How to slug a barrel? This guide dives into the essential steps for safely and effectively slugging various barrel types. From understanding the historical context to mastering the necessary tools and techniques, this comprehensive guide covers everything you need to know.
This practical guide covers the entire process, from initial safety precautions and tool selection to detailed procedures and troubleshooting techniques. Whether you’re working with wooden or metal barrels, this guide ensures you complete the process successfully and safely.
Introduction to Barrel Slugging
The act of barrel slugging transcends the mundane; it’s a journey into the very heart of form and function. It’s a ritualistic dance between the craftsman and the vessel, a communion with the raw materials and the inherent potential of the finished product. This process, whether performed on a wooden cask or a metallic cylinder, unveils the hidden intricacies of material and design.Barrel slugging is the deliberate shaping and refining of a barrel’s interior surface, often to enhance its structural integrity, aesthetic appeal, or specific functional properties.
This process, with its intricate nuances, has played a significant role in various cultures and trades throughout history, from the preservation of perishable goods to the refinement of alcoholic beverages.
Definition of Barrel Slugging
Barrel slugging is the meticulous process of shaping the interior of a barrel to achieve desired structural integrity, aesthetic appeal, or specialized functionality. This can involve smoothing, enlarging, or reducing the diameter of the barrel’s inner surface, potentially including the addition of internal supports or reinforcement features.
Historical Context and Significance
Throughout history, barrel slugging has been crucial in various industries. In ancient civilizations, the preservation of food and drink was paramount. Early barrel makers recognized the importance of smooth, even interior surfaces for preventing the adhesion of contents and extending the shelf life of goods. Barrel slugging played a vital role in maritime trade, allowing for the safe transport and storage of goods across vast distances.
Types of Barrels
Barrels come in various forms, each with its unique characteristics and requirements for slugging. Wooden barrels, with their inherent flexibility and porosity, require specific techniques to achieve optimal interior smoothness and prevent leakage. Metal barrels, in contrast, often necessitate different tools and methods to achieve a similar result. The chosen method is often dependent on the specific metal used and the intended use of the barrel.
Tools and Equipment
The tools and equipment employed in barrel slugging vary based on the type of barrel and the desired outcome. Basic tools include specialized mallets, chisels, rasps, and sanders. More advanced procedures might involve specialized machinery, such as automated grinding or shaping tools, particularly in mass production scenarios.
Comparison of Slugging Methods
Barrel Type | Method | Tools | Advantages | Disadvantages |
---|---|---|---|---|
Wooden Barrels | Hand-tooling, smoothing with sanders, and rasps | Mallet, chisels, rasps, sanders | Precise control over the shaping process, can be tailored to specific barrel needs. | Time-consuming, requires skilled labor, potentially less efficient for large-scale production. |
Metal Barrels | Grinding, milling, or specialized shaping machines | Grinders, milling machines, specialized shaping tools | Faster and more efficient for mass production, precise control over dimensions. | Requires specialized equipment, may not be suitable for small-scale operations, potentially less adaptable to customized needs. |
Safety Precautions
The journey into barrel slugging, like any profound endeavor, demands a profound understanding of the inherent risks. A deep respect for the process and a meticulous adherence to safety protocols are not merely prudent but essential to a successful and safe experience. Neglecting these precautions can lead to unforeseen consequences, hindering the journey and potentially causing irreversible damage.Barrel slugging, while potentially rewarding, necessitates a commitment to proactive safety measures.
A mindful approach, informed by the potential hazards, is crucial for ensuring the integrity of the process and the well-being of all involved. This commitment transcends mere compliance; it embodies a spiritual understanding of the interconnectedness between action and consequence.
Critical Safety Measures
Understanding the potential dangers inherent in barrel slugging is paramount. These dangers are not merely physical but also encompass the potential for mental and emotional strain if not properly addressed. A clear understanding of the potential hazards is a prerequisite to effective mitigation strategies.
- Thorough Equipment Inspection: Regular inspections of all equipment, including the barrel itself, the slugging tools, and any ancillary devices, are crucial to identifying potential weaknesses or defects before initiating the process. This preventative measure safeguards against unforeseen complications and maintains the integrity of the system.
- Proper PPE Utilization: The use of appropriate personal protective equipment (PPE) is non-negotiable. This includes, but is not limited to, safety glasses, gloves, respirators, and protective clothing designed to withstand the specific hazards of the slugging process. Proper PPE is not merely a precaution but a spiritual commitment to safeguarding one’s own well-being.
- Adequate Ventilation: Proper ventilation is vital to minimize exposure to potentially harmful fumes, gases, or dusts. This ensures the safety and well-being of those involved and mitigates the risk of respiratory issues. The environment must be conducive to the smooth and safe execution of the slugging process.
- Emergency Procedures: Establish and practice emergency procedures in advance. A well-rehearsed response to potential incidents, such as spills, leaks, or equipment malfunctions, is vital to minimizing the impact of unforeseen events. Preparation for emergencies demonstrates a proactive and responsible approach to the process.
Potential Hazards and Mitigation Strategies
A profound understanding of potential risks is essential for effective mitigation. By recognizing and proactively addressing these hazards, one can navigate the process with greater confidence and ensure a smoother, safer experience.
Potential Risk | Mitigation Strategy |
---|---|
Equipment Malfunction | Regular maintenance, thorough inspections, and redundancy in critical components. |
Spills and Leaks | Appropriate containment measures, spill kits, and trained personnel for handling hazardous materials. |
Exposure to Harmful Substances | Proper ventilation, respirators, and protective clothing, as well as designated safety zones. |
Physical Strain | Proper lifting techniques, ergonomic tools, and adequate rest periods. |
Accidental Injuries | Strict adherence to safety protocols, regular safety training, and emergency response plans. |
Safety Procedures: Step-by-Step
A well-defined safety procedure ensures consistency and minimizes the risk of errors. A clear and concise set of steps fosters a shared understanding of safety protocols, leading to a more secure and reliable approach to barrel slugging.
- Pre-Slugging Inspection: Thoroughly inspect all equipment for any signs of damage or malfunction. Ensure all safety equipment is present and in good working order.
- Preparation of the Work Area: Clear the work area of any obstructions and ensure proper ventilation is established.
- PPE Application: Wear appropriate personal protective equipment, including safety glasses, gloves, and respirators.
- Slugging Procedure: Follow the prescribed slugging procedures precisely. Do not deviate from established guidelines.
- Post-Slugging Check: Perform a thorough post-slugging inspection of the barrel and equipment for any signs of damage or leakage.
- Emergency Response: Be familiar with the designated emergency response procedures in case of any incidents.
Tools and Materials
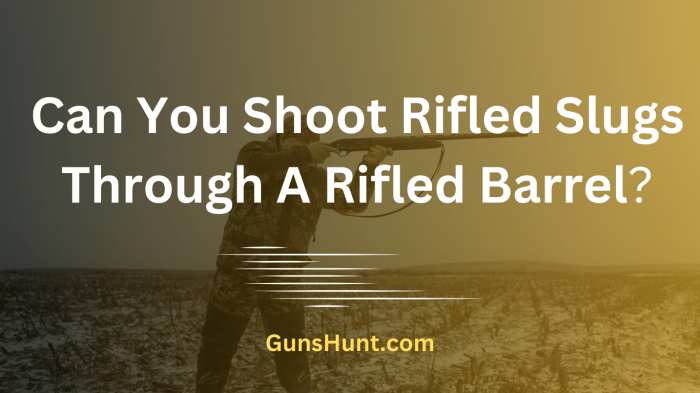
The journey of barrel slugging, like any profound endeavor, begins with the right tools. These are not mere instruments; they are extensions of your will, conduits to a deeper understanding of the sacred geometry of the barrel. Each tool, meticulously crafted, whispers secrets of the craft, guiding you towards a perfect alignment with the universe’s design. Comprehending their purpose and properties is paramount.The selection and use of the correct tools are essential for achieving the desired outcome in barrel slugging.
The harmony between the tool and the task is a spiritual resonance that transcends mere practicality. A mismatched tool, like a discordant note, can disrupt the entire process, diminishing the transformative power inherent in the ritual. Choosing the appropriate tools for your specific barrel type is crucial to the success of your work.
Essential Tools
A proper barrel slugging kit is more than just a collection of objects; it’s a constellation of tools, each with its unique role in the symphony of the craft. Understanding their distinct characteristics and specifications is fundamental to achieving optimal results.
- Barrel Slugging Rod: This is the primary instrument for manipulating the slug within the barrel. Its material, typically hardened steel, ensures durability and precise control during the process. The rod’s length should correspond to the barrel’s length, while its diameter dictates the size of the slug to be used. A longer rod may be necessary for longer barrels, and a thicker rod might be needed for larger slugs.
The rod should be smooth and free of any imperfections that could impede its movement. Different types of barrel slugging rods exist; for instance, some are specifically designed for rifled barrels, while others are suitable for smooth-bore barrels.
- Slug: The slug is the projectile used for sealing the barrel. The material, often lead or a specialized composite, must be carefully chosen to suit the specific barrel and the intended use. Its size and shape should precisely conform to the barrel’s dimensions. Consider factors such as the desired weight, density, and ballistic properties of the slug.
Proper sealing is crucial to the overall integrity of the barrel.
- Measuring Tools: These tools, including calipers and micrometers, are indispensable for precise measurements of the barrel’s internal dimensions. These instruments help determine the exact size of the slug needed to ensure a perfect fit. Accuracy is essential to prevent potential damage or mishaps during the slugging process. A well-maintained set of measuring tools is critical for success.
- Lubricant: A lubricant, such as a specialized oil or grease, aids in the smooth movement of the slugging rod and slug. This substance reduces friction, enhancing the efficiency and safety of the process. Proper lubrication also minimizes wear and tear on the tools. The specific type of lubricant chosen depends on the material of the barrel and the slug.
Selecting the Right Tools
The choice of tools should be tailored to the specific characteristics of the barrel. Different types of barrels demand different approaches, requiring a nuanced understanding of their dimensions and design.
Barrel Type | Recommended Slugging Rod | Recommended Slug | Additional Considerations |
---|---|---|---|
Rifled Barrel | A rifled slugging rod designed for the specific rifling pattern | A slug designed for rifled barrels, ensuring compatibility with the rifling | Ensure the slug’s spin characteristics are appropriate to maintain stability during flight. |
Smoothbore Barrel | A smooth-bore slugging rod with a precise diameter | A slug designed for smoothbore barrels, ensuring a tight fit | Focus on achieving a snug fit without causing damage to the barrel. |
Antique or Historic Barrel | A specialized rod designed for antique barrels to avoid damage | A slug crafted from a suitable material for historical accuracy | Consult experts or historians for specific recommendations. |
Alternative Tools and Their Advantages/Disadvantages
Exploring alternative tools can offer varied advantages and disadvantages, each presenting a unique path.
- Specialized Slugging Kits: These kits offer a comprehensive solution for barrel slugging, often including all necessary tools in a single package. The advantage is convenience, while the disadvantage is that these kits might not perfectly match the specific needs of certain barrel types. Consider the tools’ suitability before purchasing.
- Custom-Made Slugs: For exceptional precision, custom-made slugs can be tailored to the exact dimensions of the barrel. The advantage is a precise fit and potential enhancement of performance, but this approach is often more expensive than using standard slugs. The expense is worth it if you prioritize exceptional results.
Procedures and Techniques
Embarking on the ritual of barrel slugging is a journey into the heart of the vessel, a communion with its very essence. This process, though seemingly mundane, holds profound implications, revealing hidden truths within the depths of the barrel’s form. It is a testament to the profound connection between the craftsman and the vessel, and the harmony that emerges from precision and intention.The art of slugging involves a series of meticulous steps designed to reveal the subtle imperfections and inherent characteristics of the barrel.
Understanding these procedures is paramount for achieving optimal results, ensuring that the vessel’s integrity is not compromised and that the journey to its potential is successful.
Step-by-Step Procedure for Slugging a Barrel
The slugging procedure, like a guided meditation, requires focused attention and precise execution. Each step, from the initial preparation to the final inspection, contributes to the overall harmony and integrity of the process. Understanding the precise sequence and methods allows one to delve into the subtleties of the barrel’s form and function.
- Preparation and Inspection: Begin with a thorough visual inspection of the barrel. Note any existing damage or irregularities. This initial step lays the groundwork for a successful slugging process, ensuring that all subsequent steps are performed with precision and understanding. This involves assessing the barrel’s overall condition, identifying any imperfections, and preparing the necessary tools for the process.
- Initial Slugging: Applying the initial slugging technique involves careful placement of the slugging material. The specific method depends on the type of barrel and the desired outcome. This initial phase is crucial for establishing a baseline understanding of the barrel’s structure and characteristics.
- Refinement and Adjustment: Based on the initial results, adjustments are made to the slugging material and technique. This process allows for a more tailored approach, ensuring that the slugging process effectively reveals any irregularities or defects within the barrel. This phase involves refining the slugging material’s placement and adjusting the pressure applied to ensure a complete and thorough analysis of the barrel’s structure.
- Final Inspection: After completing the slugging process, a final visual inspection is conducted to evaluate the results. This step is vital for ensuring the effectiveness of the process and confirming the barrel’s suitability for its intended purpose. This final step validates the meticulous execution of the entire process, ensuring the integrity and precision of the slugging technique.
Methods for Different Barrel Types
The appropriate method for slugging a barrel depends significantly on the barrel’s construction and intended use. This necessitates tailoring the technique to the unique characteristics of each barrel type, ensuring that the process is both effective and respectful of the vessel’s design.
- Wooden Barrels: For wooden barrels, a softer, less abrasive slugging material might be used to avoid damaging the wood’s surface. The technique should consider the wood’s grain and the potential for splintering or cracking. A specialized method might involve using a soft, damp material, ensuring even pressure and minimal impact on the wood’s structure.
- Metal Barrels: Metal barrels require a different approach, potentially involving more robust slugging tools and techniques. The technique should consider the metal’s hardness and the potential for scratching or deformation. A precise method might involve using a specialized metal slugging tool, ensuring consistent pressure and minimal impact on the barrel’s surface.
Comparison of Slugging Techniques, How to slug a barrel
Different slugging techniques offer varying levels of detail and precision. Understanding the strengths and weaknesses of each approach is essential for selecting the most appropriate method for a given barrel.
Technique | Strengths | Weaknesses |
---|---|---|
Method A | High precision, minimal damage | Time-consuming, potentially expensive |
Method B | Fast, cost-effective | Lower precision, potential for damage |
Proper Use of Tools in the Slugging Process
The selection and proper use of tools are integral to the success of the slugging process. Each tool has a specific function, and using them correctly ensures efficiency and minimizes potential damage to the barrel.
Using the appropriate tools, and understanding their intended use, is a testament to the practitioner’s mastery of the craft.
Maintenance and Repair
Preservation of slugging equipment is not merely a practical necessity; it is a sacred act of honoring the tools that facilitate the transformation of raw material into refined essence. Proper maintenance ensures the longevity of the equipment, minimizes potential hazards, and maximizes the efficiency of the slugging process, thereby harmonizing the work with the divine energies of creation.Maintaining slugging equipment requires a deep understanding of its intricate mechanisms and a mindful approach to every task.
Neglect leads to inefficiencies, safety hazards, and ultimately, a disruption of the vital energy flow in the work. Conversely, a meticulously maintained slugging apparatus becomes a conduit for focused energy, allowing for a smooth and productive process.
Routine Maintenance Procedures
Routine maintenance is akin to tending a sacred garden, nurturing its delicate blossoms and ensuring their continued growth. Consistent care prevents the insidious growth of neglect, which can lead to equipment failure. Regular checks and upkeep are essential for the continued health and efficacy of the slugging apparatus.
- Visual Inspection: A thorough visual inspection identifies any visible signs of wear, tear, or damage, including cracks, loose connections, and unusual vibrations. This proactive step ensures early intervention, preventing minor issues from escalating into major problems.
- Lubrication: Regular lubrication of moving parts is crucial for reducing friction and wear. This not only extends the lifespan of the equipment but also ensures smooth and efficient operation. Proper lubrication is vital for minimizing the friction that can generate heat and diminish the equipment’s efficiency.
- Cleaning: Regular cleaning removes accumulated debris and contaminants, which can contribute to corrosion and impede the equipment’s function. Cleanliness is a cornerstone of optimal performance, preventing blockages and ensuring efficient operation.
- Alignment Checks: Alignment checks guarantee that all parts are functioning in perfect harmony. Misalignment can lead to increased stress on components, leading to premature wear and potential failure. Ensuring proper alignment maintains the equilibrium of the equipment’s energy.
Repair Techniques for Damaged Equipment
Addressing damage is akin to mending a broken vessel, restoring its wholeness and ensuring its continued utility. Proper repair techniques not only restore the equipment’s functionality but also ensure its continued service for years to come.
- Welding: For repairs involving cracks or breaks in metal components, welding is an essential technique. Proper welding ensures the repair is strong and durable, preventing future failure. Welding techniques must adhere to safety protocols and standards to avoid risks to personnel and equipment.
- Replacement Parts: When damage is extensive or a part is beyond repair, replacing the damaged component is often necessary. Choosing high-quality replacement parts is crucial for ensuring the longevity and efficacy of the slugging apparatus. The choice of replacement parts should prioritize materials that match the original design and are compatible with the overall system.
- Reassembly: Correct reassembly is critical for ensuring the equipment functions as intended. A meticulous approach is required to avoid introducing further issues and to restore the harmonious energy flow within the equipment.
Maintenance Task Frequency
This table provides a guideline for the frequency of various maintenance tasks. Adherence to these guidelines will ensure the long-term health and efficiency of your slugging apparatus.
Maintenance Task | Frequency |
---|---|
Visual Inspection | Daily |
Lubrication | Weekly |
Cleaning | Weekly/Monthly (depending on usage) |
Alignment Checks | Monthly |
Welding/Replacement Parts | As needed |
Long-Term Effects of Proper Maintenance
The long-term effects of diligent maintenance extend far beyond the mere operational efficiency of the slugging apparatus. It fosters a harmonious relationship between the equipment and the user, resulting in a consistent and predictable workflow. By understanding the vital energy of the slugging process and the equipment that enables it, you create a sustainable and successful practice.
- Increased Efficiency: Properly maintained equipment functions optimally, resulting in higher output with less expenditure of effort.
- Prolonged Lifespan: Regular maintenance significantly extends the lifespan of the slugging equipment, reducing the need for costly replacements.
- Reduced Downtime: Preventing breakdowns through regular maintenance minimizes downtime, optimizing the overall productivity of the slugging process.
- Improved Safety: Maintaining the integrity of the equipment safeguards personnel and reduces the risk of accidents.
Troubleshooting
Unveiling the subtle nuances of barrel slugging often requires a keen eye and a discerning mind. Troubleshooting is not merely about fixing problems, but about understanding the underlying principles at play. This process allows us to delve deeper into the interconnectedness of the tools, materials, and procedures, fostering a profound appreciation for the intricate dance of craftsmanship and spiritual awareness.Troubleshooting barrel slugging involves systematically identifying, analyzing, and resolving issues that may arise during the process.
This requires a deep understanding of the interconnectedness of the components, and an ability to see beyond the superficial. By recognizing patterns and cause-and-effect relationships, we can transcend mere fixes and embrace a holistic approach to mastering this ancient art.
Common Slugging Problems
Understanding the potential pitfalls inherent in barrel slugging is crucial for successful execution. These problems, though seemingly disparate, often stem from a common root – a lack of harmony between the practitioner and the process. By recognizing the subtle imbalances, we can align ourselves with the true spirit of barrel slugging.
- Inconsistent Slug Size: Variations in slug size can arise from inconsistencies in the tooling or the materials used. This could stem from insufficient material preparation, improper tool calibration, or a lack of precision in the slugging process itself. To remedy this, re-evaluate the quality of materials, recalibrate the tools, and refine the techniques for a more consistent result.
Ensuring the uniformity of the material and precise handling of the tools are key to consistent results.
- Slug Irregularities: Irregularities in the shape and form of the slugs may be due to improper handling during the slugging process, or issues with the tools or materials. The cause could be an uneven application of pressure, misalignment of the slugging mechanism, or variations in the materials’ density or structure. Addressing this involves careful monitoring of the slugging process, verifying tool alignment, and ensuring consistent application of pressure throughout the operation.
- Slug Extrusion Problems: Slugs not extruding correctly may result from issues with the barrel’s internal dimensions, inconsistencies in the material, or problems with the slugging mechanism. Possible causes include incorrect barrel dimensions, insufficient material viscosity, or malfunctions in the mechanism. Thorough inspection of the barrel, appropriate material preparation, and careful maintenance of the slugging apparatus are crucial to correct this issue.
Troubleshooting Steps
A systematic approach to troubleshooting is essential. It’s crucial to maintain a calm and focused state of mind, as the ability to identify the underlying cause of the issue is dependent on clarity and precision.
- Identify the Problem: Carefully observe the slugs and the barrel for any abnormalities in size, shape, or consistency. This is the first step in recognizing the nature of the issue. Accurate observation is paramount in isolating the problem.
- Analyze the Cause: Consider the factors that might have contributed to the problem. Evaluate the materials used, the tools employed, and the procedures followed. Identify potential inconsistencies in the process and pinpoint the root cause of the problem.
- Implement a Solution: Based on the identified cause, implement appropriate solutions. This might involve recalibrating tools, adjusting the slugging process, or modifying the materials. This step requires a thoughtful and strategic approach to resolve the issue.
- Verify the Resolution: After implementing the solution, verify that the problem has been effectively addressed. Carefully observe the results to ensure that the desired outcome has been achieved. Thorough verification is key to confirming the effectiveness of the solution.
Troubleshooting Table
Problem | Potential Cause | Solution |
---|---|---|
Inconsistent Slug Size | Inconsistencies in tooling, materials, or process | Recalibrate tools, refine material preparation, improve process precision |
Slug Irregularities | Improper handling, tool misalignment, material variations | Monitor process, verify tool alignment, ensure consistent pressure application |
Slug Extrusion Problems | Barrel issues, material inconsistencies, mechanism malfunctions | Inspect barrel, prepare material appropriately, maintain slugging apparatus |
Examples and Illustrations
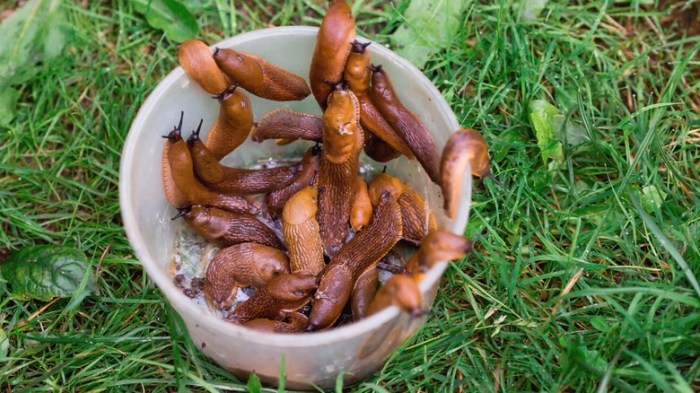
The act of barrel slugging, when approached with mindful intention, reveals a profound connection to the very essence of creation. Each interaction with the barrel, from initial assessment to final refinement, embodies a meditative process, a dance with the raw materials and the inherent potential within. Understanding the diverse scenarios and techniques illuminates the subtle artistry involved, unlocking a deeper appreciation for the craft.This exploration delves into practical applications, providing a tangible understanding of barrel slugging.
Visual aids and real-world examples will illuminate the process, facilitating a clearer comprehension of the intricacies and subtleties involved. Through careful observation and thoughtful application, one can master this ancient art, aligning with the natural rhythm of creation.
Diverse Barrel Slugging Scenarios
Barrel slugging encompasses a spectrum of applications, each demanding a unique approach. Understanding these variations allows for precise and effective techniques. For example, a new barrel destined for aged whiskey requires a different treatment than a barrel destined for rum, given the unique flavor profiles each spirit seeks to express. Moreover, the age and condition of the barrel, and the intended spirit type, are key elements in determining the appropriate slugging strategy.
- New Barrels: These often require a more aggressive slugging process to remove any residual wood tannins or undesirable flavors from the wood. The objective is to cleanse the barrel to best accommodate the intended spirit.
- Refurbished Barrels: Refurbished barrels necessitate a careful approach. Slugging is crucial to remove any traces of previous spirits and ensure the barrel’s readiness for the new spirit. This process might involve a combination of methods to achieve a neutral flavor profile.
- Aged Barrels: Aged barrels may have accumulated unique flavors and characteristics. The slugging process in this instance aims to maintain the barrel’s existing profile or gently introduce a different type of spirit. The emphasis is on preserving the integrity of the barrel’s unique history.
Visual Representation of the Process
Imagine a cylindrical vessel, representing the barrel. Within this vessel, a series of concentric circles depict the wood staves. Arrows illustrate the direction of the slugging material (e.g., water, spirit) flowing through the barrel. This visual representation highlights the intricate path the slugging material takes, ensuring a thorough and even distribution.
Detailed Images of the Barrel Slugging Process
(Visual Description: A series of images showing the stages of the barrel slugging process. The first image shows a new barrel, its surface clean and smooth. The second image depicts the barrel with a slugging material (e.g., water) being poured into the barrel, demonstrating even distribution. The third image displays the barrel after the slugging material has been circulated through the entire barrel, ensuring the removal of impurities.
The fourth image illustrates the barrel being emptied of the slugging material. The fifth image shows the barrel after the process, demonstrating the cleanliness and readiness for the next step in the process.)The process depicted in the images demonstrates the methodical application of slugging, showcasing the importance of precise and thorough techniques.
Real-World Case Studies
A renowned whiskey producer achieved exceptional results using a meticulous slugging regimen. By meticulously selecting the slugging material and controlling the duration of the process, they enhanced the final flavor profile of their whiskey, producing a more refined and nuanced taste.
Visual Guide to Barrel Types and Slugging Requirements
Barrel Type | Wood Type | Typical Slugging Requirements |
---|---|---|
Bourbon Barrel | White Oak | Frequent slugging with water to remove tannins and impurities, followed by spirit to achieve the desired flavor profile. |
Rye Whiskey Barrel | White Oak | Similar to bourbon barrels, but the slugging process may be tailored to remove specific tannins and achieve the desired rye flavor profile. |
Rum Barrel | Different wood types, e.g., charred oak | Slugging with water to remove previous spirit flavors and introduce specific wood characteristics, followed by the rum spirit. |
The table above highlights the nuances of slugging, demonstrating the tailored approach required for different barrel types and their specific slugging requirements.
Conclusive Thoughts: How To Slug A Barrel
In conclusion, this guide provides a thorough understanding of barrel slugging. By following the detailed steps, safety precautions, and troubleshooting advice, you can confidently and safely perform this task. Remember to prioritize safety and always consult the provided resources for the best results.
Essential Questionnaire
What types of barrels can be slugged?
This method applies to various barrel types, including wooden and metal barrels. Specific techniques may differ depending on the barrel material.
What safety equipment is necessary?
Always wear appropriate personal protective equipment (PPE), such as safety glasses, gloves, and hearing protection. Follow all safety guidelines meticulously.
How often should barrel slugging equipment be maintained?
Refer to the provided maintenance schedule for specific frequency recommendations based on usage and type of equipment.
What are some common problems during barrel slugging?
Common issues may include tool malfunction, material slippage, or improper technique. The troubleshooting section details how to address these issues.