How to rewire John Deere Z425? This comprehensive guide unravels the intricacies of electrical system repair and maintenance for your John Deere Z425, providing a step-by-step roadmap for tackling common issues. From diagnosing problems to executing repairs, we’ll equip you with the knowledge and tools to confidently navigate the electrical landscape of your machine.
Delve into the world of your Z425’s electrical, hydraulic, and engine systems. We’ll break down each component, detailing troubleshooting procedures and repair strategies. Learn how to maintain your Z425’s efficiency and performance through a meticulous understanding of its inner workings.
Troubleshooting Common Issues
A John Deere Z425, while a marvel of agricultural engineering, can, like any machine, succumb to the occasional hiccup. This section delves into the most frequent problems encountered, providing a systematic approach to diagnosing and resolving them. A well-equipped and well-maintained Z425 is a testament to the adage, “A stitch in time saves nine.”Understanding the intricacies of your Z425’s systems is key to efficient troubleshooting.
This guide offers a structured approach to identifying and rectifying issues, allowing you to keep your machine humming along.
Engine Problems
Engine issues are often the first port of call when a Z425 exhibits problematic behavior. Identifying the source of the problem involves methodical checks and observations.
- Starting Difficulties: A stubborn refusal to ignite can stem from various factors, including a weak battery, a faulty starter motor, or even a clogged fuel filter. Checking the battery’s voltage, inspecting the starter motor’s operation, and ensuring a clear fuel pathway are essential initial steps.
- Lack of Power: Reduced power output could indicate a myriad of problems, such as low fuel pressure, a clogged air filter, or a malfunctioning fuel injection system. Careful inspection of fuel lines, air filter condition, and fuel pressure readings are crucial to pinpoint the cause.
- Overheating: High operating temperatures can indicate a compromised cooling system. Checking coolant levels, inspecting the radiator for obstructions, and ensuring proper fan operation are essential steps in addressing this problem.
Hydraulic System Problems
Hydraulic systems are the workhorses of a Z425. Troubleshooting issues involves systematic checks.
- Leaks: Hydraulic leaks can result in reduced fluid levels and, in severe cases, system failure. Identifying the source of the leak through visual inspection and tracing the hydraulic lines is a critical first step. Remember to wear appropriate safety gear.
- Sluggish Operation: Slow or unresponsive hydraulic functions could be indicative of low fluid pressure or a blocked hydraulic line. Checking fluid levels, inspecting the hydraulic pump’s operation, and examining the hydraulic lines for obstructions are vital troubleshooting steps.
- Valving Issues: Malfunctioning hydraulic valves can lead to erratic or non-responsive operation. Careful inspection of valve functionality and pressures, often involving specialized tools, are necessary.
Electrical System Problems
Electrical issues are common and can often be challenging to diagnose. This section details a systematic approach.
- Malfunctioning Lights: Faulty bulbs, wiring problems, or a malfunctioning electrical control unit are all potential causes. Checking the bulb’s condition, examining wiring connections, and inspecting the control unit are essential steps.
- Inoperative Implements: Implement control systems can fail, resulting in an inability to operate attachments. Checking the wiring, inspecting the implement’s control unit, and ensuring proper connections between the implement and the machine are essential steps.
- Power Issues: A lack of power to the implements or other components might stem from a faulty fuse or a wiring problem. Inspecting fuses and the associated wiring is crucial to resolving the issue.
Troubleshooting Table
Problem | Symptoms | Potential Causes | Solutions |
---|---|---|---|
Engine Won’t Start | No engine crank, no spark | Dead battery, faulty starter motor, fuel delivery issues | Check battery voltage, inspect starter motor, check fuel lines |
Hydraulics are Sluggish | Slow or unresponsive implement operation | Low hydraulic fluid, clogged hydraulic lines, malfunctioning pump | Check fluid levels, inspect hydraulic lines, check pump operation |
Lights Don’t Work | No illumination from any lights | Faulty bulbs, loose connections, blown fuse | Check bulb condition, tighten connections, inspect fuses |
Electrical System Repair and Maintenance
A John Deere Z425, while a marvel of agricultural engineering, relies on a complex electrical system for its operation. Understanding this system, and how to keep it humming along, is crucial for maximizing productivity and minimizing downtime. Proper maintenance and repair can transform a frustrating electrical issue into a quick fix, saving you precious time and potentially a considerable amount of money.The electrical system of the Z425 is a network of wires, connectors, and components working in harmony to power everything from the lights to the hydraulics.
Knowing how these parts interact and how to troubleshoot them is akin to having a secret decoder ring for your machine. This section will guide you through the system’s intricate workings, equipping you with the knowledge to maintain and repair electrical issues with confidence.
Electrical System Components
The Z425’s electrical system consists of several key components. Understanding their function is vital to diagnosing and resolving problems. These include the battery, starter motor, alternator, various sensors, relays, switches, and wiring harnesses. Each component plays a specific role, contributing to the overall functionality of the machine. For instance, the battery provides the initial power surge for starting the engine, while the alternator keeps the system charged while running.
Checking and Maintaining Electrical Components
Regular checks and maintenance are essential for the longevity and reliable operation of the Z425’s electrical system. Routine inspections can help identify potential problems before they escalate into major issues. Visual inspection for frayed wires, loose connections, or corrosion on components like terminals are vital. This proactive approach helps prevent costly repairs down the road.
- Battery Inspection: Check the battery’s terminals for corrosion. Clean them with a wire brush and baking soda solution, then reapply dielectric grease. Measure the voltage using a multimeter to ensure it meets the manufacturer’s specifications.
- Wiring Harness Inspection: Inspect the wiring harnesses for any signs of damage, such as cuts, kinks, or exposed wires. Ensure all connections are tight and secure.
- Switch and Sensor Testing: Verify the functionality of all switches and sensors using a multimeter. Compare readings against the manufacturer’s specifications.
Troubleshooting and Repair Procedures
A systematic approach to troubleshooting is key when dealing with electrical problems. The following table Artikels common electrical issues and their solutions.
Step | Action | Tools Required | Safety Precautions |
---|---|---|---|
1 | Identify the malfunctioning component by checking for continuity in the circuits. | Multimeter, test leads | Disconnect the battery terminals before working on the electrical system. |
2 | Locate the faulty wire or connector. | Wire strippers, needle-nose pliers, electrical tape | Ensure the area is well-lit and that you are wearing appropriate safety gear. |
3 | Replace the faulty wire or connector with a new one, ensuring proper connections. | New wire, connectors, crimping tool | Double-check all connections to avoid short circuits. |
4 | Test the system to confirm that the repair is effective. | Multimeter, test leads | Reconnect the battery terminals carefully. |
Example: A flickering headlight could indicate a loose connection in the headlight circuit. Tracing the circuit and tightening the connection would solve the problem.
Example: A no-start condition could be due to a faulty starter motor or a bad battery. Testing the battery voltage and checking the starter motor’s connections would pinpoint the issue.
Hydraulic System Overview and Repair

The hydraulic system of the John Deere Z425 is a marvel of engineering, enabling the machine to perform its tasks with impressive force and precision. Understanding its intricate workings is key to maintaining its performance and preventing costly breakdowns. Imagine a network of interconnected pipes and pumps, working in harmony to move fluids and generate power – that’s the essence of the hydraulic system.This system relies on pressurized hydraulic fluid to transmit power to various components, such as the lift arms, the implements, and the steering mechanisms.
Proper maintenance and understanding of potential problems will keep this intricate system running smoothly, ensuring a productive and trouble-free operation.
Hydraulic System Components and Functions
The Z425’s hydraulic system is composed of several crucial components, each playing a vital role in the overall operation. A pump generates the pressure required for movement. Valves control the direction and force of the fluid, ensuring precise control. Cylinders convert the hydraulic pressure into mechanical force, moving the machine’s implements. Pipes and hoses transport the pressurized fluid throughout the system.
Accumulators store extra fluid, ensuring consistent pressure and preventing pressure fluctuations.
Hydraulic Fluid Changes and Filter Replacements
Regular fluid changes and filter replacements are essential for maintaining optimal hydraulic system performance. Proper fluid levels and quality are critical for preventing wear and tear on components and maintaining smooth operation. The manufacturer’s recommended schedule for fluid changes should be meticulously followed. This helps prevent contamination and ensures the fluid retains its lubricating properties. Regularly checking the fluid level and ensuring it meets the manufacturer’s specifications is also crucial.
Component Checks and Diagnostics
Thorough component checks are vital to identifying potential problems before they escalate. Visually inspecting hoses and fittings for leaks, cracks, or damage is a crucial part of routine maintenance. Checking the condition of the pump and valves is also important. Listen for unusual noises or vibrations. Pay attention to any unusual operation.
These checks are preventive measures that prevent costly repairs.
Troubleshooting Common Hydraulic Problems, How to rewire john deere z425
Problem | Symptoms | Causes | Solutions |
---|---|---|---|
Low Hydraulic Pressure | Sluggish operation, difficulty lifting implements, inconsistent force | Low fluid level, air in the system, clogged filters, worn pump, faulty valves | Check fluid level, bleed air from the system, replace filters, inspect the pump, repair or replace faulty valves. |
Hydraulic Leaks | Fluid pooling around components, dampness, reduced fluid level | Damaged hoses, cracked fittings, worn seals, loose connections | Locate the leak, replace damaged hoses or fittings, replace worn seals, tighten loose connections. |
Hydraulic System Failure | Sudden loss of power, no movement of the implements, unusual noises | Electrical issues, faulty valves, pump failure, hydraulic fluid contamination | Check the electrical system, inspect valves, repair or replace the pump, change the hydraulic fluid. |
System Malfunctions | Inconsistent implement control, loss of control | Damaged or faulty control valves, leaking hoses, hydraulic fluid contamination | Replace faulty control valves, repair or replace damaged hoses, change the hydraulic fluid. |
Repairing Hydraulic Leaks and Component Failures
Addressing hydraulic leaks and component failures requires a methodical approach. First, identify the source of the leak. Then, replace the damaged or faulty components. If the leak is minor, tightening connections or replacing seals might suffice. However, significant leaks may necessitate replacing entire hoses or fittings.
If a component fails, such as a pump or valve, consult the manufacturer’s repair manual for the specific steps involved in replacing the part. Proper tools and safety precautions are critical for this process.
Closure
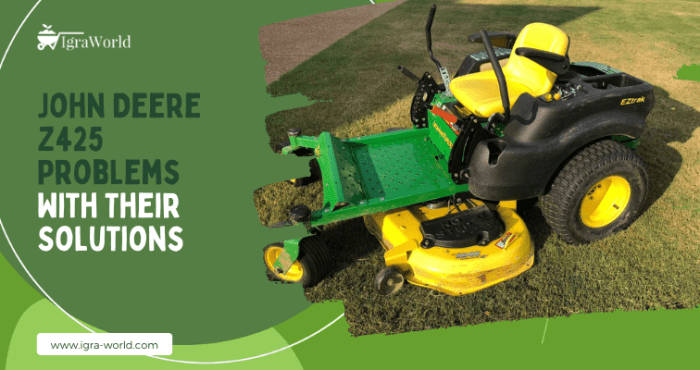
Mastering the art of re-wiring your John Deere Z425 goes beyond simply fixing a broken wire; it’s about understanding the intricate interplay of its systems. This guide empowers you to not only troubleshoot but also prevent future problems. Armed with the knowledge within, you’re now well-equipped to maintain your Z425’s optimal performance and longevity.
Quick FAQs: How To Rewire John Deere Z425
What are the most common electrical problems with a John Deere Z425?
Common electrical issues include faulty wiring, damaged connectors, and issues with the starter motor or alternator. Symptoms can range from intermittent operation to complete system failure.
How do I diagnose a hydraulic leak in my Z425?
Inspecting the hydraulic lines and components for leaks is crucial. Look for visible fluid stains, dampness, or unusual noises. Pay attention to the fluid levels and check the filters for blockages.
What safety precautions should I take when working on the electrical system?
Always disconnect the battery before performing any electrical work. Use appropriate safety gear, including gloves and eye protection. Ensure the work area is well-lit and clear of obstructions.
What tools are needed for basic electrical repairs on a Z425?
Basic tools like screwdrivers, pliers, wire strippers, and a multimeter are essential. More complex repairs may require specialized tools. Consult the service manual for specific tool recommendations.