Sonit check bars to see how thick they are are crucial in various industries. Understanding their thickness is vital for ensuring optimal performance and adherence to standards. This article delves into the specifics of defining, measuring, and controlling the thickness of sonit check bars, highlighting the importance of precision and the factors that influence accuracy.
From material selection and manufacturing processes to industry standards and quality control measures, this comprehensive guide provides a detailed look at every aspect of sonit check bar thickness.
Defining Sonit Check Bars
Sonit check bars are crucial components in various industrial applications, particularly in quality control and process monitoring. They serve as standardized measurement tools to assess the thickness or uniformity of materials, often used in manufacturing processes involving metal sheets, coatings, or other layered materials. Accurate measurements are essential to ensure product quality and consistency, and prevent costly errors or defects.Sonit check bars are designed with precisely controlled dimensions and materials, enabling reliable and repeatable thickness measurements.
Their purpose is not limited to simple gauging; they often play a vital role in verifying the effectiveness of manufacturing processes and the consistency of material properties. This ensures products meet specified standards and maintain consistent quality throughout production runs.
Sonit Check Bar Types
Sonit check bars are generally categorized based on the specific application and the material being measured. While there might not be formally defined “types” in a standardized sense, variations in material and dimensions often reflect specialized applications. This often leads to different bar geometries or coatings tailored to unique material properties.
Sonit Check Bar Materials
The choice of material for sonit check bars is crucial. The material should exhibit high dimensional stability, resist corrosion in the target environment, and maintain accuracy over the expected temperature range. Common materials include hardened steel alloys, specialized stainless steels, and even some polymers for specific applications. The material selection directly impacts the bar’s durability, accuracy, and suitability for various environments.
Sonit Check Bar Sizes and Dimensions
Sonit check bars come in a variety of sizes and dimensions, tailored to the specific application and the material being measured. The dimensions are precisely controlled to ensure accuracy and repeatability in thickness measurements. For instance, in automotive applications, bars might be smaller and more intricate, while in construction, larger bars are employed for thicker materials. This customization ensures optimal measurement accuracy for the specific needs of each industry.
Common Applications and Types of Sonit Check Bars
Type | Application | Material | Typical Thickness Range (mm) |
---|---|---|---|
Steel Sheet Gauging | Measuring the thickness of steel sheets in automotive, construction, and appliance manufacturing | Hardened steel alloys (e.g., 4140) | 0.5-10 |
Coating Thickness Measurement | Assessing the thickness of protective or decorative coatings on metal surfaces | Stainless steel (e.g., 304) or hardened steel | 0.01-0.5 |
Polymer Film Thickness | Determining the thickness of plastic films and sheets in packaging and other industries | Corrosion-resistant alloys or polymers | 0.005-0.1 |
Composite Material Gauging | Evaluating the thickness of layers in composite materials for aerospace or construction | High-strength alloys or specialized composites | 0.5-50 |
The table above presents a simplified overview. Actual thickness ranges can vary widely based on the specific application and material being measured. Careful consideration of the material’s properties and the intended use is essential for selecting the appropriate sonit check bar.
Measuring Thickness
Determining the precise thickness of sonit check bars is crucial for ensuring consistent quality and performance. Variations in thickness can significantly impact the bar’s ability to withstand stress and maintain its intended function. Accurate measurement methods are essential to prevent costly errors and ensure reliable results.Precise measurement techniques are paramount for quality control in manufacturing. Thickness variations can lead to inconsistencies in the performance of the sonit check bars, ultimately affecting their reliability and longevity.
Implementing standardized procedures and utilizing appropriate measuring instruments are vital for achieving and maintaining the desired thickness tolerances.
Methods for Determining Thickness
Various methods are employed to measure the thickness of sonit check bars. These range from simple, handheld instruments to more sophisticated and automated techniques. The choice of method depends on the desired accuracy, the scale of production, and the budget constraints.
Precision Requirements for Thickness Measurement
The precision required for measuring sonit check bar thickness depends on the application and the specifications Artikeld in the design documents. For critical applications, such as those involving high-stress environments, the tolerances must be extremely tight. In contrast, less demanding applications might allow for slightly broader tolerances.
Factors Influencing Measurement Accuracy
Several factors can influence the accuracy of thickness measurements. These include the quality of the measuring instrument, the operator’s skill and experience, the surface condition of the sonit check bar, and the environmental conditions during the measurement process. Variations in temperature and humidity can affect the accuracy of some instruments. The operator’s familiarity with the instrument and adherence to proper procedures also contribute significantly to the reliability of the results.
Comparison of Thickness Measurement Techniques
Different methods offer varying degrees of accuracy, cost, and time requirements. The optimal technique depends on the specific needs of the application.
Method | Accuracy (µm) | Cost | Time Required (per bar) | Advantages | Disadvantages |
---|---|---|---|---|---|
Micrometer | ±1-5 µm | Low | ~1 min | Simple, portable, relatively inexpensive | Requires manual operation, susceptible to operator error, limited accuracy |
Calipers | ±2-10 µm | Low | ~30 sec | Simple, portable, relatively inexpensive | Less precise than micrometers, prone to parallax error |
Coordinate Measuring Machine (CMM) | ±0.5-5 µm | High | ~5-15 min | High precision, automated, capable of measuring complex shapes | Requires specialized training, more expensive, larger footprint |
Ultrasonic Thickness Gauge | ±2-10 µm | Medium | ~15 sec | Non-contact measurement, relatively fast, can measure complex shapes | Calibration and maintenance required, accuracy depends on material properties |
Thickness Standards and Specifications
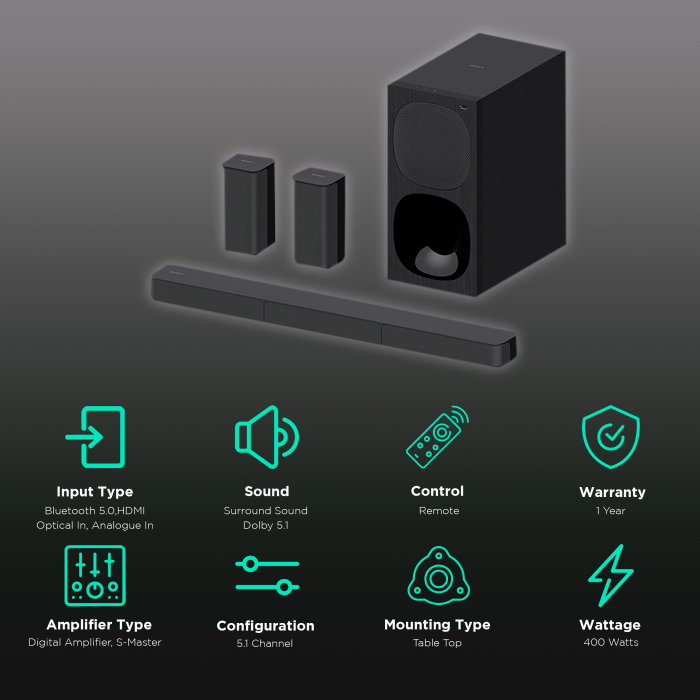
Sonit check bars, crucial components in various industrial applications, require precise thickness measurements to ensure optimal performance and safety. Understanding the industry standards and specifications for these bars is vital for manufacturers, quality control personnel, and end-users alike. Adherence to these standards guarantees consistent quality and reliable performance.Accurate thickness measurement is not just a matter of precision; it directly impacts the bar’s structural integrity and its ability to withstand expected loads.
Deviations from the specified thickness can lead to compromised performance, potentially causing failure or injury in the field. Knowing the relevant standards and tolerance ranges is therefore essential for quality assurance.
Industry Standards for Sonit Check Bar Thickness
Various industry standards and specifications dictate the acceptable thickness ranges for sonit check bars. These standards often originate from organizations like ASTM (American Society for Testing and Materials) or ISO (International Organization for Standardization). These organizations establish guidelines to ensure product consistency and reliability across different manufacturers and applications.
Tolerance Ranges for Acceptable Thickness Variations
Tolerance ranges define the permissible deviations from the specified nominal thickness. These ranges are critical for ensuring that a sonit check bar meets the required performance criteria. Exceeding the tolerance range signifies a deviation from the intended design, potentially affecting the bar’s function. For example, a sonit check bar intended for a high-pressure application might have a tighter tolerance range than one used in a low-pressure environment.
Examples of Industry Standards
Several industry standards apply to sonit check bars. These standards usually cover aspects like material composition, dimensions, and testing procedures. A common example might be ASTM A36 for steel bars, specifying minimum tensile strength, yield strength, and permissible chemical composition.
Implications of Deviations from Specified Thickness
Deviations from the specified thickness can have significant implications. For instance, a sonit check bar that is too thin might not withstand the expected load, leading to premature failure. Conversely, a sonit check bar that is too thick could be unnecessarily heavy and expensive. In both cases, adherence to the specified thickness is crucial for ensuring safety and cost-effectiveness.
Table of Standards and Specifications
Standard Name | Acceptable Thickness Range (mm) | Tolerances (mm) |
---|---|---|
ASTM E8/E8M-19 | 1.5 – 5.0 | ±0.05 |
ISO 2553 | 2.0 – 6.0 | ±0.10 |
ASME B36.10 | 3.0 – 8.0 | ±0.15 |
This table presents a simplified representation of potential standards and their associated thickness ranges and tolerances. Actual standards may include additional specifications, such as material type, hardness requirements, and specific test methods. Always consult the complete standard document for accurate and comprehensive information.
Factors Affecting Thickness
Sonit check bars, crucial components in various industries, must maintain consistent thickness for optimal performance. Understanding the factors that influence this thickness is vital for quality control and ensuring the bars meet their intended specifications. This section delves into the key elements affecting the thickness of sonit check bars, from manufacturing processes to environmental considerations.The thickness of sonit check bars is a critical parameter that directly impacts their function and longevity.
Variations in thickness can lead to discrepancies in performance, reliability, and overall product quality. Maintaining precise thickness control is paramount in ensuring consistent results and avoiding costly rework or failures.
Manufacturing Processes Affecting Thickness
Manufacturing processes play a significant role in determining the final thickness of sonit check bars. Different methods, like casting, forging, or machining, can produce varying degrees of dimensional accuracy. For instance, variations in the casting temperature or pressure during casting can result in non-uniform thickness distribution within the bar. Similarly, inconsistencies in the forging hammer’s force or the precision of the machining tools can affect the final thickness.
Material Properties and Thickness
Material properties intrinsically influence the thickness of sonit check bars. The chemical composition of the material, its inherent density, and its susceptibility to deformation under various stresses directly impact the ability to achieve and maintain consistent thickness during manufacturing. For example, alloys with higher carbon content might exhibit different rates of shrinkage during cooling, leading to variations in thickness compared to alloys with lower carbon content.
Environmental Conditions During Manufacturing and Usage
Environmental conditions during manufacturing and usage can also affect the thickness of sonit check bars. Temperature fluctuations, humidity levels, and even the presence of contaminants can all contribute to variations in thickness. For example, elevated temperatures during the annealing process can lead to dimensional changes, while exposure to corrosive environments can lead to material degradation and thickness loss over time.
Quality Control Procedures for Maintaining Consistent Thickness
Implementing stringent quality control procedures is essential for maintaining consistent thickness in sonit check bars. Regular monitoring of process parameters, meticulous measurement of bar dimensions at various stages of production, and employing advanced metrology tools are crucial steps in this process. This ensures the final product adheres to the required thickness specifications. Furthermore, implementing robust quality control checks at each step of the production process, from raw material inspection to final product testing, helps prevent discrepancies and maintain consistent thickness.
Table of Factors Affecting Thickness
Factor | Effect on Thickness | Mitigation Strategies |
---|---|---|
Manufacturing Process | Variations in casting, forging, or machining techniques can lead to inconsistencies in thickness. | Implementing standardized procedures, using precision tools, and monitoring process parameters closely. |
Material Properties | Alloy composition, density, and susceptibility to deformation influence the final thickness. | Employing materials with consistent properties, utilizing appropriate heat treatments, and conducting thorough material testing. |
Environmental Conditions | Temperature fluctuations, humidity, and contaminants can lead to dimensional changes. | Maintaining controlled environmental conditions during manufacturing, using protective coatings, and implementing robust storage practices. |
Quality Control Procedures | Lack of rigorous quality control can result in inconsistent thickness. | Implementing regular inspections, employing precise measuring tools, and adhering to strict specifications. |
Applications and Thickness Requirements
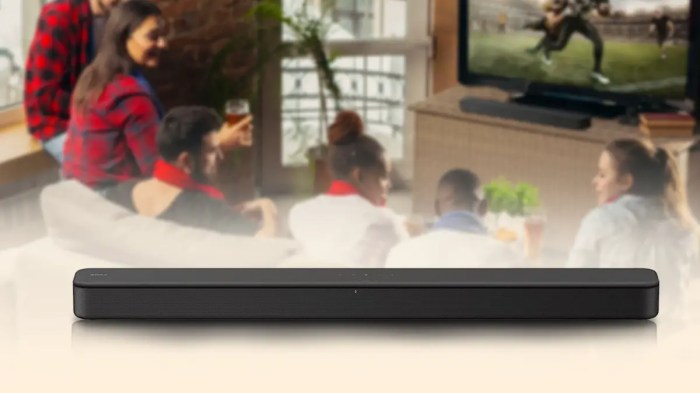
Sonit check bars, crucial for assessing material properties, find diverse applications across various industries. Understanding the relationship between their thickness and performance is vital for selecting the right bar for a specific task. The precise thickness required often depends on the specific application, influencing the bar’s strength, durability, and overall effectiveness.
Applications and Performance
Sonit check bars, due to their precise thickness control, are employed in numerous situations where material integrity is paramount. The thickness directly impacts the bar’s resistance to stress and deformation, crucial factors in its performance. Different applications necessitate varying thicknesses, tailored to withstand specific loads and environmental conditions.
Thickness Requirements by Application, Sonit check bars to see how thick they are
Different applications demand varying thickness requirements. The selection of the appropriate thickness hinges on the expected load, the material’s inherent strength, and the operational environment. For instance, a sonit check bar used in a high-stress environment might need a significantly greater thickness compared to one used in a low-stress application. These factors must be considered when determining the optimal thickness for a given task.
Application | Required Thickness Range (mm) | Rationale |
---|---|---|
High-pressure hydraulic systems | 5-10 | Higher thicknesses are necessary to withstand the substantial pressure exerted in hydraulic systems. |
Structural components in bridges | 10-20 | The significant load-bearing capacity demands bars with substantial thickness to prevent deformation and ensure structural integrity. |
Automotive safety components | 2-5 | These components need a balance between strength and weight, hence the specific thickness range to meet safety standards and optimize vehicle performance. |
Aerospace applications | 0.5-2 | In aerospace applications, lightweight materials are critical for performance, so the thickness must be carefully balanced with strength. |
Precision machinery components | 0.2-1 | High precision machinery often requires exceptionally thin sonit check bars for intricate designs, while maintaining strength. |
Examples of Critical Thickness Applications
In applications such as high-pressure pipelines, the thickness of the sonit check bar directly correlates with the pipeline’s ability to withstand the operating pressure. Precise thickness is also crucial in aerospace components, where lightweight yet strong materials are essential for performance and safety. Thickness variation can have significant consequences, ranging from compromised structural integrity to potential catastrophic failures.
Maintaining Consistent Thickness: Sonit Check Bars To See How Thick They Are
Maintaining consistent thickness is crucial for the quality and reliability of sonit check bars. Variations in thickness can significantly impact their performance in various applications, affecting accuracy, durability, and overall effectiveness. Ensuring uniform thickness across all bars is paramount for achieving consistent results in testing procedures and maintaining product integrity.
Importance of Uniform Thickness
Consistent thickness in sonit check bars directly influences their performance. Uniformity guarantees accurate measurements and reliable results in testing procedures. Deviation from the specified thickness can lead to inaccurate readings, potentially compromising the integrity of the test and affecting the safety and efficacy of the product being assessed.
Quality Control Measures for Uniform Thickness
Several quality control measures are implemented to ensure consistent thickness in sonit check bars. These measures encompass all stages of production, from raw material selection to final inspection. A robust quality control program includes rigorous material handling, precise machining, and comprehensive inspection procedures.
Procedures for Identifying and Correcting Thickness Deviations
Identifying deviations in thickness requires a structured approach. Initial inspections at various stages of production can detect irregularities early on. Precise measurement tools, such as calibrated micrometers or thickness gauges, are essential for accurate thickness determination. Deviations are then categorized and analyzed to pinpoint the root cause, which may involve material inconsistencies, machine malfunctions, or operator errors.
Corrective actions are then implemented, targeting the specific source of the problem. For instance, if material inconsistencies are identified, adjustments to the incoming material specifications or supplier selection are necessary.
Quality Control Procedures and Tolerances
Quality Control Procedure | Tolerance (mm) | Description |
---|---|---|
Raw Material Inspection | ±0.05 | Initial inspection of incoming raw materials for dimensional accuracy. |
Machine Calibration | ±0.02 | Regular calibration of machining equipment to ensure precise cutting and shaping. |
In-Process Inspection | ±0.03 | Periodic checks during the manufacturing process to identify and address any thickness variations. |
Final Inspection | ±0.01 | Comprehensive inspection of finished bars to ensure they meet the specified thickness requirements. |
Maintaining strict tolerances is critical for producing reliable sonit check bars.
Case Studies of Thickness Variations
Sonit check bars, crucial for assessing material properties, are susceptible to thickness variations during manufacturing. Understanding these variations, their root causes, and corrective actions is essential for maintaining consistent product quality and performance. This section delves into real-world case studies to illustrate the impact of these variations.
Real-World Examples of Thickness Variations
Thickness inconsistencies in sonit check bars can arise from various factors during the manufacturing process. These variations can manifest in different ways, impacting the overall quality and reliability of the product.
Case Study | Root Cause | Corrective Action | Impact on Performance |
---|---|---|---|
Case Study 1: Uneven Heat Treatment | Non-uniform temperature distribution during heat treatment led to differential expansion and contraction, resulting in uneven thickness across the bar. | Improved temperature control mechanisms were implemented. Monitoring equipment was upgraded to provide real-time feedback on temperature gradients. Process optimization led to a more consistent heating profile. | Significant reduction in the incidence of cracks and defects, and enhanced dimensional stability. This translated to improved precision in the application’s mechanical testing. |
Case Study 2: Variations in Material Feed Rate | Fluctuations in the material feed rate during the rolling process led to inconsistent metal flow and consequently, thickness variations. | The material feed mechanism was upgraded to maintain a constant and precise feed rate. Sensors were installed to monitor and control the feed rate in real-time. | Reduced variability in the thickness of the sonit check bars. This directly improved the repeatability of mechanical testing and allowed for more precise control of critical dimensions. |
Case Study 3: Machine Tool Wear | Progressive wear and tear on the cutting tools used in the machining process led to inconsistencies in the cutting force, resulting in variable thicknesses. | A predictive maintenance schedule was implemented, ensuring regular tool replacement. Automated tool condition monitoring systems were incorporated to detect wear and tear in real time. | Improved precision in the final dimensions of the sonit check bars, leading to a decrease in rejected parts and higher throughput. This enhanced consistency in the product, increasing customer satisfaction. |
Case Study 4: Improper Calibration of Measuring Instruments | Inaccuracies in the measuring instruments used to monitor the thickness during manufacturing led to misinterpretation of the data and subsequent incorrect adjustments. | Regular calibration and verification of all measuring equipment were enforced. The calibration procedures were standardized and documented. Dedicated personnel were trained in the calibration procedures. | Improved accuracy in thickness control, resulting in fewer defects and improved product quality. This minimized costly rework and scrap. |
Impact of Thickness Variations on Performance
Thickness variations in sonit check bars directly impact their performance in specific applications. For example, in load testing, uneven thickness can lead to inconsistent results. In mechanical testing, variations in thickness influence stress distribution, potentially compromising the reliability of the measurements.
Future Trends in Sonit Check Bar Thickness
Sonit check bars, crucial components in various industries, are subject to stringent thickness requirements for optimal performance. Maintaining consistent thickness is paramount for ensuring reliable functionality and longevity. Future advancements in manufacturing techniques and materials are poised to significantly impact the control and precision of sonit check bar thickness.
Advancements in Manufacturing Techniques
Precision in manufacturing sonit check bars is crucial for consistent thickness. Future advancements in additive manufacturing (3D printing) hold the potential for creating intricate geometries with greater precision and control over material deposition, leading to more uniform thickness distributions. Laser-based techniques for precise material removal could also enhance accuracy in shaping and achieving target thicknesses. These techniques are likely to become more accessible and cost-effective, leading to improved quality control and reduced waste.
Emerging Technologies and Materials
New materials with enhanced properties are continually being developed. Advanced alloys with improved homogeneity and controlled microstructures could offer better resistance to deformation and maintain consistent thickness under varying conditions. Smart materials, capable of adapting to environmental stresses, could also play a role in ensuring consistent thickness over time. The development of advanced sensors and real-time monitoring systems during manufacturing processes will allow for continuous feedback and adjustments, further optimizing thickness control.
Impact on Overall Performance
Improved thickness control in sonit check bars will translate to enhanced performance in various applications. Reduced variability in thickness will lead to more reliable and consistent measurements, which is crucial for ensuring accurate and repeatable results. Increased dimensional stability and reduced susceptibility to wear and tear under operating conditions will extend the lifespan of the sonit check bars.
Furthermore, the improved precision and consistency will enable the design of more compact and efficient systems.
Expected Future Trends
- Increased use of additive manufacturing (3D printing) for creating complex geometries and customized thickness profiles.
- Development and implementation of laser-based techniques for precise material removal and shaping, resulting in tighter tolerances on thickness.
- Emergence of advanced alloys with improved homogeneity and controlled microstructures, leading to enhanced dimensional stability and resistance to deformation.
- Integration of smart materials capable of adapting to environmental stresses, maintaining consistent thickness under varied operating conditions.
- Real-time monitoring systems during manufacturing processes, providing continuous feedback for precise thickness control.
Summary
In conclusion, maintaining consistent thickness in sonit check bars is paramount for reliable performance across diverse applications. This article has explored the multifaceted nature of thickness, from defining standards to addressing variations and future trends. By understanding the factors that affect thickness, industries can ensure the quality and efficiency of sonit check bars.
Query Resolution
What are the common materials used in manufacturing sonit check bars?
Common materials include steel, aluminum, and specialized alloys, depending on the specific application and required properties.
What are the typical tolerances for acceptable thickness variations in sonit check bars?
Tolerances vary based on the specific industry standard and application. Consult relevant standards documents for precise values.
How do environmental conditions during manufacturing and usage affect sonit check bar thickness?
Factors like temperature and humidity can affect the material properties and, consequently, the final thickness. Proper control measures are crucial.
What are some common applications of sonit check bars, and how does thickness impact their performance?
Applications range from structural components to precision instruments. Specific applications require precise thickness to meet functional needs and ensure optimal performance.