How to restore refurbish yellow zinc? This guide provides a comprehensive approach to revitalizing yellow zinc, from initial assessment to long-term maintenance. Understanding the material’s properties and the reasons for restoration are crucial first steps. Different restoration techniques, each with varying levels of cost and complexity, are explored.
This detailed guide will walk you through the entire process, from preparing the surface for restoration to selecting appropriate materials and implementing safety measures. Case studies and examples of successful projects will be examined, offering practical insights and inspiration. Finally, we’ll discuss the vital steps for maintaining your restored yellow zinc structure.
Introduction to Yellow Zinc Restoration
Yellow zinc, a type of galvanized steel, is widely used in construction due to its durability and corrosion resistance. This metallic alloy, primarily composed of zinc with a small amount of other elements, forms a protective layer when exposed to the atmosphere. This layer, known as a patina, acts as a barrier against further corrosion, providing a significant lifespan for the material.Common reasons for restoring or refurbishing yellow zinc structures include the deterioration of the protective layer, leading to rust and weakening of the underlying metal.
Damage from environmental factors, such as exposure to harsh weather conditions, salt spray, or industrial pollutants, can accelerate this process. Furthermore, structural integrity issues often necessitate restoration to prevent collapse or further damage. Proper preparation is paramount for successful restoration work, as it ensures the effectiveness of the applied coatings and the longevity of the repaired structure.
Material Properties of Yellow Zinc
Yellow zinc, or galvanized steel, boasts exceptional corrosion resistance. This is primarily due to the zinc coating acting as a sacrificial anode. When exposed to oxygen and moisture, the zinc corrodes preferentially, protecting the underlying steel from rust. The thickness of the zinc layer and the composition of the alloy significantly influence the material’s lifespan and resistance to corrosion.
Reasons for Restoration or Refurbishment
Several factors contribute to the need for restoring or refurbishing yellow zinc structures. Damage from exposure to elements, like rain, snow, and strong winds, can cause pitting and deterioration of the protective zinc layer. Salt spray from coastal environments is particularly aggressive, rapidly corroding the zinc. Industrial pollutants, such as acid rain, can also compromise the zinc’s protective properties.
Furthermore, the structure’s age and the intensity of the corrosive environment play a key role in determining the restoration requirements.
Importance of Proper Preparation
Thorough preparation is critical for the success of any restoration project. This includes removing loose or damaged zinc coatings, cleaning the surface to remove contaminants, and ensuring a proper surface profile to ensure adequate adhesion of new coatings. Improper preparation can lead to premature failure of the restoration, requiring further costly interventions in the future. Careful consideration of the specific conditions and type of zinc coating is essential for selecting the right restoration method.
Types of Yellow Zinc Structures
Yellow zinc is frequently employed in various structural applications. Common examples include roofing systems, where its corrosion resistance protects the building from leaks and structural failure. Zinc railings are another prominent use, offering a durable and aesthetically pleasing solution for walkways and staircases. Other applications include fences, gates, and even architectural elements like decorative trim, showcasing the material’s versatility in construction.
Surface Preparation Methods
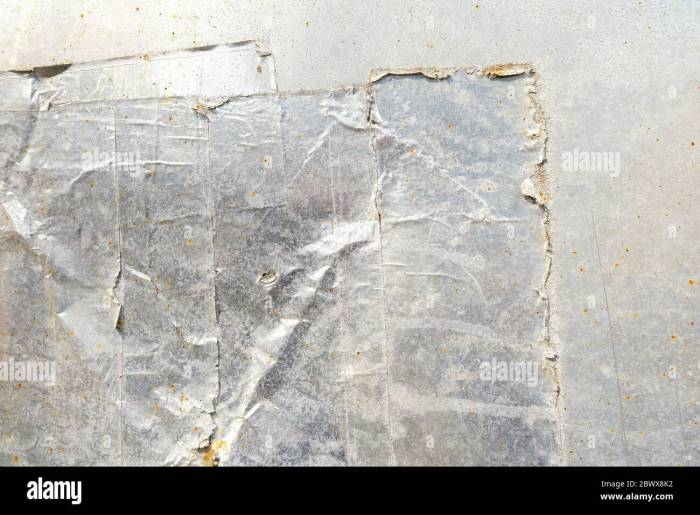
Proper surface preparation is crucial for successful yellow zinc restoration. It removes contaminants, ensuring a strong and lasting bond for the protective coatings applied later. This step directly impacts the longevity and aesthetic appeal of the finished restoration. A thorough understanding of different methods, their effectiveness, and safety precautions is vital for achieving optimal results.
Cleaning Methods for Yellow Zinc
Effective cleaning methods remove dirt, rust, and other contaminants from the yellow zinc surface, preparing it for subsequent restoration steps. Different cleaning agents and techniques have varying levels of effectiveness and safety.
- Pressure Washing: High-pressure water jets are effective for removing loose dirt, dust, and debris. This method is generally safe and relatively inexpensive. However, excessive pressure can damage the zinc surface, especially if it’s already compromised or porous. Proper nozzle selection and water pressure control are critical for avoiding damage.
- Chemical Cleaning: Specific chemical solutions can remove stubborn contaminants like rust or paint. These solutions should be chosen carefully, considering the type of contaminant and the zinc’s condition. Always follow the manufacturer’s instructions and safety precautions, as some chemicals can be harmful if not handled correctly. Examples include specialized zinc cleaning solutions and alkaline cleaners for removing rust.
- Abrasive Cleaning: Mechanical methods like wire brushing or sanding can remove tough contaminants and achieve a rougher surface for better adhesion of subsequent coatings. However, this method can potentially damage the zinc, so it should be used cautiously. The level of abrasiveness should be carefully chosen based on the zinc’s condition and the desired surface profile.
Comparing Surface Preparation Methods
A comparative analysis of different surface preparation methods provides insight into their effectiveness and safety.
Method | Effectiveness | Safety | Cost | Suitability |
---|---|---|---|---|
Pressure Washing | Good for loose debris | Generally safe | Low | Suitable for mild contamination |
Chemical Cleaning | Effective for stubborn contaminants | Variable, depends on chemical | Moderate | Suitable for moderate to severe contamination |
Abrasive Cleaning | Effective for deep cleaning | Potentially hazardous | Moderate to high | Suitable for heavily contaminated or damaged surfaces |
Correct Procedures and Safety Precautions
Adhering to the correct procedures and safety precautions is crucial for preventing accidents and ensuring effective surface preparation.
- Pressure Washing: Use appropriate nozzle settings and water pressure to avoid damaging the zinc surface. Wear safety glasses and appropriate protective clothing. Work in a well-ventilated area to avoid inhaling dust or debris.
- Chemical Cleaning: Always wear appropriate personal protective equipment (PPE), including gloves, eye protection, and a respirator. Follow the manufacturer’s instructions carefully and use appropriate safety equipment for handling chemicals.
- Abrasive Cleaning: Use appropriate personal protective equipment, including safety glasses, respirators, and protective clothing. Use appropriate sanding or wire brushing tools and techniques. Dispose of contaminated materials properly.
Signs of Effective Surface Preparation
Recognizing the signs of effective surface preparation ensures the subsequent restoration steps are properly executed.
- Removal of Contaminants: The surface should be free from visible dirt, rust, paint, or other contaminants.
- Uniform Surface Texture: The surface should exhibit a consistent texture, allowing for proper adhesion of the restoration materials.
- Dry and Clean Surface: The surface should be completely dry and free from any residue.
Corrosion Prevention Strategies
Protecting yellow zinc from further deterioration requires a multi-faceted approach that considers the various types of corrosion it faces and the mechanisms driving them. Effective strategies encompass surface treatments, protective coatings, and environmental modifications. This section delves into these critical elements for maintaining the integrity and longevity of yellow zinc components.
Types of Zinc Corrosion
Yellow zinc, like other metals, is susceptible to several forms of corrosion. Understanding these types is crucial for developing effective prevention strategies. Common types include uniform corrosion, pitting corrosion, crevice corrosion, and galvanic corrosion. Uniform corrosion, characterized by even deterioration across the surface, is often the initial stage. Pitting corrosion involves localized attack, leading to small, deep holes.
Crevice corrosion occurs in confined spaces where oxygen access is limited. Galvanic corrosion results from dissimilar metals contacting each other in an electrolyte, creating an electrochemical cell. Understanding these specific forms of corrosion allows for targeted prevention measures.
Mechanisms of Zinc Corrosion
Zinc corrodes primarily through electrochemical reactions. Exposure to moisture and oxygen, often in the presence of electrolytes (like salts or acids), creates an electrochemical cell. The zinc metal acts as the anode, undergoing oxidation (loss of electrons) and dissolving into the electrolyte. Simultaneously, oxygen is reduced at the cathode, completing the electrochemical circuit. This process is accelerated by factors like temperature and the concentration of corrosive substances.
The specific chemical reactions involved are complex, but the underlying principle is the conversion of zinc metal to zinc ions in solution.
Methods for Preventing Further Corrosion, How to restore refurbish yellow zinc
Several methods are employed to prevent or mitigate zinc corrosion. These include surface preparation techniques, application of corrosion-resistant coatings, and environmental controls. Proper surface preparation, removing any existing corrosion and contaminants, creates a clean and uniform substrate for effective coating adhesion. Environmental controls, like reducing moisture or electrolyte presence, can significantly slow the corrosion process.
Role of Coatings in Protecting Yellow Zinc
Coatings play a vital role in protecting yellow zinc from corrosion. They act as a barrier between the metal and the corrosive environment. Coatings create a physical separation, hindering the contact between zinc and the elements causing corrosion. Different types of coatings offer varying degrees of protection, depending on their chemical composition, thickness, and application method. Selecting the appropriate coating is essential for maximizing protection and longevity.
Corrosion-Resistant Coatings for Yellow Zinc
Type of Coating | Description | Advantages | Disadvantages |
---|---|---|---|
Epoxy Coatings | Two-part epoxy resins providing excellent adhesion and chemical resistance. | High durability, good chemical resistance, available in various colors. | Can be brittle, may require specialized application techniques. |
Zinc-Rich Paints | Paints containing a high percentage of zinc powder, which provides sacrificial protection. | Excellent corrosion resistance, zinc acts as a sacrificial anode, prolonging the life of the underlying metal. | May require specialized application techniques, can be more expensive than other options. |
Polyurethane Coatings | Durable coatings with good resistance to abrasion, chemicals, and solvents. | High durability, excellent resistance to abrasion and weathering. | Can be more expensive than epoxy coatings, application process can be more complex. |
Powder Coatings | Powdered resins that are fused onto the surface by heat. | Excellent durability, high resistance to chemicals and abrasion, smooth finish. | Requires specialized equipment for application, can be more expensive than other types of coatings. |
Organo-Metallic Coatings | Coatings combining organic polymers with metallic compounds. | Excellent adhesion and corrosion resistance, can be customized to specific needs. | Cost and availability can be limiting factors. |
Proper selection of coatings and meticulous application techniques are critical to ensuring their effectiveness in protecting yellow zinc.
Restoration Techniques
Restoring yellow zinc structures requires careful consideration of various techniques, each with its own set of advantages and disadvantages. Choosing the right method depends on the extent of damage, the desired lifespan of the restoration, and the budget constraints. Factors like the structure’s location, exposure to environmental elements, and accessibility during the restoration process further influence the selection of appropriate methods.Effective restoration often involves a combination of techniques, focusing on both surface treatments and underlying structural integrity.
Proper preparation, including thorough cleaning and surface inspection, is crucial for the longevity and effectiveness of any chosen restoration approach.
Painting
Painting is a common method for restoring yellow zinc, offering a relatively affordable and accessible solution. It provides a protective layer against further corrosion and improves the aesthetic appeal of the structure.
- Preparation: Thorough cleaning is essential to remove loose rust, dirt, and any existing paint. The surface should be properly primed to enhance adhesion and provide a barrier against moisture. Sanding or scraping may be necessary to create a suitable surface for the new paint.
- Application: Apply multiple coats of appropriate paint, ensuring each coat is thoroughly dry before the next is applied. Choose a paint specifically designed for metallic surfaces to maximize adhesion and durability. Consider using a zinc-rich primer to provide enhanced corrosion protection.
- Examples: Residential fences, railings, and architectural elements can be effectively restored with a suitable paint system. A painted yellow zinc surface can withstand weathering for several years if the correct paint type is used and the surface is properly prepared.
Galvanizing
Galvanizing is a more robust approach, providing superior long-term protection against corrosion. This process involves coating the yellow zinc with a layer of zinc, creating a sacrificial barrier that protects the underlying metal.
- Process: The yellow zinc is immersed in a molten zinc bath or coated with zinc through electroplating. This creates a robust barrier against corrosion, extending the lifespan of the structure significantly.
- Applications: This technique is particularly suitable for structures that are frequently exposed to harsh weather conditions, like bridges, water tanks, or industrial equipment. Galvanized yellow zinc is more resistant to rust and corrosion, extending its life span considerably compared to paint.
- Considerations: Galvanizing is generally more expensive than painting, but the extended lifespan and improved protection often make it a worthwhile investment. Careful handling and adherence to safety procedures are necessary during the galvanizing process.
Other Suitable Methods
Other methods, such as powder coating, can provide an aesthetically pleasing and durable finish. These methods often require specialized equipment and expertise.
- Powder Coating: A durable and aesthetically versatile method, powder coating involves applying a fine powder coating to the yellow zinc surface and curing it under heat. This results in a smooth, highly resistant coating that’s resistant to chipping and scratches.
- Example: Powder coating is often used for architectural elements, like gutters, downspouts, or exterior cladding. The process creates a smooth, uniform finish that can be easily customized to match desired colors and aesthetics.
Step-by-Step Guide for Restoring a Yellow Zinc Fence
A step-by-step guide for restoring a yellow zinc fence can include these phases:
- Assessment and Planning: Inspect the fence for damage, assess the extent of corrosion, and determine the appropriate restoration method. Plan the restoration process, including material procurement and safety measures.
- Surface Preparation: Remove loose rust and debris from the fence. Clean the surface thoroughly using appropriate cleaning agents and tools. Repair any structural damage. Prime the surface to ensure better adhesion of the chosen coating.
- Restoration Technique Application: Apply the chosen restoration technique, such as painting, galvanizing, or powder coating. Follow the manufacturer’s instructions carefully to ensure the best results. Apply multiple coats if necessary.
- Drying and Curing: Allow the coating to dry completely according to the manufacturer’s recommendations. Monitor the curing process to ensure proper adhesion and durability.
- Final Inspection: Inspect the restored fence for any defects or imperfections. Ensure the restoration is effective and aesthetically pleasing. Document the restoration process for future reference.
Comparison of Restoration Techniques
Technique | Cost | Time | Effectiveness |
---|---|---|---|
Painting | Low | Moderate | Moderate |
Galvanizing | High | High | High |
Powder Coating | Medium | Moderate | High |
Factors such as the extent of corrosion, the desired lifespan of the restoration, and the specific environment where the yellow zinc structure is located should be considered when making the decision.
Material Selection for Restoration
Choosing the right material for restoring yellow zinc is crucial for achieving long-term durability and aesthetic appeal. Incorrect material selection can lead to premature failure, requiring costly and time-consuming rework. The ideal restoration material should effectively protect the zinc from further corrosion, match the existing aesthetic, and withstand the environmental conditions. This section details the properties of various materials, highlighting their suitability for yellow zinc restoration, and considering potential compatibility issues.
Properties of Suitable Materials
Various materials can be used for restoring yellow zinc, each with unique properties influencing its suitability. Metals like aluminum, stainless steel, and copper alloys offer corrosion resistance, while polymers like epoxy coatings provide a barrier against environmental factors. The choice depends on factors such as the severity of corrosion, the desired aesthetic, and the environmental exposure. For instance, in highly corrosive environments, a metal with exceptional corrosion resistance, such as stainless steel, is preferred over a less resistant material.
Importance of Material Selection
Selecting the right material for a specific application is paramount. This ensures that the restoration effectively addresses the problem, and the restoration process is not a repeat of the previous damage. The chosen material must not only protect the zinc but also adhere well, maintain its integrity over time, and complement the existing aesthetic. Consideration of the material’s compatibility with the existing yellow zinc substrate is essential to avoid any adverse reactions that might compromise the restoration’s longevity.
Durability and Longevity of Different Materials
The durability and longevity of restoration materials directly impact the long-term effectiveness of the restoration project. Materials with superior resistance to corrosion, high tensile strength, and excellent adhesion to the substrate will generally provide better durability. For instance, a coating material with poor adhesion may peel or blister over time, leading to the need for repeat restoration. Understanding the expected lifespan and potential for degradation of different materials is essential for long-term success.
Potential Compatibility Issues
Compatibility issues between the restoration material and the yellow zinc can compromise the restoration’s longevity. Chemical reactions, galvanic corrosion, and differing expansion rates can lead to cracking, delamination, or other forms of failure. For instance, using a material incompatible with the zinc’s composition might lead to the formation of corrosion products, accelerating the deterioration of the restored surface.
Comparison of Restoration Materials
Material | Pros | Cons |
---|---|---|
Epoxy Coatings | Excellent barrier against corrosion, wide range of colors, relatively inexpensive | Can be brittle, may require multiple layers for adequate protection, potential for cracking |
Aluminum | High corrosion resistance, excellent adhesion to zinc, cost-effective | May require specialized application techniques, potentially less aesthetic appeal |
Stainless Steel | Exceptional corrosion resistance, durable, can be used in various forms (sheets, coatings) | Can be more expensive than other options, might require specialized fabrication |
Copper Alloys | Good corrosion resistance, aesthetic appeal, relatively easy to apply | May not be as durable as stainless steel in extremely harsh environments, potential for galvanic corrosion |
Zinc-rich Primer | Excellent corrosion resistance, adheres well to zinc, cost-effective | May not be suitable for all aesthetic requirements, limited color options |
The table above provides a general comparison of various restoration materials. Specific applications might require a tailored assessment based on the specific environmental conditions and desired outcomes. For example, a zinc-rich primer might be the ideal choice for a restoration project in a mildly corrosive environment requiring a budget-friendly solution.
Safety Precautions During Restoration
Restoring yellow zinc structures requires careful attention to safety protocols. Improper handling of materials and inadequate personal protective equipment (PPE) can lead to significant health risks for workers. Understanding the potential hazards and adhering to safety guidelines is crucial for successful and safe restoration projects.Adhering to strict safety protocols is paramount during yellow zinc restoration. This involves not only understanding the potential risks associated with the materials being used but also implementing preventive measures to minimize exposure and mitigate potential accidents.
A comprehensive approach to safety includes the selection of appropriate personal protective equipment, the understanding of emergency procedures, and the implementation of proper handling techniques for the materials involved in the restoration process.
Essential Safety Precautions for Handling Yellow Zinc and Restoration Materials
Safety during restoration is not just a precaution; it’s a necessity. A well-planned safety strategy ensures a healthy and productive work environment for all involved. The correct handling of materials and the consistent use of personal protective equipment are key components of a comprehensive safety plan.
- Proper ventilation is crucial in minimizing inhalation of dust and fumes. This often involves the use of exhaust systems and respiratory protection, such as respirators.
- Handling yellow zinc and associated restoration materials should be done with appropriate tools and techniques. Using gloves and protective clothing prevents direct skin contact with the substances, preventing potential allergic reactions or chemical burns.
- Ensure proper storage of materials. Materials should be stored in designated areas, away from heat sources and potential ignition points, to prevent accidental fires or explosions.
- Avoid working in poorly lit or cluttered areas to minimize the risk of slips, trips, and falls.
Importance of Personal Protective Equipment (PPE)
Personal Protective Equipment (PPE) acts as a crucial barrier between workers and potential hazards during restoration. Proper selection and consistent use of PPE significantly reduce the risk of exposure to harmful substances.
- Protective eyewear, such as safety glasses or goggles, is essential to safeguard the eyes from flying debris, dust, and chemical splashes.
- Gloves, made from appropriate materials such as nitrile or neoprene, should be worn to prevent skin contact with chemicals and corrosion agents.
- Protective clothing, including long-sleeved shirts and pants, should be worn to minimize skin exposure to dust and chemicals. Waterproof aprons can also offer additional protection.
- Respiratory protection, such as respirators, is essential when working with materials that generate dust or fumes.
Risks of Exposure to Hazardous Materials
Exposure to hazardous materials during yellow zinc restoration can lead to various health problems. Understanding these risks is essential for implementing appropriate safety measures.
- Inhalation of dust or fumes can cause respiratory problems, ranging from minor irritation to more severe conditions like bronchitis or lung cancer.
- Skin contact with corrosive materials can lead to burns, rashes, and allergic reactions. The severity depends on the material’s potency and the duration of contact.
- Eye contact with certain chemicals can cause irritation, corneal damage, or even blindness.
- Ingestion of hazardous materials can lead to internal damage and potential poisoning.
Emergency Procedures in Case of Accidents
Having well-defined emergency procedures in place is crucial for swift action in case of accidents.
- Establish a clear communication system to quickly alert relevant personnel in case of an emergency.
- Ensure the availability of first aid supplies and trained personnel to provide immediate assistance.
- Know the location and operation of fire extinguishers and other safety equipment.
- Establish evacuation procedures in case of fire or other significant emergencies.
Summary of Safety Guidelines for Different Restoration Techniques
This table summarizes safety guidelines for different restoration techniques, highlighting the specific precautions needed for each method.
Restoration Technique | Specific Safety Precautions |
---|---|
Acid washing | Use appropriate ventilation, wear full PPE including acid-resistant gloves and goggles. Ensure proper disposal of waste acids. |
Electrochemical cleaning | Strict adherence to electrical safety protocols, including proper grounding and insulation. Monitor for any signs of electrical arcing or sparks. |
Mechanical abrasion | Wear appropriate eye protection, respiratory protection, and protective clothing. Control dust generation through proper ventilation techniques. |
Coatings application | Ensure proper ventilation and avoid breathing in fumes. Use appropriate gloves and protective clothing. Follow manufacturer’s instructions for handling and disposal of solvents. |
Case Studies of Yellow Zinc Restoration Projects
Restoring yellow zinc structures, often found in historical buildings or industrial sites, presents unique challenges. Careful planning, meticulous execution, and a thorough understanding of the material are crucial for successful projects. This section examines real-world examples, highlighting successful restoration approaches, challenges encountered, and long-term effectiveness.Successful restoration projects demonstrate the importance of a phased approach. This involves careful assessment of the existing structure, determining the extent of damage, and developing a comprehensive restoration plan.
This often necessitates identifying the specific types of corrosion present and the underlying causes, guiding the choice of appropriate materials and techniques.
Successful Restoration Project 1: The Victorian Warehouse
This project focused on restoring a historically significant Victorian warehouse with yellow zinc cladding. The zinc exhibited extensive pitting and corrosion, compromising its structural integrity. A comprehensive assessment identified the presence of chloride-induced corrosion.
- Planning Phase: Detailed documentation of the building’s history and material specifications was critical. This involved consulting historical records and analyzing existing material samples. The project team employed advanced non-destructive testing techniques to assess the extent of corrosion and pinpoint vulnerable areas.
- Execution Phase: Selective removal of severely corroded sections was carried out using specialized tools and techniques. This was followed by meticulous cleaning and surface preparation to ensure optimal adhesion of the new zinc coatings. A zinc-rich primer was applied before the final coating to enhance corrosion resistance. The restoration team meticulously adhered to the original design specifications, ensuring aesthetic consistency.
- Assessment Phase: Post-restoration, the warehouse underwent rigorous structural testing to verify its stability and integrity. Visual inspections were performed to evaluate the adherence and appearance of the new coatings. Environmental monitoring was implemented to track the long-term performance of the restoration. The results demonstrated significant improvement in the structural integrity and longevity of the zinc cladding.
Successful Restoration Project 2: The Industrial Plant
A large industrial plant, relying on yellow zinc for its roof structure, suffered significant corrosion damage due to atmospheric pollution. The restoration aimed to preserve the structure while mitigating future corrosion.
- Planning Phase: The project team recognized the need for preventative measures to mitigate future corrosion. They conducted extensive environmental monitoring to identify the pollutants affecting the zinc. This led to the development of a corrosion-resistant coating system specifically designed to combat the pollutants.
- Execution Phase: The project employed a combination of surface preparation techniques. This included the use of high-pressure water jets to remove loose corrosion products, followed by application of a special corrosion-inhibiting primer. Finally, the application of a durable, weather-resistant topcoat was done with meticulous care. The team also ensured that the restoration was environmentally sustainable.
- Assessment Phase: After the restoration, the zinc roof underwent extended monitoring for performance. This included regular visual inspections and periodic corrosion testing. Results showed that the corrosion rate was significantly reduced compared to the pre-restoration levels, highlighting the efficacy of the preventative approach.
Long-Term Effectiveness
Long-term effectiveness is contingent on proper material selection, meticulous execution, and ongoing monitoring. Projects that consider environmental factors and incorporate preventative measures demonstrate sustained performance. The long-term success of the restoration projects is further demonstrated by the reduced need for future maintenance and repair.
Maintaining Restored Yellow Zinc
Extending the lifespan and preserving the aesthetic appeal of restored yellow zinc requires a proactive approach to maintenance. Regular inspections and preventative measures are crucial in mitigating potential issues and ensuring the long-term integrity of the restored surface. Proper cleaning techniques and prompt responses to emerging problems are key components in this ongoing process.
Regular Inspections
Regular inspections are vital for identifying any signs of deterioration, corrosion, or damage that might not be immediately apparent. These inspections help in catching problems early, enabling prompt intervention and minimizing potential damage. Visual assessments, coupled with tactile examination where appropriate, should be part of the routine. Careful attention should be paid to areas prone to moisture accumulation or exposure to harsh environmental factors.
Early detection of issues like minor corrosion or surface cracking can prevent them from escalating into larger, more costly repairs.
Preventative Maintenance Schedule
A well-defined preventative maintenance schedule is essential for consistent upkeep of the restored yellow zinc. A schedule should be tailored to the specific environmental conditions and the nature of the restored structure. For example, structures exposed to high humidity or saltwater environments may require more frequent inspections and maintenance compared to those in dry, sheltered locations. Frequency of inspections can range from monthly for high-risk areas to quarterly for less vulnerable locations.
Cleaning Procedures
Maintaining the pristine appearance and structural integrity of restored yellow zinc surfaces necessitates appropriate cleaning procedures. Harsh chemicals should be avoided as they can damage the restored surface. Instead, mild detergents and water are often sufficient for routine cleaning. For tougher stains or accumulations, a solution of mild acid (e.g., diluted vinegar) can be employed, but should be used with caution and rinsed thoroughly afterward.
Power washing should be avoided unless absolutely necessary, and even then, the pressure should be kept low to prevent surface damage. Thorough rinsing is critical to remove all residues, preventing further issues and ensuring the restored surface retains its beauty.
Handling Common Issues
Addressing potential problems promptly is crucial for maintaining the restored yellow zinc’s condition. Common issues include:
- Surface discoloration: This could be due to environmental factors or contamination. Cleaning with appropriate solutions, followed by a thorough rinsing, can often resolve this issue. If the discoloration persists, professional consultation might be necessary.
- Minor corrosion: Localized corrosion can be tackled with specialized cleaning agents or, in minor cases, mechanical removal. Corrosion should be addressed promptly to prevent its spread.
- Moisture accumulation: Regular inspections and proper drainage are vital. Addressing the source of moisture accumulation, such as leaky roofs or inadequate gutters, will prevent further corrosion.
- Loose or missing fasteners: Regular inspections should identify and address these issues promptly. Replacing or tightening fasteners is critical to maintaining the structure’s integrity and preventing further damage.
A proactive approach to maintaining restored yellow zinc ensures its longevity, preserving its aesthetic value, and reducing the need for extensive repairs in the future.
Wrap-Up

In conclusion, restoring yellow zinc involves a multi-faceted approach. Thorough surface preparation, corrosion prevention, and appropriate restoration techniques are essential for achieving long-term success. Careful material selection and strict adherence to safety protocols are crucial for both a successful restoration and a safe working environment. Regular maintenance is key to preserving the restored beauty and longevity of your yellow zinc structure.
Key Questions Answered: How To Restore Refurbish Yellow Zinc
What are the most common reasons for restoring yellow zinc?
Yellow zinc structures may require restoration due to corrosion, damage from weather, or aesthetic concerns. Often, restoration is necessary to maintain the structure’s integrity and prevent further deterioration.
What are the potential compatibility issues when choosing restoration materials?
Incompatible materials can lead to degradation of the restored surface. It’s crucial to consider the chemical composition of both the existing yellow zinc and the chosen restoration material to avoid unforeseen issues.
How can I identify the signs of effective surface preparation?
Signs of effective surface preparation include a clean, smooth, and uniform surface free of contaminants. The surface should be thoroughly inspected for any remaining imperfections or loose particles before proceeding with the restoration process.
What is the best method for cleaning yellow zinc surfaces, pressure washing or sandblasting?
The best method depends on the specific structure and the extent of contamination. Pressure washing is often suitable for less severe contamination, while sandblasting is better for tougher, more stubborn residue. A detailed assessment of the surface is crucial for determining the most appropriate cleaning method.