships with journalists, bloggers, and influencers can generate positive media coverage, increasing brand visibility and credibility. Costs may involve media kits, press releases, and event sponsorships.
- Promotional Events and Road Shows: Hosting motorcycle test rides, participating in trade shows, and organizing promotional events at dealerships or public venues are powerful tools. Costs include venue rentals, staffing, promotional materials, and potential contingency plans for unforeseen issues.
- Digital Marketing: Websites, search engine optimization (), social media management, and content creation are essential for online engagement. Costs include website development, services, social media advertising, and content creation (writing, photography, videography).
Distribution Costs
Distributing motorcycles efficiently from the manufacturer to the consumer involves several crucial steps, each with associated costs. Effective logistics are essential for timely delivery and minimizing financial burdens.
- Transportation and Logistics: Motorcycle transport from the manufacturing facility to dealerships requires careful planning and execution. Factors influencing costs include distance, volume, mode of transport (trucking, rail), and potential insurance or security measures. The cost is highly variable based on the distance and volume of shipments. Real-world examples include using specialized trucking for sensitive cargo or hiring third-party logistics providers.
- Warehousing and Inventory Management: Storing motorcycles in warehouses and managing inventory levels are critical for ensuring availability and minimizing stockouts. Costs include warehouse rental, handling equipment, storage space, and potential security measures. Efficient inventory management software can help optimize storage and reduce costs.
- Retailer Support: Supporting dealers with training, marketing materials, and sales incentives can contribute to a successful distribution network. Costs involve training programs, sales collateral, and possibly incentives for meeting sales targets. Successful examples include providing specialized sales training for motorcycle dealerships, ensuring they have the tools and knowledge to promote and sell the product.
Pricing Strategies
Developing a comprehensive pricing strategy for motorcycles involves careful consideration of manufacturing costs, material costs, labor costs, and all other factors discussed previously. This is further influenced by market demand, competitor pricing, and perceived value.
- Cost-Plus Pricing: Adding a markup to the total cost of production to determine the selling price. This is often used when precise cost figures are readily available. The markup percentage is dependent on industry standards and profit margins.
- Value-Based Pricing: Pricing based on the perceived value of the motorcycle to the customer. This strategy often requires thorough market research to understand customer preferences and determine the appropriate price point for a product.
Motorcycle Type Variations
The spectrum of motorcycle types, from the nimble sportbike to the robust touring machine, each presents unique manufacturing challenges and cost implications. Understanding these differences is crucial for appreciating the intricate interplay between design, materials, and the final price tag.
Cost Differences Across Motorcycle Types
Different motorcycle types necessitate varying levels of engineering sophistication, material choices, and production processes. These distinctions directly translate into variations in manufacturing costs. Sportbikes, renowned for their aerodynamic designs and high-performance engines, often involve more intricate machining and specialized components. Cruisers, with their emphasis on comfort and relaxed riding positions, typically use simpler yet robust designs. Touring bikes, engineered for long-distance travel, require advanced suspension systems, spacious storage compartments, and durable frames, all contributing to higher manufacturing costs.
Factors Influencing Cost Variations
Several factors contribute to the differing costs between motorcycle categories. Firstly, the complexity of the design plays a significant role. High-performance sportbikes, with their intricate aerodynamic shapes and high-revving engines, demand a more complex and precise manufacturing process, leading to higher material and labor costs. Secondly, the selection of materials impacts the cost. Advanced alloys for sportbikes and high-quality leather for cruisers influence the final price.
Thirdly, the quantity of components and their sophistication also affects the cost. Touring bikes, with their advanced electronic controls and sophisticated suspension systems, utilize more components and more intricate parts, increasing the overall cost.
High-Performance vs. Basic Models
The difference in manufacturing costs between high-performance and basic models is substantial. High-performance motorcycles, like sportbikes, often utilize premium materials like titanium or carbon fiber for critical components. These materials, owing to their properties and rarity, are significantly more expensive than the materials used in basic models. High-performance engines necessitate specialized machining and testing procedures, adding to the manufacturing overhead.
Conversely, basic models often rely on readily available and more affordable materials and manufacturing processes, resulting in lower costs.
Custom Motorcycle Production Costs
Custom motorcycles represent a unique challenge in terms of cost. The customization aspect introduces considerable variability. The unique design features, often hand-crafted elements, and the use of exotic or bespoke materials dramatically increase the cost. Furthermore, the labor required for individual customization adds significantly to the overall production expense. Extensive testing and quality control procedures are often necessary to ensure the quality and reliability of each unique design.
The intricacy of each custom design, from hand-stitched leather to hand-forged components, often necessitates specialized tools and equipment, contributing to a significant price increase.
Cost Comparison Table
Motorcycle Type | Material Costs | Labor Costs | Equipment Costs | Total Estimated Cost |
---|---|---|---|---|
Sportbike | High | High | High | High |
Cruiser | Medium | Medium | Medium | Medium |
Touring Bike | High | High | High | Very High |
Custom Bike | Very High | Very High | Very High | Extremely High |
Note: Costs are relative and can vary based on specific features, manufacturer, and market conditions.
Ending Remarks
So, building a bike isn’t cheap. The final price reflects a whole lotta stuff: materials, labor, tech, and even marketing. From the factory to the consumer, each step adds to the overall cost. Ultimately, it’s a balancing act between quality, price, and demand.
FAQ Overview
What’s the biggest cost driver in motorcycle manufacturing?
Labor costs, especially skilled labor, are often the largest factor, varying greatly by region and skill set. High-end components, complex designs, and specialized manufacturing processes can also drive up the overall cost.
How do different motorcycle types affect manufacturing costs?
Sportbikes, needing lighter materials and advanced components, usually cost more to produce than simpler cruisers. Custom bikes often command higher prices due to the bespoke nature of the build.
What’s the impact of automation on motorcycle manufacturing costs?
Automation can reduce labor costs, but initial investment in equipment is high. The ROI depends on production volume and the complexity of the manufacturing process.
How important is quality control in determining the final cost?
Rigorous quality control, while crucial for maintaining reputation, adds to the manufacturing cost. The more extensive the testing and inspection procedures, the higher the expense.