How to measure barrel length? This guide dives deep into the crucial process of accurately determining barrel dimensions, covering everything from basic firearm measurements to advanced techniques used in manufacturing and research. Understanding barrel length is vital for performance, accuracy, and safety, no matter the application. From plumbing pipes to high-powered rifles, precise measurements are key.
We’ll explore the essential tools, methods, and factors influencing accuracy, ensuring you’re equipped to tackle any barrel length measurement task with confidence. We’ll also delve into safety protocols and common troubleshooting steps, empowering you to work safely and effectively.
Introduction to Barrel Length Measurement
Barrel length, a critical dimension in various applications, represents the linear distance from the muzzle to the breech of a barrel. Accurate measurement is paramount for performance, safety, and functionality, ranging from firearms to plumbing. The precision of this measurement impacts crucial aspects like projectile velocity, accuracy, and overall system effectiveness.Accurate barrel length measurement is vital in numerous applications.
In firearms, it directly influences the ballistic performance of projectiles, impacting range, accuracy, and stopping power. In plumbing, precise barrel length is crucial for proper water flow and pressure regulation within pipes. Furthermore, in various industrial applications, accurate barrel length measurement ensures proper functionality and safety of equipment.
Units of Measurement for Barrel Length
Barrel length is typically measured in units of length. The most common units used are inches (in), centimeters (cm), and millimeters (mm). The specific unit employed often depends on the application and regional standards.
Typical Barrel Length Ranges for Different Firearm Types
The following table Artikels typical barrel length ranges for common firearm types. Variations exist based on specific model and manufacturer, but these ranges provide a general guideline.
Firearm Type | Typical Barrel Length Range (inches) |
---|---|
Pistols | 3-5 |
Revolvers | 3-7 |
Rifles (Hunting Rifles) | 20-30 |
Rifles (Assault Rifles) | 16-24 |
Shotguns | 18-36 |
Tools and Equipment for Measurement
Accurate barrel length measurement is crucial for ensuring proper functionality and performance in firearms, artillery, and other applications. This process requires precise tools and equipment, carefully selected to match the intended application and the desired level of accuracy. The correct tools minimize error and contribute to the reliability of the measurement process.Precise measurement techniques rely on specialized tools that provide repeatable and accurate readings.
Different types of tools are suitable for various barrel geometries and measurement requirements. Understanding the characteristics of each tool, including its accuracy and cost, allows for informed selection and optimization of the measurement process.
Essential Tools for Barrel Length Measurement
A range of tools can be employed for accurate barrel length measurement, including but not limited to calipers, micrometers, and laser distance measurement devices. The choice of tool depends on the specific application and the desired level of precision.
Types of Measuring Tools, How to measure barrel length
Several types of measuring tools are employed for barrel length measurement. Each tool offers specific advantages and limitations in terms of accuracy and application.
- Caliper Measurements: Vernier calipers and digital calipers are commonly used for precise linear measurements. Vernier calipers, often used in mechanical workshops and machining, utilize a sliding jaw and a vernier scale for fractional readings. Digital calipers offer the advantage of automatic display, simplifying the reading process and minimizing errors associated with manual reading. Their application is widespread in diverse manufacturing and quality control environments.
- Micrometer Measurements: Micrometers, particularly the outside micrometer, are used for extremely precise measurements, often in situations where high accuracy is paramount. These tools excel in measuring very small dimensions, and the screw mechanism enables accurate and repeatable readings. Their application is crucial in precision engineering and manufacturing where minute variations in dimensions significantly impact functionality.
- Laser Distance Measurement Devices: Laser-based distance measuring tools, often found in construction and surveying, are effective for determining the overall length of the barrel. These tools use light beams to measure the distance, offering a fast and non-contact measurement method. However, their accuracy is influenced by factors like the surface reflectivity and environmental conditions. Laser-based methods are increasingly employed in automated quality control processes for high-throughput applications.
Accuracy and Precision of Measuring Instruments
The accuracy and precision of measuring tools are critical factors in ensuring the reliability of barrel length measurements. Accuracy refers to how close a measurement is to the true value, while precision describes the repeatability of the measurement.
“High precision does not necessarily imply high accuracy. A measuring instrument might consistently provide the same reading, but that reading might be significantly different from the true value.”
Variations in the construction and calibration of measuring tools can affect the accuracy and precision of the measurement. Tools should be regularly calibrated to maintain accuracy and ensure reliable measurements.
Comparison of Measuring Tools
The table below summarizes the accuracy and cost of different measuring tools used for barrel length measurement.
Tool | Accuracy (mm) | Typical Cost ($) |
---|---|---|
Vernier Caliper | 0.02 – 0.05 | 20 – 100 |
Digital Caliper | 0.01 – 0.02 | 50 – 200 |
Micrometer | 0.001 – 0.005 | 100 – 500 |
Laser Distance Meter | 0.5 – 5 (depending on the model) | 100 – 1000 |
Note: Costs are approximate and can vary depending on the brand, features, and specific model.
Methods for Measuring Barrel Length
Accurate barrel length measurement is critical in various applications, from manufacturing quality control to firearm identification. Precise determination ensures proper functionality and safety, especially in firearms. Different methods offer varying degrees of precision and practicality, each with unique advantages and disadvantages.
Direct Measurement Methods
Direct methods involve physically measuring the barrel’s length using a tool calibrated for the task. These methods offer high accuracy but may be impractical or impossible in certain situations.
- Caliper Measurement: A caliper, with its precision jaws, provides a direct reading of the barrel’s length. This method is effective for relatively straight barrels. Calibration of the caliper is crucial for accurate results.
- Rule or Tape Measure: A standard ruler or tape measure can also be used for direct measurement, especially for shorter barrels. Care must be taken to ensure the measuring tool aligns precisely with the barrel’s axis to avoid errors. High accuracy is challenging with this method, depending on the length and complexity of the barrel’s profile.
Indirect Calculation Methods
Indirect methods utilize calculations based on known dimensions or features of the barrel to determine its length. These methods can be useful for complex geometries or when direct measurement is impossible.
- Using a Coordinate Measuring Machine (CMM): A CMM employs precise coordinates to calculate distances. This is valuable for complex shapes or irregularly shaped barrels. The CMM measures points along the barrel’s exterior, and software then calculates the length based on the defined coordinates. Advanced CMMs provide extremely high accuracy.
- Using a Laser Distance Measuring Tool: Laser-based distance tools provide accurate measurements. However, this method often requires special considerations to account for the barrel’s curvature or shape. The laser must be aligned perpendicularly to the barrel’s axis for an accurate reading.
Caliper Measurement Procedure
This method is commonly used for precise measurement of barrel length. The following steps provide a comprehensive guide.
- Safety Precautions: Always prioritize safety. Ensure the barrel is securely held and cannot move during the measurement process. Avoid contact with any sharp edges or components.
- Caliper Selection: Choose a caliper with a suitable measurement range and appropriate precision for the barrel’s length. Ensure the caliper is properly calibrated before use.
- Positioning the Caliper: Carefully position the caliper’s jaws against the barrel’s ends. The jaws should be positioned parallel to the barrel’s axis. Ensure that the caliper’s jaws make consistent contact with the barrel’s exterior, and the caliper’s measuring scale is aligned with the barrel’s axis.
- Reading the Measurement: Read the measurement indicated on the caliper’s scale. Record the value precisely.
- Verification: Repeat the measurement procedure several times to ensure consistency and reduce errors. Any significant variations in the readings should be investigated. Note the measurement units and ensure they are consistent with the expected unit for the barrel length.
Comparison of Methods
Method | Advantages | Disadvantages |
---|---|---|
Direct Measurement (Caliper) | High precision, relatively simple to use | Limited to relatively straight barrels, potential for operator error |
Direct Measurement (Rule/Tape) | Simple and readily available | Lower precision, more prone to error |
Indirect Calculation (CMM) | High precision, suitable for complex shapes | Requires specialized equipment, potentially more complex setup |
Indirect Calculation (Laser) | High precision, contactless measurement | Requires careful alignment, potentially affected by reflective surfaces |
Factors Affecting Barrel Length Measurement Accuracy
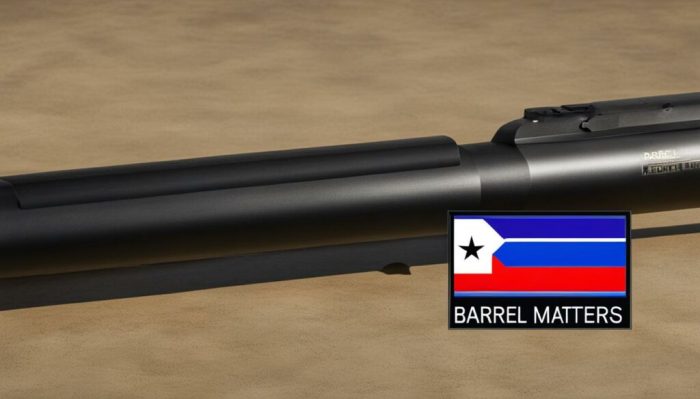
Precise measurement of barrel length is crucial for various applications, from firearm manufacturing to industrial processes. Inaccurate measurements can lead to significant consequences, including safety hazards, production defects, and economic losses. Understanding the factors that influence measurement accuracy is vital for achieving reliable and repeatable results.
Environmental Conditions
Environmental factors significantly impact the accuracy of barrel length measurements. Temperature fluctuations cause metal components to expand or contract, altering the measured length. Similarly, humidity can affect the dimensional stability of the measuring tools, introducing errors.
- Temperature Fluctuations: Changes in ambient temperature directly affect the dimensional properties of the barrel and the measuring instrument. Linear expansion coefficients for different materials vary, thus a temperature change will result in differing dimensional alterations for the barrel and the measuring tool. For example, a 10°C increase in temperature could cause a steel barrel to expand by a few hundredths of a millimeter, leading to a significant error if not accounted for.
Proper temperature control in the measurement environment is essential.
- Humidity Variations: High humidity can lead to moisture absorption in the barrel and measuring instruments, causing dimensional changes. This effect is often less pronounced than temperature changes but can still contribute to measurement error, especially for materials prone to moisture absorption. Control of humidity levels in the measurement environment is recommended.
Material Properties
The inherent characteristics of the barrel material itself can affect measurement accuracy. Variations in the material’s composition and microstructure can influence its dimensional stability. Different manufacturing processes can also induce internal stresses within the barrel, which can affect its measured length.
- Material Composition: Different metals have different coefficients of thermal expansion. Variations in the chemical composition of the barrel material can alter its response to temperature changes. For instance, a barrel made from a steel alloy with a higher carbon content may have a slightly different expansion rate compared to a standard carbon steel barrel.
- Internal Stresses: Manufacturing processes like forging or machining can introduce internal stresses in the barrel. These stresses can cause the barrel to deform slightly, leading to errors in length measurements. Careful consideration of these internal stresses is critical, especially for highly stressed or complex geometries.
Measurement Instrument Factors
The quality and characteristics of the measuring instruments themselves contribute to measurement accuracy. Calibration errors, wear and tear, and limitations of the instrument’s resolution can introduce errors in the measurement process.
- Calibration Errors: The accuracy of a measuring instrument depends on its calibration. If the instrument is not calibrated correctly, the measurements will be inaccurate. Regular calibration checks are essential to ensure the instrument’s accuracy.
- Instrument Wear: Repeated use and wear can affect the precision of the instrument. This includes wear in the measuring mechanism or the physical deformation of the instrument. Regular maintenance and replacement of worn parts are essential to maintain accuracy.
- Resolution Limitations: Each measuring instrument has a limited resolution. This means that it cannot measure lengths smaller than a certain value. Using an instrument with insufficient resolution can result in a loss of precision in the measurement. Choosing the appropriate instrument for the required level of accuracy is critical.
Error Minimization Strategies
Source of Error | Minimization Strategy |
---|---|
Temperature Fluctuations | Maintain a stable and controlled temperature environment during measurement. Use temperature-compensated instruments or correct for temperature variations in the calculations. |
Humidity Variations | Maintain a stable and controlled humidity environment during measurement. Consider using humidity-controlled enclosures for measurements. |
Material Composition Variations | Use well-characterized materials with known thermal expansion properties. Control the manufacturing process to minimize internal stresses. |
Instrument Calibration Errors | Regular calibration of measuring instruments against certified standards. Use traceable calibration certificates for measurements. |
Instrument Wear | Regular maintenance and inspection of measuring instruments. Replace worn parts promptly. |
Instrument Resolution Limitations | Select measuring instruments with appropriate resolution for the application. Employ appropriate measurement techniques to enhance precision. |
Applications of Barrel Length Measurement
Accurate barrel length measurement is critical in various applications, impacting performance characteristics and ensuring safety. The precise determination of barrel length is vital for achieving desired outcomes in fields ranging from firearm manufacturing to scientific research. This section explores the significance of barrel length in different contexts.
Impact on Firearm Performance
Barrel length directly influences firearm performance, impacting accuracy, range, and muzzle velocity. A longer barrel typically results in a higher muzzle velocity, greater accuracy at longer ranges, and a more stable trajectory. Conversely, shorter barrels may be preferred for certain applications, such as handguns, where compactness and maneuverability are paramount.
- Accuracy: A longer barrel provides more time for the projectile to stabilize within the rifling grooves, leading to improved accuracy. This stabilization reduces the effect of imperfections in the projectile or barrel, improving the consistency of the shot pattern.
- Range: Increased barrel length typically translates to a greater effective range. The longer barrel allows for a higher muzzle velocity, which is crucial for maintaining accuracy and impact force at greater distances. The longer barrel also allows for more time for the projectile to stabilize, improving trajectory.
- Muzzle Velocity: The relationship between barrel length and muzzle velocity is often described as directly proportional. A longer barrel allows for a greater acceleration of the projectile down the barrel, resulting in a higher muzzle velocity. Higher muzzle velocities enhance the kinetic energy of the projectile, potentially increasing its destructive power. This is especially significant in applications like hunting and military engagements.
Barrel Length in Manufacturing
Accurate barrel length measurement is critical in the manufacturing process. Variations in barrel length can affect the functionality and safety of the firearm.
- Consistency: Maintaining consistent barrel lengths is crucial in mass production. Deviation from the intended length can result in sub-optimal performance or safety issues, making quality control procedures critical.
- Caliber Compatibility: Barrel length must be precisely matched to the intended caliber. Mismatched lengths can lead to malfunctions or dangerous scenarios. Precise measurement ensures that the barrel and cartridge are compatible for safe and effective operation.
- Safety Standards: Compliance with safety standards mandates accurate barrel length measurements to ensure that the firearm meets the required specifications. This is crucial for preventing accidents and injuries during usage.
Barrel Length in Research and Development
In research and development, precise barrel length measurement is essential for studying projectile dynamics and optimizing firearm designs.
- Projectile Ballistics: Researchers use precise barrel length measurements to collect data on projectile trajectories, velocities, and impacts. This information aids in the development of improved firearm designs, and in the study of the behavior of ammunition in various conditions.
- Material Science: Analyzing how barrel length affects the performance of different materials is crucial in the development of new materials for firearm barrels. The effects of barrel length on factors like stress distribution and material deformation can be studied, which may improve the durability and longevity of the barrel.
- Gunsmithing: Gunsmiths frequently need to measure barrel lengths to restore or modify firearms. Accurate measurements ensure that the modifications comply with the intended specifications, ensuring the safe and effective operation of the firearm.
Real-World Examples
Accurate barrel length measurement is vital in various real-world scenarios, from firearm manufacturing to scientific research.
- Gunsmithing: Gunsmiths must precisely measure barrel lengths when restoring or modifying firearms to maintain accuracy and safety standards. Modifications to the barrel length can affect the balance and performance of the firearm.
- Manufacturing: Manufacturers of firearms must accurately measure barrel lengths to ensure that the firearms meet required standards and quality control requirements. Inaccurate measurements could lead to a batch of defective firearms. This process is essential to maintaining safety and functionality.
- Ballistics Research: Researchers in ballistics study the impact of barrel length on projectile characteristics. Precise measurement of barrel length is essential for the accuracy and reliability of the data collected. The data from these studies helps in the development of new and improved ammunition designs and firearm configurations.
Troubleshooting and Error Analysis
Accurate barrel length measurement is crucial in various applications, from manufacturing to quality control. However, several factors can introduce errors into the process. Understanding these potential issues and their corresponding solutions is essential for maintaining accuracy and reliability. This section details common problems, corrective actions, and methods for error analysis.
Common Issues and Errors
Several factors can contribute to inaccuracies in barrel length measurements. These include instrument calibration issues, operator error, and environmental conditions. Instrument malfunctions, improper use of measuring tools, and human oversight can all compromise the reliability of the measurements. Understanding these factors allows for proactive strategies to mitigate these errors.
Solutions and Corrective Actions
Addressing the identified issues requires a systematic approach. Calibration checks are paramount to ensure instruments are functioning correctly. Proper training for operators and adherence to standardized procedures reduce human error. Environmental controls, like maintaining stable temperature and humidity, can mitigate the impact of external factors.
- Calibration Issues: Regular calibration of measuring instruments is essential. This involves comparing the instrument’s readings against a known standard, such as a certified ruler or gauge. If discrepancies are found, the instrument should be recalibrated or repaired. Detailed calibration records should be maintained for traceability and accountability.
- Operator Error: Proper training and adherence to established measurement procedures are critical. This includes precise positioning of the barrel and instrument, ensuring accurate readings, and recording measurements meticulously. Operator training should encompass understanding the limitations of the measuring tools and techniques.
- Environmental Factors: Temperature and humidity fluctuations can affect the accuracy of measurements, especially for longer barrels. Maintaining a stable environment during measurement reduces the impact of these factors. Using appropriate measuring tools designed for different conditions is also important.
Error Analysis and Improvement Techniques
Analyzing errors in barrel length measurements involves identifying the sources and magnitudes of these errors. This includes examining the accuracy of the measuring instrument, the consistency of the operator’s technique, and the stability of the environmental conditions. Statistical methods, such as calculating the standard deviation and mean, can be used to quantify the magnitude of errors and assess the overall precision of the measurement process.
Troubleshooting Guide
Possible Problem | Solution |
---|---|
Instrument not calibrated | Recalibrate the instrument using a certified standard. |
Operator misalignment of the barrel | Ensure proper positioning of the barrel and the measuring tool. Provide operator training. |
Temperature fluctuations | Maintain a stable environment during the measurement process. |
Parallax error | Ensure the measuring device is held perpendicular to the barrel and at the correct distance to avoid parallax. |
Improper use of measuring tool | Use the measuring tool according to its intended use. Ensure proper technique and training for using the specific tool. |
Reading error | Double-check readings. Use multiple measurements and average the results. |
Advanced Measurement Techniques

Advanced techniques for barrel length measurement are crucial for achieving high precision in applications requiring exacting tolerances, such as firearm manufacturing and aerospace engineering. These methods often involve sophisticated instrumentation and data processing, allowing for detailed analysis and identification of subtle variations that might be missed by simpler methods. Such precision is essential for ensuring consistent performance and safety in critical applications.
Laser Scanning
Laser scanning technology offers a non-contact method for acquiring three-dimensional data of a barrel’s surface. This approach is particularly valuable for complex geometries, providing a comprehensive representation of the barrel’s shape. The process typically involves directing a laser beam across the surface, and capturing the reflected light patterns. Sophisticated software then processes these data points to construct a detailed 3D model of the barrel.
- Equipment: High-resolution laser scanners, specialized software for data acquisition and processing, and a stable platform for mounting the barrel are essential components. The choice of laser scanner depends on the desired resolution and the size of the barrel. High-precision scanners with sub-micron accuracy are crucial for demanding applications.
- Procedure: The barrel is meticulously positioned on the scanner’s platform. The laser scanner systematically scans the barrel’s entire surface, recording the distance from the laser to each point on the surface. This data is then processed using dedicated software to create a detailed 3D model.
- Advantages: Laser scanning provides a comprehensive, non-contact measurement of the barrel’s shape, capturing subtle deviations in length and profile. It eliminates the potential for errors introduced by contact measurements, ensuring high accuracy.
- Disadvantages: Laser scanning can be expensive, requiring specialized equipment and software. The complexity of data processing and analysis can be challenging. Precise calibration and careful handling of the barrel during scanning are critical for accuracy.
3D Modeling
D modeling, often integrated with other techniques, allows for virtual representation and measurement of the barrel’s geometry. It involves creating a digital model of the barrel from various data sources, enabling precise calculations of length and other dimensions. The accuracy of the model depends heavily on the quality of the input data.
- Equipment: 3D scanners, CAD (Computer-Aided Design) software, and a stable environment for data acquisition are essential. CAD software allows for manipulating the 3D model to analyze various aspects of the barrel’s geometry.
- Procedure: The barrel is scanned using various methods, such as laser scanning, to generate a point cloud. This point cloud is then processed and used as input for 3D modeling software. The software creates a digital representation of the barrel’s shape, enabling precise calculations of length, diameter, and other features.
- Advantages: 3D modeling allows for a detailed visualization of the barrel’s shape and provides a comprehensive representation for analysis and modification. It allows for virtual experimentation and design changes before physical prototypes are built.
- Disadvantages: Accuracy is dependent on the quality of the input data, which is subject to measurement error from the scanning method. Significant computational resources might be needed for complex models. Detailed understanding of the 3D modeling software and processes is essential for accurate interpretation.
Comparison of Techniques
Technique | Equipment | Accuracy | Cost | Ease of Use | Applications |
---|---|---|---|---|---|
Laser Scanning | High-resolution laser scanners, specialized software | High | High | Moderate | High-precision manufacturing, complex geometries |
3D Modeling | 3D scanners, CAD software | High | Medium to High | Moderate | Design analysis, virtual prototyping |
Basic Methods (e.g., calipers, micrometers) | Simple measuring tools | Lower | Low | High | General inspection, rough estimations |
Safety Considerations During Measurement
Proper safety precautions are paramount during barrel length measurement, particularly when dealing with potentially hazardous materials or equipment. Neglecting these precautions can lead to serious injuries or equipment damage. Adherence to established safety protocols minimizes risks and ensures a secure and productive measurement environment.Ensuring the safety of personnel and the integrity of the measuring equipment is crucial. A comprehensive understanding of potential hazards and appropriate mitigation strategies is essential.
This section details the importance of safe handling procedures for measuring tools and equipment, along with preventative measures to address potential risks.
Safety Protocols for Handling Measuring Tools and Equipment
Implementing standardized safety protocols is vital for personnel working with measuring tools and equipment. These protocols minimize the risk of accidents and ensure a safe work environment.
- Personal Protective Equipment (PPE): Always wear appropriate PPE, such as safety glasses, gloves, and hearing protection, depending on the specific measurement context. This safeguards against potential hazards like flying debris, sharp edges, or loud noises from machinery or equipment.
- Equipment Inspection: Thoroughly inspect all measuring tools and equipment before use. Check for any visible damage, malfunctioning parts, or loose connections. Ensure the equipment is properly calibrated and functioning correctly. Damaged or malfunctioning equipment can lead to inaccurate measurements and potentially hazardous situations.
- Secure Work Area: Maintain a clean and organized work area. Remove any potential tripping hazards and ensure adequate lighting. A secure workspace minimizes the risk of accidents and promotes efficiency in measurement tasks.
- Proper Handling Techniques: Use appropriate handling techniques for measuring tools and equipment. Do not force or misuse any equipment. Following manufacturer instructions and established procedures ensures safe and efficient operations.
- Emergency Procedures: Familiarize yourself with emergency procedures, including evacuation routes, fire extinguishers, and first-aid stations. Having clear emergency procedures in place helps in responding effectively to any unexpected situations.
Potential Hazards and Mitigation Strategies
Understanding potential hazards and implementing appropriate mitigation strategies are crucial for a safe measurement environment. Different measurement contexts may present varying risks.
- Sharp Edges/Moving Parts: Barrels may have sharp edges or moving parts during certain stages of manufacturing or use. Ensure that appropriate personal protective equipment, like safety glasses and gloves, is used. If moving parts are present, ensure the area is properly fenced and protected to prevent accidental contact.
- Compressed Air/High-Pressure Systems: If compressed air or high-pressure systems are involved in the measurement process, appropriate safety measures should be implemented. This may include using pressure gauges, safety valves, and proper ventilation. Compressed air hoses should be secured to prevent accidental displacement or entanglement.
- Electrical Hazards: If electrical equipment is used in the measurement process, follow electrical safety guidelines. Ensure proper grounding, use appropriate voltage ratings, and avoid contact with exposed wires or circuits. Disconnect power sources when not in use or during maintenance.
- Material Handling Risks: Proper handling of barrels, particularly when they contain heavy or hazardous materials, is essential. Utilize appropriate lifting equipment and follow material handling procedures. This minimizes the risk of injuries and ensures the safety of personnel handling barrels.
Ending Remarks
In conclusion, mastering barrel length measurement involves understanding the tools, methods, and factors that impact accuracy. This comprehensive guide provides a thorough overview of the process, equipping you with the knowledge to confidently measure barrels for a variety of applications. Remember safety is paramount, and precision is key for achieving desired results. Now you’re equipped to tackle any barrel length measurement with confidence!
FAQ Section: How To Measure Barrel Length
What are the most common units for measuring barrel length?
Inches and centimeters are the most common units for measuring barrel length. Other units might be used in specific contexts.
What is the difference between direct and indirect methods of measuring barrel length?
Direct methods involve using a measuring tool to directly measure the barrel length, while indirect methods use calculations based on other measurements.
How does temperature affect barrel length measurement?
Temperature changes can affect the expansion and contraction of materials, leading to slight variations in measured barrel length. Using a tool that accounts for temperature fluctuations is crucial for precise results.
What are some common errors when measuring barrel length?
Common errors include incorrect tool use, parallax error, and inaccurate readings due to environmental factors. Careful attention to detail and proper technique minimizes these errors.