How much water to put in recycler rig is a crucial factor for efficient and safe recycling operations. Different recycling rig types, from residential to industrial, have varying water needs depending on the materials processed and the specific steps in the recycling process. Understanding these needs is essential for optimal performance and avoiding potential issues.
This guide will walk you through the various factors affecting water usage in recycling rigs, including rig type, water quality, procedures, troubleshooting, and water conservation techniques.
Understanding Recycler Rig Types
Yo, recycling is totally a game-changer, and these rigs are the real MVPs in the process. From tiny residential units to massive industrial setups, each rig is tailored for a specific job. Knowing the differences is key to maximizing efficiency and minimizing waste, which is seriously important.So, let’s break down the different types of rigs and their unique roles in the recycling world.
Think of it like choosing the right tool for the job – you wouldn’t use a tiny screwdriver to fix a car engine, right? Same goes for recycling!
Residential Recycling Rigs
Residential rigs are the everyday heroes of recycling. They’re designed for the average household, handling recyclables like paper, plastic, and glass. These are usually smaller and simpler, focusing on convenience and ease of use for the consumer. The design prioritizes compactness and minimal water usage, usually integrated with a compact system for easy operation.
Commercial Recycling Rigs
Commercial rigs are the powerhouses of the recycling game, handling massive volumes of materials from businesses. Think offices, restaurants, or stores – these rigs are built to handle the sheer amount of recyclables generated by these operations. The design is typically more robust and automated, with features like conveyor belts and automated sorting systems to accommodate higher throughput.
Water usage is likely higher due to the increased volume of material processed and potential need for cleaning components.
Industrial Recycling Rigs
Industrial recycling rigs are the titans of the industry. These monsters tackle the biggest and most complex recycling tasks, often handling materials like construction debris, metal scrap, or electronic waste. These rigs are extremely complex, often featuring advanced separation technologies and specialized equipment for handling hazardous materials. Water usage can vary drastically based on the materials processed and the specific cleaning requirements, sometimes even involving specialized cleaning solutions.
Components of a Recycling Rig and Water Usage
Understanding the different components of a recycling rig is essential for appreciating how water plays a crucial role. Different components have varying water needs, and these vary by rig type.
Component Name | Function | Approximate Water Requirements (per load/operation) | Notes |
---|---|---|---|
Sorting Conveyors | Transport and separate different materials | Low (minimal for material movement, but potentially higher if cleaning components) | Typically automated systems with minimal direct water use, but cleaning may require water. |
Shredders/Grinders | Reduce material size for processing | Moderate (for cleaning the components and rinsing the processed materials) | Water is used for cooling and cleaning the grinding components, and rinsing the processed materials. |
Washing Systems | Clean recyclables to remove contaminants | High (essential for cleaning) | The amount depends on the material being processed and the degree of contamination. This is critical for efficient recycling. |
Storage Bins/Hoppers | Temporary storage for materials | Low (minimal for maintenance) | Occasional cleaning or rinsing may require small amounts of water. |
Balers | Compresses recyclables into bales for transport | Low (minimal water use for maintenance) | Water may be used for lubricating the components or for periodic cleaning, but not during operation. |
Water Requirements Based on Rig Type
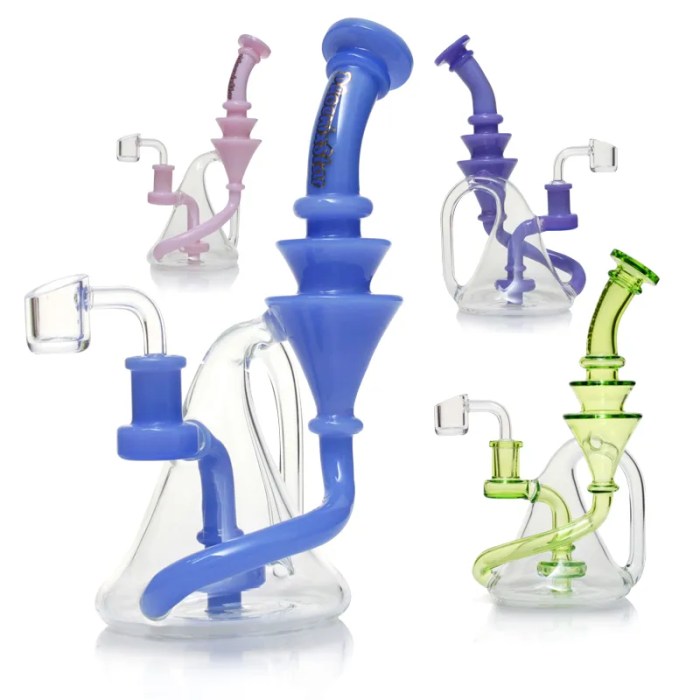
Yo, recycling rigs are totally different beasts, and the water they need depends majorly on the specific process. Think of it like making different kinds of smoothies – a strawberry smoothie needs different amounts of liquid than a mango one. Each recycling method has its own hydration needs.Different recycling processes demand varying amounts of water, and understanding these differences is crucial for efficient and effective operation.
This isn’t just about keeping things running smoothly; it’s about maximizing the output and minimizing waste. The amount of water used impacts the overall cost and environmental footprint of the recycling process.
Typical Water Volumes for Different Recycling Processes
Different recycling processes within various rig types have different water needs. This is because the chemistry and physical nature of the materials being processed change, affecting how much water is necessary for each step. Just like a recipe for baking a cake needs different ingredients and amounts for the batter, the frosting, and the final decoration, the amount of water required for different recycling processes varies significantly.
- Mechanical Recycling: This process often involves washing and sorting materials. Think of it like giving your recycling bin a good bath and then sorting the clean stuff. The water volume required is generally lower compared to other methods, focusing more on rinsing and cleaning. For instance, a plastic bottle recycling rig might use 10-20 gallons of water per ton of bottles for rinsing and cleaning.
The frequency of water use would likely be several times during the process, depending on the specific materials and rig design.
- Chemical Recycling: This method involves using chemicals to break down materials. This is like using special juices to separate and extract components from a fruit mixture. The water usage here is more complex and variable. The type and amount of chemicals used directly influence the water needed for the reactions and clean-up. Some processes might require significant water volumes for diluting or removing the chemicals.
An example could be a rig for recycling plastic bags using chemical hydrolysis, needing several hundred gallons of water per ton, potentially needing frequent additions for the reactions.
- Thermal Recycling: This is like using extreme heat to melt down materials. This often involves a lot of water for cooling. Think of melting down old aluminum cans – you’d need a lot of water to cool down the molten metal to make it usable. The water volume is quite high, and it’s used to cool the equipment and the recycled materials during the process.
A rig processing tons of paper using pyrolysis might use 50-100 gallons of water per ton, with the water needed for cooling and quenching the materials.
Comparative Water Usage Table
This table shows a simplified comparison of water usage per stage in the recycling process across different rig types. It highlights the differences in volume and frequency of water application, showing how each method differs. It’s important to remember that these are just estimates, and actual usage will vary based on specific rig design, material type, and operating conditions.
Recycling Rig Type | Washing/Cleaning (Gallons/Ton) | Chemical Reaction (Gallons/Ton) | Cooling/Quenching (Gallons/Ton) | Frequency |
---|---|---|---|---|
Mechanical (Plastic Bottles) | 10-20 | 0 | 0 | Multiple times |
Chemical (Plastic Bags) | 20-50 | 100-500+ | 50-100 | Several times |
Thermal (Paper) | 5-10 | 0 | 50-100 | Multiple times |
Water Quality Considerations

Yo, recycler rig owners, lemme break down the crucial role water quality plays in your operation. Think of it like this: you wouldn’t put premium gas in a junker, right? Similarly, using subpar water in your recycling rig is gonna seriously impact your results. From efficiency to the final product, water quality is key. This ain’t your grandma’s water cooler; this is the stuff that makes your recycler rig sing!
Importance of Water Quality for Optimal Recycling Performance
Water quality directly impacts the efficiency and effectiveness of the recycling process. Contaminants and impurities can interfere with the separation and purification stages, leading to reduced yields and lower-quality recycled materials. This isn’t just about getting the job done; it’s about doing it right.
Acceptable Levels of Contaminants and Impurities
The acceptable levels of contaminants and impurities in recycling water vary depending on the specific recycling process and the materials being processed. Excessive levels of certain substances can foul the machinery, hindering its performance and potentially causing long-term damage. It’s like throwing a wrench into the works – you want to keep those contaminants at bay.
Effects of Different Water Qualities on the Recycling Process
Different water qualities have distinct effects on the recycling process. Hard water, for example, can lead to scale buildup in the equipment, reducing its efficiency over time. Conversely, water with excessive suspended solids can clog filters and hinder the flow of the recycling process. This isn’t rocket science, but understanding these nuances is crucial for maximizing your rig’s performance.
Water Quality Parameters and Acceptable Ranges
Maintaining optimal water quality involves monitoring various parameters. Here’s a breakdown of critical factors and their ideal ranges:
Parameter | Units | Acceptable Range | Consequences of exceeding range |
---|---|---|---|
Suspended Solids | ppm | 0-10 | Clogging of filters, reduced flow rate, premature equipment failure. |
Total Dissolved Solids | ppm | 0-500 | Scaling of equipment, reduced efficiency, potential for equipment corrosion. |
pH | 6.5-8.5 | Corrosion of equipment, damage to materials being recycled, and negative impacts on the overall process. | |
Turbidity | NTU | 0-5 | Impeded visibility, hindering proper filtration, and potential contamination issues. |
Total Organic Carbon | ppm | 0-50 | Reduced efficiency, clogging of filters, and potential for contamination in recycled products. |
This table provides a general guideline. Specific ranges may vary based on the type of recycling process and materials being processed. Consult with equipment manufacturers and recycling experts for tailored recommendations. Don’t be afraid to ask questions; it’s all about keeping your rig running smoothly.
Water Usage Procedures and Methods
Yo, recycling rig owners! Getting the water right in your rig is crucial for a smooth, efficient operation. This ain’t no amateur hour; we’re talking about precision and safety. From the high-pressure sprays to the immersive soaking, we’ll break down the best ways to get your rig hydrated, and keep it that way.Understanding the ideal water pressure and flow rate, along with the proper safety protocols, is key to maximizing your recycling output and minimizing potential hazards.
Different recycling rig types require different approaches, so knowing your rig’s specs is essential.
Water Introduction Methods
Different recycling rigs use different methods for introducing water. Some rigs are built for high-pressure sprays, while others rely on submersion tanks for more controlled, even hydration. Knowing the method is critical to the success of the entire process.
- Spray Nozzles: These are great for large-scale recycling operations. High-pressure spray nozzles are effective for quickly wetting materials, but proper nozzle selection is critical. Nozzles with adjustable spray patterns can cover the material evenly, ensuring all parts get the necessary hydration. The pressure should be adjusted according to the material being recycled and the desired saturation level.
Too much pressure can damage the material or equipment, while too little pressure might not effectively wet the material. Think of it like a professional car wash; you want the right amount of pressure to get the job done right.
- Immersion Tanks: These are ideal for smaller recycling projects, or when precise hydration is needed. Materials are fully immersed in water, providing a consistent level of moisture. The optimal immersion time varies greatly depending on the material type, but the goal is to saturate without causing damage or excessive water buildup. Imagine a giant bathtub for your recycling material, ensuring thorough hydration.
Optimal Water Pressure and Flow Rate
Finding the sweet spot for water pressure and flow rate is crucial. Over-pressurized water can damage the equipment or the materials, while under-pressurized water might not be effective enough to achieve the desired outcome.
Water Introduction Method | Optimal Pressure (psi) | Optimal Flow Rate (gpm) | Explanation |
---|---|---|---|
Spray Nozzles | 50-150 | 2-10 | Adjust pressure and flow based on material type and desired saturation. Higher pressure is generally used for tougher materials, and lower pressure for more delicate materials. |
Immersion Tanks | 0-5 | 0.5-2 | Lower pressure is vital to avoid damaging materials. Flow rate depends on the tank size and the desired soaking time. |
Safety Procedures
Safety is paramount when working with water systems. Always wear appropriate safety gear, like safety glasses, gloves, and sturdy footwear. Never operate equipment near water sources without the necessary safety measures in place. Make sure you have a properly grounded electrical system. Consider using specialized gloves and footwear for added protection, particularly if handling potentially hazardous materials.
Always prioritize safety when working with water systems. Follow all safety protocols to avoid accidents.
Step-by-Step Procedure for Adding Water to a Specific Rig Type, How much water to put in recycler rig
Let’s take a look at a step-by-step procedure for adding water to a conveyor-belt recycling rig using spray nozzles.
- Preparation: Shut down the conveyor belt and all associated equipment. Verify that the power supply is disconnected and the water system is turned off. Inspect the spray nozzles for any damage or blockages.
- Water Source Connection: Connect the water supply line to the recycling rig’s water input. Make sure all connections are tight and leak-free.
- Pressure Adjustment: Adjust the water pressure to the optimal range (e.g., 75 psi). Use a pressure gauge to ensure accuracy.
- Flow Rate Control: Adjust the flow rate to the desired level (e.g., 5 gpm). This can be done by using a flow meter or regulating valve.
- Material Saturation: Begin the conveyor belt operation. Monitor the material saturation level to ensure that the material is adequately hydrated.
- Monitoring and Adjustment: Continuously monitor the water pressure, flow rate, and material saturation. Adjust as needed to maintain optimal hydration.
- Shutdown: Once the material is properly hydrated, turn off the water supply and the conveyor belt. Disconnect the water supply line and all associated equipment.
Troubleshooting Water Issues
Yo, recycling rig owners! Water problems can totally throw a wrench in your whole operation. Knowing how to identify and fix these issues is key to keeping your rig running smooth as silk, and avoiding those major breakdowns that’ll have you calling your recycling guru for help. Let’s dive into the nitty-gritty of water troubleshooting.Understanding the potential pitfalls and having a solid plan to address them is crucial for maintaining a successful recycling operation.
We’ll cover common problems, from minor annoyances to major disasters, and give you the tools to fix them yourself. This is your ultimate guide to water-related recycling rig problems.
Common Water-Related Problems
Water issues in recycling rigs can range from minor annoyances to major headaches. Knowing the telltale signs of these problems is the first step in finding a solution. Common issues include leaks, clogs, and inadequate water flow. These issues can stem from various factors, such as worn-out components, improper installation, or the quality of the water being used.
Leaks
Leaks in recycling rigs can be frustrating, leading to wasted water and potential damage. They can range from tiny drips to gushing torrents, impacting your recycling process and your budget. Pinpointing the source of the leak is essential. Possible causes include worn seals, cracked pipes, or loose connections. Addressing leaks promptly is crucial to prevent further damage and costly repairs.
- Signs of a Leak: Look for water pooling around the rig, damp spots on the floor, or unusual water levels in the reservoir. A steady drip, drip, drip is a classic sign. Also, keep an eye out for any unusual noises like hissing or gurgling, which might indicate a leak somewhere in the plumbing.
- Solutions: Tighten loose connections, replace worn seals or gaskets, and repair any damaged pipes. Using leak-detection tools can pinpoint the exact location of the leak quickly. If the leak is severe, consult a professional for help.
Clogs
Clogs in the recycling rig’s water system can disrupt the entire process. Imagine trying to squeeze through a tiny pipe! This can happen due to debris, sediment, or even biological growth. Regular maintenance can significantly reduce the likelihood of clogs.
- Signs of a Clog: Reduced water flow, uneven water distribution, or the recycling process slowing down are all signs of potential clogs. Check for unusual pressure fluctuations or noises, like gurgling, in the water system.
- Solutions: Use a specialized clog remover designed for recycling systems. You can also try flushing the system with a strong stream of water. If the clog persists, you might need to dismantle the affected section to remove the obstruction. Avoid using harsh chemicals that could damage the system’s components.
Inadequate Water Flow
An inadequate water flow can impact the efficiency of your recycling rig. A slow trickle might not be enough to process the materials, resulting in a drop in throughput and output quality.
- Signs of Inadequate Flow: The recycling process might seem sluggish or incomplete. The water pressure might feel noticeably weak, and the materials being processed might not be properly rinsed or cleaned.
- Solutions: Check for clogs in the water lines or filters. Ensure the water pump is functioning correctly. If the issue persists, consult a professional to diagnose the problem.
Preventative Maintenance
Regular preventative maintenance can go a long way in minimizing water issues. This includes checking for leaks, cleaning filters, and ensuring proper water quality.
- Regular Inspections: Visually inspect the water system regularly for leaks, cracks, or any signs of damage. This includes checking connections, pipes, and seals. Checking for unusual buildup in the water lines or pumps is essential.
- Proper Filter Maintenance: Replace filters according to the manufacturer’s recommendations. Dirty filters can restrict water flow and cause clogs.
- Water Quality Monitoring: Monitor the water quality to ensure it meets the requirements of your recycling rig. If the water is contaminated, it could damage equipment or hinder the recycling process.
Troubleshooting Table
Problem | Cause | Solution |
---|---|---|
Leaks | Worn seals, cracked pipes, loose connections | Tighten connections, replace seals, repair pipes |
Clogs | Debris, sediment, biological growth | Use a clog remover, flush the system, remove obstructions |
Inadequate Water Flow | Clogged lines, faulty pump, low water pressure | Check for clogs, ensure pump functionality, check water pressure |
Water Conservation Strategies: How Much Water To Put In Recycler Rig
Saving H2O in your recycling rig is like scoring major points in a water-wise Olympics! Smart strategies can drastically cut down on water use without sacrificing efficiency, which is totally rad. Think of it as a win-win for the environment and your bottom line.Implementing water conservation techniques in recycling rigs is a serious game-changer, especially for large-scale operations.
It’s about maximizing output while minimizing your water footprint, which is a total win-win.
Water-Efficient Recycling Processes
Different recycling processes have varying water needs. Some methods, like advanced mechanical sorting, can significantly reduce the need for copious amounts of water compared to older methods. Optimizing these processes is key to achieving a serious water-saving performance.
- Air Classification: This method uses air to separate materials based on density, minimizing the need for water-based washing. It’s like a high-tech air-powered sorting system, making it ideal for materials like plastics and metals. Imagine a giant, industrial-strength air-sorter, separating materials with precision. It’s a huge win for water conservation.
- Magnetic Separation: This technique uses magnets to remove ferrous metals from the recycling stream. No water needed! It’s like having a giant magnet that pulls out all the metal bits, making it ideal for sorting scrap metal and preventing contamination of other materials. This method is extremely efficient in reducing water usage, and is a crucial element in a modern, sustainable recycling facility.
- Advanced Mechanical Sorting: These systems use sophisticated equipment to sort materials based on size, shape, and density. The equipment is designed to reduce the amount of water needed compared to traditional methods, and is often used in tandem with other water-saving techniques. These systems are becoming increasingly popular as they significantly improve efficiency and reduce water usage.
Minimizing Water Usage in Existing Processes
Even if you’re already using a recycling rig, there are ways to minimize water usage without sacrificing quality. Implementing these strategies can make a huge difference in your water bill and your environmental impact.
- Improved Washing Techniques: Using high-pressure spray nozzles and precise water delivery systems can drastically reduce the amount of water used in the washing process. It’s like a water-saving showerhead for your recycling rig! Instead of using a flood, use controlled jets to get the job done. This is a critical step in optimizing your recycling process, especially for plastic recycling, and can reduce water consumption by 30-50% in some cases.
- Water Recycling Systems: Implementing closed-loop systems for recycling water used in the process is a game-changer. It’s like having a water-recycling machine, capturing and reusing the wastewater. This technique can significantly reduce water consumption, which is a crucial element in a sustainable recycling facility. These systems collect and treat wastewater for reuse in the process, drastically cutting down on fresh water usage.
- Efficient Cleaning Procedures: Implementing rigorous cleaning schedules, using less harsh chemicals, and employing advanced cleaning technologies can help minimize the amount of water needed to clean equipment. It’s like a smart cleaning regime that ensures you get the job done with less water. This can include using specialized cleaning agents that require less water, or cleaning equipment more frequently with less water.
Implementing Water Conservation Measures in Recycling Rigs
Real-world examples showcase how water conservation measures can be successfully integrated into recycling operations. These case studies demonstrate the viability and impact of these strategies.
Recycling Facility | Conservation Method | Impact |
---|---|---|
ABC Recycling | Water recycling system | Reduced water consumption by 40% |
XYZ Recycling | Advanced mechanical sorting | Decreased water usage by 25%, increased sorting accuracy |
Green Recycling Solutions | Improved washing techniques | Reduced water usage by 15%, improved material quality |
Illustrative Examples of Water Usage in Different Rigs
Recycling rigs, whether they’re crushing cans or shredding plastics, all have one thing in common: they need water, sometimes a lot of it. Just like a Hollywood blockbuster needs a huge budget, these rigs need a precise amount of water for optimal performance. Understanding how different rigs use water is key to efficiency and preventing costly downtime.Different recycling rigs have vastly different water needs, just like a high-budget movie set might have different water requirements than a low-budget indie flick.
Each rig has a specific process and a unique relationship with the water it uses. Let’s dive into some real-world examples to see how these processes work.
Plastic Recycling Rig Water Usage
Plastic recycling, from PET bottles to styrofoam, demands careful water management. The process often involves cleaning and prepping the plastic before it can be processed.
- Pre-Washing: Plastic streams, often from sorting or collection, are washed to remove debris, dirt, and other contaminants. This is crucial to ensure the plastic is clean enough for the next step. Water pressure and flow rates are critical for effective cleaning without damaging the plastic.
- Cleaning & Sorting: Different types of plastic require different cleaning methods. For example, PET bottles often need a harsher cleaning solution than HDPE containers. Specific cleaning agents and the amount of water used depend on the plastic type and the degree of contamination.
- Water Treatment: The wastewater from the washing process needs to be treated before discharge. This is critical to environmental protection. Treatment methods, including filtration and sedimentation, remove pollutants from the water before it’s released back into the environment. >Water quality standards are essential to prevent environmental damage.
Metal Recycling Rig Water Usage
Metal recycling, from aluminum cans to steel scrap, also uses water, though often in different ways than plastic recycling.
- Cooling: Melting down metals, especially aluminum, requires a significant amount of water for cooling. This is crucial to prevent overheating and maintain the temperature of the metals during the process. The water must be carefully monitored to prevent contamination of the metal.
- Washing: The metal components are washed to remove impurities, like dirt or other metals, before the recycling process. Water jets or sprays are commonly used for this step, and the amount of water and the pressure of the jets need to be precisely calibrated.
- Cleaning: Depending on the type of metal, additional cleaning methods, like chemical treatments, may be used. The amount of water used in these processes depends on the concentration of the cleaning solution and the desired level of cleanliness.
Illustrative Water Flow Pathways
Imagine a simplified flow diagram for a plastic recycling rig. Water enters a system, flowing through various stages of cleaning. The cleaned plastic is then processed further, while the wastewater is directed towards a treatment plant. This illustrates the importance of controlling water flow in each step to prevent contamination and ensure optimal output. Similarly, in a metal recycling rig, water flows through cooling systems, washing stations, and other stages of the process.
Rig Type | Water Usage | Procedure |
---|---|---|
Plastic Recycling | Pre-washing, cleaning, sorting, water treatment | Different water pressures and solutions for different plastics, wastewater treatment before discharge |
Metal Recycling | Cooling, washing, cleaning | Water for cooling molten metals, washing to remove impurities, potential chemical treatments |
Ending Remarks
In conclusion, careful consideration of water volume, quality, and application methods is paramount for successful recycling operations. Following the guidelines provided in this comprehensive guide, you can optimize your recycling rig’s performance while minimizing water consumption. Remember to always prioritize safety and consult the manufacturer’s instructions for specific rig models.
FAQ Corner
How often should I add water to the recycler rig?
The frequency of water addition depends on the rig type, the recycling process, and the material being processed. Refer to the manufacturer’s instructions or the specific recycling process guidelines for the rig in use.
What kind of water should I use in the recycler rig?
Ideally, use clean, potable water. Avoid using water with excessive contaminants or impurities that could affect the recycling process. Check the manufacturer’s recommendations for specific water quality requirements.
What are some common causes of leaks in the recycler rig’s water system?
Common causes of leaks include loose connections, damaged hoses, and worn-out seals. Regular maintenance and inspections can help prevent these issues. Consult the manufacturer’s guidelines for specific maintenance recommendations.
What are the safety precautions when working with the water system in the recycler rig?
Always wear appropriate personal protective equipment (PPE) such as safety glasses and gloves. Ensure the water system is turned off and properly secured before any maintenance or repair work. Follow safety guidelines provided by the manufacturer.