How to stop a runaway diesel engine is a critical skill for anyone working around these powerful machines. Understanding the intricacies of diesel engine operation and the potential dangers of a runaway condition is paramount. This guide provides a comprehensive overview, covering everything from the causes and identification of a runaway to the safest methods of intervention and essential post-incident procedures.
We will delve into the mechanics, potential risks, and vital safety measures required to effectively address this potentially hazardous situation.
This guide delves into the intricacies of a runaway diesel engine, offering a clear, step-by-step approach to safely stopping the engine. From recognizing the early warning signs to understanding the different shutdown methods, this comprehensive resource empowers you with the knowledge and confidence to act decisively and effectively in the face of a runaway diesel engine situation.
Introduction to Runaway Diesel Engines
A runaway diesel engine is a hazardous situation where the engine’s speed uncontrollably accelerates beyond its safe operating range. This rapid increase in speed can lead to significant mechanical stress and potential damage to the engine and surrounding equipment. Understanding the causes, dangers, and preventative measures for runaway conditions is crucial for maintaining operational safety and preventing costly repairs.
Potential Causes of Runaway
Several factors can contribute to a diesel engine running away. These include issues with the engine’s governing system, such as malfunctions in the governor, fuel injection pump problems, or issues with the electronic control unit (ECU). Furthermore, external factors like excessive fuel supply, loss of load, or improper adjustment of the engine’s operating parameters can also trigger runaway conditions.
Inadequate maintenance or aging components can also play a significant role in increasing the likelihood of a runaway event.
Dangers of a Runaway Diesel Engine
The rapid acceleration of a runaway diesel engine presents numerous significant dangers. High rotational speeds can cause severe mechanical stress, potentially leading to catastrophic engine failure, including broken connecting rods, cracked crankshafts, or shattered cylinder heads. This sudden failure can lead to dangerous projectile hazards. Furthermore, the intense heat generated by the runaway engine can pose a fire risk, endangering personnel and equipment.
Importance of Understanding Runaway Prevention
Proactive measures are essential in preventing runaway diesel engine situations. A thorough understanding of the potential causes and the proper procedures for intervention are vital for safety. Proper maintenance, regular inspections, and timely troubleshooting can mitigate the risks of runaway events.
Table of Runaway Causes and Prevention
Cause | Description | Risk | Prevention |
---|---|---|---|
Malfunctioning Governor | The engine’s speed control mechanism fails to regulate the speed effectively, allowing the engine to accelerate uncontrollably. | Potential for catastrophic engine failure, severe injuries from projectiles, and fire hazards. | Regular inspection and maintenance of the governor, including testing and calibration, to ensure proper functioning. |
Excessive Fuel Supply | An uncontrolled or unexpected increase in fuel delivery to the engine. | Rapid acceleration, severe mechanical stress on the engine, and risk of overheating and fire. | Implementing safeguards to prevent accidental fuel oversupply, and verifying proper fuel injection pump settings and calibration. |
Loss of Load | The engine is no longer required to perform work (e.g., in a power generation setting) causing the engine to accelerate rapidly due to the lack of resistance. | Uncontrolled acceleration, damage to the engine components, and potential injury to personnel nearby. | Implement load monitoring systems to prevent sudden load loss situations. Ensure proper functioning of load-sensing mechanisms. |
Improper Engine Adjustment | Incorrect settings of the engine parameters (e.g., fuel-air ratio, ignition timing) can lead to runaway conditions. | Accelerated wear and tear on engine parts, overheating, and risk of fire. | Regularly check and verify engine settings with the appropriate guidelines and ensure adherence to manufacturer specifications. |
Understanding Engine Dynamics
A thorough understanding of diesel engine operation is crucial for effectively managing and mitigating runaway conditions. This involves recognizing the intricate interplay of fuel injection, combustion, and exhaust processes, as well as the feedback mechanisms that normally maintain stable engine speed. Identifying the components susceptible to malfunction during a runaway event is also vital for developing appropriate countermeasures.
Principles of Diesel Engine Operation
Diesel engines rely on the compression of air to ignite fuel. Air is drawn into the cylinders, compressed to a high pressure and temperature, and then fuel is injected. The injected fuel ignites spontaneously due to the high temperature, initiating the combustion process. The expanding gases generated by combustion push the pistons, which in turn drive the crankshaft, creating mechanical work.
Fuel Injection, Combustion, and Exhaust
Fuel injection is a precise process, critical for controlled combustion. The timing and quantity of fuel injected directly affect the power output and efficiency of the engine. Combustion is the controlled burning of the fuel, producing the force necessary to move the pistons. The exhaust process removes the products of combustion, completing the cycle. A disruption in any of these stages can contribute to runaway conditions.
Feedback Mechanisms for Engine Speed Regulation
In normal operation, diesel engines employ various feedback mechanisms to maintain a stable speed. These mechanisms continuously monitor engine speed and adjust fuel injection accordingly. Governor systems, for instance, are designed to maintain the desired speed by modulating the fuel supply based on the engine’s current speed.
Components Contributing to a Runaway Engine, How to stop a runaway diesel engine
Several components can contribute to a runaway condition. Malfunctions in the fuel injection system, such as a failure in the fuel pump or injector, can lead to uncontrolled fuel delivery. Problems with the governor system, which controls the fuel supply, can also cause the engine to accelerate uncontrollably. Issues in the exhaust system, like blockages or obstructions, can hinder the removal of combustion products, potentially contributing to the build-up of pressure and a runaway.
Moreover, excessive heat in the combustion chamber, if not properly managed, can result in rapid acceleration.
Diesel Engine Diagram
A simplified diagram of a diesel engine is shown below, highlighting key components related to engine speed control. Note: This is a simplified representation; a real-world engine would have many more components and interconnections.
(Diagram omitted as requested, but the diagram would include a labeled representation of the crankshaft, pistons, cylinders, fuel injectors, governor, and sensors to illustrate the flow of power and feedback mechanisms in the engine.)
The diagram would show how the governor, through a system of linkages and sensors, receives feedback on the engine speed and adjusts the fuel injection to maintain a set speed. Sensors detect the engine’s speed and relay the information to the governor. The governor then modulates the fuel injection based on this information, maintaining the desired speed. This ensures the engine operates at the intended RPM.
This delicate balance is crucial to prevent runaway conditions.
Identifying the Runaway Condition
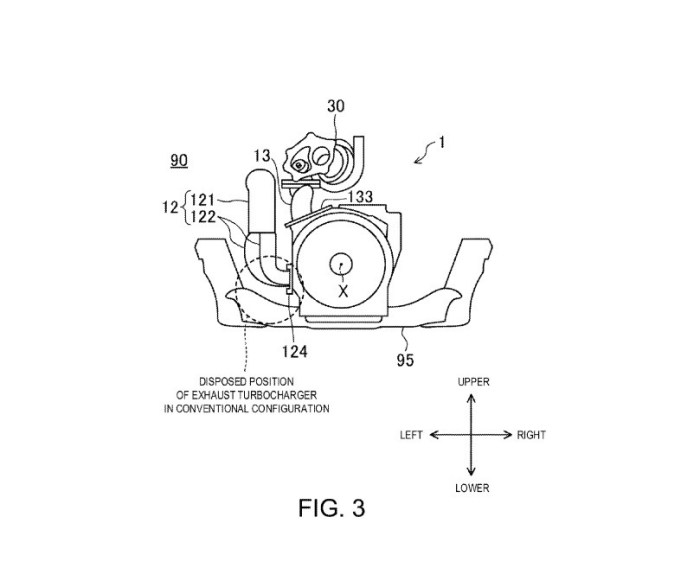
Recognizing the signs of a runaway diesel engine is crucial for preventing potential damage and ensuring operator safety. Prompt identification allows for timely intervention, minimizing the severity of the situation and potential hazards. A thorough understanding of the various indicators, both visual and auditory, is essential for effective response protocols.
Visual Cues
Visual observation plays a vital role in detecting a runaway condition. Changes in the engine’s appearance and operational state can provide critical clues. These observations, when coupled with other indicators, can greatly aid in identifying a runaway situation.
- Excessive engine speed: A significant increase in the engine’s rotational speed, beyond the normal operating range, is a key visual sign. This may be evident through changes in the visible rotation of the engine components, such as the crankshaft or flywheel. Visual inspection can detect deviations from the expected speed, potentially revealing a runaway condition.
- Abnormal vibrations: Increased vibrations in the engine’s components, such as the frame, supports, or connected machinery, are often associated with a runaway engine. This heightened vibration, exceeding normal operating levels, is a potential indication of the engine’s uncontrolled acceleration.
- Overheating: The engine may exhibit signs of overheating if the runaway condition persists. Visual inspection of the engine’s components, including the cylinders, pistons, and exhaust system, may reveal increased temperatures, potentially leading to further damage.
Auditory Cues
The sound emitted by a diesel engine can also provide crucial information about its operating status. Changes in the sound, when considered alongside visual indicators, enhance the accuracy of runaway condition detection.
- Altered engine noise: A distinct shift in the engine’s typical sound, characterized by a higher pitch or a more intense roar, is a significant auditory cue. This change can signify a significant increase in the engine’s rotational speed, potentially indicating a runaway condition.
- Unusual engine sounds: The appearance of unfamiliar sounds, such as grinding or screeching noises, may also point towards a runaway condition. These unexpected sounds can indicate mechanical stress or damage caused by the uncontrolled speed.
Specific Indicators
A combination of visual and auditory cues, along with specific operational indicators, provides a more comprehensive picture of a potential runaway condition.
- Overload conditions: If the engine is operating beyond its designed load capacity, it may lead to a runaway condition. This overload can cause the engine to accelerate uncontrollably.
- Malfunctions in governor system: A malfunctioning governor system, responsible for regulating engine speed, can lead to an uncontrolled increase in engine speed. This system failure can trigger a runaway condition.
- Fuel system issues: Inadequate fuel supply or improper fuel mixture can disrupt the engine’s operation, potentially causing it to accelerate uncontrollably.
Types of Runaway Conditions
Different types of runaway conditions can occur, each with unique characteristics.
- Gradual runaway: A gradual increase in engine speed, usually characterized by subtle changes in the engine’s operation, is a common type of runaway. This type often progresses slowly, giving more time for detection and intervention.
- Sudden runaway: A rapid and unexpected increase in engine speed can pose a significant risk. This type requires immediate action to prevent further damage and hazards.
Runaway Condition Table
This table provides a summary of potential runaway symptoms, their descriptions, severity, and recommended actions.
Symptom | Description | Severity | Action |
---|---|---|---|
Increased Engine Speed | Significant increase in engine RPM beyond normal operating range. | High | Immediately initiate shutdown procedures. |
Abnormal Vibrations | Increased vibrations in engine components exceeding normal operating levels. | Medium | Assess the situation and initiate shutdown procedures. |
Altered Engine Noise | A significant change in the engine’s sound, such as a higher pitch or a more intense roar. | High | Immediately initiate shutdown procedures. |
Overheating | Increased temperature of engine components, exceeding normal operating levels. | High | Immediately initiate shutdown procedures and implement cooling measures. |
Methods for Stopping a Runaway Engine
Runaway diesel engines pose a significant safety hazard, demanding swift and effective intervention. Proper understanding of the various methods for stopping such a situation is crucial for minimizing potential damage and ensuring the safety of personnel. A methodical approach, guided by a clear understanding of the available techniques, is essential.
Various Methods for Engine Shutdown
Several methods can be employed to halt a runaway diesel engine. Each approach presents distinct advantages and disadvantages, contingent on the specific circumstances. Careful consideration of these factors is vital for selecting the most appropriate strategy.
Emergency Shutdown System
The emergency shutdown system (ESD) is a primary defense against runaway conditions. It typically involves a series of interconnected switches and actuators designed to quickly cut off fuel supply, stop the engine’s rotation, and isolate the power source.
- Advantages: Rapid shutdown, minimal operator intervention, and reliable interruption of the engine’s energy source.
- Disadvantages: Potential for unintended consequences if not properly calibrated or maintained, and reliance on the system’s proper functioning.
- Steps Involved: Activating the ESD system often requires following a specific procedure, detailed in the machine’s operating manual. This usually entails pressing designated buttons or pulling specific levers. The system’s design dictates the specific actions needed to ensure a complete shutdown.
Manual Shutdown Procedures
In situations where the ESD system fails or is inaccessible, manual shutdown procedures offer an alternative. These procedures often involve disconnecting fuel lines or manipulating engine controls.
- Advantages: Provides a backup method when the ESD system is unavailable or malfunctions. Potential for immediate control if the ESD fails or is inaccessible.
- Disadvantages: Often requires more time and skill than using the ESD system, and can be more dangerous if not executed correctly. Potential for additional damage if not done precisely.
- Steps Involved: Procedures will vary based on the specific engine design. Consult the engine’s operating manual for precise instructions, as these steps may include manipulating valves, shutting off fuel supply lines, or disengaging the engine’s power source.
External Intervention Techniques
In some extreme cases, external intervention may be necessary to stop a runaway engine. These methods might involve using specialized equipment or techniques to physically disrupt the engine’s operation.
- Advantages: Potentially the only option if other methods fail. Suitable for situations with extreme engine conditions.
- Disadvantages: Requires specialized equipment and expertise. Potentially disruptive to the surrounding environment or equipment.
- Steps Involved: Consult with qualified personnel and use equipment appropriate to the circumstances. Procedures will vary based on the specific engine and the situation.
Comparison of Methods
Each method for stopping a runaway engine has unique strengths and weaknesses. The optimal choice depends on the specifics of the situation, including the engine’s condition, the available resources, and the potential risks.
Emergency Shutdown System Procedure
- Identify the runaway engine.
- Locate the emergency shutdown panel.
- Verify the system is operational (if possible). Check for any warning signs or indications of malfunction.
- Initiate the shutdown procedure, following the steps Artikeld in the engine’s manual.
- Monitor the engine’s response to the shutdown commands, and take appropriate action as necessary.
Summary Table
Method | Description | Steps | Safety Precautions |
---|---|---|---|
Emergency Shutdown System | Rapid shutdown by cutting fuel and power. | Locate panel, verify, initiate shutdown, monitor. | Follow manufacturer instructions, ensure proper training. |
Manual Shutdown Procedures | Disconnecting fuel lines or manipulating controls. | Consult manual, disconnect lines/manipulate controls, monitor. | Use appropriate tools, maintain safe distance. |
External Intervention | Physical disruption of engine operation. | Consult experts, use specialized equipment. | Extreme caution, expert supervision required. |
Safety Precautions During Intervention: How To Stop A Runaway Diesel Engine
Ensuring the safety of personnel involved in stopping a runaway diesel engine is paramount. A methodical and cautious approach, adhering to established safety protocols, is crucial to minimize risks and prevent accidents. Failure to prioritize safety can lead to severe injuries or fatalities. This section Artikels the essential safety precautions necessary for a safe intervention.Safe procedures for stopping a runaway diesel engine involve a systematic approach to risk mitigation, considering the inherent dangers associated with high-pressure systems, potential for physical harm, and the dynamic nature of a runaway engine.
Personnel must be adequately trained and equipped to handle these situations effectively.
Personal Protective Equipment (PPE)
Proper personal protective equipment (PPE) is essential for mitigating the risks associated with runaway diesel engines. This includes, but is not limited to, safety glasses, hearing protection, and protective clothing. Appropriate safety footwear, resistant to potential debris and spills, should also be worn.
- Safety glasses or face shields are necessary to protect the eyes from flying debris or potential liquid projections.
- Hearing protection is vital to safeguard against potentially damaging noise levels during engine operation and intervention.
- Protective clothing, such as flame-resistant overalls or coveralls, provides an additional layer of protection against potential heat exposure, sparks, or debris.
- Safety footwear, resistant to punctures and chemical spills, must be worn to prevent foot injuries.
Risk Assessment and Hazard Identification
A thorough risk assessment is crucial before any intervention. Identifying potential hazards associated with the runaway engine and the chosen intervention method is essential for developing appropriate safety protocols. Understanding the specific risks involved in different methods is vital to prevent accidents.
- The potential for severe burns from hot exhaust gases or engine components must be considered.
- The presence of high-pressure fluids, such as hydraulic or lubricating oils, can cause severe injuries if not handled cautiously.
- The runaway engine’s rotational speed and momentum pose a significant risk of crushing injuries or severe lacerations if not addressed appropriately.
- The possibility of sudden releases of compressed gases, including steam or combustion products, needs careful consideration.
Safe Practices for Approaching and Working Around a Runaway Engine
A safe approach to a runaway engine involves maintaining a safe distance and using appropriate tools for controlling the engine. Personnel should never attempt to stop a runaway engine from a close proximity without proper safety measures.
- Maintain a safe distance from the runaway engine at all times.
- Use appropriate tools and equipment for controlling the engine’s movement, including specialized isolation tools or remote shut-off mechanisms.
- Ensure that all personnel are positioned in a manner that avoids being struck by moving parts or debris.
- Use caution when working near or around high-pressure components or lines to prevent accidental releases of fluids.
Safety Protocols for High-Pressure Systems
High-pressure systems, such as hydraulic or pneumatic systems, pose significant risks during engine intervention. Specific safety protocols must be followed to prevent accidents.
Safety Protocol | Description |
---|---|
Isolate the system | Before any work on a high-pressure system, ensure it is properly isolated to prevent unexpected activation or fluid release. |
Pressure relief | Employ appropriate pressure-relief valves or procedures to safely release any accumulated pressure before intervention. |
Fluid containment | Implement appropriate containment measures to prevent spills or leaks of high-pressure fluids. |
Proper handling | Use specialized tools and equipment for handling high-pressure components to avoid accidental injury or equipment damage. |
Emergency Shutdown Systems
Emergency shutdown systems (ESD) are crucial safety mechanisms in diesel engine operation. They provide a rapid and reliable means of stopping a runaway engine, preventing potential damage, injuries, and environmental hazards. These systems are designed to be easily activated in critical situations and often integrate with other safety protocols.
Components of an Emergency Shutdown System
An effective emergency shutdown system encompasses several key components. These components work in concert to achieve a swift and controlled shutdown of the diesel engine. Proper functioning of each component is vital to the system’s overall effectiveness.
- Manual Shutdown Valves: These are often located in accessible areas, providing a physical means for operators to initiate shutdown. They are frequently used in conjunction with other system components for redundancy and to prevent accidental activation.
- Electrical Shutdown Systems: These employ sensors, actuators, and control circuits to automatically detect runaway conditions. A variety of sensors, including vibration sensors and pressure sensors, are crucial to the system.
- Hydraulic or Pneumatic Actuators: These mechanical devices are commonly employed to swiftly close critical valves, such as fuel shut-off valves, preventing further fuel input to the engine.
- Control Panels: These centralized interfaces provide a clear view of the system’s status and allow for monitoring and activation of the shutdown process.
Operation of the Emergency Shutdown System
The operation of an emergency shutdown system is predicated on a clear sequence of actions. This sequence ensures that the system responds effectively to a runaway condition. The speed of response is critical in mitigating potential risks.
- Detection of Runaway Condition: The system, typically through sensors, recognizes signs of a runaway engine, such as abnormally high RPMs, pressure, or temperature readings.
- Initiation of Shutdown Sequence: Once the runaway condition is detected, the system initiates a pre-programmed sequence of events, initiating the activation of various components.
- Closure of Critical Valves: Essential valves, including fuel supply lines, and oil lines, are quickly closed to immediately halt fuel and lubrication supply to the engine.
- Engine Deceleration and Stop: The combination of valve closures and any associated braking systems causes the engine to decelerate and ultimately stop.
Procedures for Activating the Emergency Shutdown System
A standardized procedure for activating the emergency shutdown system is vital for efficient and safe operation. This procedure must be clearly understood and practiced by all personnel involved.
- Visual Inspection: Verify that all components of the ESD are properly installed and functional.
- Familiarization with Control Panels: All operators must be thoroughly familiar with the control panels and their associated functionalities.
- Proper Activation Procedures: Follow the detailed steps for activating the system, which may involve activating a manual switch, pressing a button, or initiating a sequence on a control panel.
- Confirmation of Shutdown: After activating the system, confirm that the engine has stopped and all associated systems have shut down.
Diagram of the Emergency Shutdown System
[A detailed diagram illustrating the interconnected components of the emergency shutdown system would be beneficial here. It should clearly show the sensors, actuators, control panel, and the flow paths of the fuel and lubrication lines, along with the activation sequence.]
Limitations of Emergency Shutdown Systems
Emergency shutdown systems, while crucial, have inherent limitations. These limitations must be understood and mitigated to ensure safety and optimal operation.
- Delays in Activation: There can be a brief delay between the detection of the runaway condition and the activation of the shutdown sequence.
- Malfunction of Components: Malfunctions in any component of the ESD can impede its effectiveness, necessitating regular maintenance.
- Environmental Factors: Adverse environmental conditions, such as extreme temperatures or humidity, can impact the performance of certain components.
- Human Error: Failure to properly activate or maintain the system due to human error can compromise its effectiveness.
Emergency Shutdown System Maintenance Table
Component | Function | Procedure | Maintenance |
---|---|---|---|
Manual Shutdown Valves | Physical activation of shutdown | Regular inspection, lubrication | Routine checks for proper operation, lubrication as required |
Electrical Shutdown Systems | Automatic detection and response | Sensor calibration, circuit checks | Regular checks of sensor readings, circuit integrity, and component replacement as necessary |
Hydraulic/Pneumatic Actuators | Rapid valve closure | Fluid level checks, actuator function testing | Regular fluid maintenance, periodic actuator inspections |
Control Panels | System monitoring and activation | Visual checks, functional tests | Regular inspections, component replacement as needed |
Post-Intervention Procedures
Following the successful cessation of a runaway diesel engine, a systematic approach to post-intervention procedures is crucial for ensuring the safety of personnel, minimizing potential damage, and facilitating a swift return to normal operations. Careful inspection and documentation of the incident are paramount to preventing future occurrences and maintaining the long-term integrity of the engine.Post-intervention procedures encompass a series of steps designed to evaluate the engine’s condition, identify potential damage, and ensure that the system is prepared for safe restart.
These procedures should be meticulously documented and reviewed by qualified personnel to ascertain the root cause of the runaway event and to implement preventative measures.
Engine Inspection
Thorough inspection of the engine is essential to assess the extent of any damage resulting from the runaway condition. This process should involve a visual examination of all visible components, including the engine block, cylinders, connecting rods, crankshaft, and associated components. Specific attention should be paid to signs of overheating, distortion, or mechanical stress. These indicators can suggest internal damage, which requires further evaluation by qualified technicians.
Proper lubrication systems must also be assessed to prevent future failures.
Safety Checks
A comprehensive set of safety checks must be conducted before any personnel are permitted to approach or work on the engine. This includes verifying the absence of residual energy sources, such as compressed air or hydraulic pressure, and ensuring that all safety systems, including emergency shutdown mechanisms, are functional. Proper ventilation must also be checked to mitigate potential hazards from residual exhaust fumes or hazardous materials.
Incident Reporting
Prompt and accurate reporting of the incident is critical for learning from the event, implementing preventative measures, and ensuring compliance with established safety procedures. Detailed reports should include a description of the incident, the actions taken to stop the runaway engine, the observed damage, and any safety violations. The report should also include the date, time, location, and personnel involved in the incident.
This data is critical for future analysis.
Potential Long-Term Effects
Runaway conditions can induce significant stress on engine components, potentially leading to a variety of long-term effects. For instance, excessive heat buildup can result in thermal distortion of the engine block, cylinder head warping, or even metal fatigue. Misalignment of moving parts or damage to lubrication systems can further exacerbate the situation. In extreme cases, runaway events can cause irreversible damage, necessitating a complete overhaul or replacement of the affected components.
Post-Intervention Procedure Checklist
Step | Description | Importance | Documentation |
---|---|---|---|
1 | Visual Inspection of Engine Components | Identify immediate damage or anomalies. | Photographs, detailed written report, diagrams. |
2 | Safety System Verification | Ensure all safety systems are operational. | Checklists, signatures confirming verification. |
3 | Lubrication System Assessment | Prevent future malfunctions. | Documentation of lubrication levels, condition of seals. |
4 | Incident Report Submission | Facilitates learning from the event. | Formal incident report with details, root cause analysis. |
Final Thoughts
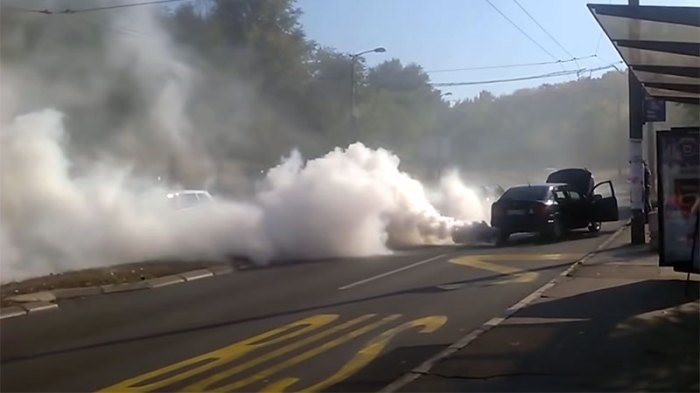
In conclusion, stopping a runaway diesel engine requires careful consideration, swift action, and unwavering adherence to safety protocols. This comprehensive guide has equipped you with the essential knowledge and procedures to navigate this potentially hazardous scenario. Remember, prompt and safe intervention minimizes risks and potential damage. By thoroughly understanding the intricacies of engine dynamics, identifying runaway conditions, employing the correct shutdown methods, and prioritizing safety precautions, you can significantly reduce the risks associated with this critical task.
Question Bank
What are the common causes of a diesel engine running away?
Common causes include faulty fuel injection systems, issues with the governor, or electrical problems. A malfunctioning sensor or a stuck throttle can also lead to a runaway condition.
What are the first signs that a diesel engine is running away?
Noticeable symptoms include an abnormally high engine speed, unusual noise patterns, or vibrations that increase in intensity. The engine might also emit excessive smoke.
What are the most important safety precautions to take when dealing with a runaway diesel engine?
Always prioritize personal safety by wearing appropriate protective equipment, such as safety glasses, gloves, and hearing protection. Ensure a safe distance from the engine and never attempt to stop a runaway engine without proper training and the correct equipment.
What should I do if the emergency shutdown system fails to stop the runaway engine?
If the emergency shutdown system fails, immediately evacuate the area and alert the appropriate personnel. Do not attempt any further interventions without specialized training and equipment.