How to get silicone off epoxy? This comprehensive guide delves into the intricate world of silicone and epoxy removal, providing a detailed roadmap for tackling this common challenge. From understanding the nuances of different epoxy types to mastering various removal techniques, this guide equips you with the knowledge to confidently navigate this process. We’ll explore the necessary precautions, the diverse methods, and troubleshooting tips to ensure a successful outcome, leaving your epoxy surfaces pristine and ready for their next adventure.
Epoxy and silicone combinations can present unique removal challenges. Different types of epoxy react differently to various removal methods, and proper preparation is key. The guide will detail how to identify your epoxy type and choose the right approach, whether it’s mechanical or chemical methods. Furthermore, this guide will equip you with the knowledge to tackle various scenarios, from accidental spills to planned restorations, and to understand the importance of safety measures.
Introduction to Silicone and Epoxy Removal: How To Get Silicone Off Epoxy
Removing silicone from epoxy surfaces presents a significant challenge due to the inherent properties of both materials. Silicone’s flexibility and often non-reactive nature, coupled with epoxy’s strength and curing process, create a complex adhesive system that is difficult to break down without damaging either component. Careful preparation and selection of appropriate solvents or mechanical methods are crucial for successful removal, minimizing potential damage to the underlying epoxy structure.
Safety precautions are paramount due to the potential hazards associated with various solvents and chemical reactions.Understanding the specific types of silicone and epoxy encountered is vital for effective removal strategies. Different formulations of both materials react differently to various solvents and mechanical forces. This knowledge helps tailor the approach for optimal results. Silicone removal from epoxy is necessary in a wide array of situations, from accidental spills to planned repairs and restorations.
Understanding the context of the removal will significantly impact the chosen methodology and materials.
Types of Silicone and Epoxy Combinations
Silicone and epoxy combinations are used in numerous applications, leading to a variety of possible formulations. Understanding these combinations is crucial for determining the most effective removal methods. Some common examples include:
- Silicone sealants on epoxy countertops: These sealants are often used to create a water-resistant barrier on epoxy countertops, and removal might be necessary due to damage or aesthetic concerns.
- Silicone adhesives bonded to epoxy parts: In industrial settings, silicone adhesives are often used to bond epoxy components. Removal might be required for repair or modification purposes.
- Silicone coatings on epoxy castings: Silicone coatings can be applied to epoxy castings to improve their properties. Removal might be necessary for restoration or to reveal the underlying epoxy.
Situations Requiring Silicone Removal from Epoxy
Silicone removal from epoxy is needed in various scenarios. Identifying the specific situation helps determine the best approach. These situations include:
- Accidental spills: Silicone spills on epoxy surfaces require prompt attention to prevent the silicone from bonding permanently.
- Repair work: Damaged or deteriorated epoxy structures might require the removal of existing silicone before applying new epoxy or other materials.
- Restoration projects: Restoring antique or historical items involving silicone-coated epoxy may necessitate the removal of the silicone to reveal the original epoxy structure.
- Modification and upgrade: Replacing or modifying components often necessitates the removal of silicone from epoxy substrates for new material applications.
Epoxy Types and Silicone Resistance
Different epoxy formulations exhibit varying degrees of resistance to silicone. This table provides a comparison of common epoxy types and their relative resistance to silicone:
Epoxy Type | Strength | Resistance to Silicone | Weaknesses |
---|---|---|---|
Polyester Epoxy | High | Moderate | Susceptible to cracking and stress |
Epoxy Resin | High | Good | Can be brittle if cured improperly |
Polyurethane Epoxy | Very High | Excellent | More expensive than other types |
Note: The table above is a general comparison and the specific resistance of a given epoxy type can vary based on the curing conditions, filler materials, and other factors.
Mechanical Removal Methods
Removing silicone from epoxy often requires a delicate touch, as harsh methods can damage the epoxy substrate. Mechanical removal methods, ranging from simple scraping to specialized tools, offer a variety of approaches to address this challenge. Understanding the nuances of each method is crucial for achieving effective and safe removal without compromising the integrity of the epoxy surface.
Scraping
Scraping is a fundamental mechanical method, especially useful for removing large, loose pieces of silicone. Its effectiveness hinges on the consistency and adhesion of the silicone to the epoxy. For this method, a sharp, rigid scraper is essential to avoid scratching or damaging the epoxy. Using a scraper that’s too soft can result in the silicone pulling the epoxy along with it.
- Tools: A variety of scrapers are available, from metal scrapers with different blade shapes to plastic scrapers designed for gentler removal. The choice depends on the hardness of the silicone and the sensitivity of the epoxy surface. A utility knife or a razor blade can be used, but extreme care is necessary to avoid gouging the epoxy.
Plastic scrapers are recommended for delicate epoxy surfaces.
- Procedure: Begin by applying gentle pressure and a controlled scraping motion. Work in small, overlapping sections to ensure thorough removal. For stubborn silicone, consider using a solvent-based cleaner to soften the material before scraping. Always start with minimal pressure and gradually increase it only if needed.
- Force Level: Low to medium pressure is recommended. Excessive force can damage the epoxy surface, leading to undesirable imperfections.
- Surface Suitability: Scraping is ideal for surfaces where the silicone is easily detached and doesn’t have intricate patterns. It’s suitable for smooth, flat surfaces with minimal detail.
Sanding
Sanding is a viable option for removing silicone when scraping isn’t sufficient. Its effectiveness depends on the type of sandpaper and the desired level of precision. The grit size and type of abrasive should be selected carefully to minimize epoxy damage. A higher grit sandpaper will provide a smoother finish but can require more time and effort.
- Tools: Sandpaper of various grits (e.g., 80-220 grit) is needed. A sanding block or a sanding sponge provides better control and prevents the creation of uneven surfaces. An orbital sander or a rotary sander is also an option for large surfaces, but requires more experience and care.
- Procedure: Begin with a lower grit sandpaper to remove the bulk of the silicone. Gradually move to higher grit sandpaper to achieve a smoother finish. Always apply even pressure to prevent creating scratches or grooves. Using a sanding block or sponge will reduce the risk of accidentally applying too much pressure.
- Force Level: Medium pressure is generally suitable. Heavy pressure can cause deep scratches or gouges in the epoxy surface. Avoid excessive back-and-forth motion, instead focus on a smooth, continuous sanding motion.
- Surface Suitability: Sanding is effective on surfaces with more complex geometries or textures. It’s suitable for larger areas and is better suited to removing stubborn silicone that is deeply embedded.
Specialized Tools
Specialized tools, such as silicone removal tools, can provide greater precision and control. These tools often have a combination of scraping and wedging elements for more effective and targeted removal. They are particularly useful for removing silicone in tight corners or intricate patterns.
- Tools: These tools typically consist of a blade or a wedge-shaped tool with a handle. They may also include a suction cup or other attachments. Some tools are designed for specific shapes or geometries.
- Procedure: Follow the manufacturer’s instructions for using the specialized tool. Apply controlled pressure, avoiding excessive force that could damage the epoxy. Focus on applying pressure directly to the silicone, not the epoxy. Small, targeted movements are often more effective than large, sweeping motions.
- Force Level: Moderate pressure is typically required. Carefully inspect the tool’s design to determine the appropriate pressure to apply. Refer to the tool’s manual for specific guidelines.
- Surface Suitability: These tools are useful for detailed work on intricate surfaces, including corners, edges, and curves. They are ideal for removing silicone from complex epoxy structures or delicate surfaces.
Comparison Table
Method | Tools | Effectiveness | Speed | Potential Damage | Suitable Surfaces |
---|---|---|---|---|---|
Scraping | Metal/Plastic Scrapers, Utility Knife | High for loose silicone | Medium | Low if controlled | Flat, smooth surfaces |
Sanding | Sandpaper, Sanding Block | High for embedded silicone | Low to Medium | Medium if grit is appropriate | Complex, textured surfaces |
Specialized Tools | Silicone Removal Tools | High for precision | Medium | Low if used correctly | Intricate, detailed surfaces |
Chemical Removal Methods
Removing silicone from epoxy often requires more than just brute force. Chemical methods offer a targeted approach, but choosing the right agent is crucial. These methods can be effective, but careful consideration of the epoxy type and potential risks is paramount. Improper use can lead to damage or degradation of the epoxy substrate, further complications, or even safety hazards.Chemical agents offer a targeted approach to silicone removal, but selecting the correct chemical is vital.
The effectiveness of these methods depends heavily on the specific chemical composition and its compatibility with the epoxy type. The chosen chemical’s reactivity, safety profile, and environmental impact must be evaluated to ensure responsible and effective removal.
Chemical Agents for Silicone Removal
Various chemical solvents can be used to dissolve or break down silicone, allowing for its separation from the epoxy. These solvents often work by exploiting the different chemical structures of silicone and epoxy. Common agents include certain types of solvents and specialized silicone removers. Understanding their specific compositions and effects is crucial for safe and successful application.
Chemical Compositions and Effects
Many silicone removers are based on strong organic solvents like ketones, esters, or alcohols. These solvents can effectively dissolve the silicone polymer, breaking the bonds holding it to the epoxy. However, the choice of solvent significantly impacts the epoxy itself. Some solvents might be aggressive enough to degrade or soften the epoxy resin, leading to unintended damage.
For instance, certain highly reactive solvents might cause pitting or discoloration in the epoxy surface. Careful selection and application are critical to prevent such outcomes.
Comparison of Chemical Solutions
Different chemical solutions exhibit varying degrees of reactivity, safety, and environmental impact. For instance, some solvents may be highly flammable, posing fire risks, while others might produce harmful fumes during application. The environmental impact should also be considered. Some solvents have a high toxicity level and can contaminate the surrounding environment. Comparing these factors helps determine the most appropriate chemical for a specific application.
Safety Precautions
When working with chemical agents for silicone removal, stringent safety precautions are crucial. Always wear appropriate personal protective equipment (PPE), such as gloves, eye protection, and a respirator. Ensure the work area is well-ventilated to minimize exposure to harmful fumes. Follow all manufacturer’s instructions and safety data sheets (SDS) meticulously. Working in a controlled environment, with proper ventilation, and by adhering to safety procedures minimizes the risk of accidents and protects the user’s health.
Table: Chemical Solvents and Epoxy Compatibility
Solvent | Chemical Composition | Epoxy Compatibility | Safety Guidelines |
---|---|---|---|
Acetone | (CH3)2CO | Generally compatible with some epoxy types, but can soften some. | Highly flammable, use in well-ventilated areas, wear appropriate PPE. |
MEK (Methyl Ethyl Ketone) | CH3COCH2CH3 | Moderately compatible with some epoxy types. Can cause damage to certain types. | Flammable, use with caution, proper ventilation is essential. |
Isopropyl Alcohol | CH3CHOHCH3 | Generally compatible with most epoxy types, but may not effectively remove silicone. | Relatively safe, but can cause skin irritation, use with appropriate PPE. |
Specialized Silicone Removers | Mixture of solvents and surfactants | Generally more effective at removing silicone from epoxy without harming the epoxy itself. | Refer to manufacturer’s instructions for safe handling and disposal. |
Note: This table is for illustrative purposes only. Always consult the Material Safety Data Sheet (SDS) for specific information regarding a particular chemical and its compatibility with the epoxy. The specific compatibility depends on the epoxy type and the exact chemical formulation of the solvent.
Preparation and Surface Treatment
Proper surface preparation is crucial for successful silicone and epoxy removal. Ignoring this step can lead to incomplete removal, damage to the underlying substrate, or ineffective application of removal methods. Careful masking, thorough cleaning, and protective measures ensure the integrity of the surrounding area and the efficiency of the removal process. A well-defined strategy for surface preparation will significantly impact the outcome.Effective preparation involves a systematic approach to ensure the integrity of the treated area and surrounding materials.
This meticulous process minimizes the risk of damage to the substrate and surrounding surfaces. By implementing the following steps, the chance of a successful removal is maximized.
Masking Procedures
Prioritizing the protection of unaffected areas is paramount. Proper masking prevents damage from chemicals or mechanical abrasion. Use high-quality masking tape or specialized masking films that are compatible with the materials being handled. Ensure a secure seal to avoid leakage or chemical penetration.
Surface Cleaning
Thorough cleaning is essential to remove any contaminants, loose debris, or previous residues that could hinder the effectiveness of the removal process. This step removes contaminants that might interfere with the adhesion or reaction of the cleaning agents. Contaminants can include dust, dirt, grease, or other foreign substances.
Protective Measures
Protecting surrounding areas from chemical exposure or mechanical damage is critical. This involves using appropriate barriers, such as plastic sheeting, to contain any potential contaminants. The use of safety glasses and respirators is vital to safeguard the health of the person performing the removal process. Appropriate ventilation is essential to minimize the risk of inhalation of harmful fumes.
Step-by-Step Surface Preparation Procedure
Step | Action | Cleaning Method | Protection Measures |
---|---|---|---|
1 | Inspect the area for any loose or damaged materials. | Visual inspection | Use safety glasses and gloves. |
2 | Mask off the areas to be protected using high-quality masking tape. | N/A | Ensure complete coverage and secure adhesion of the masking tape. |
3 | Remove any loose debris, dust, or contaminants from the epoxy surface. | Brush, vacuum, or compressed air. | Use a dust mask if necessary. |
4 | Clean the epoxy surface with a suitable solvent or cleaner (e.g., mineral spirits, acetone). | Solvent or cleaner application. | Work in a well-ventilated area and wear appropriate protective equipment (e.g., gloves, safety glasses, and respirator). |
5 | Thoroughly rinse the epoxy surface with clean water to remove any residue. | Water rinse | Continue to work in a well-ventilated area and use appropriate protective equipment. |
6 | Allow the epoxy surface to dry completely. | Air drying | Ensure adequate drying time before proceeding to the next step. |
Safety Considerations
Removing silicone from epoxy can be a hazardous undertaking, especially when dealing with chemical solvents. Careless handling can lead to severe health issues, fire hazards, and environmental damage. Adhering to strict safety precautions is paramount to ensure a safe and successful removal process.Proper safety measures are not just a good practice; they are essential for preventing accidents and protecting both the worker and the surrounding environment.
This section Artikels crucial safety considerations, including the potential hazards of various removal methods, the importance of ventilation and personal protective equipment (PPE), and the proper disposal of chemical waste.
Potential Hazards of Removal Methods
Various methods for removing silicone from epoxy present different hazards. Chemical solvents, for instance, can cause respiratory irritation, skin burns, and eye damage if not handled with extreme caution. Some solvents are flammable and can pose a significant fire risk, especially in poorly ventilated areas. Mechanical abrasion, while generally less hazardous than chemical methods, can still cause skin irritation or injury if not performed carefully.
The risk of releasing harmful dust or particles also exists in some mechanical processes.
Importance of Ventilation
Adequate ventilation is critical during any epoxy and silicone removal process, especially when using chemical solvents. Poor ventilation can lead to the accumulation of harmful vapors, increasing the risk of inhalation and potential health problems. A well-ventilated area should be equipped with exhaust fans or other ventilation systems to remove solvents and fumes promptly. This will significantly reduce exposure to hazardous substances.
Personal Protective Equipment (PPE)
Proper personal protective equipment (PPE) is essential to minimize exposure to harmful substances. This includes respirators to protect the lungs from chemical vapors, gloves to prevent skin contact with solvents, safety glasses or goggles to shield the eyes, and protective clothing to prevent contact with potentially corrosive materials. The specific PPE required will depend on the removal method and the chemicals involved.
Chemical Waste Disposal
Proper disposal of chemical waste is crucial for environmental protection. Improper disposal can contaminate soil and water sources, harming ecosystems and human health. Chemical waste generated during silicone and epoxy removal should be disposed of according to local regulations and guidelines. Consult with local environmental authorities or hazardous waste disposal services to determine the appropriate procedures.
Safety Guidelines for Handling Materials
Material | Safety Precautions | PPE Recommendations |
---|---|---|
Chemical Solvents (e.g., acetone, methylene chloride) | Store in a cool, well-ventilated area away from ignition sources. Avoid direct contact with skin and eyes. Use with proper ventilation and exhaust systems. | Respirator, gloves (nitrile or neoprene), safety glasses/goggles, protective clothing. |
Abrasive Materials (e.g., sandpaper, steel wool) | Wear appropriate eye protection and dust mask. Ensure proper work area ventilation. | Safety glasses/goggles, dust mask, gloves (depending on the material), protective clothing. |
Mechanical Equipment (e.g., grinders, sanders) | Use appropriate guards and safety mechanisms on the equipment. Wear appropriate eye protection and ear protection. | Safety glasses/goggles, ear protection, gloves (depending on the work). |
Troubleshooting and Problem Solving
Removing silicone from epoxy can be a delicate process, fraught with potential pitfalls. Understanding potential issues and how to address them effectively is crucial to prevent further damage and ensure a successful outcome. Improper techniques can lead to epoxy degradation, incomplete silicone removal, or other unwanted consequences. A methodical approach to troubleshooting is essential for achieving optimal results.
Potential Problems During Silicone Removal
Silicone removal from epoxy presents a range of potential challenges. Incorrect chemical selection, inadequate preparation, or mechanical abrasion can all contribute to complications. Understanding these potential issues is vital for preventing costly errors and achieving successful removal.
Epoxy Damage Mitigation
Epoxy resin is susceptible to damage during the removal process. Aggressive chemical agents or excessive mechanical force can lead to cracking, pitting, or even complete delamination of the epoxy layer. Identifying and mitigating these risks is paramount. Properly assessing the epoxy’s condition before initiating removal and selecting appropriate tools and techniques are crucial for minimizing damage. For instance, using a solvent that is too strong can cause the epoxy to soften or dissolve, leading to uneven removal and potentially creating voids or imperfections.
Incomplete Silicone Removal
Incomplete silicone removal can be a frustrating problem. This is often due to inadequate chemical contact, insufficient dwell time, or improper application of the removal agent. It’s important to ensure complete saturation of the silicone with the chosen solvent. Using a high-quality, specialized silicone remover tailored to the specific epoxy and silicone type is often essential for achieving a complete removal.
Incorrect application of the removal agent, such as applying it in a thin layer or insufficiently penetrating the silicone, may also result in incomplete removal.
Assessing Damage Extent and Seeking Professional Help
Determining the extent of damage is critical. Visual inspection, along with evaluating the material’s mechanical properties (flexibility, strength, etc.), can help gauge the severity of the issue. If significant damage is suspected or if the removal process is proving difficult, consulting a professional restoration specialist or material scientist is advisable. This approach is especially important for intricate or high-value applications.
For example, a delicate antique piece with epoxy coatings might require specialized expertise to avoid further damage.
Step-by-Step Troubleshooting Approach, How to get silicone off epoxy
A systematic approach is key to troubleshooting issues effectively. Start by meticulously inspecting the affected area for any visible damage. Identify the specific type of silicone and epoxy being used. Select the appropriate removal method and chemical agents based on these factors. Carefully follow the manufacturer’s instructions for each step, from preparation to removal and post-treatment.
Document the steps taken for future reference and potential further analysis. Regularly monitor the removal process and adjust techniques as needed to avoid damage to the epoxy.
Table of Troubleshooting Scenarios
Problem | Description | Potential Cause | Solution | Illustration |
---|---|---|---|---|
Epoxy Damage | Cracking, pitting, or delamination of epoxy. | Excessive chemical strength, improper mechanical methods. | Reduce chemical concentration, use gentler mechanical techniques. Consider using a specialized solvent for the epoxy type. | (Image: Epoxy with visible cracks and pitting.) |
Incomplete Silicone Removal | Residual silicone remains on the epoxy surface. | Inadequate chemical contact, insufficient dwell time. | Ensure thorough saturation of silicone with solvent, increase dwell time, or repeat the removal process with a fresh application. | (Image: Epoxy with some silicone residue remaining.) |
Unexpected Reactions | Unforeseen reactions between epoxy and silicone or removal agent. | Incompatible solvents or improper application. | Use appropriate solvents and application methods. Test on a small, inconspicuous area first. | (Image: Epoxy with bubbling or discoloration.) |
Case Studies and Examples
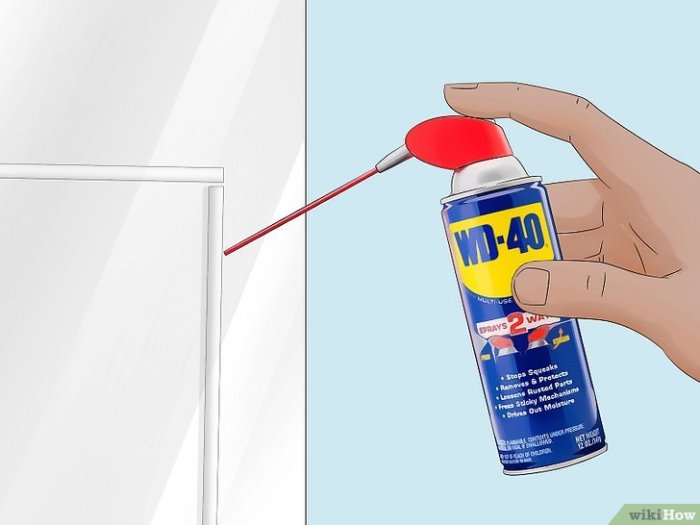
Removing silicone from epoxy presents unique challenges depending on the specific materials and application. Real-world examples highlight the importance of careful material identification, selection of appropriate removal methods, and meticulous preparation for successful outcomes. These cases demonstrate how understanding the nuances of different epoxy and silicone types can significantly impact the success rate of the removal process.Successful silicone removal from epoxy often requires a multi-faceted approach, combining mechanical and chemical methods.
Careful consideration of the epoxy’s composition, the silicone’s properties, and the desired outcome (complete removal versus minimal alteration) is crucial for effective and safe removal. This section will delve into various scenarios, showcasing the diverse approaches and considerations necessary for successful removal.
Successful Silicone Removal from Electronic Components
Identifying the epoxy type and the specific silicone used is crucial for choosing the appropriate removal method. For example, in the repair of electronic components, a two-part epoxy resin system (often used in circuit boards) might require different treatment than a structural epoxy. Silicone, used as a sealant or insulation, might also vary in its hardness and adhesion properties.
Careful consideration of these factors is essential for selecting the correct solvents or mechanical abrasion techniques. The use of specialized tools and techniques can prevent damage to delicate components during the removal process.
Silicone Removal from Automotive Parts
Automotive applications often involve complex epoxy systems, such as those used for bonding or coating. The specific epoxy system, its curing characteristics, and the nature of the silicone residue will influence the chosen removal strategy. For instance, if the silicone is a sealant used for a weatherproof application, the removal method may differ from silicone used in a specific component assembly.
Mechanical methods, such as abrasive blasting or specialized scrapers, might be employed in conjunction with chemical solvents for optimal results. Careful attention to the underlying materials and potential for damage to the substrate is paramount.
Silicone Removal from Concrete Structures
In concrete applications, the epoxy system might be used for reinforcement or repair. The presence of concrete and other construction materials requires careful selection of removal methods. Chemical methods should be chosen cautiously to avoid damaging the concrete substrate. Mechanical removal methods, such as specialized grinders or chisels, might be necessary for larger areas. The specific characteristics of the concrete, the type of epoxy, and the silicone’s properties will significantly influence the removal process.
A thorough understanding of the epoxy-silicone system and its interaction with the concrete is essential.
Summary Table of Case Studies
Case Study | Epoxy Type | Silicone Type | Removal Method | Outcome |
---|---|---|---|---|
Electronic Component Repair | Two-part epoxy resin | Flexible, adhesive silicone | Solvent-based chemical removal, followed by mechanical scrubbing | Complete silicone removal without component damage |
Automotive Part Repair | High-strength epoxy | High-temperature, resistant silicone | Abrasive blasting, solvent application, and specialized scraping | Silicone removal with minimal damage to the underlying part |
Concrete Structure Repair | Epoxy mortar | Polydimethyl siloxane sealant | Mechanical removal (grinding) with controlled chemical application | Silicone removal without harming the concrete structure |
Closing Summary
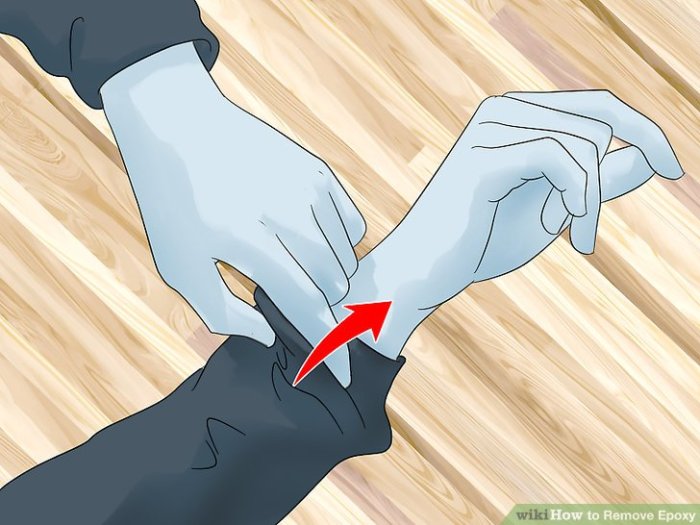
In conclusion, successfully removing silicone from epoxy involves careful consideration of various factors. Understanding the epoxy type, selecting the appropriate removal method, and prioritizing safety are crucial steps. By following the comprehensive guide provided, you can confidently approach this task, ensuring a successful outcome and a pristine epoxy surface. Remember, preparation and safety are paramount throughout the process.
FAQ Summary
What are the most common types of epoxy and silicone encountered in this context?
Common epoxy types include polyester, vinyl ester, and phenolic epoxy resins. Silicone types include various elastomers, often found in sealants and adhesives.
Can I use any solvent to remove silicone from epoxy?
No, not all solvents are compatible with all epoxy types. Using the wrong solvent can damage the epoxy surface. Always consult the product specifications and safety data sheets before using any chemical solvent.
What are some common problems encountered during silicone removal, and how can they be solved?
Common problems include incomplete removal, damage to the epoxy surface, and chemical reactions. Careful selection of the removal method and proper safety precautions can mitigate these issues.
How do I dispose of chemical waste generated during the removal process?
Dispose of chemical waste according to local regulations. Consult your local waste disposal authorities for proper procedures.