How to find zero lift line for a wing is crucial in aerodynamic design. Understanding this fundamental concept is essential for optimizing aircraft performance, from the initial design stages to the analysis of flight characteristics. This comprehensive guide will explore the methods, factors, and applications surrounding zero lift line determination, offering a practical approach for engineers and enthusiasts alike.
This guide will detail the theoretical and experimental techniques for identifying the zero lift line, encompassing factors like wing shape, twist, and surface roughness. It will also explain how this knowledge is used in aircraft design, performance analysis, and the design of control surfaces. The discussion will cover diverse applications, from aircraft design to wind turbine blade analysis, providing a clear and actionable framework.
Introduction to Zero Lift Lines
The zero-lift line of a wing, a pivotal concept in aerodynamics, unveils the wing’s intricate relationship with lift. It represents the imaginary line along the wing’s chord where, at a given angle of attack, the aerodynamic forces perfectly balance, resulting in zero lift. Understanding this line is paramount for optimizing wing performance and is critical for precise aircraft design.
Its position reveals the wing’s inherent characteristics, influencing its behavior and ultimately, its flight characteristics.This crucial aerodynamic parameter, the zero-lift line, provides designers with a precise metric to assess the wing’s performance in various flight conditions. Understanding its position and its relationship to other key wing characteristics, like camber and chord, allows engineers to fine-tune the wing’s lift characteristics.
This is fundamental to creating aircraft that meet the demands of specific missions, from high-speed jets to nimble helicopters.
Defining the Zero Lift Line
The zero-lift line is the theoretical line along the wing’s chord where the aerodynamic forces, precisely balanced, produce no lift at a specific angle of attack. This critical point is essential for evaluating the wing’s lift generation mechanism and its susceptibility to stalling. In essence, it’s the baseline for understanding the wing’s aerodynamic properties.
Significance in Aerodynamic Design, How to find zero lift line for a wing
The zero-lift line is instrumental in aircraft design. Its precise location influences the wing’s lift characteristics, which in turn affects the aircraft’s performance, stability, and control. By knowing the zero-lift line, designers can anticipate the wing’s behavior in various flight conditions, ensuring safe and efficient flight. This knowledge allows them to make crucial decisions regarding wing shape, angle of attack, and other critical design parameters.
Relationship to Wing Characteristics
The zero-lift line is intricately linked to other critical wing parameters. Camber, the curvature of the wing’s upper and lower surfaces, directly affects the zero-lift line’s position. Symmetrical wings, with no camber, have a zero-lift line that coincides with the chord line. Conversely, cambered wings, with their characteristic curvature, shift the zero-lift line away from the chord line.
Furthermore, the chord length and its distribution along the wing span also play a critical role in defining the zero-lift line’s position.
Comparison of Zero Lift Lines
Understanding the zero-lift line’s relationship to different wing types is essential for effective aerodynamic design.
Wing Type | Zero Lift Line Position | Description |
---|---|---|
Symmetrical Wing | Coincides with the chord line | These wings have no camber; lift is generated entirely by the angle of attack. |
Cambered Wing | Located ahead or behind the chord line | Cambered wings generate lift at lower angles of attack, and the zero-lift line is displaced from the chord line based on the amount of camber. |
Highly Cambered Wing | Substantially displaced from the chord line | These wings are designed for high lift coefficients, at the expense of higher drag at cruise speeds. |
The zero-lift line position is a crucial element in aerodynamic design, enabling engineers to fine-tune the wing’s performance and the aircraft’s overall flight characteristics.
Determining Zero Lift Line Position: How To Find Zero Lift Line For A Wing
Unveiling the elusive zero-lift line demands a meticulous approach, akin to deciphering a hidden code etched onto the wing’s very essence. The precise location of this crucial reference point dictates the wing’s aerodynamic behavior, influencing lift, drag, and ultimately, flight performance. Understanding its determination is paramount for both theoretical calculations and experimental validation.This pivotal position, the zero-lift line, marks the chordwise location where the lift generated by the wing is precisely zero.
Determining its exact placement within the airfoil is essential for accurate aerodynamic analysis and design. Methods range from sophisticated wind tunnel experiments to intricate theoretical calculations. Each method, while distinct, ultimately aims to pinpoint this elusive aerodynamic landmark.
Experimental Determination of the Zero Lift Line
Experimental methods provide tangible evidence of the zero-lift line’s position, bridging the gap between theoretical models and practical application. These approaches rely on meticulous measurements and controlled environments, ensuring accurate data collection.
- Wind Tunnel Testing: Wind tunnel testing emerges as a cornerstone in experimental determination. By systematically varying the angle of attack of the wing within the controlled wind tunnel environment, researchers meticulously record the lift generated at each angle. A key step involves plotting the lift coefficient against the angle of attack. The intersection of this curve with the zero lift coefficient axis reveals the zero-lift angle of attack.
Crucially, this angle is then translated to the chordwise position. This approach is crucial for validating theoretical models and gaining practical insight into the wing’s performance.
Theoretical Calculation of the Zero Lift Line
Theoretical approaches offer a powerful alternative to experimental methods, providing valuable insight into the intricate interplay of aerodynamic forces. These approaches often rely on established airfoil data and computational fluid dynamics.
- Utilizing Airfoil Data: Airfoil data, meticulously collected from wind tunnel tests or computational simulations, provides a wealth of information about the aerodynamic properties of the airfoil. This data typically includes lift coefficient versus angle of attack curves for various Reynolds numbers. By analyzing this data, the zero-lift angle of attack can be extracted. This angle, coupled with the airfoil’s geometry, facilitates the determination of the zero-lift line’s position.
- Computational Fluid Dynamics (CFD): Sophisticated CFD simulations provide an alternative avenue for predicting the zero-lift line. By numerically solving the governing equations of fluid mechanics, CFD tools can model the airflow around the wing at various angles of attack. This allows for a comprehensive evaluation of lift distribution, leading to the precise location of the zero-lift line. These simulations can be used to examine the impact of different airfoil shapes or boundary conditions.
Steps in Experimental Zero Lift Line Determination
Step | Description |
---|---|
1 | Prepare the Wing Model: Carefully mount the wing model within the wind tunnel, ensuring precise alignment and minimal disturbances. |
2 | Vary Angle of Attack: Systematically adjust the angle of attack of the wing model, recording the corresponding values. |
3 | Measure Lift: Accurately measure the lift generated by the wing at each angle of attack. Specialized instruments, such as force balances, are essential for this step. |
4 | Plot Lift Coefficient vs. Angle of Attack: Plot the lift coefficient against the angle of attack. This crucial step often reveals the linear relationship between lift coefficient and angle of attack, which is critical for the next step. |
5 | Determine Zero Lift Angle: Locate the point on the plot where the lift coefficient intersects the zero axis. This point represents the zero-lift angle of attack. |
6 | Calculate Zero Lift Line Position: Using the zero-lift angle and the wing’s geometry, determine the precise chordwise position of the zero-lift line. |
Calculating Zero Lift Line from Airfoil Data
This method leverages existing airfoil data to deduce the zero-lift line’s position. It involves extracting key aerodynamic parameters from readily available data sources.
- Obtain Airfoil Data: Begin by accessing airfoil data, which typically includes lift coefficient curves against angle of attack. A crucial aspect of this process is verifying the data’s accuracy and reliability.
- Identify Zero Lift Angle: Locate the angle of attack where the lift coefficient is zero. This is a critical step, as it directly informs the next step.
- Determine Zero Lift Line Position: Using the airfoil’s geometry and the identified zero-lift angle, determine the precise chordwise position of the zero-lift line. This involves leveraging the airfoil’s camber and thickness distribution to accurately pinpoint the zero-lift line’s location.
Factors Affecting Zero Lift Line Position
The elusive zero lift line, the enigmatic fulcrum of aerodynamic performance, is not a static entity. Its precise location, a critical parameter for wing design, is intricately sculpted by a symphony of wing characteristics. Understanding these influences is paramount to achieving optimal lift and minimizing drag.
Wing Shape’s Influence
The very form of the wing dictates the zero lift line’s position. A wing’s camber, the curvature of its upper and lower surfaces, profoundly affects the distribution of pressure. A wing with pronounced camber, for instance, typically possesses a zero lift line positioned closer to the wing’s leading edge. Conversely, a flatter wing profile will exhibit a zero lift line closer to the mean aerodynamic chord.
This subtle shift in shape can dramatically alter the wing’s performance characteristics.
Wing Twist’s Impact
Wing twist, a deliberate variation in the angle of incidence along the span, further complicates the determination of the zero lift line. Twist introduces a non-uniform aerodynamic environment across the wing, influencing the lift distribution. A twisted wing, often employed to enhance maneuverability or stall characteristics, possesses a zero lift line that is not a simple straight line.
Instead, the zero lift line will trace a path reflective of the twist’s gradient.
Surface Roughness’s Effect
Surface roughness, seemingly a trivial factor, plays a significant role in altering the zero lift line’s position. Imperfections, no matter how minute, disrupt the smooth flow of air over the wing. These disturbances generate localized pressure differentials, affecting the overall aerodynamic forces. A rough wing will have a zero lift line that deviates from the smooth wing’s position, potentially causing drag and a reduction in performance.
Aspect Ratio’s Role
The aspect ratio, the ratio of a wing’s span to its chord, is a powerful determinant of the zero lift line’s position. A higher aspect ratio, indicative of a longer and narrower wing, tends to position the zero lift line closer to the wing’s quarter-chord point. This relationship stems from the influence of the wing’s span on the lift distribution.
Consider the slender wings of supersonic jets; their high aspect ratios contribute to a zero lift line positioned relatively close to the quarter-chord.
Boundary Layer Characteristics’ Influence
The boundary layer, the thin layer of air adhering to the wing’s surface, significantly impacts the zero lift line’s location. A laminar boundary layer, characterized by smooth, ordered airflow, results in a zero lift line situated closer to the aerodynamic center. Conversely, a turbulent boundary layer, marked by chaotic air motion, causes the zero lift line to shift.
The transition from laminar to turbulent flow, driven by factors like surface roughness and Reynolds number, is crucial in determining the precise location of the zero lift line. A wing designed for high speeds may experience a turbulent boundary layer, impacting the zero lift line’s location.
Applications of Zero Lift Line Knowledge
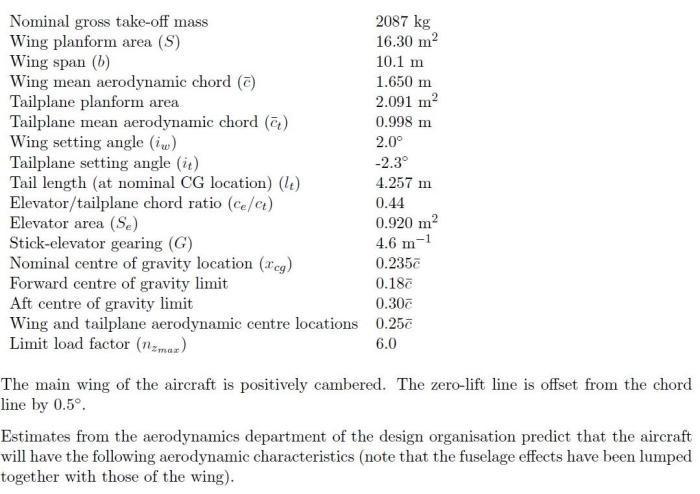
The zero lift line, a pivotal concept in aerodynamics, unveils the heart of a wing’s performance. Understanding its precise location unlocks a wealth of crucial design and analytical capabilities, transforming theoretical principles into tangible aircraft and wind turbine advancements. Its influence transcends mere geometric positioning, dictating stability, control, and ultimately, the very flight characteristics of an aerial machine.Accurate determination of the zero lift line profoundly impacts various facets of aircraft engineering.
Its position, a meticulously calculated parameter, underpins the intricate dance of forces shaping the aircraft’s behavior. This knowledge empowers engineers to design control surfaces, optimize aerodynamic performance, and ensure aircraft stability.
Aircraft Design Applications
Precise knowledge of the zero lift line is paramount in aircraft design. It guides the selection of the wing’s aerodynamic shape and its placement relative to the aircraft’s center of gravity. This strategic positioning ensures proper trim and equilibrium during flight. By carefully considering the zero lift line’s location, engineers can tailor the wing’s profile to achieve optimal lift and drag characteristics, minimizing the effort required for flight.
For instance, adjusting the zero lift line’s position can alter the aircraft’s pitch stability, crucial for a controlled and predictable flight path.
Performance Analysis Applications
The zero lift line plays a critical role in performance analysis. Analyzing the zero lift line’s position allows engineers to accurately predict the aircraft’s aerodynamic behavior in various flight conditions. This detailed understanding enables the estimation of lift, drag, and moment coefficients. For instance, by understanding the influence of the zero lift line, engineers can predict the aircraft’s stall characteristics and optimize the design for safe and efficient flight operations.
This allows engineers to determine the critical angle of attack, ensuring that the aircraft doesn’t stall at unexpected moments.
Control Surface Design Applications
The zero lift line’s position directly impacts the design of control surfaces, such as ailerons, elevators, and rudders. Understanding the zero lift line’s position allows engineers to precisely calculate the forces generated by these surfaces. This allows for precise control inputs, ensuring precise aircraft maneuvers. This information is fundamental in the design of control systems, leading to responsive and predictable aircraft handling.
Wind Turbine Blade Design Applications
The principles of zero lift line apply analogously to the design of wind turbine blades. The zero lift line’s location on a blade dictates the aerodynamic forces experienced during operation. Engineers leverage this information to optimize the blade’s profile for maximum power extraction from the wind. This optimized profile ensures efficient energy capture and reduces the forces exerted on the turbine.
The resulting improvement in power output and reduced stress on the structure are significant advantages.
Impact on Stability and Control
The zero lift line’s position fundamentally affects the stability and control characteristics of an aircraft. Its location relative to the aircraft’s center of gravity directly impacts the aircraft’s inherent stability. This position influences the aircraft’s pitching moment, which is critical for controlled flight. Engineers meticulously calculate the position of the zero lift line to achieve the desired stability and control characteristics.
This calculated precision prevents unwanted oscillations or tendencies to pitch, ensuring a smooth and predictable flight path. Aircraft with a proper zero lift line position are less prone to unexpected maneuvers.
Zero Lift Line and Airfoil Characteristics
The zero-lift line, a pivotal concept in aerodynamics, dictates the precise location where an airfoil experiences zero lift at a given angle of attack. This critical point is intrinsically linked to the airfoil’s very essence, its shape, and its inherent aerodynamic properties. Understanding this relationship is paramount for optimizing aircraft performance and ensuring predictable flight characteristics.The shape of an airfoil profoundly impacts its zero-lift line.
Airfoils are meticulously designed, with their contours carefully sculpted to generate lift. This intricate interplay of shape, coupled with the airflow dynamics, directly influences the location of the zero-lift line. The fundamental principles of fluid mechanics, coupled with the specific geometry of the airfoil, dictate the position of this crucial point.
Influence of Airfoil Section Shape
The precise geometry of an airfoil section significantly dictates its aerodynamic characteristics, including the location of the zero-lift line. The curvature and thickness distribution, intricately woven into the airfoil’s design, are critical determinants. Airfoil sections with complex curvature patterns exhibit a zero-lift line positioned in a more intricate manner compared to simpler shapes.
Thickness and Camber Impact
The thickness and camber of an airfoil section are fundamental factors influencing the zero-lift line. Greater thickness generally results in a zero-lift line positioned further aft, while increased camber shifts it forward. This nuanced interplay of geometry plays a crucial role in shaping the aerodynamic response of the airfoil. Consider the effect of a thicker, more cambered airfoil; it will generate more lift at a given angle of attack, but the zero-lift line will be displaced accordingly.
Comparison of Zero Lift Line Positions for Various Airfoil Types
Different airfoil types exhibit varying zero-lift line positions, directly reflecting their unique aerodynamic characteristics. Symmetrical airfoils, due to their inherent design, often possess a zero-lift line located near the airfoil’s geometric center. Conversely, cambered airfoils, engineered for higher lift at lower angles of attack, exhibit a zero-lift line situated further forward. A classic example of this difference is the NACA 2412, a cambered airfoil with a more forward zero-lift line compared to a symmetrical airfoil like the NACA 0012.
This difference in position underscores the vital role of airfoil design in shaping flight characteristics.
Zero Lift Line Positions for a Range of Airfoil Profiles
Airfoil Profile | Approximate Zero Lift Line Position (Chord Length) |
---|---|
NACA 0012 | 0.5 |
NACA 2412 | 0.4 |
NACA 4412 | 0.35 |
Clark Y | 0.4 |
Eppler E3 | 0.3 |
This table presents a concise overview of the approximate zero-lift line positions for a selection of commonly used airfoil profiles. The data provides a valuable benchmark for understanding the relationship between airfoil design and aerodynamic performance. Note that these values are approximate and can vary slightly based on specific manufacturing tolerances and testing conditions.
Zero Lift Line and Flight Performance
The zero lift line, a critical aerodynamic parameter, dictates the wing’s performance characteristics across the entire flight envelope. Understanding its influence on stability, maneuverability, and stall behavior is paramount for aircraft designers and pilots alike. This knowledge directly translates to a safer, more efficient, and controllable flight experience.The position of the zero lift line profoundly shapes the aircraft’s response to control inputs, affecting everything from gentle turns to abrupt maneuvers.
This intricate relationship underscores the importance of precise zero lift line determination in aircraft design.
Zero Lift Line and Aircraft Stability
The zero lift line’s position significantly impacts the aircraft’s static stability. A properly positioned zero lift line, typically located near the aerodynamic center, ensures that the aircraft exhibits stable tendencies in various flight conditions. This inherent stability allows the aircraft to return to its desired flight path after disturbances. Conversely, an improperly positioned zero lift line can lead to undesirable dynamic instabilities, making the aircraft susceptible to oscillations or unwanted deviations from the intended trajectory.
Modern aircraft designs meticulously account for this factor, ensuring predictable and stable flight.
Zero Lift Line and Aircraft Maneuverability
The zero lift line’s location directly influences the aircraft’s response to control inputs. A zero lift line situated closer to the wing’s leading edge enhances the aircraft’s maneuverability, enabling sharper turns and more agile responses to pilot commands. This responsiveness is particularly crucial in high-performance aircraft requiring quick and precise maneuvers. However, a zero lift line positioned further aft reduces maneuverability, potentially resulting in sluggish responses.
Zero Lift Line and Aircraft Stall Characteristics
The zero lift line’s position plays a significant role in the aircraft’s stall characteristics. A zero lift line positioned further aft typically results in a more gradual stall, providing a noticeable warning to the pilot before a critical loss of lift occurs. This is crucial for ensuring pilot awareness and preventing abrupt stall events. Conversely, a zero lift line located closer to the leading edge may lead to a more abrupt stall, requiring the pilot to react more quickly to maintain control.
Zero Lift Line and Flight Control Systems
Zero lift line data is essential for designing effective flight control systems. By accurately determining the zero lift line, engineers can calibrate the control surfaces and create feedback mechanisms that maintain desired flight characteristics. This allows for precise control over the aircraft’s attitude and trajectory. The system’s sensitivity to control inputs is directly linked to the zero lift line’s location.
Modern flight control systems leverage this data to create a stable and responsive aircraft.
Zero Lift Line and Aircraft Lift and Drag
The zero lift line’s position, although not a direct measure, influences lift and drag characteristics. A zero lift line positioned closer to the aerodynamic center generally results in a more efficient lift-to-drag ratio. This is achieved through optimized aerodynamic design, which reduces the drag and maximizes the lift produced by the wing. Understanding the interplay between zero lift line position, lift, and drag allows for aircraft design optimization, ensuring maximum performance and efficiency.
Advanced Considerations
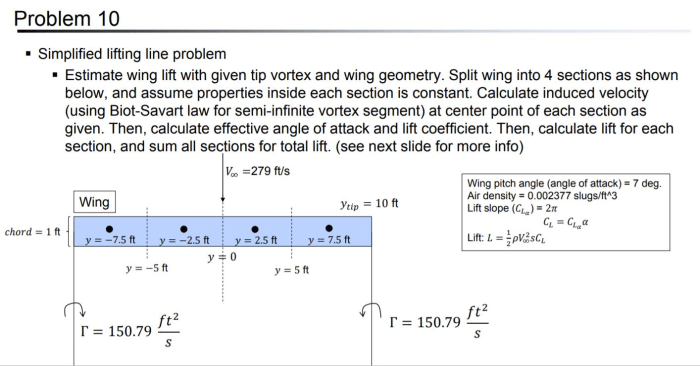
The quest to pinpoint the zero-lift line transcends mere theoretical exercises; it’s a cornerstone in aircraft design, influencing stability, performance, and ultimately, flight. Delving deeper, we uncover intricate relationships with aerodynamic center, CFD simulations, and the subtle yet profound impact of varying flow conditions. Mastering these advanced concepts unlocks the secrets to achieving optimal flight characteristics.
Aerodynamic Center and its Relation to the Zero Lift Line
The aerodynamic center (AC) is a pivotal point on an airfoil. Crucially, the aerodynamic forces acting on the wing, particularly lift and moment, remain constant about this point regardless of the angle of attack. This remarkable property renders the AC a significant reference for analyzing and designing aircraft wings. The zero-lift line, in turn, is the line that passes through the aerodynamic center when the lift is zero.
This fundamental link is critical in understanding the stability and maneuverability of an aircraft.
Computational Fluid Dynamics (CFD) in Zero Lift Line Determination
Computational fluid dynamics (CFD) emerges as a powerful tool in modern aerodynamics. Sophisticated CFD simulations model the intricate airflow patterns around a wing, enabling precise calculations of lift, drag, and moment coefficients. These simulations provide detailed insights into the wing’s behavior, allowing for the precise determination of the zero-lift line position, an essential parameter in aircraft design. Furthermore, CFD allows for analysis of complex wing geometries and flow conditions, something experimental methods often struggle with.
Examples include analyzing wings with complex leading edges, or simulating flow around a wing at high angles of attack.
Impact of Flow Conditions on Zero Lift Line Position
The air’s properties, particularly its compressibility, profoundly influence the zero-lift line position. At lower speeds, the air behaves as an incompressible fluid. As flight speeds increase, the air’s compressibility becomes significant, and the zero-lift line position can shift. The shock waves generated by supersonic flight can significantly alter the pressure distribution around the wing, impacting the aerodynamic center and zero-lift line location.
This phenomenon necessitates careful consideration in the design of high-speed aircraft. The supersonic regime, for instance, demands highly specialized analysis tools and consideration of the impact of compressibility on the zero lift line.
Experimental Setup for Zero Lift Line Determination in a Wind Tunnel
A meticulously crafted experimental setup in a wind tunnel is indispensable for determining the zero-lift line. A precise balance system measures the aerodynamic forces acting on the wing at various angles of attack. The wing is mounted on a pivot, and the balance system records the moment generated about a chosen reference point. By systematically varying the angle of attack and measuring the corresponding moment, the position of the zero-lift line is determined.
Sophisticated sensors and data acquisition systems are crucial to ensure accuracy and precision in these measurements. The wind tunnel’s controlled environment minimizes extraneous factors and ensures the data’s reliability.
Comparison of Zero Lift Line Determination Methods Using Software Tools
Software Tool | Method | Advantages | Disadvantages |
---|---|---|---|
XFOIL | Iterative solution of the airfoil equations | Relatively simple to use, readily available | Limited accuracy for complex geometries, may not handle compressible flow effectively |
Fluent | CFD simulations | Handles complex geometries and flow conditions, high accuracy | Computational intensive, requires specialized expertise |
MATLAB with airfoil functions | Implementation of airfoil theory using numerical methods | Adaptable for various analyses, allows for customization | Requires in-depth knowledge of airfoil theory |
This table highlights the key aspects of different software tools in zero-lift line determination. Each method possesses unique strengths and weaknesses, necessitating a tailored approach based on the specific application and desired level of accuracy. XFOIL, for instance, is a suitable choice for basic airfoil analyses, while CFD simulations offer a more comprehensive view of the flow field around a wing.
Epilogue
In conclusion, accurately determining the zero lift line is paramount for effective aerodynamic design. This guide has explored the theoretical and practical aspects of this crucial concept, highlighting its significance across various engineering disciplines. By understanding the methods for determining zero lift line position and the influence of various factors, engineers can optimize wing design for improved performance and efficiency.
The practical examples and detailed explanations provided offer a robust foundation for further study and application.
Query Resolution
What is the difference between zero lift line and aerodynamic center?
The zero lift line is the point along the chord line where the lift force is zero for a given angle of attack. The aerodynamic center is a point on the airfoil where the moment coefficient about that point is independent of the angle of attack.
How does wind tunnel testing help determine the zero lift line?
Wind tunnel testing allows for controlled measurements of lift and drag forces at various angles of attack. By plotting these forces, the zero lift line can be identified as the point where the lift coefficient is zero.
What are some common errors in determining zero lift line experimentally?
Errors can arise from inaccurate measurements of lift and drag forces, improper calibration of the wind tunnel, and neglecting factors like wing support effects.