How to test oil pump effectively is crucial for maintaining optimal system performance and preventing costly breakdowns. This guide delves into the various methods for inspecting, pressurizing, and evaluating oil pump function, from visual inspections to detailed flow rate measurements. Understanding the specific needs of different oil pump types is key to accurate assessment and timely repairs.
Proper oil pump testing ensures efficient lubrication, critical for machinery longevity and safety. This comprehensive guide equips you with the knowledge and tools needed to confidently assess your oil pump’s health.
Introduction to Oil Pump Testing
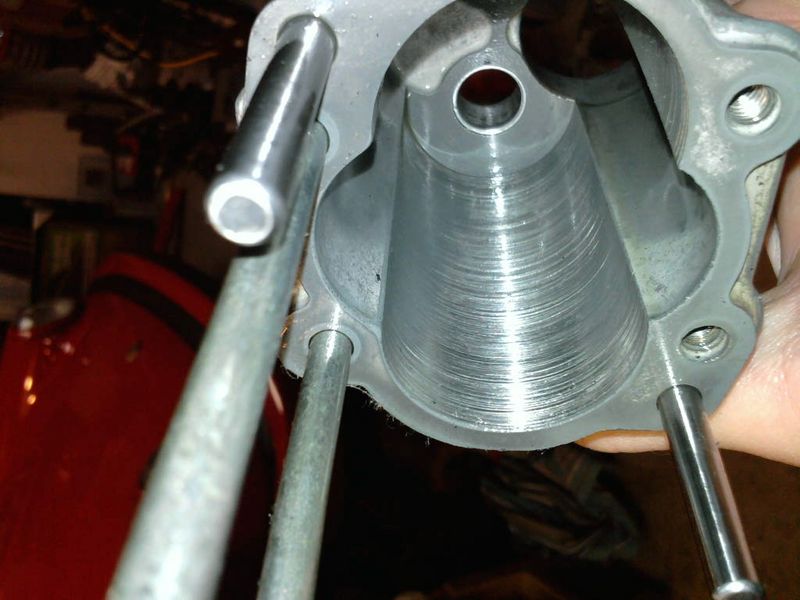
Yo, fam! Keeping your oil pump in tip-top shape is crucial for smooth operations, whether it’s your car, a machine at the factory, or even something at home. A faulty pump can lead to major headaches, from engine issues to breakdowns. So, let’s dive into how to check your oil pump like a pro.Understanding different oil pump types and their applications is key.
Knowing the pump type helps in determining the right testing procedures. Different pumps, like gear pumps, vane pumps, and axial pumps, have unique designs and functionalities, leading to varying maintenance needs. This knowledge is essential for preventing costly repairs and downtime.
Importance of Oil Pump Testing
Regular oil pump testing is vital for preventing major issues. A failing oil pump can cause engine damage, system failure, and potentially dangerous situations. Early detection of problems through testing allows for timely repairs, minimizing downtime and costly replacements. Imagine a factory production line halting because of a faulty pump – that’s a huge loss! Checking the pump regularly is a proactive step to avoid such scenarios.
Different Types of Oil Pumps and Their Applications
Oil pumps come in various designs, each with its own strengths and weaknesses. Here’s a quick rundown:
- Gear Pumps: These are common in many applications, from cars to industrial machinery. They’re known for their simplicity and reliability, but their efficiency can be lower compared to other types.
- Vane Pumps: These are often used in systems requiring a variable flow rate, like hydraulic systems. Their ability to adjust flow makes them versatile but potentially more complex to maintain.
- Axial Pumps: These are frequently found in high-pressure systems, often in heavy machinery. Their design allows for high flow rates, but they can be more sensitive to wear and tear.
Potential Consequences of Faulty Oil Pumps
A faulty oil pump can lead to a cascade of problems. Low oil pressure can cause engine damage, resulting in costly repairs. Insufficient lubrication can lead to component wear, reducing the lifespan of critical parts. It can also lead to overheating, causing further damage to your machinery. In short, a faulty oil pump is a recipe for disaster.
General Procedure for Inspecting an Oil Pump
A basic inspection involves visually checking for leaks, unusual noises, and signs of wear. Listen carefully for any unusual noises like grinding or screeching. Look for any obvious leaks or signs of fluid build-up around the pump. A thorough inspection helps identify potential issues before they escalate.
Comparing Oil Pump Types and Testing Procedures
This table provides a simplified comparison of oil pump types and their typical testing procedures.
Pump Type | Typical Applications | Testing Procedures |
---|---|---|
Gear Pump | Cars, small machinery | Check for leaks, listen for unusual noises, inspect the gear teeth for wear. |
Vane Pump | Hydraulic systems, variable flow | Check for leaks, verify proper vane movement, examine for wear on vanes. |
Axial Pump | High-pressure systems, heavy machinery | Check for leaks, verify proper shaft alignment, check for cavitation. |
Visual Inspection Techniques
Yo, peeps! So, you wanna check your oil pump without getting all greasy and technical? Visual inspection is your first stop, fam. It’s like a quick scan to spot any obvious problems before you dive into more complex tests. It’s crucial for identifying potential issues early, saving you time and headaches later.
Visual Inspection Steps
Visual inspection is all about methodically checking the pump for any signs of trouble. Start by gathering your tools – good lighting is key, and a magnifying glass helps if you’re extra thorough. Then, carefully examine each component, noting anything out of the ordinary.
- Examine the pump housing: Look for any cracks, dents, or unusual bulges. A distorted housing could indicate internal damage. Think of it like checking a car’s bumper – you don’t want any surprises.
- Inspect seals and gaskets: Check for any leaks, cracks, or signs of excessive wear on the seals and gaskets. A leaky seal means potential pressure loss and wasted oil.
- Inspect the bearings: Look for any signs of damage, scoring, or excessive play. Bad bearings can lead to noise and eventual failure. Imagine a rusty hinge – not ideal, right?
- Check for leaks: Inspect the entire pump for any leaks around the connections or fittings. A steady drip is a red flag. Think of it as a treasure hunt for tiny leaks – every little bit adds up!
- Note any unusual noises: Listen for unusual sounds during the inspection. Grinding or screeching noises can indicate problems with the bearings or other components. Think of a car with a grinding transmission; it’s not good news.
Common Visual Defects
Spotting these common problems early can save you a major repair bill down the line.
- Leaks: Leaks are a common problem. Look for oil stains around the pump or on the surrounding surfaces. A steady leak means a potential pressure issue. Think of a dripping faucet – you need to fix it.
- Damage: Check for any cracks, dents, or other damage to the pump housing or components. Physical damage can compromise the pump’s integrity and lead to failure. Imagine a cracked phone screen; it’s not going to last.
- Wear: Look for signs of wear and tear on the seals, gaskets, and bearings. Excessive wear can lead to leaks, decreased efficiency, and eventual failure. Imagine a well-worn pair of shoes – they need replacing eventually.
Importance of Lighting
Proper lighting is essential for a thorough visual inspection. Poor lighting can obscure small defects, leading to missed problems. Good lighting ensures you see every detail clearly. Think of trying to find a tiny screw in a dark room – hard to do, right?
Visual Inspection Checklist
This table provides a quick reference for checking different types of oil pumps.
Oil Pump Type | Inspection Points |
---|---|
Gear Pump | Housing, seals, gaskets, bearings, shaft alignment, gears, lubrication |
Screw Pump | Housing, seals, gaskets, bearings, screws, lubrication |
Centrifugal Pump | Housing, seals, gaskets, bearings, impeller, shaft alignment, lubrication |
Pressure Testing Procedures

Yo, pump heads! Pressure testing is crucial for makin’ sure your oil pump is pumpin’ like a boss. It’s like a health check for your mechanical heart, identifyin’ any potential issues before they become major problems. Let’s dive into the nitty-gritty of how to do it right!This section breaks down the steps for pressure testing an oil pump, equipin’ you with the tools and knowledge to do it safely and effectively.
We’ll cover the essential equipment, proper connection methods, and how to interpret the pressure readings. It’s all about makin’ sure your pump is workin’ at peak performance!
Equipment Needed for Pressure Testing
To nail this pressure test, you need the right tools. This isn’t rocket science, but you gotta have the right gear to get the job done right.
- A reliable pressure gauge capable of measuring the expected pressure range for your oil pump. This is a must-have. Make sure it’s calibrated and in good working order, otherwise, your results will be off, which is a total no-no.
- Appropriate pressure hoses and fittings to connect the pressure gauge to the oil pump’s output port. Matching the right size and type of hose to the pump and gauge is key to avoid leaks and ensure accurate readings. A leak can throw off your readings.
- Safety glasses and gloves are a must! It’s not just about lookin’ cool, it’s about protecting yourself from potential hazards during the testing process. Always wear the proper safety gear.
- A suitable container to catch any potential oil leaks. This is a super important part of the process.
Step-by-Step Pressure Testing Procedure
This step-by-step guide will walk you through the pressure test procedure, makin’ it as easy as ABC.
- Prepare the oil pump. Make sure the pump is clean, and the oil reservoir is filled with the correct type of oil for the application. Check all connections and make sure everything is tight. Also, check that the pump is properly lubricated.
- Connect the pressure gauge securely to the oil pump’s output port using the appropriate hoses and fittings. This is a critical step; ensure a tight connection to prevent leaks and inaccurate readings. Use the correct size and type of fittings for the pump and gauge.
- Start the oil pump at a slow speed. This will let the pump build pressure gradually. Gradually increase the pump speed, but do it in a controlled manner. This way, you can observe the pressure changes as the speed increases.
- Monitor the pressure readings on the gauge as the pump operates. Note the pressure readings at various speeds and keep track of the data. Record your readings.
- Maintain a safe operating speed for the oil pump. Don’t push it too hard, and be mindful of any unusual pressure fluctuations. Make sure the pump isn’t overheating or straining.
- Compare the pressure readings with the expected values. This comparison will help determine if the oil pump is functioning correctly. Make sure you compare the readings with the specified pressure ranges for your specific application. Check the manufacturer’s specifications.
- Disconnect the pressure gauge and clean up any spills. Make sure to properly dispose of any waste oil. Clean all equipment used in the test and put them away properly.
Pressure Ranges for Various Applications
Different oil pumps have different pressure requirements depending on the application. This table provides a general guideline for different applications.
Application | Expected Pressure Range (psi) |
---|---|
Hydraulic System | 1000-3000 |
Lubrication System | 20-50 |
Industrial Machinery | 500-2000 |
Automotive | 50-150 |
Flow Rate Testing Methods
Yo, pump enthusiasts! Flow rate testing is crucial for making sure your oil pump is performin’ like a champ. Knowing how much oil it’s pumpin’ per minute is key for everything from proper lubrication to preventing system issues. Let’s dive into the different methods and gear needed to get the job done right.
Various Flow Rate Measurement Methods
Different methods exist for measuring oil flow rate, each with its own pros and cons. The best choice depends on the pump type and the accuracy needed. Some common methods include volumetric measurements, using calibrated tanks, and more advanced flow meters.
- Volumetric Measurement: This method involves using calibrated containers to catch the oil pumped over a specific time period. It’s a relatively simple and affordable method for rough estimates. However, it can be less precise than other methods, especially if the oil flow isn’t steady.
- Flow Meters: These are devices specifically designed to measure fluid flow rate. Different types exist, each with varying degrees of accuracy and complexity. Turbine flow meters measure the rotation speed of a turbine, while positive displacement flow meters count the number of times a chamber fills and empties. These are generally more accurate and versatile than volumetric methods, especially for precise measurements.
For example, a turbine flow meter would be suitable for a high-volume industrial pump, while a more basic flow meter could suffice for a small-scale hydraulic system.
- Time-Based Calculation: This method uses a known volume and a measured time to calculate flow rate. For instance, if a tank of 10 liters fills up in 2 minutes, the flow rate is 5 liters per minute. This approach is practical when high accuracy isn’t critical. Useful for quick checks, but not ideal for precise readings.
Equipment for Flow Rate Testing
Getting the right tools is essential for accurate flow rate testing. The equipment needed will depend on the method you choose.
- Calibrated Containers/Tanks: These containers should be meticulously calibrated to ensure accuracy. For example, a 1-liter graduated cylinder is suitable for smaller flow rates, while a larger tank might be necessary for high-volume pumps.
- Stopwatch/Timer: An accurate stopwatch is crucial for timing the oil flow duration.
- Flow Meters: Different flow meters are available, ranging from simple, affordable ones to sophisticated digital instruments. Consider the pump’s flow rate and required accuracy when choosing a flow meter.
- Oil Pump: Obviously, you need the pump you want to test!
Calculating Flow Rate
The calculation for flow rate depends on the method used. For volumetric measurement, the formula is straightforward:
Flow Rate (Q) = Volume (V) / Time (t)
Where:
- Q is the flow rate (e.g., liters per minute, gallons per hour)
- V is the volume of oil collected (e.g., liters, gallons)
- t is the time taken for the volume to be collected (e.g., minutes, hours)
Comparison of Flow Rate Measurement Devices
Different flow rate measurement devices have varying advantages and disadvantages.
- Volumetric Methods: Simple, inexpensive, but less accurate for precise measurements.
- Flow Meters: More accurate and versatile, but often more expensive.
Flow Rate Testing Procedure Table
This table Artikels the equipment and procedures for flow rate testing different pump types.
Pump Type | Measurement Method | Equipment Needed | Procedure |
---|---|---|---|
Small Hydraulic Pumps | Volumetric | Calibrated beaker, stopwatch | Collect oil in beaker for a set time. Calculate flow rate. |
Large Industrial Pumps | Flow Meter | Turbine flow meter, timer | Connect flow meter to pump output. Record flow rate reading. |
Component-Specific Testing
Yo, pump heads! Let’s dive into the nitty-gritty of checking specific parts in your oil pump. Knowing how each component performs is crucial for keeping your pump in tip-top shape and avoiding major headaches down the line. We’ll break down gear, vane, and shaft testing, plus the potential problems and how they affect the whole pump.
Gear Inspection
Gear wear is a common issue in oil pumps. Proper gear inspection is key to preventing costly repairs. Bent or chipped gears lead to leaks, reduced efficiency, and eventually, pump failure. The crucial thing is to catch these problems early.
- Visual Inspection: Check the gears for any signs of damage, like nicks, dents, or cracks. Look for excessive wear on the teeth. This is like checking your shoes—notice any damage before they fall apart.
- Lubrication Analysis: If the oil looks weird (like it has metal flakes or isn’t as smooth as it should be), it’s a sign of potential gear wear. This is a bit like checking your engine oil. Abnormal color or texture can point to trouble.
- Dimensional Measurements: Use calipers to measure the gear’s thickness and teeth spacing. Compare these measurements against the manufacturer’s specs to find out if there’s any significant wear.
Vane Assessment, How to test oil pump
Vanes are crucial for oil pumps that use a vane-type design. Damage to these vanes can cause serious performance issues.
- Visual Inspection: Look closely at the vanes for any signs of warping, cracking, or detachment. Make sure they’re firmly attached to the housing. It’s like checking the wings of a plane – any damage could cause trouble in the air.
- Microscopic Analysis: Under a microscope, you can see tiny imperfections on the vanes that might not be visible to the naked eye. This can help spot early wear.
- Functional Test: If possible, test the pump’s flow rate while monitoring the vane movement. Any unusual noises or vibrations could indicate a problem with the vanes.
Shaft Examination
Shaft problems can be a real pain in the neck for oil pumps. It’s crucial to examine them carefully.
- Visual Inspection: Inspect the shaft for any bends, cracks, or corrosion. Look for unusual wear patterns on the shaft’s surface. This is like checking the steering wheel of a car. Any issues will affect the overall drive.
- Hardness Testing: Measure the shaft’s hardness using a Rockwell hardness tester. This will give you an idea of how well it can withstand stress. It’s like checking the strength of a metal beam.
- Alignment Check: Ensure the shaft is properly aligned with the other components. Misalignment can lead to vibrations and premature wear.
Component Performance and Testing Table
Component | Expected Performance | Testing Procedures |
---|---|---|
Gears | Smooth rotation, no unusual noises, no visible damage | Visual inspection, lubrication analysis, dimensional measurements |
Vanes | Firm attachment, smooth movement, no vibrations | Visual inspection, microscopic analysis, functional test |
Shafts | Straight, no bends or cracks, proper alignment | Visual inspection, hardness testing, alignment check |
Troubleshooting Common Oil Pump Issues
Nah, dealing with a wonky oil pump can be a real headache. It’s like trying to fix a leaky faucet in a monsoon—you gotta know what’s causing the problem before you can fix it. This section dives into common oil pump problems, their telltale signs, and the steps to diagnose and solve ’em.
Identifying Common Oil Pump Problems
Understanding the common issues with oil pumps is key to efficient troubleshooting. Different problems manifest in distinct ways, impacting the pump’s performance and potentially causing damage to your system. Recognizing these signs is the first step towards a speedy fix.
Symptoms of Oil Pump Problems
Oil pump issues often show up in subtle ways at first, but if ignored, they can escalate into major headaches. Here’s a look at the common symptoms:
- Low oil pressure: This is a major red flag. Low pressure means the pump isn’t circulating oil adequately, which can lead to engine damage. It’s like your body not getting enough blood flow—critical for everything to function smoothly. You might notice this with an oil pressure gauge reading below the specified minimum.
- Oil leaks: A telltale sign of a potential internal or external oil pump problem. Leaks can be subtle drips or gushing streams, depending on the severity. This is a big warning sign that something might be amiss with your oil pump’s seals or housing.
- Unusual noises: A noisy oil pump is another common symptom. Strange grinding, whirring, or clicking sounds might indicate a problem with the pump’s internal components. This is like a car with a weird engine sound—something is wrong.
- Pump not starting: If your oil pump refuses to kick on, it’s a significant issue. This could indicate a power supply problem, or even a blockage in the oil line. This is like your car’s engine not starting – a serious issue.
- Oil overheating: High oil temperatures can point to a clogged filter, low oil flow, or even a problem with the pump itself. Overheated oil can cause significant damage to your system. This is like letting your engine overheat – it’s a major warning sign.
Potential Causes of Oil Pump Problems
Several factors can contribute to oil pump malfunctions. Understanding the potential causes helps you target the right solution.
- Clogged oil filters: A clogged oil filter restricts oil flow, leading to low pressure and overheating. It’s like having a clogged drain in your house—it backs up and creates problems.
- Damaged or worn-out seals and bearings: Over time, seals and bearings can wear down, causing leaks and reduced performance. This is like a car tire with a flat—it won’t work properly.
- Electrical issues: Problems with the electrical components that power the pump can prevent it from functioning correctly. This is like your fridge not working because the power is off.
- Internal pump damage: Impact or damage to the pump’s internal components, like the impeller or gears, can cause serious issues. This is like a broken part inside your car engine.
- Incorrect oil viscosity: Using oil with the wrong viscosity can affect the pump’s performance. This is like putting the wrong kind of fuel in your car—it won’t run right.
Troubleshooting Steps for Oil Pump Problems
Troubleshooting involves systematic investigation to identify the root cause. Here’s a breakdown of steps to take:
- Check oil pressure: Use an oil pressure gauge to determine if the pressure is within the manufacturer’s specifications. This is the first step to diagnose the issue.
- Inspect for leaks: Visually inspect the pump and surrounding areas for any leaks. This is a critical step in finding the problem.
- Listen for unusual noises: Pay close attention to any unusual noises coming from the pump. This could point to a damaged component.
- Check the electrical connections: Ensure all electrical connections are secure and functioning correctly. This could be a simple solution.
- Replace worn parts: If any parts are damaged or worn out, replace them with new ones. This is a common solution.
Summary Table of Oil Pump Issues
Issue | Symptoms | Potential Causes | Troubleshooting Steps |
---|---|---|---|
Low Oil Pressure | Low oil pressure gauge reading, engine misfiring, etc. | Clogged filter, worn seals/bearings, internal damage, etc. | Check filter, inspect seals/bearings, check for internal damage, etc. |
Oil Leaks | Visible oil leaks from the pump housing, etc. | Damaged seals/bearings, cracks in housing, etc. | Inspect seals/bearings, repair or replace damaged parts, etc. |
Unusual Noises | Grinding, whirring, or clicking sounds | Worn bearings, damaged gears, etc. | Inspect bearings, check gears for damage, etc. |
Pump Not Starting | Pump doesn’t turn on | Electrical problems, power supply issues, etc. | Check electrical connections, ensure power supply is working, etc. |
Oil Overheating | High oil temperature | Clogged filter, low oil flow, etc. | Check filter, ensure adequate oil flow, etc. |
Safety Precautions During Testing
Testing an oil pump ain’t no joke, bro. Safety first, always. Neglecting precautions can lead to serious accidents, from minor scrapes to major injuries. It’s way better to be safe than sorry, especially when dealing with potential hazards like high pressure, moving parts, and potentially harmful fluids.Proper safety procedures and gear are crucial to prevent accidents and ensure everyone involved is safe and sound.
Following manufacturer guidelines and using the right equipment are key for a smooth and successful test.
Potential Hazards
Oil pump testing involves various potential hazards. High-pressure oil can cause serious injuries if not handled correctly. Loose or damaged components can cause flying debris, potentially injuring personnel nearby. Leaks of oil, especially certain types, can pose environmental and health risks. Lastly, the machinery itself can have moving parts that are dangerous if not properly guarded or operated.
Safety Equipment and Procedures
Appropriate safety gear is paramount during testing. Always wear safety glasses or goggles to protect your eyes from flying debris or splashes. Heavy-duty gloves should be worn to prevent skin contact with oil and other potential hazards. Hearing protection is important for loud noises that might occur during testing. Proper footwear that protects your feet is a must, too.
Lastly, ensure that the area is well-lit and clear of obstacles to maintain good visibility and avoid tripping hazards.
Following Manufacturer Guidelines
Manufacturers provide crucial information regarding safe operating procedures and potential hazards. Thoroughly reading and understanding these guidelines is essential. Following these guidelines prevents potential accidents and ensures the test is conducted correctly. Don’t just glance at it; make sure you grasp the nuances and specifics.
Safety Guidelines and Procedures
Safety Guideline | Procedure |
---|---|
Eye Protection | Always wear safety glasses or goggles. |
Hand Protection | Wear heavy-duty gloves to prevent skin contact with oil. |
Foot Protection | Use appropriate safety shoes or boots. |
Hearing Protection | Use earplugs or muffs if necessary. |
Protective Clothing | Wear appropriate clothing that covers exposed skin to prevent accidental contact with moving parts. |
Clear Workspace | Ensure the work area is clear of obstacles and well-lit. |
Lockout/Tagout Procedures | Follow lockout/tagout procedures to prevent unintended start-up of equipment. |
Proper Handling of Oil | Use appropriate oil handling procedures to prevent spills and leaks. |
Emergency Procedures | Know and practice emergency procedures in case of accidents. |
Illustrative Examples
Yo, so you wanna see how to actually test these oil pumps? Let’s break it down with some real-world examples. We’ll cover a typical pump, the testing process step-by-step, and some crucial tools. Get ready to level up your oil pump game!
Typical Oil Pump and Its Parts
This ain’t rocket science, but understanding the parts is key. A typical gear pump, for example, usually has an inlet, outlet, gears, a casing, and a drive shaft. The gears spin, creating suction at the inlet and pushing oil out through the outlet. The casing houses everything, and the drive shaft connects the pump to its power source.
Different types of pumps, like vane or piston pumps, have varying components, but the core idea is the same: move the oil.
Oil Pump Testing Process
Alright, let’s map out the testing steps. First, visually inspect the pump for any obvious damage. Look for leaks, cracks, or anything amiss. Then, pressure test the pump to ensure it’s pushing oil at the right pressure. Finally, check the flow rate to see how much oil it’s moving.
Each step builds on the previous one, like a domino effect, making sure everything is functioning smoothly.
Detailed Diagram of Oil Pump Components
Imagine a simple gear pump, with the casing like a box. Inside, you see two gears meshing, and an inlet pipe leading into the pump, and an outlet pipe coming out. The drive shaft, connecting to a motor, spins the gears. This diagram visually shows how the gears move oil.
Using Tools to Test Oil Pumps
Different tools are crucial for testing oil pumps. A pressure gauge helps measure the pressure the pump generates. A flow meter precisely determines the volume of oil the pump moves per unit of time. A multimeter can help you check the electrical connections to the pump if it’s electric. You’ll also need a torque wrench if you’re working on the drive shaft.
Each tool has a specific role in verifying the pump’s performance.
Types of Oil Pump Testing Equipment
Here’s a visual representation of the tools we just talked about:
Tool | Description |
---|---|
Pressure Gauge | Measures the pressure generated by the pump. |
Flow Meter | Measures the volume of oil flowing per unit of time. |
Multimeter | Checks electrical connections to the pump. |
Torque Wrench | Used for tightening/loosening the drive shaft. |
These tools, like pressure gauges, flow meters, and multimeters, are essential for precise and accurate testing. Each plays a vital role in verifying the pump’s output.
Final Wrap-Up: How To Test Oil Pump
In conclusion, testing an oil pump involves a multi-faceted approach encompassing visual checks, pressure evaluations, flow rate measurements, and component-specific examinations. By following the Artikeld procedures and safety precautions, you can ensure your oil pump operates at peak efficiency and avoid potential issues. Remember, proper maintenance through regular testing contributes to the long-term reliability and performance of your equipment.
Commonly Asked Questions
What are the typical pressure ranges for different oil pump applications?
Pressure ranges vary significantly depending on the application. A table in the full guide will detail the typical pressure ranges for various types of oil pumps and their intended use. Consult the manufacturer’s specifications for precise recommendations.
What equipment is needed for flow rate testing?
Flow rate testing requires specialized equipment such as flow meters, which come in various types depending on the volume and viscosity of the oil being measured. The selection of the right equipment is critical for accurate results. Detailed information on the different flow meters and their usage is covered in the full guide.
How can I identify common visual defects in an oil pump?
Visual defects include leaks, cracks, damage to the housing, seals, and bearings. A detailed visual inspection checklist, specific to different pump types, is provided in the guide. Pay close attention to any unusual noises or vibrations during the visual inspection.
What safety precautions should I take during oil pump testing?
Always prioritize safety. The guide includes a detailed section on safety precautions, including proper personal protective equipment (PPE) and adherence to manufacturer guidelines. Understanding potential hazards and proper handling procedures is essential for a safe testing environment.