Liftmaster 8500 motor change how to is a crucial guide for homeowners tackling garage door opener maintenance. This comprehensive guide walks you through the process, from initial disconnection to final testing, emphasizing safety and efficiency throughout. Understanding the steps is vital for successful replacement and ensures your garage door operates smoothly for years to come.
Replacing a Liftmaster 8500 motor involves several key steps, from safely disconnecting power to carefully installing the new motor. Proper procedures and attention to detail are essential for a successful outcome.
Introduction to Liftmaster 8500 Motor Replacement
The Liftmaster 8500 garage door opener motor replacement is a relatively straightforward process for a homeowner with basic mechanical aptitude. Proper execution requires careful attention to safety procedures and a methodical approach to ensure a successful and safe outcome. This guide provides a comprehensive overview of the process, from initial power disconnection to the final motor installation.Replacing the motor on a Liftmaster 8500 garage door opener often involves addressing issues such as mechanical wear, electrical faults, or component damage.
This guide will help identify potential causes of motor failure and Artikel the necessary steps for a safe and effective replacement. Thorough preparation and adherence to the provided steps will minimize the risk of injury and ensure a successful outcome.
Necessary Tools and Materials
A comprehensive list of tools and materials is essential for a smooth and safe motor replacement. This will prevent unnecessary delays and ensure a successful outcome. Failure to prepare adequately may lead to complications during the procedure.
- Screwdrivers (Phillips and flathead)
- Wrench set (various sizes)
- Wire strippers/cutters
- Safety glasses
- Work gloves
- New Liftmaster 8500 motor
- Electrical tape
- Voltage tester
Safe Power Disconnection Procedure
Proper disconnection of the power supply is paramount for safety during the motor replacement. Neglecting this step can result in electrical shock or damage to the system.
- Locate the circuit breaker for the garage door opener and turn it off. A voltage tester should be used to confirm the power is completely disconnected from the circuit.
- Verify that the power is off by checking for voltage at the motor’s electrical connections. Ensure the breaker is in the “off” position and the circuit is completely de-energized.
- Tag the circuit breaker to indicate it has been turned off for maintenance to prevent accidental re-energization.
Safety Precautions
Adherence to safety precautions is critical to prevent injuries and damage during the motor replacement process. Neglecting these precautions could lead to serious consequences.
- Always disconnect the power supply before starting any work on the motor.
- Wear safety glasses and work gloves to protect your eyes and hands.
- Ensure the work area is clear of obstructions to prevent tripping hazards.
- If unsure about any step, consult a qualified technician.
- Be mindful of the garage door’s weight and potential for unexpected movement during the procedure.
Potential Causes of Motor Failure
The following table Artikels potential causes for Liftmaster 8500 motor failure, providing a framework for diagnosing and addressing the issue. Identifying the root cause will facilitate more effective troubleshooting and replacement.
Potential Cause | Description |
---|---|
Mechanical wear | Components such as gears, springs, and bearings can wear over time, leading to motor malfunction. |
Electrical faults | Issues with wiring, connections, or the control board can disrupt the motor’s operation. |
Overheating | Excessive use or inadequate ventilation can cause the motor to overheat, leading to failure. |
Incorrect installation | Improper installation procedures can lead to component misalignment or improper electrical connections, causing motor failure. |
External damage | Physical impact or exposure to extreme weather conditions can damage the motor, leading to failure. |
Disassembling the Old Motor
Careful disassembly of the old motor is crucial to prevent damage to the garage door opener and ensure a smooth installation of the replacement. Improper procedures can lead to malfunctions, requiring further repairs or replacements. Adhering to the steps Artikeld below will minimize risks and maximize efficiency.Properly disconnecting electrical connections and carefully removing mounting brackets are essential steps.
Incorrect removal can result in broken wires, damaged brackets, or even electrical shocks. Thoroughness in each step is paramount.
Electrical Disconnections
Disconnecting the electrical power supply to the garage door opener is the first and most critical step in any repair or replacement procedure. This safeguards against electrical hazards and ensures the safety of the technician and the surrounding environment. Failure to disconnect the power supply can result in severe electrical shock or damage to the equipment.
- Locate the circuit breaker for the garage door opener and switch it off. This will prevent any electrical flow to the opener.
- Verify the power disconnection by checking for voltage using a non-contact voltage tester. Failure to verify the power disconnection could lead to accidental activation of the opener during the disassembly process.
- Disconnect the electrical wires from the motor. Carefully identify each wire and its corresponding terminal. Note the wire color codes for proper reconnection. Improper identification can lead to incorrect wiring, causing damage or malfunctions.
Removing Mounting Brackets
Removing the mounting brackets requires careful attention to detail to avoid damaging the opener’s structure or the brackets themselves. The appropriate tools must be selected for each fastener type to prevent breakage.
- Identify all mounting screws and bolts. Note the type and size of each screw for future reference.
- Loosen and remove the screws and bolts that secure the motor’s mounting brackets. Use the correct size and type of wrench or screwdriver to avoid damaging the screws or the bracket.
- Carefully detach the brackets from the opener’s frame. Be mindful of any additional components attached to the brackets, such as limit switches or safety sensors.
Potential Problems and Solutions
Unexpected situations might arise during disassembly. Addressing them promptly is vital to maintaining the integrity of the process.
- Stuck Screws: If a screw is stuck, try using penetrating oil to loosen it. If that does not work, a different type of screwdriver or a screw extractor may be needed. Over-tightening or incorrect tools can damage the screw or the surrounding material.
- Damaged Components: If a bracket or wire shows signs of damage, document the extent of the damage. Replacing the damaged component will prevent further issues.
- Incorrect Tools: Using the wrong tools can damage the components. Ensure proper tool selection to prevent this.
Screw Type Comparison, Liftmaster 8500 motor change how to
Different types of screws are used for different applications. Using the correct type of screw is essential for a secure and reliable installation.
Screw Type | Description | Typical Use |
---|---|---|
Phillips Head | A cross-shaped head | General purpose fastening |
Flat Head | A flat head with a slotted design | Fastening in places where a countersunk head is required |
Torx | A star-shaped head | High-strength applications where a secure fastening is critical |
Installing the New Motor
Proper installation of the new LiftMaster 8500 motor is crucial for the safe and reliable operation of the garage door opener. Incorrect installation can lead to malfunctions, damage to the system, and potential safety hazards. This section details the steps for a successful installation, focusing on mounting, electrical connections, adjustments, and potential alignment issues.
Mounting the New Motor
Before mounting the new motor, ensure the garage door opener frame is clean and free of debris. Verify that all necessary mounting hardware, including screws and brackets, is present and in good condition. Align the motor’s mounting holes with the corresponding holes in the frame. Secure the motor using the provided screws, ensuring they are tightened to the manufacturer’s specifications.
Over-tightening can damage the motor or frame.
Electrical Connections
Correctly reconnecting the electrical components is paramount for safe operation. Carefully disconnect the power supply to the garage door opener before beginning any electrical work. Match the wires from the old motor to the corresponding wires on the new motor. Utilize wire connectors to ensure a secure and reliable connection. Double-check all connections to prevent short circuits or electrical shocks.
Ensure proper grounding. Consult the motor’s wiring diagram for precise wire identification and connection procedures.
Adjusting Motor Settings and Functions
Adjusting the motor’s settings and functions after installation is critical for optimal performance. This may involve adjusting the travel limits of the garage door. Verify that the garage door opens and closes smoothly within its intended range. Adjust the force settings to match the weight of the garage door. A suitable force setting prevents the door from binding or moving too quickly.
Check the safety reversing mechanisms to ensure they operate correctly and are fully functional.
Alignment Issues and Solutions
Potential misalignment issues can arise during the installation process. Verify that the motor is properly centered on the track. Check the alignment of the garage door itself. Any misalignment can cause the door to bind or malfunction. Use a level to ensure the motor and the garage door are properly aligned.
If misalignment persists, consult a qualified technician for assistance.
Torque Specifications for Fasteners
Precise torque specifications are critical for securing fasteners and preventing damage. Failure to adhere to these specifications can lead to premature failure of the components. The table below Artikels the recommended torque values for various fasteners used in the installation.
Fastener Type | Torque Specification (ft-lbs) |
---|---|
Motor Mounting Screws | 15-20 |
Bracket Screws | 10-15 |
Electrical Connectors | N/A |
Note: These torque specifications are approximate and may vary depending on the specific components and manufacturer recommendations. Always refer to the manufacturer’s instructions for the exact torque values.
Testing and Final Adjustments
After installing the new LiftMaster 8500 motor, rigorous testing and fine-tuning are crucial to ensure optimal garage door operation. Proper testing verifies the motor’s functionality, the door’s smooth movement, and identifies any potential issues before permanent use. This section details the procedures for comprehensive testing and adjustment.
Thorough Motor Testing
The initial motor test verifies the replacement motor’s performance characteristics. Ensure the power source is connected and the garage door is disengaged from any automatic operation mechanisms. Manually operate the door to assess the motor’s responsiveness and strength. The motor should initiate and maintain a consistent lifting and lowering speed, and it should not exhibit any hesitation or stalling.
Check the motor for excessive noise or unusual vibrations. These can indicate a mechanical problem that requires immediate attention. Observe the motor’s thermal performance during operation, noting any overheating or unusual temperature changes.
Garage Door Opener Functionality Checks
The functionality of the entire garage door opener system needs to be verified. This involves activating the remote control or keypad, confirming that the door operates smoothly in all directions, and confirming that the door reverses correctly. Carefully monitor the entire process to ensure that the opener functions as expected throughout the lifting and lowering cycle. Examine the sensors to ensure they are correctly positioned and functioning.
If there are any malfunctions, identify the exact point in the cycle where they occur.
Ensuring Smooth Door Operation
Smooth operation is essential for both the motor’s longevity and the safety of the door. The door should move in a straight line, without any noticeable side-to-side or up-and-down deviations. Adjust the limit switches, if necessary, to fine-tune the door’s travel range. Check the rollers and tracks for any signs of damage or wear. Lubricate all moving parts to maintain proper functionality and minimize friction.
Verify the door is balanced correctly. A properly balanced door will move easily in both directions without requiring excessive force.
Troubleshooting Operation Issues
If the garage door opener encounters problems, a systematic troubleshooting approach is necessary. First, check the power supply and confirm that the power outlet is operational. Then, verify the remote control and keypad operation by ensuring the buttons function correctly and respond appropriately. If the door is not opening or closing, check the safety sensors for proper alignment and function.
If the door binds or stalls, inspect the tracks and rollers for obstructions or damage. If the door is moving erratically, check the balance and adjust it if needed. Record each step taken to resolve the issue for future reference.
Unusual Noises During Operation
Unforeseen noises during operation can indicate various issues, requiring prompt attention to prevent further damage. A systematic analysis of these sounds is critical to identifying the source and implementing a suitable solution. The table below lists common causes of unusual noises.
Noise | Possible Cause |
---|---|
Grinding or Scraping | Worn or damaged rollers, tracks, or springs; misaligned parts. |
Clicking or Rattling | Loose or damaged gears, cables, or hardware; a misaligned motor bracket. |
Screeching or Squeaking | Insufficient lubrication of moving parts; a binding mechanism. |
Humming or Vibrating | Faulty motor; a misaligned or unbalanced door; problems with the door’s torsion springs. |
Safety Considerations
Proper safety precautions are paramount during any motor replacement procedure, particularly when working with electrical components and potentially hazardous machinery. Adhering to these guidelines minimizes the risk of injury and ensures a safe working environment for the technician and those around them.Adherence to safety procedures is not merely a precaution but a critical aspect of the process. Ignoring safety guidelines can lead to severe consequences, ranging from minor injuries to potentially fatal accidents.
Failure to prioritize safety compromises the integrity of the work and could have legal implications.
Importance of Personal Protective Equipment (PPE)
A comprehensive safety strategy begins with appropriate personal protective equipment (PPE). Wearing safety glasses, gloves, and sturdy work boots is crucial for protecting the eyes, hands, and feet from potential hazards. The specific PPE requirements may vary based on the individual work environment and the potential hazards involved.
Electrical Safety Procedures
Handling electrical components necessitates stringent safety protocols. Before initiating any electrical work, ensure the power supply to the garage door opener is disconnected at the circuit breaker. Double-checking the disconnection is critical to avoid accidental electrical shocks. Working with live electrical circuits can lead to severe injury or death.
Safe Working Environment
Maintaining a secure working environment is essential. Ensure the work area is well-lit, free of obstructions, and appropriately ventilated. A cluttered or dimly lit area increases the risk of slips, trips, and falls. Proper ventilation is necessary to prevent the buildup of potentially harmful fumes or gases.
Potential Hazards and Mitigation
Potential hazards during a motor replacement include electrical shocks, cuts from sharp metal components, and falls from heights if working on a raised platform. To mitigate these risks, ensure proper grounding procedures are followed, use insulated tools when handling electrical components, and use appropriate safety equipment such as harnesses and scaffolding when working at heights. Protective measures should be in place to prevent any potential hazards.
Emergency Procedures
In the event of an incident, a well-defined emergency procedure is vital. A first-aid kit should be readily available, and emergency contact numbers should be clearly displayed. Knowing how to use fire extinguishers and having a plan for evacuation in case of fire are also essential aspects of emergency preparedness. A comprehensive emergency procedure can help mitigate the effects of accidents and injuries.
- Immediate Actions: If an incident occurs, immediately stop work, assess the situation, and provide immediate first aid, if necessary. Contact emergency services or appropriate personnel if needed.
- Emergency Contact Information: Keep a readily available list of emergency contacts, including local emergency services, and any relevant personnel involved in the project.
- First Aid Kit: Maintain a well-stocked first-aid kit with essential supplies for treating minor injuries.
- Evacuation Procedures: Develop and practice evacuation procedures for the work area in case of fire or other emergencies. This should be a documented process, and everyone involved should be familiar with the procedures.
Troubleshooting Common Issues
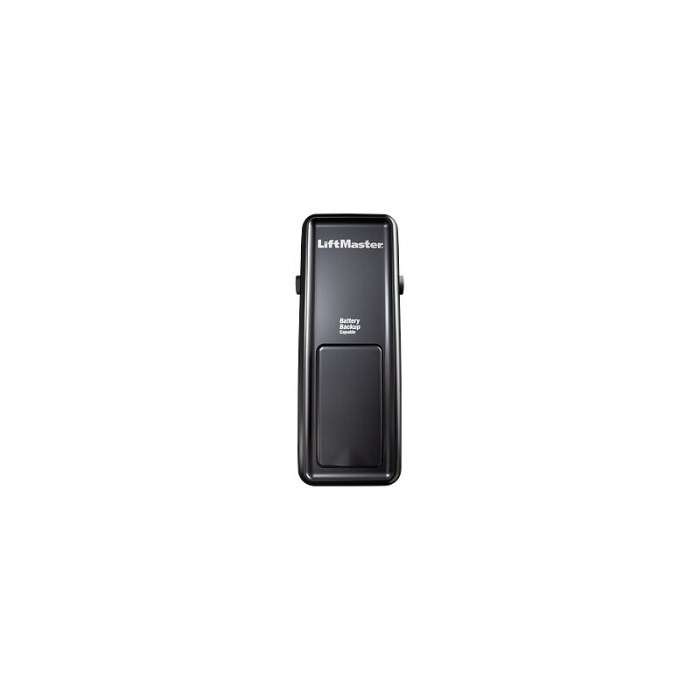
Motor replacement procedures, while generally straightforward, can sometimes encounter unexpected challenges. Thorough troubleshooting is crucial to identify and resolve these issues, ensuring the garage door operates reliably and safely. Proper diagnosis and resolution of problems prevent further damage to the system and ensure a smooth and efficient operation.
Identifying Motor Operation Problems
Troubleshooting begins with a systematic assessment of the motor’s operational characteristics. Careful observation of the motor’s behavior during each stage of operation (opening, closing, reversing) is essential for accurate diagnosis. This includes listening for unusual noises, such as grinding, clicking, or buzzing, and paying attention to any discrepancies in the motor’s speed or smoothness of operation. A malfunctioning motor may fail to engage or disengage correctly.
Proper assessment of the operation helps to pinpoint the problem area.
Diagnosing Alignment Issues
Improper alignment of the new motor can lead to a variety of operational problems. Misalignment can cause the door to bind, operate erratically, or fail to operate at all. Visually inspecting the motor’s mounting position against the door’s track is crucial. Ensuring the motor’s mounting bolts are securely fastened is vital for a stable and reliable operation.
Precise measurement of the motor’s position relative to the track ensures smooth operation and avoids unnecessary strain on the system. Adjustments, if needed, should be made carefully and in accordance with the manufacturer’s instructions.
Troubleshooting Intermittent Operation
Intermittent operation, characterized by sporadic functioning, can be caused by several factors. A loose connection within the motor’s wiring harness or a problem with the limit switches can lead to inconsistent operation. Checking the connections at the motor, control panel, and limit switches is crucial. Carefully inspect the limit switches for proper engagement and ensure that the door’s travel is within the expected range.
A failing capacitor can also cause intermittent operation. Checking for capacitor functionality is important in such cases. An electrical test of the components can help pinpoint the cause of intermittent operation.
Troubleshooting Motor Alignment Issues
Precise alignment of the motor and door tracks is paramount for reliable operation. Misalignment can manifest as binding, uneven movement, or complete failure to operate. Using a straight edge or level to check the motor’s position relative to the track ensures accurate alignment. Any deviation from the recommended alignment must be corrected. Measuring the distance between the motor and the track, and comparing it to the manufacturer’s specifications, will help identify any alignment issues.
Appropriate adjustments to the motor mounting position may be necessary.
Table of Common Errors and Solutions
Error | Possible Cause | Solution |
---|---|---|
Motor does not operate at all | Faulty motor, loose connections, tripped circuit breaker | Verify power supply, check connections, reset circuit breaker. If the problem persists, replace the motor. |
Motor operates erratically | Misaligned motor, damaged gear or drive components, faulty limit switches | Ensure proper alignment, inspect gear and drive components for damage. If the problem persists, replace the limit switches. |
Motor operates intermittently | Loose connections, faulty capacitor, limit switch issues | Check all electrical connections, replace the capacitor, and verify the operation of the limit switches. |
Door binds or jams | Misaligned motor, obstructed tracks, worn components | Ensure proper alignment, clear any obstructions, and inspect the door and track for wear. Consider replacement of damaged components. |
Additional Tips and Recommendations
Replacing a LiftMaster 8500 motor requires careful attention to detail and specific considerations for different models and long-term maintenance. Proper installation and subsequent care are crucial for ensuring the longevity and reliable operation of the new motor. This section provides essential tips for maximizing the lifespan and performance of the upgraded system.
Specific Considerations for Different LiftMaster 8500 Models
Variations in LiftMaster 8500 models may necessitate adjustments to the installation process. Consult the specific model’s installation manual for precise instructions and potential differences in wiring configurations, component placement, or required tools. Discrepancies may exist in the dimensions or compatibility of replacement parts across various 8500 series models. Thorough research and adherence to the manufacturer’s specifications are paramount.
Preventive Maintenance Procedures for the New Motor
Implementing a proactive maintenance schedule for the new motor is essential for sustained performance and reduced future issues. Regular lubrication of the motor’s moving parts, such as the gears and bearings, is crucial. Follow the manufacturer’s recommendations for lubrication frequency and appropriate lubricant types. Inspect the motor housing and surrounding areas for signs of corrosion or damage after each use.
Regular visual inspections can prevent potential issues before they escalate.
Recommendations for Long-Term Motor Care
Long-term motor care involves a combination of preventive measures and proactive problem-solving. Periodic checks of the motor’s operation, including the smoothness of the gate’s movement and the absence of unusual noises, are essential. Note any inconsistencies and address them promptly to prevent escalated damage. Storing the replacement motor in a dry, protected environment is vital to prevent moisture-related issues.
Using appropriate protective covers during periods of inactivity is a recommended practice.
Additional Resources for Further Information
Numerous online resources provide detailed information on LiftMaster 8500 motor replacements and maintenance. The LiftMaster website and various online forums dedicated to home automation systems often host valuable troubleshooting guides, FAQs, and community discussions. Seek out these resources for further insights and practical solutions to potential problems.
Comparison of Motor Brands
Brand | Features | Typical Price Range | Known Strengths | Known Weaknesses |
---|---|---|---|---|
LiftMaster | Known for reliability, compatibility with existing systems, wide range of models. | $300 – $600 | High quality components, durable construction, wide availability of replacement parts. | Can be slightly more expensive than other brands. |
Chamberlain | Competitive pricing, readily available parts. | $200 – $400 | Affordable, good value for the price. | May have slightly lower quality components compared to LiftMaster. |
Genie | Known for innovative designs, advanced features, often come with integrated safety features. | $350 – $700 | Safety features, user-friendly designs. | Potentially more expensive than Chamberlain or basic LiftMaster models. |
Note that the price range is an estimate and may vary depending on the specific model, features, and retailer.
Last Recap: Liftmaster 8500 Motor Change How To

In conclusion, this guide provides a clear and detailed roadmap for replacing your Liftmaster 8500 garage door opener motor. By following the step-by-step instructions and safety precautions, you can confidently undertake this maintenance task. Remember to prioritize safety throughout the entire process. If you encounter difficulties, consult the provided troubleshooting tips or seek professional assistance.
Commonly Asked Questions
What tools are needed for the replacement?
The necessary tools will vary, but typically include screwdrivers, a wrench, and a voltage tester. Always double-check the specific tools needed for your model.
How long does the replacement typically take?
The time needed for replacement depends on your familiarity with the process and the complexity of the situation. Allow several hours for a complete and thorough replacement.
What are some common causes of motor failure?
Common causes include worn-out components, electrical issues, and faulty wiring. Refer to the table in the guide for a detailed list.
What should I do if I encounter a problem during installation?
If you encounter problems during installation, refer to the troubleshooting section. If the issue persists, contact a qualified technician.