How to replace shifting cable? This ain’t no easy feat, but we’re breaking it down for you, fam. From cars to motorcycles, understanding how these cables work and what to do when they go kaput is key. This guide is your one-stop shop for everything you need to know about replacing those vital shifting cables.
Replacing a shifting cable can seem daunting, but with the right tools and a step-by-step approach, it’s totally doable. We’ll cover everything from the basics of shifting cables to advanced troubleshooting techniques, ensuring you’re equipped to tackle this repair like a pro.
Introduction to Shifting Cables
Shifting cables are the vital conduits that link your vehicle’s gearbox to the gear selector, allowing you to smoothly transition between gears. From the zippy little sports car to the hulking lorry on the motorway, these cables are crucial for the smooth operation of the transmission system. Without them, you’re stuck in a single gear, potentially causing a catastrophic mechanical failure.
They’re a fundamental part of the drivetrain, enabling everything from delicate downshifts in a sports car to the powerful gear changes in a truck.
Function of Shifting Cables
Shifting cables transmit the force from the gear selector to the internal mechanisms of the gearbox. This allows the driver to engage different gears, enabling the engine to work at optimum efficiency. The cable’s precise movement translates to the correct gear engagement within the transmission. Without this crucial connection, your vehicle wouldn’t be able to change gears at all, rendering it useless.
Modern vehicles often use more complex systems, but the basic principle remains the same: a controlled movement of the cable directly impacts the transmission.
Signs a Shifting Cable Needs Replacement
Several telltale signs can indicate that your shifting cable is on its last legs. Rough or inconsistent gear changes are a common symptom. You might find that gears are difficult to select, or that they ‘catch’ or ‘skip’ during shifting. A noticeable “clunk” or “grind” when shifting can be a clear indicator of wear and tear. This is because the cable may be frayed or stretched, and not moving the linkage properly.
Another symptom is a general loss of power, which could stem from an issue with the transmission’s internal mechanisms being affected by a malfunctioning cable.
Types of Shifting Cables
Different vehicle types and manufacturers employ various cable types, each with its own advantages and disadvantages. The choice often depends on factors such as cost, durability, and the specific requirements of the vehicle’s transmission system.
Cable Type | Material | Pros | Cons |
---|---|---|---|
Metal Cable | Steel or similar metal alloys | High tensile strength, durable, often reliable in heavy-duty applications. | Can be heavier, more prone to rust, and may require more maintenance over time. |
Plastic Cable | High-strength polymers | Lightweight, corrosion-resistant, generally lower maintenance. | Lower tensile strength, may be less reliable in high-stress applications. More prone to damage. |
This table highlights the key differences between metal and plastic shifting cables, offering a quick comparison of their properties. The choice between these materials depends heavily on the specific application and the vehicle’s operating conditions.
Tools and Materials Needed
Right, so you’re tryna replace a shifting cable? First things first, you need the right kit. This ain’t rocket science, but you gotta have the right tools and materials to avoid any dramas. Improper tools can lead to more hassle and potential damage.
Essential Tools
This section Artikels the vital tools needed for a smooth cable replacement. Having the right kit prevents unnecessary headaches and ensures a tidy job.
Tool Name | Description | Image Description |
---|---|---|
Cable Cutter | A specialised tool for precisely cutting cables without damaging them. Essential for removing the old cable cleanly. | A hand-held tool with a sharp, angled blade, designed for cable cutting. |
Cable Stripper | Used for removing the outer jacket of the cable, exposing the inner wires for splicing. | A tool with a set of jaws or blades for gripping and stripping the cable jacket. |
Screwdrivers (various sizes) | Essential for adjusting or removing components related to the shifting mechanism. | A set of screwdrivers, including Phillips and flathead types, in different sizes. |
Pliers (needle-nose, slip-joint) | Handy for gripping small parts, adjusting cable clamps, or bending cable ends. | Two types of pliers: needle-nose for precision gripping and slip-joint for a wider range of jobs. |
Cable Clamp Set | Ensures the new cable is secured correctly to the shifting mechanism. | A set of cable clamps, designed for securing the cable to various components. |
Cable End Splicing Tool | Provides precise and neat splicing of cable ends for a secure connection. | A tool with multiple blades and sections to ensure proper alignment and secure splicing of the cable ends. |
Torque Wrench | Needed for tightening bolts and screws with the right amount of force, preventing damage or misalignment. | A tool with a dial to measure torque and a handle for tightening components. |
Bike Stand | A sturdy stand to keep the bike securely in place while working on it. | A bicycle stand that provides a stable support for the bike during maintenance. |
Materials
These bits and bobs are equally vital for a smooth repair. Without ’em, you’re screwed.
- New Shifting Cable
- Cable Lubricant (bike specific)
- Cable Clips (or cable ties)
- Cable end ferrules (if needed)
- Grease (if required)
Safety Gear
Safety first, right? These are essential for a safe and successful repair. Ignoring these can lead to injury.
- Work Gloves
- Safety Glasses/Eye Protection
Step-by-Step Replacement Procedure
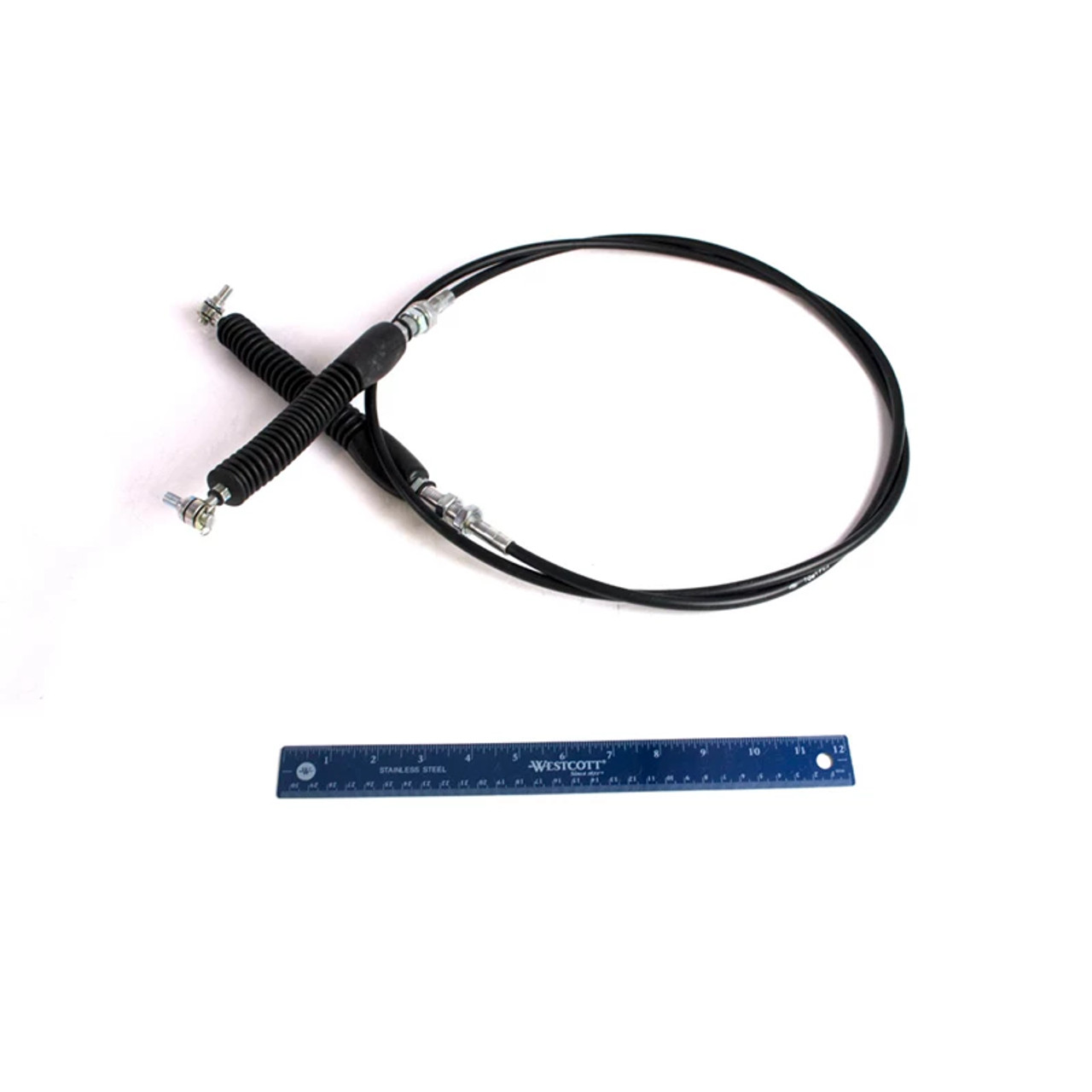
Right, so you’ve got a dodgy shifting cable, eh? Replacing it’s not rocket science, but precision is key. Follow these steps to get it sorted. Think of it as a bit of a mechanical puzzle, and you’ll nail it.
Removing the Old Shifting Cable
Before you start tearing things apart, make sure you’ve got the right tools and the new cable ready. This section Artikels the removal process. Carefulness is paramount to avoid damaging surrounding components.
Step | Description | Image Description |
---|---|---|
1 | Locate the cable entry points on the shifter and the derailleur. Identify any cable housing clamps or fasteners. | A close-up view of the derailleur and shifter, highlighting the cable entry points and any visible cable housing clamps. |
2 | Carefully loosen and remove any cable housing clamps or fasteners. Use the appropriate tools, like pliers or a cable housing clamp remover. | The same view as step 1, but now showing the tools being used to remove the cable housing clamps. Pliers or a cable housing clamp remover are clearly visible. |
3 | Gently pull the old cable out of the housing, working from the shifter end first. Be mindful of any potential kinks or bends in the cable. | A view of the cable housing, showing the old cable being carefully extracted from the housing. Any bends or kinks are highlighted. |
4 | Once the cable is completely removed, carefully disconnect any cable end caps or ferrules. | A close-up of the cable ends, showing the end caps or ferrules being carefully disconnected from the cable. |
Inspecting the Old Cable
A quick visual check can save you a lot of hassle. Look for obvious damage like cuts, kinks, or fraying. If it’s got a history of problems, you might want to consider upgrading to a more robust cable.
- Visual inspection: Check the cable for any signs of damage, including cuts, kinks, or fraying. A damaged cable will likely need replacement, no matter how minor the issue seems.
- Functionality assessment: Does the cable feel stiff or sluggish? Is there any noticeable friction when pulling it? A stiff or sluggish cable will need replacement, as this indicates potential internal wear.
Installing the New Shifting Cable, How to replace shifting cable
Now, let’s get the new cable installed. This is largely the reverse of the removal process. Pay attention to the correct routing for optimal shifting performance.
- Thread the new cable through the housing, ensuring it’s smooth and free of kinks. The cable should glide easily.
- Carefully re-attach the cable end caps or ferrules to the cable ends, ensuring a secure fit. Tighten the ferrules appropriately to prevent damage.
- Route the new cable through the housing, making sure it aligns with the original path. This will ensure smooth shifting.
- Reinstall the cable housing clamps or fasteners, ensuring they are properly tightened. This is critical for cable stability and longevity.
Testing the New Cable
Now, time to test your handiwork. Make sure the new cable shifts smoothly and efficiently through the entire range of gears. This final step is essential to ensure a proper replacement.
- Gear shifting: Check the shifting function across all gears to confirm smooth and precise transitions. Any issues should be addressed immediately.
- Friction check: Assess for any friction or sticking points during shifting. If any issues are noted, re-route the cable or adjust the housing for optimal performance.
- Durability check: Give the cable a few test shifts over time to ensure that it remains reliable and durable. This step will give you a clear idea of its long-term performance.
Troubleshooting Common Issues
Right, so you’ve got your shifting cables sorted, but things can go pear-shaped. Knowing the potential pitfalls and how to fix ’em is key to a smooth repair. This section will cover common problems, their causes, and how to diagnose and resolve them.Understanding the potential hiccups during the cable replacement process can save you a ton of time and frustration.
By anticipating possible issues, you can quickly identify and address them, avoiding a complete rebuild. Proper troubleshooting is crucial for a successful repair.
Potential Problems During Replacement
Common issues during shifting cable replacement include incorrect cable routing, damaged housing, or seizing cables. Proper cable routing is paramount to ensure smooth shifting action.
- Incorrect Cable Routing: Improper routing can lead to cable binding or interference with other components. This can cause the cable to rub against parts of the bike, or kink. This results in a rough, clunky shifting experience. Double-check the routing diagrams, or ask a mate who knows their bikes inside and out. Correct routing ensures the cable runs smoothly through its designated path.
- Damaged Housing: A damaged cable housing can cause friction, leading to stiff shifting or cable breakage. Check for cracks, tears, or any signs of wear and tear. Replacing the housing or cable itself might be needed, depending on the extent of the damage. Replacing the housing prevents further damage.
- Seized Cables: If the cables are seized, they won’t move smoothly through the housing. This can be caused by corrosion, or just plain neglect. Lubricating the cables and housing with a proper lubricant, like bike cable lube, can often resolve this problem. Make sure the cable is lubricated throughout the entire length of the cable.
Common Causes of Shifting Cable Failure
Cable failure can stem from various factors, including wear and tear, corrosion, or improper lubrication. These factors contribute to a less-than-ideal shifting experience.
- Wear and Tear: Over time, the cables and housing wear out, leading to increased friction and stiffness. Regular maintenance and replacement are vital to keep the shifting system in tip-top shape. Routine checks for wear are crucial for longevity.
- Corrosion: Moisture and environmental factors can cause corrosion, which can seize the cables and make them less effective. Protecting the cables from moisture can prevent this issue. Consider using a waterproof casing if the environment is particularly harsh.
- Improper Lubrication: Insufficient or incorrect lubrication can lead to cable sticking and binding. Using the right lubricant for the cable type is essential. The right lubricant ensures smooth shifting. Choosing the wrong lubricant can cause problems down the line.
Troubleshooting Table
This table summarizes potential issues, their causes, and corresponding solutions.
Issue | Cause | Remedy |
---|---|---|
Stiff Shifting | Incorrect routing, damaged housing, seized cables, or wear and tear | Check routing, replace housing, lubricate cables, or replace cables. |
Cable Breakage | Excessive stress on the cable, sharp bends, or damaged housing | Inspect for stress points, ensure smooth bends, replace damaged housing, or use reinforced cable. |
Rough Shifting | Seized cables, corrosion, improper lubrication, or wear and tear | Lubricate cables, use a cable lubricant, replace cables, or clean the cable housing. |
Vehicle Specific Shifting Cable Replacements
Right, so we’ve covered the basics, now let’s drill down into the specifics for different vehicles. Knowing the nuances of each platform is crucial for a smooth swap. Different vehicles have different cable routing, access points, and tools needed, so nailing the right procedure is key to avoid any nasty surprises.
Car Shifting Cable Replacement
This procedure assumes a standard car setup with a cable-operated manual transmission. First, you’ll need to safely support the vehicle using jack stands. Then, locate the cable’s access point, usually behind the transmission or under the dashboard. Carefully disconnect the cable from the transmission linkage and the shift lever. Use the right tools to remove any retaining clips or clamps.
Next, inspect the old cable for wear and tear. A worn cable might need replacing. Install the new cable in the reverse order, ensuring proper alignment with the linkage and shift lever. Secure all connections, and lower the vehicle. Test the gear shifting function before you sign off.
Motorcycle Shifting Cable Replacement
Motorcycle shifting cables often require more precise handling due to the compact nature of the machine. Locate the cable’s access points, usually concealed under the engine or behind the handlebar. Support the bike using a sturdy stand. Disconnect the cable from the shifter and the transmission. Use small, precise tools to release any retaining clips.
Inspect the cable for damage. Install the new cable in the reverse order, ensuring the cable runs smoothly through the routing. Tighten all connections carefully. Double-check that the shifter moves freely through all gears.
Truck Shifting Cable Replacement
Truck shifting cables are typically more robust and complex, often requiring specialized tools and procedures. Ensure the truck is securely parked on a level surface and supported by jack stands. Locate the cable access points, which might be under the cab or behind the transmission. Disconnect the cable from the transmission and the shift lever. Note the cable’s routing carefully; trucks frequently have intricate cable runs.
Inspect the old cable, noting any significant wear. Install the new cable in the reverse order, ensuring correct routing. Tighten all connections firmly. Check the entire gear shifting range before you drive.
Comparison Table of Shifting Cable Replacement Procedures
Vehicle Type | Access Points | Specific Tools | Cable Routing | Potential Issues |
---|---|---|---|---|
Car | Behind transmission/under dashboard | Screwdrivers, pliers, cable cutters | Relatively straightforward | Loose connections, misalignment |
Motorcycle | Under engine/behind handlebar | Small screwdrivers, pliers, cable cutters | Compact routing, precision needed | Bent cables, damaged housings |
Truck | Under cab/behind transmission | Wrench sets, specialized tools, pliers | Complex routing, potentially heavy cables | Damaged sheaves, broken linkages |
Maintaining Shifting Cables
Keeping your gearbox happy and your shifting smooth requires a bit more than just a slapdash replacement. Proactive maintenance is key to avoiding future drama with your shifting cables. Ignoring these simple steps could lead to costly repairs down the line, and frankly, a less enjoyable driving experience.
Preventive Maintenance Tips
Regular care is crucial for the longevity of your shifting cables. A well-maintained system translates to less wear and tear, resulting in a smoother, more responsive gear shift. Ignoring these simple steps could lead to premature failure.
- Lubrication is Key: Regular lubrication is vital. Dry cables are prone to seizing, leading to stiffness and potentially damaging the cable housing. Proper lubrication ensures smooth operation and reduces friction, significantly extending the life of the cable. Using the correct lubricant, such as a cable specific grease, is paramount. Avoid using generic lubricants, as they may not be compatible with the cable materials and could even be detrimental.
- Visual Inspection Frequency: Regular checks are essential. Inspecting the cables for damage, kinks, or excessive wear should be a part of your routine. The frequency of these checks depends on the usage of your vehicle. High-mileage or frequently used vehicles require more frequent checks than those used less often. A good rule of thumb is to visually inspect the cables at least every 3000 miles, or after any significant repairs to the transmission.
Lubrication Procedure
Correct lubrication techniques are critical for optimal cable performance. Improper lubrication can lead to issues with cable operation, including binding or breakage. Using the correct tools is crucial to prevent damage.
- Gather Supplies: Ensure you have the correct lubricant for your specific cable type. This is not a DIY job; consult your vehicle’s manual for the recommended lubricant. You’ll also need a lubricant applicator, or a small tube of grease, depending on the design of the cable. A small, clean rag is also useful.
- Access the Cable: Carefully locate the access points for the shifting cables. You might need to remove some panels or covers. Your vehicle’s manual should detail these access points. Take care not to damage any other components while accessing the cable.
- Apply Lubricant: Apply a small amount of lubricant along the length of the cable, focusing on the areas prone to friction or wear. Avoid over-lubricating, as excess lubricant can attract dirt and debris, potentially causing more harm than good. Apply a thin, even coating to the cable and its housing.
Basic Cable Inspection Procedure
A thorough visual inspection can identify potential problems before they escalate. Early detection can prevent costly repairs and ensure your transmission functions efficiently.
- Visual Examination: Inspect the cable for any visible damage, such as kinks, cracks, or tears. Look for signs of excessive wear or corrosion on the cable and its housing. Pay close attention to the areas where the cable connects to the transmission and the steering column. These are common points of stress and failure.
- Functionality Check: Operate the gear shift lever to check for smooth and consistent movement. Any unusual resistance, binding, or noise warrants further investigation. A smooth, consistent shift pattern is indicative of a healthy cable.
- Housing Integrity: Inspect the cable housing for any signs of damage or deterioration. Look for cracks, bulges, or any areas where the housing appears weakened. A compromised housing could lead to cable failure.
Safety Precautions: How To Replace Shifting Cable
Replacing shifting cables can be a bit of a faff, but with the right precautions, it’s totally manageable. Following safety protocols is crucial, preventing potential hazards and keeping you safe from harm. Failing to do so could lead to injuries and potentially damage to the vehicle.Proper safety procedures are paramount to avoid accidents and ensure a smooth and successful replacement process.
This involves understanding the importance of each step, from disconnecting the battery to working safely under the vehicle.
Battery Disconnection
Ensuring the battery is disconnected before starting any work is a fundamental safety measure. This prevents the risk of accidental electrical shocks, which could lead to serious injuries. Failure to disconnect the battery can result in electric shocks, short circuits, or other electrical hazards.
- Locate the negative (-) terminal of the battery.
- Use a suitable wrench to disconnect the negative (-) terminal cable from the battery terminal. Always use the correct size wrench for the job to avoid damaging the cable or the battery terminal.
- Disconnect the positive (+) terminal cable from the battery terminal in a similar manner, using a suitable wrench.
Working Safely on Vehicles
Working safely on a vehicle involves several key procedures. These precautions help mitigate risks associated with working in confined spaces or with potentially hazardous materials.
- Ensure the vehicle is securely parked on a level surface and supported by appropriate stands or jack stands. This is essential for preventing the vehicle from moving unexpectedly during the repair process.
- Wear appropriate personal protective equipment (PPE), such as safety glasses, gloves, and closed-toe shoes. This helps protect you from potential hazards like flying debris, sharp edges, or chemicals.
- Use adequate lighting to improve visibility in the workspace. Poor lighting can lead to accidents, so ensuring sufficient lighting is vital, especially when working under the vehicle.
- Have a buddy system in place, especially when working under the vehicle. A second pair of eyes can help prevent accidents, like a vehicle dropping from the jack or tools falling.
Working Under the Vehicle
Working under a vehicle requires specific precautions due to the elevated risk of falling objects and potential vehicle movement. These precautions are crucial to avoid serious injury.
- Position the vehicle securely on jack stands, ensuring they are correctly positioned and stable. Ensure that the stands are rated for the weight of the vehicle and properly placed.
- Use appropriate safety gear when working under the vehicle, including gloves, safety glasses, and sturdy footwear. This will help protect you from potential hazards.
- Maintain clear visibility and adequate lighting to avoid accidents due to obstructed vision. This is critical for safety when working under the vehicle.
- Be cautious when moving around under the vehicle. Ensure you have a clear path and avoid obstructions that could cause you to trip or fall.
Final Conclusion

So, there you have it – a comprehensive guide to replacing your shifting cable. Now you’re ready to tackle any shifting cable issues that come your way. Remember to prioritize safety and follow the steps carefully. If you’re still feeling a bit lost, hit up the FAQs below for extra help. Good luck, and happy wrenching!
FAQ
Q: What are some common signs that my shifting cable needs replacing?
A: Hard shifting, clunky gear changes, or a complete lack of gear shifting are all major red flags. You might also notice a strange noise or feel a resistance when shifting.
Q: What kind of tools do I need to replace a shifting cable?
A: You’ll need a wrench set, pliers, a screwdriver, and likely some specialized tools depending on your vehicle. A torque wrench is also a good idea.
Q: How often should I lubricate my shifting cables?
A: Regular lubrication, like every few thousand miles or so, depending on your vehicle’s manual, helps prevent wear and tear and ensures smooth shifting.
Q: What if I can’t get the cable out?
A: Sometimes the cable is stuck or seized. Try using penetrating oil or a lubricant to help loosen it. If that doesn’t work, you might need to use more force, but proceed carefully to avoid damage.