How to lower my ethanol percentage is a critical issue across various sectors, from fuel production to beverage formulation. Understanding the intricacies of ethanol reduction methods is essential for optimizing processes and ensuring compliance with industry standards.
This guide delves into the multifaceted aspects of ethanol reduction, covering everything from fundamental concepts to advanced techniques, equipment requirements, and safety protocols. We’ll explore the diverse applications where ethanol percentage manipulation is crucial, from optimizing fuel efficiency to refining beverage quality.
Understanding Ethanol Percentage
Ethanol, a versatile alcohol, plays a crucial role in various applications, from fueling our vehicles to crafting delicious beverages. Understanding its concentration, or percentage, is essential for safety, performance, and proper application. This section delves into the significance of ethanol percentage in different contexts, providing a clear definition and examining its impact.Ethanol percentage, often denoted as a volume percentage (vol%), signifies the proportion of ethanol present in a mixture, typically expressed as a percentage.
This measurement is crucial for determining the potency of alcoholic beverages and the performance characteristics of fuels. Different measurement methods and units might be used depending on the context, which will be clarified below.
Ethanol Percentage in Fuels
The incorporation of ethanol into fuels, like gasoline, has gained significant traction as a renewable alternative. Understanding the specific percentage of ethanol in different fuels is vital for optimal engine performance and safety.
Fuel Type | Ethanol Percentage (vol%) | Remarks |
---|---|---|
E10 | 10 | Commonly used blend, offering a moderate level of ethanol content. |
E85 | 85 | Higher ethanol content, often requiring specialized engines for optimal performance. |
E15 | 15 | A blend with 15% ethanol, suitable for various vehicles. |
Pure Ethanol | 100 | Used in specialized applications, requiring appropriate infrastructure. |
Implications of High Ethanol Percentage
High ethanol percentages in fuels can influence engine performance and require adjustments in vehicle design and maintenance practices. The higher the ethanol percentage, the greater the potential for certain issues, such as corrosion or fuel system incompatibility.
Ethanol Percentage in Beverages
The concentration of ethanol in alcoholic beverages directly impacts their strength and flavor profile. Different types of alcoholic beverages contain varying ethanol percentages, which are legally regulated in many regions.
Definition and Measurement Units
Ethanol percentage is defined as the volume of ethanol present in a given volume of a mixture, usually expressed as a percentage (vol%). The measurement unit for ethanol percentage is volume percent (vol%).
Impact of High Ethanol Percentage in Various Applications
High ethanol percentages in fuels can lead to a variety of implications. For instance, increased corrosion in fuel systems or potential compatibility issues with certain vehicle components. In beverages, higher ethanol percentages lead to stronger alcoholic effects. In other applications, high ethanol concentrations might be necessary for specific reactions or processes.
Methods for Reducing Ethanol Percentage
Reducing the ethanol content in fuel or other substances requires careful consideration of various methods. Each technique presents a unique set of advantages and disadvantages, impacting practicality and cost. Understanding these factors is crucial for selecting the most suitable approach for a given situation. Safety precautions must always be prioritized during the process.Different techniques offer varying degrees of effectiveness in achieving the desired ethanol percentage reduction.
Choosing the right method depends on factors like the starting ethanol concentration, the desired final concentration, and the available resources. The methods discussed below provide a comprehensive overview of the available options.
Distillation Techniques
Distillation methods are commonly used for separating substances based on their boiling points. This process involves heating the mixture to vaporize the component with the lower boiling point (in this case, often the desired non-ethanol component). The vapor is then condensed back into a liquid, effectively concentrating the desired substance. Different types of distillation, like fractional distillation, are used to achieve higher purity levels.
- Pros: Distillation is a relatively effective method for separating components with differing boiling points. It can yield a high degree of purity if done properly.
- Cons: Distillation can be energy-intensive, particularly for large volumes. Specialized equipment is often required, adding to the initial investment cost. The process can be complex and require significant technical expertise.
- Safety Precautions: Always handle the equipment with care and follow safety protocols for high-temperature operations. Ensure proper ventilation to avoid inhalation of potentially harmful vapors. Appropriate personal protective equipment (PPE), like safety glasses and gloves, should be worn.
- Effectiveness: The effectiveness of distillation depends on the specific setup and the volatility difference between the ethanol and the desired component. Fractional distillation can yield higher purity levels compared to simple distillation.
Absorption Methods
Absorption techniques utilize a specific material, called an absorbent, to selectively remove ethanol from the mixture. The absorbent material interacts with the ethanol, effectively drawing it away from the main substance. Common absorbents include activated charcoal and specific chemical compounds.
- Pros: Absorption methods can be relatively simple to implement, often requiring less specialized equipment compared to distillation. Some absorbents are reusable, potentially lowering the overall cost.
- Cons: Absorption methods may not be as effective at achieving very high purity levels. The efficiency of the process can be affected by factors like the concentration of ethanol and the properties of the absorbent.
- Safety Precautions: Follow manufacturer instructions carefully for the specific absorbent material being used. Ensure proper disposal procedures for the saturated absorbent, as it may contain residual ethanol.
- Effectiveness: The effectiveness of absorption methods varies significantly depending on the chosen absorbent and the specific conditions of the process. Effectiveness is often measured by the amount of ethanol removed per unit of absorbent.
Extraction Techniques
Extraction methods use solvents to selectively dissolve the ethanol from the mixture. The ethanol is then separated from the solvent, leaving a product with a lower ethanol concentration. Common solvents include specific types of alcohols and organic compounds.
- Pros: Extraction can be efficient for removing significant amounts of ethanol from a substance. The process can be relatively fast compared to other methods.
- Cons: Extraction often involves the use of potentially hazardous solvents, requiring strict safety measures. The cost of the solvent and the disposal of the solvent-ethanol mixture can be significant.
- Safety Precautions: Handle solvents with extreme caution, adhering to safety guidelines. Proper ventilation is essential. Always wear appropriate PPE, including gloves and safety glasses. Carefully dispose of the solvent mixture according to local regulations.
- Effectiveness: The effectiveness of extraction methods depends on the solvent chosen and the process parameters. The desired ethanol reduction percentage can be achieved by adjusting the solvent concentration and the duration of the process.
Method | Steps for Ethanol Reduction |
---|---|
Distillation | 1. Heat the mixture; 2. Collect the vapor; 3. Condense the vapor; 4. Collect the distillate. |
Absorption | 1. Contact the mixture with absorbent; 2. Separate the absorbent; 3. Treat the absorbent. |
Extraction | 1. Mix the substance with solvent; 2. Separate the phases; 3. Recover the extract. |
Factors Affecting Ethanol Reduction
Optimizing ethanol reduction procedures hinges on understanding the intricate interplay of various factors. A nuanced comprehension of these elements allows for targeted adjustments to maximize efficiency and minimize potential challenges. The success of any reduction method is not solely dependent on the chosen technique, but also on the interplay of variables, such as the starting concentration, temperature, and pressure.
Understanding these influences allows for proactive strategies to mitigate potential obstacles and achieve the desired ethanol percentage.
Influence of Starting Ethanol Concentration
The initial ethanol concentration significantly impacts the effectiveness of reduction methods. Higher initial concentrations necessitate longer treatment times or more aggressive methods, potentially increasing costs and energy consumption. Conversely, lower starting concentrations may be amenable to simpler and faster reduction procedures. This initial level dictates the amount of material that needs to be processed, influencing the overall cost-effectiveness of the operation.
For example, a solution with 20% ethanol requires different strategies than one with 5% ethanol, demanding different operational parameters and treatment durations.
Impact of Temperature on Reduction
Temperature significantly influences the kinetics of ethanol reduction processes. Elevated temperatures generally accelerate reaction rates, potentially speeding up the reduction process. However, excessive heat can sometimes lead to undesired side reactions or even damage the equipment. The optimal temperature often needs to be determined empirically for a specific system. For instance, in certain enzymatic reduction methods, higher temperatures can denature the enzymes, rendering the process ineffective.
Conversely, lower temperatures might prolong the reduction time, potentially leading to operational inefficiencies.
Impact of Pressure on Reduction
Pressure plays a crucial role in some ethanol reduction methods. Increased pressure can sometimes enhance the extraction or reaction rates, while excessively high pressure might introduce safety concerns or necessitate specialized equipment. Pressure variations can also impact the solubility of ethanol in the solvent, influencing the effectiveness of the reduction process. For instance, in distillation processes, higher pressure can alter the boiling points of ethanol and the target solvent, potentially leading to incomplete separation.
Potential Challenges in Ethanol Reduction
Several obstacles can hinder successful ethanol reduction. These include the potential for incomplete reduction, the generation of byproducts, and equipment limitations. Further, the presence of impurities in the feedstock can sometimes interfere with the reduction process, necessitating additional purification steps. Understanding these potential issues is vital to designing effective strategies to mitigate them. In industrial applications, the presence of dissolved solids or other impurities can foul the equipment or decrease the efficiency of the reduction method, necessitating additional pre-treatment steps.
Relationship Between Factors and Reduction Outcomes
Factor | Impact on Reduction Outcome |
---|---|
Starting Ethanol Concentration | Higher concentrations require longer processing times and potentially more aggressive methods. |
Temperature | Higher temperatures generally accelerate reactions but can lead to unwanted side reactions or equipment damage. |
Pressure | Increased pressure can enhance extraction/reaction rates, but excessively high pressure presents safety concerns. |
Impurities | Impurities in the feedstock can interfere with the reduction process, requiring additional purification. |
Applications and Examples: How To Lower My Ethanol Percentage
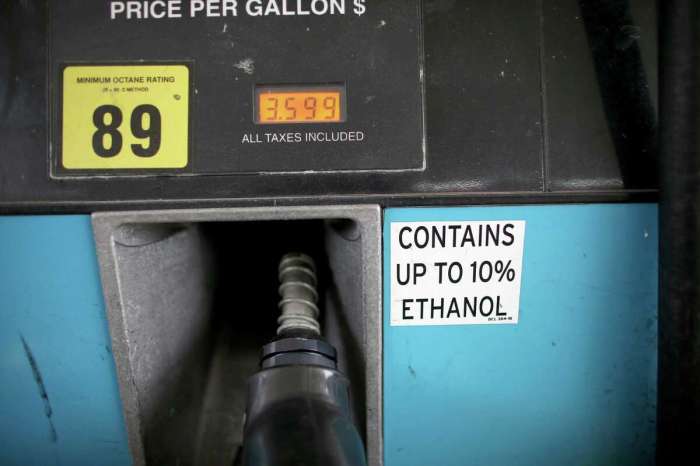
Fine-tuning the ethanol content in various products is crucial for achieving optimal performance and safety. From industrial applications to consumer goods, adjusting ethanol percentages is a vital step in ensuring quality and compliance with regulations. This section delves into specific applications requiring ethanol reduction, highlighting the reasons behind the need for lowered ethanol percentages and the desired levels in each case.Understanding the specific requirements for different applications is key to selecting the most effective ethanol reduction method.
The methods previously discussed are versatile and can be adapted to various contexts, but careful consideration of the particular application is essential for success. Different substances and environments will react differently to the chosen techniques, so understanding the specifics of the situation is crucial.
Fuel Blends
Fuel blends, such as gasoline and ethanol, are ubiquitous in modern transportation. Achieving the ideal ethanol percentage is critical for engine performance and fuel efficiency. Varying ethanol levels in fuels can impact ignition, combustion, and overall engine health.
- Gasoline blends with varying ethanol content (E10, E85) demand precise ethanol percentages for optimal performance. Engine knock, fuel economy, and emissions are directly affected by the concentration of ethanol. For example, using E85 fuel in a vehicle not designed for it can cause severe engine damage.
- The need for ethanol reduction in certain fuel blends arises when the engine’s design or the desired fuel properties conflict with high ethanol concentrations. Engines not designed to handle high ethanol content may experience performance degradation, leading to reduced fuel efficiency or increased emissions. This highlights the importance of using the correct ethanol blend for the intended application.
- The desired ethanol percentage in gasoline blends varies widely depending on the vehicle’s design and the intended use. Regulations and fuel standards dictate permissible levels to ensure engine compatibility and safety. For example, E10 fuel (10% ethanol) is commonly used in many vehicles, whereas E85 (85% ethanol) is designed for flex-fuel vehicles specifically built to handle high ethanol concentrations.
Beverage Production
Maintaining precise ethanol percentages is paramount in beverage production. The level of alcohol content directly affects the taste, quality, and overall consumer experience. Different types of alcoholic beverages require different ethanol concentrations.
- In the production of spirits like whiskey or vodka, maintaining a specific ethanol percentage is essential for achieving the desired taste profile. Different methods are used to achieve precise ethanol levels to maintain the desired flavor and quality characteristics.
- Regulations and consumer preferences often dictate the desired ethanol content in various beverages. Consumers frequently prefer beverages with a specific ethanol percentage, and manufacturers must meet these demands to ensure product appeal and maintain market share.
- The desired ethanol percentage varies significantly based on the type of beverage. Wine, for instance, requires a lower ethanol concentration than spirits, while beers have a range of acceptable ethanol percentages.
Industrial Solvents, How to lower my ethanol percentage
Ethanol serves as a crucial solvent in various industrial applications. Controlling the ethanol concentration is vital for achieving the desired properties of the solution.
- In industrial cleaning and chemical processing, maintaining specific ethanol percentages is crucial for safety and effectiveness. The ethanol concentration in these solutions directly impacts the effectiveness of the cleaning process, influencing the removal of contaminants.
- Specific industrial applications often require different ethanol concentrations for optimal performance. For example, in the production of certain chemical compounds, a precise ethanol percentage is necessary to achieve the desired reaction and outcome.
- Maintaining the correct ethanol concentration in industrial solvents prevents unintended reactions or harmful side effects. High concentrations of ethanol can compromise the integrity of the materials being processed or create safety hazards. For instance, high ethanol levels can alter the properties of polymers, leading to structural failures or degradation over time.
Table: Ideal Ethanol Percentage Ranges
Application | Ideal Ethanol Percentage Range (%) |
---|---|
Gasoline Blends | E10 (10%): widely used; E85 (85%): flex-fuel vehicles |
Beverages (Spirits) | 40-50% |
Beverages (Wine) | 10-15% |
Industrial Solvents | Dependent on specific application |
Equipment and Materials Required
Precise ethanol reduction often hinges on the right tools. Selecting and properly maintaining equipment is crucial for effective results and safety. Different methods necessitate varying equipment, each with specific specifications to ensure accurate measurements and controlled processes. This section details the equipment and materials needed for various ethanol reduction techniques, emphasizing the importance of proper selection and safety precautions.The appropriate equipment and materials directly impact the success and safety of ethanol reduction procedures.
Careful consideration of specifications and characteristics is essential. Inaccurate measurements or improper handling of materials can lead to compromised results and safety hazards. This section will systematically Artikel the necessary equipment for each reduction method.
Equipment for Distillation
Distillation is a common method for separating components based on their boiling points. Appropriate equipment is vital for controlled and efficient separation.
- Stills: Various types of stills are available, including pot stills, column stills, and continuous stills. Pot stills are simpler and more common for small-scale operations, while column stills offer greater precision for higher-purity separation. Continuous stills are used in large-scale industrial settings. Selecting the appropriate still depends on the scale of the operation and the desired purity of the final product.
Important considerations include the material of construction (e.g., stainless steel, copper), capacity, and heating elements. For example, a stainless steel still is suitable for food-grade ethanol, whereas copper stills might be preferred for certain chemical applications.
- Heating Elements: Electric heating mantles or immersion heaters are common choices. The heating element should be compatible with the material of the still and capable of providing consistent and controlled heat for efficient distillation. Overheating can lead to vapor lock and damage to the equipment. For instance, using an inadequate heating element in a large-scale distillation could lead to uneven heating, resulting in incomplete separation.
- Condenser: A condenser is used to cool the vapor and convert it back into a liquid. Common types include Liebig condensers, Allihn condensers, and others. The condenser material, cooling method (e.g., water or air cooling), and length significantly influence the efficiency of the process. Consider the desired output rate and the temperature of the cooling medium when choosing a condenser.
For instance, an inadequate condenser might lead to inefficient condensation, resulting in incomplete separation or product loss.
- Fractionating Columns: Used in column distillation, fractionating columns are essential for separating components with close boiling points. The design, material, and length of the column affect separation efficiency. Column packing materials and internal structures also contribute to separation effectiveness. For example, a poorly packed column could lead to a mixture of desired and undesired components in the output.
Equipment for Absorption
Absorption methods use a solvent to selectively remove ethanol. Proper equipment is essential for controlling the process and ensuring efficient absorption.
- Mixing Vessels: These are used to combine the ethanol solution with the solvent. The size and design of the mixing vessel depend on the volume of the solution being treated. For example, a small-scale mixing vessel may be adequate for laboratory-scale operations, while industrial-scale operations would require large-scale vessels.
- Solvent Tanks: Storing the solvent in appropriate tanks is crucial. Solvent tanks should be compatible with the solvent used and provide adequate storage capacity. The solvent should be handled with care to avoid spills and ensure proper safety procedures are followed. For example, improper storage of flammable solvents can create safety hazards.
- Separators: Separators are used to separate the solvent from the treated solution. The type of separator depends on the specific solvent used and the properties of the solution. For instance, a decanter centrifuge might be suitable for separating liquids with different densities.
Equipment for Other Methods
Other methods, like membrane separation, require specific equipment for efficient and safe implementation.
- Membrane Modules: Membrane modules are essential for selective separation. The type of membrane, its surface area, and its pore size greatly influence the efficiency of the process. Specific membrane modules are used based on the targeted separation and desired purity. For instance, choosing the wrong membrane module for a specific application can result in incomplete separation.
Equipment and Materials Summary
Method | Equipment/Materials | Specifications/Characteristics |
---|---|---|
Distillation | Stills, heating elements, condensers, fractionating columns | Material compatibility, capacity, efficiency |
Absorption | Mixing vessels, solvent tanks, separators | Volume, compatibility with solvent, separation efficiency |
Membrane Separation | Membrane modules | Membrane type, surface area, pore size |
Safety Considerations
Proper equipment selection and maintenance are crucial for safety. Equipment should be regularly inspected for leaks, damage, and proper functioning. Specific safety precautions must be followed for each method. For instance, proper ventilation is essential during distillation to prevent the accumulation of hazardous vapors.
Safety Considerations
Reducing ethanol percentage, while often beneficial, requires careful consideration of potential hazards. Improper procedures can lead to dangerous situations, ranging from minor irritations to severe health risks. Understanding the potential dangers and implementing robust safety measures is crucial for a safe and successful ethanol reduction process.Proper safety precautions, encompassing personal protective equipment (PPE), controlled environments, and appropriate handling techniques, are paramount.
Adherence to these measures safeguards personnel and the surrounding environment from harm. This section Artikels the critical safety considerations for various ethanol reduction methods.
Potential Hazards of Ethanol Reduction Procedures
Ethanol, while commonly used, can be hazardous if mishandled. Its flammability and potential for toxicity necessitate careful procedures. In reduction processes, the presence of other chemicals or byproducts can further amplify the risks. Improper handling or inadequate ventilation can lead to inhalation, skin contact, or eye irritation. Spills or leaks can create flammable environments, increasing the risk of fire or explosion.
Safety Measures to Minimize Risks
Implementing stringent safety measures is essential to mitigate the risks associated with ethanol reduction. These measures include proper ventilation, appropriate personal protective equipment (PPE), and controlled procedures. Regular maintenance of equipment and adherence to safety protocols are critical to minimize the likelihood of accidents. Safety training for personnel is paramount to ensure awareness and proper handling of potential hazards.
Comprehensive List of Safety Precautions
- Always work in a well-ventilated area. Adequate ventilation prevents the accumulation of harmful vapors and gases.
- Wear appropriate personal protective equipment (PPE), including gloves, eye protection, and a respirator if necessary. The specific PPE required will depend on the specific reduction method and the chemicals involved.
- Store ethanol and other chemicals in designated, properly labeled containers. Proper labeling is crucial for identification and safe handling.
- Avoid open flames or sparks in the vicinity of ethanol or any chemicals involved in the reduction process. This precaution is essential to prevent fire or explosion hazards.
- Never mix chemicals without proper instruction or guidance from a qualified professional. Uncontrolled reactions can release harmful vapors or create hazardous situations.
- Handle glassware and equipment with care to prevent breakage. Broken glass can lead to cuts or injuries.
- Immediately report any spills or leaks to the appropriate personnel. Prompt action can prevent the spread of hazardous materials and limit potential harm.
- Follow all safety guidelines and protocols provided by the manufacturer or supplier of the chemicals and equipment used.
- Maintain a clean and organized workspace to minimize the risk of accidents.
Safety Procedures for Different Ethanol Reduction Methods
Reduction Method | Safety Procedure |
---|---|
Distillation | Use a properly designed and maintained distillation apparatus. Ensure proper ventilation and adequate cooling systems. Wear appropriate PPE. |
Absorption | Ensure proper containment for the absorbent material. Employ adequate ventilation to prevent the accumulation of vapors. Wear gloves and eye protection. |
Chemical Reaction | Strictly adhere to the reaction protocol. Use appropriate reaction vessels and equipment. Employ appropriate ventilation and handle chemicals carefully. |
Appropriate Personal Protective Equipment (PPE)
Appropriate PPE is crucial to protect personnel from exposure to potential hazards. The specific PPE required will depend on the method of ethanol reduction and the chemicals involved. For example, when dealing with potentially corrosive materials, full body suits, chemical resistant gloves, and full face shields might be necessary. For tasks involving flammable vapors, flame-resistant clothing and safety goggles are essential.
Alternative Solutions
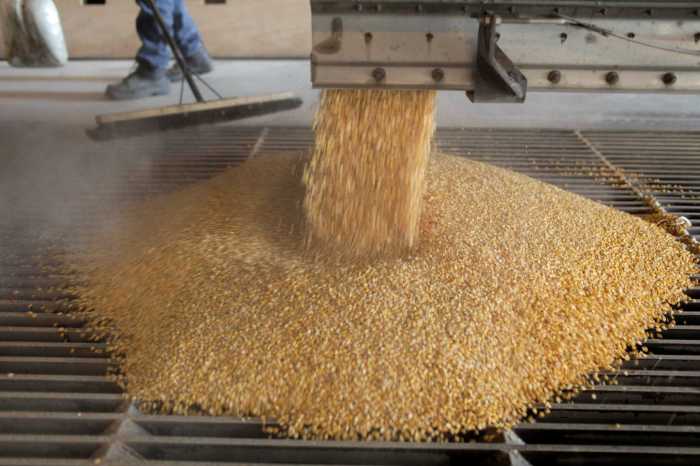
Beyond traditional methods of reducing ethanol percentage, innovative approaches offer compelling alternatives. These strategies, while sometimes less widely adopted, hold potential benefits in terms of efficiency, cost, and environmental impact. Understanding their feasibility and practicality is crucial for a comprehensive approach to ethanol management.
Exploring Alternative Solvents
Various solvents can effectively replace or reduce the concentration of ethanol in a given mixture. The choice depends on the specific application and the desired outcome. A key consideration is the compatibility of the alternative with the existing components and the overall process.
- Isopropyl Alcohol (IPA): IPA is a common alternative, exhibiting similar properties to ethanol in some applications. However, its higher toxicity and potential flammability necessitate careful handling and adherence to safety protocols. Its cost-effectiveness and readily available nature often make it an attractive option, but the environmental impact of IPA production and disposal needs careful assessment.
- Water: Diluting with water is a straightforward and frequently used method. It effectively reduces the ethanol percentage. The environmental impact is minimal as water is readily available and biodegradable. However, its effectiveness depends on the specific properties of the mixture and the desired ethanol concentration.
- Other Organic Solvents: A wider range of organic solvents can be used, but their suitability depends on the specific application. Factors like volatility, toxicity, and cost play a significant role in the selection process. The environmental impact of these solvents varies greatly depending on their chemical composition and disposal methods. Detailed analysis is required to ensure responsible usage.
Evaluating Environmental Impact
The environmental impact of alternative solutions is a critical factor. The production, use, and disposal of various substances all have different environmental footprints. For instance, the production of some solvents may require significant energy and generate harmful emissions. Proper disposal methods are crucial to minimize environmental contamination. Careful evaluation of the life cycle of each alternative is essential for a responsible approach.
- Carbon Footprint Analysis: Analyzing the entire life cycle of a solvent, from production to disposal, is critical. This comprehensive approach includes energy consumption, emissions, and waste generation. Comparing the carbon footprint of different alternatives helps identify the most environmentally friendly options.
- Waste Management Strategies: The disposal of waste generated from the reduction process should be managed responsibly. Recycling, incineration, or other appropriate disposal methods can significantly minimize the environmental impact. A proper waste management plan is vital for sustainable operations.
- Sustainable Practices: Implementing sustainable practices throughout the process, including using renewable energy sources, reducing waste, and promoting responsible disposal, can significantly lower the environmental footprint of ethanol reduction. Continuous monitoring and optimization are necessary to maintain sustainability.
Comparative Analysis of Ethanol Reduction Methods
The table below offers a comparative overview of traditional ethanol reduction methods and alternative solutions, highlighting key factors like cost, efficiency, and environmental impact.
Factor | Traditional Ethanol Reduction | Alternative Solutions (e.g., Water Dilution) | Alternative Solutions (e.g., Isopropyl Alcohol) |
---|---|---|---|
Cost | Moderate | Low | Variable |
Efficiency | High | High | Variable |
Environmental Impact | Moderate | Low | Moderate to High |
Safety | Moderate | Moderate | High |
Compatibility | High | High | Variable |
Specific Cases and Scenarios
Navigating the complexities of ethanol reduction often requires a tailored approach. Different applications demand varying degrees of precision and methods. Understanding the specific circumstances, from industrial processes to laboratory experiments, is crucial for effective ethanol percentage manipulation. This section explores key scenarios where lowering ethanol content is vital, along with the specific techniques and challenges involved.
Industrial Fuel Blends
Industrial fuel blends often necessitate precise ethanol reduction. Fluctuations in ethanol levels can affect fuel performance and compatibility with various machinery. For example, certain engines or industrial equipment may not tolerate high ethanol concentrations. The desired ethanol percentage in a fuel blend can vary significantly based on the intended application.
- Engine Compatibility: Diesel engines, for instance, might exhibit decreased performance or damage if the ethanol content in the fuel surpasses a certain threshold. Careful monitoring and reduction techniques are crucial to ensure consistent engine operation.
- Storage Stability: High ethanol content can affect the long-term stability of fuel blends, leading to potential separation or precipitation of components. Maintaining the desired ethanol percentage can enhance the shelf life and usability of fuel blends. Lowering ethanol levels may improve the storage stability of the fuel blend.
- Regulatory Compliance: Various regions have specific regulations governing the ethanol content in fuels. Meeting these standards necessitates precise ethanol reduction strategies.
Laboratory Experiments
In controlled laboratory settings, precise ethanol reduction is essential for various analytical techniques. The concentration of ethanol must be meticulously maintained to achieve accurate results. For instance, in chemical reactions, the presence of a specific ethanol concentration is often a critical factor for success.
- Titration Analysis: Ethanol concentration determination through titration often requires the use of a standardized ethanol solution. Adjusting the ethanol concentration through controlled dilution is a common practice.
- Spectroscopic Measurements: Spectroscopic techniques, such as UV-Vis spectroscopy, rely on accurate ethanol concentrations for proper interpretation of results. Maintaining the exact ethanol concentration is essential to ensure reliable data acquisition.
- Biochemistry Experiments: Many biochemical reactions involve the use of specific ethanol concentrations. Maintaining the desired ethanol level is vital to ensuring the accuracy and reproducibility of the experiment.
Beverage Production
Precise ethanol reduction is a key aspect of beverage production. The desired ethanol percentage in beverages, from spirits to wines, can vary considerably depending on the type of product.
- Wine Production: Maintaining the desired ethanol percentage in wine is crucial to its taste and quality. Careful monitoring and reduction techniques are often employed to achieve the optimal ethanol concentration.
- Spirits Distillation: The ethanol content in spirits is a key factor in their taste profile. Distillation methods, combined with other techniques, are utilized to control and adjust the ethanol concentration to the desired level.
Table: Scenarios and Associated Challenges
Scenario | Challenges | Effective Methods |
---|---|---|
Industrial Fuel Blends | Engine compatibility, storage stability, regulatory compliance | Dilution, distillation, extraction |
Laboratory Experiments | Accuracy, reproducibility, specific concentration requirements | Dilution, evaporation, distillation |
Beverage Production | Desired taste profile, specific regulations | Dilution, distillation, fermentation adjustments |
Final Wrap-Up
In conclusion, effectively lowering ethanol percentage requires a thorough understanding of the specific application, the available methods, and the potential challenges. By carefully considering the factors affecting ethanol reduction and adhering to strict safety protocols, individuals and organizations can achieve desired results while mitigating risks. This guide has provided a roadmap for navigating this process, equipping readers with the necessary knowledge to confidently address ethanol reduction needs in a variety of contexts.
Clarifying Questions
What are the most common methods for reducing ethanol concentration in fuel?
Several methods exist, including distillation, absorption, and membrane separation. The most suitable method depends on factors such as the specific fuel type, desired ethanol percentage, and available resources.
What are the safety precautions when working with ethanol reduction equipment?
Always prioritize safety. Ensure proper ventilation, use appropriate personal protective equipment (PPE), and follow manufacturer instructions meticulously. Proper handling and storage of chemicals are paramount.
How does temperature impact ethanol reduction processes?
Temperature significantly affects the efficiency of various ethanol reduction methods. For example, higher temperatures can sometimes accelerate certain separation processes, but improper temperature control can also lead to adverse outcomes.
What are some alternative solutions to lowering ethanol percentage?
Alternative solutions may involve using different types of alcohols or blending with other substances to modify the overall composition. However, the feasibility of alternatives hinges on factors such as cost, availability, and environmental impact.