How to keep 1/2 inch copper unions from leaking? This comprehensive guide delves into the intricacies of preventing leaks, from installation to troubleshooting and environmental considerations. Understanding the causes, proper installation techniques, and potential issues is crucial for maintaining a leak-free system.
This guide explores the common reasons for leaks, focusing on crucial aspects like torque, pipe preparation, and material selection. It provides detailed steps for preventing leaks during installation, troubleshooting existing issues, and selecting the right materials for optimal performance. We also examine environmental factors affecting copper unions, offering solutions for corrosion and temperature fluctuations.
Causes of Copper Union Leaks: How To Keep 1/2 Inch Copper Unions From Leaking
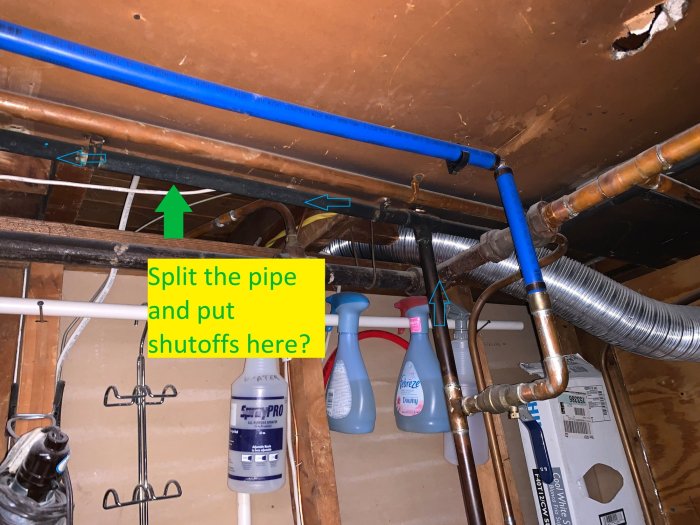
Copper unions, vital for connecting pipes, can unfortunately leak. Understanding the reasons behind these leaks is crucial for effective maintenance and repair. Preventing leaks often hinges on meticulous installation practices and an understanding of the materials and environmental factors involved.Copper unions, though reliable, can fail if not handled with care. Improper installation, material defects, and environmental stresses are key contributors to leakage.
Thorough attention to detail during installation and awareness of potential stressors are essential to ensure longevity and avoid costly repairs.
Improper Installation
Poor installation practices are a significant cause of copper union leaks. Correct torque application and precise tightening procedures are paramount. Incorrect torque can lead to insufficient clamping force, allowing water or other fluids to seep through. Conversely, excessive tightening can distort the union components or damage the pipes. A properly calibrated torque wrench is essential for consistent and accurate tightening.
Referencing the manufacturer’s recommendations is critical for the appropriate torque setting. Following manufacturer guidelines ensures consistent and effective clamping force, minimizing the risk of leakage.
Material Defects
Material defects in the copper unions themselves can also contribute to leaks. Imperfections like pinholes, cracks, or inconsistent metal thickness can weaken the union’s ability to seal. Careful visual inspection of the union components during installation is necessary to detect potential flaws. Unions with apparent defects should be rejected and replaced to avoid potential leaks. The quality of the copper used in the unions also influences their integrity.
Environmental Factors
Environmental factors, such as fluctuating temperatures and pressures, can affect the integrity of copper unions. Expansion and contraction of the union components due to temperature variations can disrupt the seal. Sudden pressure changes can also cause leaks. Maintaining consistent operating temperatures and pressures within the recommended ranges for the union type can help mitigate these effects. In environments prone to extreme temperature swings, appropriate insulation or thermal protection measures may be necessary to ensure the union’s longevity and prevent leaks.
Torque and Tightening Procedures
Proper torque application is crucial for achieving a secure and leak-free connection. A torque wrench, set to the manufacturer’s recommended value, ensures consistent clamping pressure across all unions. Over-tightening can damage the threads or the union itself, while under-tightening will not provide adequate clamping force.
Pipe Preparation
Proper pipe preparation is essential for successful union installations. Cleanliness and deburring are vital. Dirt, debris, and burrs on the pipe ends can prevent a tight seal, leading to leaks. Thorough cleaning and deburring of the pipe ends ensures a smooth surface for the union to create a reliable seal.
Different Types of Copper Unions
Various types of copper unions exist, each with its own characteristics and susceptibility to leaks. Different designs may handle varying pressure and temperature ranges differently. Consulting the manufacturer’s specifications for the specific union type is essential to determine its suitability for the application. Understanding the intended use and the operating conditions of the system is important for selecting the appropriate type of union.
Temperature and Pressure Fluctuations
Temperature and pressure fluctuations can significantly impact the performance of copper unions. Significant temperature variations cause material expansion and contraction, potentially affecting the tightness of the seal. Extreme pressure changes can also stress the union, potentially causing leaks. Ensuring stable temperatures and pressures within the specified operating parameters of the union is vital to prevent leakage.
Preventing Leaks During Installation
A properly installed copper union is a crucial component in any plumbing system. Preventing leaks during installation is paramount to ensuring long-lasting performance and avoiding costly repairs. This section will detail the steps for a leak-free installation.Careful installation significantly reduces the likelihood of future problems. By following the steps Artikeld here, you can achieve a strong, reliable connection.
Step-by-Step Installation Procedure
Careful preparation is key to a successful copper union installation. Start by ensuring the pipe ends are clean and free of burrs. A burr can act as a stress point, potentially leading to a leak.
- Thorough Pipe Preparation: Clean the pipe ends with sandpaper or a wire brush to remove any rust, scale, or imperfections. This creates a smooth surface for the union to grip firmly.
- Proper Union Assembly: Place the union on the pipe, ensuring the threads align properly. Then, insert the pipe ends into the union body. Careful alignment is crucial to ensure the connection is even.
- Sealant Application: Apply a thin, even layer of pipe sealant to the threads of the union. Too much sealant can create a weak point and potentially trap contaminants. A small amount of quality sealant is best.
- Tightening the Union: Follow the recommended tightening method and torque specifications to achieve a secure connection. This step is critical in preventing leaks and ensuring the longevity of the union.
- Leak Testing: After tightening, turn on the water supply slowly and monitor for any leaks. Check the connections carefully. If leaks are present, re-tighten or re-evaluate the installation process.
Tightening Methods Comparison
Different tightening methods have different advantages and disadvantages. Choosing the right method is crucial for a leak-free installation.
Method | Description | Advantages | Disadvantages |
---|---|---|---|
Hand-tightening | Tightening by hand, applying even pressure. | Easy to control, suitable for initial tightening. | Can be inconsistent, might not achieve sufficient torque. |
Wrench Tightening | Using a wrench to apply controlled torque. | Provides consistent torque, good for achieving proper tightening. | Requires proper technique to avoid over-tightening. |
Torque Specifications | Tightening to a specific torque value using a torque wrench. | Ensures consistent tightening, prevents over-tightening. | Requires a torque wrench, can be more complex to implement. |
Troubleshooting Potential Issues
Unforeseen problems can arise during installation. Knowing how to troubleshoot these issues can save time and prevent further damage.
- Leaking Union: If a leak occurs, first check the sealant application. If it is sufficient, re-tighten the union, following the correct method. If the leak persists, re-examine the pipe ends for any imperfections and re-apply sealant.
- Pipe Damage: Damaged pipe ends can lead to leaks. Inspect the pipe ends for any imperfections and replace them if necessary. Ensure that the pipe ends are correctly prepared before assembling the union.
- Incorrect Sealant Application: Insufficient or excessive sealant can cause leaks. Apply a thin layer of sealant to the threads. Excess sealant can weaken the connection and cause leaks.
Preparing Pipe Ends
Proper preparation of the pipe ends is essential for a strong and leak-free connection. Ensure the ends are clean and free of any imperfections that might compromise the union’s integrity.Preparing pipe ends involves removing any rust, scale, or burrs that might weaken the connection. This creates a smooth surface for the union to grip. Using sandpaper or a wire brush to smooth the pipe ends ensures a better seal.
Using Appropriate Pipe Sealant
Choosing the right pipe sealant is crucial for a leak-free installation. A quality sealant adheres properly and prevents leaks. Apply the sealant evenly to the threads of the union. Too much or too little sealant can lead to issues.Use a suitable pipe sealant designed for copper unions. Apply a thin layer to ensure the threads are properly lubricated.
Avoid applying excessive amounts of sealant.
Troubleshooting Existing Leaks
A leaky copper union can be frustrating, but with a systematic approach, you can often pinpoint the problem and get it fixed quickly. Understanding the causes and symptoms is key to effective troubleshooting.Identifying the source of the leak and the appropriate repair method is crucial to preventing further damage and maintaining the integrity of your plumbing system.
Systematic Leak Diagnosis
A systematic approach to diagnosing leaks involves a combination of visual inspection, pressure testing, and identifying the specific type of leak. This allows for a targeted repair approach.
Visual Inspection
Visual inspection is often the first step. Look closely at the union for any visible signs of damage, such as cracks, dents, or corrosion. Check the threads for damage or improper alignment. Examine the connection points where the union meets the pipe. Look for any signs of water accumulation or dampness around the joint.
Even small drips can be a symptom of a larger problem, requiring attention.
Pressure Testing
Pressure testing is a more involved method for identifying leaks. It helps to isolate the leak’s location and severity. Use a suitable pressure gauge and carefully apply pressure to the system, monitoring the gauge. Any sudden drop in pressure indicates a leak. Note the exact location where the pressure drops, as it pinpoints the area needing repair.
Use caution during pressure testing, following safety guidelines and using appropriate tools.
Types of Leaks and Causes
Leaks can vary in severity, from minor drips to major bursts. Minor drips might indicate loose connections or minor corrosion, while major bursts could point to significant structural issues.
- Minor Leaks (Drips): These are often caused by loose connections, corrosion, or slight misalignment of the union threads. A simple tightening of the union nut or a minor adjustment in alignment can resolve this type of leak.
- Moderate Leaks: Moderate leaks might suggest more significant issues, like corrosion progressing or a damaged union. Careful examination of the union and connections will help to determine the cause and appropriate repair.
- Major Leaks (Bursts): Major leaks typically stem from severe damage, such as cracks in the union or pipe, or significant corrosion. In this case, immediate action is required to contain the leak and prevent further damage to the plumbing system. Replacement is usually necessary in such situations.
Repairing Minor Leaks
For minor leaks, several steps can help. First, turn off the water supply to the affected area. Next, carefully tighten the union nut, ensuring it’s snug but not over-tightened. Inspect the threads and ensure they are clean and properly aligned. If corrosion is a factor, use a suitable corrosion inhibitor.
Reapply sealant if necessary. Re-check the connection after a period to ensure the leak is resolved.
When to Replace a Union
While tightening and adjustments can often fix minor leaks, some issues necessitate replacement. A union with significant damage, corrosion, or cracks should be replaced to prevent further leaks and ensure long-term system integrity. If the leak is persistent despite repeated attempts at repair, replacement is generally the best course of action. Don’t risk a potential larger problem down the road.
Material Selection and Quality
Choosing the right materials for your 1/2-inch copper unions is crucial for leak-free connections. The quality of the copper itself, and the way it’s processed, directly affects the union’s longevity and resistance to leaks. Understanding the nuances of different copper alloys and their properties will help you make informed decisions.Copper, in its various forms, is a popular material for plumbing connections due to its inherent corrosion resistance and ductility.
However, not all copper is created equal. The specific alloy, manufacturing processes, and quality control procedures all influence the union’s performance. Carefully examining the materials and specifications of your unions is a critical step in ensuring their durability.
Copper Alloy Types
Copper alloys, often containing small amounts of other metals like tin, zinc, or lead, influence the union’s properties. Different alloys offer varying levels of strength, ductility, and corrosion resistance. Understanding these differences is vital for choosing the appropriate material for a specific application.
- Copper (Cu): Pure copper, while excellent in corrosion resistance, might not be strong enough for all applications, potentially leading to leaks if not appropriately handled during installation. Its softness is often a concern.
- Copper-Tin Alloys (Cu-Sn): These alloys, typically containing 1-2% tin, often show improved strength and durability over pure copper. This increased strength makes them suitable for applications requiring more stress or vibration.
- Copper-Zinc Alloys (Cu-Zn): These alloys, also known as brass, offer a good balance of strength and ductility. They’re often utilized in applications requiring higher strength and better wear resistance. The zinc content can affect the resistance to corrosion.
Importance of Quality Control, How to keep 1/2 inch copper unions from leaking
Ensuring the quality of purchased copper unions is paramount. Look for certifications, manufacturing standards, and any documentation provided by the supplier.
- Certifications and Standards: Look for certifications like those from recognized organizations (e.g., ASTM standards). These certifications often indicate adherence to quality standards, helping to ensure consistency and reliability in the material’s properties.
- Manufacturing Processes: Consider the manufacturing process employed. Processes like cold-drawing or annealing can significantly impact the final properties of the union. A well-defined manufacturing process can contribute to leak resistance.
- Supplier Reputation: Choose reputable suppliers known for providing quality materials and adherence to industry standards. A supplier’s history of reliability can be a valuable indicator of the quality of the unions they offer.
Signs of Poor-Quality Unions
Identifying signs of poor-quality copper unions can help you avoid potential problems.
- Uneven Thickness or Surface Irregularities: Inspect the union for uneven thickness or surface irregularities. These imperfections can compromise the union’s strength and lead to leaks over time.
- Visible Defects: Look for signs of defects like cracks, pitting, or discoloration. These defects often indicate a problem with the material’s quality or manufacturing process.
- Excessive Flexibility: A union that is excessively flexible or bends easily may not be suitable for the intended application. This could lead to leaks and other problems.
Consequences of Using Substandard Materials
Using substandard materials for copper unions can have serious consequences.
- Early Failure: Substandard materials are more likely to fail prematurely, leading to leaks and costly repairs.
- Increased Risk of Leaks: The weakened structure of substandard materials increases the risk of leaks, potentially damaging property or causing safety hazards.
- Reduced Service Life: The lifespan of unions made with substandard materials will likely be shorter than those made with high-quality materials.
Environmental Considerations
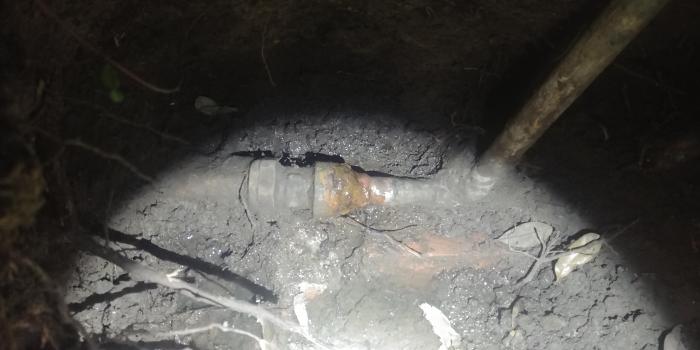
Copper unions, while robust, are susceptible to environmental factors. Understanding these influences is crucial for ensuring long-term performance and preventing leaks. Proper installation in various environments necessitates careful consideration of potential stresses.Environmental factors, like temperature fluctuations and humidity, can impact the integrity of copper unions. Corrosion, another significant concern, can weaken the material over time. By understanding these influences, you can safeguard your installations and avoid costly repairs.
Temperature Extremes
Temperature variations can cause thermal expansion and contraction in the piping system. If not properly accounted for, these stresses can lead to leaks. Extreme cold can also reduce the ductility of copper, making it more prone to cracking. Conversely, high temperatures can cause the copper to soften and deform.
Humidity and Moisture
High humidity and moisture can accelerate corrosion, even in seemingly benign environments. Moisture trapped within the union or the surrounding area can foster a corrosive environment.
Corrosion
Corrosion is a significant threat to copper unions, leading to weakening and eventual leaks. The presence of certain chemicals or minerals in the water supply can accelerate this process. The resulting pitting or erosion can compromise the integrity of the union.
Specific Environments Requiring Caution
Certain environments necessitate extra care during copper union installation. For instance, coastal areas with high salt content in the air or water are particularly susceptible to corrosion. Areas with fluctuating temperatures, such as those experiencing frequent freeze-thaw cycles, require careful consideration.
Protecting Unions from Corrosive Elements
Protecting copper unions from corrosive elements is paramount. Using corrosion-resistant materials for surrounding components, employing protective coatings, and selecting appropriate materials for the water supply are essential preventive measures. Proper drainage to prevent moisture accumulation is another crucial step.
Environmental Factors and Potential Effects
Environmental Factor | Potential Effect on Copper Unions |
---|---|
Extreme Temperatures (High/Low) | Thermal expansion/contraction stresses, reduced ductility, potential for cracking or deformation |
High Humidity/Moisture | Accelerated corrosion, moisture accumulation, potential for pitting or erosion |
Presence of Corrosive Chemicals/Minerals | Accelerated corrosion, pitting, erosion, weakening of the union |
Coastal Environments | Increased risk of corrosion due to salt content in air or water |
Freeze-Thaw Cycles | Increased risk of cracking and leaks due to repeated expansion and contraction |
Visual Aids and Illustrations
Properly installed copper unions are crucial for preventing leaks and maintaining plumbing systems. Visual aids can significantly enhance understanding and help ensure correct installation techniques. These visual tools provide a clear and concise method for learning and applying the knowledge needed to work safely and efficiently with copper unions.Visual representations of proper installation and potential issues are essential for effective learning.
They provide a concrete understanding that transcends textual descriptions, making the process of installing and maintaining copper unions much safer and more reliable.
Properly Installed 1/2-Inch Copper Union
A properly installed 1/2-inch copper union features a smooth, clean surface with no burrs or imperfections. The union’s compression ring is fully engaged and seated within the union body, ensuring a tight seal. The pipe ends are properly prepared, with the threads matching the union’s threads precisely. The union nuts are snugly tightened, avoiding over-tightening. The visual should demonstrate the union’s connection to the pipes, clearly showing the aligned threads and the compressed ring.
Types of Leaks and Their Causes
This illustration shows various leak types, each with its distinct cause. A leak from the compression ring indicates improper seating or insufficient tightening. A leak at the pipe threads suggests mismatched threads or damaged pipe ends. A leak from the union nut indicates over-tightening or loose nuts. Each leak type is visually distinguished, with arrows highlighting the affected area and a concise caption explaining the cause.
Torque Application Diagram
A detailed diagram of the correct torque application is essential for preventing leaks. The diagram should use a graduated scale to indicate the correct torque settings for different pipe sizes. An arrow would indicate the direction of tightening and illustrate the torque wrench application method for the union nuts. A table showing recommended torque settings for 1/2-inch copper unions would be helpful.
Tools for Installation and Maintenance
A labeled image displaying the necessary tools for copper union installation is helpful. The tools include a pipe cutter, pipe threader, pipe wrench, adjustable wrench, a torque wrench (essential for proper tightening), a pipe vise, and a pipe cleaner. The tools are displayed with clear labels indicating their purpose in the installation process.
Common Mistakes in Union Installation
This visual aid illustrates common mistakes, such as insufficient thread preparation, over-tightening of the union nuts, and improper compression ring engagement. The diagram clearly shows the visual differences between a correctly installed union and one with these common mistakes, emphasizing the criticality of each step in the process. Arrows would point to the problematic areas, highlighting the potential for leaks and damage if these mistakes are not corrected.
Final Review
In conclusion, preventing leaks in 1/2 inch copper unions involves a multi-faceted approach. Careful installation, correct torque application, and meticulous pipe preparation are key to avoiding future problems. This guide provides a systematic approach to diagnosis and repair, along with crucial insights into material selection and environmental considerations. By understanding the intricacies of copper unions, you can ensure a leak-free and long-lasting system.
Query Resolution
What are the most common causes of leaks in 1/2 inch copper unions?
Improper installation, inadequate tightening, material defects (like poor-quality copper or damaged unions), and environmental factors like temperature fluctuations or corrosion can all contribute to leaks.
How can I prevent leaks during the installation process?
Thoroughly clean and deburr pipe ends, use the correct pipe sealant, and apply appropriate torque during tightening. Refer to the manufacturer’s specifications for recommended torque values.
What are some common mistakes in union installation that lead to leaks?
Insufficient tightening, using incorrect pipe sealant, improper pipe preparation (e.g., not deburring), and not checking the quality of the union are common errors. Over-tightening can also cause damage.
How do I troubleshoot existing leaks in copper unions?
Begin with a visual inspection, looking for obvious issues. Pressure testing can identify leaks and help determine the source. Depending on the leak’s severity, you may be able to repair it with proper tools and materials. If the leak is significant or persistent, replacing the union may be necessary.