How to determine bolt face diameter is critical for ensuring structural integrity and safety in various applications. Understanding the nuances of direct and indirect measurement techniques, along with factors influencing selection, is essential for professionals in engineering, manufacturing, and construction. Different bolt types and their associated face diameters, as well as standard practices and tolerances, are discussed to provide a complete picture of this crucial aspect of mechanical design.
This guide delves into the essential methods for accurate bolt face diameter determination, from basic techniques to handling complex geometries. It explores the relationship between bolt face diameter, material properties, and design specifications, providing practical insights into the selection process. The importance of adhering to industry standards and tolerances is highlighted to ensure optimal performance and safety.
Introduction to Bolt Face Diameter: How To Determine Bolt Face Diameter
Knowing the precise bolt face diameter isn’t just a matter of precision; it’s about ensuring your structures stand the test of time and your projects don’t end up looking like a poorly-assembled Jenga tower. A correct bolt face diameter is crucial for the structural integrity and longevity of anything from bridges to bicycles. Ignoring this seemingly small detail can lead to significant problems down the road, and trust us, no one wants a catastrophic failure.This crucial dimension dictates how the bolt interacts with the surrounding materials, influencing everything from clamping force to overall load distribution.
Understanding the implications of various bolt face diameters is essential for ensuring safety and preventing costly repairs or, worse, catastrophic failures.
Importance of Bolt Face Diameter
Accurate bolt face diameter is fundamental to achieving a secure and reliable connection. The correct diameter ensures the bolt head or nut seats evenly, preventing stress concentrations and premature wear. This, in turn, guarantees the long-term integrity of the joint. Incorrect dimensions lead to uneven loading, potential slippage, and, ultimately, structural weakness.
Applications Requiring Precise Bolt Face Diameter
Bolt face diameter is critical in a vast array of applications, ranging from everyday appliances to complex engineering projects. In bridges, precise face diameters are vital to ensure structural stability and prevent catastrophic collapses. In aircraft construction, even slight discrepancies can compromise the integrity of the entire structure. In machinery, consistent bolt face diameters are critical to ensure smooth operation and prevent malfunctions.
Think about the intricate assembly of a high-speed train – each bolt face diameter is meticulously controlled to maintain the train’s performance and safety.
Bolt Types and Their Face Diameters
Different types of bolts are designed for different purposes, and each type typically requires a specific bolt face diameter. The face diameter is carefully selected to provide the correct clamping force and prevent excessive stress on the components. For instance, machine bolts, typically used in heavy-duty machinery, need larger face diameters to accommodate greater loads. High-strength bolts, commonly employed in high-stress applications, are often accompanied by precisely machined face diameters.
Significance of Correct Bolt Face Diameter in Structural Integrity and Safety
Using the correct bolt face diameter is paramount to achieving a strong and safe joint. An incorrectly sized bolt face diameter can lead to stress concentrations, uneven load distribution, and ultimately, failure. Consider a building under construction – if the bolt face diameters are inconsistent, the building’s structural integrity could be compromised.
Consequences of Using Incorrect Bolt Face Diameter
Using an incorrect bolt face diameter can have severe consequences. Uneven clamping force can lead to premature wear and tear of the components. Stress concentrations can result in localized failures, potentially compromising the structural integrity of the assembly. These issues can result in costly repairs, safety hazards, and even catastrophic failures. Imagine a critical component failing in a bridge due to a seemingly insignificant discrepancy in bolt face diameter – the potential ramifications are enormous.
Methods for Determining Bolt Face Diameter
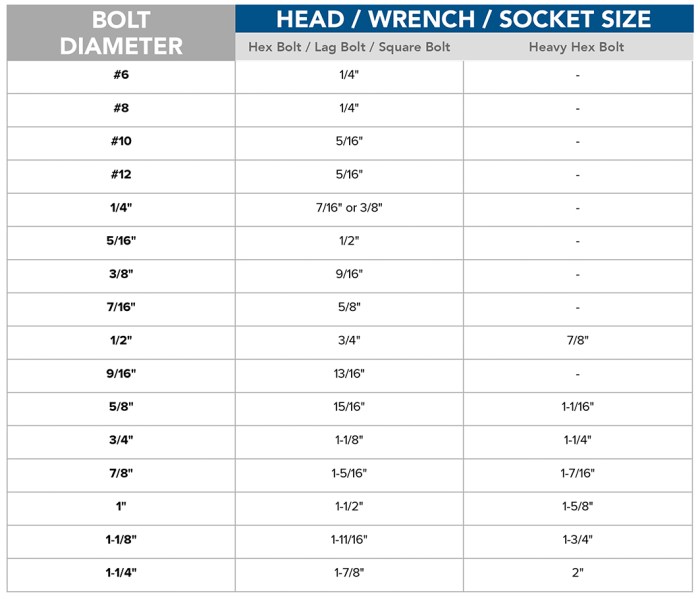
Unlocking the secrets of a bolt’s face diameter is like deciphering a cryptic message left by a mischievous engineer. It’s crucial for everything from ensuring proper assembly to preventing catastrophic failures. Accurate measurements are paramount, so let’s delve into the various methods available, from the straightforward to the subtly sophisticated.
Direct Measurement Methods
Direct measurement methods, like a direct hit to the target, offer the highest degree of accuracy. These methods involve physically measuring the bolt face diameter using tools specifically designed for precision. These methods are often the gold standard in demanding applications where the slightest deviation can have serious consequences.
- Caliper Measurement: Caliper tools are like trusty compasses, guiding you to the precise diameter. A set of calipers, typically digital or mechanical, is employed to grasp the bolt face. The readings, displayed clearly on the tool, represent the diameter. This method works best for simple, round shapes. Be sure to choose calipers appropriate for the size of the bolt face to avoid errors.
For example, using a small caliper on a large bolt face could lead to an inaccurate measurement.
- Micrometer Measurement: Micrometers are the epitome of precision. These sophisticated instruments, with their calibrated screw mechanisms, allow for extremely accurate measurements. To measure, position the bolt face firmly against the micrometer’s anvil. Carefully rotate the thimble to make the measurement. Micrometers are ideal for highly precise measurements, often used in manufacturing environments where tolerances are extremely tight.
- Vernier Caliper Measurement: Vernier calipers are a great compromise between accuracy and simplicity. They are a more accessible option than micrometers. The Vernier scale allows for fractional readings, enabling more precise measurements than traditional calipers. These are valuable for a wide range of applications, including general engineering work and quality control.
Indirect Measurement Methods
Indirect measurement methods are like solving a puzzle by finding clues. They rely on formulas or calculations to determine the bolt face diameter from other measurable characteristics. These methods, while less precise than direct measurements, are often faster and more practical in certain situations.
- Using Drawings/Specifications: Many blueprints or specifications include the bolt face diameter. This is a rapid method, but relies on the accuracy of the document. Ensure that the document is up-to-date and reliable. Incorrect data from drawings can lead to serious errors.
- Using a Template: For bolts with standardized designs, templates can be used to measure the face diameter. This approach is helpful when dealing with repetitive measurements, but only works with predefined sizes. Templates, if carefully made, provide consistency in measurements, preventing errors.
Comparison Table
Method | Advantages | Disadvantages | Applications |
---|---|---|---|
Direct Measurement | High accuracy, immediate results | Specialized tools required, potential for operator error | Precision machining, critical assemblies |
Indirect Measurement | Ease of use, faster for repetitive tasks | Potentially lower accuracy, reliant on accurate data | General maintenance, routine inspections |
Step-by-Step Procedures (Direct Measurement)
These procedures are for direct measurement using calipers. Following these steps meticulously will yield the most accurate results.
- Preparation: Ensure the bolt face is clean and free from any debris or contaminants. A clean surface is essential for accurate measurements.
- Caliper Selection: Select calipers appropriate for the bolt face diameter to avoid errors.
- Positioning: Position the calipers around the bolt face, ensuring the jaws are firmly in contact with the face.
- Reading: Read the displayed measurement from the caliper, ensuring the correct units are used. Remember to account for any scale factors on the device.
Factors Affecting Bolt Face Diameter
Picking the perfect bolt face diameter is like choosing the right pair of shoes for a marathon – it’s not just about looks, it’s about functionality and performance. A poorly chosen face diameter can lead to headaches, potentially damaging the whole assembly. Understanding the factors influencing this crucial dimension is key to a successful fastening project.Bolt face diameter isn’t just a random number; it’s a calculated decision based on various factors.
These factors interact in complex ways, so it’s important to consider them all to ensure a secure and reliable fastening solution.
Material Properties
Material properties play a significant role in determining the appropriate bolt face diameter. Different materials have varying strengths and tolerances. A softer material, like aluminum, needs a smaller face diameter to avoid stressing the material beyond its limits, while a tougher material like steel can handle a larger face diameter. This relationship between material strength and face diameter is crucial for ensuring the joint’s integrity.
The bolt face diameter must be selected carefully to ensure the material stresses are within acceptable limits, preventing failure or deformation.
Bolt Head Style
The bolt head style directly influences the effective face diameter. A large, robust head, such as a hex head, will require a larger face diameter to distribute the clamping force evenly. Conversely, a small, flush head will typically need a smaller face diameter. This is a critical design consideration; the face diameter must be large enough to avoid stress concentrations under the head, but not so large as to create excess material.
Essentially, the bolt head’s design dictates the minimum acceptable face diameter to ensure safe and efficient fastening.
Thickness of Connecting Parts, How to determine bolt face diameter
The thickness of the connecting parts significantly impacts the bolt face diameter selection. Thicker materials need a larger face diameter to effectively transmit the clamping force across the entire surface. Think of it like a bridge – a thicker support structure requires a wider base for stability. The bolt face diameter needs to account for the thickness of the parts being joined, preventing excessive stress on the thinner material and ensuring the assembly can withstand expected loads.
Design Specifications
Design specifications, often overlooked, are critical factors. These specifications, including load requirements, operating conditions, and safety margins, all dictate the ideal bolt face diameter. For example, a high-stress application, like a heavy-duty machine, will require a larger face diameter to handle the increased loads. Meeting these design specifications is paramount for avoiding potential failures and maintaining safety.
Ultimately, design specifications establish the necessary parameters for selecting the optimal bolt face diameter.
Standard Bolt Face Diameters
Bolt face diameters, those crucial flat surfaces where bolts meet their mates, aren’t some whimsical design choice. They’re the unsung heroes of structural integrity, ensuring a proper clamping force and preventing premature failure. Understanding standard bolt face diameters is essential for engineers and DIY enthusiasts alike, ensuring everything from your garden shed to a skyscraper stands tall.
Common Standard Bolt Face Diameters
Bolt face diameters aren’t randomly assigned; they’re carefully selected to match the bolt’s size and the intended application. This ensures consistent clamping forces and prevents issues like uneven loading or excessive stress concentrations. The following table provides a glimpse into the world of standard bolt face diameters, connecting bolt sizes to their typical counterparts.
Bolt Size | Face Diameter | Material | Application |
---|---|---|---|
M6 | 10mm | Steel | General use, light-duty fasteners |
M8 | 12mm | Steel | General use, medium-duty fasteners |
M10 | 15mm | Steel/Stainless Steel | Medium to high-stress applications, structural connections |
M12 | 18mm | Steel/Stainless Steel | Heavy-duty applications, machinery |
M16 | 22mm | Steel/Stainless Steel | High-stress applications, demanding environments |
Industry Standards
Various industry standards dictate bolt face diameters, ensuring consistency and interchangeability. These standards are vital for maintaining safety and reliability across diverse applications. For instance, the American Society of Mechanical Engineers (ASME) publishes standards that specify dimensions and tolerances for bolts, which include face diameters. Similarly, international standards organizations like ISO provide guidelines for consistent bolt face diameters, fostering compatibility between parts from different manufacturers.
These standards aren’t just guidelines; they are a guarantee of quality and safety in the world of engineering.
Comparison of Standards
While the basic principle remains the same—matching face diameter to bolt size—subtle differences in specifications exist between different standards. These differences are typically related to the tolerances allowed for the face diameter, ensuring the bolt fits correctly within its intended application. For example, one standard might specify a tighter tolerance for critical applications requiring precise clamping, while another might be more lenient for less demanding tasks.
These variations ensure that the right standard is chosen for the specific application, avoiding potential issues and ensuring the safety and reliability of the structure.
Measuring Bolt Face Diameter in Complex Geometries

Sometimes, determining bolt face diameter isn’t as straightforward as measuring a flat circle. Imagine a bolt head nestled in a contorted chassis, or a bolt that’s part of a complex, three-dimensional assembly. We need a toolbox of techniques to handle these “bolt-shaped-obstacles” and still get precise measurements.Dealing with complex geometries requires adapting our approach. Direct measurement is often impossible, so we must rely on indirect methods, like triangulation, and employ specialized tools to overcome the challenges posed by awkward angles and hard-to-reach areas.
Advanced Measurement Techniques
To conquer the complexities of irregular bolt faces, a multi-pronged approach is essential. Our strategy will include a variety of methods to obtain accurate measurements. This requires a combination of ingenuity and precision tools.
Indirect Measurement Methods
Direct measurement is not always possible when dealing with complex geometries. Fortunately, indirect methods provide alternative approaches. One common method is triangulation. Imagine two strategically placed points of reference, and using a calibrated measuring device (e.g., a digital caliper), you can calculate the bolt face diameter using geometric principles.
- Triangulation: This method involves establishing two points on the bolt face, whose distances from each other and from the center of the bolt are precisely known. These points are then used to calculate the diameter via trigonometric relationships. This is particularly useful when the bolt face is not entirely visible or is obstructed by parts of the machine.
- Coordinate Measurement Machines (CMMs): These machines are capable of extremely precise three-dimensional measurements. CMMs can accurately map the bolt face in complex geometries, and calculate the diameter based on the collected data. They are invaluable when dealing with intricate components where direct measurement is impractical.
Specialized Tools and Equipment
Specialized tools are essential for handling challenging situations. A borescope, a long, thin tube with a camera at one end, is invaluable for viewing hard-to-reach areas. Using the borescope, we can capture detailed images of the bolt face, enabling accurate measurements from a distance.
- Borescopes: These optical tools allow us to see into tight spaces and hard-to-reach areas. Using a borescope with a calibrated scale, we can measure the bolt face’s diameter with high accuracy, even in complex, difficult-to-access situations.
- 3D Scanning Systems: These systems create a digital representation of the object, including the bolt face. Sophisticated software can then extract the diameter data from the 3D model with remarkable precision, even in challenging geometries.
Example: Measuring a Bolt in a Curved Housing
Imagine a bolt embedded within a curved housing. Direct measurement is impossible. To determine the bolt face diameter, we could employ triangulation. Two points are marked on the bolt face, and their distances from the center are carefully measured. These measurements are then used in a simple trigonometry calculation to determine the bolt face diameter.
Flowchart for Measuring Bolt Face Diameter in Complex Geometries
The flowchart illustrates a methodical approach, progressing from initial assessment to final measurement, ensuring the process is efficient and produces accurate results.
Importance of Tolerances in Bolt Face Diameter
Bolt face diameters, while seemingly straightforward, are crucial components in any mechanical assembly. Just like a perfectly fitted glove, precise tolerances are the secret sauce to ensure a snug, reliable, and safe connection. Without proper attention to tolerances, you could be setting the stage for a disastrous assembly, from a loose connection to a catastrophic failure. Let’s dive into the fascinating world of tolerance specifications and how they affect your bolt face diameter.
Understanding Tolerances
Tolerances, in the context of bolt face diameter, are the permissible variations in the measured diameter. Think of it as a range of acceptable values around a target diameter. This range is crucial because manufacturing processes are never perfectly precise. Slight variations are inevitable, and tolerances account for these discrepancies. A well-defined tolerance range ensures that bolts and their mating surfaces will still interlock reliably.
Impact on Functionality and Safety
Tolerances directly influence the functionality and safety of a mechanical assembly. Too loose a tolerance could lead to the bolt face slipping, which can cause vibrations, looseness, or even failure over time. Conversely, a tolerance that is too tight can lead to difficulties in assembly, potential damage to the parts, or even prevent the assembly from happening at all.
Proper tolerance specifications ensure that the bolt face diameter is not too loose or too tight, maintaining a balance between reliability and ease of assembly. This is akin to a well-fitting lock and key—neither too loose nor too tight, but just right.
Interpreting Tolerance Specifications
Tolerance specifications are usually expressed as a plus-minus value (e.g., ±0.1 mm) from a nominal (target) diameter. This means that the actual diameter can vary within a range of 0.1 mm above or below the nominal value. For example, if the nominal diameter is 25 mm, the actual diameter can be anywhere between 24.9 mm and 25.1 mm, and still be considered acceptable.
It’s like a target range for the bolt face, allowing for manufacturing variations while ensuring the final product functions as intended.
Tolerance Classes and Applications
Different tolerance classes cater to different precision requirements. The appropriate tolerance class is selected based on the specific application. Some applications demand high precision, while others might tolerate slightly wider variations. A high-precision instrument, for instance, will require a tighter tolerance than a simple machine part. This table Artikels some common tolerance classes and their applications:
Tolerance Class | Tolerance Value | Application |
---|---|---|
Class A | ±0.1mm | High precision applications like aerospace components, highly sensitive instruments, or where a tight fit is essential for reliable function. |
Class B | ±0.2mm | General-purpose applications, where slightly wider variations are acceptable, such as in many mechanical assemblies. |
Class C | ±0.5mm | Applications where cost is a significant factor and some flexibility in the final dimension is permissible. |
Conclusion
In conclusion, accurately determining bolt face diameter is paramount for reliable and safe mechanical assemblies. This guide has explored the various methods, factors, and considerations involved, providing a comprehensive resource for professionals needing to select and measure bolt face diameters. By understanding the interplay between different techniques and industry standards, readers can ensure the structural integrity and safety of their designs.
Answers to Common Questions
What are the common tools used for direct measurement of bolt face diameter?
Calipers and micrometers are commonly used tools for direct measurement. Their accuracy and precision depend on the specific application and the type of caliper or micrometer employed.
How do tolerances affect the functionality of a bolted assembly?
Tolerances in bolt face diameter directly impact the fit and function of the assembly. Tight tolerances ensure precise alignment and reduce the risk of failure, while looser tolerances can allow for some flexibility but may increase the risk of misalignment or premature wear.
What are some examples of complex geometries where indirect measurement might be necessary?
Complex geometries like those found in curved surfaces or internally-threaded components often require indirect measurement techniques. These techniques involve calculating the face diameter based on known dimensions and utilizing specialized formulas or software.
What are the implications of using an incorrect bolt face diameter?
Using an incorrect bolt face diameter can lead to compromised structural integrity, reduced load-bearing capacity, and potential safety hazards. It’s crucial to adhere to the correct specifications to prevent catastrophic failure.