How to fix a void when concrete form is removed is a critical concern in construction. This comprehensive guide dives into the various aspects of identifying, diagnosing, and repairing voids, offering practical strategies for restoring structural integrity. From assessing the extent of the damage to choosing the right repair method, this article provides a complete solution.
Different types of voids can occur, ranging from minor shrinkage cracks to more significant structural issues caused by construction errors or material deficiencies. Understanding these variations is crucial for effective repair. This article examines the underlying causes, enabling informed decisions about the best repair methods. Visual identification techniques and structural integrity assessments are detailed to guide the reader through the process.
Identifying the Void’s Characteristics
Upon removal of concrete forms, voids of varying types and severity can emerge. Understanding these voids’ characteristics, including their potential causes and visual indicators, is crucial for effective assessment and repair. A thorough inspection enables the determination of the void’s impact on the surrounding concrete’s structural integrity.Careful evaluation of voids is essential to guide appropriate repair strategies, preventing further structural issues.
Accurate identification of the void’s nature, extent, and depth facilitates informed decisions regarding the necessary remedial measures.
Types of Voids
Various factors can contribute to the formation of voids in concrete. These include improper formwork placement, insufficient concrete mix design, or issues during the pouring and curing processes. Shrinkage cracks, stemming from the concrete’s drying and contraction, are common occurrences. Construction errors, such as inadequate form support, can also lead to the creation of voids. Material deficiencies, including insufficient reinforcement or low-quality aggregates, can create weaknesses in the concrete, increasing the risk of void formation.
Visual Identification Methods
Visual assessment plays a vital role in identifying the extent and depth of a void. Non-destructive techniques like visual inspection using a borescope, a long, thin, flexible tube with a camera at one end, can provide a detailed view of the interior of the void. Careful examination can detect the size, shape, and irregularities within the void. Using a high-resolution camera mounted on a tripod allows for the capturing of detailed images and videos of the void for comprehensive documentation.
Specialized tools, like depth gauges, can precisely measure the depth of the void. The use of a laser scanner can produce detailed 3D models of the void, aiding in the assessment of its extent and irregularities.
Assessing Structural Integrity
Evaluating the structural integrity of the concrete surrounding the void is critical. Load-bearing capacity assessment is essential. A structural engineer’s expertise is often required for accurate load-bearing capacity estimations. They can conduct load tests or finite element analysis to determine the impact of the void on the overall structure. The location of the void in relation to critical structural elements, such as beams or columns, should be considered.
Analyzing the surrounding concrete’s compressive strength and its compliance with design specifications can provide insights into the potential risks associated with the void.
Void Characteristics Table
Void Type | Causes | Typical Visual Characteristics |
---|---|---|
Shrinkage Cracks | Insufficient curing, rapid drying, low humidity | Fine cracks, often hair-line, running parallel or radiating from a point |
Construction Errors | Improper formwork placement, inadequate support, uneven concrete placement | Large irregular cavities, possible tilting or misalignment of structural elements |
Material Deficiencies | Low-quality aggregates, insufficient reinforcement, inadequate concrete mix design | Pockets or cavities, weak or fractured concrete around the void |
Determining the Cause of the Void
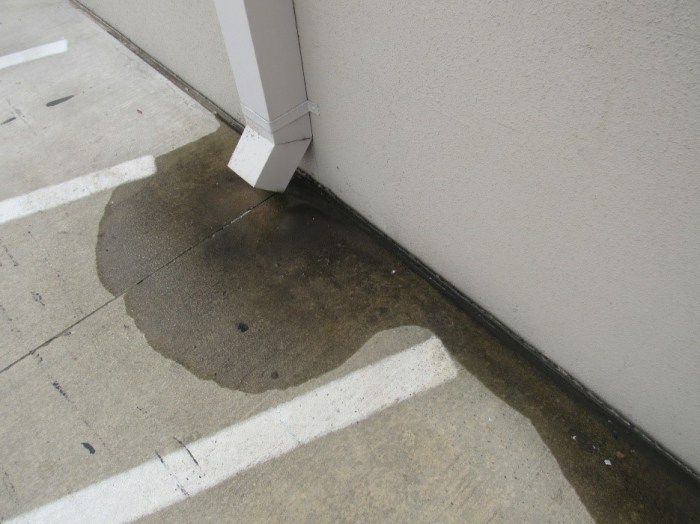
Identifying the precise cause of a void in concrete is crucial for effective repair and prevention of future issues. Thorough investigation, encompassing formwork analysis, concrete mix evaluation, and construction practice review, is essential. Understanding the factors influencing void formation helps pinpoint the root cause and implement corrective measures.
Potential Reasons for Void Formation
Various factors can contribute to void formation during concrete form removal. Issues in formwork design, inadequate concrete mix proportioning, and improper construction practices all play a role. Poor formwork design may lead to insufficient support, uneven pressure distribution, or inadequate form separation. Incorrect concrete mix proportioning, such as insufficient cement content or inadequate water-cement ratio, can result in a less durable concrete susceptible to voids.
Construction practices, including insufficient vibration, improper placement, or inadequate curing, also contribute to void formation.
Formwork Design Considerations
Formwork design significantly impacts void formation. Inadequate form support can cause pressure differentials and stress concentrations, leading to voids. Poor form separation techniques may trap air or other materials, creating voids during removal. Proper formwork design should ensure even pressure distribution, sufficient support, and effective form separation.
Concrete Mix Proportioning Analysis
The concrete mix proportioning plays a vital role in concrete quality. Insufficient cement content can lead to a weaker concrete matrix, prone to voids. Incorrect water-cement ratios can result in a concrete mix that is more susceptible to shrinkage and air entrapment, leading to void formation. Material tests, including slump tests and compressive strength tests, can help assess the mix quality and identify any deviations from the design specifications.
Construction Practice Evaluation
Construction practices significantly influence the final quality of the concrete. Insufficient vibration during placement can lead to uncompacted concrete, resulting in voids. Improper placement techniques may cause segregation, leading to voids. Inadequate curing conditions, such as insufficient moisture content or inadequate temperature control, can impact the concrete’s strength and density, potentially creating voids. Examining construction logs, site observations, and personnel interviews are essential for evaluating construction practices.
Impact of Factors on Void Characteristics
Curing conditions, weather patterns, and formwork quality all impact the appearance and size of the void. Rapid drying conditions can lead to shrinkage and cracking, creating or enlarging voids. Heavy rainfall or temperature fluctuations during curing can affect the concrete’s strength and density, contributing to void formation. Formwork quality, including its stability and alignment, significantly influences the homogeneity of the concrete placement and subsequent void formation.
Comparative Analysis of Void Causes
Possible Cause | Common Symptoms |
---|---|
Inadequate Form Support | Voids concentrated along form edges, uneven surface |
Insufficient Cement Content | Small, scattered voids throughout the concrete, lower compressive strength |
Incorrect Water-Cement Ratio | Larger voids, possible cracking, reduced concrete durability |
Insufficient Vibration | Voids concentrated in areas with poor compaction, uneven surface |
Improper Placement Techniques | Voids in specific areas, segregation visible |
Inadequate Curing | Small, scattered voids, reduced strength |
Repair Strategies for Voids
Identifying the appropriate repair strategy for concrete voids depends heavily on the void’s size, location, and the overall structural integrity of the affected area. A thorough assessment of the void’s characteristics and the underlying cause is crucial to implementing a sustainable and effective repair solution. Choosing the right repair method minimizes the risk of future problems and ensures the long-term stability of the concrete structure.Repair methods vary greatly depending on the scale of the void.
Small voids often require simple patching techniques, while extensive cavities necessitate more complex solutions involving reinforcement and structural support. Proper planning and execution are key to successful void repair, maximizing the longevity and structural integrity of the concrete structure.
Small Void Repair Methods
Small voids, typically less than 10cm in diameter, can often be addressed with patching techniques. These techniques are cost-effective and relatively quick to implement. Different materials and techniques can be employed depending on the specific characteristics of the void and the surrounding concrete.
- Epoxy patching: This method utilizes epoxy resin and aggregates to create a strong and durable patch. Epoxy resins are known for their high strength and adhesion to various surfaces, making them suitable for filling small voids in concrete structures. The cost can vary based on the size of the void and the required amount of epoxy.
- Cement-based patching: A common and cost-effective approach. A mix of cement, sand, and water is used to create a patch material that can effectively fill small voids. This method is suitable for voids in areas with minimal stress. The curing time for cement-based patches can be longer compared to epoxy patches, which might affect the overall project timeline.
- Polymer-modified concrete patching: This method combines the benefits of cement-based patching with the enhanced properties of polymers. This results in a patch that offers improved strength, durability, and water resistance. Polymer-modified patching is often used for small voids in areas exposed to harsh weather conditions. The cost is typically higher than conventional cement-based patching.
Extensive Cavity Repair Methods, How to fix a void when concrete form is removed
Extensive cavities, significantly larger than 10cm, often require more comprehensive repair strategies to ensure structural integrity. These repairs frequently involve reinforcing the surrounding concrete and filling the cavity.
- Shotcrete: A sprayed concrete method, suitable for filling large cavities. This method involves spraying a high-flow concrete mix into the void. Shotcrete offers a fast and cost-effective way to fill extensive cavities. The quality of the shotcrete fill depends on the expertise of the application crew and the equipment used.
- Grout injection: Suitable for filling large cavities, this method uses a specialized grout material to fill the void. The grout is often a high-strength material that can penetrate and fill intricate cavity shapes. Grout injection is a less disruptive option compared to other methods, but may require careful planning to ensure complete filling.
- Reinforced concrete filling: This approach involves creating a new concrete section within the existing structure. This technique strengthens the surrounding concrete and fills the void with a reinforced concrete structure. Reinforced concrete filling provides a very strong and durable solution but is more complex and time-consuming than other methods. It also has higher associated costs due to the labor and materials required.
Repair Procedure Example: Epoxy Patching
Objective: To repair a small void in a concrete slab using epoxy patching.
- Preparation: Thoroughly clean the void and surrounding concrete, removing loose debris and dust. Ensure the concrete surface is dry and free from contaminants that might inhibit adhesion.
- Void Sizing: Accurately measure the void’s dimensions. This will determine the required amount of epoxy and aggregates.
- Epoxy Mixing: Follow the manufacturer’s instructions to properly mix the epoxy resin and hardener. Carefully measure the components to ensure the correct ratio.
- Void Filling: Pour the mixed epoxy into the void, ensuring it fills the entire cavity. Use a trowel or other suitable tool to compact the epoxy and remove any air bubbles.
- Aggregate Incorporation (Optional): Add aggregates to the epoxy mix, if required, for added strength and durability.
- Curing: Allow the epoxy to cure according to the manufacturer’s specifications. Proper curing time is essential for achieving the desired strength and longevity of the patch.
- Finishing: Smooth and finish the patch to match the surrounding concrete surface.
Reinforcement and Strengthening
Restoring the structural integrity of concrete around voids requires careful reinforcement techniques. These techniques not only address the immediate problem of the void but also prevent future cracking or damage, ensuring the long-term stability of the structure. Effective reinforcement strategies consider the void’s characteristics, the cause of the void, and the desired level of structural restoration.Reinforcing the concrete surrounding the void is crucial for restoring its original strength and preventing further deterioration.
The choice of reinforcement method depends on several factors, including the size and location of the void, the type of concrete, and the anticipated load on the structure. Different materials and techniques offer varying degrees of effectiveness, impacting the repair’s cost, complexity, and long-term performance.
Reinforcement Materials
Various materials can be employed for reinforcing concrete around voids. Understanding the suitability of each material is essential for a successful repair.
- Steel reinforcement bars (rebar): Steel rebar is a common and effective reinforcement material. Its high tensile strength and ductility make it suitable for resisting tensile stresses and preventing cracking. Rebar can be placed around the void, extending into the surrounding concrete, to provide a strong anchoring point. Proper anchorage and spacing of rebar are vital to maximize its effectiveness.
Examples include reinforcing concrete beams or columns around a void.
- Fiber-reinforced polymer (FRP) composites: FRP composites offer a lightweight alternative to steel rebar. Their high tensile strength and resistance to corrosion make them suitable for applications where steel is impractical or undesirable. FRP composites can be molded into various shapes and sizes, accommodating different void geometries. Examples include using FRP to reinforce concrete slabs with voids in high-humidity environments, where steel corrosion is a concern.
- Epoxy resin and grout: Epoxy resins and specialized grouts are used to fill and reinforce the void itself. These materials offer high compressive strength and can effectively bond with the surrounding concrete, creating a monolithic structure. The choice between epoxy and grout depends on the void’s size and the desired strength of the repair.
Reinforcement Methods
Different methods exist for reinforcing the concrete around voids, each with its own advantages and disadvantages.
- Injection grouting: Injection grouting involves injecting a suitable material, such as epoxy resin or grout, into the void to fill it completely. This method is suitable for smaller voids and provides a strong bond with the surrounding concrete. The effectiveness of injection grouting depends on the void’s accessibility and the ability to achieve full penetration.
- Post-tensioning: Post-tensioning involves applying tension to steel tendons or bars embedded within the concrete. This method is often used for large voids or when significant load capacity is required. The tendons are stressed after the concrete has cured, creating a significant tensile force that strengthens the surrounding concrete. Post-tensioning is a complex method requiring specialized equipment and expertise.
- External reinforcement: External reinforcement involves attaching reinforcement elements to the surface of the concrete. This method is often used when the void is located in a highly visible or accessible area. External reinforcement can include the use of FRP composites or steel plates bonded to the surface. It is less effective in addressing internal void issues.
Comparison of Reinforcement Methods
The following table compares different reinforcement methods based on material cost, installation complexity, and long-term performance.
Reinforcement Method | Material Cost | Installation Complexity | Long-Term Performance |
---|---|---|---|
Injection Grouting | Medium | Medium | Good |
Post-tensioning | High | High | Excellent |
External Reinforcement | Medium | Low | Good |
Prevention Strategies: How To Fix A Void When Concrete Form Is Removed
Proactive measures are crucial in minimizing the risk of voids in concrete structures. By understanding common pitfalls in formwork design, concrete placement, and curing procedures, potential issues can be anticipated and addressed before they manifest as costly repairs. Careful attention to detail during each stage of the construction process can lead to a significantly higher quality final product, free from the inherent weaknesses that voids represent.Effective void prevention hinges on a meticulous approach, ensuring that every step in the process is executed correctly and with a keen awareness of the potential consequences of errors.
This proactive strategy will ultimately reduce the likelihood of encountering voids and save time and resources in the long run.
Common Formwork Design Errors Leading to Voids
Improper formwork design can create spaces that lead to void formation. Insufficient form support, inadequate bracing, and improper form ties are frequent culprits. A poorly designed form, particularly in areas of high stress, can deflect or distort, causing gaps that cannot be filled during concrete placement. Furthermore, formwork that is not properly sealed can result in air pockets being trapped within the concrete.
Unforeseen or overlooked issues in the formwork design will manifest as voids in the concrete.
Concrete Placement Errors Contributing to Void Formation
Inadequate concrete placement techniques can also result in voids. Insufficient vibration during concrete placement prevents the expulsion of entrapped air bubbles, which can accumulate and manifest as voids. Uneven concrete placement, where some areas receive less concrete than others, can lead to localized voids. Also, using improper equipment or techniques for concrete delivery and placement can cause significant variations in concrete density.
These issues will leave voids in the final concrete product.
Importance of Proper Concrete Curing for Void Prevention
Proper concrete curing is essential for strength development and void prevention. Insufficient curing allows moisture to evaporate too quickly from the concrete surface, hindering hydration and increasing the risk of shrinkage and cracking. This rapid moisture loss creates a drying effect, causing the concrete to lose strength and develop weaknesses, including voids. Proper curing techniques, such as covering the concrete with plastic sheeting or using water sprays, are vital to ensure sufficient moisture retention for adequate hydration and development of concrete strength.
Mix Proportioning and Void Mitigation
Accurate concrete mix proportioning is crucial for controlling void formation. Inconsistent or inaccurate ingredient ratios can lead to variations in concrete density and strength. Improper water-cement ratios directly impact the final product’s quality, affecting workability, strength, and shrinkage. Excessive water content results in a less dense and more porous concrete, increasing the risk of void formation. Carefully monitoring and controlling mix proportions through rigorous quality control measures is essential for minimizing the risk of voids.
A well-proportioned concrete mix, with the right amount of cement, aggregate, and water, will result in a strong, durable concrete product.
Case Studies and Examples
Real-world scenarios involving voids during concrete form removal highlight the importance of meticulous planning and execution. Analyzing these cases provides valuable insights into potential causes and effective repair strategies, ultimately preventing similar issues in future projects. Understanding the specific details of each case helps in developing a comprehensive approach to void management.
Real-World Void Formation Scenarios
Examining actual instances of void formation during concrete form removal offers a practical understanding of the factors contributing to these issues. This section presents specific examples, illustrating the causes and corresponding solutions implemented.
Case Study 1: Insufficient Form Support
This case study examines a scenario where insufficient support for the formwork resulted in a significant void in the concrete slab. The formwork, designed for a specific weight and pouring schedule, proved inadequate under the actual load and pouring rate. The inadequate support system caused the forms to shift and distort, creating a large void during removal. The repair involved careful removal of the affected concrete, followed by the placement of a reinforced concrete patch.
The image below displays the void before repair. The void is approximately 2 feet by 3 feet, and it extends nearly the full depth of the slab. Cracking is visible around the void edges. After the repair, a reinforced concrete patch, visually matching the surrounding slab, is installed, concealing the repair area.
Case Study 2: Improper Form De-shoring
This case study illustrates a project where the de-shoring process, the removal of temporary supports, was not executed correctly. The premature removal of the shoring led to concrete slab settlement and cracking, creating a void in the slab. This scenario highlights the critical need for a detailed de-shoring plan and adherence to the schedule. The repair strategy included the removal of damaged concrete, the placement of reinforcing steel, and the pouring of a new concrete patch, carefully integrating it with the existing slab.
The image below demonstrates the void in the concrete slab. The void is roughly 1 foot by 2 feet and situated near the center of the slab. The concrete around the void shows signs of significant cracking and spalling, which is a visible indication of the slab’s structural damage. The image after repair showcases a seamless transition between the patched area and the surrounding concrete.
Case Study 3: Incorrect Form Material Selection
This case study discusses a project where the concrete form material proved unsuitable for the specific project requirements. The form material’s inadequate strength led to significant deformation during the concrete pouring process. This deformation resulted in a void after the form removal. The solution involved removing the affected concrete, replacing it with a new section of concrete reinforced with a mesh, ensuring proper form material selection for future projects.
The image below shows the void, approximately 1.5 feet in diameter, located near the corner of the concrete wall. The formwork material used in the original construction is visible in the image. The image after repair demonstrates a seamless integration of the new concrete patch into the existing wall.
Summary of Case Studies
Case Study | Void Type | Cause | Repair Method | Outcomes |
---|---|---|---|---|
Case Study 1 | Slab Void | Insufficient Form Support | Concrete removal and reinforced patch | Successful repair, restored structural integrity. |
Case Study 2 | Slab Void | Improper Form De-shoring | Concrete removal, reinforcement, and patch | Successful repair, improved slab stability. |
Case Study 3 | Wall Void | Incorrect Form Material | Concrete removal, reinforcement, and patch | Successful repair, improved structural integrity. |
Closing Notes

In conclusion, fixing voids resulting from concrete form removal demands a meticulous approach. This guide has provided a detailed framework, encompassing identification, diagnosis, repair strategies, reinforcement, and prevention. By understanding the potential causes and employing appropriate repair techniques, you can ensure the structural integrity and longevity of your concrete structures. Remember, proper planning and execution are key to successful repair and prevention of future issues.
Common Queries
What are the most common causes of voids in concrete?
Voids can stem from improper formwork design, inadequate concrete mix proportions, issues with curing processes, or construction errors. Weather conditions, such as extreme temperatures, can also contribute. Poor formwork quality, insufficient compaction of the concrete mix, and material defects can also lead to voids.
How can I determine the extent of the void?
Visual inspection, using tools like measuring tapes and boroscopes, is crucial. Non-destructive testing methods, like ultrasonic testing, can help assess the depth and structural integrity of the surrounding concrete without causing further damage. Careful examination of construction documentation and site records can provide additional insights.
What are the different repair methods for voids?
Repair methods vary depending on the void’s size and location. Small voids might be filled with patching compounds, while larger cavities may require more extensive repairs like grouting, injection, or structural reinforcement.
What materials are needed for a typical concrete void repair?
Materials required will depend on the repair method. Common materials include patching compounds, grouts, reinforcing bars, and appropriate admixtures. Tools for mixing, applying, and shaping the materials are also necessary.