How to install vapor barrier under slab Florida? This guide breaks down everything you need to know about keeping your Florida slab dry and happy. From choosing the right materials to navigating Florida’s unique climate, we’ve got you covered. This ain’t your grandma’s DIY project; we’re talkin’ serious waterproofing for maximum peace of mind.
Installing a vapor barrier under a concrete slab in Florida is crucial for preventing moisture issues. Florida’s humid climate and potential for flooding mean you need a barrier that can handle the elements. This guide will walk you through the process, from selecting the right barrier to ensuring proper installation for long-term protection.
Introduction to Vapor Barriers under Slabs in Florida
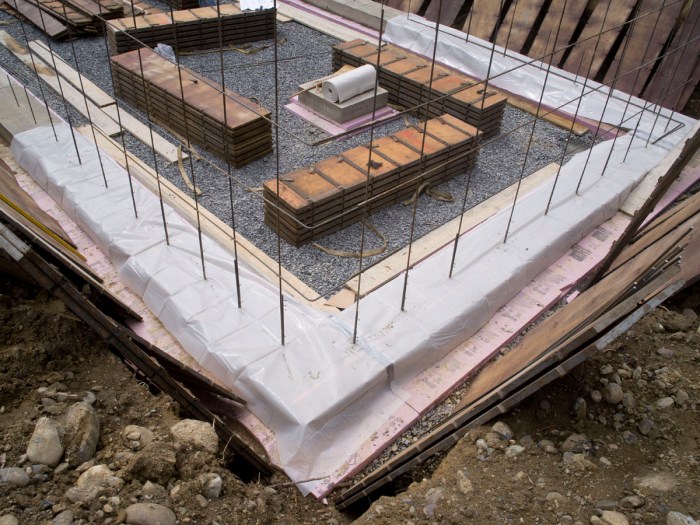
Vapor barriers are crucial components in concrete slab construction, acting as a critical line of defense against moisture intrusion. They prevent moisture vapor from rising from the ground up through the slab, which can lead to significant issues like mold, mildew, and structural damage. This is particularly important in Florida’s climate, where high humidity and frequent rainfall can create a moist environment conducive to moisture problems.
Proper installation of a vapor barrier is paramount in ensuring the longevity and structural integrity of concrete slabs.Florida’s climate presents unique challenges when installing vapor barriers. The high humidity and potential for ground moisture, combined with the region’s frequent rainfall, necessitate a robust and effective vapor barrier system. This proactive approach prevents moisture from penetrating the slab and causing long-term damage to the structure and the building’s interior.
Choosing the correct vapor barrier material and installation method is vital for preventing these issues.
Understanding the Function of Vapor Barriers
Vapor barriers are essentially a material with low vapor permeability, often a polyethylene sheet. They act as a barrier, preventing moisture vapor from moving through the concrete slab. By interrupting this vapor transmission, the vapor barrier reduces the potential for condensation, which can damage the structure and create a breeding ground for mold and mildew. Properly installed, the barrier significantly minimizes the risk of moisture-related problems.
Challenges in Florida’s Climate, How to install vapor barrier under slab florida
Florida’s humid climate presents specific challenges for vapor barrier installation. The high humidity levels can increase the potential for moisture to permeate the slab if the vapor barrier is not properly installed or the correct materials are not used. The region’s frequent rainfall and potential for groundwater fluctuations further underscore the importance of a robust vapor barrier system.
Furthermore, the ground’s moisture content can vary greatly, influencing the vapor pressure differential and requiring careful consideration during installation.
Importance of Proper Installation
Proper vapor barrier installation is critical for preventing moisture-related issues in concrete slabs. Improper installation can lead to moisture penetration, resulting in significant problems like:
- Mold and mildew growth: Moisture accumulation provides ideal conditions for mold and mildew growth, leading to health concerns and aesthetic damage.
- Structural damage: Moisture can weaken the concrete, potentially causing cracks and structural problems over time.
- Reduced lifespan of the slab: Moisture penetration shortens the lifespan of the slab, requiring costly repairs or replacements in the future.
- Interior discomfort: Moisture issues can manifest as condensation on interior surfaces, impacting comfort and potentially causing discomfort.
Ensuring a properly sealed and installed vapor barrier is a preventative measure that can save significant costs and repairs in the future.
Comparing Vapor Barrier Types
Different types of vapor barriers are available, each with its own characteristics and applications. The choice of material depends on factors such as cost, performance, and installation ease.
Vapor Barrier Type | Description | Pros | Cons |
---|---|---|---|
Polyethylene Sheeting | Common, affordable, and readily available. | Cost-effective, readily available, and relatively easy to install. | Can be susceptible to punctures and tears, and may not provide the same level of long-term performance as other options. |
Modified Bitumen Membranes | A more robust option with enhanced durability and resistance to punctures. | High durability, resistance to punctures and tears, and good vapor resistance. | Higher cost compared to polyethylene, and may require specialized installation techniques. |
Built-Up Roofing Membranes | Highly durable, offering superior resistance to moisture penetration. | Excellent long-term performance and resistance to moisture. | Most expensive option, and installation can be complex. |
Selecting the appropriate type of vapor barrier is crucial for effectively managing moisture in Florida’s climate. The table highlights key considerations in choosing the right barrier for a particular project.
Types of Vapor Barriers Suitable for Florida
Florida’s humid subtropical climate presents unique challenges for slab-on-grade construction. Proper vapor barrier selection is crucial to prevent moisture issues, maintain structural integrity, and ensure the longevity of the building. Understanding the various types of vapor barriers available, along with their strengths and weaknesses, is vital for informed decision-making.
Materials Suitable for Florida’s Climate
A range of materials can effectively serve as vapor barriers in Florida’s climate. Choosing the right material depends on factors like budget, desired performance characteristics, and installation complexity. These considerations are paramount for successful implementation.
Polyethylene Sheeting
Polyethylene sheeting is a common and cost-effective vapor barrier option. Its low cost makes it attractive for many projects, especially those with tight budgets. However, it has limitations regarding its resistance to puncture and its durability in harsh environments. Proper installation is critical to avoid punctures and maintain its effectiveness.
Polypropylene Sheeting
Polypropylene sheeting offers enhanced puncture resistance compared to polyethylene. This improved durability translates to a longer lifespan and reduced maintenance requirements. However, its higher cost may be a deterrent for some projects. The increased cost is offset by its superior long-term performance.
Built-up Roofing Membranes
Built-up roofing membranes provide a robust and durable vapor barrier. Their multi-layered construction offers excellent moisture resistance and longevity, suitable for projects requiring a long-term solution. However, the installation process is more complex and labor-intensive, which contributes to higher installation costs. The extra labor and materials can result in higher initial costs, but this often translates to long-term savings.
Modified Bitumen Membranes
Modified bitumen membranes offer a balance between cost and performance. They are relatively affordable and can be installed in a variety of situations. Their durability and resistance to Florida’s climate are sufficient for many projects, but may not be ideal for extreme conditions or high-moisture areas. While they are a practical choice for many projects, their performance might not be ideal for all situations.
Table: Key Properties of Vapor Barrier Materials
Material | Moisture Resistance | Durability | Cost | Installation Complexity |
---|---|---|---|---|
Polyethylene Sheeting | Good | Moderate | Low | Moderate |
Polypropylene Sheeting | Good | High | Moderate | Moderate |
Built-up Roofing Membranes | Excellent | Excellent | High | High |
Modified Bitumen Membranes | Good | Good | Moderate | Moderate |
Long-Term Performance and Maintenance
The long-term performance of a vapor barrier is significantly influenced by its material properties and installation quality. Proper installation is critical for preventing leaks and maintaining the integrity of the barrier. Regular inspections can help identify potential problems early, preventing costly repairs later. Proactive maintenance and monitoring can help avoid costly repairs down the line. A well-maintained vapor barrier ensures the structural integrity and longevity of the building.
Installation Procedures and Methods
Proper installation of a vapor barrier under a concrete slab in Florida is crucial for preventing moisture damage and extending the lifespan of the structure. Florida’s humid climate, combined with the potential for ground water fluctuations, necessitates careful attention to detail during the installation process. Substandard installations can lead to costly repairs and structural issues in the future.
Step-by-Step Installation Process
The installation process for a vapor barrier under a concrete slab involves several critical steps, each requiring precision and adherence to best practices. These steps, when followed meticulously, will contribute to a durable and moisture-resistant slab foundation.
- Preparation of the Subgrade: The subgrade must be level, compacted, and free of debris, large stones, or organic matter. Adequate drainage is essential to prevent water accumulation. This foundational step ensures a stable and uniform base for the vapor barrier and subsequent concrete slab.
- Vapor Barrier Placement: The vapor barrier material is carefully laid directly on the prepared subgrade, ensuring it is free of wrinkles, creases, and overlaps. The material should extend beyond the perimeter of the slab by at least 6 inches. This prevents water from seeping beneath the edges of the barrier.
- Seam Sealing: All seams and overlaps in the vapor barrier must be sealed using an appropriate sealant. This is critical to create a continuous barrier, preventing moisture penetration. The sealant should be compatible with the vapor barrier material and be able to withstand the Florida climate’s temperature fluctuations.
- Perimeter Protection: The vapor barrier should be adequately protected from damage during the pouring of the concrete slab. This often involves the use of metal edging or similar protective barriers around the perimeter of the vapor barrier.
- Concrete Slab Pouring: The concrete slab is poured over the vapor barrier, ensuring even distribution and proper compaction. The concrete should be appropriately mixed and cured according to the manufacturer’s recommendations to maintain strength and moisture resistance.
- Curing and Protection: The concrete slab requires proper curing to achieve its full strength. Protecting the slab from excessive drying or water damage is crucial. Florida’s hot and humid conditions require specific curing procedures.
Critical Considerations for Florida Conditions
Florida’s unique climate presents specific challenges for vapor barrier installation. Understanding these considerations is crucial for ensuring a successful and durable installation.
- Moisture Levels: Florida’s high humidity and potential for ground water fluctuations necessitate a robust vapor barrier. The barrier must effectively prevent moisture from penetrating the slab, protecting the building from moisture damage.
- Drainage: Proper drainage is essential to prevent water from accumulating beneath the slab. Careful consideration should be given to the surrounding landscape to ensure water flows away from the slab area. This prevents water from seeping into the slab through capillary action or hydrostatic pressure.
- Temperature Fluctuations: Florida’s wide temperature variations can affect the performance of the vapor barrier and the concrete. Materials must be chosen that can withstand these fluctuations without compromising their effectiveness.
- Pest Control: Pest control measures must be considered to prevent damage to the vapor barrier from rodents or other pests. This is particularly important when using certain types of vapor barriers.
Comparison of Installation Methods
Different methods are available for installing vapor barriers under concrete slabs. Choosing the appropriate method depends on several factors, including the type of vapor barrier material and the specific project requirements.
Installation Method | Description | Advantages | Disadvantages |
---|---|---|---|
Roll-on | The vapor barrier is rolled out onto the subgrade. | Relatively quick and easy. | Requires careful handling to avoid wrinkles and creases. Not suitable for uneven surfaces. |
Adhesive | The vapor barrier is adhered to the subgrade using an appropriate adhesive. | Provides a strong, continuous barrier. | More labor-intensive than roll-on. Requires careful application of adhesive. |
Sheet/Panel | Pre-cut sheets or panels are installed and joined. | Easy to handle and install, especially for large areas. | Requires precise cutting and sealing of joints. |
Considerations for Florida’s Climate: How To Install Vapor Barrier Under Slab Florida
Florida’s unique climate, characterized by high humidity and temperature fluctuations, presents specific challenges for vapor barrier installation under slabs. Understanding these factors and implementing appropriate countermeasures is crucial for ensuring the longevity and performance of the slab and the building structure. Proper installation techniques, coupled with the right materials, can minimize the risks associated with Florida’s climate, protecting against moisture damage and structural issues.Florida’s humid subtropical climate significantly impacts vapor barrier installations.
High humidity levels contribute to moisture migration through the slab, potentially leading to condensation and mold growth. This is especially critical beneath concrete slabs, where moisture can accumulate and degrade the structural integrity of the building over time.
Humidity and Temperature Fluctuations
High humidity levels in Florida can lead to moisture condensation on the vapor barrier, particularly during periods of temperature fluctuations. This moisture can seep into the slab, potentially causing structural damage, mold growth, and compromising the integrity of the building’s foundation. Proper selection of a vapor barrier material with high moisture resistance and the incorporation of appropriate drainage systems are crucial.
For example, a polyethylene vapor barrier, when properly installed, can significantly reduce moisture migration and mitigate condensation issues. Furthermore, ensuring adequate air circulation and ventilation around the slab helps prevent moisture accumulation and accelerates drying times.
Proper Ventilation and Drainage
Adequate ventilation and drainage around the slab are essential to manage moisture and prevent water accumulation. Properly designed and installed drainage systems, including gutters, downspouts, and French drains, direct water away from the slab foundation, minimizing the risk of waterlogging and subsequent moisture problems. Furthermore, sufficient air circulation through the slab’s perimeter allows for efficient moisture evaporation, reducing the likelihood of condensation.
For instance, ensuring proper spacing between the slab and surrounding landscaping elements allows air to circulate and reduces the potential for moisture buildup.
High Groundwater Tables
Florida’s high groundwater tables in certain areas pose a significant challenge for vapor barrier installations. The proximity of groundwater can lead to capillary action, drawing moisture into the slab. Implementing a well-designed vapor barrier system, including a properly sloped slab surface, is crucial to prevent moisture migration. For instance, using a thicker vapor barrier material or adding a layer of gravel beneath the slab can help mitigate the impact of high groundwater tables.
The design and installation of the vapor barrier should consider the local groundwater table elevation to prevent issues.
Hurricanes and Flooding
Florida’s vulnerability to hurricanes and flooding necessitates careful consideration in vapor barrier design. The potential for storm surge and flooding requires vapor barriers to withstand significant water pressure and prolonged exposure to moisture. The use of waterproof materials and robust installation techniques are crucial in mitigating potential damage. Additionally, the design should consider the potential for water infiltration and incorporate methods for rapid drainage and evacuation.
For example, elevated slab designs or using water-resistant concrete admixtures can minimize the impact of flooding on the vapor barrier and the slab itself. Furthermore, proper grading and drainage around the slab are critical for diverting floodwaters away from the foundation.
Troubleshooting and Maintenance
Proper installation of a vapor barrier under a slab in Florida is crucial for preventing moisture issues, but even with meticulous installation, problems can arise. Understanding potential issues and their solutions is essential for maintaining a sound foundation and preventing costly repairs down the line. This section delves into common problems, their causes, and effective remedies, along with long-term maintenance strategies.
Common Installation Issues
Florida’s unique climate, with its combination of high humidity and occasional heavy rainfall, presents specific challenges to vapor barrier installation. Improper sealing or inadequate overlapping of the barrier materials can lead to moisture infiltration. Incorrect installation techniques, such as insufficient lapping or using improper adhesive types, can also compromise the barrier’s integrity. A poorly installed barrier can lead to significant issues, ranging from minor dampness to more severe water damage, potentially impacting the structural integrity of the building.
Causes and Remedies for Moisture Intrusion
- Improper Barrier Material Selection: Using a vapor barrier not suited for Florida’s climate, such as one that doesn’t resist moisture penetration or isn’t sufficiently resistant to UV degradation, can result in moisture intrusion. Choosing a high-quality, properly rated material that is designed for high humidity environments is crucial.
- Insufficient Overlap and Sealing: Gaps or inadequate overlaps between vapor barrier sections allow moisture to seep into the slab. Careful, precise lapping and sealing of seams using appropriate materials, such as specialized tapes and adhesives, are critical for a robust barrier.
- Poor Installation Techniques: Improper handling or placement of the barrier material, such as inadequate support or improper placement on the subgrade, can create vulnerabilities. Thorough training for installers and adhering to manufacturer specifications are key to achieving a leak-proof barrier.
Troubleshooting Table
Issue | Cause | Remedy |
---|---|---|
Moisture intrusion | Improper barrier material, insufficient overlap, poor installation | Select appropriate barrier, ensure proper overlaps and sealing, and use trained installers |
Cracking or tearing | Poor material quality, improper handling, temperature fluctuations | Use high-quality materials, handle carefully, and consider climate-appropriate installation techniques. |
Pooling water under the slab | Blocked drainage, poor grading around the foundation | Ensure proper drainage around the foundation, fix any drainage issues, and review the grading plan. |
Mildew or mold growth | Moisture trapped under the barrier | Proper installation to eliminate moisture, use moisture-resistant materials and ensure proper ventilation |
Long-Term Maintenance and Inspection
Regular inspection and maintenance are vital for a vapor barrier’s longevity in Florida’s climate. Visual inspections should be conducted periodically to detect any signs of damage, such as cracking, tearing, or moisture intrusion. Addressing any identified issues promptly will help maintain the integrity of the vapor barrier and prevent further problems. Regular maintenance and proactive inspection, potentially including moisture testing or using moisture sensors, are vital to prevent costly repairs or structural damage later.
This proactive approach can save significant costs and ensure the longevity of the building.
Illustrative Examples and Case Studies
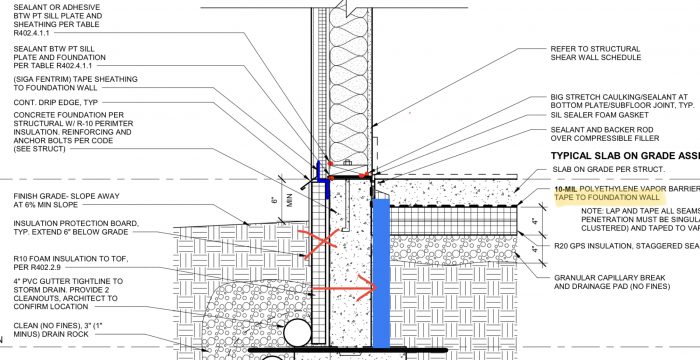
Florida’s unique climate, with its high humidity and frequent rainfall, presents specific challenges when installing vapor barriers under slabs. Understanding successful and unsuccessful installations, along with the reasons behind their outcomes, is crucial for homeowners and contractors alike. This section delves into real-world examples, highlighting both positive and negative experiences with vapor barriers, and offers valuable insights for optimal installation practices.
Successful Vapor Barrier Installations in Florida
Several successful installations in Florida have demonstrated the effectiveness of properly applied vapor barriers. These installations have consistently shown reduced moisture intrusion, improved slab durability, and enhanced the longevity of the structures. A notable example involves a custom home builder who used a polyethylene sheet vapor barrier under a concrete slab for a new construction project. The meticulous installation process, which included careful sealing of seams and proper drainage, resulted in a dry, stable slab with no visible signs of moisture damage after several years.
Another instance involved a homeowner retrofitting an existing slab with a reinforced, multi-layered vapor barrier system. This homeowner experienced a significant reduction in moisture problems that had previously plagued the property. The use of a thicker barrier, coupled with careful sealing around pipes and utilities, played a key role in the success.
Challenges and Solutions in Florida Installations
Florida’s humid climate necessitates specific attention to detail during vapor barrier installation. One common challenge is improper sealing around penetrations, such as plumbing and electrical conduits. Solutions often involve using specialized sealant tape and caulking, ensuring a complete barrier against moisture infiltration. Another challenge arises from inadequate drainage around the perimeter of the slab. This can lead to water pooling and subsequent moisture issues beneath the slab.
Solutions include proper grading and the use of perimeter drains to effectively manage rainwater runoff.
A Case Study of Vapor Barrier Failure
A recent case study highlighted a vapor barrier failure in a commercial building. The installation, while initially appearing sound, suffered from inadequate sealing around utility pipes. Moisture seeped through these gaps, creating significant moisture buildup beneath the slab. Over time, this led to structural damage, mold growth, and ultimately, substantial repair costs. The root cause of failure was the lack of attention to detail in sealing all penetrations.
This failure underscores the critical importance of meticulous sealing to prevent moisture intrusion.
Proper Installation Technique: A Visual Guide
The following diagram illustrates the correct installation procedure for a vapor barrier under a slab. Proper sealing of the barrier around pipes and utilities is emphasized. Careful attention to detail in sealing the perimeter, creating proper drainage, and ensuring a complete vapor barrier is essential.
Diagram Description: A labeled diagram showcasing the installation of a vapor barrier under a slab. Key elements depicted include the vapor barrier itself (e.g., polyethylene sheeting), the concrete slab, pipes (e.g., plumbing, electrical conduits), and critical sealing areas (e.g., seams, penetrations). The diagram emphasizes proper overlap, sealing with sealant tape and caulking, and the importance of perimeter drainage.
Regulations and Codes in Florida
Florida building codes and regulations play a crucial role in ensuring the safety and structural integrity of construction projects, including those involving vapor barriers under slabs. Adherence to these codes is essential for preventing potential issues like moisture intrusion, structural damage, and mold growth. Understanding these regulations is vital for both contractors and homeowners to ensure compliance and avoid costly mistakes or legal complications.
Relevant Building Codes and Regulations
Florida’s building codes are primarily based on the International Building Code (IBC) and adapted by the state for specific conditions. These codes often incorporate standards for moisture control, including the use of vapor barriers. Specific sections within the Florida Building Code address the requirements for moisture control in concrete slabs-on-grade. These sections detail the materials, installation procedures, and inspection criteria to ensure proper installation of vapor barriers.
Key Requirements and Guidelines
Florida building codes mandate the use of vapor barriers in certain situations, especially when dealing with concrete slabs-on-grade. Key requirements typically include specifying the type of vapor barrier material, its installation method, and its proper attachment to the slab. The code also often Artikels the necessary clearances between the barrier and the building’s foundation and the slab’s reinforcement.
Further, the code may mandate regular inspections throughout the construction process to ensure compliance.
Local Variances and Interpretations
Local jurisdictions within Florida might have specific variances or interpretations of the state building codes. These variances can arise from local environmental conditions or unique building practices. For example, areas with higher humidity levels may have specific guidelines for vapor barrier thickness or material selection. It’s important to consult with the local building department to understand any locally specific requirements.
Importance of Consulting Local Building Officials
Prior to commencing any construction project, it’s imperative to consult with the local building department and obtain necessary permits and approvals. Building officials can provide specific guidance regarding the application of state codes in your particular location. They can clarify any ambiguities or answer specific questions related to vapor barrier installation. This proactive approach is crucial to ensure the project is completed in compliance with local regulations and avoids costly rework or delays.
This ensures the project aligns with the local conditions and standards, minimizing potential problems. Consulting with local officials is not merely an option but a crucial step to successful and compliant construction.
Cost Estimation and Budgeting
Estimating the cost of installing a vapor barrier under a slab in Florida involves considering various factors, including material selection, labor rates, and project complexity. Accurate cost estimation is crucial for project planning and successful completion. A well-defined budget allows for informed decision-making and avoids potential cost overruns.
General Cost Estimate
A general cost estimate for installing a vapor barrier under a slab in Florida ranges from $5 to $20 per square foot, depending on several factors. This range accounts for the labor, materials, and potential site-specific conditions. Factors like the size of the slab, the type of vapor barrier, and the complexity of the installation will significantly influence the final price.
Factors Influencing Final Cost
Several key factors contribute to the total cost of vapor barrier installation. Material type is a primary driver. High-performance, multi-layered barriers or those with enhanced moisture resistance tend to be more expensive than basic options. Labor rates vary depending on local market conditions, contractor experience, and the scope of the project. The size of the slab significantly affects the overall cost, with larger slabs generally requiring more labor and materials.
Site conditions, such as the presence of obstacles or uneven ground, can also impact labor costs. The complexity of the installation, such as the need for specialized equipment or additional reinforcement, will affect the overall project cost.
Cost-Effectiveness of Different Vapor Barrier Options
The cost-effectiveness of different vapor barrier options varies based on the project’s specific needs and environmental conditions. A simple polyethylene sheet might be economical for straightforward applications but may not provide the same level of protection as a more advanced, multi-layered barrier in a high-moisture environment. While the initial cost of a more robust barrier might be higher, its long-term benefits in terms of reduced moisture-related issues and improved slab performance can make it a cost-effective choice in the long run.
Typical Material and Labor Costs
Material | Approximate Cost per Square Foot | Notes |
---|---|---|
Polyethylene sheeting (basic) | $0.50 – $2.00 | Low initial cost, suitable for simpler applications. |
Reinforced polyethylene sheeting | $1.00 – $3.00 | Offers better tensile strength and puncture resistance. |
Specialized vapor barriers (e.g., with added waterproofing) | $2.00 – $5.00 | Provides enhanced moisture protection, especially in high-humidity areas. |
Labor (installation per square foot) | $2.00 – $10.00 | Dependent on complexity, site conditions, and labor rates in the area. |
Note: These figures are approximate and may vary based on the specific location, vendor, and contractor. Always obtain detailed quotes from multiple contractors to ensure accurate cost comparisons.
Ultimate Conclusion
So, there you have it! A comprehensive guide on how to install a vapor barrier under your Florida slab. By following these steps, you can protect your home from moisture damage and ensure a long-lasting, dry foundation. Remember, proper installation is key. Don’t cut corners; your investment deserves the best! Now go forth and build that beautiful, moisture-free slab!
Frequently Asked Questions
What are some common issues that can arise during vapor barrier installation in Florida?
Common issues include improper sealing, inadequate drainage around the slab, and not accounting for Florida’s high humidity levels. Problems can also stem from improper ventilation or inadequate preparation of the sub-slab area.
How does Florida’s climate affect vapor barrier installation?
Florida’s humidity and temperature fluctuations can significantly impact the performance of vapor barriers. Extreme temperatures and high humidity can affect the barrier’s effectiveness, so proper installation is crucial.
What are the different types of vapor barriers available for Florida slabs?
Common materials include polyethylene sheeting, reinforced membranes, and specialized waterproof coatings. Each material has its own pros and cons in terms of cost, installation, and performance in Florida’s climate.
What building codes and regulations should I follow in Florida for vapor barrier installation?
Consult local building codes and regulations for specific requirements. These codes vary by city and county, so checking with local officials is essential.