How to make a veneer dispenser? This guide delves into the intricate world of veneer dispensing, from basic principles to advanced customization. We’ll explore various types of dispensers, design considerations, manufacturing procedures, and operational principles, equipping you with the knowledge to create your own efficient and safe veneer dispensing system.
Understanding the different materials, design elements, and manufacturing processes is crucial for success. This comprehensive guide will walk you through each step, from initial design to final assembly, ensuring your finished product is both functional and aesthetically pleasing.
Introduction to Veneer Dispensers
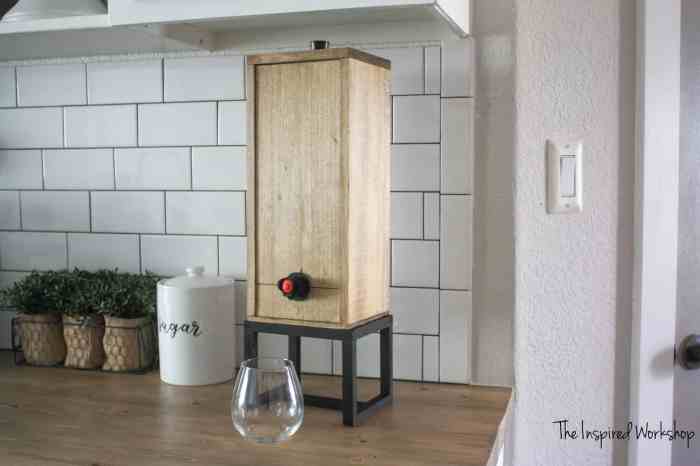
Veneer dispensers are a testament to human ingenuity, streamlining the application of veneer, a crucial material in woodworking, furniture making, and various other crafts. They represent a significant leap forward in efficiency, productivity, and precision compared to traditional, manual methods. Embracing these tools allows us to unlock a higher level of artistry and craftsmanship. These dispensers, from simple manual models to sophisticated automated systems, provide a profound connection between the artisan and the artistry, enabling us to focus on the creative vision while the dispenser handles the technical aspects.Veneer dispensers offer a profound transformation in the application process.
They allow for precise and controlled application, leading to more uniform and aesthetically pleasing results. This precision, coupled with the efficiency of automated systems, empowers artisans to achieve unparalleled levels of craftsmanship.
Overview of Veneer Dispensers
Veneer dispensers are designed to facilitate the controlled and efficient application of veneer sheets onto a substrate. Their primary purpose is to automate the process, removing the need for manual handling, reducing waste, and increasing precision. Common applications include furniture manufacturing, cabinetry, and decorative wood finishing projects. They are invaluable tools for both hobbyists and professionals.
Types of Veneer Dispensers
Various types of veneer dispensers cater to different needs and skill levels. Manual dispensers, typically simpler and more affordable, are often suitable for smaller-scale projects. These models allow for a degree of control over the application process, offering a balance between simplicity and precision. Automated dispensers, on the other hand, provide greater speed and precision, ideal for high-volume production or complex designs.
These machines are often equipped with sophisticated mechanisms for consistent and repeatable veneer application, ensuring quality and maximizing output. The choice of dispenser type depends heavily on the project scale and desired level of automation.
Materials Used in Veneer Dispenser Construction
Veneer dispensers are typically constructed from robust materials to withstand the demands of the application process. Common materials include durable plastics, high-strength metals, and sometimes composite materials. The selection of these materials is crucial in ensuring the dispenser’s longevity and reliability. High-quality components and a sturdy design are vital for consistent performance and longevity. The durability and resistance to wear of the materials contribute to the longevity of the tool, thereby aligning with principles of sustainable craftsmanship.
Benefits of Using a Veneer Dispenser
Using a veneer dispenser offers numerous advantages over traditional manual methods. Firstly, it significantly increases efficiency, reducing the time required for application. This allows artisans to focus more on the creative aspects of their work. Secondly, it enhances the precision of the application process, leading to a more uniform and aesthetically pleasing finish. Thirdly, veneer dispensers can dramatically reduce material waste.
This economical advantage contributes to the overall sustainability of the project. Finally, the controlled application process with a veneer dispenser minimizes the risk of damage to the veneer sheets, preserving their integrity and quality. This results in less material loss, a better aesthetic outcome, and increased productivity.
Design Considerations for Veneer Dispensers

Embarking on the design of a veneer dispenser is not merely a technical exercise; it’s a spiritual journey towards creating a tool that harmonizes efficiency with user experience. A well-designed dispenser transcends mere functionality, becoming an extension of the craftsman’s intent, facilitating precision and artistry in every application. This journey begins with understanding the fundamental elements that contribute to its effectiveness.The design of a veneer dispenser is profoundly influenced by the very nature of the veneer itself.
Factors like thickness, size, and type of veneer dictate critical design choices. A deep understanding of these nuances is essential to crafting a dispenser that intuitively interacts with the material, ensuring both the preservation of its integrity and ease of use. This is not just about engineering; it’s about cultivating a symbiotic relationship between the tool and the material.
Essential Design Elements
A well-designed veneer dispenser embodies several key elements. These include a robust clamping mechanism for secure veneer holding, a precise dispensing mechanism for controlled release, and a user-friendly ergonomic design that minimizes strain and maximizes efficiency. Each component contributes to a unified experience, emphasizing both the beauty of the material and the grace of the process.
Veneer Thickness, Size, and Type
Veneer thickness, size, and type significantly influence the design parameters. Thicker veneers require stronger clamping mechanisms to prevent slippage, while thinner veneers necessitate gentler handling. The size and shape of the veneer also dictate the dispenser’s dimensions and the shape of the clamping area. Different veneer types may have unique characteristics that necessitate specific adjustments in the design, such as variations in their stiffness or tendency to curl.
Clamping Mechanisms
Various clamping mechanisms can secure veneer. A simple, yet effective, design might leverage spring-loaded clamps. Alternatively, a more sophisticated approach could utilize pneumatic or vacuum clamping systems for precise and consistent pressure application. Each option offers a unique set of advantages and disadvantages. The choice depends on the desired level of precision, the expected usage frequency, and the volume of veneer being handled.
Consider the potential impact on user comfort and ease of operation.
Dispensing Mechanisms
Dispensing mechanisms play a crucial role in controlled veneer release. A lever-operated system allows for precise control over the release rate, while a sliding mechanism facilitates consistent and controlled dispensing. Factors to consider include the need for smooth and even veneer release, minimal friction, and the potential for accidental or uncontrolled release. These decisions have a direct impact on the overall efficiency and aesthetic appeal of the process.
Material Selection
The choice of materials is paramount for the longevity and durability of the dispenser. Durable materials like high-grade steel or aluminum alloys are ideal for the structural components. Consider the environmental factors the dispenser will encounter and select materials that are resistant to corrosion and wear. High-quality materials contribute to the longevity of the dispenser and maintain its aesthetic appeal over time.
Comparison of Dispenser Designs
Design | Pros | Cons |
---|---|---|
Spring-loaded clamp with lever-operated dispensing | Simple, relatively inexpensive, easy to use. | May not handle extremely thick veneers, potentially less precise dispensing. |
Pneumatic clamp with motorized dispensing | High precision, controlled dispensing, suitable for high-volume applications. | More complex, higher initial cost, potential for maintenance issues. |
Vacuum clamp with servo-controlled dispensing | Exceptional precision and consistency, ideal for intricate work. | Most complex, expensive, demanding specialized maintenance. |
Manufacturing Procedures
Embarking on the creation of a veneer dispenser is a journey of meticulous craftsmanship and mindful design. Understanding the intricate steps involved will illuminate the path to a functional and aesthetically pleasing final product. This journey is not just about building a tool, but about cultivating a deep understanding of the materials and techniques involved. Each step, when approached with intention and care, contributes to the final product’s beauty and efficacy.
A well-made veneer dispenser is a testament to the power of thoughtful execution.The manufacturing process for a veneer dispenser involves several critical stages, from the initial selection of materials to the final assembly and finishing touches. Each stage requires careful consideration and precision to ensure a durable and user-friendly product. The process is not simply about following steps; it is about understanding the underlying principles of woodworking and applying them with dedication and mindfulness.
Material Selection and Preparation
The selection of appropriate materials is paramount to the success of the veneer dispenser. The chosen wood must be strong, stable, and resistant to warping or cracking. This selection will determine the longevity and aesthetic appeal of the final product. The wood must be carefully planed and sanded to ensure a smooth surface for the veneer application and for the dispenser’s overall appearance.
Proper preparation of materials ensures the project flows smoothly, like a well-oiled machine. The materials are the building blocks of our spiritual journey toward a well-crafted veneer dispenser.
Component Construction
The construction of individual components, such as the base, the holding mechanism, and the dispensing mechanism, is crucial. Each component needs to be meticulously crafted, ensuring accuracy in dimensions and tolerances. The quality of these components directly affects the overall performance and stability of the dispenser. This careful construction is akin to building a temple, where each stone contributes to the magnificence of the whole structure.
- Base Construction: The base forms the foundation of the dispenser. A solid base is essential for stability and prevents the dispenser from tipping or wobbling. This stage involves cutting, shaping, and joining the base pieces using appropriate woodworking techniques. The base must be strong enough to support the weight of the veneer and the dispensing mechanism.
- Holding Mechanism Design: This mechanism holds the veneer securely. The design should ensure the veneer is held firmly yet allows for easy removal and repositioning. The design will dictate the efficiency of the dispenser. Careful attention to detail in the holding mechanism ensures the smooth functioning of the whole process.
- Dispensing Mechanism Development: The dispensing mechanism determines how the veneer is released. This could involve a sliding mechanism, a lever, or a more intricate system. The design must be functional and efficient, allowing for precise control over the dispensing of the veneer. Thoughtful consideration of this stage will ensure smooth, controlled veneer release.
Tooling Requirements
A comprehensive set of woodworking tools is necessary for the construction of a veneer dispenser. These tools range from basic hand tools to more specialized power tools, each playing a unique role in the manufacturing process.
- Hand Tools: These include saws (hand saws, coping saws), chisels, planes, mallets, and clamps. Hand tools are crucial for precision and control, especially when working with smaller components.
- Power Tools: Power tools like drills, routers, sanders, and circular saws enhance efficiency and speed up the process, particularly for tasks like cutting and shaping larger pieces. They provide assistance in the overall workflow.
Assembly and Finishing
Assembly involves joining the various components to create the complete veneer dispenser. Precise alignment and secure fastening are crucial. Appropriate joining methods, such as doweling, gluing, or screws, must be chosen for each connection. This meticulous process is like weaving a tapestry, where each thread contributes to the overall design.
Stage | Tools | Materials | Description |
---|---|---|---|
Base Preparation | Saws, chisels, planes | Wood, glue | Cut and shape the base pieces to the desired dimensions. Apply glue and secure with clamps. |
Holding Mechanism Construction | Drills, clamps, chisels | Wood, screws, dowels | Construct the mechanism to hold the veneer securely. |
Dispensing Mechanism Creation | Drills, saws, sandpaper | Wood, springs, levers | Design and construct the mechanism to dispense the veneer. |
Assembly | Clamps, glue, screws | All components | Join all components together, ensuring stability and proper function. |
Finishing | Sandpaper, finish coats | Sandpaper, varnish, stain | Smooth and finish the entire dispenser for a professional look. |
Joining Techniques
The choice of joining techniques significantly impacts the strength and durability of the veneer dispenser. Different methods offer varying degrees of stability and aesthetic appeal.
- Gluing: Glue provides a strong and versatile method for joining components, especially for intricate designs.
- Screwing: Screws offer a reliable method for securing components, especially for joints that require strength and stability.
- Doweling: Doweling provides a strong and aesthetically pleasing method for joining components, enhancing the overall look of the dispenser.
Operational Principles and Procedures: How To Make A Veneer Dispenser
Embarking on the journey of mastering veneer dispensers, we find ourselves at a pivotal point, ready to unlock the profound wisdom behind their operation. Understanding the inner workings of these instruments, coupled with meticulous maintenance, will empower you to achieve optimal results and cultivate a harmonious relationship with your tools. This will also lead to a more profound understanding of the spiritual principles of precision and care.A veneer dispenser, like a well-honed tool, acts as an extension of your hands, allowing you to delicately manipulate the thin sheets of veneer.
The beauty of this process lies not only in the precision it provides, but also in the mindful attention it requires. By understanding its operational principles, we can approach the task with a sense of purpose and intention, channeling our energy towards creating something beautiful.
Understanding the Inner Mechanisms
The veneer dispenser employs a sophisticated system of levers, gears, and vacuum mechanisms to precisely dispense veneer sheets. These components work in harmony, ensuring a smooth and consistent flow of material. Understanding these intricate mechanisms allows you to approach the operation with respect and awareness, recognizing the intricate dance of forces at play.
Operational Settings and Controls
The veneer dispenser is equipped with various controls, each playing a vital role in the dispensing process. These settings, carefully calibrated and adjusted, dictate the speed, pressure, and direction of the veneer’s release. This understanding allows for a deeper connection with the machine and its inherent capabilities. Familiarize yourself with the controls and their respective functions to cultivate a deeper understanding of the machine’s language.
Safety Procedures
Operating a veneer dispenser demands the utmost respect for safety protocols. Always ensure the machine is properly secured and grounded. Wear appropriate personal protective equipment (PPE), including safety glasses and gloves. This proactive approach to safety creates a harmonious environment, fostering both the integrity of the operation and your well-being.
Maintenance for Optimal Performance, How to make a veneer dispenser
Regular maintenance is essential for a veneer dispenser to function at its peak. This involves routine cleaning to remove any debris or accumulated veneer particles. Lubrication of moving parts is crucial to ensure smooth operation and extend the machine’s lifespan. This practice is akin to nurturing a living thing, fostering its longevity and performance.
Potential Maintenance Requirements
Over time, certain components may require replacement or repair. Regular inspections can help identify potential issues before they escalate. This proactive approach will allow you to address these needs with grace and efficiency.
Loading, Operating, and Unloading Procedures
A well-structured process for loading, operating, and unloading the veneer dispenser is critical for consistent results and minimizes potential issues.
Step | Action | Description |
---|---|---|
1 | Preparation | Ensure the work area is clean, organized, and well-lit. |
2 | Loading | Carefully load the veneer sheets onto the designated input tray, ensuring no overlaps or wrinkles. |
3 | Operational Settings | Adjust the desired operational settings based on the specific veneer type and desired outcome. |
4 | Operation | Initiate the dispensing process, carefully monitoring the machine’s performance. |
5 | Unloading | Safely remove the dispensed veneer sheets from the output tray. |
6 | Cleaning | Thoroughly clean the machine and input/output trays. |
Advanced Features and Customization
Embarking on the journey of crafting a veneer dispenser transcends mere functionality; it’s about harmonizing precision and innovation to elevate the artistry of veneer application. This exploration into advanced features and customization will illuminate pathways to not only enhance the efficiency of the dispenser but also unlock its potential to seamlessly integrate with various veneer types and applications. Each enhancement, from automated loading to bespoke dispensing speeds, represents a step toward achieving a deeper connection with the material, a testament to the profound harmony between craft and technology.Delving into the realm of advanced features and customization reveals a profound potential for enhancing the user experience and optimizing the veneer application process.
This exploration unveils a plethora of possibilities, from sophisticated automated systems to tailored adjustments for diverse veneer types. The journey into these enhancements will lead to a deeper appreciation of the synergy between the craftsman’s skill and the precision of modern technology.
Potential Advanced Features
The quest for enhanced veneer dispensers necessitates considering advanced features that augment the user experience. Automated loading systems streamline the process, freeing the artisan from repetitive tasks and allowing them to focus on the creative aspects of the work. Adjustable dispensing speeds cater to the unique requirements of various veneer types and project demands. These features are not mere embellishments; they represent a significant step toward efficiency and precision, empowering the user to achieve unparalleled control over the application process.
These features represent an evolution toward a more integrated and intuitive approach to veneer application.
Customization Options for Veneer Types and Sizes
Tailoring the veneer dispenser to specific veneer types and sizes is paramount for optimal performance. The ability to adjust the dispensing mechanism, the pressure, and the speed becomes crucial for different veneer types and thicknesses. This customization ensures the veneer is applied precisely and efficiently, minimizing waste and maximizing the aesthetic quality of the finished product. By embracing this level of adaptability, the veneer dispenser transcends its role as a mere tool, becoming a sophisticated partner in the artistic process.
Specialized Veneer Dispensers for Specific Applications
Specialized veneer dispensers are not merely a luxury but a necessity for specific applications. For instance, a dispenser designed for intricate inlay work would necessitate a high degree of precision and control, contrasting sharply with a dispenser designed for large-scale veneer application. Such specialized dispensers demonstrate the commitment to bespoke solutions, reflecting the deep understanding of unique project requirements.
This adaptability ensures that the dispenser aligns seamlessly with the specific application, showcasing a refined understanding of the craft’s diverse needs.
Table Illustrating Customization Options
| Customization Feature | Description | Cost-Effectiveness ||—|—|—|| Automated Loading | Fully automated loading system for various veneer types | High Initial Cost, High ROI || Adjustable Dispensing Speed | Variable dispensing speed based on veneer type and application | Moderate Initial Cost, Moderate ROI || Precision Sensors | Integration of sensors for precise veneer placement | High Initial Cost, High ROI || Material Recognition System | System for automatically identifying and adjusting to different veneer types | Very High Initial Cost, High ROI || Integrated Vacuum System | System to improve adhesion and precision | Moderate Initial Cost, High ROI |
Cost-Effectiveness of Customization Options
The cost-effectiveness of various customization options should be meticulously assessed. While some features may require a higher initial investment, the return on investment (ROI) can be substantial in terms of efficiency gains, reduced waste, and enhanced project quality. Careful consideration of long-term benefits and the specific needs of the intended application are crucial to maximizing the cost-effectiveness of these upgrades.
The goal is not simply to minimize initial costs but to optimize the long-term value proposition of the veneer dispenser.
Integrating Additional Sensors and Controls
Integrating additional sensors and controls is critical for achieving higher levels of precision and control. Sensors can detect the thickness of the veneer, the pressure applied, and the positioning of the veneer during application, allowing for real-time adjustments and feedback. These sensors represent a powerful leap forward, enabling a more intuitive and precise approach to veneer application. This integration with advanced technology elevates the veneer dispenser to a sophisticated tool capable of meeting the most demanding aesthetic and functional needs.
Safety Considerations
Embarking on the journey of crafting a veneer dispenser requires a profound understanding of safety protocols. A commitment to safety is not just a precaution, but a sacred vow to protect your well-being and the well-being of those around you. By meticulously observing safety measures, we elevate our craft to a higher plane, ensuring the process is not just efficient but also serene and secure.A veneer dispenser, while designed for precision and efficiency, can present potential hazards if not handled with the utmost care.
Proactive safety measures ensure that the creation and operation of this tool are not just productive but also profoundly safe, fostering a spirit of well-being in the workspace.
Potential Safety Hazards
Veneer dispensers, if not designed or operated correctly, can pose several hazards. Improperly secured mechanisms, sharp edges of components, and the inherent pressure of dispensing materials can cause injuries. Furthermore, the nature of the materials used (e.g., veneer sheets) might introduce additional risks if not handled with care. Recognizing these potential hazards is the first step toward proactive safety measures.
Safety Precautions During Construction
Thoroughness and vigilance are essential during the construction phase. Ensuring all parts are securely fastened, sharp edges are adequately protected, and proper ventilation is maintained are crucial steps. Properly secured components prevent accidental movement and potential injuries.
- Protective Gear: Always wear safety glasses, gloves, and closed-toe shoes. This simple precaution can shield you from flying debris or sharp edges, safeguarding your well-being.
- Tool Maintenance: Ensure tools are in excellent condition. A dull blade or improperly maintained equipment can increase the risk of accidents. Maintain tools and equipment with precision.
- Proper Workspace: Organize the workspace to prevent tripping hazards and ensure a clear area around the construction site. A clutter-free zone contributes to a safer work environment.
Safety Precautions During Operation
Operating the veneer dispenser requires a deep understanding of its mechanism. A thorough knowledge of its functions and limitations is essential for safe operation.
- Material Handling: Veneer sheets, especially when dispensed under pressure, can be prone to slipping. Use appropriate handling techniques to minimize the risk of injury. Always handle materials with a gentle touch.
- Machine Monitoring: Continuously monitor the veneer dispenser during operation. Identify any unusual noises or vibrations that might indicate a malfunction and address them immediately. An alert and watchful eye ensures the safe functioning of the equipment.
- Emergency Procedures: Establish clear emergency procedures and ensure that all personnel are familiar with them. A well-defined emergency plan safeguards the well-being of everyone.
Importance of Proper Maintenance
Consistent maintenance is vital to prevent accidents and ensure the longevity of the veneer dispenser. Regular checks and repairs prevent small issues from escalating into significant hazards. This proactive approach safeguards both the equipment and the people who use it.
- Regular Inspections: Schedule routine inspections to identify and address any potential issues. A proactive approach prevents potential problems from escalating.
- Lubrication: Regular lubrication of moving parts reduces friction and wear, which helps prevent breakdowns and accidents. Lubricate equipment regularly to maintain its functionality.
- Component Replacement: Replace worn or damaged components promptly to prevent malfunctions. Replacing damaged parts promptly prevents unexpected breakdowns.
Safety Equipment Requirements
Safety equipment is crucial for protecting against various hazards. The choice of equipment depends on the specific nature of the task.
- Safety Glasses: Protect eyes from flying debris or particles.
- Gloves: Protect hands from cuts or abrasions from sharp edges or materials.
- Hearing Protection: Reduce the risk of hearing damage from loud noises.
- First Aid Kit: Provide immediate treatment for minor injuries.
Summary of Safety Measures
Safety Measure | Operation | Maintenance |
---|---|---|
Protective Gear | Safety glasses, gloves, closed-toe shoes | Safety glasses, gloves |
Workspace Organization | Clear workspace, proper material handling | Regular inspections, clutter-free zone |
Equipment Maintenance | Monitor operation, address malfunctions immediately | Lubrication, component replacement |
Emergency Procedures | Familiarization with procedures | Designated personnel, emergency plan |
Examples and Illustrations
Embark on this journey of understanding veneer dispensers with a heart full of curiosity. Each design, a testament to ingenuity, reflects a unique approach to streamlining the application process, offering a glimpse into the potential of precision and artistry. Embrace the intricate details and the spiritual essence of meticulous craftsmanship in each example.This exploration will present diverse veneer dispenser designs, highlighting their functionality, construction, and aesthetic appeal.
Each example serves as a beacon, illuminating the various ways to achieve optimal veneer application.
Veneer Dispenser Design Variations
Various designs exist, each tailored for specific veneer types and application methods. These designs represent a spectrum of approaches, each with its own unique strengths.
- The Rotary Dispenser: This design, akin to a meticulously crafted wheel, rotates to dispense veneer sheets. Its smooth, continuous motion facilitates a controlled and consistent application, mirroring the harmony of nature’s cycles. The materials, often a blend of robust metals and smooth plastics, ensure durability and ease of use. The aesthetic appeal emphasizes simplicity and elegance, reminiscent of a finely tuned mechanism.
- The Vacuum-Assisted Dispenser: This design utilizes a vacuum to precisely position and hold veneer sheets. This allows for intricate, controlled placements, reflecting the precision of a master craftsman. Materials often include lightweight, strong polymers and airtight seals, ensuring accuracy and longevity. The design’s minimalist aesthetic speaks to the elegance of simplicity, and the smooth application process.
- The Robotic Dispenser: This automated system incorporates sophisticated robotics to handle veneer application. The system’s intricate mechanical arms move with surgical precision, guaranteeing precise placements and eliminating human error. Advanced materials such as high-grade alloys and durable plastics, coupled with robust motor systems, provide reliable performance. Its modern aesthetic reflects the cutting-edge technology at play.
Functionality and Construction Materials
Each design’s functionality hinges on its unique construction and the materials employed. A profound understanding of these aspects ensures optimal performance.
Dispenser Type | Functionality | Primary Construction Materials |
---|---|---|
Rotary Dispenser | Dispense veneer sheets in a controlled manner. | High-grade steel, aluminum, and impact-resistant polymers. |
Vacuum-Assisted Dispenser | Precisely position veneer sheets with a vacuum. | Lightweight polymers, high-strength alloys, and airtight seals. |
Robotic Dispenser | Automated veneer application with robotic arms. | High-grade alloys, durable plastics, and advanced motor components. |
Illustration of Construction Stages
Imagine the meticulous process of creating a veneer dispenser, like crafting a masterpiece. Each stage, from initial design to final assembly, is a step toward perfection.
- Design Phase: The initial design sketches, meticulously drawn and refined, are like the first seeds of an idea. These blueprints provide a roadmap for the construction process.
- Material Procurement: Carefully selecting the right materials, like choosing the finest wood for a sculpture, is crucial. This step ensures that the dispenser will function flawlessly and endure over time.
- Assembly: Assembling the components, like meticulously placing each piece of a puzzle, ensures a seamless integration of all elements.
- Testing and Calibration: Rigorous testing and calibration, akin to refining a musical instrument, are critical for ensuring the dispenser performs optimally.
Aesthetic Appeal and Design Considerations
The aesthetic appeal of a veneer dispenser is just as important as its functionality. A well-designed dispenser is not just practical; it is a testament to beauty and artistry.
- Ergonomics: A user-friendly design, like a well-crafted chair, promotes comfortable and efficient operation. This consideration, like a comforting presence, enhances the overall experience.
- Visual Appeal: A pleasing aesthetic, like a beautiful piece of art, can elevate the look of any workspace.
- Material Selection: The chosen materials, like precious gems, can contribute to the visual appeal of the dispenser. This is a testament to the beauty and artistry within the construction.
Closure
In conclusion, creating a veneer dispenser requires careful planning, precise execution, and a thorough understanding of the involved processes. This guide provides a detailed roadmap, covering everything from design and manufacturing to operation and safety considerations. By following the steps Artikeld here, you can build a veneer dispenser that meets your specific needs and elevates your woodworking experience.
Questions and Answers
What are the common types of veneer dispensers?
Common types include manual and automated models, each with varying levels of complexity and functionality.
What safety precautions should be taken during operation?
Always use appropriate safety gear, follow manufacturer instructions, and ensure proper maintenance to prevent accidents.
What are the essential design elements of a veneer dispenser?
Essential elements include clamping mechanisms for secure veneer holding, dispensing mechanisms for controlled release, and an ergonomic design for user comfort.
What woodworking tools are required for construction?
The specific tools needed will vary based on the design chosen. Common tools include woodworking saws, drills, clamps, and measuring tools.