How to cut alumina? This guide dives deep into the world of alumina cutting, covering everything from its properties to the best methods and safety precautions. We’ll explore the various types of alumina, their unique characteristics, and how these affect the cutting process. From mechanical methods to laser cutting, we’ll dissect the advantages and disadvantages of each technique.
Understanding alumina’s properties is crucial for safe and efficient cutting. This comprehensive guide will equip you with the knowledge and tools to tackle alumina cutting projects with confidence, from initial selection of the right method to post-cutting considerations.
Introduction to Alumina Cutting
Alumina, also known as aluminum oxide (Al 2O 3), is a crucial industrial material prized for its exceptional hardness, high melting point, and excellent chemical resistance. Its diverse applications span various sectors, from high-performance ceramics to advanced engineering components. Understanding the different types of alumina and their specific properties is paramount for effective and safe cutting processes.Alumina exists in various crystalline forms, each with unique characteristics impacting its machinability.
Common forms include alpha-alumina, beta-alumina, and others. Alpha-alumina, for instance, typically exhibits higher hardness and a more stable structure than beta-alumina. This structural variation influences the cutting forces and tool wear during machining operations.Cutting alumina requires careful consideration of its properties. Common applications where alumina cutting is essential include manufacturing of high-precision tools, aerospace components, and advanced ceramic parts.
Failure to account for alumina’s diverse characteristics can lead to significant challenges in achieving desired cutting accuracy and tool life. Understanding the relationship between the specific alumina type and the required cutting parameters is critical for efficient and safe operations.
Alumina Types and Properties
Different types of alumina exhibit varying degrees of hardness and melting points, significantly impacting the cutting process. Understanding these differences is crucial for selecting the appropriate cutting tools and parameters.
- Alpha-alumina, known for its high hardness and stability, often presents a more challenging cutting scenario compared to other types. Its superior wear resistance, however, allows for the use of specific cutting tools, and precise control of cutting parameters.
- Beta-alumina, with slightly lower hardness compared to alpha-alumina, generally allows for faster cutting speeds. However, the lower hardness might require the use of tougher cutting tools to maintain the desired cutting precision and prevent tool failure.
Comparison of Alumina Types
The table below highlights the comparative hardness and melting point of various alumina types. These values are critical in selecting appropriate cutting tools and procedures.
Alumina Type | Hardness (Mohs Scale) | Melting Point (°C) |
---|---|---|
Alpha-alumina | 9 | 2050-2072 |
Beta-alumina | 8.5-9 | 2072 |
Delta-alumina | 9 | 2050-2072 |
Theta-alumina | 9 | 2050-2072 |
Methods for Cutting Alumina
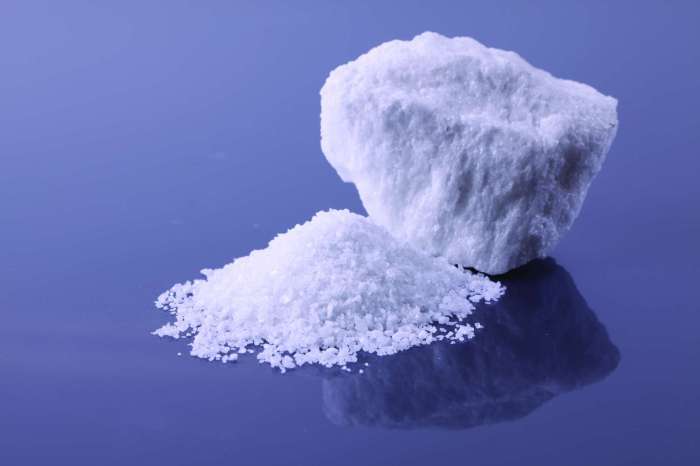
Alumina, a highly versatile and robust material, finds applications in diverse industries, from aerospace to manufacturing. Its exceptional hardness and strength necessitate specialized cutting techniques. Different mechanical methods offer varying degrees of precision, cost-effectiveness, and material removal rates, each with its own set of advantages and disadvantages. Understanding these nuances is crucial for selecting the appropriate cutting method for a specific application.The choice of cutting method for alumina depends on factors such as the desired precision, the size and shape of the workpiece, the required material removal rate, and the budget constraints.
Each method presents a unique trade-off between these factors, influencing the overall efficiency and cost of the manufacturing process.
Mechanical Cutting Methods
Various mechanical methods are employed for cutting alumina, each with its own characteristics. These methods include grinding, sawing, and laser cutting, each offering unique benefits and drawbacks. The selection of the most suitable method depends on the specific requirements of the application.
Grinding
Grinding is a common mechanical cutting method for shaping alumina components. It involves the use of abrasive tools to progressively remove material from the workpiece. This method is particularly effective for achieving precise shapes and intricate details.
- Advantages: Grinding allows for high precision and the creation of complex geometries. It is suitable for producing highly finished surfaces.
- Disadvantages: Grinding can be a relatively slow process, particularly for large workpieces. It can also generate a significant amount of heat, which can affect the integrity of the alumina. The cost of specialized grinding equipment can be high.
Sawing
Sawing, another mechanical cutting technique, employs a saw blade with abrasive teeth to cut through the alumina. This method is often chosen for its ability to cut large pieces quickly and efficiently.
- Advantages: Sawing is generally faster than grinding for larger components and less precise cuts. It can be used for a wider range of alumina grades. It is suitable for cutting relatively simple shapes.
- Disadvantages: The precision of sawing is often lower than grinding, making it less suitable for intricate geometries. The saw blade can become dull and require frequent replacement. The resulting surface finish is often less smooth than grinding.
Laser Cutting
Laser cutting utilizes a high-powered laser beam to vaporize or melt the alumina material. This method offers high precision and allows for complex cutting patterns.
- Advantages: Laser cutting is exceptionally precise and can produce intricate patterns. It generates minimal heat input, which can be beneficial for certain alumina types. The process is fast and efficient, suitable for high-volume production.
- Disadvantages: Laser cutting equipment is expensive. The process can be limited by the material thickness, and the cost of the cutting material can be high for thicker alumina pieces.
Impact of Cutting Parameters
Cutting speed and feed rate significantly affect the quality of the cut. Higher cutting speeds can lead to faster material removal, but may result in increased heat generation and reduced precision. Optimal feed rates need to be carefully balanced to minimize tool wear and ensure smooth material removal.
Abrasive Tools
Abrasive tools, such as grinding wheels and cutting blades, are crucial for effectively cutting alumina. These tools use abrasive particles to remove material from the workpiece. The selection of the appropriate abrasive material and grain size depends on the specific alumina grade and the desired finish.
Equipment Comparison
Cutting Method | Equipment Required |
---|---|
Grinding | Grinding machine, abrasive wheels, coolant system |
Sawing | Sawing machine, saw blade, coolant system |
Laser Cutting | Laser cutting machine, specialized alumina cutting parameters |
Precision Comparison
The precision achievable with each method varies. Laser cutting generally offers the highest precision, followed by grinding. Sawing provides the lowest precision, making it suitable only for simple shapes.
Factors Affecting Alumina Cutting
Alumina, renowned for its exceptional hardness and strength, presents unique challenges during the cutting process. Understanding the factors influencing the selection of a cutting method is crucial for achieving optimal results and minimizing potential risks. These factors encompass material properties, cutting parameters, and safety considerations. The choice of cutting method significantly impacts the final product quality, cost, and safety.Material characteristics, including hardness and brittleness, significantly influence the cutting process.
The selection of cutting tools and methods directly correlates with the desired surface finish and the tolerance for potential damage. Temperature fluctuations during the cutting process can also affect the final outcome.
Material Properties and Their Impact
The inherent hardness and brittleness of alumina directly influence the choice of cutting method. Extremely hard materials like alumina require specialized tools and techniques to prevent premature tool wear and ensure clean cuts. Brittleness, a characteristic of alumina, predisposes it to chipping and cracking during the cutting process. This property necessitates careful consideration of cutting speed and feed rates to minimize such occurrences.
The selection of the right cutting tool geometry is also crucial to reduce the potential for chipping.
Role of Cutting Fluids (if used)
Cutting fluids, when used, play a vital role in minimizing friction and heat buildup during the cutting process. Lubrication and cooling, the primary functions of these fluids, reduce the risk of tool wear and maintain a stable cutting environment. The selection of the appropriate cutting fluid depends on the specific alumina grade and the cutting method employed. Proper lubrication and cooling enhance the efficiency and safety of the cutting process.
Choosing the wrong fluid can lead to issues such as tool damage, material contamination, or even safety hazards.
Safety Hazards and Preventive Measures
Alumina cutting can pose several safety hazards, including the generation of sharp fragments and dust particles. These particles can be inhaled, leading to respiratory issues. High temperatures generated during cutting can cause burns or ignite flammable materials. Protective equipment, such as safety glasses, respirators, and appropriate clothing, is essential for minimizing the risks associated with alumina cutting.
Adequate ventilation systems should be in place to control dust and fumes. Proper handling and storage of cutting fluids are also crucial safety considerations.
- Potential Hazards: Sharp fragments, dust inhalation, high temperatures, flammable materials, eye injuries, and skin contact with cutting fluids.
- Preventive Measures: Appropriate personal protective equipment (PPE), including safety glasses, respirators, and protective clothing; adequate ventilation; proper handling and storage of cutting fluids; and a safe working environment.
Effect of Temperature on Alumina During Cutting
High temperatures generated during the cutting process can affect the microstructure and properties of the alumina. Elevated temperatures can lead to thermal stress and potentially affect the dimensional accuracy of the workpiece. Careful control of cutting parameters, such as speed and feed, is crucial to manage the temperature generated during the cutting process. The use of cutting fluids, as mentioned earlier, plays a significant role in dissipating heat and maintaining a safe cutting environment.
Selection of the appropriate cutting fluid can directly influence the temperature management during the process.
Material Thickness, Desired Shape, and Surface Finish
The material thickness significantly impacts the choice of cutting method. Thicker materials often require more powerful cutting tools and specialized techniques. The desired shape and surface finish of the alumina also play a significant role in the selection of the cutting method. Precision cutting methods are essential for achieving intricate shapes and high-quality surface finishes. The tolerance for surface imperfections and dimensional accuracy also directly affects the selection of the cutting method.
Safety Precautions During Alumina Cutting
Alumina, a hard and chemically inert material, requires specialized cutting techniques and stringent safety measures. Improper procedures can lead to significant health risks. Understanding and adhering to safety precautions is crucial to preventing injuries and maintaining a safe working environment during alumina cutting operations.Effective safety measures are paramount during alumina cutting due to the potential for hazardous dust particles and equipment-related risks.
By prioritizing safety, workers can minimize the likelihood of accidents and maintain a healthy and productive work environment.
Personal Protective Equipment (PPE)
Adequate personal protective equipment (PPE) is essential for mitigating health hazards during alumina cutting. This includes specialized clothing and gear designed to shield workers from airborne contaminants and potential physical hazards. Failure to use proper PPE can result in significant health issues.
- Eye Protection: Safety glasses or full-face shields are vital to protect the eyes from flying debris and dust particles.
- Respiratory Protection: Respirators with appropriate filters are necessary to filter out harmful alumina dust, especially during high-intensity cutting operations. The type of respirator depends on the specific cutting method and the concentration of alumina dust in the air. Proper respirator fit and maintenance are critical.
- Skin Protection: Gloves and protective clothing are essential to prevent skin contact with alumina dust and potential chemical contaminants, especially during grinding and other surface preparation steps.
- Hearing Protection: If the cutting process produces significant noise, hearing protection such as earplugs or earmuffs should be worn to prevent hearing loss.
Health Hazards Associated with Alumina Dust
Alumina dust inhalation can lead to various respiratory problems, including silicosis, an irreversible lung disease. Prolonged exposure to alumina dust can cause irritation to the skin, eyes, and respiratory tract. Appropriate safety measures are critical to mitigate these risks.
- Respiratory Issues: Inhalation of alumina dust can lead to a range of respiratory issues, from mild irritation to serious lung diseases like silicosis. Symptoms of respiratory problems can be delayed, making regular health monitoring crucial.
- Skin Irritation: Direct contact with alumina dust can cause skin irritation, dryness, and allergic reactions. Frequent washing and use of protective creams can reduce these risks.
- Eye Irritation: Flying debris and dust during cutting operations can cause eye irritation, leading to discomfort and potentially more severe injuries.
Specific Safety Guidelines for Each Cutting Method, How to cut alumina
The specific safety precautions depend on the cutting method employed. Each method presents its own set of risks and requires tailored safety protocols. Following these guidelines minimizes the risk of accidents.
Cutting Method | Safety Equipment | Safety Procedures |
---|---|---|
Waterjet Cutting | Full-face shield, safety glasses, respirators, gloves, and waterproof clothing. | Maintain adequate water pressure and flow to effectively control dust. Keep the area well-ventilated. Wear proper PPE at all times. |
Laser Cutting | Eye protection, respirators, and safety glasses. | Ensure the laser cutting enclosure is properly sealed and ventilated. Use appropriate respiratory protection. Regular maintenance of the laser cutting machine is essential to prevent hazards. |
Plasma Cutting | Full-face shield, safety glasses, respirators, gloves, and hearing protection. | Maintain adequate ventilation and use proper respiratory protection. Ensure the plasma cutting machine is properly grounded. Keep a safe distance from the cutting area. |
Emergency Procedures
Establishing clear emergency procedures is vital in case of accidents during alumina cutting operations. A well-defined plan can minimize the impact of incidents and ensure swift and effective responses.
- First Aid: Ensure trained personnel are readily available to administer first aid in case of injuries. Emergency medical services should be immediately contacted for serious injuries.
- Evacuation: Develop a clear evacuation plan in case of fire or other emergencies. Ensure all workers are aware of the evacuation routes.
- Reporting: Establish a system for reporting all incidents, no matter how minor. Comprehensive reporting allows for identification of patterns and improvement of safety procedures.
Waste Disposal
Proper disposal of waste generated during alumina cutting is crucial to prevent environmental contamination. Alumina dust and other materials need careful handling to minimize environmental impact.
- Dust Collection: Utilize dust collection systems to capture alumina dust and other waste materials generated during the cutting process.
- Proper Storage: Store collected dust and waste materials in designated, sealed containers to prevent leakage and contamination.
- Regulatory Compliance: Adhere to all local, state, and federal regulations for waste disposal and handling.
Tools and Equipment for Alumina Cutting
Alumina, due to its high hardness and strength, necessitates specialized tools and equipment for efficient and safe cutting. Selecting the correct tools is critical to achieving clean cuts, minimizing material waste, and ensuring operator safety. This section details the various tools and equipment employed in different alumina cutting methods, emphasizing their functionalities and suitability for specific alumina types.Effective alumina cutting relies on a combination of factors, including the cutting tool’s material, design, and sharpness, along with the equipment’s ability to apply the required force and control the cutting process.
Choosing the right combination is essential for minimizing material damage and maximizing cutting efficiency.
Specific Tools for Abrasive Cutting
Abrasive cutting methods are commonly used for alumina due to their ability to effectively remove material without causing excessive heat buildup. Different types of abrasive tools are used, each with varying specifications and capabilities.
- Abrasive Wheels: These wheels are composed of abrasive grains bonded to a backing material. The type and size of abrasive grains, along with the wheel’s structure, significantly impact the cutting performance. For instance, high-performance alumina cutting wheels often utilize diamond or CBN (cubic boron nitride) abrasive grains for their superior hardness and durability. The wheel’s diameter, thickness, and mounting method are critical parameters for optimal cutting performance.
- Abrasive Cutters: These are specialized tools with abrasive surfaces that directly contact the alumina. They are often used in conjunction with a cutting machine for precise and controlled cutting. The specific abrasive material and the cutter’s geometry are key factors affecting cutting speed and surface finish.
- Grinding Disks/Wheels: These tools are used for smoothing and finishing cut surfaces after the initial cutting operation. The grit size and type of abrasive material determine the level of surface refinement achieved. Different alumina grades may necessitate different grinding disk specifications for achieving optimal results.
Specific Tools for Non-Abrasive Cutting
While abrasive cutting is prevalent, other methods, such as waterjet cutting, are suitable for certain alumina types and applications.
- Waterjet Cutting Equipment: This method utilizes a high-pressure water stream to cut through the material. Specialized nozzles and pumps are crucial for achieving the necessary pressure and precision. Waterjet cutting is particularly suitable for intricate shapes and thin sections of alumina due to its minimal heat generation and precise cutting capabilities.
- Laser Cutting Equipment: Laser cutting employs a focused laser beam to vaporize or melt the alumina material. The laser’s power and focus are critical for achieving precise cuts and minimizing material distortion. Laser cutting is effective for complex shapes and high-precision applications. Different laser types (e.g., CO2, fiber) will have different capabilities when cutting various alumina grades.
Tool Selection Criteria
The choice of cutting tools depends heavily on the properties of the alumina material being cut.
Alumina Type | Suitable Cutting Tool | Specifications |
---|---|---|
High-purity, hard-grade alumina | Diamond-impregnated abrasive wheels or CBN abrasive cutters | High hardness, durability, and resistance to wear are essential. |
Medium-hardness alumina | Silicon carbide abrasive wheels or waterjet cutting | Moderate hardness and strength; suitable for various applications. |
Soft alumina | Waterjet or laser cutting | Lower hardness; waterjet or laser cutting are more suitable for minimizing thermal damage. |
Maintenance Procedures
Proper maintenance of cutting tools and equipment is vital for optimal performance and safety.
- Regular Inspection: Inspect tools for damage, wear, and sharpness before each use. Inspect cutting equipment for leaks, clogs, and proper functionality. This is a critical step to prevent accidents.
- Cleaning: Clean abrasive tools after each use to remove alumina particles and debris, preventing clogging and premature wear. This also enhances the tool’s lifespan.
- Sharpening/Replacement: Sharpen or replace abrasive tools as needed to maintain their cutting edge. This is crucial for ensuring consistent cutting performance. Replacement is essential if the tool shows signs of excessive wear or damage.
- Equipment Servicing: Schedule regular servicing and maintenance for waterjet or laser cutting equipment, ensuring the system operates at optimal pressure and efficiency.
Cutting Parameters for Alumina
Optimizing cutting parameters is crucial for achieving high-quality cuts in alumina while minimizing material waste and tool wear. Selecting appropriate cutting speed, feed rate, and depth of cut directly impacts the efficiency and precision of the cutting process. Understanding the interplay between these parameters and the specific type of alumina being worked with is paramount.
Impact of Alumina Type on Cutting Parameters
Different types of alumina exhibit varying hardness and fracture toughness, significantly influencing the optimal cutting parameters. For example, high-purity alumina, often used in high-precision applications, requires a more delicate approach than coarse-grained alumina employed in structural components. Understanding these material properties is essential for choosing the correct cutting parameters to ensure a clean cut without excessive tool wear or material damage.
Cutting Speed, Feed Rate, and Depth of Cut
These three parameters are fundamental to the alumina cutting process. Cutting speed, measured in meters per minute (m/min), determines the rate at which the cutting tool interacts with the material. Feed rate, measured in millimeters per revolution (mm/rev), controls the rate at which the cutting tool advances along the workpiece. Depth of cut, measured in millimeters (mm), defines the material removal rate.
The interplay between these parameters is complex and requires careful consideration to avoid excessive tool wear, material damage, and inconsistent cuts.
Optimizing Cutting Parameters
A systematic approach to optimizing cutting parameters involves several key techniques. Experimentation with different parameter combinations is crucial to identify the optimal settings for specific alumina types and cutting methods. Monitoring tool wear and material removal rate during the cutting process provides valuable feedback for adjusting parameters. Utilizing computer-aided design (CAD) and computer-aided manufacturing (CAM) software can assist in creating precise cutting paths and estimating the required cutting parameters.
Considering the specific application and desired surface finish also plays a vital role in selecting the optimal parameters.
Examples of Cutting Parameters for Different Alumina Types and Applications
Alumina Type | Cutting Method | Cutting Speed (m/min) | Feed Rate (mm/rev) | Depth of Cut (mm) |
---|---|---|---|---|
High-purity alumina (99.9%) | Wire EDM | 10-20 | 0.05-0.1 | 0.1-0.2 |
Coarse-grained alumina (80%) | CNC milling | 50-100 | 0.2-0.5 | 1-2 |
Alumina ceramic | Waterjet | Variable (dependent on nozzle pressure and water flow rate) | Variable | Variable (dependent on nozzle size and material thickness) |
These are just examples and actual values may vary significantly based on specific alumina characteristics, tooling, and machine capabilities.
Importance of Consistent Cutting Parameters
Maintaining consistent cutting parameters is paramount for achieving high-quality cuts in alumina. Variations in these parameters can lead to inconsistent surface finishes, premature tool wear, and material defects. Implementing standardized procedures and utilizing automated control systems can help maintain consistent parameters throughout the cutting process. Regular monitoring and adjustment of parameters are vital to ensure consistent quality and productivity.
Post-Cutting Considerations: How To Cut Alumina

Post-cutting procedures for alumina are crucial for achieving the desired surface quality and ensuring the final product meets specifications. Proper surface finishing and quality control steps minimize imperfections, improve the material’s performance, and prevent potential issues during subsequent processing stages. This section details the critical steps involved in post-cutting alumina, including surface finishing methods, quality control procedures, and the impact of surface quality on the final product.
Surface Finishing Methods for Alumina
Surface finishing is essential for achieving the required surface quality in alumina components. The choice of finishing method depends on the specific application and the desired surface characteristics, including roughness, flatness, and dimensional accuracy. Different methods offer varying degrees of precision and efficiency.
- Grinding: Grinding is a common surface finishing technique for alumina, particularly for achieving a smooth surface finish. Abrasive grinding wheels remove material from the surface, resulting in a controlled reduction in surface roughness. The selection of grinding wheels, grit size, and pressure is crucial to avoid undesirable surface damage or excessive material removal. This technique is effective for achieving high precision and dimensional accuracy in various alumina applications.
- Polishing: Polishing is employed to refine the surface further, often after grinding. Polishing uses finer abrasives and a polishing compound to achieve a mirror-like finish. This method is essential for applications requiring exceptionally smooth surfaces, such as optical components or high-precision parts. Polishing removes microscopic scratches and irregularities left behind by grinding, significantly improving the surface quality.
- Lapping: Lapping is another surface finishing technique used to achieve a highly precise and smooth surface finish. It utilizes a flat lapping plate and a fine abrasive slurry to create a uniform surface. This method is often used in conjunction with grinding or polishing to achieve a final, high-quality finish. It’s particularly suitable for components requiring precise dimensional tolerances and a very low surface roughness.
- Chemical Etching: Chemical etching is a chemical process that selectively removes material from the surface of alumina. It’s often used to improve the surface finish and remove surface imperfections. The chemical solution and etching time are carefully controlled to ensure consistent results and avoid damage to the underlying material. This method can be effective in creating a specific surface texture or removing surface contamination.
Quality Control Procedures for Cut Surfaces
Rigorous quality control is essential to ensure the cut surfaces of alumina meet the required standards. These procedures verify the dimensional accuracy, surface roughness, and absence of defects, ensuring the integrity and reliability of the finished product.
- Dimensional Inspection: Measuring the dimensions of the cut alumina parts against the specified tolerances is crucial. This involves using various measuring instruments, such as calipers, micrometers, and coordinate measuring machines (CMMs), to ensure the parts meet the required dimensions. These measurements are essential to guarantee that the part fits into the intended assembly.
- Surface Roughness Measurement: Measuring surface roughness using surface roughness instruments, such as profilometers, helps determine the smoothness of the cut surface. This measurement provides data on the average surface roughness, which is a critical factor in evaluating the quality of the finished product. Different applications require varying levels of surface roughness, so precise measurements are essential.
- Visual Inspection: Visual inspection of the cut surfaces is often performed to identify any defects, such as cracks, chips, or other irregularities. Trained personnel examine the surfaces for visual imperfections, ensuring that the cut surfaces are free from flaws. Visual inspection can be complemented with other methods for comprehensive quality control.
- Material Analysis: In some cases, material analysis is performed to assess the chemical composition and microstructure of the cut surfaces. This helps determine if the cutting process has introduced any undesirable changes or contaminants. Material analysis can detect microscopic defects that might not be visible through visual inspection.
Surface Finishing Examples for Different Applications
The appropriate surface finishing technique depends on the specific application of the alumina component.
- Optical Components: Polishing is the preferred surface finishing method for optical components. The high degree of smoothness and flatness obtained through polishing ensures optimal light transmission and reflection, crucial for applications like lenses and prisms.
- Bearing Surfaces: Grinding followed by lapping is often used to prepare bearing surfaces for enhanced wear resistance and reduced friction. This combination ensures a precise surface finish and proper dimensional accuracy for the bearing’s functionality.
- Structural Components: Grinding is commonly used for structural components. The method provides a balance between surface finish and dimensional accuracy, suitable for applications requiring high mechanical strength.
Final Wrap-Up
In conclusion, cutting alumina effectively involves careful consideration of its unique properties, the chosen method, and meticulous adherence to safety protocols. This guide provided a robust overview of the entire process, from initial material characterization to post-cutting surface finishing. By understanding the nuances of alumina cutting, you can ensure successful outcomes and project completion.
FAQs
What are the most common types of alumina used in cutting applications?
Alpha and beta alumina are common types. Alpha alumina is generally harder and more stable, while beta alumina may have different properties depending on the specific application.
What are the potential health hazards associated with alumina dust?
Inhaling alumina dust can cause respiratory issues. Always wear appropriate respiratory protection and follow safety guidelines to mitigate these risks.
What are some examples of surface finishing methods for alumina?
Grinding, polishing, and chemical etching are examples of surface finishing techniques. The chosen method depends on the desired surface quality and application.
What factors influence the selection of a cutting method for alumina?
Factors such as material thickness, desired shape, surface finish, and budget influence the choice of cutting method. Consider the trade-offs between speed, precision, and cost.