How to calculate embedding loss in bolted joint? This comprehensive guide delves into the intricacies of bolted joint analysis, exploring the critical role of embedding loss in engineering design. Understanding this crucial aspect is essential for ensuring structural integrity and performance across diverse applications, from aerospace to automotive.
Bolted joints are ubiquitous in engineering, forming the foundation of numerous structures. Their effectiveness hinges on a precise understanding of embedding loss, a phenomenon that quantifies the deviation of the actual joint performance from the theoretical ideal. This guide unravels the complex interplay between geometry, material properties, and preload to provide a thorough framework for calculating embedding loss.
Introduction to Bolted Joint Embedding Loss: How To Calculate Embedding Loss In Bolted Joint
Bolted joints are fundamental in engineering, providing a strong and reliable connection between components. Think of them as the glue that holds things together, from bridges to bikes. Their efficiency and durability are crucial for structural integrity and performance. Understanding the behaviour of these joints, particularly concerning the potential for embedding loss, is vital for designing robust structures.Embedding loss, in the context of bolted joints, refers to the deformation or damage that occurs to the material surrounding the fastener hole as the bolt is tightened.
This can result in a reduction of the joint’s overall strength and stiffness. It’s a key factor in assessing the long-term reliability of bolted connections. Factors like the material properties of the joint members, the geometry of the joint design, and the bolt tightening process all contribute to the magnitude of this loss.
Geometry and Material Properties in Bolted Joints
The geometry of the bolted joint, including the hole diameter, the thickness of the connected parts, and the overall configuration, significantly influences the embedding loss. Thicker materials and larger holes tend to experience more deformation, while well-designed joints with precise hole sizing and appropriate fillet radii can minimise embedding loss. Material properties like the yield strength and ductility of the connected materials also play a crucial role.
Materials with higher yield strength, for example, will exhibit a greater resistance to deformation, mitigating embedding loss. The interaction between the material properties and joint geometry is complex and depends on the specific design parameters.
Comparison of Bolted Joint Types
Different types of bolted joints exhibit varying susceptibility to embedding loss. A comparison of common types reveals this.
Joint Type | Description | Susceptibility to Embedding Loss |
---|---|---|
Through-bolted | Fasteners extend completely through the connected parts. | Generally lower, as the load is distributed more evenly. |
Blind-bolted | Fasteners are used to connect parts without complete penetration. | Potentially higher, as the load is concentrated in a smaller area. Requires careful design considerations for proper load distribution and material selection. |
Lap-jointed | The parts are overlapped, and bolts are used to secure the joint. | Susceptibility depends on the overlap and bolt placement; the larger the overlap, the lower the potential for embedding loss. |
This table provides a basic overview; more nuanced assessments depend on specific design parameters.
Methods for Calculating Embedding Loss
Right, so we’ve established the need to quantify embedding loss in bolted joints. Now, let’s crack open the analytical toolkit and see how we can actually calculate it. Different methods are suited to different scenarios, and understanding their strengths and weaknesses is key to getting a reliable result.Various analytical approaches exist for determining embedding loss, each with its own set of assumptions and limitations.
Choosing the right method depends on factors like the complexity of the joint design, the material properties, and the desired level of accuracy. We’ll delve into the details of FEA and analytical methods, comparing their strengths and highlighting their respective applications.
Finite Element Analysis (FEA)
FEA is a powerful numerical method for modelling complex structures. It discretises the joint into a mesh of smaller elements, enabling the simulation of stress and strain distributions under various loading conditions. This allows for a detailed analysis of the embedding process, accounting for material non-linearities and geometric complexities. FEA can handle intricate geometries and material behaviours not easily captured by simpler analytical models.
However, it’s computationally intensive and often requires significant expertise to set up and interpret the results.
Analytical Methods
Analytical methods provide a more direct and often quicker approach for estimating embedding loss. They rely on established equations and formulas based on simplified models of the joint. These models often assume linear material behaviour and simplified geometries, but they can be surprisingly accurate for certain scenarios. A crucial aspect is selecting the appropriate model that accurately reflects the specifics of the joint type.
Specific Equations and Formulas
Various equations are available for estimating embedding loss, depending on the joint configuration. For example, for a simple lap joint, a simplified formula based on the shear stress distribution in the bolt and the surrounding material might be used. A more complex formula might be required for a more intricate design, considering factors like the presence of fillets or holes.
Example for a simple lap joint: Embedding loss (ε) can be estimated as ε = τ / E, where τ is the shear stress and E is the Young’s modulus of the material.
More intricate joint configurations, such as those with a gusset plate, would require more sophisticated analytical models. These might involve calculating the stress concentrations around the bolt hole and the plate edges, taking into account the material properties and the applied load.
Comparison of FEA and Analytical Methods
| Feature | FEA | Analytical Methods ||—|—|—|| Accuracy | High, especially for complex geometries | Moderate to high, depending on the model || Computational Cost | High | Low || Complexity | High | Moderate to low || Expertise Required | High | Moderate || Time to Solution | High | Low |
Steps Involved in Analytical Methods
Analytical methods, while less computationally demanding than FEA, still require careful execution to achieve reliable results. The following steps are typical:
- Define the joint geometry and material properties. This involves precisely describing the dimensions of the joint, the type of material used, and its mechanical properties like tensile strength and Young’s modulus.
- Select an appropriate analytical model based on the joint type. Different models cater to various joint configurations.
- Apply the chosen equations and formulas, incorporating the defined parameters from the previous steps. This often involves calculating stress distributions and strain values.
- Calculate the embedding loss based on the results obtained in the previous step. This involves calculating the displacement or deformation within the embedment zone.
Factors Influencing Embedding Loss
Embedding loss in bolted joints, a crucial metric in structural integrity assessments, is significantly impacted by a multitude of factors. Understanding these influences is vital for accurate predictions and effective design optimisation. A thorough analysis of these variables allows engineers to tailor designs to minimise potential failure risks.A comprehensive understanding of embedding loss in bolted joints necessitates a deep dive into the key influencing parameters.
This includes the mechanical properties of the materials involved, the geometry of the joint itself, and the external loading conditions. Considering these factors enables a more precise prediction of the embedding loss and enhances the reliability of the structural analysis.
Preload and Material Properties
Preload, the initial clamping force applied to the fastener, plays a pivotal role in embedding loss. Higher preload generally results in reduced embedding loss, as the clamping force effectively resists the tendency for the joint components to separate. Material properties, such as the yield strength and elastic modulus, directly influence the deformation behaviour of the materials involved. Softer materials exhibit greater deformation under load, leading to a higher embedding loss compared to harder materials.
Joint Geometry and Friction/Slip
Joint geometry, encompassing factors like the shape of the joint interface and the fastener hole configuration, significantly influences the embedding loss. Complex geometries can lead to stress concentrations, potentially exacerbating the embedding loss. Friction between the joint components, especially the fastener and the surrounding material, significantly influences the embedding loss. A higher coefficient of friction between the joint surfaces leads to a greater clamping force and thus a reduction in embedding loss.
However, excessive friction can also lead to stress concentrations and potential wear. Slip, the relative movement between the joint components, directly contributes to embedding loss. Slippage in the joint will reduce the effectiveness of the preload and thus increase embedding loss.
Fastener Characteristics
Fastener diameter, length, and thread type are critical parameters influencing embedding loss. Larger fastener diameters typically result in a higher embedding force and consequently lower embedding loss. Conversely, longer fasteners, particularly in cases of high loads, can enhance the embedment resistance, reducing embedding loss. The thread type can also affect the stress distribution and thus influence the embedding loss.
A well-designed thread can distribute the stress effectively, reducing the potential for embedding loss.
Material Combinations
The interaction between different material combinations significantly affects embedding loss. For instance, a steel-aluminum bolted joint may exhibit higher embedding loss compared to a steel-steel joint. This is due to the differing elastic moduli and yield strengths of the materials. The mismatch in material properties can lead to non-uniform stress distribution and greater deformation, ultimately resulting in a higher embedding loss.
Furthermore, the differing coefficients of friction between the materials also contribute to this effect. Understanding the specific characteristics of each material combination is essential for accurately predicting embedding loss.
Experimental Validation and Verification
Validating the calculated embedding loss in bolted joints requires rigorous experimental procedures. This section details various experimental setups, showcasing examples of data analysis, and demonstrating the correlation between experimental results and the analytical models. Accurate validation is crucial for refining the models and ensuring practical applicability in engineering design.
Experimental Setups for Measuring Embedding Loss
Different experimental setups are employed to measure embedding loss in bolted joints, each with its own strengths and limitations. These setups typically involve controlled loading conditions, precise measurement techniques, and careful consideration of the material properties of the joint components. A common approach involves applying a controlled tensile load to the bolted joint while simultaneously measuring the deformation and strain within the joint’s embedding region.
Variations include using strain gauges or other displacement sensors for precise measurements of deformation.
Examples of Experimental Data and Analysis
Experimental data, such as load-displacement curves, strain distributions, and fracture patterns, are crucial for validating the calculated embedding loss. For example, if a finite element analysis predicts a specific embedding loss value under a certain load, the experimental data should exhibit a similar trend. Analyzing the load-displacement curve helps identify the point of yielding or failure, providing insights into the joint’s behaviour.
The strain distribution within the embedding region can be compared to theoretical predictions from the model, providing a measure of accuracy.
Demonstrating Correlation Between Experimental Data and Analytical Models
The correlation between experimental data and the analytical models is crucial for validating the accuracy and reliability of the models. A strong correlation suggests that the model accurately represents the physical phenomena occurring in the joint. For instance, if the experimental load-displacement curve closely matches the curve predicted by the finite element model, it indicates a good agreement between the model and reality.
Deviation from the predicted values may point to areas where the model needs improvement or refinement.
Measurement Techniques in Experimental Validation
This table Artikels the different measurement techniques employed in experimental validation of embedding loss in bolted joints.
Measurement Technique | Description | Advantages | Disadvantages |
---|---|---|---|
Strain Gauges | Measure strain at specific locations within the joint | High accuracy, provides detailed strain distribution | Requires careful placement, potential for interference with the joint |
Displacement Sensors | Measure displacement of specific points in the joint | Simple to implement, provides global deformation information | Less detailed strain information compared to strain gauges |
Digital Image Correlation (DIC) | Measures displacement and strain fields using digital image analysis | Non-intrusive, provides full-field strain measurements | Requires high-quality images, computational resources |
Acoustic Emission (AE) | Detects acoustic signals generated during the loading process | Can provide early warning of damage initiation | Requires sophisticated analysis, may not directly quantify embedding loss |
Applications and Case Studies

Understanding embedding loss in bolted joints is paramount for various engineering disciplines, particularly those involving structural integrity and performance under load. This knowledge is crucial in optimising design parameters, predicting failure points, and ensuring the longevity of components. A thorough grasp of these factors is vital in diverse engineering fields, from aerospace to automotive, where reliability and safety are paramount.
Engineering Applications
Various engineering applications necessitate a meticulous understanding of embedding loss in bolted joints. These include, but are not limited to, aircraft structures, automotive chassis, and pressure vessels. Accurate prediction of the joint’s load-bearing capacity and fatigue life hinges on this understanding. Furthermore, understanding embedding loss enables engineers to optimise the design of bolted connections for maximum efficiency and safety.
Case Studies
Consider a case study involving an aircraft wing assembly. Significant embedding loss in the attachment points of the wing to the fuselage could compromise the aircraft’s structural integrity under flight conditions. The impact of this loss could manifest as premature fatigue failure or even catastrophic structural collapse. Similarly, in automotive applications, embedding loss in engine mounting bolts can lead to vibration issues, reduced engine life, and compromised vehicle performance.
Engineering Challenges
Several engineering challenges are directly addressed by an in-depth understanding of embedding loss. For example, in the design of high-pressure vessels, accurately modelling the stress distribution around the bolt holes and the effect of embedding loss is critical for preventing leaks and ensuring structural integrity. Moreover, in aerospace applications, minimising embedding loss in critical components, such as wing attachment points, is vital for ensuring the safety and reliability of aircraft operations.
Furthermore, in the development of high-performance sports cars, understanding embedding loss in the suspension components can lead to more precise handling and improved performance.
Comparison of Embedding Loss in Different Applications
Application | Specific Challenge | Impact of Embedding Loss | Mitigation Strategies |
---|---|---|---|
Aerospace | Maintaining structural integrity under extreme flight conditions | Reduced fatigue life, potential for catastrophic failure | Optimized bolt design, improved material selection, rigorous testing protocols |
Automotive | Ensuring engine mounting stability and longevity | Increased vibration, reduced engine life, compromised vehicle performance | Precise bolt tightening procedures, improved gasket materials, and enhanced design of the mounting points |
Pressure Vessels | Preventing leaks and ensuring structural integrity under high pressure | Compromised stress distribution, potential for leaks or failure | Advanced Finite Element Analysis (FEA) models that account for embedding loss, and use of advanced materials. |
Optimization Strategies
Minimising embedding loss in bolted joints is crucial for achieving robust and reliable mechanical assemblies. Effective optimization strategies encompass material selection, surface treatments, and meticulous preloading techniques. These approaches are vital for ensuring structural integrity and performance across diverse engineering applications.Optimizing bolted joint design to minimise embedding loss necessitates a multifaceted approach. This involves not only understanding the underlying principles of material behaviour but also the practical considerations of manufacturing processes and assembly procedures.
Careful attention to detail in each stage can lead to significant reductions in embedding loss, translating to improved overall system performance.
Material Selection and Surface Treatments
Selection of advanced materials with superior mechanical properties and reduced tendency for deformation is paramount. For instance, high-strength alloys like advanced steels exhibit higher yield strengths, leading to reduced embedding loss compared to conventional materials. Surface treatments like shot peening can enhance surface hardness and compressive residual stresses, further minimizing deformation and thus embedding loss. These treatments also contribute to fatigue resistance, increasing the longevity of the bolted joint.
Preloading and Tightening Strategies
Optimal preloading and tightening procedures are critical for minimizing embedding loss. Precise control over the applied preload ensures a consistent clamping force across the joint, preventing localized deformation. Employing calibrated torque wrenches and controlled tightening sequences are essential for accurate preload application. Advanced techniques, such as those incorporating feedback mechanisms, further optimize the tightening process, reducing the risk of over-tightening or under-tightening, both of which can negatively impact the final outcome.
Optimization Techniques and Impact on Embedding Loss
Optimization Technique | Potential Impact on Embedding Loss | Example Application |
---|---|---|
High-strength steel bolts with improved surface finish | Reduced deformation, improved load transfer | Aircraft fuselage assembly, high-pressure vessels |
Shot peening of bolt threads and mating surfaces | Increased surface hardness, enhanced compressive residual stresses | Heavy machinery components, pressure vessel joints |
Precise preloading using calibrated torque wrenches | Uniform clamping force, minimized localized deformation | Automotive engine block assemblies, structural connections |
Controlled tightening sequences with feedback mechanisms | Optimal preload application, minimized risk of over/under-tightening | High-precision instrumentation, critical structural elements |
Optimized fastener selection (e.g., considering thread geometry and material properties) | Reduced stress concentrations, improved load distribution | Bridges, building structures |
Future Trends and Research Directions
A deeper understanding of embedding loss in bolted joints is crucial for optimising structural integrity and reliability. Future research should move beyond current methodologies to explore emerging technologies and materials, leading to more robust and efficient designs. This necessitates an exploration of novel analytical and experimental approaches to quantify embedding loss with greater accuracy and precision.
Emerging Research Areas, How to calculate embedding loss in bolted joint
Current research predominantly focuses on empirical estimations of embedding loss. Future research should explore advanced computational modelling techniques, integrating finite element analysis (FEA) with machine learning algorithms. This will allow for more accurate predictions of embedding loss under complex loading conditions, including fatigue and cyclic loading, and improve the understanding of material behaviour in bolted connections.
Potential Future Developments in Analytical Techniques
Integrating advanced FEA with machine learning algorithms is crucial. This can model complex stress distributions within the joint with greater precision. Developing novel constitutive models for materials under high stress and deformation is also important. Furthermore, the use of advanced non-destructive evaluation (NDE) techniques for real-time monitoring of embedding loss during operation is a key area for future research.
This would facilitate real-world applications and enhance predictive maintenance strategies.
Potential Future Developments in Experimental Techniques
The development of advanced experimental setups, capable of replicating real-world loading conditions and environments, is critical. Using advanced microscopy techniques for detailed analysis of the embedded fastener and surrounding material will provide valuable insights. Furthermore, employing advanced sensor technology to measure local stress and strain during loading, will offer invaluable insights into the mechanisms of embedding loss. This will allow for a deeper understanding of the relationship between material properties and embedding loss.
Impact of New Materials and Technologies
The use of advanced materials, such as high-strength steels, composites, and advanced polymers, will necessitate new models and approaches to quantify embedding loss. Moreover, the rise of additive manufacturing (3D printing) for creating complex geometries will require the development of new analytical methods to assess the integrity of bolted joints in these configurations. This presents an opportunity to tailor the material properties to mitigate embedding loss and optimise joint performance.
Furthermore, the exploration of smart materials with embedded sensors could enable real-time monitoring of embedding loss, leading to proactive maintenance and improved reliability.
Need for Further Research in Bolted Joint Design and Analysis
The need for a comprehensive framework for designing and analysing bolted joints is paramount. This framework must account for the variability in material properties, loading conditions, and manufacturing tolerances. Development of design guidelines incorporating realistic estimations of embedding loss is essential for ensuring the structural integrity and longevity of bolted connections. Additionally, further research is needed to understand the influence of surface treatments, such as coatings and surface roughness, on embedding loss in various material combinations.
Last Word
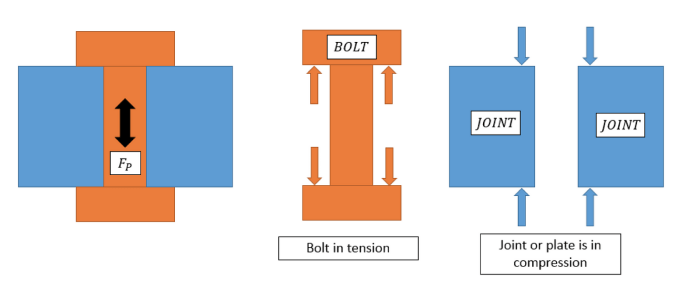
In conclusion, calculating embedding loss in bolted joints requires a multi-faceted approach encompassing analytical methods, finite element analysis, experimental validation, and optimization strategies. This guide has provided a robust framework for tackling this critical engineering challenge. By understanding the factors influencing embedding loss, engineers can design more reliable and efficient bolted joints, optimizing performance and longevity across various applications.
Clarifying Questions
What are the common types of bolted joints susceptible to embedding loss?
Through-bolted and blind-bolted joints are examples, with through-bolted joints often exhibiting higher susceptibility due to the greater potential for deformation. The specific susceptibility depends on factors like joint geometry and material properties.
How does preload affect embedding loss?
Preload significantly influences embedding loss. Higher preload generally results in reduced embedding loss, as it helps distribute stress more effectively across the joint. However, excessive preload can lead to other issues, highlighting the need for careful optimization.
What role does friction play in embedding loss?
Friction between the joint components plays a crucial role. High friction can reduce embedding loss, but excessive friction can lead to localized stress concentrations, potentially impacting the joint’s overall integrity. Proper material selection and surface treatment can influence friction and consequently embedding loss.
What are the typical experimental setups used to measure embedding loss?
Experimental setups vary, but they typically involve applying controlled loads and measuring deformation. Strain gauges, displacement sensors, and load cells are commonly used to obtain accurate data. The specific setup depends on the joint type and the aspect of embedding loss being investigated.