How to bend aluminum tubing, a crucial skill for various applications, is explored in this comprehensive guide. Understanding the properties of aluminum, selecting the right tools, and mastering different bending techniques are key to achieving professional-quality bends. We’ll cover everything from basic hand bending to sophisticated machine methods, ensuring you’re well-equipped to tackle any aluminum tubing project.
This guide delves into the essential aspects of aluminum tubing bending, providing detailed instructions and insights. From understanding the different types of aluminum tubing to mastering various bending techniques, you’ll gain a practical knowledge base. We’ll also discuss the factors influencing bend quality and how to troubleshoot potential issues, ensuring successful bends every time.
Introduction to Aluminum Tubing Bending
Aluminum tubing, a versatile material in various industries, offers a unique blend of strength and formability. Its lightweight nature and excellent corrosion resistance make it a popular choice for applications requiring both structural integrity and aesthetic appeal. Understanding its properties, particularly its behavior during bending, is crucial for achieving precise and durable results.Aluminum tubing’s malleability and ductility are key characteristics enabling its bending.
Malleability describes the material’s ability to be shaped by hammering or pressure without fracturing. Ductility, on the other hand, refers to its capacity to be drawn or stretched into wires or shapes without breaking. These properties, combined with the diverse tempering options, allow for a wide range of bending techniques and applications.
Aluminum Tubing Types
Aluminum tubing is available in various temper designations, each influencing its bendability and suitability for specific applications. These temper designations reflect the heat treatment processes applied during manufacturing. Understanding these distinctions is vital for selecting the right tubing for a given project.
Bending Characteristics Comparison
Different temper designations directly affect the bending characteristics of aluminum tubing. The table below highlights the typical bendability, hardness, and suitable applications for various types.
Tubing Type | Bendability | Hardness | Suitable Applications |
---|---|---|---|
Hard Temper (e.g., H18) | Lower | High | Structural components requiring high strength, where slight bending is expected, such as automotive parts. |
Soft Temper (e.g., O) | High | Low | Applications demanding high bendability, such as decorative elements or components requiring intricate shapes, like architectural designs. |
Half-Hard Temper (e.g., H14) | Medium | Medium | General-purpose applications where a balance between bendability and strength is desired. Ideal for many industrial piping systems. |
The selection of the appropriate aluminum tubing type hinges on the specific requirements of the project. A project demanding high bendability, such as a decorative display, would benefit from soft temper tubing. Conversely, applications prioritizing structural integrity, such as in aerospace or automotive, would often utilize hard temper tubing. Half-hard temper strikes a balance between these extremes, making it suitable for a broader spectrum of applications.
Tools and Equipment for Bending Aluminum Tubing
Unveiling the artistry of shaping aluminum tubing requires a discerning eye and a keen understanding of the tools that sculpt these metallic forms. Mastering the techniques of bending aluminum tubing hinges on selecting and employing the appropriate equipment. From precision bending mandrels to powerful tube benders, each tool plays a crucial role in achieving the desired curves and contours.Aluminum tubing, with its malleability and strength, presents unique challenges and rewards in the bending process.
Choosing the right tools ensures not only the desired shape but also the safety and efficiency of the operation. Understanding the functionality of each tool is paramount to successful bending projects.
Essential Bending Tools, How to bend aluminum tubing
A variety of tools are crucial for shaping aluminum tubing. The right tools translate into precision and safety, allowing the creation of intricate designs and structural components. Selecting the appropriate tool for the job is essential to avoid unnecessary complications or potential damage.
- Tube Benders: These machines are designed for consistent and repeatable bends in various shapes and sizes. Hydraulic tube benders, for example, are particularly useful for larger or heavier-duty aluminum tubing, offering significant leverage for complex bends. The ability to adjust the bend angle and radius on these machines is crucial for producing customized shapes.
- Bending Mandrels: Mandrels, often cylindrical or shaped to match the desired curve, are used for creating precise bends, especially for smaller diameter tubing. These mandrels provide a template that allows for the accurate bending of the tube, often with a smaller radius than a tube bender would allow. Their precision is especially valuable in creating tight, controlled curves.
- Rotary Tube Benders: These tools excel in producing consistent, controlled bends, especially for intricate patterns and curves. They offer a rotational movement, allowing for precise control over the bending angle and radius. This characteristic makes them suitable for high-volume production or projects with repeating curves.
- Hand Benders: Ideal for smaller jobs, hand benders offer manual control over the bending process, enabling the creation of precise shapes. They are particularly useful for smaller diameter aluminum tubing or prototyping where a high degree of accuracy is not critical.
Safety Precautions
Safety should always be prioritized during the bending process. Aluminum tubing, while strong, can still be damaged if not handled properly. Proper safety precautions are essential for both the well-being of the worker and the integrity of the work itself.
- Eye Protection: Always wear safety glasses or goggles to protect your eyes from flying debris or metal shards that may occur during the bending process.
- Personal Protective Equipment (PPE): Wear appropriate gloves and protective clothing to shield your skin from contact with sharp edges or potential burns from heat generated during bending.
- Proper Tool Handling: Use the right tools for the job, following the manufacturer’s instructions carefully. Ensure that all tools are properly maintained and in good working order. Avoid bending tubing that is excessively cold or brittle.
- Secure Work Area: Maintain a clear and organized work area to prevent accidents. Use appropriate supports and clamps to prevent the tubing from slipping or moving during the bending process. Ensure the work surface is stable and level.
Bending Tool Specifications
The table below Artikels various bending tools and their specific applications, emphasizing safety precautions to be considered.
Tool | Description | Application | Safety Precautions |
---|---|---|---|
Tube Bender (Hydraulic) | Machine for bending tubing using hydraulic pressure. | Large diameter tubing, complex shapes. | Use appropriate safety glasses and clothing. Ensure proper clamping and securing of the tubing. |
Bending Mandrel | Cylindrical or shaped tool inserted into tubing to create a precise bend. | Small diameter tubing, precise curves. | Wear gloves to protect hands from sharp edges. Use appropriate lubricants if necessary. |
Rotary Tube Bender | Rotates the tube for consistent bends. | Complex patterns, high-volume production. | Ensure secure clamping and support of the tube. Use appropriate eye protection. |
Hand Bender | Manual tool for bending smaller tubing. | Small diameter tubing, prototyping. | Be cautious when applying force. Use protective gloves. |
Bending Techniques and Procedures
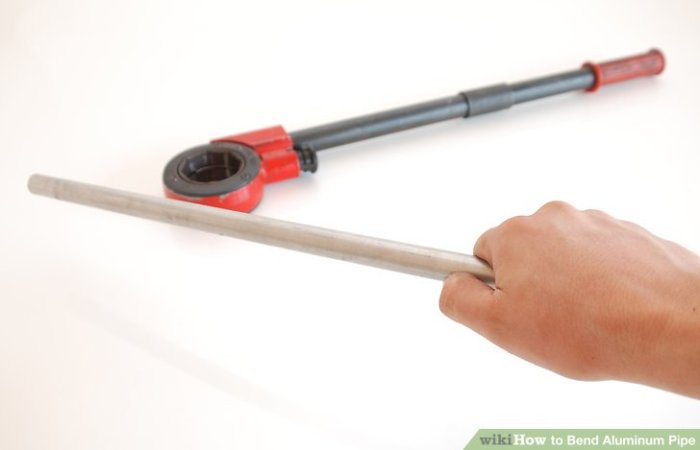
Unveiling the artistry of shaping aluminum tubing requires a deep understanding of its malleability and the techniques employed to achieve desired forms. From delicate curves to robust angles, the right approach can transform raw material into functional and aesthetically pleasing structures. Mastering these bending methods allows for precision and control, ensuring the final product meets the exacting standards of design and application.
Hand Bending Techniques
Hand bending, a time-honored method, offers a degree of control and adaptability not always achievable with machinery. Its versatility makes it ideal for prototyping, small-scale production, and intricate designs. The tactile nature of hand bending fosters a deeper connection with the material, allowing for adjustments and modifications during the shaping process.
- Preparation is Paramount: Ensure the tubing is clean, free of burrs, and properly supported. Lubrication, often a paste or a light oil, is crucial for reducing friction and enhancing the bending process. Appropriate clamping or securing mechanisms are vital to prevent slippage or unwanted movement.
- The Initial Bend: Employ a gradual and consistent force to achieve the desired initial bend. The bending tool, often a specialized hand bender, should be positioned correctly to minimize stress concentrations and ensure even pressure distribution. Consider the material’s yield point, which is the point at which the material starts to deform permanently.
- Refinement and Finalization: The initial bend should be evaluated and adjusted as needed. Repeat the bending process using the tool and technique, meticulously ensuring accuracy. Accurate measurements and meticulous technique will yield the desired bend angle, and the final result should be checked against specifications.
Machine Bending Techniques
Machine bending offers greater speed, precision, and repeatability for larger-scale production or when consistent bends are required. Automated equipment ensures high-quality results and reduces human error. Different machine types are designed for various bend radii and tube sizes, each with unique operating parameters.
- Setting Up the Machine: The tubing must be securely clamped within the machine’s designated area. Precise measurements are critical, and appropriate settings must be entered into the machine’s control panel.
- Initiating the Bending Process: Activate the bending mechanism and allow the machine to complete the bending process. The process should be monitored to ensure the machine operates as expected.
- Final Inspection and Verification: After the bending cycle, the tubing should be carefully inspected for any imperfections or deviations from the intended shape. Verify the final bend against the specified dimensions and tolerances. A post-bend check for uniformity is essential for quality assurance.
Importance of Support and Clamping
Proper support and clamping during bending are essential for preventing deformation, ensuring accuracy, and maintaining the integrity of the tubing. Support points must be strategically placed to distribute the bending force evenly.
- Support Mechanisms: Utilizing appropriate supports, such as bending fixtures or specialized jigs, can minimize the risk of buckling or kinking.
- Clamping Devices: Clamping devices secure the tube and maintain the alignment during the bending process. The chosen clamping methods must be robust enough to prevent movement and ensure the desired bend angle.
- Positioning: Precise positioning of the tube is crucial for achieving accurate bends. A well-defined and supported setup is essential for success.
Creating Different Bend Shapes
The possibilities for shaping aluminum tubing are extensive. Beyond simple 90-degree bends, various techniques allow for curves, spirals, and intricate patterns.
- 90-Degree Bends: These are fundamental bends, easily achievable with both hand and machine methods. Specific techniques are applied for each method, such as the use of specialized bending tools.
- Curves: Various radii and shapes can be created. Careful consideration of the bend radius and the material’s properties is necessary to avoid excessive stress or damage.
- Spirals: These intricate designs require careful planning and potentially multiple bending steps. Specific bending tools and fixtures are commonly employed to create the repeating curve pattern.
Step-by-Step Procedure for Hand Bending a 90-Degree Angle
This procedure focuses on creating a 90-degree angle using a hand bending tool.
- Prepare the Tube: Measure and mark the desired bend point. Apply a light lubricant to the area where the bend will occur.
- Apply Support: Position the tube between two sturdy supports, ensuring the bend area is adequately supported. Secure the tube to the supports using clamps.
- Apply Force: Using the hand bending tool, apply even pressure to the bend point, progressively increasing the bending force to form the 90-degree angle. Gradually increase the pressure, avoiding sudden or uneven force.
Factors Affecting Bending Quality
Transforming raw aluminum tubing into precise, functional shapes hinges on understanding the delicate dance between design parameters and the material’s inherent properties. Mastering these interactions unlocks the potential for flawlessly formed bends, each curve a testament to the craftsman’s precision and the material’s inherent strength. Ignoring these factors can lead to catastrophic failure, or, at best, a finished product far from the designer’s vision.Precise bending, like sculpting a masterpiece, requires a keen understanding of the forces at play.
Different factors influence the outcome, from the simple radius of the bend to the material’s thickness, and the skill of the tooling used. This comprehensive exploration delves into these crucial elements, illuminating the path to achieving superior bending quality.
Influence of Radius on Bend Quality
The radius of a bend profoundly impacts the final product’s integrity and aesthetics. A smaller radius concentrates stress, potentially leading to localized deformation or even cracking. Conversely, a larger radius distributes stress more evenly, resulting in a smoother, more durable bend. Consider a pipe fitting for plumbing. A tight radius bend might cause the pipe to fail under pressure, while a larger radius provides a robust and reliable connection.
Optimizing the radius is critical to ensuring the structural integrity and the visual appeal of the final product.
Impact of Bend Angle on the Final Product
Bend angle significantly influences the part’s functionality and appearance. Extreme angles can induce significant stress concentrations, leading to material fatigue or even fracture. Precise control of the bend angle is essential for achieving the desired shape and function. For example, in aerospace components, even a slight deviation in the bend angle can affect the structural integrity and aerodynamic performance of the aircraft.
Role of Material Thickness on Bending Limitations
Aluminum tubing thickness dictates the bending limitations. Thicker tubing requires more significant force to bend, often necessitating specialized equipment. Exceeding these limits can result in material buckling or tearing, rendering the part unusable. This is particularly crucial in applications requiring high precision, like creating precise curves in complex architectural elements. Thinner tubing is more susceptible to damage, while thicker tubing demands stronger bending tools and techniques.
Effect of Tooling on the Accuracy of Bends
The quality of bending tooling directly affects the accuracy of the bends. High-quality tooling ensures consistent and repeatable bends, while sub-par tooling leads to inconsistencies, imperfections, and potential material damage. Consider the precision required in automotive components. Using inadequate tools can result in a poorly formed part that compromises the vehicle’s structural integrity. Investment in top-notch tooling is a key component of a successful bending process.
Importance of Correct Alignment During Bending
Accurate alignment of the tubing during the bending process is paramount. Misalignment can result in uneven bends, introducing stress concentrations and compromising the final product’s integrity. In precision applications like manufacturing medical devices, even minor misalignments can lead to failures and render the parts useless. Maintaining precise alignment is a critical step for high-quality bending.
Summary of Factors Affecting Bending Quality
Factor | Description | Impact on Quality |
---|---|---|
Bend Radius | The curvature of the bend | Smaller radius increases stress concentration, larger radius distributes stress more evenly. |
Bend Angle | The degree of the bend | Extreme angles increase stress concentrations, potentially leading to failure. |
Material Thickness | The depth of the tubing | Thicker tubing requires more force and specialized equipment, thinner tubing is more susceptible to damage. |
Tooling | The quality and type of bending equipment | High-quality tooling ensures consistent and repeatable bends, while sub-par tooling leads to inconsistencies. |
Alignment | The positioning of the tubing during bending | Accurate alignment is critical to achieving uniform bends and avoiding stress concentrations. |
Troubleshooting Bending Issues: How To Bend Aluminum Tubing
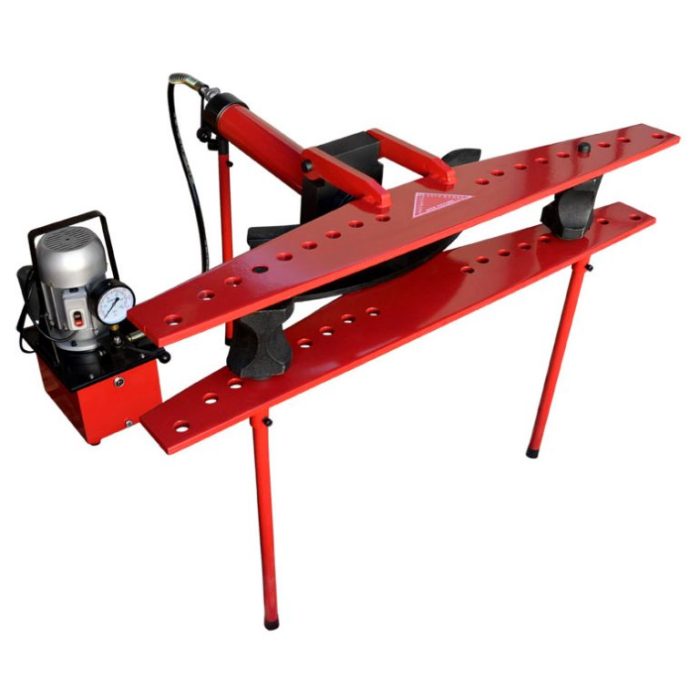
Embarking on the journey of aluminum tubing bending requires not just skill, but also a keen eye for potential pitfalls. Understanding the common problems and their underlying causes empowers you to navigate challenges with confidence and precision, transforming imperfections into opportunities for improvement. Mastering troubleshooting techniques is a cornerstone of achieving flawless bends and realizing the full potential of this versatile material.Aluminum tubing bending, while precise, can be susceptible to various issues.
Careful attention to detail, combined with a deep understanding of the process, allows you to proactively identify and resolve these issues, ultimately leading to consistently high-quality bends.
Common Bending Problems
Recognizing the potential pitfalls in aluminum tubing bending is crucial for achieving optimal results. Problems range from minor imperfections to significant structural flaws, each requiring a tailored solution. By anticipating these issues, you equip yourself with the knowledge to maintain control and precision throughout the bending process.
- Kinks: Unwanted sharp bends or folds in the tubing, often resulting from insufficient support or improper bending technique. Kinks manifest as localized distortions, detracting from the intended shape and potentially compromising the structural integrity of the tubing. Addressing kinks promptly ensures that the bend’s intended aesthetic and functional integrity are preserved.
- Uneven Bends: A departure from the desired curvature, characterized by inconsistencies in the bend’s radius or angle. Uneven bends arise from various sources, including misaligned bending tools, inconsistent material properties, or improper support during the bending process. A critical aspect of addressing uneven bends is maintaining consistent pressure and support across the bend’s entire length.
- Buckling: A deformation of the tubing’s cross-section, causing it to bow or warp, often evident in long or thin sections. Buckling often occurs when the material’s strength is insufficient to withstand the applied bending force or when the tubing lacks adequate support during the process. Employing appropriate bending tools and techniques, along with carefully controlling the bending radius, are essential in minimizing the risk of buckling.
- Overbending: Exceeding the tubing’s bending limit, leading to permanent deformation or breakage. Overbending is often caused by excessive force, incorrect bending tools, or inappropriate bending techniques. A fundamental principle in preventing overbending is to recognize the tubing’s material limitations and adjust the bending force accordingly. Consult material specifications for critical information.
Causes of Bending Problems
Delving into the root causes of bending problems provides valuable insight into the bending process itself. A systematic understanding of these causes empowers you to implement preventive measures and address issues proactively.
- Inadequate Support: Insufficient support during the bending process can lead to kinks, uneven bends, and buckling. Providing proper support, particularly for longer or more delicate tubing, prevents these problems by ensuring the tubing maintains its shape under stress.
- Incorrect Bending Technique: Employing an inappropriate bending technique can introduce various issues, such as kinks, uneven bends, and overbending. Learning and practicing the correct bending technique for aluminum tubing, considering factors like material properties and tool usage, is critical to prevent these problems.
- Improper Tool Selection: Using the wrong bending tools can lead to bending problems. Selecting the right bending tools for the specific tubing size and material type is essential for achieving accurate bends.
- Material Variations: Differences in the aluminum tubing’s material properties, such as hardness or thickness, can influence the bending process. Understanding the material specifications and adjusting the bending process accordingly is critical to preventing bending problems. Precisely matching the bending technique to the material type is essential.
Solutions to Bending Problems
Addressing bending problems requires a targeted approach, tailored to the specific issue at hand. By implementing the appropriate solutions, you can restore the tubing to its intended shape and maintain the quality of your work.
- For kinks, carefully rebend the section with support to achieve the desired curve. Apply gentle pressure and ensure consistent support along the bend.
- For uneven bends, re-adjust the bending tools and re-bend the tubing with a consistent bending radius.
- For buckling, reduce the bending radius, provide additional support, or use a different bending tool.
- For overbending, use a less forceful bending technique, consider alternative bending tools, or select a less stiff aluminum alloy.
Preventing Bending Problems
Implementing preventive measures is crucial for maintaining consistent quality in aluminum tubing bending. A proactive approach reduces the likelihood of issues arising and allows for a smoother and more efficient workflow.
- Employ appropriate bending tools for the tubing size and material type.
- Maintain proper support for the tubing during the bending process.
- Use consistent bending techniques and practice regularly.
- Thoroughly examine the tubing material specifications for relevant information regarding its bending characteristics.
Troubleshooting Table
Problem | Cause | Solution |
---|---|---|
Kinks | Insufficient support, improper technique | Re-bend with support, adjust technique |
Uneven Bends | Misaligned tools, inconsistent pressure | Re-align tools, maintain consistent pressure |
Buckling | Insufficient support, excessive force | Increase support, reduce force, adjust radius |
Overbending | Excessive force, incorrect tool, material limitations | Reduce force, use appropriate tools, select suitable material |
Illustrative Examples of Aluminum Tubing Applications
Aluminum tubing, with its exceptional strength-to-weight ratio and remarkable formability, finds widespread use in diverse applications. Its versatility, coupled with the ability to be precisely bent, allows for innovative designs and functional solutions across industries. This section explores compelling examples of bent aluminum tubing, showcasing its adaptability and aesthetic appeal.
Architectural Design and Lighting Fixtures
Aluminum tubing, expertly bent into intricate shapes, becomes a key element in modern architectural designs. Its lightweight nature enables the creation of elaborate structures without compromising strength. Imagine a breathtaking chandelier, where meticulously bent aluminum tubes form a graceful cascade of light, casting soft, ethereal glows. A close-up image of a bent aluminum tube forming part of a futuristic lamp fixture, highlighting the smooth, precise curve, illustrates the potential for artistic expression.
Another example showcases a sleek, contemporary building facade, where bent aluminum tubing, carefully crafted into panels, creates a visually stunning and structurally sound exterior.
Industrial Equipment and Machinery
In industrial settings, bent aluminum tubing plays a vital role in the construction of machinery and equipment. Its corrosion resistance and lightweight nature make it ideal for various applications, from robotic arms to conveyors. A panoramic view of a robotic arm with intricate, bent aluminum tubing supporting its delicate movements, emphasizing the precision required in industrial applications, is a powerful visual.
Similarly, a conveyor belt system, utilizing bent aluminum tubing for its structural integrity and lightweight design, would effectively demonstrate the practical applications of this material.
Transportation and Aerospace Components
Aluminum tubing’s exceptional strength and durability find significant use in the transportation sector, especially in aerospace. Its lightweight yet robust nature allows for the creation of streamlined designs, contributing to increased fuel efficiency. A detailed image of an aircraft wing component, incorporating bent aluminum tubing, showcasing its crucial role in structural support, highlights the material’s crucial function. Similarly, a close-up of a bicycle frame, using bent aluminum tubing for its exceptional strength and lightweight properties, exemplifies the material’s adaptability to various transportation needs.
Furniture and Consumer Goods
The versatility of aluminum tubing extends to consumer products and furniture design. Its sleek aesthetic and adaptability allow for the creation of stylish and functional pieces. A striking image of a modern chair frame, with its graceful, bent aluminum tubing, perfectly captures the material’s blend of strength and sophistication. Similarly, a beautifully crafted table featuring a unique, intricately bent aluminum tube base, emphasizes the design flexibility of the material.
This versatility translates into innovative solutions for everyday use.
Final Thoughts
In conclusion, mastering the art of bending aluminum tubing involves a combination of understanding its properties, selecting appropriate tools, and employing precise techniques. This guide has provided a comprehensive overview of the entire process, from initial preparation to final troubleshooting. By following the steps and tips Artikeld, you can confidently tackle various bending projects and achieve high-quality results.
General Inquiries
What are the different types of aluminum tubing commonly used?
Aluminum tubing comes in various temper designations (e.g., hard, soft, half-hard). The temper affects the material’s malleability and bendability. Hard temper tubing is more rigid and requires more force for bending, while soft temper tubing is more flexible.
What safety precautions should I take when using bending tools?
Always wear appropriate safety glasses and gloves. Ensure the work area is well-lit and ventilated. Be mindful of sharp edges and potential pinch points when using bending tools. Never force a bend beyond the tool’s capacity.
How can I prevent kinks during the bending process?
Using proper support and clamping during bending is crucial. Ensure the tubing is adequately supported along the entire length of the bend. Avoid excessive pressure on a single point of the tubing, which can lead to kinks. Using the appropriate bending tools and techniques also prevents kinks.
What are the common causes of uneven bends?
Uneven bends can stem from incorrect alignment, insufficient support, or improper use of the bending tools. Ensure the tubing is properly aligned with the bending tool’s axis. Ensure the tubing is adequately supported along the entire bend path. Avoid applying excessive pressure at any single point on the tubing. Using the right tools for the job also reduces the risk of uneven bends.