How to stop leaking at control valve and riser is a crucial aspect of industrial maintenance. Understanding the root causes, implementing effective troubleshooting strategies, and adopting preventative maintenance practices are essential for minimizing downtime and ensuring operational safety. This comprehensive guide provides a detailed analysis of the problem, offering insights into identifying leaks, performing repairs, and ultimately preventing future occurrences.
This guide delves into the intricacies of control valve and riser leaks, covering a range of critical aspects from material selection to regulatory compliance. It explores various potential causes, ranging from faulty seals to improper installation, and provides practical troubleshooting techniques for identifying and isolating the source of the leak. Furthermore, the guide provides strategies for repair, maintenance, and preventative measures to ensure long-term operational reliability.
Identifying the Cause of Leakage
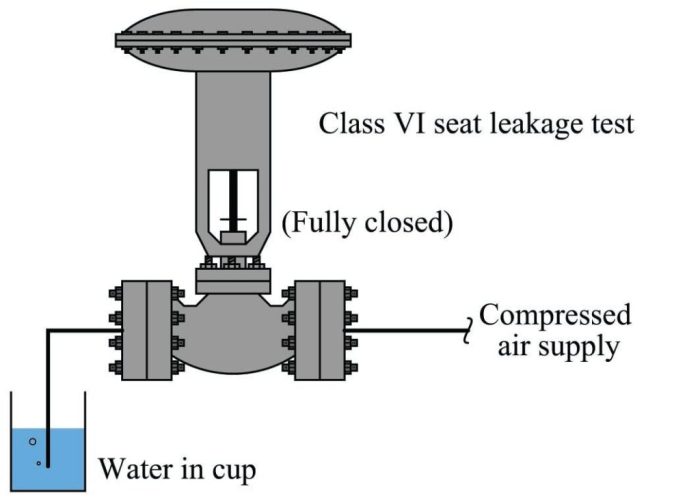
Uncontrolled leakage from control valves and risers can lead to significant operational issues, impacting safety, efficiency, and environmental compliance. Understanding the root causes is paramount to effective troubleshooting and preventing future incidents. This requires a thorough analysis of potential factors, from faulty seals to improper installation practices. A deep dive into the various contributing factors will equip us with the knowledge to diagnose and resolve these problems effectively.
Potential Causes of Leakage
Leakage at control valves and risers can stem from a multitude of factors. These include issues with the valve’s components, improper installation procedures, or fluctuations in operating conditions.
- Faulty Seals: Control valves rely heavily on seals to prevent leakage. Damaged or deteriorated seals are a common source of leakage. Different seal types exhibit different failure modes. Examples include worn O-rings, damaged packing materials, or improper seal alignment. Improper installation, or repeated cycles of high pressure, can accelerate seal degradation.
- Worn Parts: Prolonged operation and exposure to harsh conditions can lead to wear and tear on internal valve components like stems, diaphragms, and valve bodies. Wear often manifests as increased leakage. This can lead to costly maintenance and potential safety hazards.
- Improper Installation: Incorrect installation procedures can lead to misalignment, improper seating, and other issues that contribute to leakage. Factors like insufficient torque during installation or incorrect valve positioning can cause leakage.
- Pressure Fluctuations: Sudden or significant pressure changes can stress seals and components, potentially causing leakage. Such fluctuations can be caused by pump issues or unexpected process demands. Sudden pressure spikes can cause existing minor damage to become critical, leading to leakage.
- Material Degradation: The materials used in the construction of control valves and risers can degrade over time due to exposure to corrosive fluids, high temperatures, or other environmental factors. This degradation can weaken the material, potentially leading to leakage. For instance, stainless steel exposed to acidic environments may develop pitting corrosion.
- Flow Rate Variations: Changes in the flow rate can impact the stresses and forces acting on the valve components. High flow rates can exacerbate existing wear, leading to leakage. Similarly, abrupt changes in flow rate can impact sealing components.
Types of Seals and Failure Modes
Control valves utilize various seal types, each with unique characteristics and susceptibility to failure.
- O-rings: O-rings are commonly used in control valves due to their simplicity and cost-effectiveness. However, they are prone to compression set and extrusion. Damage can result from improper installation, or excessive pressure.
- Packing: Packing materials are used in various valve designs to create a seal. Wear, degradation, and improper tensioning are common failure modes. The type of packing material used is crucial for the application, and the process operating conditions can affect its lifespan.
- Diaphragms: Diaphragms are employed in some valve designs. Tears, punctures, and material degradation can lead to leakage. Improper mounting or excessive pressure can lead to these issues.
Operating Conditions and Their Influence
Operating conditions significantly impact the performance and longevity of control valves.
- Pressure: High operating pressures can stress seals and components, leading to leakage. The relationship between pressure and leakage is generally exponential, with leakage increasing significantly as pressure increases.
- Temperature: High temperatures can accelerate the degradation of seals and other materials, increasing the risk of leakage. Different materials have different tolerances for high temperatures.
- Flow Rate: High flow rates can increase the shear and impact forces on the components, potentially causing leakage. Abrupt changes in flow rate can have a detrimental effect on seals and other critical parts.
Control Valve Material Resistance to Leakage
The choice of material for control valves directly impacts their resistance to leakage.
Material | Resistance to Leakage | Comments |
---|---|---|
Carbon Steel | Moderate | Susceptible to corrosion in specific environments |
Stainless Steel | High | Offers better resistance to corrosion and wear |
Alloy Steel | Very High | Excellent resistance to corrosion and wear, but more expensive |
Hastelloy | Excellent | Highly resistant to corrosion by a wide range of chemicals |
Materials selection is critical in preventing leakage. Factors like the operating environment, temperature, and pressure need careful consideration.
Troubleshooting Techniques
The heart-wrenching experience of a leaking control valve or riser demands a methodical and precise approach. We must move beyond the initial shock and fear of the unknown to systematically diagnose the source of the leak and implement swift, effective solutions. A measured, step-by-step approach is crucial to preventing further damage and costly repairs. Understanding the source and severity of the leak is the first critical step in ensuring the safety and functionality of the entire system.A thorough inspection is not just a task; it’s a meticulous process demanding unwavering attention to detail.
This proactive approach is crucial for not only containing the leak but also preventing potentially catastrophic consequences, such as further damage or dangerous pressure fluctuations. Every step, from visual assessments to advanced leak detection methods, contributes to a comprehensive understanding of the problem.
Systematic Inspection Procedures
A methodical approach to inspecting control valves and risers is vital. Begin with a visual examination, meticulously scrutinizing every joint, fitting, and connection. Look for any signs of corrosion, wear, or deformation. Pay particular attention to areas known to be susceptible to stress or strain. Next, carefully check for any signs of leakage, including drips, puddles, or visible streams.
Document these observations meticulously. If possible, consider using specialized tools like borescopes for deeper examination of hard-to-reach areas.
Assessing Leakage Severity
Accurate assessment of the leakage severity is essential for effective containment and repair. Visual inspection provides a preliminary assessment, but more definitive methods are often required. Pressure testing involves carefully applying controlled pressure to the system while monitoring for leaks. This allows for precise identification of the leak’s location and severity. Specialized leak detection techniques, such as dye penetrants or acoustic emission, can pinpoint even minute leaks that might be missed by visual inspection.
Each method offers a unique perspective, enabling a comprehensive understanding of the problem’s scale.
Isolation of the Affected Section
Swift isolation of the affected section is paramount to containing the leakage and preventing further damage. This often involves shutting down valves strategically to restrict the flow of fluids. Carefully consider the potential impact on other parts of the system, and meticulously follow safety protocols to prevent unintended consequences. The goal is to isolate the source of the leak, allowing for controlled repair without jeopardizing the safety of personnel or equipment.
Safety must always be the top priority.
Necessary Tools and Equipment
Category | Tool/Equipment | Description |
---|---|---|
Visual Inspection | Borescope, Flashlight, Magnifying Glass | Essential for examining hard-to-reach areas and detecting subtle signs of damage or leakage. |
Pressure Testing | Pressure Gauge, Pressure Pump, Valves | Enables precise identification of leak location and severity. |
Leak Detection | Dye Penetrant Kit, Acoustic Emission Detector | Pinpoints minute leaks missed by visual inspection. |
Isolation | Valves, Shut-off mechanisms | Crucial for containing the leak and preventing further damage. |
Safety | Safety Glasses, Gloves, Personal Protective Equipment | Essential for ensuring the safety of personnel during the troubleshooting process. |
Repair and Maintenance Strategies
A heart-wrenching experience arises when a control valve or riser leaks. It’s not just a mechanical problem; it’s a potential threat to efficiency, safety, and profitability. Addressing these leaks demands a proactive approach, moving beyond simply fixing the immediate issue and delving into preventative maintenance. The following strategies offer a roadmap to long-term success, ensuring your systems remain robust and reliable.
Repair Options for Leakage Problems
Different leakage scenarios necessitate tailored repair approaches. Understanding the root cause is crucial to selecting the right solution. Here are several potential repair options:
- Seal Replacement: Damaged seals are a common culprit. Replacing worn-out seals with high-quality, compatible replacements is often the most effective solution. This ensures a tight, leak-free seal, preventing further damage and costly downtime. For example, a faulty packing gland in a pneumatic control valve may need a complete replacement, ensuring no air escapes through the gland.
- Valve Adjustments: In some cases, minor adjustments to valve settings can resolve leaks. Calibration and fine-tuning of valve parameters can restore proper operation and eliminate leaks. This is a cost-effective approach if the problem is linked to improper valve positioning or pressure settings. Precise adjustments to the valve stem and packing can restore its sealing capabilities.
- Component Repair: If a specific valve component is damaged, such as the actuator or body, repair or replacement may be necessary. A damaged actuator might require specialized repair or replacement to ensure smooth operation and prevent future leaks. Careful examination of the affected part is essential to determine the extent of the damage and the best repair strategy.
- Riser Inspection and Repair: Leaking risers often point to corroded or damaged sections. Thorough inspection of the riser, including visual checks and pressure testing, is critical to pinpoint the exact location of the damage. Repair options include welding, patching, or replacing corroded sections, ensuring the integrity of the riser is restored. For instance, a crack in a riser pipe may necessitate welding to prevent further leaks and potential safety hazards.
Best Practices for Maintaining Control Valves and Risers
Proactive maintenance is paramount to preventing leaks. Implementing a comprehensive maintenance schedule, including regular inspections and preventative measures, significantly reduces the likelihood of future problems. It is an investment in safety, efficiency, and long-term cost savings.
- Regular Inspections: Visual inspections of valves and risers, coupled with periodic pressure testing, are essential to detect potential issues early. This allows for timely intervention, preventing small problems from escalating into major leaks and costly repairs. Regular checks for corrosion, wear, and misalignment are vital in preventing future issues.
- Proper Lubrication: Maintaining proper lubrication of moving parts, like valve stems, reduces friction and wear, extending the lifespan of the components. Consistent lubrication minimizes the risk of leaks due to mechanical wear and tear. This proactive approach minimizes the need for emergency repairs.
- Cleaning and Flushing: Regular cleaning and flushing of the system can remove debris and contaminants that can contribute to corrosion and leakage. This is especially crucial in harsh environments where contaminants are prevalent. This crucial step is an investment in the integrity of the system.
- Documentation and Records: Maintaining detailed records of maintenance activities, including dates, procedures, and findings, is critical for future troubleshooting and planning. This comprehensive documentation ensures that necessary maintenance is performed and that any issues are promptly identified and resolved.
Importance of Regular Maintenance Schedules
Regular maintenance schedules are vital for minimizing leakage frequency and ensuring the longevity of your control valves and risers. Consistent maintenance reduces unexpected downtime and prevents significant financial losses associated with costly repairs.
“Proactive maintenance is significantly more cost-effective than reactive maintenance, where issues are addressed only after they have escalated.”
Maintenance Procedures for Various Valve Types
A tailored maintenance approach is essential for different valve types. This table Artikels the specific procedures for various control valve types:
Valve Type | Inspection Procedures | Maintenance Procedures |
---|---|---|
Pneumatic Valves | Check for leaks in pneumatic lines, inspect actuators for damage | Lubricate actuators, replace seals if necessary |
Electric Valves | Inspect wiring, check motor operation | Clean contacts, lubricate moving parts |
Diaphragm Valves | Inspect diaphragm for damage, check seals | Replace damaged diaphragms, ensure proper seating |
Globe Valves | Check for leaks in the body, inspect stem for wear | Replace worn parts, lubricate stem |
Preventing Future Leaks
A constant fear hangs over every operation, the specter of leaks. But prevention isn’t just about stopping the drips; it’s about building a system where leaks are anomalies, not the norm. This crucial step involves a shift in perspective, moving from reactive fixes to proactive design and maintenance. By understanding the root causes and employing smart strategies, we can forge a future where leaks are minimized, operations run smoothly, and everyone can breathe a collective sigh of relief.
Design Considerations for Control Valves and Risers, How to stop leaking at control valve and riser
The design of control valves and risers directly impacts their susceptibility to leaks. Careful consideration of materials, tolerances, and pressure ratings is paramount. Employing high-quality, corrosion-resistant materials in the valve bodies and riser piping is crucial to withstand the rigors of operation. Precision in manufacturing and assembly reduces stress points, thus minimizing the risk of fatigue-induced cracking, a frequent culprit in long-term leaks.
Thorough stress analysis during the design phase can help identify and mitigate potential weak points.
Importance of Proper Installation Procedures
Installation errors are a frequent source of leaks, a silent threat lurking within seemingly perfect systems. Proper installation procedures, meticulously followed, are vital for a leak-free operation. A misaligned valve, improperly tightened connections, or inadequate support for the riser can all lead to leaks that escalate over time. Training personnel on proper installation techniques, using the correct tools, and adhering to established protocols are essential safeguards.
Employing leak detection equipment during installation can catch issues early, saving time and preventing major problems down the line. Furthermore, rigorous quality checks and regular inspections throughout the installation process should be enforced to maintain high standards.
Preventative Maintenance Strategies
Proactive maintenance is the cornerstone of leak prevention. Regular inspections, timely maintenance checks, and diligent monitoring of critical components can significantly reduce the likelihood of future incidents. This includes checking for corrosion, verifying proper valve operation, and monitoring pressure fluctuations in the riser system. Using specialized tools and equipment for leak detection can identify potential issues early on.
Regular lubrication and adjustments of moving parts in control valves can significantly extend their lifespan and prevent premature wear, a common cause of leakage.
Control Valve Designs and Leakage Prevention Features
Valve Design | Leakage Prevention Features | Example Application |
---|---|---|
Ball Valve | Simple design, often with double seals and high-quality sealing materials; readily available for various sizes and pressures. | General purpose control applications |
Globe Valve | Precise control over flow rates; various seat designs for different fluid viscosities and pressures. | Applications requiring precise flow regulation |
Butterfly Valve | Compact design, suitable for high-flow applications; often used with resilient seals. | Large-diameter pipelines, high-flow control |
Diaphragm Valve | Seals with resilient diaphragms, good for corrosive fluids and applications requiring low maintenance; typically used in chemical processes. | Chemical processing, corrosive liquids |
Each design has unique advantages and disadvantages in preventing leakage, so the best choice depends on the specific application. Understanding these features is key to selecting the appropriate valve for a given process and minimizing the risk of leaks.
Case Studies and Examples
A relentless battle against leaks, whether in control valves or risers, often tests the resilience of engineering teams. These leaks aren’t just inconvenient; they represent a cascade of potential problems, from production downtime and costly repairs to safety hazards and environmental damage. Understanding past struggles and triumphs in mitigating these issues is crucial to developing proactive and effective strategies for the future.
Let’s delve into some real-world scenarios.The frustration of dealing with a persistent leak, the hours spent on diagnostics, and the relief of finally finding a solution are all part of the human experience in engineering. These case studies illuminate the diverse challenges and showcase successful strategies for preventing these unwelcome occurrences. The detailed analysis of these real-world situations provides valuable lessons for implementing effective preventative measures.
Case Study 1: The Corroded Control Valve
A chemical processing plant experienced a recurring leak in a control valve responsible for regulating pressure in the reactor. Initial troubleshooting revealed significant corrosion in the valve’s body, caused by the aggressive nature of the process fluid. The corrosion had weakened the valve’s structure, leading to a gradual increase in leakage over time. The solution involved replacing the corroded valve with a more resistant material, such as a high-nickel alloy, and implementing a more rigorous maintenance schedule that included regular inspection and cleaning of the valve.
The plant also switched to a less corrosive fluid, where possible, reducing the risk of future corrosion.
Case Study 2: The Riser System Failure
A power plant experienced a significant leak in a riser pipe used for transporting high-pressure steam. The leak originated from a stress-induced crack in the riser’s weld. The troubleshooting involved meticulous examination of the weld joints, material analysis, and pressure testing to identify the root cause. The repair involved a comprehensive weld repair procedure, followed by a thorough pressure test to ensure the integrity of the repaired section.
Subsequent monitoring and a refined inspection schedule prevented further problems. A key takeaway from this case study was the importance of stringent weld quality control and regular inspection of critical components.
Case Study 3: The Valve Stem Sticking
A water treatment plant encountered a valve stem sticking issue, leading to intermittent leakage from the control valve. The analysis showed that the valve stem was accumulating deposits over time, reducing lubrication and causing friction. The solution involved implementing a preventative maintenance strategy that included periodic valve stem lubrication and cleaning. They also examined the process parameters to identify any factors that might contribute to the accumulation of deposits.
In addition, the plant investigated alternative lubrication techniques, which proved to be an effective strategy for preventing future stem sticking and leaks.
Prevention Strategies and Evaluation
A successful leak prevention strategy relies on a multi-faceted approach, combining proactive maintenance with rigorous inspection and monitoring. In all three case studies, the effectiveness of the implemented prevention strategies was evaluated through regular monitoring of the affected components. The data collected was used to fine-tune the maintenance schedule and identify any emerging trends or potential risks. A comprehensive approach is essential to preventing leaks.
Key Learnings and Best Practices
Case Study | Root Cause | Troubleshooting | Repair/Solution | Prevention Strategy |
---|---|---|---|---|
Corroded Control Valve | Aggressive process fluid | Corrosion inspection | Material replacement, improved maintenance | Material selection, regular inspection |
Riser System Failure | Stress-induced crack in weld | Weld examination, pressure testing | Weld repair, pressure testing | Stringent weld quality control, regular inspections |
Valve Stem Sticking | Deposit accumulation, reduced lubrication | Valve stem lubrication, process parameter analysis | Periodic lubrication, process adjustments | Preventative maintenance, lubrication optimization |
These case studies highlight the critical importance of a proactive and data-driven approach to leak prevention. A comprehensive evaluation of potential causes, coupled with appropriate troubleshooting and repair strategies, is crucial for minimizing downtime and ensuring safety.
Material Selection and Compatibility: How To Stop Leaking At Control Valve And Riser
Choosing the right materials for control valves and risers is not just about picking something that looks strong; it’s about ensuring the long-term health and safety of the entire system. A material incompatible with the process fluid can lead to catastrophic failures, causing not only costly repairs but also potential environmental damage and safety hazards. This careful selection is paramount for maintaining a reliable and efficient operation.Selecting materials compatible with the process fluid and operating conditions is critical to prevent leakage.
A mismatch between material and environment can trigger corrosion, erosion, or other degradation processes, ultimately leading to leaks and failures. This delicate balance between material properties and the process environment directly impacts the system’s lifespan and overall performance.
Factors Influencing Material Selection
Material selection for control valves and risers hinges on several critical factors. Corrosion resistance, a material’s ability to withstand the corrosive effects of the process fluid, is paramount. Temperature tolerance is another key consideration, as extreme temperatures can cause materials to weaken or change their properties over time. The operating pressure and the expected service life of the equipment also play a crucial role in material choice.
Furthermore, cost-effectiveness and availability are also essential factors in the decision-making process.
Long-Term Performance and Stability
The long-term performance and stability of a material are directly related to its resistance to degradation. Over time, materials can experience stress cracking, pitting, or other forms of damage due to factors like corrosion, erosion, or fatigue. The specific operating conditions, including temperature fluctuations, pressure variations, and exposure to aggressive chemicals, greatly impact the material’s longevity. Understanding the long-term stability of different materials in the specific environment is crucial for preventing costly failures and downtime.
For example, stainless steels are known for their corrosion resistance in many environments, but their performance in high-temperature, high-pressure applications might require specialized alloys.
Comparison of Material Properties
The table below illustrates the properties of various materials suitable for control valves and risers. It’s crucial to match the material’s properties to the specific requirements of the process environment to ensure optimal performance and longevity.
Material | Corrosion Resistance | Temperature Tolerance (°C) | Strength | Cost |
---|---|---|---|---|
Carbon Steel | Moderate | Up to 450 | Good | Low |
Stainless Steel (316L) | Excellent | Up to 800 | Good | Medium |
Hastelloy C-276 | Excellent (aggressive chemicals) | Up to 650 | High | High |
Monel | Excellent (sea water, some acids) | Up to 650 | High | Medium-High |
Nickel-Based Alloys | Excellent (highly corrosive environments) | Up to 1100 | High | High |
Regulatory Compliance and Safety
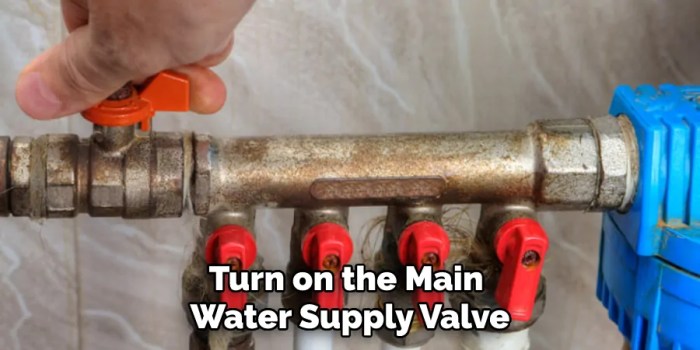
A sense of profound responsibility hangs heavy over the prevention of leaks in control valves and risers. These systems, vital to countless operations, demand unwavering adherence to safety protocols and regulations. Failing to meet these standards can have devastating consequences, not just financially, but also in terms of human life and environmental impact. Understanding and meticulously implementing regulatory compliance is paramount for safeguarding lives and protecting our planet.A thorough grasp of safety regulations isn’t just a matter of ticking boxes; it’s about building a culture of safety that permeates every aspect of operation, inspection, and maintenance.
This proactive approach prevents accidents, minimizes potential harm, and instills a deep sense of security in those who rely on these critical systems.
Regulatory Requirements for Leakage Prevention
Compliance with regulatory requirements is essential for ensuring the safe and reliable operation of control valves and risers. These regulations often dictate specific design standards, material specifications, and operational procedures to mitigate the risks associated with leaks. This ensures that every aspect of the system is built with safety as its cornerstone.
Safety Protocols During Inspection, Repair, and Maintenance
Safeguarding personnel during inspection, repair, and maintenance is paramount. A comprehensive set of safety protocols must be rigorously followed. These protocols should encompass personal protective equipment (PPE), confined space entry procedures, and lockout/tagout protocols to prevent accidental exposure to hazardous conditions.
Importance of Emergency Response Plans for Leakage Incidents
Preparedness for leakage incidents is crucial. A well-defined emergency response plan, incorporating communication protocols, evacuation procedures, and the deployment of appropriate resources, is essential for minimizing the impact of any leakage incident. A swift and organized response is vital to containing the damage and safeguarding those involved.
Table of Relevant Safety Regulations
The table below Artikels key safety regulations and their applicability across different industries. Understanding these regulations and their specific requirements within each industry is crucial for appropriate compliance.
Safety Regulation | Description | Applicability |
---|---|---|
OSHA (Occupational Safety and Health Administration) | Comprehensive set of standards for worker safety and health in the United States. | Wide range of industries, including oil & gas, manufacturing, and construction. |
API (American Petroleum Institute) | Standards specifically for the oil and gas industry, covering equipment design, operation, and maintenance. | Oil and gas production, refining, and transportation. |
EPA (Environmental Protection Agency) | Regulations focused on environmental protection, including controlling emissions and hazardous substance releases. | Industries that handle hazardous materials, including chemical processing and manufacturing. |
NFPA (National Fire Protection Association) | Standards addressing fire safety and prevention, including the handling of flammable and combustible materials. | Industries handling flammable materials, including chemical plants and storage facilities. |
Final Conclusion
In conclusion, effectively managing control valve and riser leaks requires a multi-faceted approach encompassing thorough inspection, systematic troubleshooting, and proactive maintenance. By understanding the root causes, implementing appropriate repair strategies, and adopting preventative measures, industries can minimize downtime, ensure safety, and enhance the overall operational efficiency of their systems. This guide offers a comprehensive roadmap for achieving these goals.
User Queries
What are common causes of control valve leaks besides faulty seals?
Improper installation, worn parts, pressure fluctuations, and incompatible materials can also lead to leaks. Operating conditions such as temperature and flow rate can also influence the likelihood of leakage.
What tools are necessary for troubleshooting valve and riser leaks?
Tools needed for troubleshooting may vary based on the severity and nature of the leak, but typically include visual inspection tools, pressure gauges, leak detection equipment, and potentially specialized wrenches and dismantling tools.
What are some preventative maintenance strategies to reduce leakage incidents?
Regular maintenance schedules, proper installation procedures, and using compatible materials for the specific application are key strategies to prevent leaks. Design considerations for valves and risers should also factor in the potential for leaks.
How do regulatory requirements affect leakage prevention?
Specific industries and locations have regulations regarding leakage prevention. Following safety protocols during inspection, repair, and maintenance is crucial, as well as having emergency response plans in place.