How to clean rust off circuits is a crucial skill for anyone working with electronic components. Rust, a common enemy of circuits, can lead to serious malfunctions and costly repairs. Understanding the various forms of rust, the safe removal techniques, and the proper post-cleaning procedures is vital for maintaining the integrity of your circuits. This guide will walk you through the entire process, from identifying the rust to preventing its return, using traditional Batak wisdom to ensure thorough understanding.
This comprehensive guide will detail the process of removing rust from electronic circuits, ensuring optimal functionality and longevity. The article will delve into mechanical and chemical methods, providing a detailed comparison of their advantages and disadvantages. Furthermore, it will address the importance of safety precautions, highlighting the potential risks associated with improper handling of cleaning solutions. Understanding the unique characteristics of different circuit components and their respective cleaning procedures is essential, as different components require different approaches.
Introduction to Rust Removal
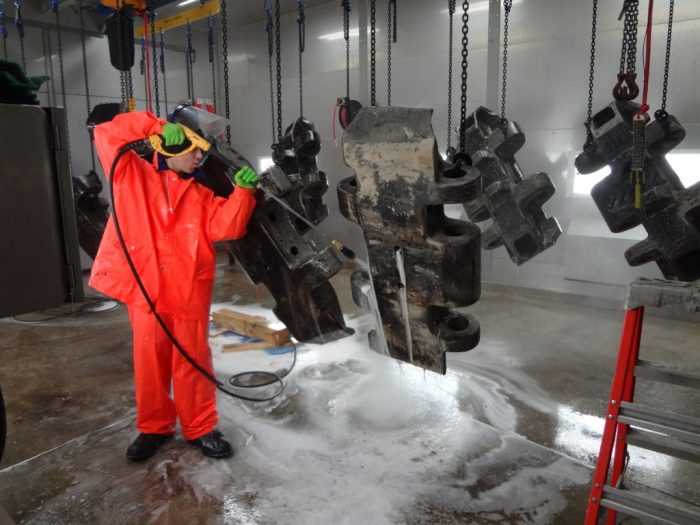
Hai semuanya! Kita semua tahu betapa pentingnya menjaga komponen elektronik kita dalam kondisi prima. Tapi, kadang-kadang, musuh tak terlihat bernama karat muncul dan menyerang sirkuit kita. Mari kita bahas tentang bagaimana karat bisa merusak sirkuit dan apa yang perlu kita lakukan untuk mengatasinya. Jangan sampai karat merusak kerja keras kita!Karat adalah senyawa oksida yang terbentuk ketika logam bereaksi dengan oksigen dan air.
Pada sirkuit elektronik, karat bisa muncul di berbagai komponen, mulai dari konektor hingga resistor. Ini bisa menyebabkan masalah serius, seperti korsleting, penurunan kinerja, dan bahkan kegagalan total. Bayangkan deh, seperti air yang masuk ke dalam rumah, lama-lama bisa merusak fondasinya. Begitu juga dengan karat, lama-lama bisa bikin komponen elektronik kita rusak. Penting banget untuk segera membersihkannya sebelum masalahnya makin parah!
Understanding the Problem of Rust
Karat pada sirkuit elektronik merupakan masalah yang serius karena dapat menyebabkan kerusakan yang tak terduga. Jika dibiarkan, karat dapat menyebabkan konduktivitas listrik yang buruk, sehingga mengganggu aliran arus yang tepat. Hal ini bisa menyebabkan komponen bekerja tidak normal atau bahkan gagal total. Bayangkan, seperti jalur yang macet, aliran listrik pun terganggu dan bisa menyebabkan kerusakan pada komponen.
Consequences of Ignoring Rust
Mengabaikan karat pada sirkuit dapat berdampak buruk bagi performa dan umur komponen elektronik. Beberapa konsekuensi yang mungkin terjadi meliputi:
- Kinerja komponen menurun. Misalnya, kapasitor yang berkarat akan mengurangi kapasitasnya, sehingga mengurangi kemampuannya menyimpan muatan listrik. Hal ini bisa berakibat pada penurunan performa perangkat elektronik.
- Korsleting. Jika karat membentuk jalur konduktif antara dua titik yang seharusnya terisolasi, korsleting bisa terjadi. Ini bisa menyebabkan panas berlebih dan bahkan kebakaran.
- Kerusakan permanen. Jika karat tidak ditangani, komponen elektronik bisa mengalami kerusakan permanen. Hal ini bisa membuat perangkat menjadi tidak berfungsi sama sekali.
Importance of Proper Cleaning Methods
Membersihkan karat pada sirkuit elektronik membutuhkan metode yang tepat untuk mencegah kerusakan lebih lanjut. Metode yang salah dapat memperparah kerusakan yang sudah ada. Jangan sembarangan ya, karena bisa memperburuk keadaan.
- Penggunaan alat yang tepat. Gunakan alat yang sesuai dengan jenis karat dan permukaan yang akan dibersihkan. Jangan sampai alat yang kita gunakan malah menggores atau merusak sirkuit.
- Pencegahan. Lakukan pencegahan dengan menyimpan komponen elektronik di tempat yang kering dan terhindar dari kelembapan. Hindari kontak dengan air atau zat kimia yang dapat menyebabkan karat.
- Pemeriksaan berkala. Lakukan pemeriksaan berkala pada komponen elektronik untuk mendeteksi karat sejak dini. Dengan demikian, kita bisa segera mengatasinya dan mencegah kerusakan yang lebih parah.
Identifying Types of Rust: How To Clean Rust Off Circuits
Hai semuanya! Knowing the different kinds of rust is crucial for effective removal. Like identifying different flavors of teh, understanding the type of rust helps you choose the right cleaning method. It’s like knowing whether you need a gentle sip or a strong brew to tackle the problem!Rust on circuits isn’t always the same. It varies in severity and appearance, depending on the metal and the environment.
Just like how a beautiful batik design can be ruined by a stain, rust can damage the delicate workings of your circuit boards. Understanding the type of rust helps you know how aggressive you need to be in your cleaning process.
Visual Cues for Rust Differentiation
Recognizing the differences between light surface rust and severe corrosion is essential. Light surface rust is like a thin layer of reddish-brown paint, while severe corrosion is more like a thick, chunky layer, possibly even creating holes. This difference in appearance directly correlates with the damage done to the circuit. Severe corrosion can completely alter the conductive pathways of the circuit, potentially leading to malfunctions.
Rust Appearance on Different Metals
Different metals react differently to rusting. Copper, for example, can develop a greenish-blue patina, while iron shows the familiar reddish-brown rust. Aluminum, on the other hand, often develops a thin, whitish-gray layer. Understanding the specific metal of a circuit component is key to choosing the right cleaning method. Each metal type needs a different approach, just like choosing the right spices for a dish!
Methods for Visual Inspection of Circuit Boards
Visual inspection is the first step in determining the extent of rust. Using a magnifying glass can reveal tiny spots of rust that might otherwise go unnoticed. Good lighting is essential, as shadows can hide the rust. A bright light source, like a lamp or flashlight, will allow you to see the rust clearly. Sometimes, you might even need to carefully lift or separate parts of the circuit to get a complete view of the rust.
Like a detective meticulously examining a crime scene, you need to be thorough and systematic in your inspection!
Safety Precautions
Handling rust removal solutions and equipment requires careful attention to safety. Like a wise Palembang ibu preparing a special dish, you need to be mindful of the ingredients and tools to avoid any unpleasant surprises. Following safety precautions is crucial to ensure a safe and successful cleaning process.Proper safety measures are essential for protecting yourself from potential hazards associated with cleaning solutions and equipment.
Just like a careful craftsman, you must understand the potential risks and take necessary precautions. This includes using appropriate protective gear and maintaining proper ventilation.
Essential Protective Gear
Understanding the importance of personal protective equipment (PPE) is paramount for a safe rust removal process. Just like a Palembang craftsman carefully selecting the right tools for the job, you must choose the appropriate protective gear. This protects you from harmful chemicals and potential injuries.
- Gloves: Chemical-resistant gloves are crucial for preventing direct skin contact with cleaning solutions. Choose gloves made from materials like nitrile or neoprene to offer the best protection. Avoid cotton gloves as they are easily permeated by chemicals.
- Eye Protection: Safety glasses or goggles are essential to shield your eyes from splashes or fumes. Eye protection prevents irritation and damage, ensuring your vision remains clear and sharp, just like a Palembang trader’s keen eye in a bustling market.
- Respiratory Protection: If the cleaning solution generates fumes or dust, a respirator is needed to filter the air. This prevents inhalation of harmful particles, ensuring your lungs remain healthy, vital to your energy levels for your work, like a diligent Palembang trader.
Potential Hazards of Improper Handling
Improper handling of cleaning solutions can lead to significant hazards. Similar to a Palembang house, where careful storage and handling of materials are crucial to prevent damage, handling cleaning solutions incorrectly can result in unforeseen accidents. Understanding the potential risks is key to preventing mishaps.
- Skin Irritation and Burns: Some rust removal solutions are highly corrosive. Direct contact with skin can cause severe irritation, burns, and long-term damage. Just like a Palembang’s skin, it needs to be protected from the harsh chemicals.
- Eye Damage: Splashes of cleaning solutions can cause serious eye damage. This is especially important, as your eyes are just like the precious ornaments of a Palembang bride.
- Respiratory Problems: Inhaling fumes from cleaning solutions can lead to respiratory problems, such as coughing, sneezing, and difficulty breathing. These problems can be debilitating, so take precautions to prevent them, just as a Palembang’s lungs need protection from the harmful air.
Ventilation and Safety Guidelines
Adequate ventilation is crucial when working with rust removal solutions. Just like a well-ventilated Palembang house, proper airflow prevents the accumulation of harmful fumes and vapors. Maintaining good ventilation reduces the risk of health problems.
- Open Windows and Doors: Whenever possible, open windows and doors to allow fresh air to circulate. This is like ensuring the freshness of a Palembang’s home.
- Use a Fan: A fan can assist in circulating air and removing fumes. A fan, like the wind, can disperse the harmful substances and improve the air quality.
- Work in a Well-Ventilated Area: If possible, work outdoors or in a well-ventilated area. Working in an open space, like a Palembang market, provides a safer and healthier environment.
- Avoid Direct Sunlight: Some cleaning solutions are sensitive to sunlight, and their effectiveness can be affected. Just like a delicate Palembang craft, direct sunlight can damage the cleaning solution.
- Follow Manufacturer’s Instructions: Always consult the manufacturer’s instructions for the specific cleaning solution. These instructions Artikel the safe handling procedures, much like a Palembang guidebook.
Mechanical Removal Methods

Ayo, fellow circuit cleaners! Let’s get our hands dirty (carefully, of course!) with mechanical rust removal techniques. These methods are often the first line of defense, especially for smaller circuits or when you’re just starting out. We’ll explore different tools and strategies, so you can choose the best approach for your specific circuit needs.
Scrubbing Techniques
Scrubbing is a common method for gently removing surface rust. The key is to select the right brush and apply gentle, controlled pressure. Using excessive force can damage the delicate components of the circuit.
- Different types of brushes are available, including soft-bristled brushes, nylon brushes, and even specialized brushes designed for electronics. Select the brush that best suits the severity of the rust and the type of circuit material. A soft brush is ideal for delicate components, while a stiffer brush might be needed for stubborn rust.
- Applying the brush in a circular motion, or back and forth, is effective. Avoid back-and-forth strokes that can cause scratches. The circular motion helps to loosen the rust without damaging the underlying circuit.
- Ensure proper rinsing and cleaning after scrubbing to prevent further damage from rust particles.
Scraping Techniques
Scraping is a more aggressive method for removing rust, but it’s important to be careful not to damage the circuit board. Use appropriate tools and apply the technique precisely.
- Use tools like plastic scrapers, or specialized picks for electronics. Metal scrapers can cause scratches or damage, leading to short circuits. Always choose the right tool for the job. A plastic scraper is usually ideal for the majority of cases.
- Work in small, controlled areas to prevent unnecessary damage. Concentrate on the rust spots, and avoid applying excessive pressure.
- Use light pressure, especially on delicate components. Apply the scraper at a slight angle to the circuit board to prevent scratching or damaging the circuit.
Filing Techniques
Filing is suitable for removing rust from areas that are hard to reach or for areas with thicker rust deposits. Be extra careful when using files to avoid damaging the circuit board.
- Use fine-grit files to minimize damage. A coarse file can cause significant damage to the circuit, leaving deep scratches. A fine-grit file is preferable for precision work.
- Apply the file with gentle pressure, keeping the file perpendicular to the circuit. This helps ensure that you are removing rust and not damaging the surface of the circuit board.
- Check the work frequently to avoid over-filing. Over-filing can cause damage and make the circuit more prone to short circuits.
Comparison of Mechanical Methods
Method | Effectiveness | Suitability | Advantages | Disadvantages |
---|---|---|---|---|
Scrubbing | Moderate | Delicate circuits, light rust | Gentle, less abrasive | Less effective for heavy rust, can take longer |
Scraping | High | Moderate to heavy rust | Fast, effective for removing rust | Risk of damage to circuit board, requires more care |
Filing | High | Areas hard to reach, thick rust | Precise removal for specific areas | High risk of damage if not handled carefully, requires more expertise |
Chemical Removal Methods
Ayo, fellow circuit cleaners! Chemical methods can be a real lifesaver when dealing with stubborn rust. They work by dissolving the rust, leaving behind a clean surface ready for your next repair. Just remember, safety is key, and these chemicals can be tricky, so follow the steps carefully.
Chemical Solutions for Rust Removal
Various chemical solutions can effectively remove rust from circuits. The best choice depends on the severity of the rust and the type of metal involved. Common options include citric acid, oxalic acid, and specialized rust removers. Each solution has unique properties that influence its effectiveness.
Chemical Reactions in Rust Removal
Rust, chemically known as iron oxide (Feâ‚‚O₃), is formed when iron reacts with oxygen and water. Chemical rust removal involves reversing this process. The chemical solutions work by reacting with the rust, breaking down the iron oxide into its constituent elements, iron, and oxygen. For example, citric acid’s acidic nature helps dissolve the rust. This process often involves a redox reaction, where electrons are transferred between the solution and the rust.
Understanding these chemical reactions helps you pick the right solution and concentration.
Preparing and Using Chemical Solutions
Proper preparation and handling of chemical solutions are crucial for effective rust removal and safety. Always wear appropriate protective gear, like gloves and eye protection, and work in a well-ventilated area. This is vital to avoid any accidental contact with your skin. Follow the specific instructions provided with the chosen chemical solution. It’s crucial to know that different solutions require different preparation methods.
Dilution Ratios for Chemical Solutions
The concentration of the chemical solution significantly impacts its effectiveness and safety. Overly concentrated solutions can damage the circuit board, while too dilute a solution might not effectively remove the rust. The appropriate dilution ratio depends on the specific chemical and the type of rust. Always refer to the manufacturer’s instructions for the correct dilution ratio. For example, a 1:10 ratio of citric acid to water might be suitable for light rust, while a stronger solution might be needed for heavy rust.
Use a measuring cylinder or a graduated beaker to ensure accurate dilution.
Chemical | Typical Dilution Ratio | Safety Precautions |
---|---|---|
Citric Acid | 1 part citric acid to 10 parts water (or as directed) | Can cause skin irritation. Wear gloves and eye protection. |
Oxalic Acid | 1 part oxalic acid to 10-20 parts water (or as directed) | Highly corrosive. Extreme caution is required. Use in a well-ventilated area. Wear gloves, eye protection, and a respirator. |
Specialized Rust Removers | Follow manufacturer’s instructions | Consult the manufacturer’s instructions for safety guidelines. |
Choosing the Right Method
Picking the right way to remove rust from your circuits is crucial, like choosing the perfect baju for a special occasion. Sometimes, a gentle touch is needed, while other times, a stronger approach is required. We’ll explore the differences between mechanical and chemical methods, helping you make the smartest choice for your specific circuit.Mechanical and chemical methods each have their own strengths and weaknesses.
Understanding these nuances will ensure you get the best possible outcome without damaging the delicate components of your circuits. Think of it like choosing the right tool for the job; a hammer is great for driving nails, but not so good for delicate carvings.
Mechanical Rust Removal
Mechanical methods involve physically removing the rust. This approach is often ideal for smaller, localized rust patches or when you’re concerned about damaging the circuit with chemicals. The goal is to gently and precisely remove the rust without scratching or harming the underlying material. Consider the circuit’s sensitivity and the extent of the rust when deciding if mechanical methods are appropriate.
- Advantages: Mechanical methods can be precise, ideal for delicate circuits. They are often gentler and less likely to harm the underlying material. This method minimizes the risk of chemical residue. It is a good choice for localized rust patches.
- Disadvantages: Mechanical methods can be time-consuming for extensive rust damage. It requires careful handling and the right tools to avoid further damage to the circuit. Some methods may not effectively remove stubborn rust.
Chemical Rust Removal
Chemical methods use solutions to dissolve the rust. This is often faster for large-scale rust problems, but it requires caution to avoid harming the circuit components. The right chemical must be chosen based on the type of metal used in the circuit. Think of it like using the right soap for your clothes; a harsh detergent might damage delicate fabrics.
- Advantages: Chemical methods are often quicker than mechanical methods for extensive rust removal. They can effectively tackle even stubborn rust, like a strong cleaning agent for deeply stained fabrics. They can also be cost-effective in large-scale applications.
- Disadvantages: Chemical methods can potentially harm the circuit if the wrong chemicals are used. They often require protective equipment to prevent skin or eye irritation. Careful disposal of the chemical solution is also crucial. A chemical reaction could damage the circuit if the wrong solution is used. Cleaning residue from the chemical solution might be challenging.
Factors to Consider
Several factors play a role in choosing the right method. The extent of the rust, the type of metal in the circuit, the size and complexity of the circuit, and personal safety concerns all influence the decision. Imagine you’re choosing a recipe; different ingredients need different cooking methods.
- Extent of Rust: Extensive rust might necessitate chemical methods for quicker removal. Localized rust might be better handled mechanically for precision.
- Metal Type: Different metals react differently to chemicals. Consult a material science guide for the best method for your specific circuit’s metal type. Using the right chemical is critical to avoid damaging the circuit.
- Circuit Complexity: Complex circuits with intricate components might require a more cautious mechanical approach to avoid damage.
- Personal Safety: Always prioritize safety when handling chemicals. Wear appropriate protective gear like gloves and eye protection. Proper ventilation is crucial when using chemicals.
Comparison Table
Characteristic | Mechanical Method | Chemical Method |
---|---|---|
Speed | Slower | Faster |
Precision | Higher | Lower |
Safety | Generally safer | Potentially hazardous |
Rust Type | Better for localized rust | Better for extensive rust |
Circuit Damage Risk | Lower | Higher |
Cleaning Specific Components
Howdy, circuit enthusiasts! Now that we’ve tackled the general rust removal, let’s dive into the nitty-gritty of cleaning individual components. Properly cleaning delicate components is crucial to prevent further damage and ensure optimal circuit performance. We’ll be covering resistors, capacitors, and integrated circuits (ICs) with gentle, effective techniques.
Different components have different sensitivities. Understanding these sensitivities is key to successful cleaning. A gentle touch and careful consideration of the cleaning methods are paramount. We’ll detail specific procedures for each component, focusing on minimizing any risk of damage. This is like a delicate dance, where precision and care are essential steps.
Cleaning Resistors
Resistors, often the unsung heroes of a circuit, are relatively robust. However, aggressive cleaning methods can lead to damage. Use a soft brush, like a small artist’s brush, or a cotton swab dampened with the chosen cleaning solution. Gently scrub the surface of the resistor, avoiding the leads. Avoid excessive pressure to prevent cracking or breakage.
Always check the resistor’s datasheet for specific cleaning recommendations.
Cleaning Capacitors
Capacitors are a bit more delicate than resistors. Avoid harsh scrubbing, as this can damage the dielectric material. Use a cotton swab dampened with a suitable cleaning solution. Gently wipe the capacitor’s body and leads, ensuring the solution doesn’t enter the capacitor’s internal components. Carefully check the capacitor’s datasheet for specific cleaning guidelines.
Always remember to use the gentlest approach possible.
Cleaning Integrated Circuits (ICs)
Integrated circuits (ICs) are highly sensitive. Never use any sort of scrubbing or immersion in cleaning solutions. Instead, focus on the exterior surfaces, using a soft brush or cotton swab dampened with a suitable solution. Apply very gentle pressure to avoid scratching or damaging the delicate pins or the components on the chip. Again, reference the datasheet for any specific cleaning instructions.
Cleaning Sensitive Areas, How to clean rust off circuits
Sensitive areas of a circuit, such as the solder joints or connections between components, require a very delicate approach. Using a small, soft brush or cotton swab with a cleaning solution is the best way to approach these areas. Ensure the solution doesn’t reach the interior of the components. Gently wipe the affected area, applying minimal pressure to avoid further damage.
Cleaning Procedure Table
Component | Cleaning Solution | Cleaning Method | Precautions |
---|---|---|---|
Resistors | Isopropyl alcohol (70% or higher) | Gently brush or wipe with a cotton swab. | Avoid excessive pressure. |
Capacitors | Isopropyl alcohol (70% or higher) or a specialized capacitor cleaning solution | Gently wipe with a cotton swab. | Avoid getting solution inside the capacitor. |
ICs | Isopropyl alcohol (70% or higher) | Gently brush or wipe with a cotton swab. | Avoid touching the pins or the IC’s surface with excessive force. |
Solder Joints/Connections | Isopropyl alcohol (70% or higher) | Gently brush or wipe with a cotton swab. | Avoid getting solution into the component interiors. |
Post-Cleaning Procedures
Finishing up your circuit board cleaning is just as important as the initial scrubbing. Like polishing a beautiful piece of Palembang batik, you want to make sure it’s gleaming and ready for action. Proper rinsing and drying are crucial steps to prevent future problems and ensure your circuit board stays in tip-top shape.
Importance of Rinsing and Drying
Thorough rinsing and drying are essential for removing any lingering cleaning agents or moisture. Leftover chemicals can corrode the delicate components, while moisture can lead to short circuits or other electrical malfunctions, potentially causing more headaches than the initial rust. Imagine a beautiful painting ruined by water stains; similar damage can occur on a circuit board. This meticulous final step protects your investment and ensures long-term functionality.
Best Practices for Drying
Proper drying is critical to avoid potential problems. Moisture trapped in crevices or on delicate components can cause unexpected issues down the line. Rapid drying methods are preferable to prevent damage or warping of the board. A gentle air flow or controlled use of a soft, lint-free cloth is ideal for ensuring complete dryness. Avoid harsh heat sources like direct sunlight or hair dryers, as these can damage the components.
Imagine a delicate flower wilting from excessive heat; the same principle applies to circuit boards.
Thorough Cleaning and Drying
Achieving a pristine and spotless surface is paramount. This involves not just removing visible rust but also ensuring that all traces of cleaning agents and moisture are completely gone. This meticulous approach safeguards against potential future issues. A thorough cleaning is like meticulously polishing a valuable heirloom, ensuring its preservation and readiness for years to come.
Step-by-Step Post-Cleaning Procedure
- Rinse Thoroughly: Use a gentle stream of deionized water (or distilled water if deionized isn’t available) to wash away all traces of cleaning agents and any loose particles. Avoid using harsh water pressures that might damage the delicate components. Think of rinsing like gently washing a fine piece of silk; you want to be careful not to cause any damage.
- Air Dry: After rinsing, carefully place the circuit board in a well-ventilated area to allow air to circulate and remove any remaining moisture. Use a soft, lint-free cloth to blot away excess water, but avoid rubbing aggressively, as this can damage the delicate components. A gentle air dry is the best way to avoid scratching or marking the board.
- Controlled Drying (if needed): If air drying isn’t sufficient, use a low-heat, controlled drying method. A gentle stream of warm, dry air from a blower or similar tool can assist in evaporating residual moisture without causing damage. Be cautious about using excessive heat, as this could lead to component damage.
- Inspect for Residual Moisture: After the drying process, meticulously examine the board for any remaining moisture. Look for signs of condensation or dampness in any crevices or around components. This final inspection ensures that the board is completely dry before further handling.
- Allow for Complete Drying: Once you’ve inspected the board and ensured its dryness, allow it to sit in a well-ventilated area for a sufficient period to allow for complete drying. Avoid using any high heat or rapid drying methods that might harm the board.
Troubleshooting and Prevention
Sometimes, even with the best techniques, rust removal can present a few hiccups. Don’t worry, like a good repairman in Palembang, we can fix those problems! Understanding common issues and preventative measures is key to keeping your circuits sparkling clean and rust-free. This section will equip you with the knowledge to tackle those tricky situations and maintain your circuits in top condition.
Common Problems During Rust Removal
Rust removal can sometimes encounter unexpected obstacles. Understanding these potential issues will help you troubleshoot effectively. Different types of rust and varying circuit materials can present challenges.
- Rust persistence: Some stubborn rust spots may resist initial removal attempts. This could be due to the depth of the rust penetration or the type of metal used in the circuit.
- Material damage: Aggressive cleaning methods can potentially damage the underlying circuit components, especially delicate ones. Using the right tools and methods is crucial to avoid this.
- Incomplete removal: In some cases, you might not remove all the rust, leaving behind traces that could lead to further corrosion. Careful inspection and re-evaluation of the cleaning process are essential.
- Contamination: If the cleaning solution is not properly applied or if contamination occurs during the process, the circuit might be exposed to harmful chemicals or impurities. Strict adherence to safety protocols is important.
Identifying and Resolving Issues
Troubleshooting these problems requires a methodical approach. First, identify the specific issue. If rust persists, try a different cleaning method or a more aggressive approach (but always with caution). If material damage is suspected, stop the cleaning immediately and assess the extent of the damage. If incomplete removal is suspected, repeat the cleaning process, ensuring thorough coverage.
If contamination is suspected, rinse the circuit thoroughly with clean water and examine for any signs of chemical residue.
Preventing Rust Formation on Circuits
Proactive measures are crucial to prevent future rust issues. Preventing rust formation is like having a good preventive maintenance plan, ensuring your circuits stay in optimal condition.
- Environmental control: Store your circuits in a dry and well-ventilated area. Avoid humid environments and areas prone to moisture buildup. Keeping the area clean and dry is key to prevent moisture from accumulating on your circuits.
- Protective coatings: Apply protective coatings to the circuit components. This will create a barrier against moisture and oxygen, preventing rust from forming. There are various types of protective coatings available, depending on the specific application.
- Regular inspection: Conduct regular visual inspections of your circuits. This will allow you to identify any early signs of corrosion before they escalate into more significant problems. Early detection is essential for effective maintenance.
- Proper storage: Store your circuits in protective containers or packaging to safeguard them from environmental factors. This is particularly important for circuits that will be stored for an extended period. Proper packaging is like a shield against external threats.
Preventative Measures
Taking preventative measures can drastically reduce the risk of rust formation on your circuits. These measures are crucial to maintain the integrity and functionality of your circuits.
- Regular cleaning: Implement a routine cleaning schedule for your circuits. Regular cleaning helps to remove dust, debris, and other contaminants that can contribute to moisture accumulation. Regular cleaning is like giving your circuits a fresh start.
- Proper handling: Handle circuits carefully to avoid physical damage that could lead to moisture penetration and subsequent rust formation. Gentle handling is essential to maintain the integrity of your circuits.
- Humidity control: Use dehumidifiers or other humidity control measures to maintain a low humidity environment. This helps to prevent moisture buildup, which is a primary cause of rust. Controlling humidity is crucial for preventing rust.
- Protective enclosures: Use protective enclosures or covers for your circuits to shield them from the elements. This can help to prevent moisture and dust from accumulating on the components. Protective enclosures are like a shield for your circuits.
Examples and Illustrations
Hai semuanya! Kita mau liat contoh-contoh karat di komponen sirkuit, biar lebih jelas cara ngebersihinnya. Bayangin, karat itu kayak musuh yang nakal, beda-beda bentuknya, dan butuh cara berbeda buat ngalahinnya. Mari kita telusuri!Karat pada sirkuit elektronik bisa bikin masalah besar, dari kinerja menurun sampai kerusakan total. Memahami bentuk-bentuk karat penting banget buat kita memilih cara pembersihan yang tepat.
Contoh-contoh visual berikut bakal ngebantu kita pahami berbagai jenis karat dan bagaimana cara ngebersihinnya.
Types of Rust on Circuit Components
Beragam bentuk karat bisa muncul di komponen elektronik. Berikut ini beberapa contoh yang umum ditemui:
- Karat tipis dan merata: Seperti lapisan debu yang menempel di permukaan komponen, biasanya muncul akibat paparan kelembapan ringan. Karat jenis ini relatif mudah dihilangkan dengan metode mekanik.
- Karat berlapis-lapis: Karat yang lebih tebal dan mengeras, biasanya terjadi karena paparan kelembapan yang lebih lama atau kondisi lingkungan yang lebih ekstrem. Metode pembersihan mekanik yang lebih kuat atau mungkin kombinasi dengan metode kimia diperlukan.
- Karat titik-titik: Karat yang muncul di beberapa titik pada komponen, bisa jadi karena material yang berbeda atau karena ada kerusakan sebelumnya. Pemilihan metode pembersihan harus hati-hati dan disesuaikan dengan lokasi karat.
- Karat yang tersembunyi: Karat yang muncul di dalam celah atau lubang pada komponen. Cara pembersihan harus berhati-hati, karena kita harus memastikan semua karat terangkat tanpa merusak komponen.
Visual Examples of Cleaning Methods
Berikut ilustrasi beberapa metode pembersihan karat yang berbeda. Penting buat kita paham cara kerja setiap metode, supaya kita bisa memilih metode yang paling efektif untuk setiap kasus karat.
- Menggunakan sikat kawat halus: Bayangkan ada sikat kawat yang lembut, diputar dengan pelan dan hati-hati untuk membersihkan karat pada permukaan komponen. Ilustrasi: Gambar sikat kawat yang sedang digunakan untuk membersihkan karat pada permukaan yang berkarat. Sikat harus dipilih sesuai dengan ukuran dan bentuk komponen untuk menghindari kerusakan.
- Menggunakan larutan kimia khusus: Kita punya larutan kimia khusus untuk membersihkan karat, seperti larutan asam ringan. Ilustrasi: Gambar larutan kimia yang dituangkan ke komponen yang berkarat. Penting banget untuk menggunakan sarung tangan dan peralatan pelindung lainnya, karena larutan ini bisa berbahaya. Pastikan kita tahu cara menggunakannya dengan benar dan hindari kontak dengan kulit atau mata.
Before and After Cleaning Diagrams
Diagram sebelum dan sesudah pembersihan bisa ngebantu kita melihat perubahan yang terjadi. Kita bisa bandingkan kondisi komponen sebelum dan sesudah dibersihkan untuk memastikan proses pembersihan berhasil.
Sebelum Pembersihan | Sesudah Pembersihan |
---|---|
Gambar: Komponen elektronik dengan karat yang tebal dan merata. | Gambar: Komponen elektronik yang sama, sudah bersih dari karat. Permukaannya terlihat bersih dan berkilau. |
Final Review
In conclusion, removing rust from circuits requires a systematic approach that considers both the safety precautions and the specific nature of the components involved. By following the detailed methods Artikeld in this guide, you can effectively remove rust without causing further damage. This knowledge empowers you to maintain the optimal performance of your electronic circuits and extend their lifespan.
Remember, prevention is key, and by understanding the factors that contribute to rust formation, you can minimize future issues and ensure long-term reliability.
Detailed FAQs
What are the common causes of rust on circuits?
Exposure to moisture, humidity, and corrosive substances are common culprits. Poor storage conditions or environmental factors can also contribute to rust formation. The presence of contaminants can accelerate the process.
What kind of protective gear should I use during rust removal?
Always wear appropriate gloves, eye protection, and a respirator when working with cleaning solutions. Proper ventilation is crucial to minimize inhalation of harmful fumes.
Can I use sandpaper to remove rust from circuits?
While sandpaper might seem like a simple solution, it can damage the delicate components of the circuit. More precise tools are recommended for this task.
How can I prevent rust from forming on my circuits in the future?
Store electronic components in a dry, well-ventilated area. Use appropriate protective coatings and coverings for long-term storage. Regular inspections can help identify and address potential problems early on.