How to use Wilson inline dies? This guide dives deep into the world of precision metalworking, revealing the secrets behind these powerful tools. From fundamental safety precautions to advanced applications, we’ll explore every facet of mastering Wilson inline dies. Get ready to transform raw materials into exquisite forms, one precise cut at a time.
Understanding the different types of Wilson inline dies, their specific functionalities, and the crucial materials they’re crafted from is essential for achieving optimal results. We’ll also cover setup procedures, operation methods, and maintenance tips, all with a focus on safety and efficiency.
Introduction to Wilson Inline Dies
Wilson inline dies are specialized tooling components crucial in various manufacturing processes, particularly those involving sheet metal forming and extrusion. Their design facilitates precise and consistent shaping of materials, resulting in high-quality finished products. These dies are widely used in industries requiring controlled deformation of materials, from automotive components to consumer goods packaging.
Types of Wilson Inline Dies
Wilson inline dies come in diverse configurations, each tailored to specific material and shaping requirements. These variations encompass different geometries and functionalities to accommodate the wide range of applications. Understanding the distinctions between these types is essential for selecting the appropriate die for a given task.
- Punch and Die Sets: These dies are commonly used for blanking, punching, and other shearing operations. They are composed of a punch, which removes material, and a die, which shapes the remaining material. The precise geometry of these components determines the shape of the cut or punched piece. For example, a punch and die set can be used to create precise holes or shapes in sheet metal components for applications such as automotive panels or electronic enclosures.
- Forming Dies: These dies are designed for complex shaping operations, such as bending, drawing, and embossing. They are characterized by their intricate designs and specialized components, ensuring consistent deformation of the material. These dies often incorporate features like radius adjustments or progressive steps for creating elaborate shapes. A forming die can be used to create a curved section on a sheet metal component, or to impart a decorative embossed pattern.
- Extrusion Dies: These specialized dies are employed in extrusion processes, shaping the material as it passes through the die orifice. The die’s geometry determines the final cross-sectional shape of the extruded product. Extrusion dies are essential for producing profiles, tubes, and other complex shapes from various materials. An extrusion die, for instance, can create a specific profile for a window frame or a cable casing.
Benefits of Using Wilson Inline Dies
Wilson inline dies offer several advantages over alternative methods for shaping materials. These advantages contribute to enhanced efficiency and cost-effectiveness in manufacturing processes.
- High Precision and Repeatability: Wilson inline dies are meticulously crafted to ensure precise and repeatable results, minimizing variations in the final product. This consistency is crucial for meeting quality standards in mass production.
- Increased Production Speed: The streamlined design and efficient operation of Wilson inline dies enable higher production rates compared to some manual or less automated processes. This translates to faster turnaround times and improved overall productivity.
- Reduced Material Waste: The precision of Wilson inline dies contributes to less material waste during the shaping process. This translates into significant cost savings in the long run, especially in industries where material costs are high.
Materials and Properties of Wilson Inline Dies
The choice of material for Wilson inline dies is critical, as it directly impacts the die’s performance and longevity. Specific properties, such as hardness, wear resistance, and heat resistance, are essential for optimal die function.
Material | Properties | Applications |
---|---|---|
High-Speed Steel (HSS) | Excellent wear resistance, good toughness, and hardness, making it suitable for high-speed machining and high-volume production. | Punching, blanking, and other shearing operations. |
Tool Steel (e.g., M2, D2) | High hardness, good wear resistance, and toughness, ideal for demanding forming applications. | Forming dies, extrusion dies, and applications requiring high pressure or stress. |
Ceramics | Exceptional wear resistance, high hardness, and low friction, often used for high-temperature or corrosive environments. | High-temperature forming, extrusion of advanced materials. |
Essential Safety Precautions
Working with Wilson inline dies requires strict adherence to safety protocols. Neglecting these precautions can lead to severe injuries and equipment damage. This section details critical safety measures, emphasizing a safe work environment and the importance of personal protective equipment (PPE). Understanding potential hazards associated with improper use is crucial for preventing accidents.Proper handling and maintenance of Wilson inline dies are vital to ensuring a safe and productive work environment.
A proactive approach to safety, encompassing thorough preparation and meticulous execution of procedures, is paramount.
Hazard Identification and Mitigation, How to use wilson inline dies
Wilson inline dies, due to their high-pressure and high-speed operation, pose several potential hazards. These include the risk of flying debris, equipment malfunctions, and exposure to hazardous materials. Properly identifying and mitigating these hazards is crucial for preventing accidents. This involves a comprehensive understanding of the machine’s operation and the potential risks associated with different stages of the process.
Safe Work Environment Procedures
Creating a safe work environment is a crucial first step in preventing accidents. This includes maintaining a clean and organized workspace, ensuring proper ventilation, and designating a clear area for die operation. These measures reduce the risk of slips, trips, and falls, as well as minimizing the chance of equipment malfunctions leading to uncontrolled situations. Regular inspection and maintenance of the equipment are vital components of a proactive safety program.
Personal Protective Equipment (PPE)
Personal protective equipment (PPE) is essential for safeguarding personnel from potential hazards. Appropriate PPE, tailored to the specific operation, plays a vital role in mitigating risks. This includes safety glasses, gloves, and hearing protection. Ensuring the proper fit and functionality of PPE is as important as selecting the right type.
Safety Protocols and Required PPE
Implementing a clear set of safety protocols is crucial for consistent and effective safety measures. This involves outlining procedures for all stages of the die operation, from setup to cleanup. The following table Artikels safety protocols and required PPE for various operations:
Safety Protocol | Description | Required PPE |
---|---|---|
Die Setup | Ensure the die is securely mounted and all clamps are properly tightened. | Safety glasses, work gloves, closed-toe shoes |
Material Loading | Carefully feed material into the die, avoiding contact with moving parts. | Safety glasses, work gloves, closed-toe shoes, hearing protection (if applicable) |
Operation | Monitor the die’s operation, observing for any signs of malfunction or overheating. | Safety glasses, work gloves, closed-toe shoes, hearing protection (if applicable), protective apron (for high-risk operations) |
Maintenance | Follow the manufacturer’s instructions for maintenance procedures. | Safety glasses, work gloves, closed-toe shoes, hearing protection (if applicable), appropriate respiratory protection (if applicable) |
Cleanup | Thoroughly clean the workspace and dispose of debris according to established procedures. | Safety glasses, work gloves, closed-toe shoes |
Setting Up the Wilson Inline Die
Proper installation of the Wilson inline die is crucial for achieving optimal performance and preventing potential issues during the extrusion process. A correctly mounted die ensures consistent product quality, minimizes material waste, and safeguards the machine from damage. Careful attention to detail and adherence to the established procedures are paramount in this critical step.Accurate mounting and secure fastening of the die are essential to ensure smooth and consistent operation of the extrusion system.
This process involves a series of steps, requiring specific tools and equipment. Misalignments or improper fastening can lead to product defects, machine malfunctions, and potential safety hazards. Understanding the importance of precise alignment and the correct procedures is therefore vital for successful die installation.
Mounting the Die
The die mounting process requires careful handling to avoid damage to the die or the extrusion machine. Ensure the machine is properly grounded and de-energized before initiating the mounting procedure. Improper grounding can lead to electrical hazards.
Necessary Tools and Equipment
A comprehensive set of tools and equipment is essential for a successful die installation. This includes, but is not limited to: a torque wrench, appropriate fasteners (bolts, screws, nuts), alignment gauges, a set of wrenches (various sizes), safety glasses, and a designated work area free of obstructions. The selection of the appropriate tools is critical to ensuring a secure and efficient installation.
Step-by-Step Die Installation Guide
- Verify that the extrusion machine is powered off and properly grounded.
- Prepare the die mounting plate by ensuring it is clean and free from any debris or contaminants. Cleanliness prevents unforeseen issues during the mounting process.
- Position the die onto the mounting plate, aligning it precisely with the intended orientation.
- Tighten the fasteners using the torque wrench to the specified torque values. Using a torque wrench prevents over-tightening, which could damage the die or the machine.
- Verify the die alignment using alignment gauges. Ensure that the die is perfectly aligned with the extrusion barrel. Precise alignment is crucial for consistent product output.
- Thoroughly inspect all connections and fasteners for any signs of looseness or damage. Regular inspection minimizes potential issues during operation.
- Power up the machine and monitor the extrusion process to confirm proper functionality. Monitoring the process is crucial to identify any anomalies or issues promptly.
Common Mistakes and Avoidance Strategies
Common mistakes during die installation include improper alignment, inadequate torque values, and improper fastener selection. Inadequate torque values can lead to the die becoming loose during operation, causing product inconsistencies. Improper alignment can result in uneven material flow and product defects. Carefully selecting the right fasteners prevents damage to the die or the machine.
Importance of Precise Alignment
Precise alignment of the die is critical for achieving consistent product quality and preventing machine malfunctions. Misalignment can lead to uneven material flow, product defects, and potential damage to the extrusion machine. Careful attention to detail during the alignment process ensures a long-lasting and productive extrusion system.
Comparison of Die Mounting Techniques
Technique | Pros | Cons |
---|---|---|
Direct Mounting | Simple and straightforward, potentially faster installation | Requires precise alignment, higher risk of damage if not done carefully |
Indirect Mounting (using intermediate plates) | Allows for more complex die geometries, provides better support for heavier dies | Can be more complex, potentially slower installation |
Specialized Mounting Systems | Offers optimal support for complex geometries, highly precise alignment | Can be more expensive, requires specific expertise for installation |
Operating the Wilson Inline Die
Initiating the Wilson inline die operation requires meticulous attention to detail and adherence to the established procedures. Proper operation ensures consistent output quality and minimizes the risk of damage to the die or the surrounding equipment. Understanding the nuances of different materials and the associated pressure requirements is crucial for optimizing die performance.The operation of Wilson inline dies encompasses a range of techniques tailored to specific material types and desired outcomes.
This involves carefully adjusting parameters like pressure and feed rate to achieve optimal results while maintaining safety protocols. This section will provide a comprehensive overview of the operational procedures, potential issues, and troubleshooting strategies.
Initiating Die Operation
Proper die initiation is paramount to successful operation. This involves a phased approach, starting with a low-pressure test run to gauge the system’s responsiveness and identify any potential issues before escalating to higher pressures. Operators should always refer to the specific instructions provided with the Wilson inline die model. The sequence includes pre-operation checks, setting the desired parameters, and slowly increasing the pressure to the target level.
Regular monitoring is essential throughout the process.
Operation Methods for Different Materials
Different materials exhibit varying responses to pressure and die configuration. For instance, high-strength polymers may require higher pressures and slower feed rates compared to softer materials. Aluminum alloys, known for their malleability, might benefit from lower pressures to avoid excessive deformation or damage. Careful observation of the die’s performance during operation is crucial to identify any signs of material-specific issues.
A detailed understanding of the material’s properties is essential for selecting the appropriate operating parameters.
Factors Influencing Die Performance
Material properties, such as tensile strength and viscosity, significantly impact die performance. Higher pressures often lead to higher output quality but may increase the risk of material degradation or die wear. The die’s geometry and design also play a vital role, influencing the flow and shaping of the material. Consistent maintenance and proper lubrication of the die components are crucial for optimal performance and longevity.
Furthermore, environmental factors such as temperature and humidity can also affect material properties and thus die performance.
Potential Issues and Troubleshooting
Unforeseen issues may arise during operation. Material jamming is a common problem, often resolved by adjusting the feed rate or pressure. Uneven output quality can be due to inconsistencies in the material feed, requiring adjustments to the material supply system. If the die shows signs of overheating, reducing the pressure or increasing the cooling system’s efficiency may be necessary.
A detailed troubleshooting guide should be consulted for each potential issue.
- Material Jamming: This can be caused by material inconsistencies, improper feed rates, or insufficient lubrication. Troubleshooting involves adjusting feed rate, pressure, and/or lubricant application, and inspecting the material supply for blockages.
- Uneven Output: This could stem from inconsistent material properties, feed rate variations, or die wear. Troubleshooting requires checking material consistency, adjusting feed rate and pressure, and inspecting the die for wear and tear.
- Overheating: High pressures or inadequate cooling can lead to overheating. Troubleshooting involves reducing pressure, optimizing cooling system efficiency, and ensuring proper lubrication.
Monitoring During Operation
Continuous monitoring of the die during operation is critical for identifying anomalies. This includes visually inspecting the die for signs of wear, deformation, or damage, as well as monitoring pressure readings and output quality. Automated monitoring systems can provide real-time data for more comprehensive analysis. Regular checks on the material feed system and pressure regulators are also essential.
Safe Operation Shutdown
Proper shutdown procedures are vital to prevent accidents and maintain equipment longevity. Gradually reducing pressure and stopping the material feed are essential steps. Allowing the system to cool down before performing any maintenance or cleaning is crucial.
Die Operation Parameter Comparison
Parameter | Value | Effect on Output |
---|---|---|
Material Type | High-strength polymer | Higher pressure, slower feed rate required for optimal results. |
Pressure (MPa) | 10 | Lower pressure, potentially lower output quality, less stress on the die. |
Feed Rate (m/s) | 0.5 | Higher feed rate, potentially higher output, but increased wear on the die. |
Die Temperature (°C) | 120 | Higher temperature, potentially better material flow, but increased wear and potential material degradation. |
Maintaining Wilson Inline Dies
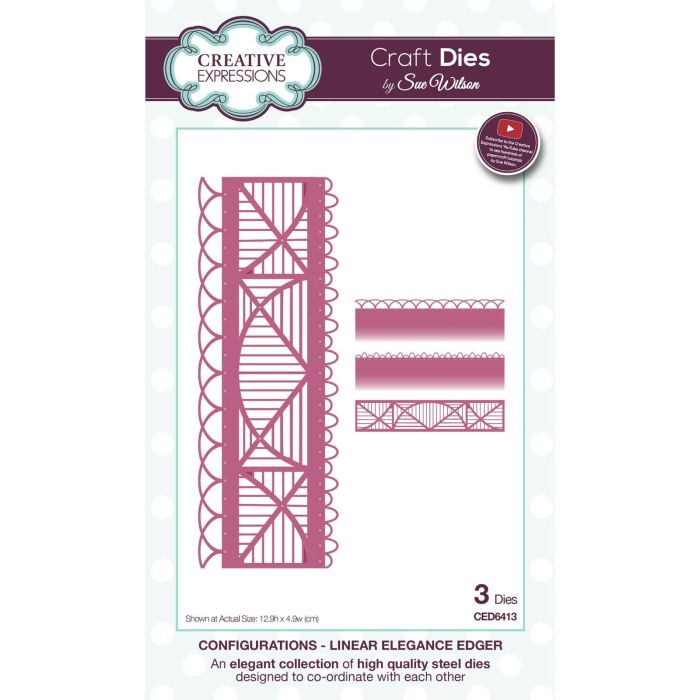
Proper maintenance of Wilson inline dies is crucial for ensuring consistent performance, extending the lifespan of the equipment, and minimizing potential downtime. Neglecting routine maintenance can lead to premature wear, increased production costs, and safety hazards. This section details the essential steps for maintaining Wilson inline dies, focusing on preventative measures and troubleshooting minor issues.
Routine Maintenance Procedures
Regular maintenance is key to maximizing the lifespan and performance of Wilson inline dies. These procedures prevent costly repairs and ensure the die remains in optimal working condition. Adhering to a scheduled maintenance plan is vital to maintaining consistent quality and production output.
- Visual Inspection: Thoroughly inspect the die for any signs of damage, such as cracks, dents, or excessive wear. Pay particular attention to the die’s cutting edges, pressure plates, and any moving components. This visual assessment helps identify potential problems early on, enabling timely repairs.
- Cleaning: Regular cleaning is essential to remove debris, metal shavings, and other contaminants that can accumulate on the die’s surfaces. Use appropriate cleaning solvents and tools to prevent scratching or damage to the die’s surface. A clean die allows for smooth operation and accurate cutting.
- Lubrication: Proper lubrication is critical for maintaining the die’s functionality and preventing friction-induced wear. Apply the recommended lubricant to all moving parts and contact surfaces. This ensures smooth operation and extends the die’s life.
Identifying Wear and Tear
Recognizing the early signs of wear and tear is vital for proactive maintenance. This proactive approach prevents small issues from escalating into significant problems.
- Uneven Cutting: If the die produces inconsistent or uneven cuts, it may indicate wear or misalignment. This could be a sign of a worn cutting edge or a damaged pressure plate. Closely examining the cutting edges is crucial in such cases.
- Excessive Vibration: Excessive vibration during operation suggests potential issues with the die’s structure or alignment. This could be caused by loose components, misalignment, or damage to the die’s mounting. Identifying and addressing these problems early on is crucial to preventing more serious damage.
- Increased Friction: Increased friction during operation often indicates insufficient lubrication or a buildup of debris on moving parts. Monitoring the level of friction during operation and applying appropriate lubrication helps identify and prevent this issue. This helps to maintain optimal cutting performance.
Storage and Protection
Proper storage and protection of the Wilson inline die are essential for preserving its integrity. These measures safeguard the die from damage, ensuring its long-term usability.
- Safe Storage: Store the die in a clean, dry environment, away from harsh chemicals and extreme temperatures. Protect the die from physical impacts that could lead to damage. Proper storage prevents premature wear and tear.
- Protective Coverings: Use appropriate protective coverings to shield the die from dust, debris, and other environmental contaminants. This protects the die from potential damage and ensures smooth operation.
Preventive Maintenance Schedule
The following table Artikels a recommended preventive maintenance schedule for Wilson inline dies. This schedule helps maintain the die’s performance and longevity.
Task | Frequency | Description |
---|---|---|
Visual Inspection | Daily | Check for any signs of damage or wear. |
Cleaning | Weekly | Remove debris and contaminants. |
Lubrication | Weekly | Apply lubricant to moving parts. |
Alignment Check | Monthly | Verify alignment of die components. |
Comprehensive Inspection | Quarterly | Thorough examination for significant wear and tear. |
Troubleshooting Common Issues
Wilson inline dies, while robust, can encounter various problems during operation. Understanding these potential issues and their corresponding solutions is crucial for maintaining optimal performance and preventing costly downtime. Thorough documentation of troubleshooting steps is essential for tracking progress, identifying recurring patterns, and improving future preventative measures.
Identifying Common Problems
Troubleshooting Wilson inline dies requires a systematic approach. Recognizing the symptoms of a problem is the first step towards finding a solution. Common issues can range from minor adjustments to more significant mechanical failures. Careful observation of die performance, material flow, and machine operation is key. Visual inspection and analysis of the die’s components and the surrounding environment are important.
Troubleshooting Steps for Specific Problems
A systematic approach to troubleshooting is essential. Start by isolating the problem. This involves gathering data on the specific conditions under which the issue arose, such as material type, machine settings, and operator actions. Consult the Wilson inline die user manual for guidance. The manual may contain specific diagnostic procedures.
If the issue persists, seek professional assistance.
Importance of Documentation
Comprehensive documentation during troubleshooting is crucial. Detailed records should include the date, time, problem description, actions taken, and outcomes. This allows for tracking the progress of the troubleshooting process and provides valuable insights into recurring problems. Such records are also helpful in case of warranty claims.
Comparison of Troubleshooting Strategies
Different troubleshooting strategies can be applied, each with varying degrees of effectiveness. For instance, a systematic, step-by-step approach is often preferred over a trial-and-error method. Using a checklist, comparing previous operations, and carefully reviewing the die’s configuration are effective strategies. This methodical approach can improve the likelihood of accurately diagnosing the root cause of the problem.
Table of Potential Problems, Causes, and Solutions
Problem | Cause | Solution |
---|---|---|
Die sticking | Excessive buildup of material, incorrect die lubrication, or wear on die components. | Clean the die thoroughly. Ensure proper lubrication. Inspect and replace worn components. |
Uneven product thickness | Incorrect die settings, variations in material properties, or misalignment of the die. | Verify die settings. Check material consistency. Ensure proper alignment. |
Material tearing or breakage | Excessive die pressure, incorrect material feed rate, or improper material handling. | Reduce die pressure. Adjust material feed rate. Improve material handling procedures. |
Die damage | Foreign objects in the material stream, excessive pressure, or impact from misaligned components. | Inspect material feed for foreign objects. Adjust machine settings to prevent excessive pressure. Ensure proper alignment of all components. |
Reduced production rate | Material jams, insufficient lubrication, or improper machine settings. | Clear material jams. Ensure proper lubrication. Adjust machine settings according to the material specifications. |
Advanced Applications
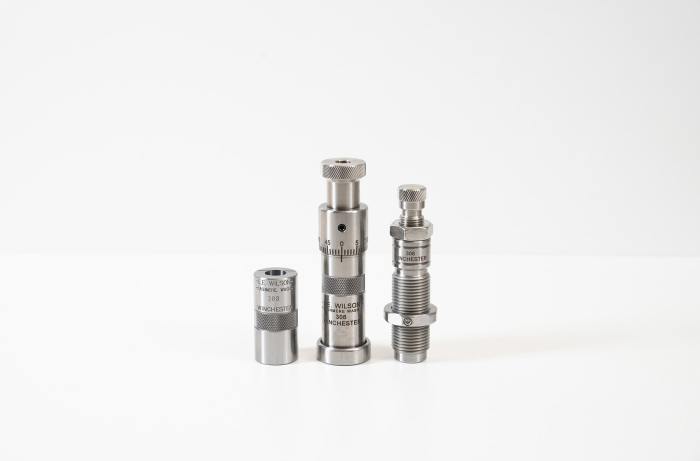
Wilson inline dies, beyond their fundamental role in shaping various materials, find specialized applications in complex manufacturing processes. These applications often require tailored die configurations, demanding a deep understanding of material properties, tolerances, and process parameters. Optimizing performance in these advanced setups involves careful consideration of the intricate interplay between die design, material characteristics, and operational parameters.Specialized applications of Wilson inline dies extend beyond the realm of basic forming and shaping.
These advanced uses often involve intricate geometries, high-precision requirements, and unique material properties. Understanding these specialized applications is crucial for achieving optimal results and preventing costly errors.
Specialized Die Configurations
Different die configurations are essential for diverse materials and desired shapes. Complex applications necessitate the integration of multiple dies, strategically arranged for optimal flow and material manipulation. For example, creating intricate shapes in metal stamping or high-precision components in plastic injection molding demands a multifaceted die structure.
Material and Tolerance Considerations
The choice of materials and the tolerance levels are critical in advanced applications. High-strength materials, such as certain alloys or composites, may require specific die materials and geometries to prevent deformation or damage. Precise tolerances are crucial to ensure the final product meets the required specifications. For instance, manufacturing microfluidic devices necessitates exceptional die precision to maintain the intricate channel structures.
The tolerances involved in these applications are typically measured in microns, demanding highly controlled manufacturing processes.
Advanced Techniques for Enhanced Performance
Several advanced techniques can enhance the performance of Wilson inline dies in complex applications. These include the use of specialized lubrication techniques to reduce friction and wear, which is especially critical for high-volume production runs. Employing advanced cooling systems to control temperature variations during the forming process can also improve the quality and consistency of the final product.
This becomes critical for materials prone to thermal sensitivity or in applications requiring uniform temperature distribution. Monitoring and controlling process parameters in real-time is vital for maintaining the desired outcome. Furthermore, utilizing simulation software to predict and optimize the forming process is a powerful tool for complex applications. This allows engineers to evaluate different die designs and process parameters before physical implementation, thereby minimizing the risk of costly errors.
Troubleshooting Specialized Applications
Troubleshooting in advanced applications can be challenging. Specialized diagnostic tools and techniques may be necessary to identify the root cause of issues. For instance, specialized inspection equipment may be needed to pinpoint deviations from expected tolerances or subtle material defects that might not be readily apparent.
Final Conclusion
In conclusion, mastering Wilson inline dies is a journey of precision and understanding. By meticulously following the safety precautions, setup guides, and operation procedures Artikeld in this comprehensive guide, you’ll unlock the full potential of these remarkable tools. Remember, practice makes perfect, and continuous learning is key to achieving exceptional results. Now go forth and create!
FAQ Compilation: How To Use Wilson Inline Dies
What are the most common materials used in Wilson inline dies?
Wilson inline dies are often made from high-strength steel alloys, chosen for their durability and resistance to wear and tear during repeated use. Specific grades will depend on the material being processed.
How often should Wilson inline dies be inspected for wear and tear?
Regular inspections are crucial. A visual check should be conducted after each use, and a more thorough inspection should be done on a weekly or monthly basis, depending on the frequency of use.
What are some common mistakes to avoid during die setup?
Improper alignment is a frequent problem. Ensure the die is precisely aligned with the machine’s components. Using the wrong tools for mounting the die can also lead to issues. Always consult the manufacturer’s instructions.
What are the typical causes of malfunction during operation?
Material incompatibility, incorrect pressure settings, and issues with lubrication can cause operational problems. Regular maintenance and proper material selection are key to avoiding these problems.