How to tighten hose clamp effectively is crucial for preventing leaks and ensuring system integrity. Proper tightening techniques depend on the type of clamp, the application, and the potential hazards involved. This guide delves into the essentials of hose clamp tightening, from identifying potential issues to advanced techniques for specialized situations.
Hose clamps are essential for maintaining pressure and preventing leaks in various applications, from plumbing to automotive systems. Understanding the different types of clamps, their materials, and appropriate tightening methods is vital for optimal performance and safety. This comprehensive guide provides a step-by-step approach, highlighting critical considerations and safety precautions.
Introduction to Hose Clamps
Hose clamps are essential fastening devices used to securely connect and hold hoses in place. They prevent leaks and ensure the proper functioning of various systems, from plumbing and HVAC to automotive and industrial applications. Their simple yet effective design allows for quick and reliable joining of hoses and tubing.Hose clamps are crucial for maintaining pressure integrity and preventing leaks in pressurized systems.
Properly tightened clamps prevent hose failure, which can lead to costly repairs, downtime, and safety hazards. A well-maintained clamp system ensures consistent performance and longevity of the connected equipment.
Types of Hose Clamps
Hose clamps are available in diverse designs, each optimized for specific applications. Understanding the different types and their characteristics is crucial for selecting the right clamp for a particular job. Spring clamps, cam clamps, and band clamps each possess unique strengths and weaknesses, influencing their suitability for different scenarios.
Spring Clamps
Spring clamps are the most common type, featuring a coiled spring mechanism. This design allows for a relatively wide range of adjustments to accommodate various hose sizes and diameters. The spring provides a continuous clamping force, holding the hose securely in place.
Cam Clamps
Cam clamps use a lever mechanism for tightening. Their advantage lies in the quick and precise clamping action, particularly suitable for applications where rapid assembly or disassembly is necessary. Cam clamps are often preferred for high-pressure situations due to their ability to exert significant clamping force.
Band Clamps
Band clamps, also known as hose straps, consist of a band of metal that is wrapped around the hose. This design offers excellent security, especially for large-diameter hoses. The robust construction ensures strong clamping forces, ideal for high-stress environments and heavy-duty applications.
Materials Used in Hose Clamp Construction
Hose clamps are constructed from various materials, each influencing the clamp’s strength, corrosion resistance, and overall performance. Common materials include stainless steel, galvanized steel, and aluminum. The selection of material is crucial in ensuring the clamp’s suitability for the specific application and environment.
Comparison of Hose Clamp Types
Type | Material | Strength | Applications |
---|---|---|---|
Spring Clamp | Steel, Stainless Steel | Moderate | General purpose, medium pressure applications, plumbing, HVAC |
Cam Clamp | Steel, Stainless Steel | High | High-pressure applications, automotive, industrial machinery |
Band Clamp | Steel, Stainless Steel | Very High | Large diameter hoses, high-stress environments, heavy-duty machinery |
Identifying the Problem
Properly functioning hose clamps are critical for maintaining the integrity of fluid systems. Neglecting loose or faulty clamps can lead to leaks, system failures, and potential safety hazards. A proactive approach to identifying problems is crucial for preventing costly repairs and downtime.A faulty hose clamp is not always immediately obvious. Early detection is key to preventing escalating damage.
Recognizing the subtle signs of a compromised clamp can save time and money.
Signs of a Loose or Faulty Hose Clamp
Hose clamps, over time, can lose their clamping force due to various factors. This can lead to leaks and potential system damage. Identifying the signs of a compromised clamp is essential for timely intervention. Signs include visible movement of the hose relative to the fitting, or the hose itself bulging or vibrating excessively. These visual indicators are often accompanied by other tell-tale signs.
Potential Causes of Hose Clamp Failure
Hose clamp failure is not a random occurrence. It often stems from factors related to the clamp itself, the application, or environmental conditions. Material degradation, improper installation, and excessive vibration are significant culprits. Corrosion, for instance, can weaken the metal of the clamp, rendering it ineffective.
Identifying the Root Cause of a Loose Hose Clamp
Pinpointing the precise reason for a loose hose clamp is often a multi-step process. It requires a thorough assessment of the clamp, the hose, and the surrounding environment. Careful observation of the clamp’s physical condition, the hose’s integrity, and the operational stresses on the system are vital. Considering environmental factors, such as exposure to harsh chemicals or extreme temperatures, can provide additional insights.
Table of Symptoms and Possible Causes
Symptom | Possible Causes |
---|---|
Visible movement of the hose relative to the fitting | Improper installation, excessive vibration, material degradation, corrosion |
Hose bulging or vibrating excessively | Undersized clamp, incorrect clamp type, excessive pressure, improper tightening, material degradation |
Leak at the clamp location | Loose clamp, damaged hose, incorrect clamp type, over-tightening |
Clamp deformation or breakage | Over-tightening, material degradation, improper clamp selection, excessive vibration |
Hose kinking or damage | Undersized clamp, improper installation, incorrect clamp type, improper tightening |
Tools and Materials Needed
Proper tightening of hose clamps is crucial for preventing leaks and ensuring the longevity of your plumbing or other systems. Neglecting the right tools and materials can lead to costly repairs and safety hazards. This section details the essential tools and materials needed for various hose clamp types, ensuring a secure and efficient clamping process.
Essential Tools
Correct tools are paramount for achieving a secure and lasting seal. Improper tools can damage the hose or clamp, leading to leaks or failure. The specific tools needed depend on the size and type of clamp. A well-equipped toolbox is a necessity for reliable hose clamping.
- Pliers (adjustable or slip-joint): Essential for gripping and tightening hose clamps. Different sizes of pliers cater to various clamp sizes, ensuring a snug fit without damaging the clamp or hose. Always choose pliers appropriate for the clamp size to avoid stripping the threads or bending the clamp.
- Screwdrivers (flathead or Phillips): Necessary for tightening certain types of hose clamps, particularly those with screws or fasteners. A screwdriver appropriate for the screw type is vital to prevent stripping the screw head or damaging the clamp.
- Wrench (adjustable or specific): Used for tightening hose clamps that require a specific torque or those that are difficult to grip with pliers. Using a wrench appropriate for the clamp and hose is crucial to avoid damaging the hose or clamp.
- Torque wrench (optional but recommended): Crucial for ensuring consistent tightening force, preventing over-tightening that could damage the hose or clamp. A torque wrench allows you to apply a specific amount of torque to the clamp, which is critical for maintaining the integrity of the system. For instance, over-tightening a clamp on a high-pressure system could cause it to leak, while under-tightening might not provide sufficient pressure to seal the connection.
Clamp-Specific Tools
Certain hose clamp types require specialized tools for optimal tightening. For example, some clamps have unique designs or materials that necessitate specific tools for efficient handling.
- Clamp type with unique design: Specific pliers, wrenches, or other tools may be needed for certain clamps. These clamps may have unique features requiring specialized tools for handling.
- Clamp type with non-standard threads: A specialized wrench designed to fit the specific thread pattern of the clamp is required. Using an improper wrench could result in damage to the clamp or hose.
Necessary Materials, How to tighten hose clamp
Lubricants can significantly improve the tightening process and prevent damage to the hose or clamp.
- Lubricant (e.g., graphite, dielectric grease): Applying a lubricant to the clamp and hose before tightening can reduce friction and prevent damage. This is especially important with rubber or plastic hoses. Lubricants help the clamp slide smoothly onto the hose, reducing the risk of damage to the hose or clamp.
Tools and Their Functions
A table outlining the tools and their functions for tightening hose clamps.
Tool | Function |
---|---|
Pliers (adjustable or slip-joint) | Gripping and tightening hose clamps |
Screwdrivers (flathead or Phillips) | Tightening clamps with screws or fasteners |
Wrench (adjustable or specific) | Tightening clamps requiring specific torque or difficult to grip |
Torque wrench (optional but recommended) | Ensuring consistent tightening force and preventing over-tightening |
Procedures for Tightening
Properly tightening hose clamps is crucial for preventing leaks and ensuring the longevity of your system. Improper tightening can lead to catastrophic failures, ranging from minor inconveniences to serious safety hazards. Understanding the nuances of tightening methods is paramount for achieving the optimal balance between secure connection and potential damage.Effective tightening ensures a secure connection without jeopardizing the hose or the fitting.
It requires precision and a methodical approach, taking into account the material properties of the hose and clamp, as well as the specific application. Ignoring these factors can result in premature failure and potential safety issues.
Hand-Tightening Procedures
Hand-tightening is often the initial step in tightening a hose clamp. It provides a tactile feel for the appropriate level of tension. This method is suitable for initial adjustments and preliminary tightening. However, it can be unreliable for achieving consistent torque.
- Position the clamp over the hose and fitting, ensuring proper alignment. Improper alignment can lead to uneven clamping pressure and potential leaks.
- Begin by hand-tightening the clamp in a clockwise direction, applying consistent pressure. This step is vital for establishing a firm initial grip.
- Gradually increase the tightening force. Observe the clamp for any signs of distortion or excessive strain on the hose. Avoid overtightening, as this can damage the hose and reduce its lifespan.
- Assess the tightness. The clamp should be snug but not excessively tight. Excessive tightness can deform the hose and compromise its integrity.
Using Tools for Tightening
Using a wrench or similar tool can provide greater precision and consistency in tightening. Tools offer a more controlled method for achieving the correct torque, eliminating the potential for over-tightening.
- Select a wrench appropriate for the size of the clamp and the required tightening force. An improperly sized wrench can result in damage or inadequate tightening.
- Position the wrench on the clamp’s adjusting mechanism, ensuring proper alignment. Ensure that the wrench is properly positioned to avoid slippage or damage.
- Apply consistent torque to the clamp, rotating the wrench in a clockwise direction. A consistent tightening force is vital for achieving a uniform clamping pressure.
- Monitor the tightness of the clamp during the tightening process. Signs of loosening, slippage, or unusual noises indicate improper tightening or an issue with the clamp itself.
Importance of Torque
Proper torque is essential for preventing hose leaks and ensuring the longevity of the system. Over-tightening can damage the hose, while under-tightening can lead to leaks. The appropriate torque is dependent on the specific hose and clamp specifications.
The ideal torque value should be determined from the manufacturer’s specifications for the hose and clamp combination. Failing to adhere to these specifications can lead to failures.
Applying Tension Correctly
Applying tension to the clamp should be done evenly across the entire circumference of the hose. Uneven tension can cause localized stress and damage. Employing a steady, controlled approach is key to achieving uniform tension.
- Distribute the clamping pressure evenly. Avoid concentrating the tightening force in a single area, which can damage the hose or cause leaks.
- Apply consistent force to avoid excessive tension in one section. This is crucial to ensure the integrity of the hose and prevent damage.
- Inspect the hose for any signs of damage or deformation. Any signs of deformation suggest the need to reduce the tightening force.
Comparison of Tightening Methods
Hand-tightening is suitable for preliminary tightening but lacks precision and control. Using tools offers greater precision and consistency in achieving the desired torque. The choice of method depends on the specific application and the required level of accuracy.
Method | Precision | Control | Torque Consistency |
---|---|---|---|
Hand-tightening | Low | Low | Low |
Tool-assisted tightening | High | High | High |
Common Mistakes and Troubleshooting
Improper tightening of hose clamps is a frequent source of leaks and system failures in various applications, from plumbing to automotive systems. Ignoring proper techniques can lead to costly repairs and potential safety hazards. This section details common errors, their consequences, and troubleshooting strategies to ensure secure connections.Over-tightening and under-tightening are two critical errors that often lead to premature failure.
Understanding these pitfalls and the associated solutions is crucial for maintaining efficient and safe systems.
Common Mistakes in Hose Clamp Tightening
Incorrect tightening techniques are a significant contributor to hose clamp failures. Understanding the proper procedure is paramount to preventing issues. Inaccurate application of force, neglecting the proper clamping surface area, and using the wrong clamp type for the hose are common errors. Failing to observe these critical details can lead to significant problems.
Consequences of Over-Tightening and Under-Tightening
Over-tightening a hose clamp can damage the hose material, leading to leaks or even hose rupture. The excessive force can distort the hose’s internal structure, creating weak points prone to failure. Conversely, under-tightening allows the hose to vibrate or move, potentially leading to leaks or detachments. Both scenarios can compromise the system’s functionality and safety. The consequences of improper tightening range from minor leaks to major system failures.
Troubleshooting Tightening Resistance
If a hose clamp resists tightening, several factors might be at play. The hose may be damaged or constricted, preventing proper clamping. Corrosion on the hose or clamp material can also create friction. Another possibility is that the clamp is the wrong size for the hose diameter, leading to inadequate clamping force. Identifying the root cause is critical for successful resolution.
Removing and Replacing Damaged Hose Clamps
Damaged or corroded hose clamps should be replaced immediately to prevent leaks and potential system failure. Carefully loosen the clamp using appropriate tools. Once the clamp is removed, inspect the hose for damage. Replace the damaged hose section if necessary, and install a new, appropriate-sized clamp. This procedure ensures a secure and reliable connection.
Table of Common Mistakes and Solutions
Mistake | Solution |
---|---|
Over-tightening the clamp | Use a gentle, consistent tightening force, ensuring even distribution of pressure. |
Under-tightening the clamp | Ensure the clamp fully encircles the hose and is correctly tightened. Adjust the clamp size if necessary. |
Incorrect clamp size | Select a clamp with a diameter that precisely matches the hose’s outer diameter. |
Damaged hose or clamp | Replace the damaged hose and/or clamp with new components. |
Corrosion on clamp or hose | Clean the affected areas and ensure they are free from corrosion before re-tightening or replacement. |
Safety Precautions
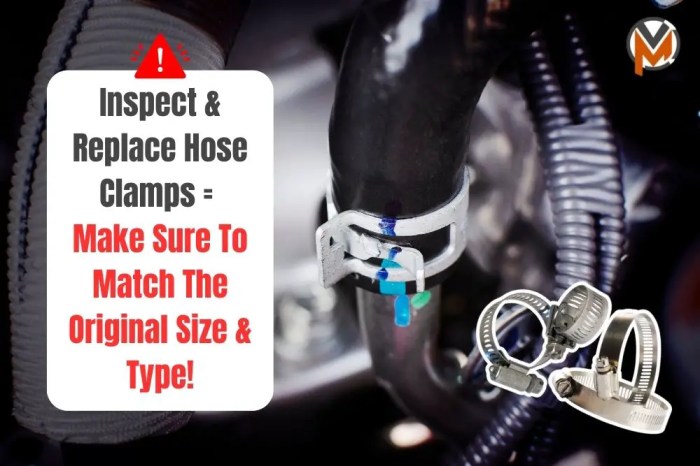
Properly tightening hose clamps is crucial, but safety must always be paramount. Neglecting safety precautions can lead to severe injuries and equipment damage. This section Artikels essential safety measures to ensure a safe and efficient clamping process.Improper tightening techniques can lead to serious hazards. For instance, over-tightening can cause hose damage, potentially leading to leaks or bursts.
Conversely, under-tightening can result in hose slippage and failure, with catastrophic consequences depending on the application. Always adhere to the manufacturer’s specifications and use appropriate tools.
Hazard Identification and Mitigation
Hose clamps and associated components can present various hazards. High-pressure systems, sharp edges, and the potential for leaks of corrosive or hazardous fluids are key considerations. Identifying and mitigating these risks is critical to preventing accidents. Always assess the potential hazards of the specific application before beginning any tightening procedure.
Personal Protective Equipment (PPE) Requirements
Adequate PPE is indispensable for a safe clamping operation. The specific PPE required depends on the environment and the materials involved. For instance, if working with pressurized systems, safety glasses or goggles are mandatory to protect the eyes from flying debris or potential fluid splashes. Gloves are essential to protect hands from cuts, abrasions, and chemical exposure.
Always wear appropriate footwear to prevent slips and falls. The choice of PPE should be based on the potential hazards present in the specific situation.
Specific Safety Measures
A detailed list of safety precautions should be meticulously followed for every clamping procedure.
- Inspect Equipment: Before starting any tightening operation, thoroughly inspect the hose, clamp, and all associated equipment for any damage or defects. A damaged clamp or hose could lead to premature failure, posing a risk of leakage or explosion.
- Isolate the System: If working with pressurized systems, always isolate the system from the power source before starting any clamping work. This prevents unexpected activation and potential injury. Failure to isolate could lead to a dangerous situation.
- Proper Handling of Materials: If the system contains hazardous materials, use appropriate handling procedures. Consult Material Safety Data Sheets (MSDS) to understand the properties of the materials and the necessary precautions for safe handling. Improper handling can expose personnel to dangerous chemicals.
- Secure the Area: Ensure the work area is clear and well-lit to prevent tripping hazards. Properly secure any potential tripping hazards. Ensure that the area is well-ventilated, particularly if working with chemicals or in enclosed spaces.
- Proper Tool Usage: Use the appropriate tools for tightening the hose clamps. Using the wrong tools can damage the hose or clamp and increase the risk of injury. Inappropriate tools can lead to accidents.
- Emergency Procedures: Familiarize yourself with emergency procedures and the location of emergency equipment. Have a clear escape route. Knowing emergency procedures and having appropriate emergency equipment available can save lives in case of an accident.
Consequences of Ignoring Safety
Ignoring safety precautions can have severe consequences. Over-tightening or under-tightening can lead to hose failure, leaks, and potentially dangerous situations. These situations can cause significant damage to equipment and even lead to personal injury. The consequences can range from minor injuries to serious accidents. Always prioritize safety above all else when working with hose clamps.
Advanced Techniques (Optional): How To Tighten Hose Clamp
Properly tightening hose clamps is critical for maintaining system integrity and preventing leaks. While basic procedures suffice for many applications, advanced techniques are essential for specialized situations, ensuring optimal performance and longevity. Ignoring these advanced methods can lead to costly repairs and safety hazards.Advanced techniques are vital for specific applications, such as high-pressure systems, hard-to-reach areas, and unique hose clamp configurations.
Understanding these methods allows for a more precise and effective tightening process, ultimately preventing potential issues.
Specialized Hose Clamp Types
Different hose clamp designs cater to specific needs. Understanding these variations is crucial for selecting and applying the correct tightening procedure. For example, certain clamps are designed for high-pressure environments, while others are optimized for vibration-prone applications. Proper selection and application are essential for optimal performance and prevent premature failure.
- High-Pressure Clamps: These clamps, often constructed from stronger materials like stainless steel, are designed to withstand significantly higher pressures. The tightening process often involves more precise torque application and may require specialized tools, like torque wrenches, to avoid over-tightening and potential damage to the hose or fitting.
- Spring-Loaded Clamps: These clamps use a spring mechanism to maintain pressure on the hose. Tightening these types of clamps often involves adjusting the spring tension to ensure a proper seal without excessive pressure, preventing damage to the hose. Careful consideration of the spring’s compression is crucial.
- Specialty Clamps (e.g., for vibration-prone systems): Certain applications, like those in automotive or industrial machinery, require clamps resistant to vibrations. These clamps often have unique designs, and their tightening procedures may differ significantly from standard clamps. Understanding the specific application and vibration characteristics is essential.
Tightening in Hard-to-Reach Areas
Accessibility often poses a challenge in tightening hose clamps. Innovative solutions are necessary to ensure proper tension without compromising safety or efficiency. Employing leverage tools, specialized clamps, or even remote tightening mechanisms can be necessary for such situations.
- Leverage Tools: Using long-handled pliers or adjustable wrenches with extensions provides increased leverage to apply torque effectively in tight spaces. This can significantly reduce the risk of injury or strain.
- Specialized Clamps: Some clamps have unique designs that allow for tightening from different angles. These specialized clamps can provide better access and ensure proper contact with the hose and fitting, minimizing damage.
- Remote Tightening: For particularly inaccessible locations, remote tightening mechanisms, such as pneumatic or hydraulic tools, may be necessary. These tools can be valuable in industrial settings or situations where direct access is limited.
Tightening Under Pressure
Hose clamps used in high-pressure systems require special attention to avoid leaks or damage. Precise torque application is essential to ensure a secure seal without compromising the integrity of the system. The pressure exerted on the hose should also be considered.
- Pressure Monitoring: Continuously monitoring pressure during the tightening process is essential in high-pressure applications. This ensures that the clamp is adequately sealing the hose and prevents catastrophic failures.
- Torque Wrench Utilization: Torque wrenches are indispensable in high-pressure environments. They ensure that the clamp is tightened to the manufacturer’s specifications, preventing over-tightening and damage to the system.
- Safety Precautions: In high-pressure scenarios, safety precautions are paramount. Use appropriate safety equipment, such as gloves and eye protection, and ensure the system is depressurized before any tightening or maintenance work is performed.
Unique Hose Clamp Applications
Various applications demand specific hose clamp requirements. These situations require careful consideration of factors such as the environment, pressure, and vibration. Each application needs a precise approach.
- Aircraft Fuel Lines: High-pressure and high-temperature environments require specialized clamps and tightening procedures. Safety is paramount in these situations.
- Marine Applications: Exposure to harsh marine environments demands corrosion-resistant materials and specialized clamps. Tightening procedures must account for potential salt and moisture.
- Industrial Piping Systems: Industrial applications often involve large-diameter hoses and high pressures. The choice of clamps and tightening methods must be carefully assessed based on the specific system parameters.
Visual Aids (Illustrative Examples)
Visual aids are crucial for understanding the intricacies of hose clamp tightening. Proper visualization of techniques, tools, and potential pitfalls ensures safe and effective clamping. The following sections will guide you through a step-by-step process, highlighting critical distinctions between correct and incorrect tightening procedures.
Step-by-Step Tightening Process
Visualizing the process of tightening a hose clamp is essential for achieving a secure and reliable seal. The procedure involves several key steps, each requiring precise execution.
- Preparation: Inspect the hose and clamp for any damage or defects. Ensure the clamp is the correct size for the hose diameter. Position the clamp on the hose, ensuring the clamp’s teeth engage with the hose evenly.
- Initial Application: Apply moderate pressure using a wrench or pliers, gradually compressing the clamp. Observe the hose for even contact and ensure no excessive twisting or bending occurs.
- Progressive Tightening: Continue tightening, monitoring the clamp’s tightening action. A properly tightened clamp will show even compression across its entire surface. Avoid over-tightening.
- Final Check: Once the clamp is secure, inspect the hose for any signs of stress or damage. Ensure the clamp is properly seated and the hose is not twisted or bulging.
Over-Tightening vs. Under-Tightening
Understanding the distinction between over-tightening and under-tightening is critical for achieving a secure connection.
- Over-tightening: Over-tightening can lead to hose damage, potentially cracking the hose or deforming the clamp. The hose may exhibit signs of bulging or uneven compression. The clamp will be excessively tight, often requiring significant force to loosen.
- Under-tightening: Under-tightening results in a weak connection. This can cause leaks and allow the hose to shift or vibrate, eventually leading to a complete failure of the connection. The clamp will exhibit a loose fit and may require more force to remain secure.
Lubricant Application
Lubricating the clamp’s contact surfaces is often beneficial, especially on rough surfaces or when working with delicate hoses.
- Selection of Lubricant: Use a suitable lubricant such as a thin, non-abrasive grease or a dry lubricant spray. Avoid lubricants that could potentially damage the hose or clamp materials.
- Application Technique: Apply a thin film of lubricant to the surfaces of the clamp that will contact the hose. Ensure the lubricant is evenly distributed. Avoid excessive application, as this could attract dirt and debris.
Tightening in Confined Spaces
Tightening hose clamps in confined spaces can be challenging but achievable with careful planning and the right tools.
- Tool Selection: Utilize adjustable wrenches, pliers, or specialized tools designed for confined spaces. These tools should allow for precise control and maneuverability.
- Positioning and Access: Strategically position yourself or the tools to maximize access to the clamp. Consider using extensions or leverage to assist with tightening.
- Gradual Tightening: Gradual tightening is essential when working in confined spaces to avoid damage to the hose or surrounding components. Monitor the clamp’s tightening action closely.
Final Summary

In conclusion, mastering how to tighten hose clamps involves understanding the specific clamp type, identifying potential issues, employing appropriate tools, and adhering to safety protocols. This guide has equipped you with the knowledge and techniques to ensure proper tightening and prevent costly repairs or safety incidents. Remember to prioritize safety and seek professional help when needed.
Quick FAQs
What are the common causes of a loose hose clamp?
Loose hose clamps can result from improper initial tightening, vibration, or the accumulation of debris. Repeated use and pressure fluctuations can also cause a clamp to loosen over time.
What is the importance of torque when tightening hose clamps?
Appropriate torque prevents leaks and damage to the hose or fitting. Over-tightening can deform the hose or fitting, leading to leaks. Under-tightening can cause leaks and the hose to loosen.
How do I safely remove a damaged hose clamp?
Carefully loosen the clamp, ensuring the hose isn’t damaged. Use appropriate tools and wear safety gear if necessary. Inspect the hose for any damage before installing a replacement clamp.
What are the symptoms of an improperly tightened hose clamp?
Common symptoms include leaks, hissing sounds, or visible movement of the hose relative to the clamp. These issues often indicate a need for re-tightening or replacement.